Sulphur 387 Mar-Apr 2020
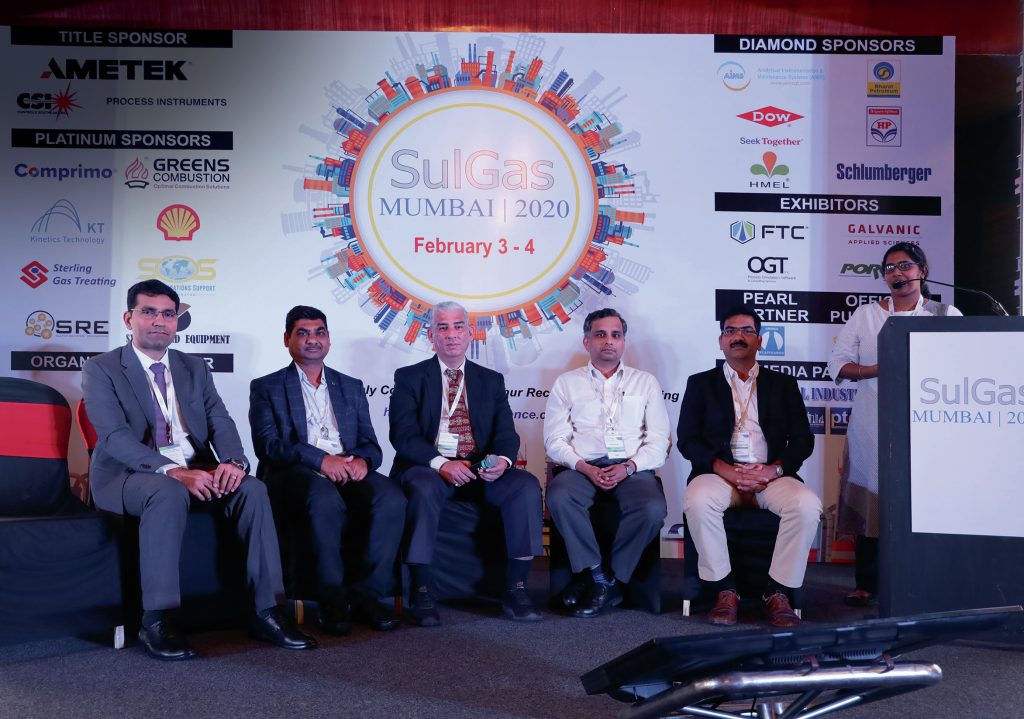
31 March 2020
SulGas 2020
CONFERENCE REPORT
SulGas 2020
Now in its second year, SulGas 2020, South Asia’s only conference on gas treating and sulphur recovery, took place 3-4 February 2020 at the Novotel – Juhu Beach, in Juhu, Mumbai, India.
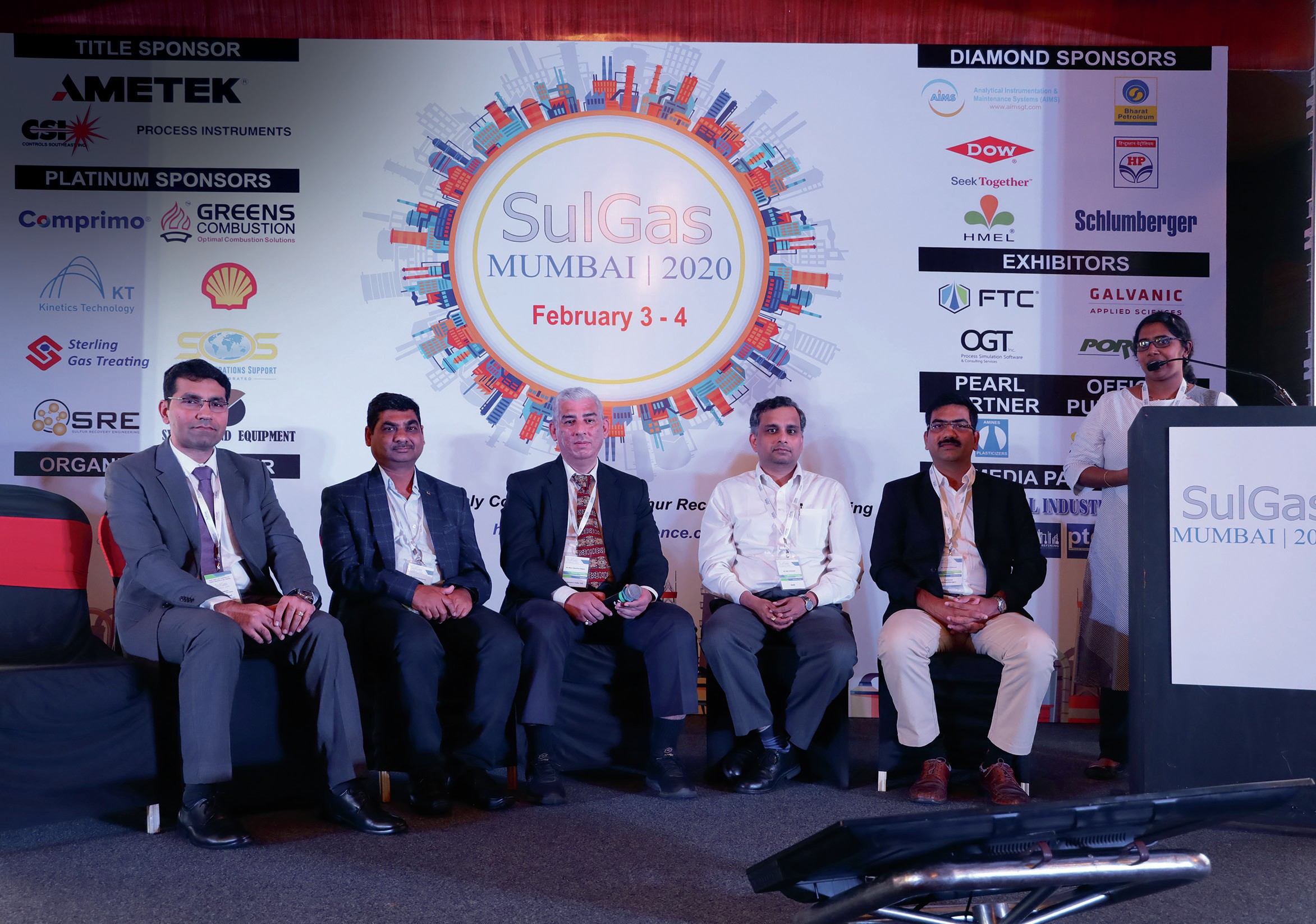
Building on the success of the first SulGas conference in 2019, this year SulGas attracted 170 delegates from 68 companies – 46 Indian companies, including 11 operating companies, and 22 international companies.
With IMO 2020 and BS-VI standards set to be in place in 2020, SulGas provides a technical forum for the sulphur and gas treating industry in the Indian subcontinent to convene and focus on understanding the problems and challenges facing the industry and to find solutions. With the processing of higher sulphur crudes and the changeover from BS-IV to BS-VI standards across all refineries in India, and the similar tightening of standards in the rest of the Southeast Asia region, the region is looking for the best way to remove, store and sell more sulphur.
The speakers at this two day event, which is organised by Three Ten Initiatives Technologies LLP, came from a variety of operating, licensing, engineering, and technology companies. SulGas focuses on issues unique to the region in the areas of:
- Equipment and process design;
- Process optimisation;
- Near misses;
- Analytical methods;
- Failures and successes of troubleshooting efforts;
- Plant operations.
The conference started off with an Experts’ Forum. Nate Hatcher of Optimized Gas Treating and Manu Miglani of Engineers India Limited provided design guidelines for heat stable salts (HSS) levels in amine systems. They discussed work undertaken to clear up a number of misconceptions that have been widespread for many years concerning HSS. Most of these misconceptions result from differing definitions, poor understanding of chemistry and the misuse of jargon. The effects of HSS on treating performance, operations and corrosion were reviewed with several quantitative case studies and corrosion measurements. With this understanding, previous design guidelines can be better understood and placed in context to their areas of applicability. For a given application, there will be a ”sweet spot” in the treating, which can only be revealed through process modelling with a truly fundamental rate-based model that uses the correct chemistry.
The next presentation in this session was by Ritesh Gulabani of Dow Chemical International (P) Ltd who discussed key points for the design and operation of low-pressure amine plants, e.g. tail gas treating units (TGTU) for sulphur recovery units, acid gas enrichment (AGE) for sulphur plant feed quality improvement and CO2 capture (CCU) from exhaust gases. Specific treating objectives, commonly employed solvents, feed gas composition, absorber operating pressure and limiting factors, typical treated gas specifications and solvent regeneration requirements for TGTU, AGE and CCU plants were discussed.
Technical programme
The technical agenda included sessions on:
- SRU optimisation and control;
- Systems and simulation;
- Gas and liquid treating applications;
- Case studies – learnings and experiences shared;
- SRU reliability enhancements;
- Innovation in design and equipment;
- Separation technology.
In addition, a round table session was held on day 2 with a panel of senior experts from the SulGas advisory committee responding to questions arising throughout the conference and discussing design, operating, and other practical issues of concern in the Indian context.