Sulphur 387 Mar-Apr 2020
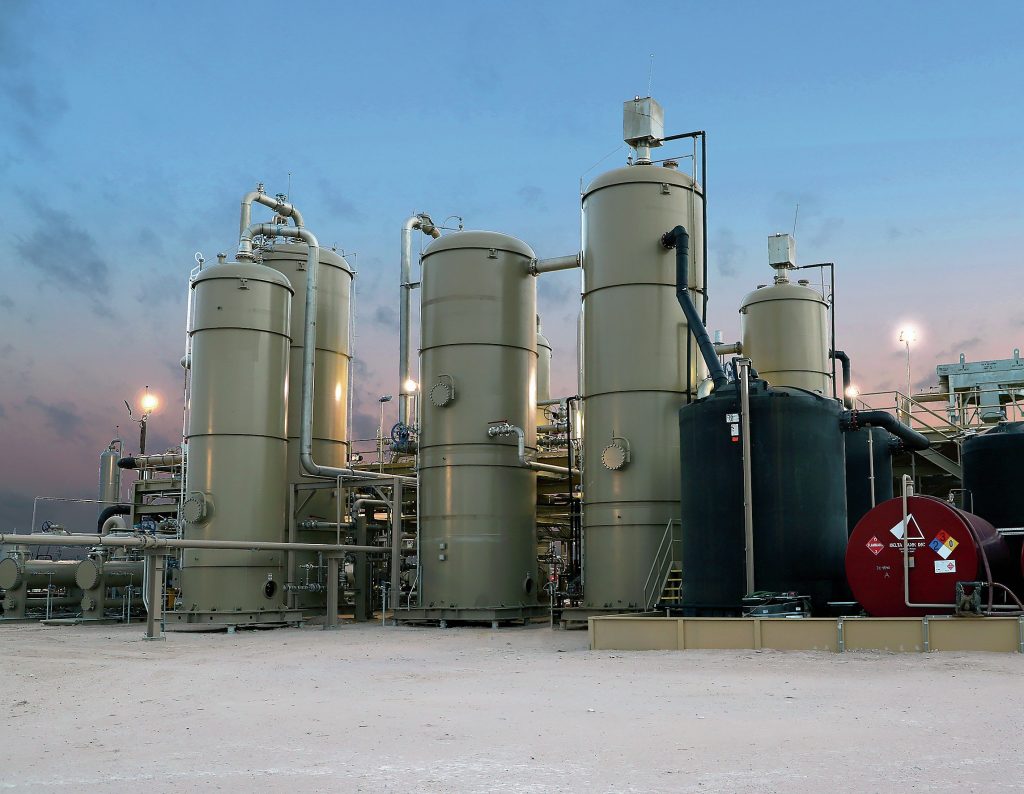
31 March 2020
Redox reborn – the Valkyrie™ process
REDOX TECHNOLOGY
Redox reborn – the Valkyrie™ process
J. C. Bourdon, F. H. Brown and P. J. Photos of Streamline Innovations Inc. present the development and commercialisation of the Valkyrie™ process, which employs new chemistries and advanced control systems to remove H2S from natural gas at size scales ranxging from single wells to entire fields, providing an operationally sustainable and commercially attractive alternative to standard H2S removal technologies.
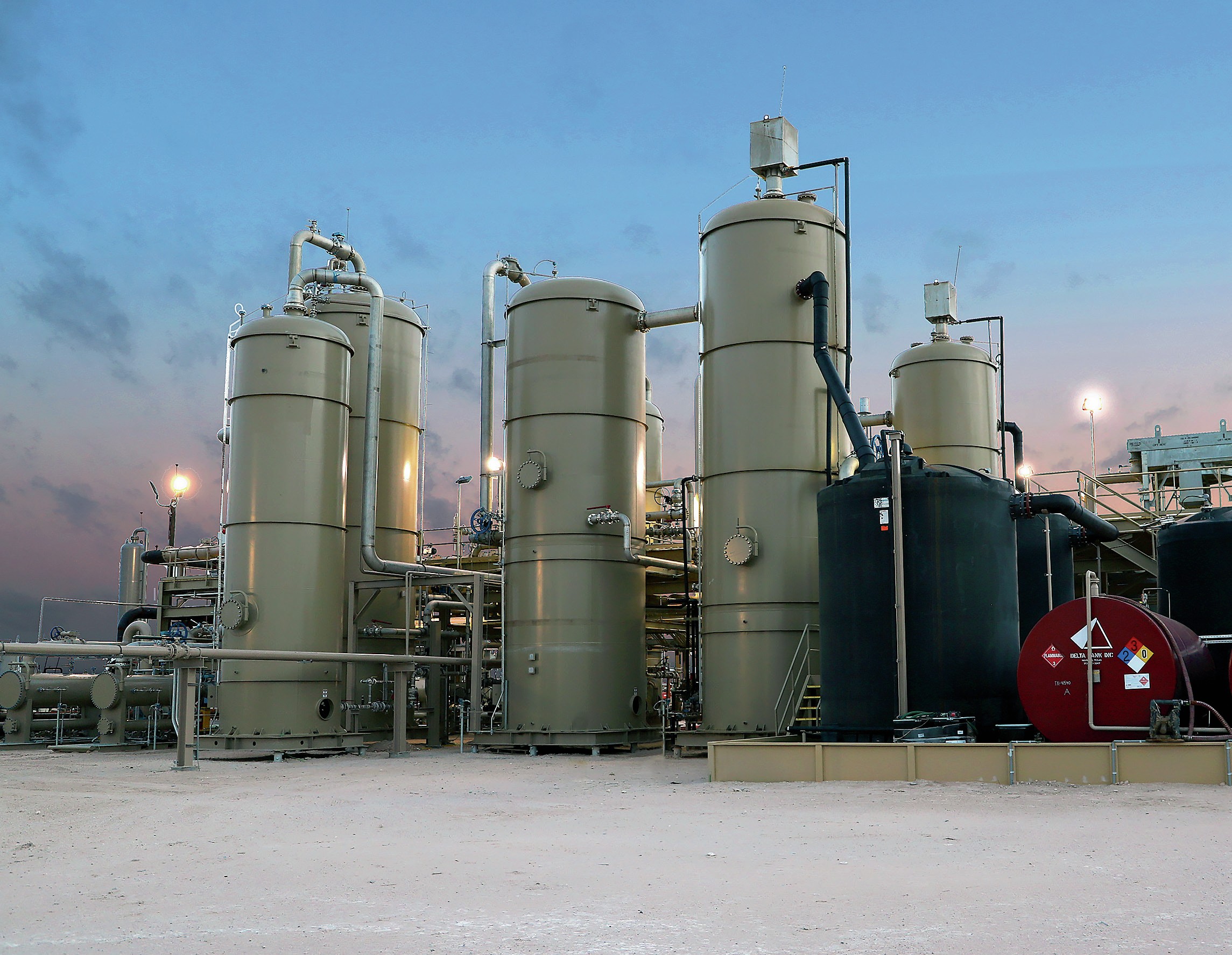
While the demand of natural gas in industrial and commercial processes has increased exponentially in the past few decades, its abundant supply and therefore relatively low cost have led to a need for efficient and economic removal of hydrogen sulphide (H2S) from the gas stream. Gas production has traditionally concentrated on sweet gas fields, but their depletion has shifted the focus towards sour greenfields and enhanced recovery in soured brownfields. In both cases, however, the large capital costs and lengthy construction times to build Claus-based sulphur recovery units (SRUs) or acid gas injection wells (AGIs) as well as the necessary sour service equipment associated with treating has caused many producers to examine treating H2S as close to the wellhead as possible. However, at-well or near-well treating can be costly from an operating standpoint as treating options for modest quantities of H2S are limited to scavenger-based treatment, such as triazine, iron oxides, or zinc oxides, historically used only to treat small quantities of sulphur. This has left producers with a decision between high capex-low opex facilities with long lead times or low capex-high opex scavenger-based units.
This capex-opex balance has been an especially difficult problem for producers when the quantity of H2S that needs to be removed is not significant enough to warrant the extensive capital investments associated with an SRU or AGI, but the chemistry costs for scavenger-based treating can be prohibitive.
Amine has always been a robust and attractive solution for removal of H2S and CO2 from gas streams, but the tail gas produced by that process requires either disposal in an AGI or processing through an SRU. Even the use of a SRU requires further treatment, as the tail gas from that process contains too much H2S for atmospheric venting or flaring. Thus, any solution involving amine treatment requires a secondary treatment methodology, each with its own cost and limitations. Further complications with downtime of AGIs1 , as well as regulatory hurdles required for their construction and maintenance add an additional complexity in determining the correct methodology to remove H2S2 .
A comparison of technologies is given in Table 1. The opex and capex of each technology can then be further analysed to yield an effective cost per pound of treatment to give a range of sizes for which each technology is most economic (Fig. 1). Redox occupies an important range between roughly 0.1 – 20 long t/d in sulphur treatment; not coincidentally, this range is also the fulcrum of the opex-capex conundrum.
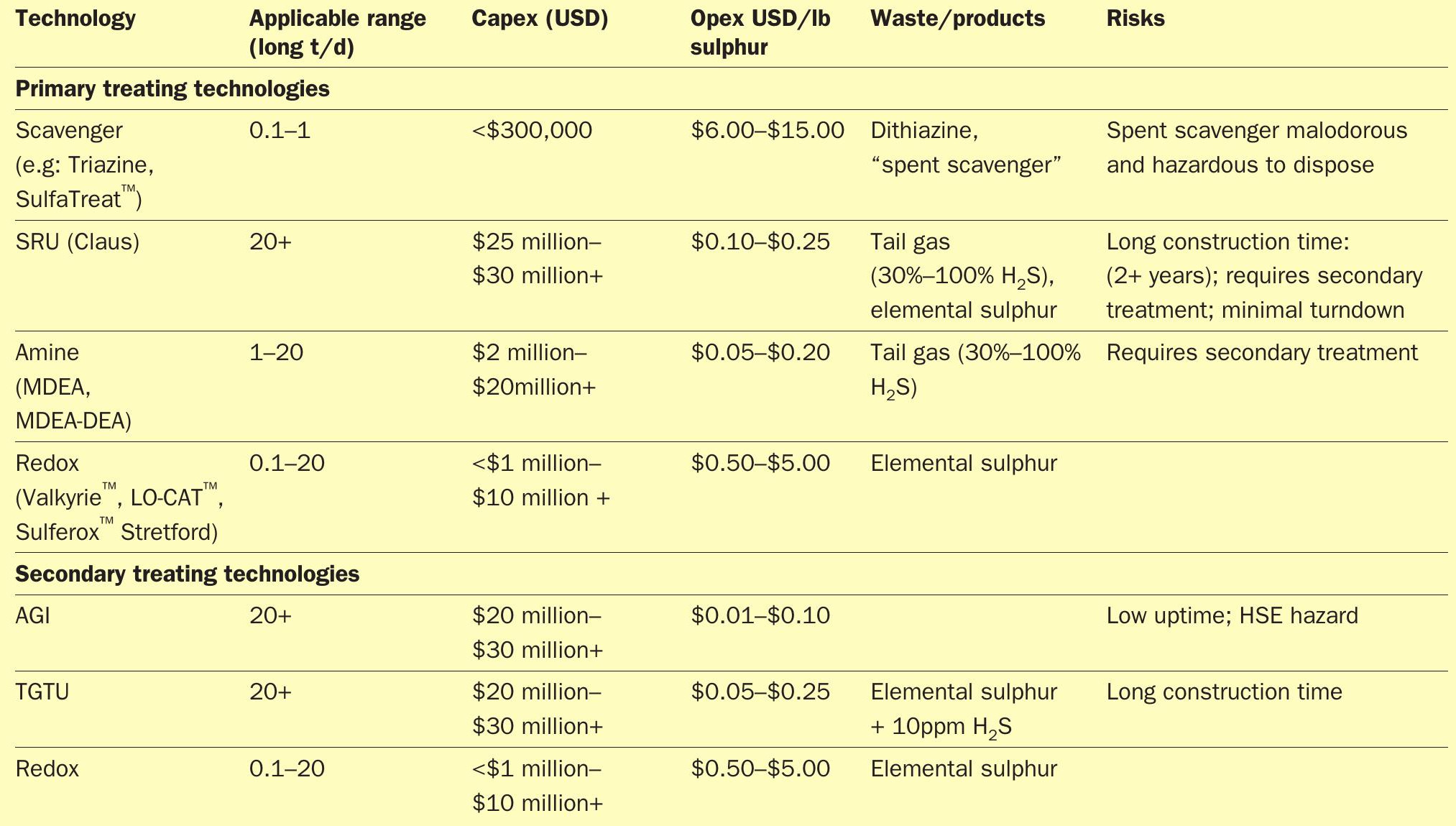
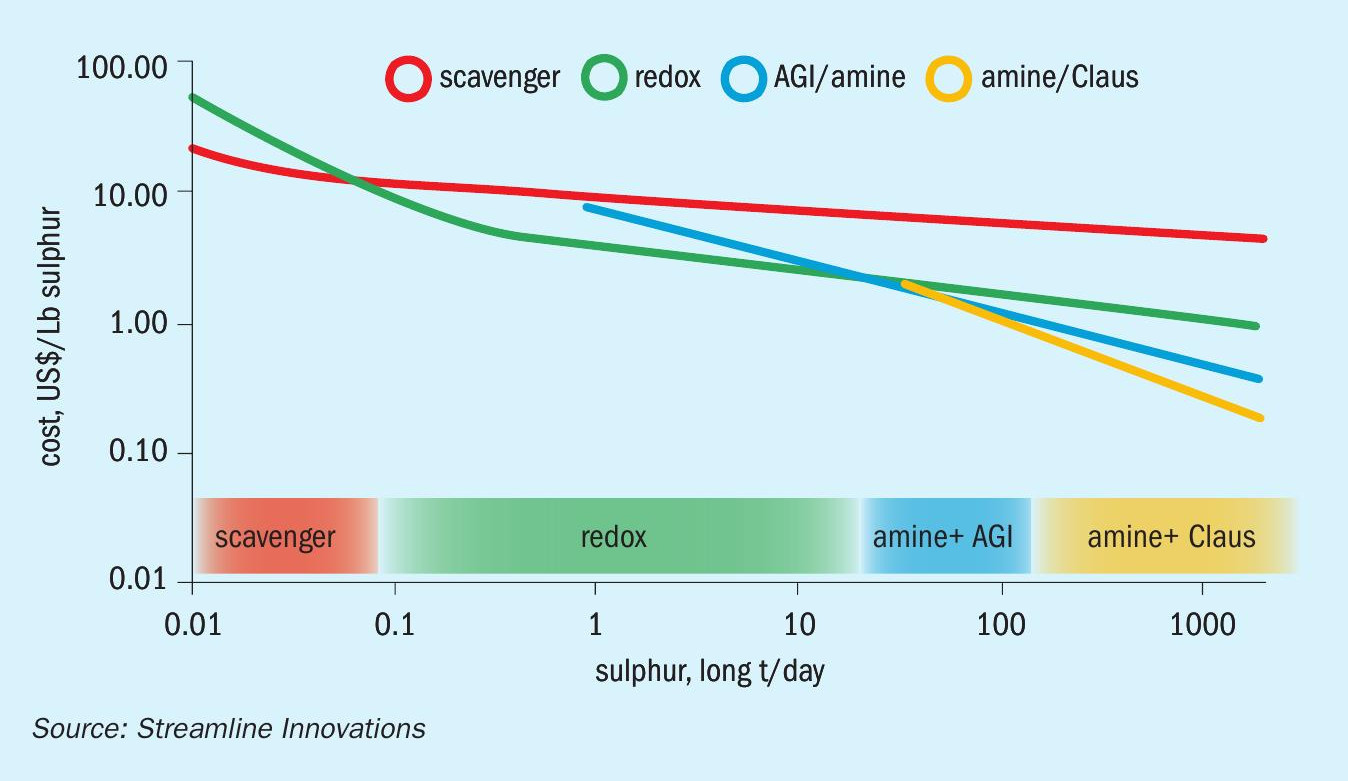
H2S removal using oxidation-reduction chemistries therefore have long been an attractive solution, as the construction costs are modest compared to SRUs or AGIs, and their operating costs are a fraction of scavengers due to their regenerative chemistry. A number of attempts at commercialisation of such processes have been made – Sulferox™ , LO-CAT™ , and Stretford™ – however, these processes have evaded ubiquitous usage due to limitations in capital construction costs, operative sustainability, and/or the use of chemistries that are difficult to manage and by-products that are hard to dispose of.
The history of redox
A variety of chemistries have been used to employ the redox process to treat H2S. Typically, any chemistry whose reversible states have reduction potentials between H2S → S↓ + 2H– and 2H– + O2 → 2OH– can be used as a pseudo-catalyst in the reaction. The first successfully commercialised process was the Stretford process developed in the late 1940s which used a chelated vanadium cation as the catalyst. However, problems with vanadium handling as well as the formation of hazardous by-products in the reaction restricted its adoption. The Sulferox and LO-CAT process, developed in the 1970s and 1980s, employed chelated iron rather than vanadium, which reduced the production of toxic side reactions. These processes showed some commercial success but eluded ubiquitous adoption due to operational difficulties, including the formation of emulsions which were difficult to manage, and wide variability in operational efficiencies. Nonetheless, these processes are still used, boasting operational successes from 0.1 long t/d of sulphur up to 20 long t/d.
The primary advantage of the redox process is that the chemistry is regenerative; many metals can work, but in the case of chelated iron, Fe3+ is reduced to Fe2+ and oxidised back to Fe3+ continuously, with the chelant keeping the cations from precipitating throughout the process. The makeup volumes, and therefore the treatment cost, depend almost exclusively on the management of chemical losses. Losses occur through either:
- degeneration of the chelant which keeps the iron in solution;
- inadvertent disposal of chemistry with the elemental sulphur removal;
- unexpected carryover of chemistry out of the system, exacerbated by foaming;
- operational losses that occur during maintenance.
Managing these channels ensures an extremely cost-effective method to remove H2S.
A further advantage of redox is that the reactions used to treat H2S occur at a wide range of pressures and at ambient temperature, and therefore do not require any compression or heating of the gas, imparting a low-energy consumption.
Despite these advantages, redox has historically only gained a niche market in the oil and gas world, as it also has a number of technical and economic challenges that made it a “less than optimal” choice for H2S removal. The choice of first generation chelants such as EDTA, and second generation chelants such as HEDTA and NTA are subject to degradation during the oxidation process to form oxalates, which lead to iron precipitation and chemistry loss. The oxalates themselves further reduce operational efficiency by imparting a stickiness to the elemental sulphur, which must be landfilled for disposal. Finally, the system is subject to the development of highly stable Pickering emulsions, due to the presence of multiple states of matter (solid sulphur, aqueous solution, hydrocarbon condensate, and natural gas and/or air), which further create undesirable solids at the tops of vessels and promote carryover out of the system.
Revisiting redox – the Valkyrie™ process
The Valkyrie™ process was developed in the late 2010s to mitigate many of the issues associated with the redox process. This process retains the chelated iron pseudo-catalyst, but extends the life of the complex with the addition of three important changes:
- selecting a novel chelant that is resistant to degradation, thereby imparting a longer circulation time, lower make-up rates, and lower oxalate formation;
- using bespoke defoaming surfactants and wetting agents to promote sulphur settling, minimise chemical loss in the filter, and destroy Pickering emulsions; and
- employing advanced process control techniques, including machine learning and artificial intelligence, as well as proprietary instrumentation to allow monitoring and control of the extent of reaction, thereby increasing chelant lifetime and optimising operation.
Chelant selection
Towards the end of the 1990s, new classes of chelants were developed to replace the use of phosphate-based rinsing agents in dishwashing detergents, which were ultimately banned in most countries by 2011. These ‘third generation’ chelants (first being chemicals such as EDTA and citrates, second being derivatives such as HEDTA and NTA) showed significant advantage over its predecessors with a greater pKa towards metal cations, eco-friendliness, and robustness of use. Not surprisingly, a number of these showed applicability in other industries, including water treatment and as scale inhibitors. After screening a number of these molecules, it was discovered that a subset can also function as iron chelates in the redox process. These species can be further augmented with the addition of protective moieties on the molecule to impart a resistance to hydroxyl degradation. The development of this proprietary chelant – called Talon™ – is a key differentiator used in the Valkyrie™ process.
Surfactant selection
Redox-based sulphur recovery from natural gas has eluded full commercialisation partially due to the complexities of the multiphase nature of the process. The presence of multiple phases – oil, water, solid, and gaseous – promotes the creation of foams and emulsions that can cause operational difficulties, namely, pump cavitation, clogging, and sensor degradation.
The multiphase composition of the streams is further complicated by a wide swing in pH and temperature often seen in day-to-day operations. Historically, these swings have restricted the use of any single surfactant and/or demulsifiers to abrogate the challenges encountered.
While the use of anionic surfactants have been reported to be used in such systems, they are non-ideal because of their extreme foaming tendencies. Classical defoamers were also avoided as they were discovered to interfere with the oxidation-reduction chemistry. Additionally, the addition of such defoamers restricts the agricultural applications of the produced sulphur.
The novel blend of surfactants act in concert to inhibit emulsion formation, promote settling of sulphur, prevent foaming, and remove the solids phase from the system. Additional chemicals augment the process by leveraging their lower costs, slower kinetics and emulsion-breaking capabilities providing a cleaner filter cake.
Control systems
In order to maintain the optimal regenerative capabilities of the system (and therefore minimise operation costs), it is necessary to maintain the extent of reaction of the two chemical steps within a narrow range. To achieve this level of control, an ‘intelligent’, tiered control schema was developed that employs 1) a typical PLC, 2) a local computer to perform complex calculations on-site, and 3) additional computers in the cloud that can perform extended calculations to maintain system health (Fig. 2).
The PLC is configured with standard interlocks and basic controls to ensure that the system maintains the operation of the unit and functions moment-to-moment without interruption. However, much of the complex algorithms and calculations are beyond the capabilities of the machine and are ‘outsourced’ to a local computer running Python. Examples of such scripts include nonlinear calculations to maintain circulation rate and ‘soft sensor’ calculations that determine intermediate values used in the process. The system is designed such that the PLC is capable of maintaining the operation of the unit even if the Linux computer fails. This ensures that the system keeps the robustness of a PLC with the intelligence of modern-day computing.
Beyond the local calculations, the intelligent control system is able to locally store data and sync with servers in the cloud bidirectionally. This allows operators to maintain, troubleshoot and operate the unit completely by mobile app; when issues occur, text messages are automatically sent and the operator merely needs to login to the app to review the issue, examine earlier performance data and trends, and change operator parameters accordingly without having to go to site.
With such cloud capabilities, additional, non-critical calculations can be done off-site. These servers are not limited by processing capacity or robustness; they are cloud machines that can be expanded to meet the processing demand ad hoc. Examples of some of these calculations include the use of machine learning to auto-tune PID loops using multivariable regression analysis which report back to the local machine and FFT calculation on pumps to predict maintenance requirements, which automatically trigger maintenance tickets. Additional third party APIs can also be employed, for example in using forecasted temperature from weather services in pre-empting process temperatures or emergency shut down procedures employed during tornado warnings.
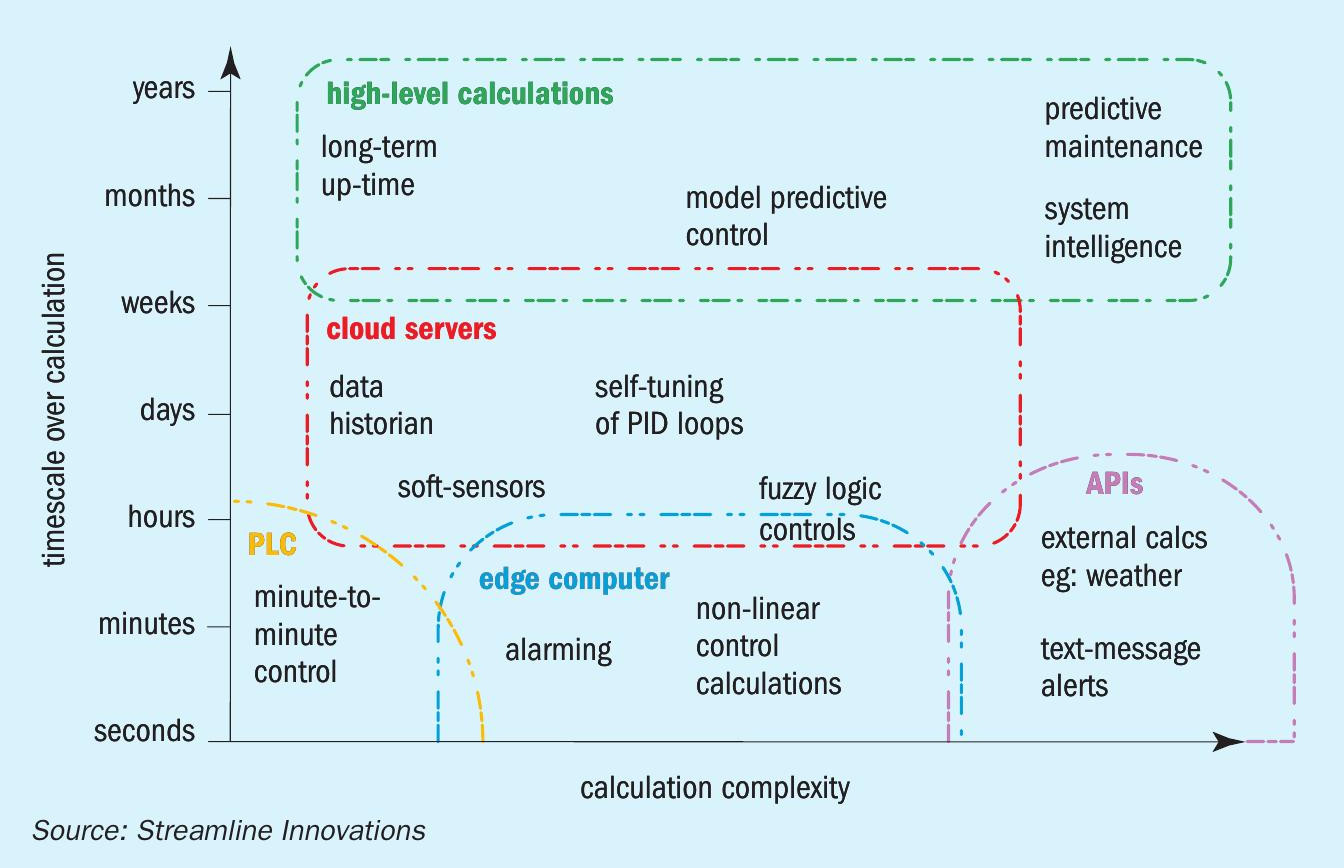
At the highest level of computing power, the reporting tools can accumulate data from all the machines, and provide operators and engineers with up-to-the-minute data. Relevant calculations between various units within one field that allow the units to ‘learn’ from one another, and improve their own autonomous operations.
Since the data is stored locally as well as in the cloud, the access to the system via the local Linux machine can viewed as the ‘primary’ human interface to the system. A ‘classic’ HMI – wherein the screen interfaces directly with the PLC itself, is limited in the number of access points and often requires proprietary equipment to control the unit. By interfacing with the Linux computer, any computer on site or on the web, properly authenticated, can operate the unit. With an ad hoc Wi-Fi network being broadcast on site, operators can use tablets in the field to access the HMI and troubleshoot, perform function checks on equipment, and even log events and information that is reported back with the raw data (Fig. 3).
The Valkyrie™ 3-step sulphur extraction system
The result of these changes means that the ‘traditional’ redox configuration can be employed to treat the H2S. The process flow diagram (Fig. 4) is similar to the Sulferox and Stretford processes.
Sour gas flows through a vapour-liquid separator and inlet filter coalescer which remove any hydrocarbon droplets. The clean, sour gas then flows into the contact tower where it contacts the Talon™ chemistry. The gas, free of hydrogen sulphide, flows out of the contactor and through a sweet gas vapour-liquid separator and outlet filter coalescer. The Talon™ chemistry containing elemental sulphur solids flows to the Talon regenerator where air is added and the Fe2+ is oxidised to Fe3+ . The regenerated Talon flows to a settling tank where the sulphur is settled and sent to filtration removing sulphur and returning the liquid Talon chemistry back to the settling tank. Clean Talon chemistry is pumped back into the contactor.
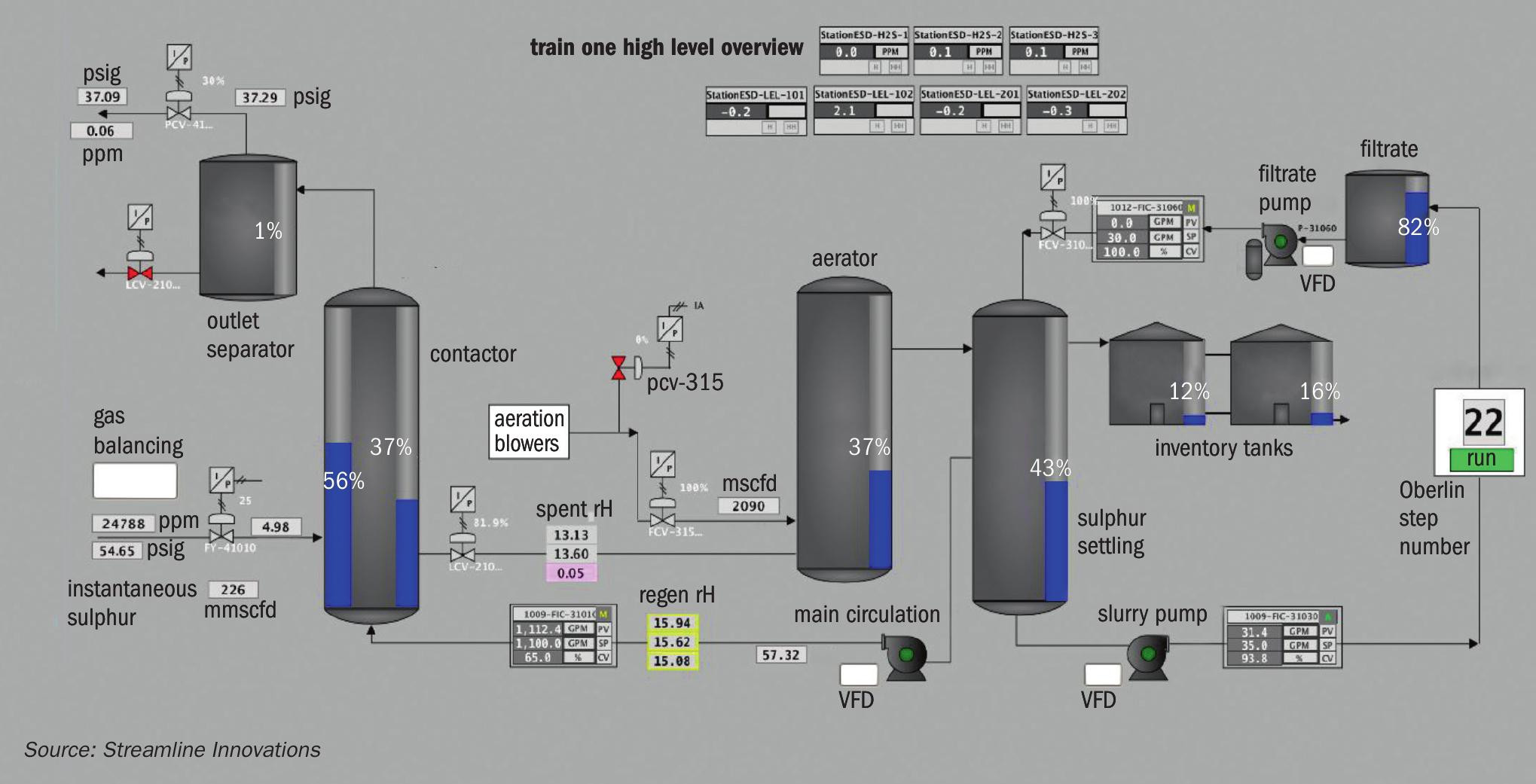
Step 1 – Combine sour gas containing H2S with “lean” chelated iron and produce elemental sulphur and “rich” chelated iron (Fig. 5).
Step 2 – “Rich” chelated iron flows to an aeration basin where it reacts with oxygen (in air) to release water and “lean” chelated iron (Fig. 6).
Step 3 – Elemental sulphur is sent to a filter press which drops sulphur cakes into a roll-off bin (Fig. 7).
Valkyrie™ applications
The Valkyrie™ redox process has several applications in oil and gas processing (Fig. 8). Since the process completely converts H2S to elemental sulphur regardless of H2S concentration, flow rate, or pressure, any sour gas stream between the wellhead and the pipeline, including tail gases, can be treated. Direct treatment – in which sour natural gas is sent through the process – can be done either at the wellhead using a small skid-based unit, or at a gathering facility with a custom-designed plant. Secondary treatment, i.e., post amine plant separation, can be performed on tail gases, giving the option of completely destroying H2S without the need for an AGI or SRU.
If NACE compression exists, applications at high pressure either direct or after amine treatment to concentrate the sour components into acid gas (H2S and CO2 ) can provide an economical alternative to acid gas injection, Claus sulphur recovery, or other technologies to remove or recover H2S.
Valkyrie™ operational results
To date, Valkyrie™ direct treat applications have been operating across west and south Texas at pressures between 30 psi to 180 psi, with designs in place to operate up to 1,440 psi, and flow rates between 0.75 and 25 million std ft3 /day.
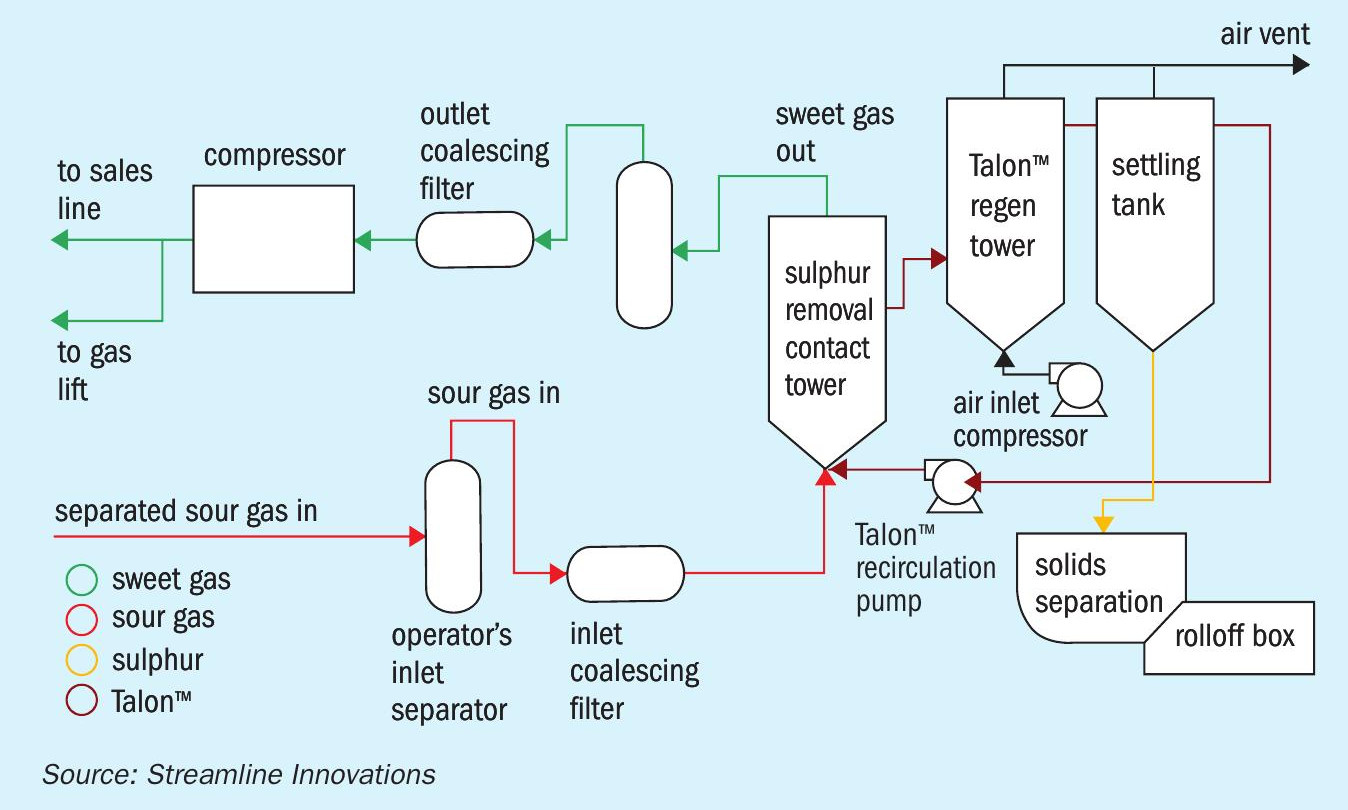
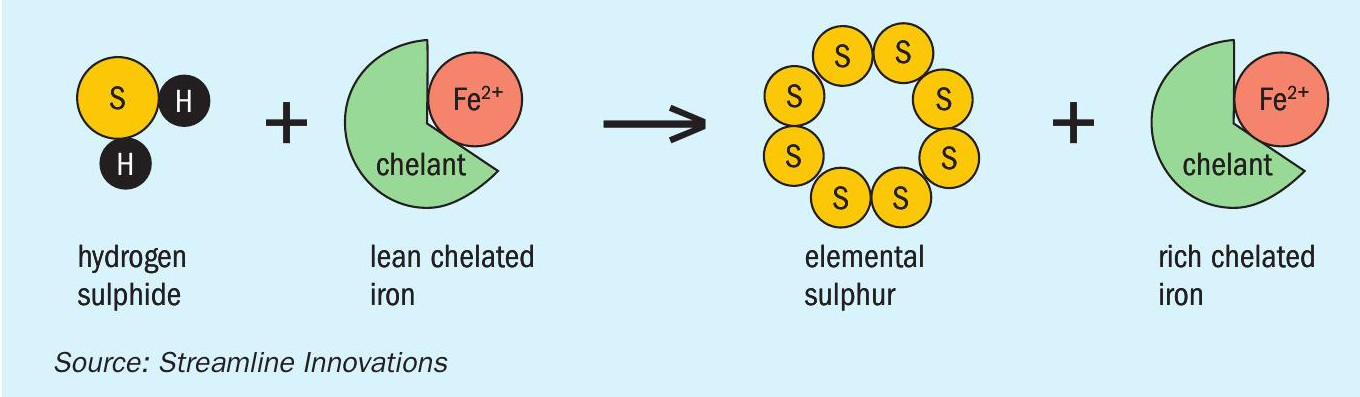
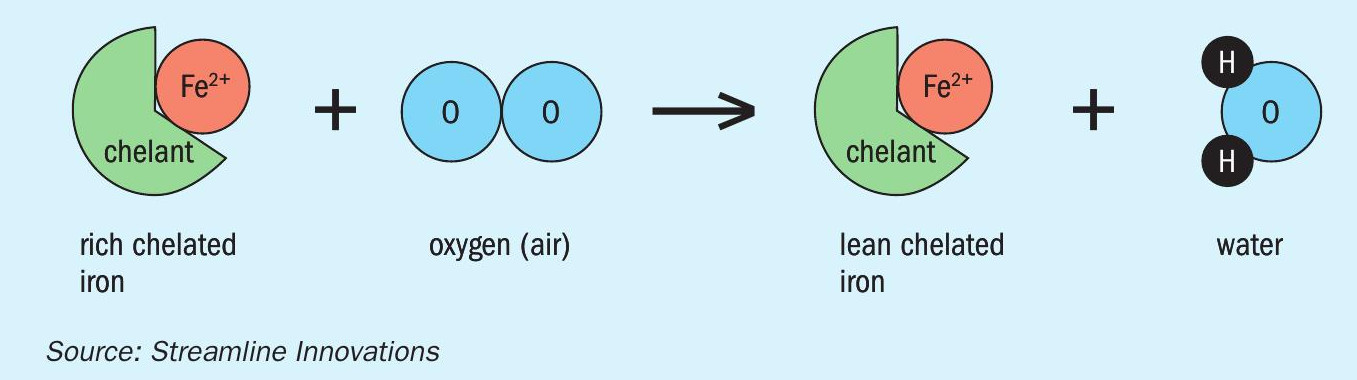
The process has successfully and continuously treated H2S levels from 200 ppm through 40,000 ppm, with a tail gas treater designed to handle 40% H2S under construction. In terms of sulphur loading, the Valkyrie™ process has demonstrated successful treatment from 0.1 long t/d up to 16 long t/d. All units have reported greater than 99% uptime, with a total number of cumulative operating hours of more than 40,000 hours. Since 2018, Valkyrie™ units have treated and produced over 9 million lbs of sulphur, or more than 4,000 long tons of sulphur. At no time was the level of H2S measured in the outlet gas stream greater than 4.0 ppm, and it was less than 1.0 ppm for greater than 99.9% of the operating time (Fig. 9).
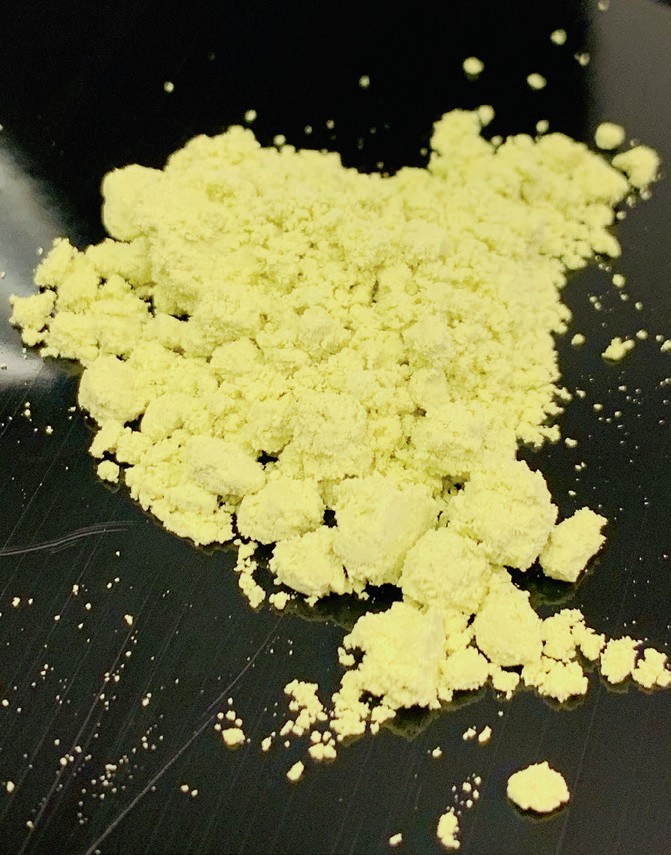
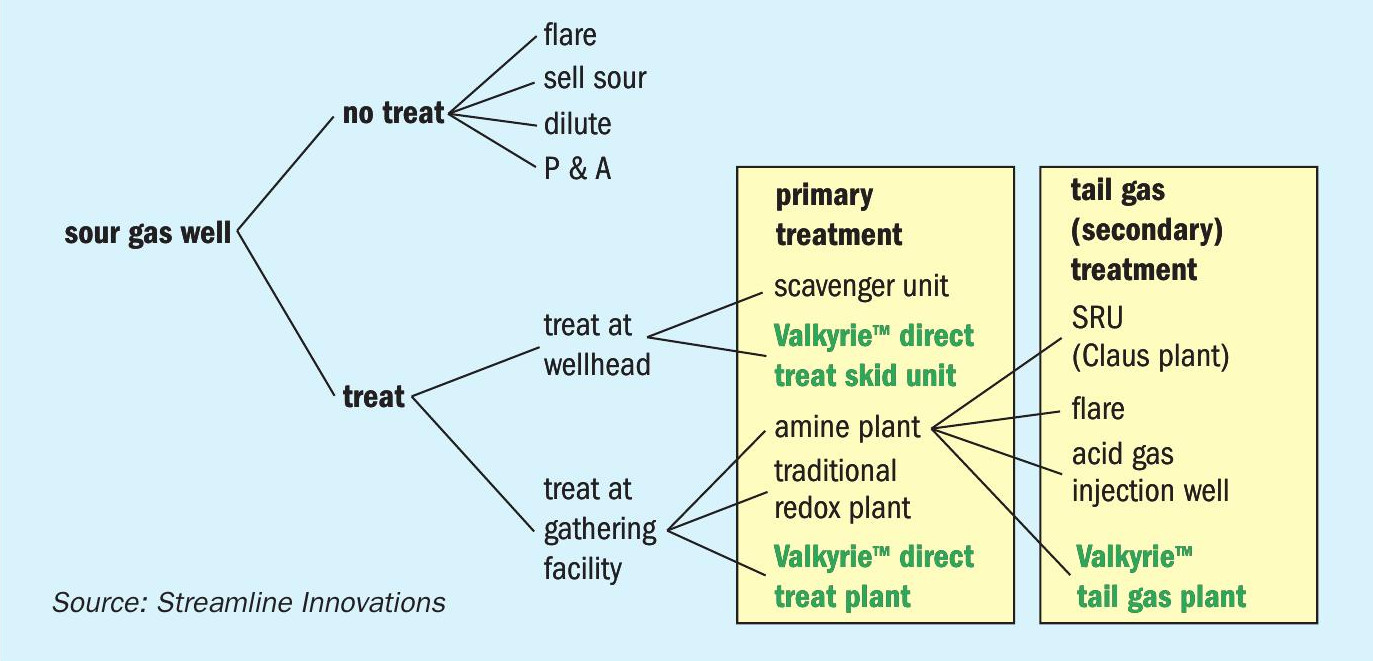
A summary of Valkyrie™ units that are in operation to date, as well as those under construction are given in Table 2.
The sulphur quality was analysed and found to be 99%+ purity, and can readily be used as an agricultural fertilizer. At 5-10 µm in diameter, the particles are ideally suited for integration into soil. The filter cake cleaning process removes nearly all the chemistry, and the cake retains about 15%-30% moisture, which can undergo further dehydration if necessary. The only other components found in the solid waste stream are trace amounts of hydrolysed surfactant, which ultimately biodegrades within days of disposal. The vent stream, i.e., that from the aerator, was also analysed and found to contain no H2S.
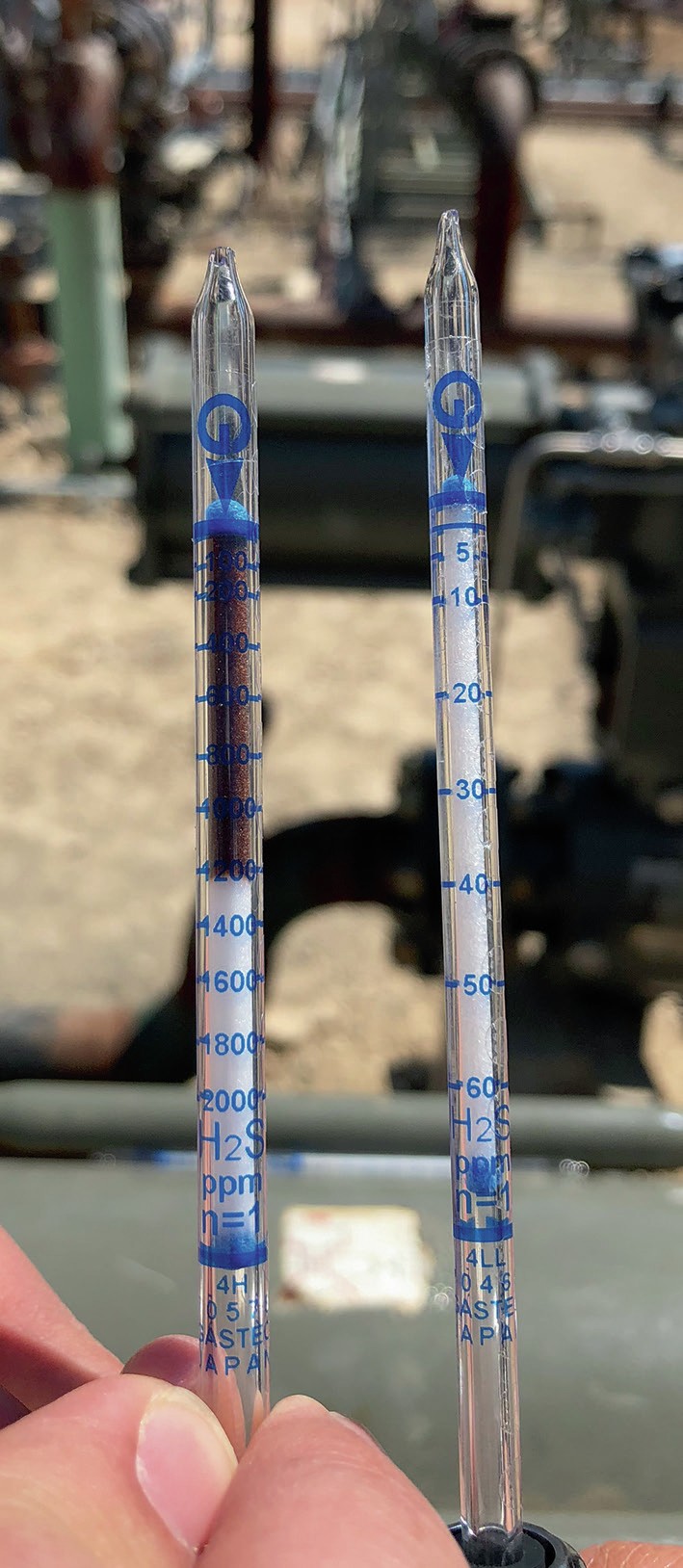
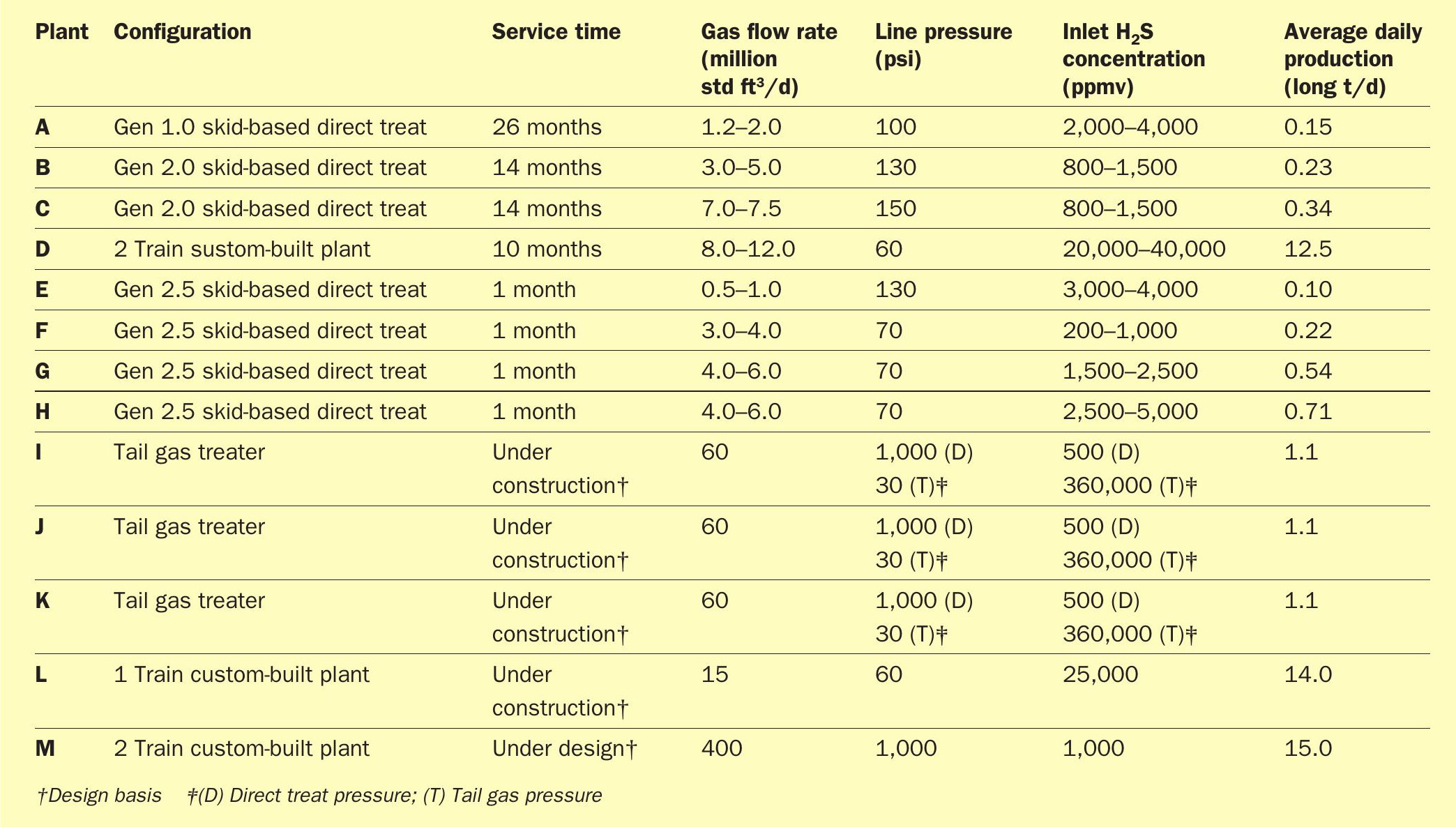
Case studies
Case 1 – Wellhead treating
An operator in South Texas was seeking to reduce lease operating expenses by replacing Triazine-based scavenger with an alternative technology. One site was selected as part of an early development program, and two subsequent sites were then chosen for commercial units after the successful pilot. The total gas flow rate for all three sites was 13 million std ft3 /day of gas containing an average of 1,300 ppm of H2S. The total sulphur production was approximately 1,400 lbs/day of sulphur (Fig. 10).
The result saw the average site treating costs reduced by 43%, including the amortised capital expenditure of the equipment. The units have operated continuously with 99% uptime since their commissioning in late 2018.
Case 2 – Large plant treating
A client in West Texas was seeking to treat H2S at its gathering facility which was initially determined to be 25 million std ft3 /day and contain approximately 1.6% (16,000 ppm) H2S, for a total of approximately 15 long t/d of sulphur. The plant was designed, built, and commissioned in a period of 29 weeks. Upon start-up, the H2S level increased significantly reaching values of over 40,000 ppm, and levelling down to approximately 20,000-25,000 ppm. The unit was able to treat this higher concentration to zero ppmv H2S outlet, and once the client was able to reduce the gas flow rate to 12-15 million std ft3 /day, the unit has treated the gas sustainably for over ten months.
An expansion (debottlenecking) of the unit is currently underway to extend the capacity of the existing units to 40,000 lb/day or 17.8 long t/d. In addition, a third train is being constructed (Fig. 11) increasing the total treating capacity to 40 million std ft3 /day and 71,360 lb/day or 31.8 long t/d of sulphur. This expansion has allowed a 150% expansion of the gathering field within a very short time, unlocked an additional 3000 barrels of oil per month based on treatment capacity of the associated gas; all at a savings of $2million per month compared to triazine.
As existing wells are aging and new sweet fields become scarce, H2S will become a greater concern for operators, and there will be a greater need in the future to find effective solutions. The liquid redox process to remove H2S from natural gas itself is not new, but prior attempts at commercialisation have been limited by operational and control issues. With current technology this article presents a workable economic solution that is able to remove H2S in an effective, low-cost, and green way. These self-contained automated units operate at both large and small scales, providing operators with a flexible and scalable solution that can be rapidly delivered to the field.
References