Sulphur 390 Sept-Oct 2020
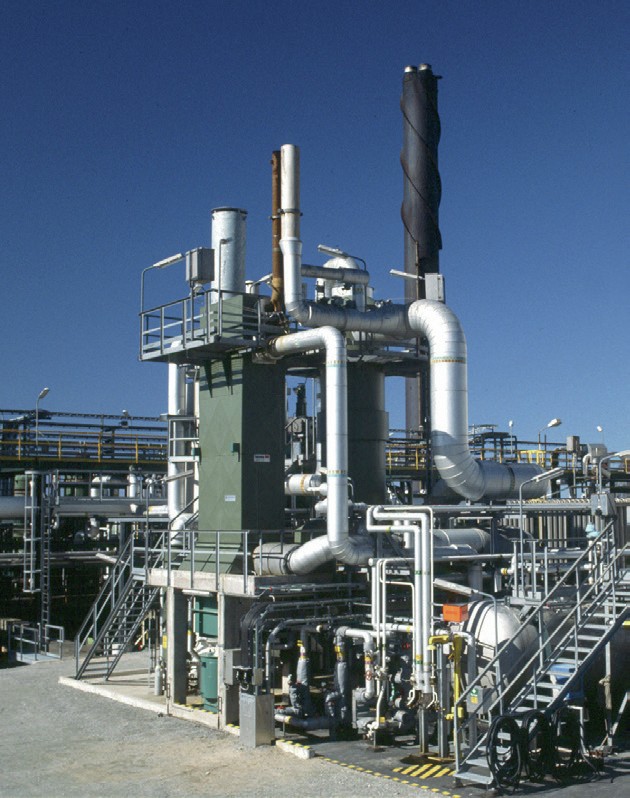
30 September 2020
Sulphur Industry News Roundup
DENMARK
Strategic alliance on TopClaus® technology
Haldor Topsoe and Comprimo® have announced a global strategic alliance to jointly license the TopClaus sulphur removal and recovery technology. TopClaus combines Topsoe’s energy efficient wet sulphuric acid (WSA) process with the industry-standard Claus process, enabling plant operators to handle acid gases and achieve sulphur removal efficiencies of above 99.9%. The Claus part of the unit recovers elemental sulphur from acid gases, and the tail gases from the Claus unit are then treated in the WSA unit, where the remaining sulphur compounds are converted into sulphuric acid.
The sulphuric acid is returned directly to the Claus reaction furnace for reprocessing to elemental sulphur, with no sulphuric acid left as by-product. However, sulphuric acid can be drawn off for specific uses or for sale as desired.
TopClaus can significantly reduce refinery CO2 production as it eliminates the need to incinerate tail gas, while the WSA unit recovers as much as 90% of the process heat in the form of superheated high-pressure steam, which can be used in other refinery processes or for generation of electricity. The companies argue that this results in lower operating costs compared to conventional amine-based technologies that use steam for amine regeneration and which requires tail gas incineration.
“We are extremely satisfied to enter into this alliance. Topsoe is an industry leader, and we share their commitment to provide customers around the world with smarter and more sustainable solutions to protect the environment,” said Frank Scheel, senior vice president, Comprimo.
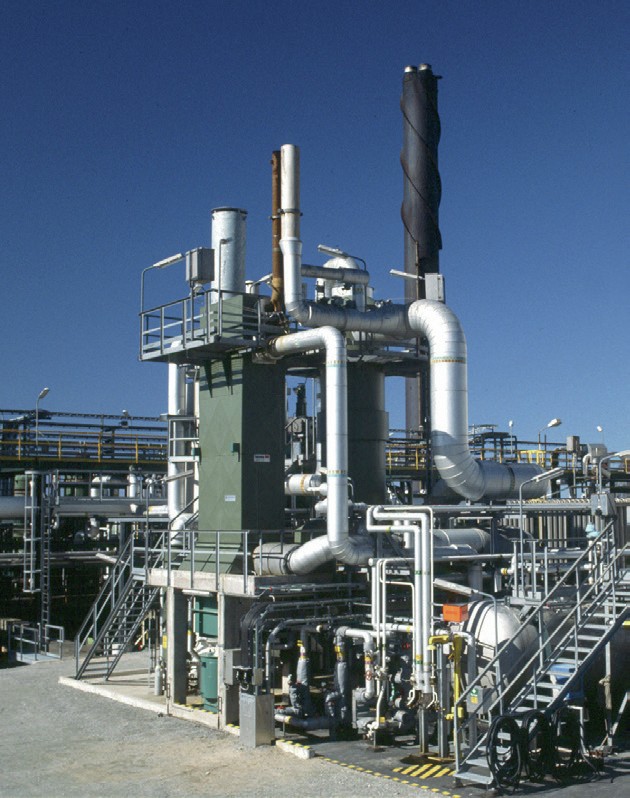
SWEDEN
IPCO celebrates 40 years of its Rotoform pastillation system
Sulphur processing and handling equipment manufacturer IPCO is celebrating 40 years’ continuous production of its Rotoform sulphur pastillation system. The rotary drop-forming technology was first developed in 1980, and was a major innovation in sulphur solidification, producing a premium formed product with consistent size, moisture and friability specifications. As formed sulphur can be handled many times between solidification and subsequent reprocessing, often being shipped between continents, IPCO argues that this predictable quality is a major advantage for the producer, the transportation company and the final customer. IPCO says that Rotoform is the most widely used sulphur pastillation system in the world in terms of number of processing units, with more than 750 machines installed to date.
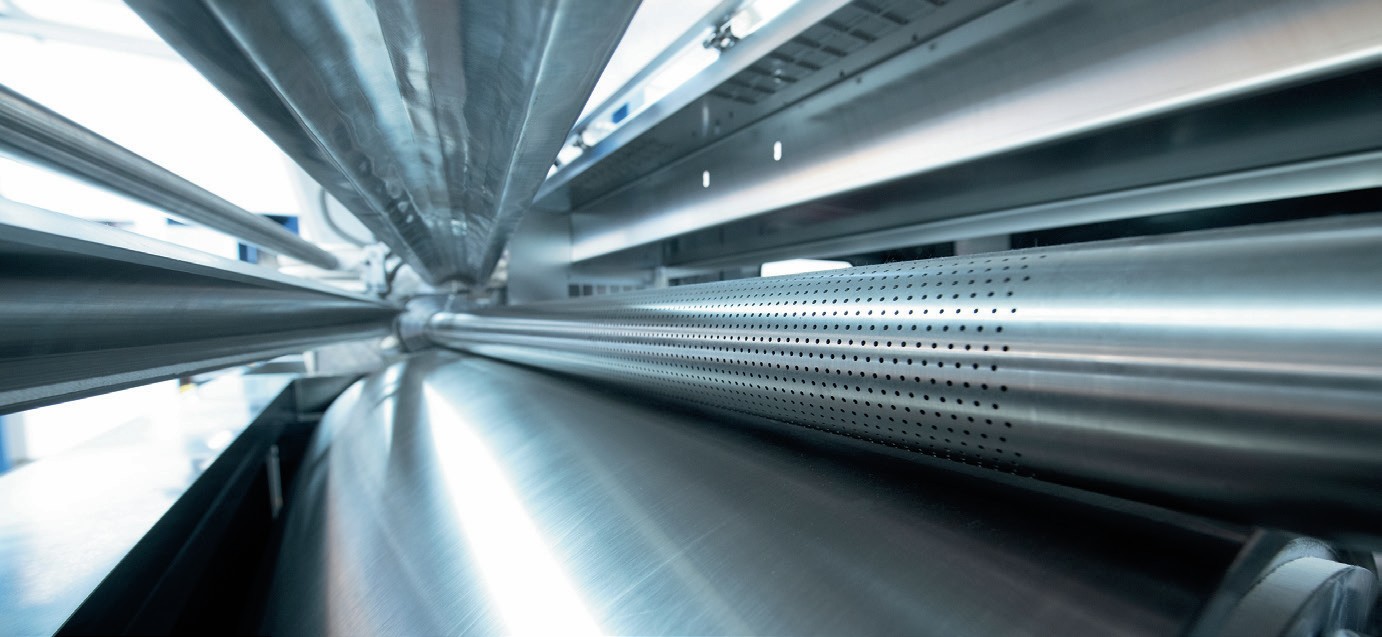
“We had been supplying flaking systems since the early 1950s,” said Johan Sjögren, Managing Director of IPCO’s Equipment division, “and our range now encompasses storage and handling solutions too, but the introduction of Rotoform was a defining moment for the company.”
While the core principle – direct melt solidification on a steel belt cooler – remains unchanged, Rotoform technology has expanded over the years to include higher capacity versions, such as the Rotoform S8, with a capacity of 140 t/d, and the Rotoform HS, a high speed model with a capacity of up to 350 t/d.
The machine consists of a heated cylindrical stator, supplied with molten sulphur via heated pipes and filter, and a perforated rotating shell that turns concentrically around the stator. Drops of the product are deposited by the nozzle bar across the whole operating width of a continuously running stainless steel belt. A system of baffles and internal nozzles built into the stator provides uniform pressure across the whole belt width, providing an even flow through all holes of the perforated rotary shell. This ensures that all pastilles are of uniform size, from one edge of the belt to the other.
The rotation speed of the machine is synchronised with the speed of the steel cooling belt to allow gentle deposition of the liquid droplets onto the moving belt. Heat released during cooling and solidification is transferred via the steel belt to cooling water sprayed underneath. This water is collected in tanks and returned to the water re-cooling system; at no stage does it come into contact with the product. After the drop has been deposited onto the steel belt, any product residue on the outer shell is returned to the Rotoform via a heated refeed bar which keeps the outer shell clean. The sulphur droplets are then discharged as solid, hemispherical pastilles at the end of the cooling system. To eliminate the possibility of damage to the pastilles during discharge, a thin film of silicon-based release agent is sprayed onto the steel belt.
IPCO argues that this process offers a number of advantages; as the cooling water never comes into direct contact with the sulphur, there is no risk of cross contamination. Secondly, solidification takes less than ten seconds so there is little time for H2 S to escape, resulting in very low emissions. And low levels of sulphur dust levels mean no need for exhaust air treatment.
CANADA
No long term effect on oil sands from Covid
Canadian oil sands production is expected to decline by nearly 175,000 bbl/d in 2020 as a result of Covid-19 − the largest annual decline on record. However, the longer-term forecast for oil sands production is expected to be little changed according to market analysts. IHS Markit projects Canadian oil sands production to reach 3.8 million bbl/d in 2030, nearly 1.1 million bbl/d higher than 2020 levels. This is down only slightly from previous forecasts of 3.9 million bbl/d in 2030. The oil sands patch is likely to see sustained but slow growth over the next decade, with transportation constraints such as a lack of adequate pipeline capacity and the resulting sense of price insecurity in western Canada weighing on new large-scale incremental investments.
Oil sands production is anticipated to rise over the back half of 2020 and into 2021 as curtailed production comes back online and existing installed capacity that has never been fully utilised ramps up. Should the Government of Alberta ease its regulated curtailment, by 2022 oil sands output could rebound from its Covid-induced declines to more than 300,000 bbl/d higher than 2019 levels.
Production would then proceed along a trajectory close to prior expectations, with most production growth to 2030 coming from Covid-19 recovery and ramp-up of already existing production capacity.
About half (over 500,000 b/d) of the rise in production is expected to come from incremental investments in new capacity, the majority of which will come from projects where some capital has already been deployed. Less than a third of anticipated growth to 2030 is expected to come from new projects that include entirely new greenfield operations or projects to expand existing facilities.
UNITED STATES
Evonik acquires Porocel
German chemical firm Evonik is acquiring the Houston-based Porocel Group for $210 million to accelerate the growth of its catalysts business. Porocel offers a technology for rejuvenation of desulphurisation catalysts, which are in increasing demand to produce low-sulphur fuel. Rejuvenation reduces CO2 emissions by more than 50% compared with the production of new desulphurisation catalysts. In addition, Porocel has available production capacity, enabling Evonik to speed up expansion of its existing business with fixed-bed catalysts. Evonik says that it expects to increase sales of the combined catalyst business to significantly more than e500 million by the end of 2025 without the need for investment in new capacities. The acquisition gives Evonik access to major customers in the refinery and petrochemicals sector. Porocel’s core competence is an efficient technology for purification adsorbents, sulphur recovery catalysts and hydroprocessing services highlighted by rejuvenation of used desulphurisation catalysts.
“This acquisition is the next logical step in the strategic development of our portfolio. Our focus is on stable and high-margin specialty chemicals,” said Christian Kullmann, chairman of Evonik’s executive board. “We are systematically expanding the share of our specialty businesses – and that at an attractive valuation.”
“Sustainability and especially circular economy play a decisive role for us when it comes to acquisitions and the orientation of our portfolio,” said Claus Rettig, head of the Smart Materials division. “With the acquisition of Porocel we are meeting increasing demand that is coming from a trend towards sulphur-free fuels as well as reducing CO2 emissions and saving resources. The catalyst rejuvenation process results in significantly less CO2 emissions than the manufacture of fresh catalysts, while yielding comparable efficiency and at a much lower cost.”
Agriculture replaces fossil fuels as largest human source of sulphur
A new study has found that fertilizer and pesticide applications to crops are now the most important source of sulphur in the environment. Sulphur used to find its way into soils via sulphur dioxide emissions from burning fossil fuels and its uptake into ‘acid rain’, a phenomenon which gained attention in the 1960s and 70s when scientists linked degradation of forest and aquatic ecosystems across the northeastern US and Europe to fossil fuel emissions from industrial centres often hundreds of kilometres away. This research prompted the Clean Air Act and its Amendments, which regulated sulphur content of fuels and emissions by power stations, driving sulphur levels in atmospheric deposition down to low levels today.
Eve-Lyn Hinckley, assistant professor of environmental studies at University of Colorado, Boulder, said: “our analysis shows that sulphur applications to croplands in the US and elsewhere are often 10 times higher than the peak sulphur load in acid rain. No one has looked comprehensively at the environmental and human health consequences of these additions.”
“Although sulphur is applied to agricultural lands to improve the production and health of crops, it can have detrimental effects to agricultural soils and downstream waters, similar to what occurred in remote forest landscapes under acid rain,” added Charles Driscoll, a professor at Syracuse University and co-author of the study.
The researchers examined trends in sulphur applications across multiple important crops in the US, including corn in the Midwest, sugarcane in Florida, and wine grapes in California. Their models of surface water sulphate export demonstrated that while areas like New England show declining trends in response to recovery from historic atmospheric deposition, sulphate export from agricultural areas is increasing.
The researchers predict that increasing trends will continue in many agricultural regions around the world, including places like China and India that are still working to regulate fossil fuel emissions, and argue that it is time for the research community to apply lessons learned while investigating the effects of nitrogen and phosphorus fertilizers to studying the implications of high sulphur use in agriculture.
Marathon closes two US refineries
Marathon Petroleum is to permanently close 200,000 bbl/d of refining capacity because of the reduction in demand for transportation fuels caused by the Covid19 pandemic. The company says that it will reduce its 166,000 bbl/d Martinez, California refinery to terminal operations and consider converting units to renewable diesel production. The company has no plans to restart its 27,000 b/d refinery Gallup, New Mexico, in any capacity. Both have been idled since April.
US gasoline demand fell by about 50% in the first months of 2020 because of the pandemic, and jet fuel consumption almost totally ceased. While there has been a recovery, with gasoline consumption now back up to about 10% below the same time as last year, jet fuel markets continue to be poor, with surplus fuel blended into diesel supplies, leading to inventory levels of ultra-low sulphur diesel being 30% up on average values.
“Our bigger view would be that we expected several million barrels to rationalise across the globe before this,” Phillips 66 executive vice president of refining Bob Herman said. “The pandemic only pushes it forward, and we probably get it sooner than later.”
North American refinery shutdowns have totalled 800,000 bbl/d in 2020, including Philadelphia Energy Solutions 330,000 bbl/d facility in Philadelphia, and Calcasieu Refining confirming that it will idle its 136,000 bbl/d refinery in Calcasieu, Louisiana, through at least August.
KUWAIT
Completion of clean fuels project in Kuwait
Fluor Corporation says that its joint venture with Daewoo Engineering & Construction and Hyundai Heavy Industries has successfully achieved final provisional turnover of the facilities for Kuwait National Petroleum Company’s (KNPC) Mina Abdullah Package 2 (MAB2) Clean Fuels Project in southern Kuwait.
The Clean Fuels Program is being executed on the three KNPC-owned and operated refineries in Kuwait. As part of the program, KNPC plans to retire existing processing facilities at the Shuaiba Refinery and perform a major upgrade and expansion of the Mina Abdullah and Mina Al-Ahmadi refineries to integrate the refining system into one complex with full conversion operations. The MAB2 package consists of a hydrogen plant, sulphur block (sour water stripper, amine regeneration unit and sulphur recovery unit) and utilities, off-sites and non-process buildings. MAB2 includes 800 t/d of additional sulphur recovery capacity for the refinery.
Mark Fields, president of Fluor’s global Energy & Chemicals business said: “It has been an honour to complete this megaproject alongside KNPC, training hundreds of their personnel and leveraging multiple local suppliers and contractors. We look forward to providing ongoing support to the refinery’s commercial operations and helping KNPC deliver on its mission to strengthen Kuwait’s economy by producing high-quality fuels to meet both local and international demand.”
INDIA
Desulphurisation project to commission this year
Chennai Petroleum Corporation Ltd (CPCL), a subsidiary of the state-owned Indian Oil Corporation, says that it is planning to commission two major projects, worth $300 million, during the 2020-21 financial year. The company has successfully completed the BS-VI revamp project, adding 600,000 t/a of capacity via a new fluid catalytic cracker gasoline desulphurisation unit. Pre-commissioning activities have begun and mechanical completion is expected during this quarter. Commissioning is expected by 4Q 2020. The new sulphur recovery block is expected to be mechanically complete by 1Q 2021.
The expansion comes at a difficult time for India’s refiners because of Covid-19. Several Indian refineries have scaled back operations, including CPCL’s 211,000 bbl/d Manali refinery, where production is down by 40%.
AUSTRALIA
Cobalt project presents revised economic projections
Cobalt Blue Holdings has released a project update on its Broken Hill cobalt sulphide project. The update reports significant improvements in project economics compared to the 2018 pre-feasibility study. It also upgraded mineral ore probable reserves by 55% to 71.8 million tonnes with a grade of 710 ppm cobalt, expanding the targeted life of mine to over 17 years.
Cobalt Blue plans to mine up to 6.3 million tonnes of ore, generating 3,5003,600 t/a of cobalt for electric vehicle batteries. The project will also produce up to 300,000 t/a of elemental sulphur from thermal decomposition of pyrites. A bankable feasibility study and final investment decision is expected to be completed in 2022.
CHINA
Saudi Aramco pulls out of Chinese refinery
Saudi Aramco has suspended a deal to build a $10 billion refining and petrochemicals complex in China, according to press reports. Aramco agreed last year to form a joint venture with Chinese partners China North Industries Group Corp and Panjin Sincen to build a 300,000 bbl/d refinery in the northeastern province of Liaoning. The joint venture, Huajin Aramco Petrochemical Co., would have taken 70% of its oil from Saudi Arabia for processing. However, the impact of Covid on oil prices and energy markets have evidently changed the calculations for Aramco, which faces deep cuts to its capital spending as it tries to maintain a $75 billion dividend amid low crude prices and rising debt. Reports indicate that the Chinese partners currently still intend to continue with the project, which also includes an ethylene cracker and a paraxylene unit.
VENEZUELA
Venezuelan oil production drops to near zero
In spite of having the largest paper oil reserves in the world, Venezuela’s oil production is declining so quickly that it may soon reach zero, according to analysis by IHS Markit. Venezuelan crude oil production is currently estimated at around 100200,000 bbl/d and falling. Production was around 650,000 bbl/d just a year ago and in 2017 was as high as 2 million bbl/d. The decline of the country’s oil industry – Venezuela’s main foreign currency earner – has been a catalogue of poor management, lack of investment and difficult security conditions, as well as a lack of domestic storage capacity, ongoing US sanctions and Covid restrictions. The country is now the third smallest producer among OPEC’s 13 members. However, travel restrictions globally due to Covid mean that global oil markets are subject to poor demand and remain oversupplied in spite of the absence of Venezuelan capacity. Venezuela’s refineries had been producing up to 700-800,000 t/a of sulphur at maximum output. n