Fertilizer International 498 Sept-Oct 2020
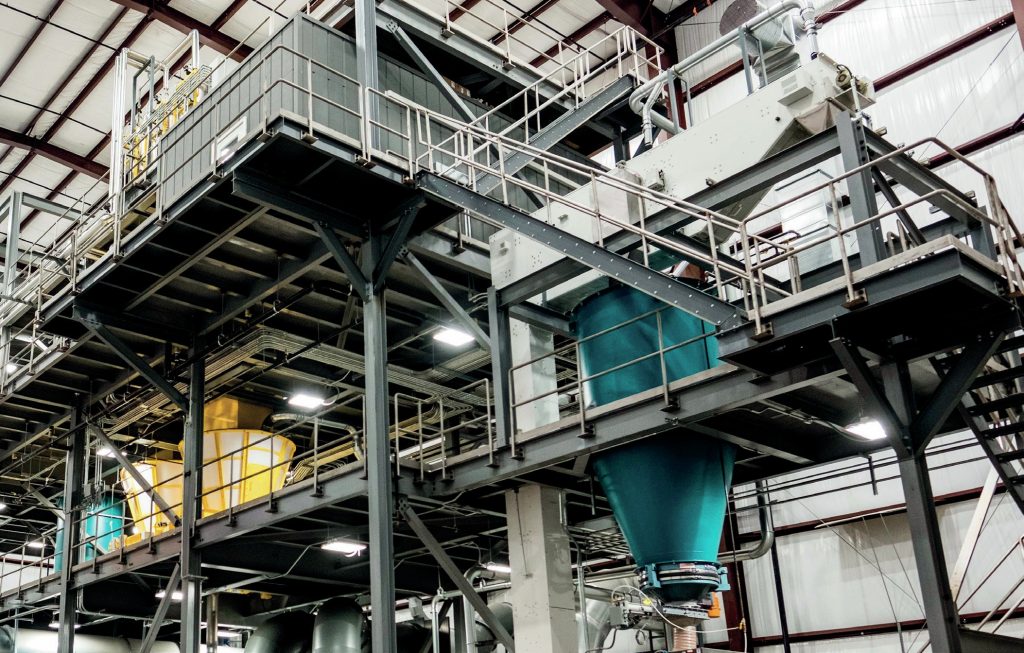
30 September 2020
Efficient fertilizers: helping profits and the planet
ENHANCED EFFICIENCY FERTILIZER
Efficient fertilizers: helping profits and the planet
Enhanced efficiency fertilizers (EEFs) occupy a small but high-value segment of the overall fertilizer market, although their production and use is accelerating. This trend is unsurprising given that their higher costs are usually more than offset by better efficiency and lower application rates.
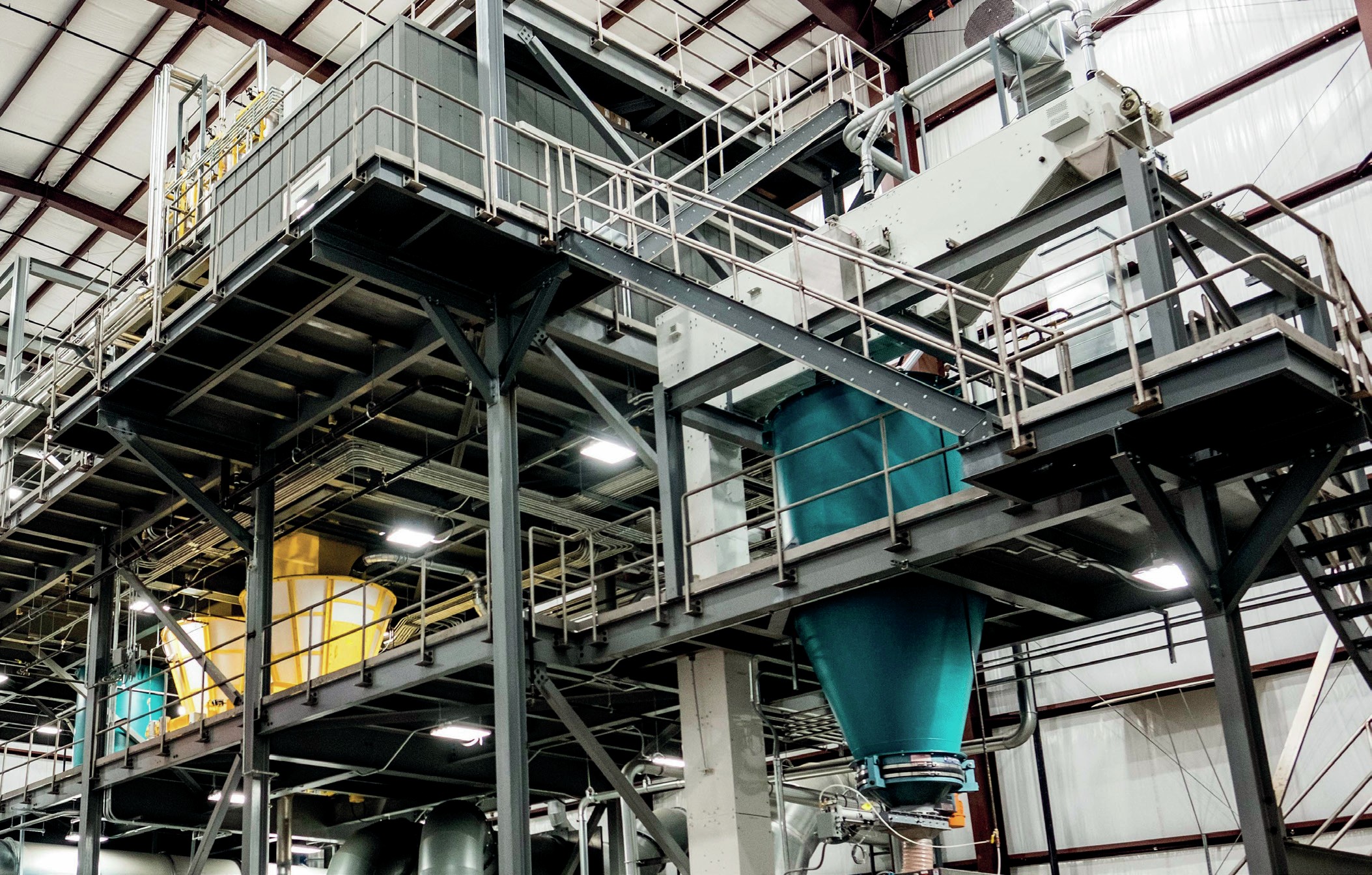
Enhanced efficiency fertilizers (EEFs) are a niche but fast-growing and high-value group of plant nutrient products. They include slow- and controlled-release and stabilised fertilizers – hence the label SCRSFs, the other widely-used term for these products.
The Association of American Plant Food Control Officials (AAFPCO) defines EEFs as: “Fertilizer products with characteristics that allow increased plant nutrient availability and reduce potential of nutrient losses to the environment when compared to an appropriate reference product.”
Previously, their relatively high cost/ benefit ratio has largely restricted the use of EEFs to turf and ornamental applications, horticulture and high-value cash crops. This is now beginning to change. EEFs are increasingly being applied to broad acre crops, as higher market volumes bring down production costs and understanding of their benefits becomes more widely understood (Fertilizer International 480, p30).
Overall, the main drivers of growth for EEFs are the desire to increase crop yields, nutrient use efficiency (NUE) and farm profitability, alongside environmental concerns. New environmental protection legislation, regulations designed to combat climate change, as well as 4R nutrient stewardship programmes, are also supporting market growth.
The main types of EEFs, their mode of action and relative costs are summarised in Table 1. Production and consumption of these products is accelerating. This trend is unsurprising given that their higher costs can be offset by better use efficiency and lower application rates.
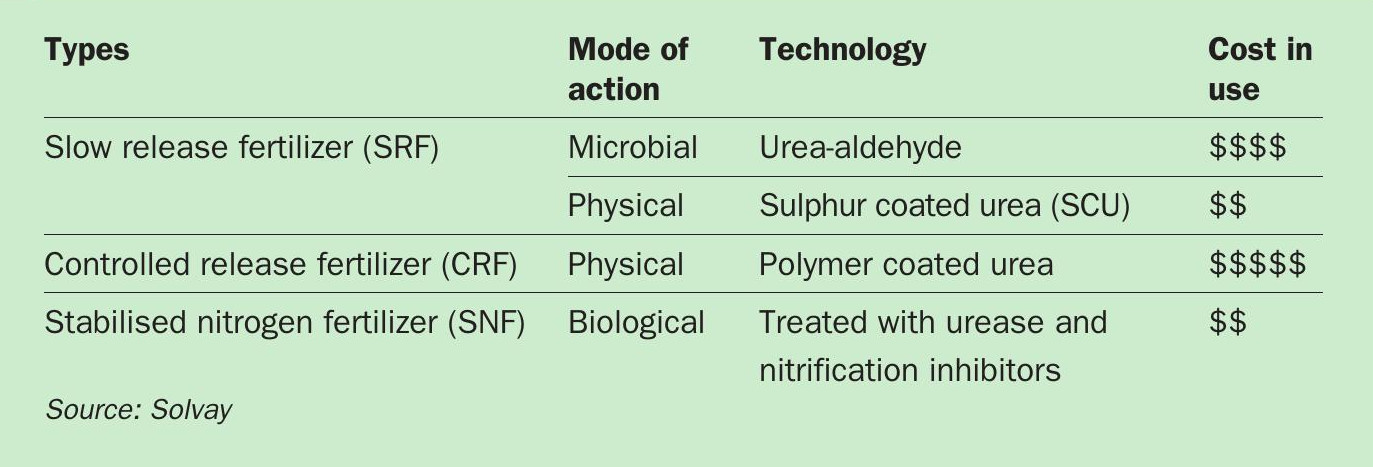

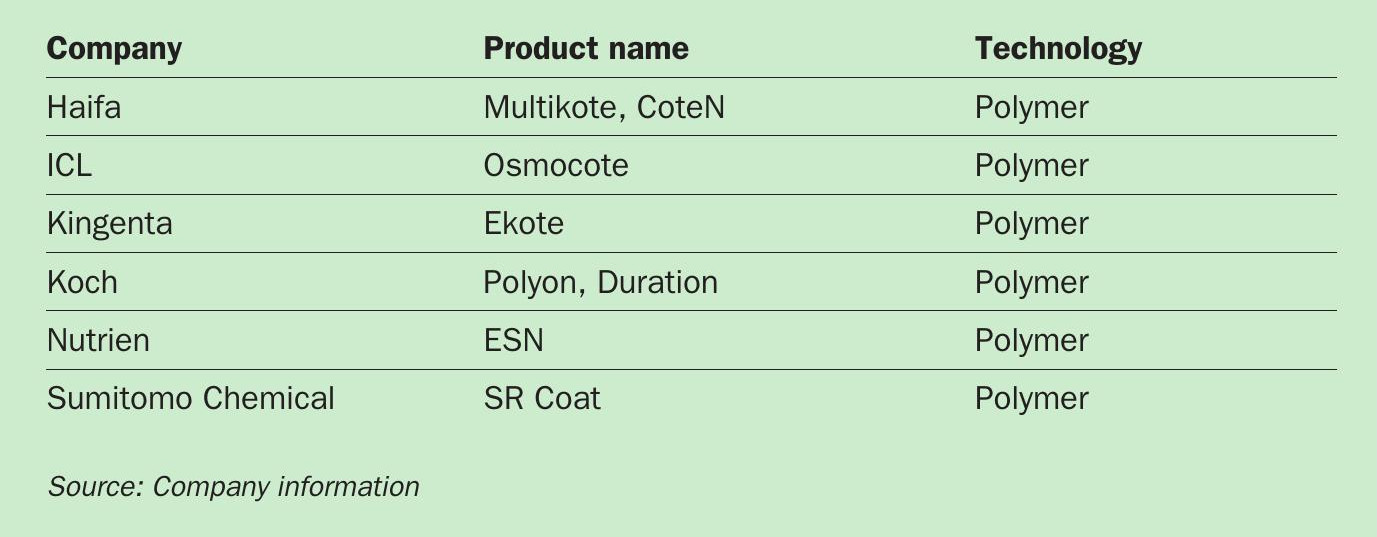
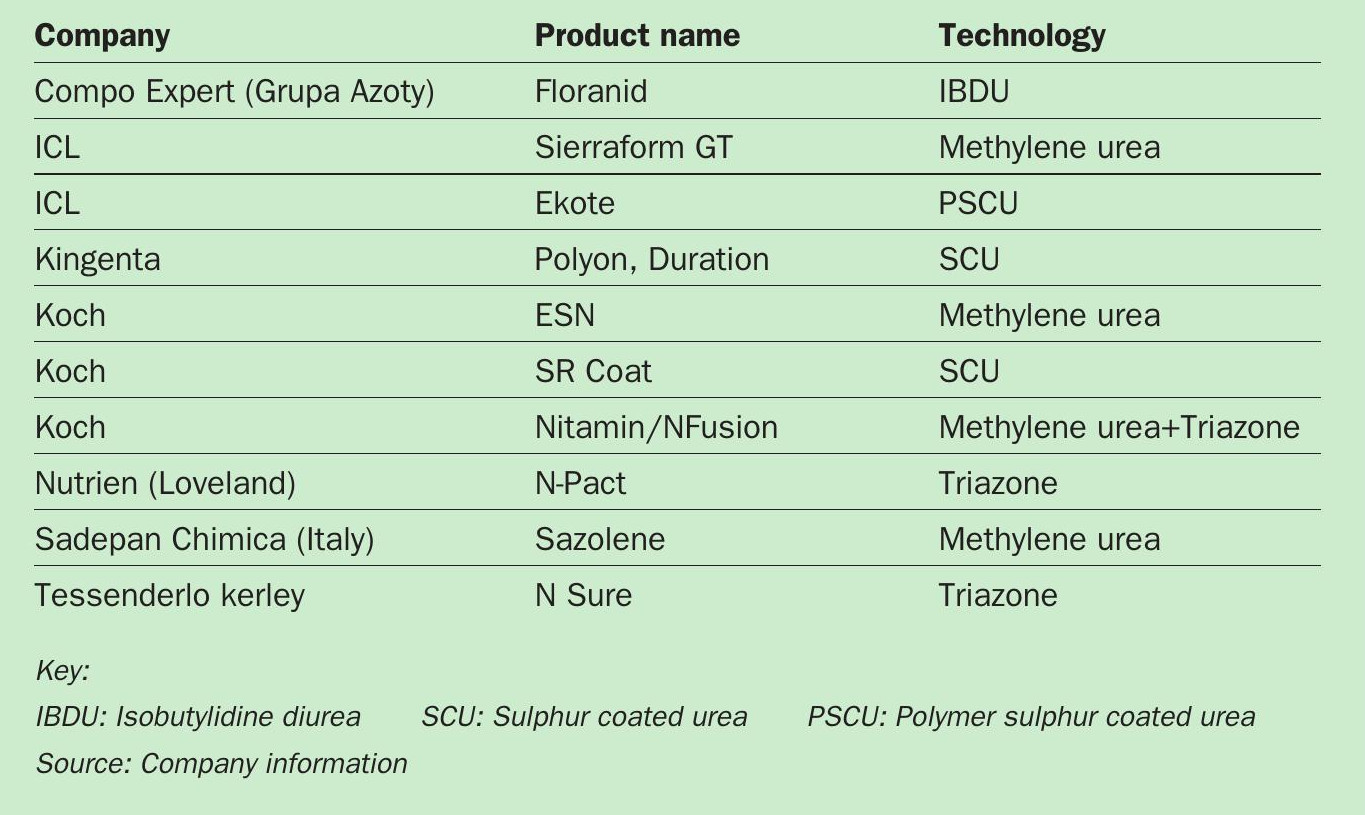
Market value, volume and growth
Enhanced efficiency fertilizers are used as value-added substitutes for standard commodity fertilizers such as urea, anhydrous ammonia and urea ammonium nitrate (UAN). While stabilised nitrogen fertilizers (SNFs) have developed a strong foothold in broad acre agriculture, the use of controlled-release fertilizers (CRFs) and slow-release fertilizers (SRFs) on broad acre crops generally requires evidence that their cost premium is justified.
An increasingly wide range of enhanced efficiency products are becoming available on the global market. A selection of leading SNF, CRF and SRF products and their producers are listed in Tables 2, 3 and 4, respectively.
For enhanced efficiency products, the value proposition – and environmental benefits – can be delivered in two ways:
- Substitution of an untreated nitrogen fertilizer with an enhanced efficiency product at the same standard application rate to deliver a yield improvement (typically 5-15 percent); or
- Substitution of an untreated nitrogen fertilizer with an enhanced efficiency product at a lower application rate to obtain the same or better yield.
On the regulatory front, SNF market growth has been strongly supported by:
- China’s zero fertilizer growth policy
- Biofuels regulation in Brazil
- Regulations in Germany making treatment of nitrogen fertilizers with inhibitors mandatory, or requiring their incorporation into the ground.
Complex and lengthy fertilizer registration processes, on the other hand, can hinder the adoption and sale of SNFs. The introduction of a new EU regulation on polymer biodegradability is also likely to limit European CRF demand in the medium-term. Several CRF producers are, however, fast-tracking the development of lower-cost biodegradable coatings to comply with the regulation.
The value of the global EEF market was estimated at $4.7 billion in 2018, and looks set to grow at nine percent p.a. to exceed $10 billion by 2028. The consumption of EEFs reached 15.7 million tonnes in 2018, up from 14.4 million tonnes in 2016 (Fertilizer International 492, p34). Market growth was mainly due to the rising popularity of SNFs, particularly urea stabilised with urease inhibitors (Figure 1).
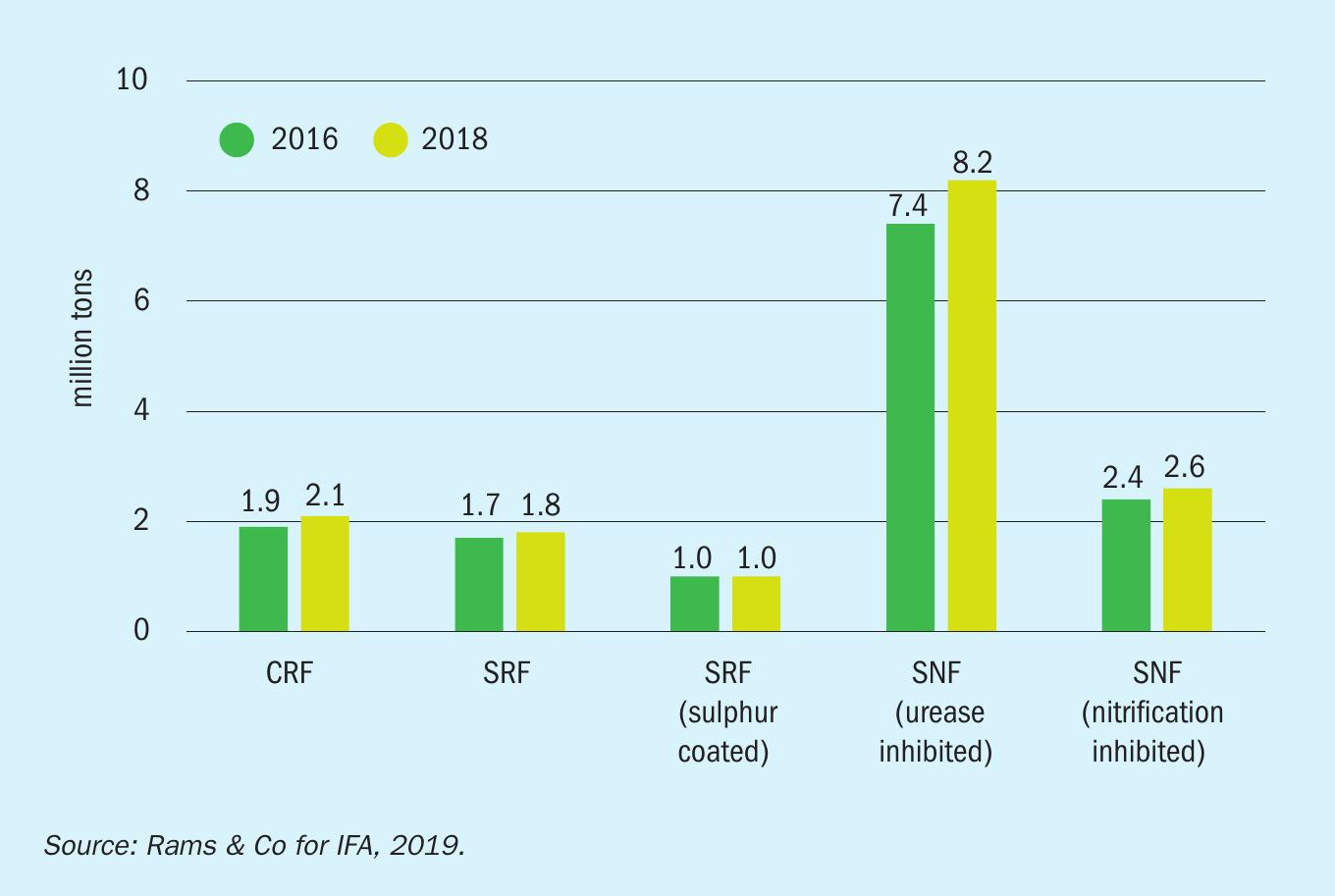
SNFs occupy a dominant position in the SCRSF market with a market share of more than 50 percent. The nitrification inhibitor market is mainly in the US where consumption is highest in the anhydrous ammonia segment.
SCRF segment
China, the United States, Western Europe and Japan are the leading global markets for slow- and controlled-release fertilizers (SCRFs). World demand is expected to grow a rate of nearly six percent p.a. during the period 2017 to 2022, according to IHS Markit (Fertilizer International 486, p25).
China’s increasing consumption of SCRFs has been particularly significant in recent years, and is projected to grow at nearly 10 percent p.a. between 2017 and 2022. An analysis by IHS Markit suggests that China currently consumes 700,000 tonnes of these products annually, nearly 46 percent of the world market, while the US consumes 560,000, close to 37 percent of the global total (Fertilizer International 486, p25).
Western Europe is the next largest SCRF market, at more than 10 percent of global demand, followed by Japan at roughly eight percent of global demand. China is also the world’s leading SCRF producer, having aggressively expanded its production during the past five years, to reach nearly 3.7 million tonnes annually (Fertilizer International 486, p25).
Production overview
Demand for EEFs is accelerating rapidly globally, albeit from a relatively low starting position. Production is fairly concentrated, both geographically and commercially. Four companies, Koch and Agrium in North America and Kingenta and Hanfeng Evergreen in China, have led the way in terms of production scale and output. Other large global players include ICL and Haifa Group in Israel, COMPO Expert in Germany, and SQM Vitas, the latter a joint venture between France’s Roullier Group and SQM of Chile (Fertilizer International 480, p30).
Large global chemical manufacturers have also been instrumental in the development of innovative nitrogen stabilisation agents. These include Belgium’s Solvay, BASF and SKW Piesterlitz in Germany, Japan’s Chisso-asahi and Dow Agrosciences in the US.
Leading global urease inhibitor brands, such as Koch’s Agrotain, Solvay’s Agrho N-Protect and BASF’s Limus products are based on the stabilisation agent NBPT (N-(N-butyl)thiophosphoric triamide) – although Limus also contains another urease inhibitor, NPPT (N-(2-nitrophenyl) phosphoric triamide). Solvay’s N-Protect and Koch’s SuperU are innovative in that they both incorporate a nitrification inhibitor (DCD) and urease inhibitor together in a single stabilised fertilizer product (Fertilizer International 480, p30).
Solvay
Solvay has developed the eco-friendly AgRho® N Protect™ range of nitrogen stabilisers. These incorporate both urease (NBPT) and nitrification inhibitors (DCD). The AgRho® N Protect™ range benefits from Solvay’s expertise in green solvent technology and agrochemical formulations, delivering active ingredients at a load capacity of up to 50 percent in a non-toxic solvent formulation (Nitrogen+Syngas 362, p36).
Solvay has shown that the use of formulations containing a nitrification inhibitor such as DCD can reduce nitrate leaching by more than 60 percent. The use of urease inhibitor such as NBPT, meanwhile, is one of the most effective management tools for preventing ammonia loss from surface applications of urea or UAN. Reductions in ammonia volatilisation of more than 80 percent have been observed with the use of NBPT.
Excess nitrogen fertilizer application is responsible for unnecessary nitrogen losses to the environment. Through the use of nitrogen stabilisation formulation, such as AgRho® N Protect™ , Solvay has also shown that N2 O emissions can be reduced by 50 percent, when compared to untreated fertilizer.
Furthermore, based on extensive field trials in different regions, AgRho® N Protect™ can deliver crop yield increases of up to 20 percent – or nitrogen fertilizer savings of up to 20 percent.
AgRho® N Protect™ works particularly well in no-till systems. This is because, normally, if urea is left on the surface then much of the applied nitrogen will be lost as ammonia into the atmosphere due to high enzyme activity. AgRho® N Protect™ stops this enzyme activity for up to two weeks. Additionally, treatment of urea with AgRho® N Protect™ improves options for fertilizer timings and the number of split applications required, potentially helping growers to save on costs and labour.
The risk of nitrogen losses through ammonia volatilisation or nitrate leaching depends on a variety of different parameters, including:
- Environmental factors such as weather and soil conditions
- The types of fertilizer(s) used
- The nitrogen programme, particularly the number of split applications.
One size does not fit all, in Solvay’s view. The company therefore recommends the selection of a tailored nitrogen stabiliser formulation that matches the grower’s specific environmental factors and nitrogen fertilization programme. To help find the right nitrogen stabiliser, Solvay has developed a web-based tool (nprotectsolvay.com). This allows the grower to select the nitrogen stabiliser formulation that best fits their needs.
Koch Agronomic Services: pioneer and innovator
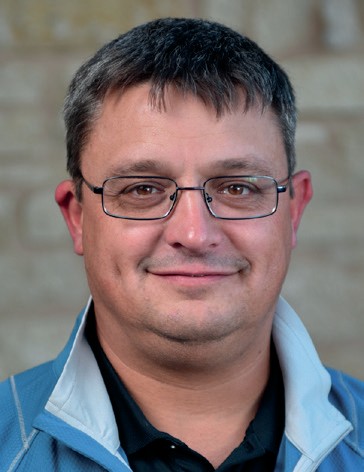
Stabilised fertilizers (SFs) are the largest segment of the speciality product market globally, according to a recent analysis by Rams & Co for the International Fertilizer Association (IFA). Indeed, urease inhibitor (UI) and nitrification inhibitor (NI) products combined now represent a 10.8 million tonne market globally. SFs are mostly applied in broad acre agriculture. North America, in particular, has been a pathfinder region for stabilised fertilizers and innovation in the development of urease and nitrification inhibitors.
We talk to Greg Schwab, Vice President, Technology and Innovation at Koch Agronomic Services (Koch), pictured left, about the current state of the market. Koch has been a pioneer in the SF market and continues to innovate.
The nitrogen stabiliser AGROTAIN® is the original and most proven urease inhibitor product on the market, being backed up by more than 25 years of trial results and the successful application on millions of acres of crops worldwide. Koch subsequently introduced ANVOL® nitrogen stabilizer in January 2019. This new product combines NBPT, the urease inhibitor found in AGROTAIN® , with Duromide to deliver longest-lasting protection against ammonia volatilisation.
Koch also launched CENTURO® nitrogen stabilizer in 2018, its next-generation nitrification inhibitor for use with anhydrous ammonia and urea ammonium nitrate (UAN). Featuring Pronitridine, CENTURO® is the first new nitrification inhibitor to receive US Environmental Protection Agency (EPA) registration in more than 40 years.
Additionally, Koch manufactures SUPERU® fertilizer, a stabilised granular urea product that contains urease and nitrification inhibitors to guard crops from denitrification, leaching and volatilisation.
What particular conditions and factors have driven the successful uptake of stabilised fertilizers in North America?
The initial adoption of urease inhibitors revolved around the desire to prevent soil erosion with reduced and no-till cropping systems. Urease inhibitors eliminated the need to incorporate the fertilizer into the soil to prevent ammonia volatilization loss. They increased in popularity as farmers began shifting to more in-season nitrogen applications to further improve fertilizer use efficiency and limit environmental impact.
While in-season nitrogen applications are very efficient, the continued growth in US farm size can make it challenging to apply all of the nitrogen fertilizer after crop emergence. Nitrification inhibitors can stabilize pre-season ammonia and urea nitrogen applications and minimize losses from leaching and denitrification.
In fact, our research has shown nitrification inhibitors like CEN-TURO ® are equally efficient, comparing pre-season applications with a nitrification inhibitor and in-season applications without. With in-season nitrogen applications, nitrification inhibitors also play a role in protecting the nitrogen from spring rains which can allow the grower greater flexibility for when and how they apply their nitrogen.
Has Koch been pleased with the take-up of ANVOL® since its launch, with customers switching over from AGROTAIN®?
AGROTAIN® is one of the few agricultural products that has been in use for more than 25 years – which is a testament to the value it brings to farmers. After discovering Duromide, we realised that its performance could surpass NBPT, the active ingredient in AGRO-TAIN® . Like any new product there is an adoption curve. However, some of our customers have already fully transitioned to ANVOL® and we are very pleased with the product’s progress in the market.
How much of a milestone and landmark moment has the launch of CENTURO® been – both for the company and the wider stabilised fertilizer market?
Developed in the US in 2010 by a team of chemists at Koch, our goal was to create a single nitrification inhibitor compatible with anhydrous ammonia and UAN. After listening to retailers and growers, we focused on designing a product that was first and foremost agronomically effective and secondarily, had improved operational benefits like being noncorrosive to the metals used in anhydrous ammonia and UAN equipment.
Over the course of the 10-year development process, we worked with several land grant universities to conduct in-field research on the impact CENTURO® could have – on improving nutrient use efficiency, optimising yield and minimising nitrogen losses to leaching. This strong body of university research, coupled with the operational efficiencies gained from the storage and handling characteristics, has created excitement in the industry for this product, and we look forward to its continued growth and adoption.
What are the main markets for SUPERU® and where is it currently manufactured and on what scale?
SUPERU® fertilizer is unique because it is the only ready-to-use incorporated urea product that protects from all three forms of loss – volatilisation, leaching and denitrification – without sacrificing nitrogen concentration [46 percent nitrogen].
Weather variability means that farmers are often uncertain which form of loss to expect. In drier years, ammonia volatilisation is the main concern, but in wetter years leaching and denitrification are the biggest problems. SUPERU® allows farmers a way to minimise loss, regardless, in one easy-to-apply product. SUPERU® is produced at our world-scale production facilities in Enid, Oklahoma in the US and at Brandon, Manitoba, Canada.
Koch is offering to license the process technology for SUPERU® fertilizer to third-party urea producers. Could this play an important part in the wider roll-out and adoption of SFs across the world?
As countries like Germany begin to require urease inhibitors for all surface-applied urea fertilizers, we believe adding inhibitors at the time of manufacturing is an efficient alternative for retailers to deliver stabilised nitrogen to the farmer. This process removes the need for local blending and allows the retailer to apply other products like micronutrients, biologicals, or crop protection products to the granule.
In fact, we’ve added the ability to make SUPERU® to all our North American urea production facilities. Globally, we are engaging with other manufacturers to license Koch’s proprietary N-TEGRATION™ technology that integrates the active ingredients evenly and homogenously into every granule.
Koch Agronomic Services
Koch Agronomic Services (Koch) helped pioneer the enhanced efficiency fertilizer (EEF) market and continues to innovate (see box). Working with leading universities and third-party researchers, the company has commissioned extensive and rigorous trials to demonstrate the efficacy of EEFs and their benefits for growers (Nitrogen+Syngas 362, p36).
Koch is well known for its market leading SUPERU® fertilizer and AGROTAIN® nitrogen stabiliser. Both are based on easy-to-implement technologies and are designed to work seamlessly in the urea manufacturing process.
Koch’s long-standing AGROTAIN® nitrogen stabiliser incorporates the urease inhibitor NBPT as an active ingredient. While its SUPERU® fertilizer incorporates two types of stabilisers, NBPT and DCD. These dual inhibitors protect fertilizer from all three forms of nitrogen loss – volatilisation, denitrification and leaching. This enables SUPERU® to deliver protection, productivity and efficiency in one homogenous urea granule, according to Koch.
A summary of the reductions in nitrogen losses delivered by AGROTAIN® and the maize and wheat yield benefits from using SUPERU® are shown in Figures 2, 3, 4 and 5.
EEFs can be produced at various points in the supply chain, including at the manufacturer, distributor and retailer level, or at the farm gate. Each of these options vary in cost and the value they offer to growers.
Koch’s N-TEGRATION® technology allows inhibitors to be incorporated during urea manufacturing. It offers nitrogen fertilizer producers a simple, cost effective, and reliable way of creating value for their end users, as well as capturing some of that value for themselves.
N-TEGRATION® technology is currently in use at Koch’s fertilizer production plants in Enid, Oklahoma, US, and Brandon, Manitoba, Canada, where it is used to produce SUPERU® fertilizer. The technology offers the following benefits:
- Minimal scope/impact: It can be bolted on to existing urea plants or incorporated in new ones
- Short installation schedule: It only takes around 10 months from the beginning of the design process to plant start up
- Operational flexibility: N-TEGRATION® technology can be easily switched on or off – allowing batch runs or continuous EEF production
- Minimal capex investment: Approximately $3-$12 million.
- Ability to capture higher margins: It delivers premium margins over commodity urea
- Differentiation = liquidity: The production of a differentiated product improves urea plant liquidity and/or net-backs in a long commodity urea market
- Sustainability: Differentiated products help operators meet growing regulations and achieve corporate sustainability goals.
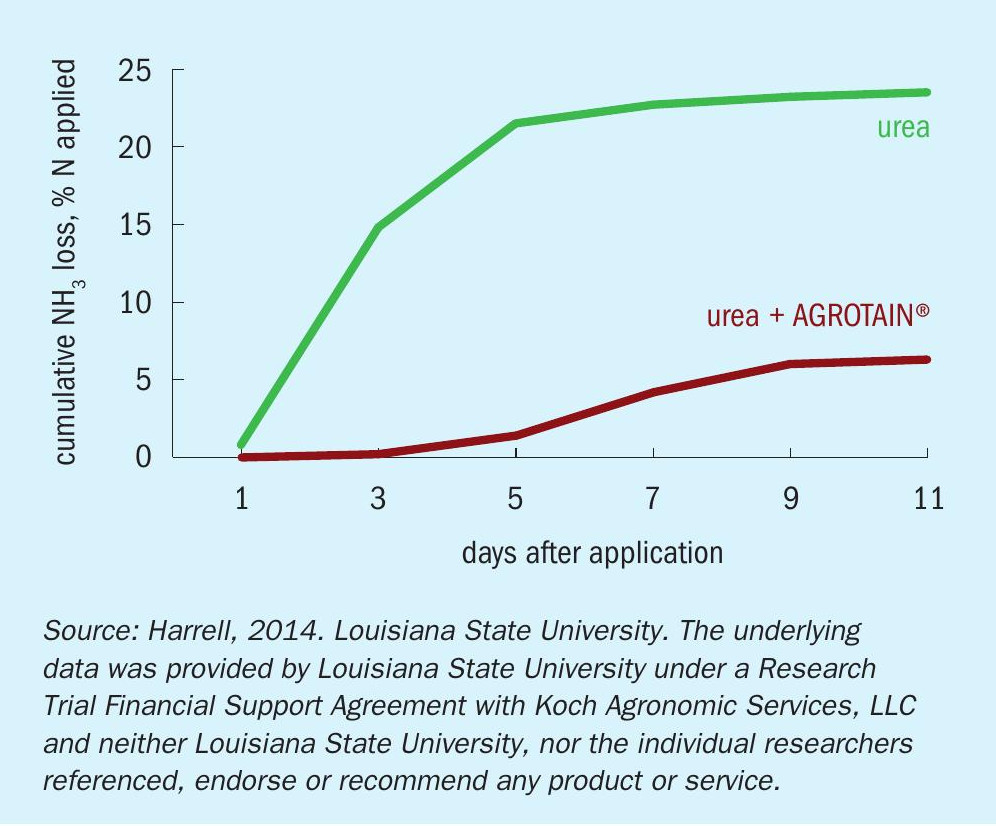
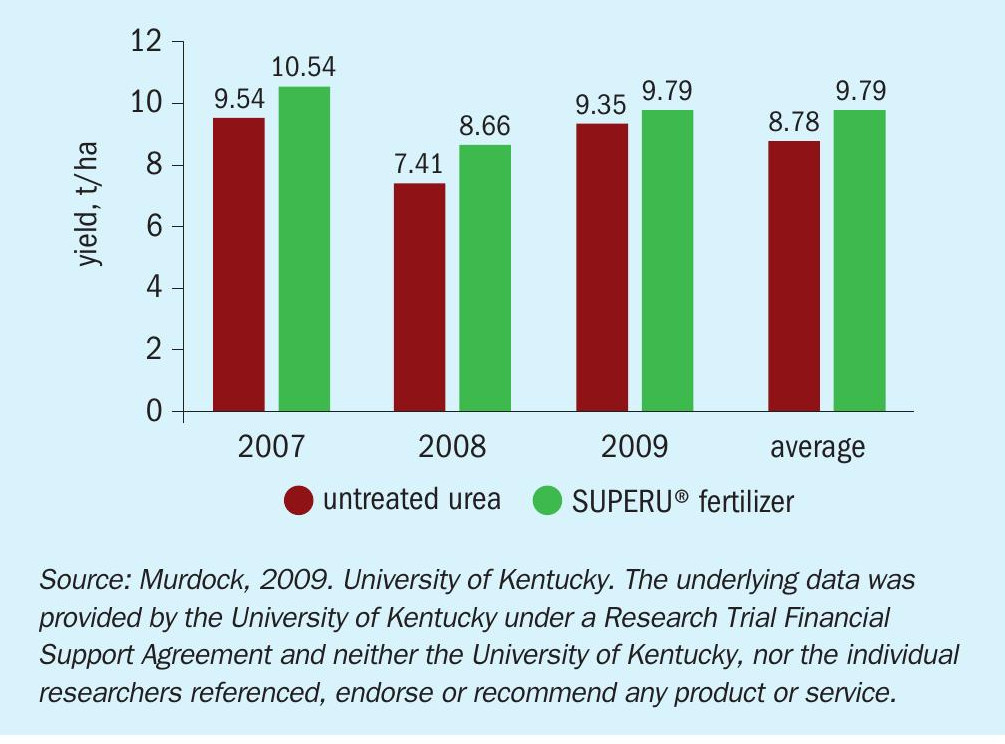
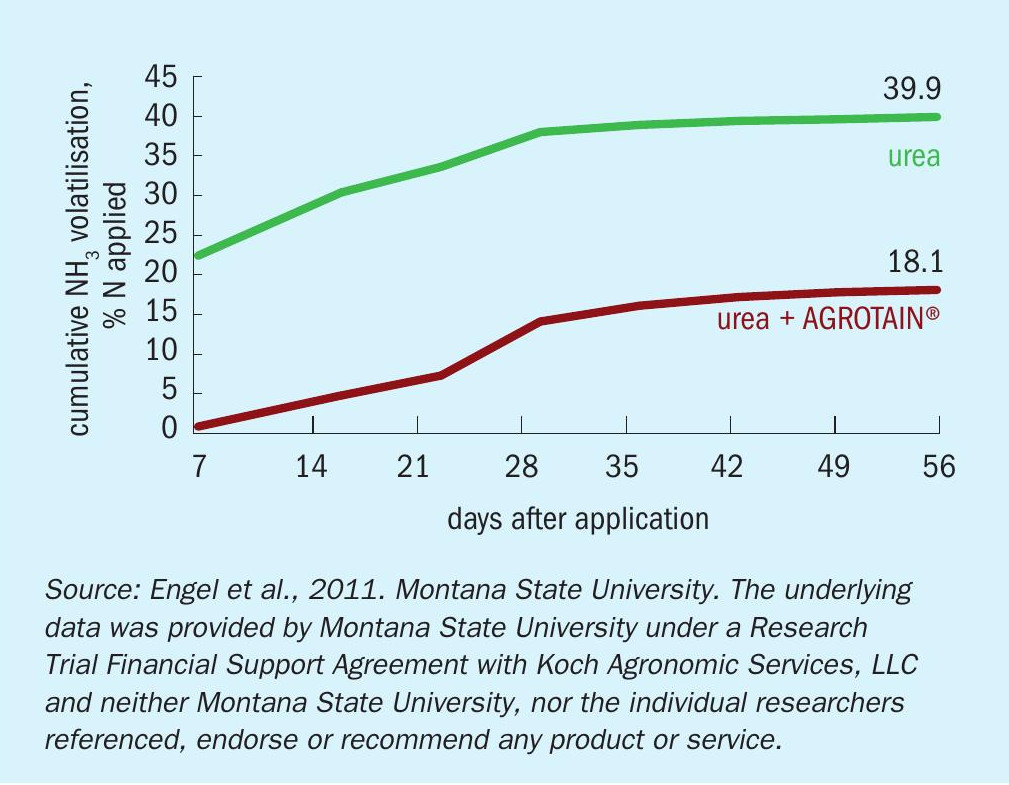
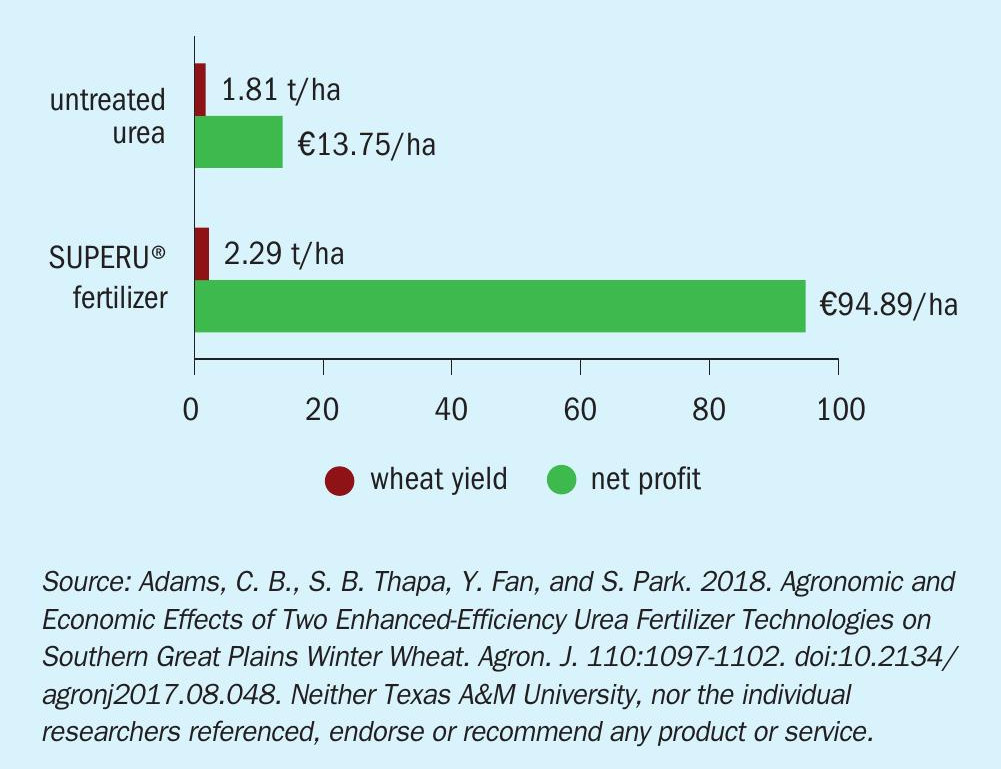
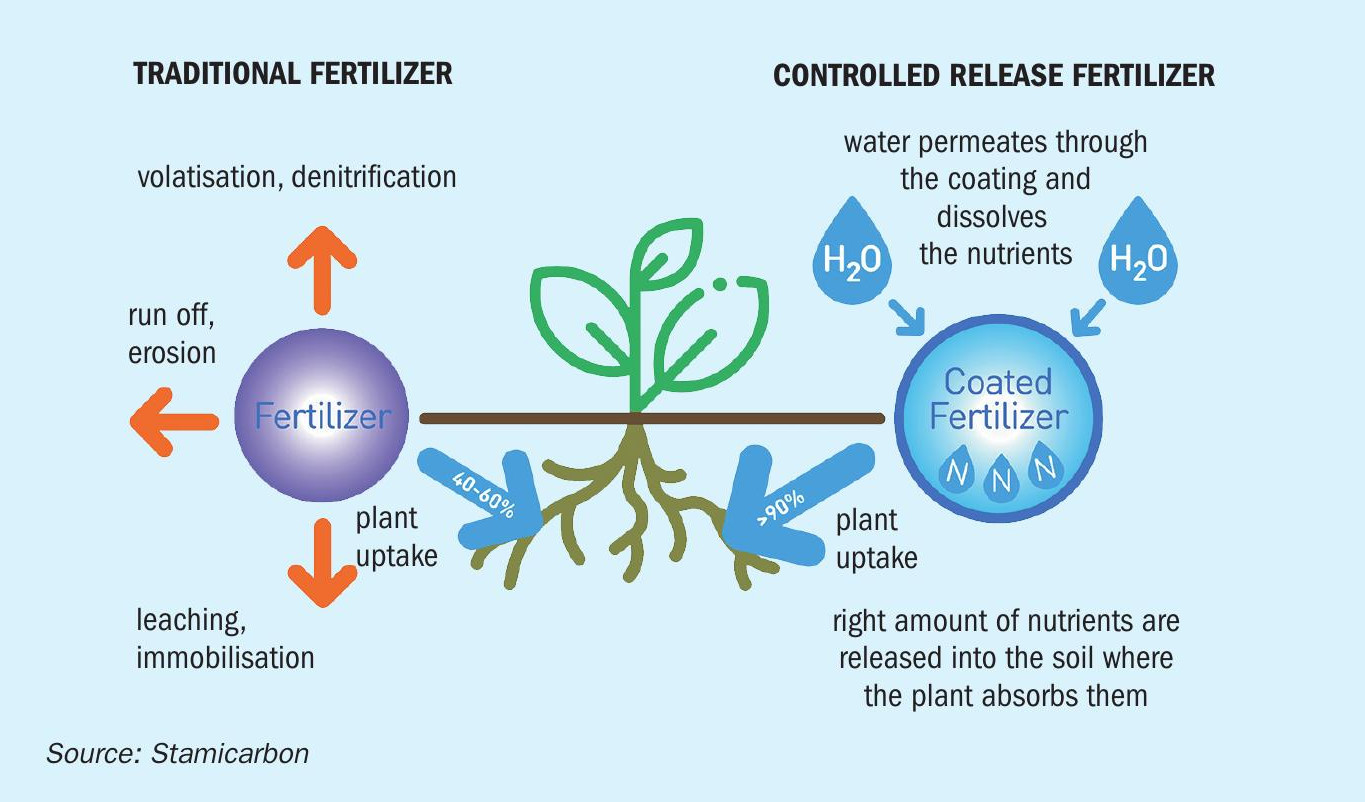
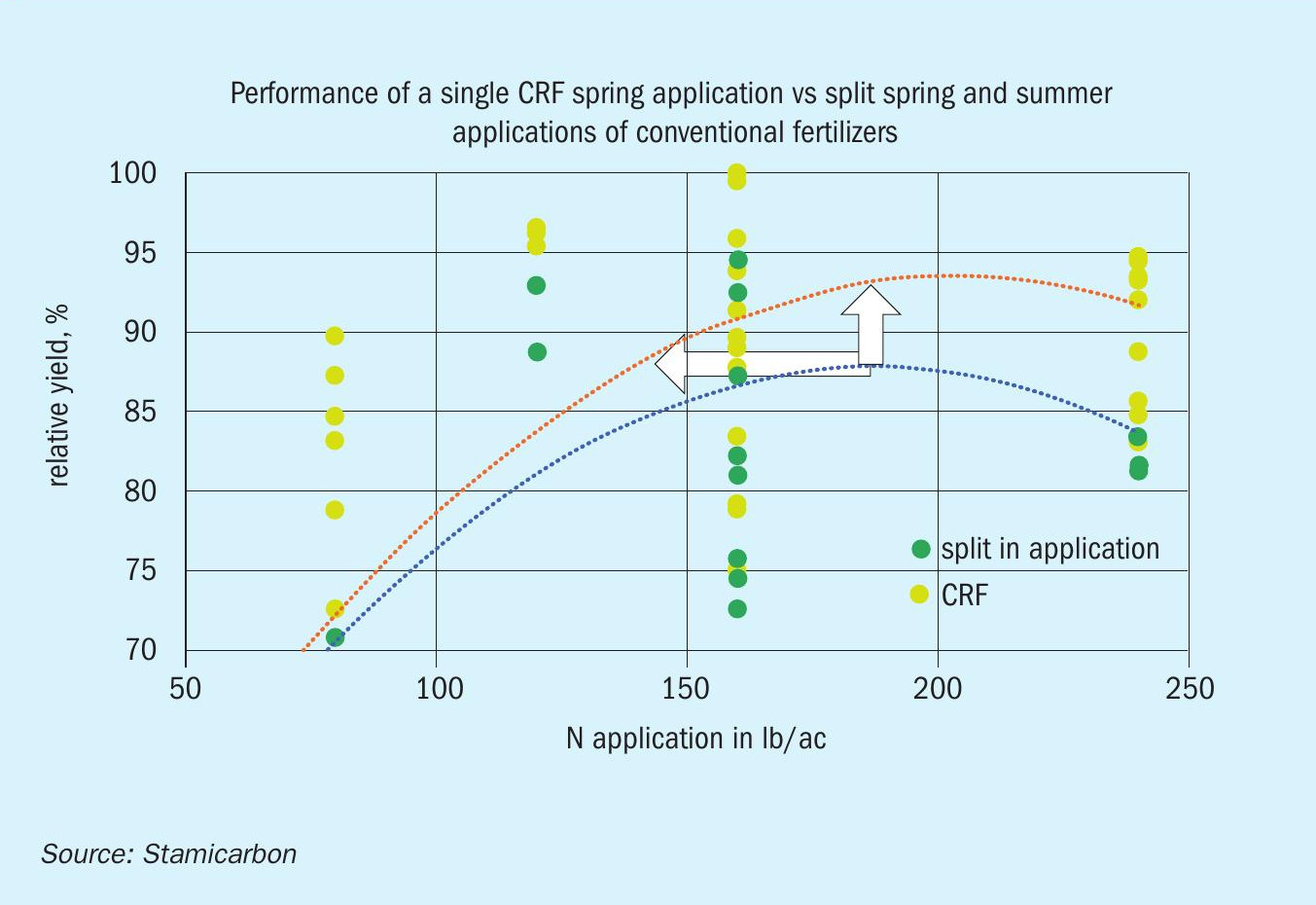
Koch continues to innovate. Because urea remains the largest nitrogen source used in agriculture, the company has sought to improve on NBPT, one of the most widely recognised and used urease inhibitors on the market. This resulted in the development of DUROMIDE™ , the patented active ingredient in Koch’s new ANVOL™ nitrogen stabiliser.
Koch made its ANVOL™ nitrogen stabiliser available to US growers in in 2019. This next-generation stabiliser, compared to other urease inhibitor technologies, provides longer-lasting protection against ammonia volatilisation. It does this by providing dual active ingredients – DUROMIDE™ and NBPT – in optimal amounts. DUROMIDE™ offers a number of distinct benefits:
- A patented chemical structure
- More stable over a wider range of soil environments
- Slows down urea hydrolysis in the soil over a longer window
- More effective than NBPT alone
- Buys more time for rainfall incorporation
- Reduces ammonia loss.
Stamicarbon/Pursell Agri-Tech
Stamicarbon in cooperation with Pursell Agri-Tech is offering a complete package for controlled-release fertilizer (CRF) production – one that is based on a novel coating technology exclusively developed for this purpose (Fertilizer International 492, p38). This production package, based on a batch coating process in a high intensity mixer, is able to encapsulate a wide variety of different fertilizer products with a new kind of polymer coating. This coats fertilizer granules within an extremely thin and durable membrane. The controlled release of nutrients can be adjusted over a time span of between one and 12 months, depending on the weight of the applied coating.
The novel polymer used in the production process is exclusively supplied by a major global polymer producer. The equipment manufacturer, also working in exclusive cooperation, is able to supply customers with complete production installations on a lump sum, turnkey basis.
The guarantees provided by these exclusive arrangements eliminate investment risks in new plant capacity, and provide a solid foundation for a major expansion in CRF production. This production package makes it possible for fertilizer producers, importers and distributors to access CRF production technology and manufacture products for their domestic customers. The production units are designed to be located close to the end-user (farmers) so as to avoid the unnecessary handling of the coated product.
The first CRF demonstration plant, operated by Pursell Agri-Tech in Sylacauga, Alabama (pictured), has been performing successfully since spring 2018. The plant is currently running 24 hours a day, in five days a week operation, providing just under 100,000 t/a of coated product capacity. The current coating line can coat nearly all fertilizer grades, including granular and prilled urea, DAP, MAP, NPK, etc.
CRFs – better farm economics
Typically, the high solubility of conventional fertilizers means that the nutrients provided dissolve quickly in the soil and are only available for the plant a short time after their application. Controlled-release fertilizers, in contrast, offer the timed release of nutrients, in-sync with the continuous crop demand for these, during the whole growing season (Figure 6).
Numerous field studies over the last decade have compared the performance of controlled-release fertilizers with conventional split-application fertilizers. The analysis shown in Figure 7 is based on US field trials with corn in 2017 and 2018. It compares a single spring application of a CRF to split applications with conventional fertilizers in spring and early summer. For each individual test site and test year, the highest yield obtained is recorded as 100 percent and used as a yardstick. All other results were then measured against this maximum reference point.
The results revealed that, in general, CRFs offer a steady yield improvement over conventional split applications. They also confirmed that CRFs improve nutrient use efficiency, delivering either higher yields, or lower application rates, due to a reduction in volatility and leaching losses.
Based on these field trial results, the following observations on cost have been made for a single CRF application versus split applications of conventional fertilizers, assuming $400/t for the urea price and $4/bushel for the corn price:
- At similar application rates: the 6-7% yield improvement achieved means CRFs are still cost competitive with conventional fertilizers even when sold at a premium of more than $200/t.
- At 25% lower application rates: the similar yield achieved by a lower amount of CRF allows for a price premium of $130/t.
The above calculations are conservative estimates as they do not include additional savings to the farmer such as the fuel saved from the single application of CRFs. In general, the business case for CRFs is always positive, providing a sound financial incentive for their increased adoption and use.
Stamicarbon and Pursell Agri-Tech have concluded that, for broad-acre agriculture in North America, targeting a $100/t price premium over urea for CRFs could provide significant financial incentives for farmers to switch from commodity to coated fertilizers.
ICL’s E-Max Release Technology
ICL Specialty Fertilizers is a long-standing and major player in the controlled-release fertilizer (CRF) market. The company’s Osmocote range – targeted at nursery stock, perennials, and pot & bedding plants – pioneered CRFs some 48 years ago.
CRFs are an important speciality product category for ICL, and the company expects their use to grow rapidly worldwide. Although originally targeted at the ornamental and turf market, as well as speciality crops, CRFs are increasingly being applied to a wide range of other crops, such as field vegetables, soft and hard fruit, maize, potatoes, rice and sugarcane, according to ICL.
In 2016, ICL responded to rising agriculture demand by starting CRF production at its Heerlen plant in the Netherlands using new E-Max Release Technology. The CRF products manufactured at Heerlen’s 25,000 t/a capacity production line are marketed under the brand names Agromaster© and Agrocote Max. ©
Production in the Netherlands added to existing production using the same technology at ICL’s Summerville plant in the United States. This has been producing CRF’s with E-Max Release Technology since 2014. ICL also has advanced plans for new CRF production lines in Asia and Latin America – key markets for these products.
E-Max Release Technology is a relatively new CRF technology that precisely releases nutrients, such as nitrogen, potassium and phosphorus, to exactly match crops needs, while limiting nutrient leaching. The technology was developed at ICL’s Netherlands-based R&D section over several years. It was specifically designed for use in agriculture and has been tested worldwide.
The basis of E-Max release Technology is a polymer coating that improves nutrient use efficiency. This semi-permeable coating regulates the supply of nutrients by releasing these over a predictable timescale. Release is influenced by both soil moisture and temperature. Nutrient release is faster at higher temperature, while at lower temperatures release is slower, mirroring the nutritional needs of the plant.
“We have developed a unique process and technology for adding a very thin coating to a fertilizer granule.
Leon Terlingen, ICL’s R&D director, explains more: “We have developed a unique process and technology for adding a very thin coating to a fertilizer granule. The new thin coating allows us to keep the nutrient level very high, while also assuring a very good release curve for the crops. A new production process enables us to produce the controlled release fertilizer in a faster way than with previous technologies. We have tested and developed this new technology in our laboratories on a special pilot installation over a number of years in order to exactly formulate and tailor the desired products to fit specific crop needs.”
CRFs have been shown to significantly increase nutrient use efficiency during agronomic trials – improving crop yields and quality as a result. Indeed, CRF products such as Agromaster© and Agrocote Max© can offer “tremendous benefits for growers”, according to ICL, as they allow the cultivation of higher yielding and better quality crops from fewer fertilizer applications.
“Our agronomists are able to design and offer the right Agromaster© NPK with the desired release pattern and longevity,” comments ICL. “We know, for example, that potatoes need nitrogen in a specific period of the growth cycle and we are able to design a product that has a nitrogen release that suits the potato crop and creates balanced NPK fertilization.”
Agromaster© and Agrocote Max© function particularly well on sandy and loamy soils, and/or in regions where there is substantial rainfall during the growing season. They can also deliver carbon savings. ICL calculates, for example, that for every 10,000 hectares of cultivated land, substituting urea [check] with Agromaster© reduces the CO2 footprint of fertilizer use by an amount equal to:
- Almost 1,500 circuits around the world in an average family car
- Planting 390,000 trees
- The annual CO2 emission of more 1,100 average EU citizens.
The key benefits of Agromaster© relative to standard urea include:
- Higher or equal crop yields – with less mineral fertilizer input – thanks to the continuous nutrient release pattern
- Fewer applications = lower costs
- Reduced leaching, volatilisation and denitrification.
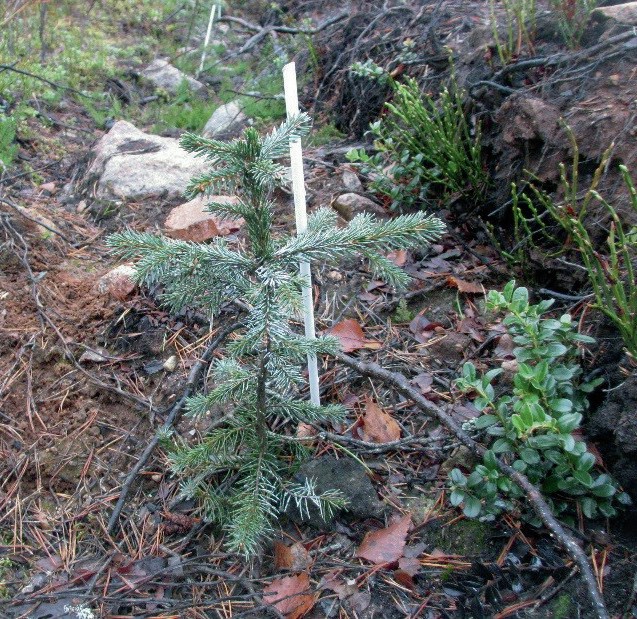
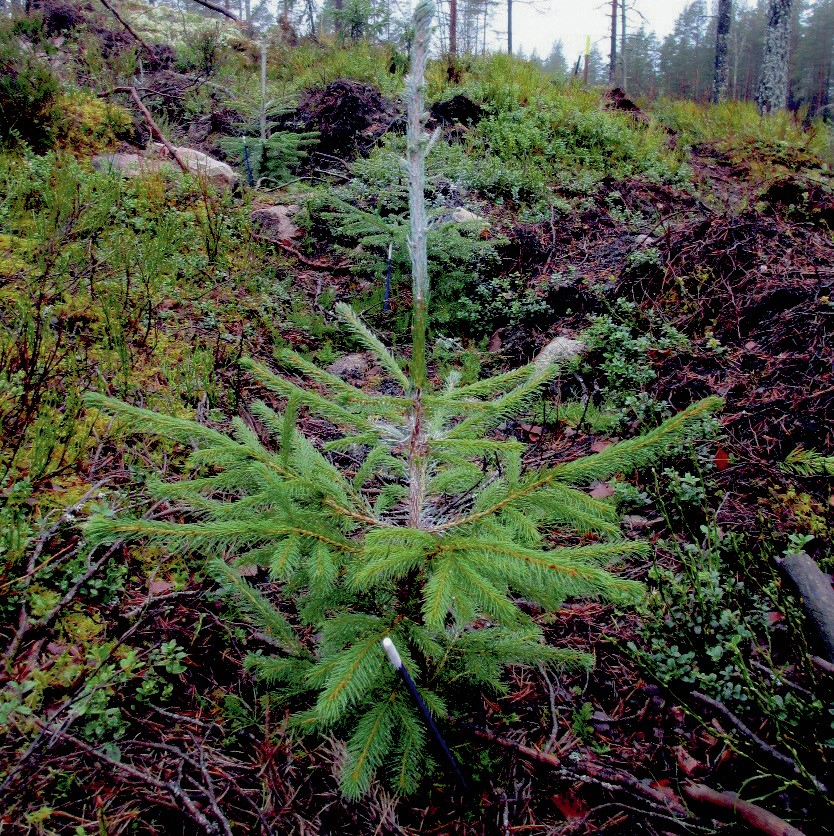
ICL trials have shown that Agromaster© outperformed commodity fertilizers and standard growing practices for rice and potato growing:
- Rice: Agromaster© can substantially improve yield and nutrient use efficiency in rice. Using this product as a controlled-release base fertilizer for nitrogen was found to significantly increase yields – at application rates that are similar to (and sometimes lower than) those used in conventional practice.
- Potatoes: on average, an eight percent yield increase could be obtained from Agromaster© versus standard grower practice.
Another of ICL’s controlled-release fertilizer products, Agroblen© , contains polymer coated NPK granules that release nutrients over a pre-determined length of time. These CRF products are used in open-field agriculture, in plant hole applications and in pots.
Agroblen© is a less labour intensive and environmentally-friendly product, compared to conventional compound NPKs, and delivers higher plant yields while reducing soil compaction. Trials have shown it to be an effective fertilizer for young fruit trees (years 1-3) when used in combination with Agromaster© :
- At planting: Agroblen© allowed a 50 percent reduction in nitrogen input and the number of applications, while improving total annual shoot growth and trunk diameter by six percent and 24 percent, respectively, in the first two years.
- Subsequent years: Compared to the control, Agromaster© provided the best results, in terms of the number of inflorescences and final yield, from a 20 percent reduction in nitrogen delivered in a single application.
Trial results published last year by ICL also demonstrated the benefits of Agroblen© for establishing newly-planted forestry seedlings, such as spruce and pine. The results of an Agroblen© trial by Sweden’s SLU university showed significant improvements in seedling growth during the first three years after planting, as measured by stem collar diameter, tree height and root volume (see photos). The trial used a 100 percent coated NPK+Mg+B compound Agroblen© fertilizer that gradually releases nutrients over 1.5-2 seasons.
InnoSolve 45N™ from Innovar Ag
InnoSolve 45N™ is the latest enhanced efficiency fertilizer from the specialist US fertilizer producer Innovar Ag, first entering the market towards the end of last year. This new urea-based, high analysis (45-0-0) fertilizer has multiple capabilities. Importantly, the product:
- Incorporates four different mechanisms for reducing nitrogen losses from volatilisation, immobilisation, denitrification, and leaching
- Has the ability to increase microbial populations by acting as a long-lasting food source
- Enables crops to better utilise phosphorus, potash, secondary nutrients and micronutrients.
The product’s active components are well-researched, both by universities and extension services. These components are all thoroughly proven and provide predictable results, according to Innovar, being backed by 1,000 cumulative studies.
InnoSolve 45N™ is manufactured by Innovar using a proprietary ‘Encapsulated Infused Fertilizer’ (EIF) process. This completely infuses each granule during granulation, but without excessive heat, ensuring superior agronomic results, says Innovar.
“In our view, InnoSolve 45N™ is the most cost effective, broad spectrum fertilizer technology on the market,” comments Carrie Garcia, Innovar Ag’s managing director. “Our revolutionary Encapsulated Infused Technology allows four different efficiency technologies to be included into a nitrogen or phosphate fertilizer.”
The thinking behind the EIF process came out of the Innovar team’s many years of experience and market development work – stretching back more than two decades – with a range of polymer-coated, urea-formaldehyde, stabilised and organic fertilizers. Innovar’s link-up with a polymer manufacturing company and a state-of-theart manufacturing plant (formerly devoted to oil and gas sector products) has also made the EIF process and the production of InnoSolve 45N™ a reality.
The company’s precision EIF manufacturing site in the US has the capacity to produce up to 500,000 tons of InnoSolve products annually. Innovar is also seeking to expand production internationally at other manufacturing sites in regions with important markets.
“Even with the best growing season predictions, mother nature has a habit of throwing a wrench into the works – leaving growers without the best fertilizer technology for the change in conditions,” comments Andrew Semple, Innovar Ag’s CEO. “A fertilizer product that combines multiple technologies has long been desired, yet operational, manufacturing and economic challenges have precluded the chances of such a development. Until now!”
Semple is proud of the new product and what’s been achieved by his colleagues: “The Innovar Ag team has introduced a new all-star fertilizer that combines multiple, proven technologies in one nutrient substrate. We now have a world where nutrient management challenges are all answered by a single fertilizer source that’s a proven compilation of nutrient efficiency technologies.”
He concludes: “It is truly exciting to see InnoSolve 45N™ at the forefront of nutrient plans being devised by agronomic managers. We see this new product as providing a ‘one stop shop of tools’ in a single fertilizer.”