Sulphur 390 Sept-Oct 2020
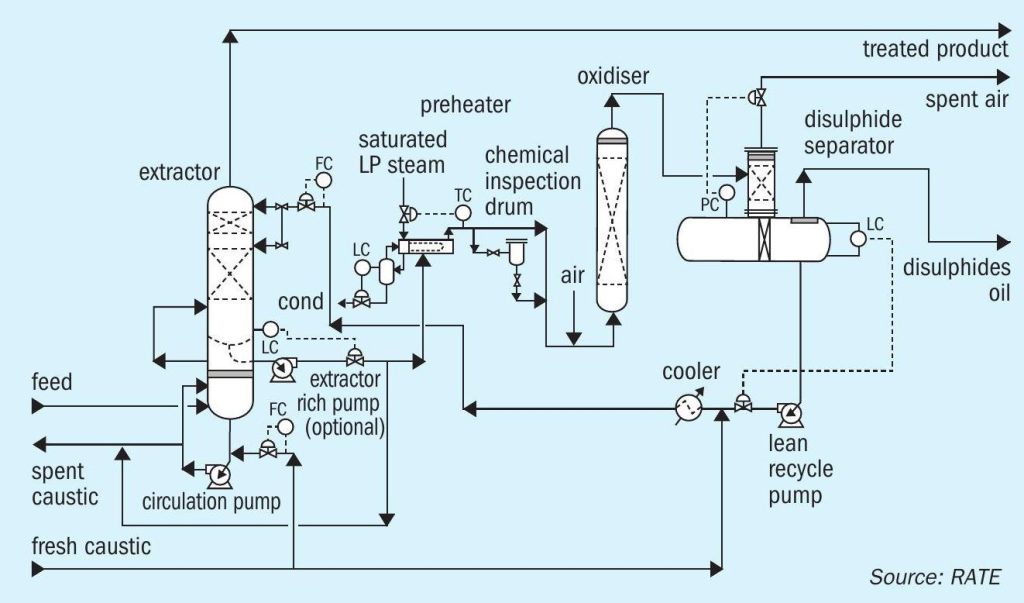
30 September 2020
Meeting sulphur specs
ADVANCED MERCAPTAN REMOVAL
Meeting sulphur specs
An advanced mecaptan removal process has been developed and implemented by RATE. The RATE-Oximer process is an oxidative air-based regeneration process, designed to remove mercaptans from liquid and vapour phases. M. Rameshini of RATE describes the key features of the process and its applications.
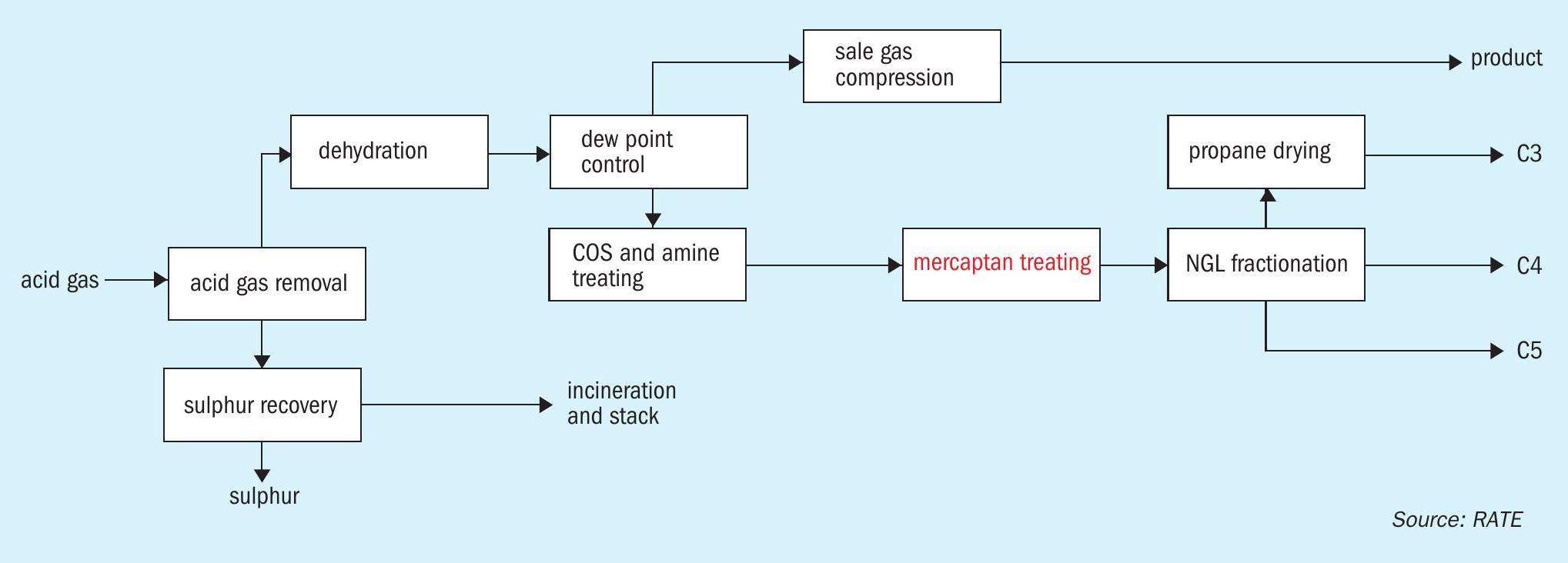
A typical sour gas processing scheme highlighting the mercaptan treatment unit is shown in Fig. 1. Often mercaptans can be removed by proper selection of a formulated amine solvent, but sometimes, e.g. where there are higher volumes of mercaptans, further processing may be required to meet the specification of the treated sales gas or pipeline criteria.
In some cases the removed mercaptans are sent to the sulphur recovery unit for processing and destruction, but for small amounts of mercaptan removal catalysts and scavengers are typically used.
The RATE-Oximer process is an efficient and economical catalytic process developed for the chemical treatment of petroleum fractions to remove sulphur present as mercaptans or to directly convert mercaptan sulphur to less objectionable disulphides. This process is used for liquid phase treating of liquefied petroleum gases (LPG), natural-gas liquids (NGL), naphtha, gasolines, kerosene, jet fuels, and heating oils. It also can be used to sweeten natural gas, refinery gas, and synthetic gas in conjunction with conventional pretreatment and post treatment processes.
The principle of the RATE-Oximer process is to use dilute caustic to absorb the mercaptan from the feed stream and then to use air over a liquid sulphonated cobalt phthalocyanine catalyst in the oxidiser reactor to regenerate the caustic. Catalyst consumption is in the range of 250 to 350 ppm, based on the concentration and volume of the caustic.
In the extractor fresh feed is charged to the column, where mercaptans are extracted by a countercurrent caustic stream. The caustic absorbs mercaptans and then flows to the oxidiser which is injected with catalyst to oxidise the absorbed mercaptan to disulphide, which is insoluble in caustic. The disulphide is then separated from the caustic and the lean caustic is recycled to the extractor.
The key features of the liquid sulphonated cobalt phthalocyanine sweetening catalyst are:
- completely miscible with caustic;
- good chemical and thermal stability;
- convenient to use;
- higher catalytic activity;
- longer cycle.
It is especially suitable for the liquid-liquid sweetening of heavy oil catalytic cracking gasoline, hydrogenation refined gasoline and LPG sweetening, processing materials including gasoline, LPG, synthesis gas, coal gas, natural gas and for the removal of hydrogen sulphide and mercaptans (deodorisation) in the gas phase.
The RATE-Oximer process has been designed for applications with and without an upstream amine unit. Those that include an amine unit have used generic DEA or MEA amine solvent. The catalyst is supplied through RATE.
The extractor can be applied to both gaseous and light liquid hydrocarbon streams. The degree of completeness of mercaptan extraction depends on the solubility of the mercaptan in the alkaline solution which, in turn, depends on the following:
- molecular weight of mercaptan;
- degree of branching of mercaptan molecule;
- caustic soda concentration;
- temperature of the system.
Mercaptan solubility in the alkaline solution decreases with increasing molecular weight of the mercaptan and with increasing branching of the mercaptan molecule.
RATE performs simulation modelling case by case based on feed composition.
Process description
In the first step, the feedstock is contacted in the trayed or packing extractor vessel with an aqueous caustic solution. The caustic solution reacts with mercaptans and extracts them. The reaction taking place in the extractor is:

In the above reaction, RSH is a mercaptan and R signifies an organic group such as a methyl, ethyl, propyl or other group. For example, the ethyl mercaptan has the formula C2 H5 SH.
The second step is referred to as regeneration and involves heating and oxidising of the caustic solution leaving the extractor. The oxidation converts the extracted mercaptans to organic disulphides (RSSR) which are liquids that are water-insoluble and can be separated and decanted from the aqueous caustic solution. The reaction taking place in the regeneration step is:

After decanting the disulphides, the regenerated “lean” caustic solution is recirculated back to the top of the extractor to continue extracting mercaptans.
The net overall caustic treating reaction covering the extraction and the regeneration step can be expressed by the following equation:

The feedstock entering the extractor must be free of any H2 S. Otherwise, any H2 S entering the extractor will react with the circulating caustic solution and interfere with the caustic treating reactions. Therefore, the feedstock is first “prewashed” by flowing through a batch of aqueous caustic to remove any H2 S. The reaction that takes place in the prewash vessel is:

The batch of caustic solution in the prewash vessel is periodically discarded as “spent caustic” and replaced by fresh caustic as required.
The caustic solution leaving the bottom of the mercaptan extractor (rich caustic) flows through a control valve which maintains the extractor pressure needed.
It is then injected with liquid catalyst (on an as needed basis), flows through a steam-heated and is injected with compressed air before entering the oxidiser vessel where the extracted mercaptans are converted into disulphides. The oxidiser vessel has a packed bed to keep the aqueous caustic and the water-insoluble disulphide well contacted and well mixed.
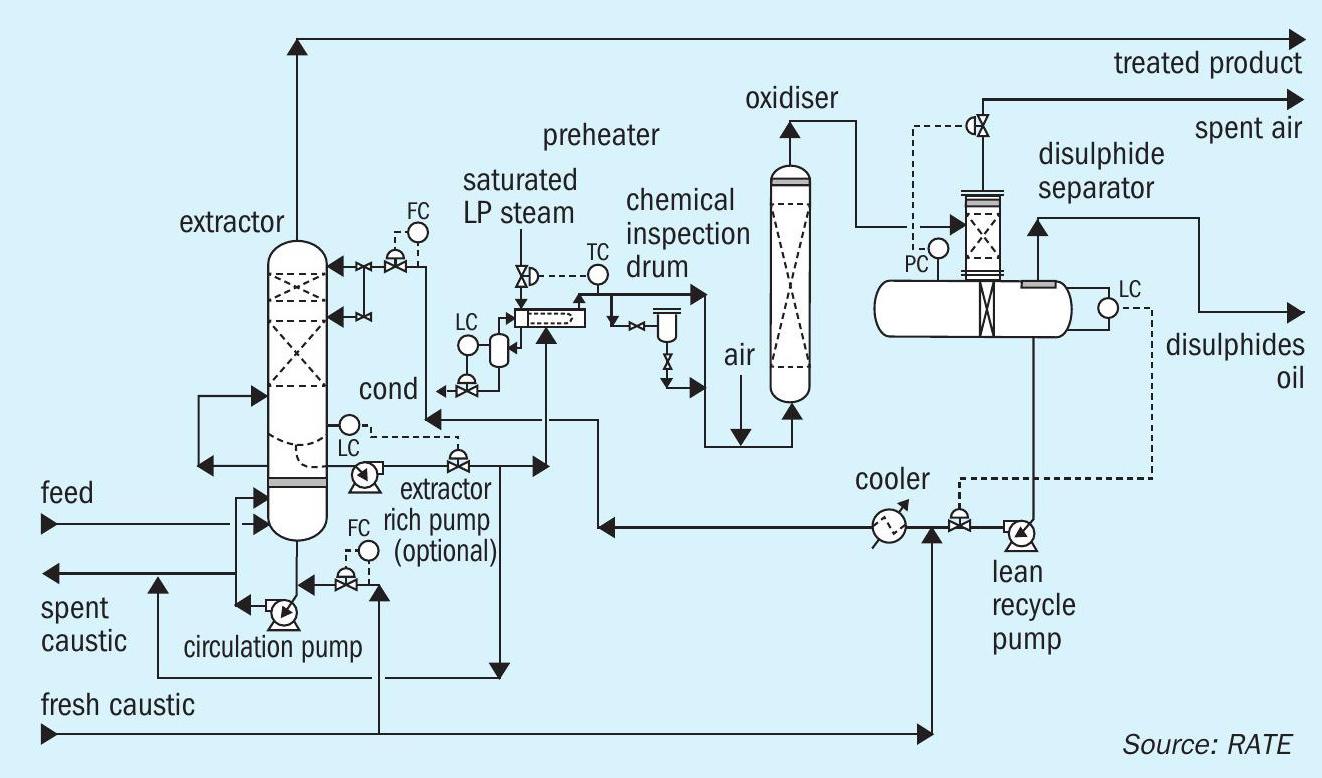
The caustic-disulphide mixture then flows into the separator vessel where it is allowed to form a lower layer of lean caustic and an upper layer of disulphides. The vertical section of the separator is for the disengagement and venting of excess air and includes a Rasching ring section to prevent entrainment of any disulphides in the vented air. The disulphides are withdrawn from the separator and routed to fuel storage or to a hydrotreater unit. The regenerated lean caustic is then pumped back to the top of the extractor for reuse.
The caustic and excess air mixture from the reactor flows into the top section of the disulphide separator. Here the air and any hydrocarbon vapour are vented to the incinerators and the caustic flows to the lower section or settler section where it is coalesced and separated. All separations are based on physical characteristics only; no chemical reactions are involved.
The caustic settler or disulphide separator is designed with sufficient residence time to handle upsets and to break down foam. A demister section at the top of the dome minimises carryover of liquid droplets in the vent gas. The vent gas leaving the dome is diluted with fuel gas to ensure that the vent gas mixture is always in the nonexplosive range.
The volume of fuel gas added is equal to 120% of the process air injection rate to the air diffuser. The minimum amount of oxygen required to support combustion in this type of mixture is about 11 vol-%. The 1.2:1 ratio of fuel gas to air reduces the oxygen content to at least 9.55 mol-%, even if no oxygen is consumed in the reactor.
It is important to mention that in the “RATE-Oximer” process if the feedstock is a vapour disulphides are not a problem, however, in the liquid phase if the specification is very tight some oil injection may be required to absorb the disulphides.
If the facility does not have caustic storage, it may be beneficial to have a small caustic inventory for the RATE-Oximer process. To date, in all projects the project specification has been met without using any oil. The low consumption of caustic and catalyst makes the process very economical. There is no product deterioration as a result of side reactions and no addition of undesirable materials to the treated product. The advantages include: a low operating cost, the caustic and the catalyst are cheap and available worldwide, the process is highly efficient, easy to operate and reliable, there is minimal waste unless excess components like CO2 come from the amine unit, and the product meets specification and environmental regulations.
If LPG contains significant disulphide an additional packing column is provided using oil as the solvent to absorb disulphides. Fig. 2 shows a process flow diagrams of the RATE-Oximer process without an amine unit.
RATE has designed several RATE-Oximer units in South America and in Russia and has supplied the process design package (PDP) to several EPC contractors. The proprietary RATE-Oximer process design is licensed by RATE with performance guarantees.