Fertilizer International 500 Jan-Feb 2021
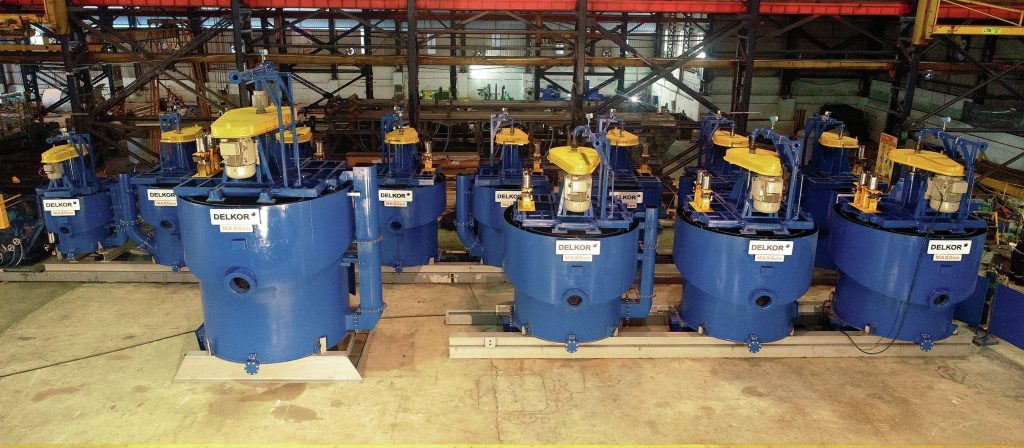
31 January 2021
Advances in phosphate flotation
MINERAL PROCESSING
Advances in phosphate flotation
Newly-developed froth flotation equipment and reagents are improving selectivity and the grade and recovery of phosphate concentrates.
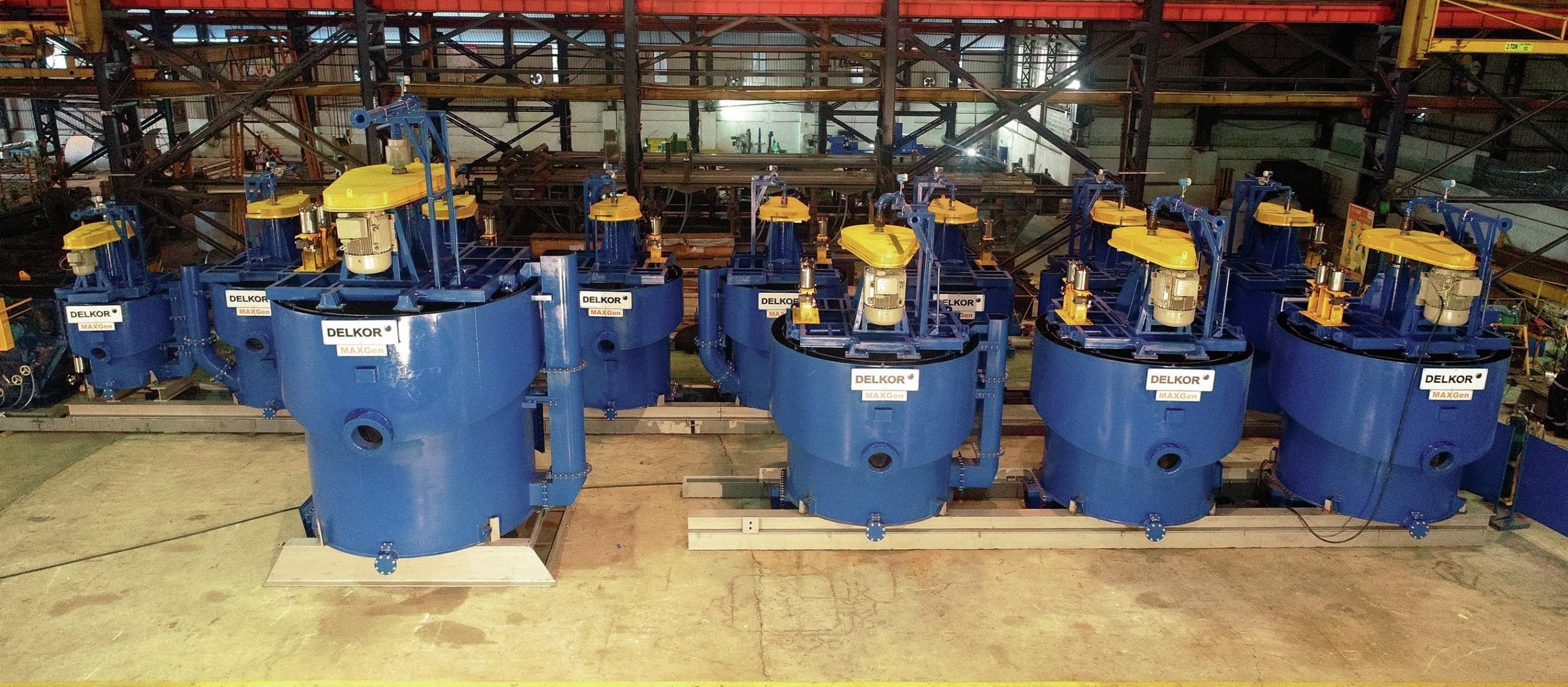
Mined phosphate rock generally needs to be processed and upgraded to meet the downstream requirements of phosphoric acid production and fertilizer manufacture. The industry requires apatite-rich rock concentrates with a high P2 O5 content and low levels of gangue minerals (silicates, carbonates and clays).
Froth flotation has become widely-adopted globally as the most effective beneficiation method for phosphate rock, since its adoption commercially in the first half of the last century. More than half of the world’s marketable phosphate, for example, and two-thirds of Florida phosphate rock, is upgraded by froth flotation (Fertilizer International 480, p53).
Flotation technologies typically fall into one of three types – mechanical, pneumatic and column flotation. Nevertheless, conventional Denver-type mechanical cells remain the most popular and well-established choice in phosphate processing plants worldwide.
Maximising the extraction of P2 O5 from phosphate rock is increasingly critical – as more efficient and less wasteful phosphate recovery from lower-grade ores has become a key challenge for the industry. This has spurred interest in new flotation technologies and reagents.
Major equipment manufacturers have responded to mining industry demands by improving the design of flotation equipment. Innovative flotation cells recently introduced by TAKRAF Group (DELKOR), FLSmidth, Eriez and others all offer attractive performance advantages – in terms of operational cost, energy consumption and process efficiency.
DELKOR’s BQR MAXGen flotation cell
TAKRAF Group launched a new type of BQR flotation cell (Figure 1) at the end of last year through its well-known DELKOR brand of liquid/solid separation and beneficiation equipment. By incorporating a new proprietary MAXGen mechanism, these latest BQR cells offer best-in-class flotation performance, according to the company.
This new mechanism, which offers both superior recoveries and higher grades, represents the culmination of extensive R&D and demonstration trials at bench-, pilot-and plant-scale.
Dr Venkoba Rao, general manager, process R&D, at DELKOR explains the benefits:
“MAXGen generates a swarm of air bubbles with an optimum size distribution. This enables the flotation of both fine and coarse particles equally. It is also highly efficient at keeping solids in suspension, so maximising the probability of bubble-particle interaction.
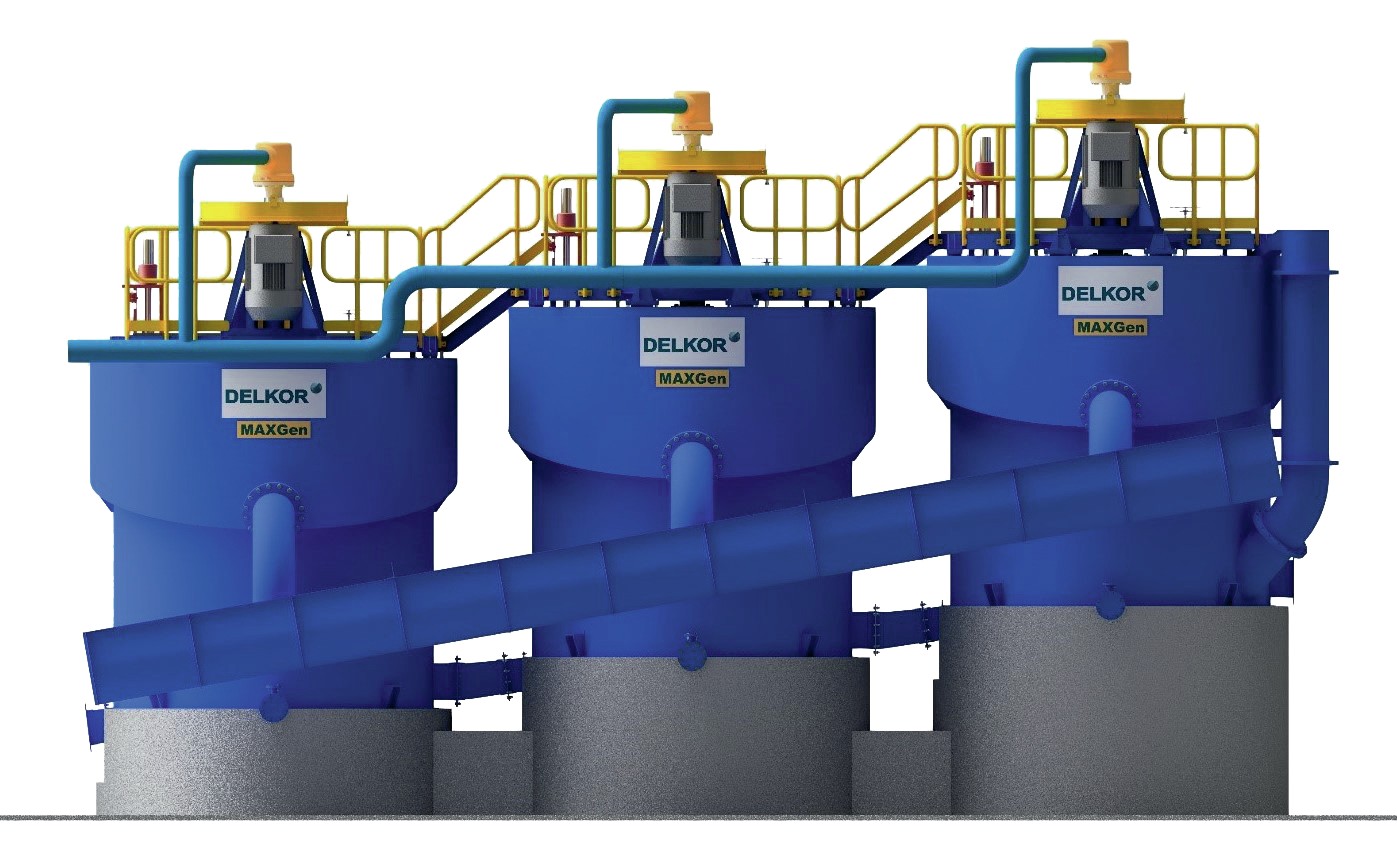
“The cell’s distinctive design configuration, meanwhile, enables the rotor to operate at a lower tip speed. This delivers operational cost savings by lowering power consumption and reducing wear.”
The BQR MAXGen cell also incorporates practical features that should improve how flotation circuits are installed, maintained and operated. One of these design features, a ‘by-pass ready’ tank, allows the easy installation of cell by-pass systems during upgrade projects, without compromising the original circuit layout or requiring modifications to the tank shell. Two of the cell’s other features – a deeper launder and higher slope – also enable froth to be evacuated quickly.
The latest MAXGen flotation cells should be well-suited to phosphate beneficiation, according to Rajiv Krishnamurthy, DELKOR’s sales manager for Europe:
“The flotation process is perhaps one of the more important operational processes within the phosphate beneficiation flowsheet. Phosphate is liberated in different size fractions depending on the specific ore deposit – with most phosphate ores demanding a flotation process for particle-size fractions between 500 µm to 45 µm.”
“Second generation BQR flotation cells equipped with the proprietary MAXGen mechanism are capable of generating a suitable bubble size distribution for this particle range – and providing an optimum agitation level. These second generation cells are suitable for direct flotation of phosphate minerals or the reverse flotation of silica in the froth.”
FLSmidth’s REFLUX™ flotation cell
FLSmidth is currently developing a revolutionary REFLUX™ flotation cell (RFC) with Australia’s Newcastle University. Its unique design is capable of achieving higher grades, recoveries and throughputs than any other flotation cell currently on the market, according to the company.
“We believe the whole system is unique in its design and mechanics,” says Lance Christodoulou, FLSmidth’s, global product manager for REFLUX™ technologies1 . “You are essentially dealing with a form of staged flotation.”
He continues1 : “The feed makes contact with air in an environment where there is high energy density and high shear rates, effectively increasing the probability of collision and attachment. This bubbly mixture is then passed down into a chamber which operates at a very high air fraction – much higher than anything currently available in the market and approaching what we would call flooding conditions.”
The incorporation of lamella plates and the enclosure of the system improves flotation kinetics in comparison to conventional cells – improving both grade and recovery at the same time. Christodoulou explains how this new design operates in practice1 :
“Having [lamella plates] allows for advanced bubble slurry segregation, enabling the RFC to operate in higher air fractions with higher air flux and higher throughput. The RFC’s lamella plates allow you to achieve the segregation – and therefore operate with a smaller bubble diameter – as well as higher superficial bubble surface area flux which then allows for better recoveries.
“We have enclosed the system… and that allows us to operate with very high wash water fluxes and very high gas fluxes, pushing us out into operating ranges that are not possible in open cell systems… simultaneously achieving higher grade and higher recovery.”
FLSmidth has already demonstrated the RFC at pilot-scale system on a continuous basis using a constant supply of feed. In addition, the company and the University of Newcastle are currently trialling a two-metre RFC machine on Australian coal. This full-scale evaluation is due to be completed in early 2021.
FLSmidth is also conducting trials on mined fertilizer raw minerals, and is confident about how its new REFLUX™ flotation cell technology will perform.
“A test is scheduled in early January on phosphate,” Christodoulou told Fertilizer International. “Based on other work we have performed, we expect the RFC to be a good candidate for treating finer phosphate feeds to produce high recovery and enhanced rejection of gangue materials, consequently providing a low MER (minor element ratio) product.”
Other flotation advances from FLSmidth
FLSmidth recently launched two other new flotation products able to enhance recovery. The company’s innovative mixedROW™ flotation system was released alongside a new ‘froth recovery upgrade package’ at the end of 2019.
Column flotation revolutionises Brazilian phosphate beneficiation
Erich Dohm and Eric Wasmund of Eriez Flotation outline the major performance benefits achieved at phosphate plants in Brazil by replacing mechanical cells with flotation columns.
Brazil’s igneous phosphate deposits contain valuable apatite as well as impurities such as barite, hematite, calcite, alumina and silicates. These ore types are typically processed in two stages. A milling circuit is firstly used to liberate the target mineral (apatite) which is then subsequently recovered by coarse and fine flotation circuits.
Mechanical versus column flotation
In Brazil, mechanically-agitated cells were the standard choice in flotation circuits for many years. However, due to the presence of finely-sized particles, mechanical cells often struggle to produce high-grade concentrates. Fine impurities such as magnetite and silica are a particular problem, as these are easily carried into the froth by hydraulic entrainment, thus lowering the quality of the final concentrate. The attrition effect within mechanical cells is also deleterious as this continuously generates and releases fresh fines into the circuit. As a result, conventional mechanical flotation usually requires chemical depressants and multiple cleaning stages to achieve acceptable grades.
Column flotation cells, in contrast, are well suited to the processing of Brazilian phosphate ore – having become a popular choice throughout the phosphate industry for the selective flotation of fine particles. Flotation columns, when equipped with well-designed froth washing systems, enhance the overall quality of the froth concentrate by minimising the carryover of fine impurities into the floated product. Accordingly, one highly efficient column flotation stage can often replace three stages of cleaning in mechanical cells. In some cases, the wash water can also lower chemical dosage rates by partially offsetting the need for depressants. Additionally, columns cells do not generate fine slimes as they do not create the intense agitation associated with the rotor/ stator in conventional mechanical cells.
Brazilian phosphate producers began replacing conventional flotation machines with column cells in the mid-1990s. These upgrades were driven by a desire to improve separation performance, reduce operating costs, and simplify plant circuitry. In fact, two phosphate beneficiation plants in Brazil have replaced their entire mechanical flotation circuit with columns cells.
Effective bubble generation essential
While columns offer many potential performance benefits, some commercial installations have failed to meet expectations due to ineffective bubble generation (gas sparging) systems. However, the Cavitation-Tube sparger in Eriez flotation columns (Figure 2) is one of the most effective sparging systems on the market – being perfectly capable of meeting the rigorous reliability standards demanded by industrial operations.
The Eriez sparger is an hour-glass shaped tubular device constructed of wear-resistant material. A centrifugal pump circulates a mixture of flotation pulp and compressed gas through the device during operation. The use of a circulation system avoids the need to introduce additional fresh or clarified water during bubble generation. Within the sparger, cavitation is induced by the higher flow velocity and lower pressure of the slurrygas mixture in the cylindrical throat, relative to the mixture in the cylinder entrance. A network of distribution pipes is used to disperse this slurry-gas mixture throughout the flotation tank.
Benefits of column flotation technology
A real example of the performance benefits delivered by column flotation technology is shown in Table 1. This compares phosphate beneficiation results obtained after mechanical cells were replaced with columns during an upgrade at a major phosphate plant in Brazil. The upgrade reduced the number of cells in the plant from 66 mechanically-agitated machines down to just six columns.
Installing column cells has proven to be extremely effective for upgrading fine material into saleable products. Indeed, the recovery of fine apatite improved markedly despite the use of less equipment. Recovery increased by 56 percent for the natural fines in the feed, for example, and by 18 percent for fines generated by the grinding circuit. The retrofit also reduced power costs by six percent, and lowered collector demand for barite and apatite by 70 percent and 86 percent, respectively.
Column flotation widely adopted
Eriez, a proven leader in column flotation, has become a trusted partner for the phosphates industry due to its ability to deliver innovative flotation technologies that reduce production costs and cut reagent and power demand. The company has installed 50 column flotation cells in Brazilian phosphate applications to date. Eriez also continues to work closely on new projects using this technology – notably Aguia Resources’ Tres Estradas phosphate project in southern Brazil (Fertilizer International 495, p46). Eriez has also piloted StackCell® two-stage flotation with Brazilian phosphate producers. This innovative technology offers additional efficiency gains, in comparison to conventional mechanical cells and columns cells. Furthermore, Eriez customers also benefit from its full in-house metallurgical testing and analytical capabilities. These are invaluable when it comes to flow-sheet development, equipment sizing, and understanding and evaluating flotation circuit options.
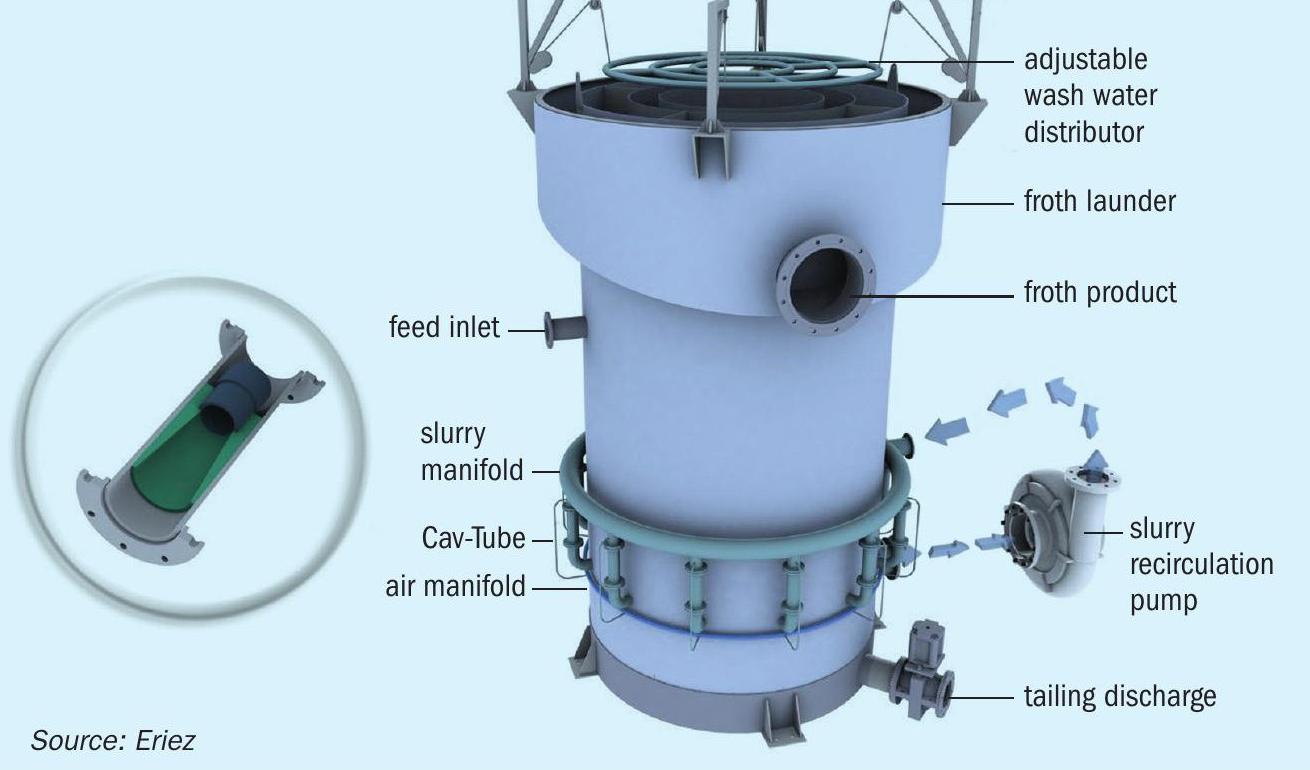
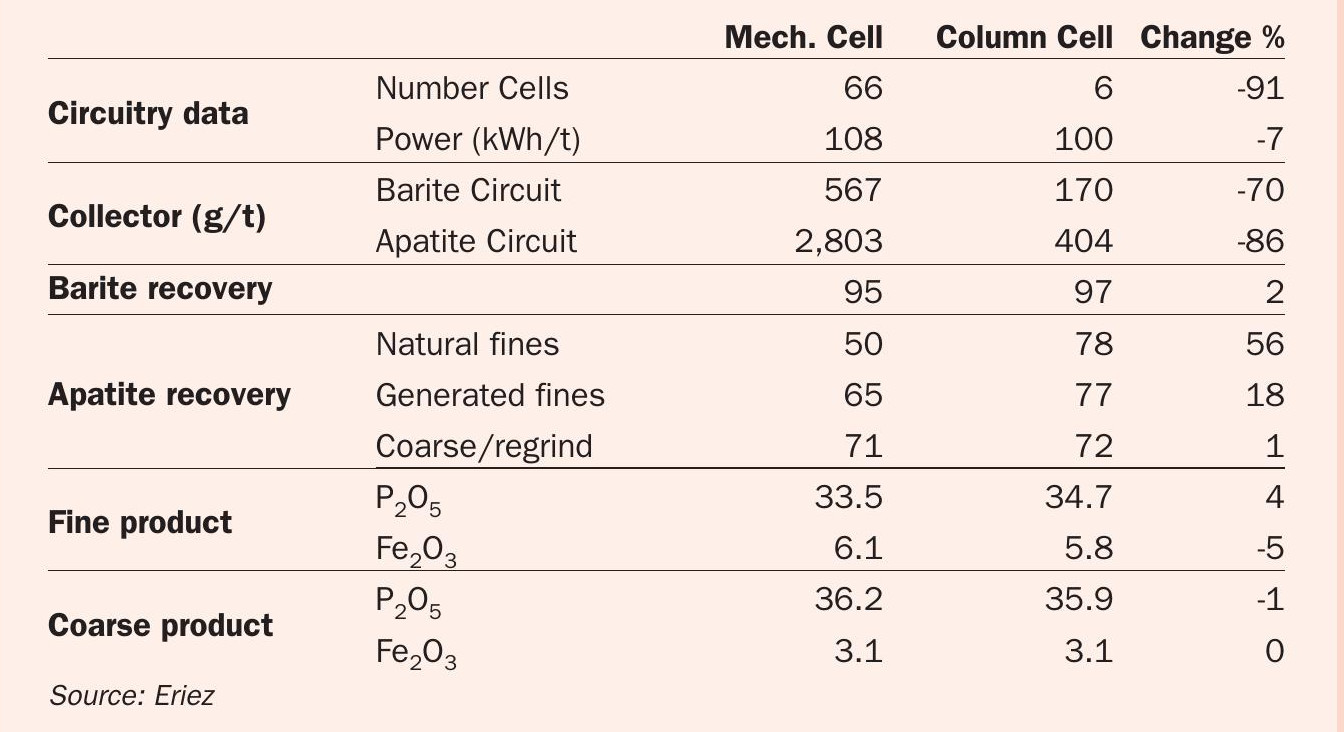
Both innovations address a pressing need, according to FLSmidth2 .
“Flotation systems are a vital technology in minerals processing and extraction. But despite their overall effectiveness, particles of valuable ore still get disposed of along with waste material. Additionally, the energy consumption that flotation systems require to function effectively is high. So while flotation systems are necessary when recovering ore, making them more sustainable and energy-efficient has been a challenge.”
The first-of-its-kind mixedROW system combines two flotation machines – the nextSTEP™ forced air cell and the Wemco® self-aspirating cell – as a way of boosting flotation recovery while reducing environmental footprint and increasing profitability.
nextSTEP machines are placed at the beginning of the flotation circuit to recover coarse material using the least amount of energy possible. This positioning lowers energy consumption by between 15-40 percent and increases recovery by up to five percent. In contrast, the Wemco machines – which are capable of treating a wider range of particle sizes – are placed at the end of the circuit to increase both coarse and fine particle recovery. The elevated rotor position within Wemco machines also cuts energy consumption by reducing the distance the froth has to travel.
The improvements in recovery possible with the mixedROW flotation system – although not large in numerical terms – can still translate into very large economic gains, potentially equal to tens of millions of dollars. Although only officially launched in 2019, the mixedROW concept has already been successfully applied in both new installations and retrofits.
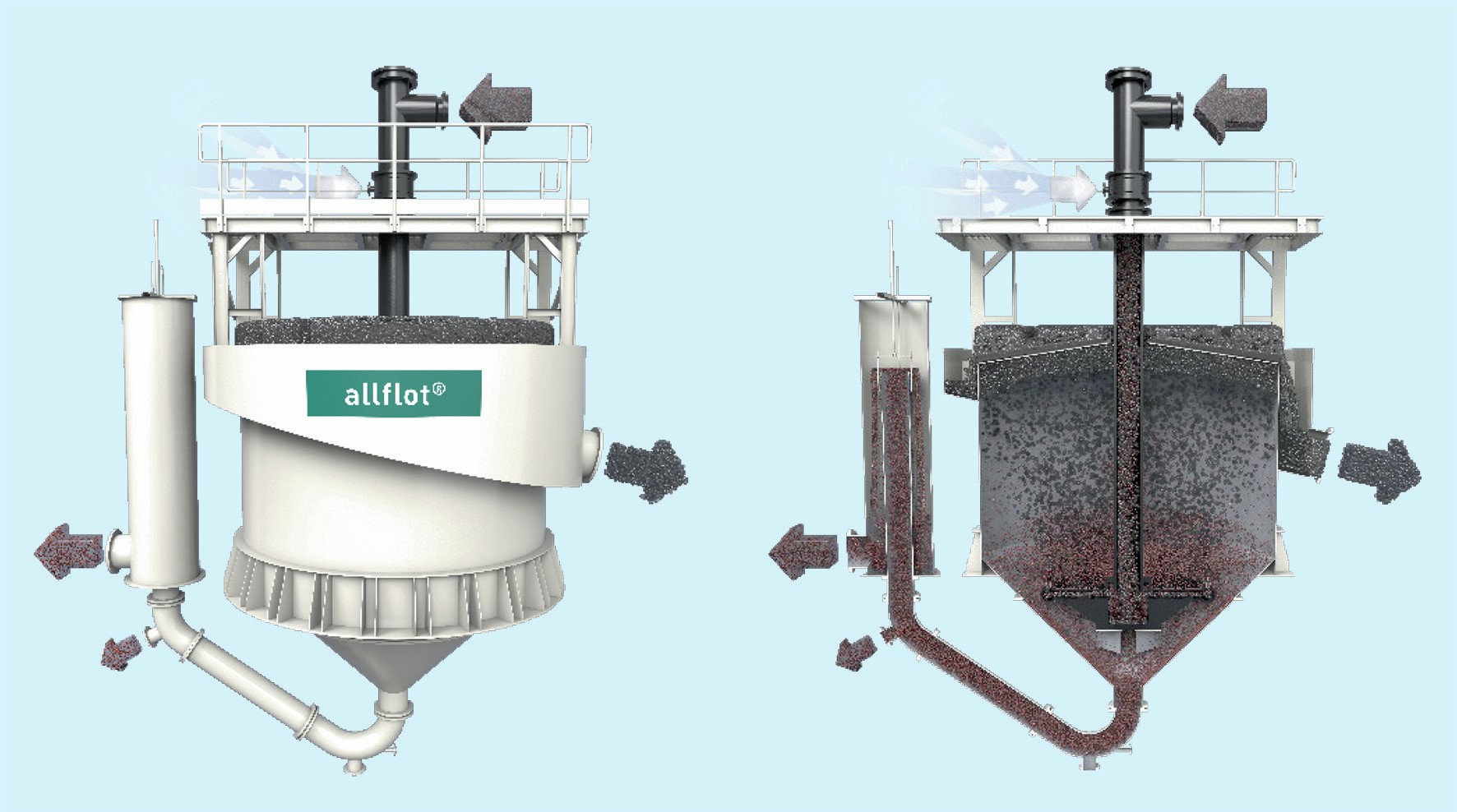
Until recently, flotation circuit losses in the mining industry were substantial, typically around 50 percent, and even running as high as 90 percent for coarse particles in some instances. FLsmidth’s ‘froth recovery upgrade package’ is designed to minimise the loss of these valuable particles, while also improving control of the froth recovery process. It does this by combining four design features:
- Adjustable radial froth crowders (ARFCs): developed in-house by FLSmidth, these mechanical devices increase either recovery or grade, regardless of the amount of froth formed at the top of the machine. They permit much higher pulling rates (to improve recovery) or much deeper froth (to boost grade)
- Advanced froth cameras: provided in cooperation with Stone Three, a market leader in vision equipment, these allow precise monitoring of the froth phase.
- Redesigned actuators: provided in cooperation with Festo, these control the position of modified dart valves inside the flotation cell.
- New and improved level sensor: provided in cooperation with HyControl, the solid state MultiSense probes accurately monitors both the slurry level and froth position.
By harnessing the combined benefits of crowders, froth cameras and actuators, processing plant operators are able to make quicker adjustments to the flotation circuit in response to changes in flow and slurry density – dramatically boosting the performance of flotation machines.
The most difficult part of the flotation process is often froth recovery in cells located at the end of the row. At this stage, because there is not enough hydrophobic particles to form a stable and deep froth, a large percentage of these can fail to be recovered. FLSmidth’s new upgrade package helps resolve this problem. Not only does it increase recovery of these particles, it also enables precise control of recovery and grade in this part of the flotation circuit.
In summary, the new upgrade package provides two major flotation process improvements – firstly, precise control of froth depth and, secondly, the choice of increasing pulling rate or froth depth. Because of this, the package can deliver either better recovery at the same grade or increased grade at the same recovery. The package can also be retrofitted into existing plants regardless of the type of mechanical cell (forced air or self-aspirated).
Pneumatic flotation
The German company EKOF manufactured the first pneumatic cell for coal flotation in 1987. The innovative design incorporated an energy saving, self-aspirating, venturi-based aerator.
The allflot® pneumatic flotation machine from Düsseldorf-based manufacturer Allmineral (Figure 3) offers several potential benefits for phosphate ore flotation. It can either function as a scavenger cell to increase recovery and/or as a cleaner cell to improve grade.
The allflot® machine operates as a high-intensity flotation cell – with a flotation throughput 2-4 times greater than an equivalent mechanical flotation cell. The machine brings mineral particles into close contact with fine bubbles within an external aerator/ contactor. The external contactor uses either pressurised air or air entrained in a fluid jet. The contactor/aerator functions as the primary collection zone while the main tank acts as the disengagement zone.
The power consumption of allflot® pneumatic flotation cells are 40 percent lower than conventional mechanical agitator cells. Their installation footprint is also smaller. Phosphate flotation experience with the machine dates back to 1996, and includes detailed test work at JPMC in Jordan, Simplot in the US and Kazphosphate in Kazakhstan. Results have demonstrated the ability of the allflot® machine to produce marketable phosphate grades and achieve high recoveries (Fertilizer International 495, p48).
Collector reagents
Clariant offers the Flotinor and Flotigam range of collectors for direct and reverse flotation of phosphate ores. The company’s Flotigam 3135 proprietary reagent – an ether propyl di-amine – has long been used as a standard collector by a leading global sedimentary phosphate mine. This mine produces nearly four million tonnes of concentrate by processing around six million tonnes of ore feed using multiple flotation cells. For 30 years, the high production mine has used Flotigam 3135 as its benchmark collector due to its ability to deliver consistently high-grade concentrates (≥32% P2 O5 and <3% SiO2 ) at recovery rates in excess of 80%.
High-grade phosphate ores which are most amenable to fatty acid flotation are becoming exhausted. As a consequence, reverse flotation using amines and specialised anionic collectors will become increasingly necessary in some parts of the world, suggests Clariant, particularly for difficult-tofloat ores where carbonates are present as gangue. This is true in Florida, where ores are becoming more dolomite-rich as extraction moves southwards. High levels of carbonate minerals are also present in new South American and African phosphate deposits.
Clariant is highly active globally, having successfully conducted direct and reverse flotation trials on a wide range of different phosphate ores from Africa and North and South America. In recent case studies, the company has been able to demonstrate how difficult-to-float ores – which do not respond to conventional low-cost anionic collectors – can be effectively beneficiated with new anionic and cationic collectors (Fertilizer International 480, p53). Clariant says its expertise in reverse flotation collectors for phosphate is helping to make these reagents the preferred choice for ores with high carbonate contents.
Arkema-ArrMaz is a leading global provider of speciality chemicals to the global phosphate mining and industrial minerals sectors. Its participation in the phosphates industry dates back to 1967, when the company pioneered phosphate flotation chemistry in Florida’s bone valley.
There is no universal reagent scheme or flowsheet for phosphate flotation. Arkema-ArrMaz therefore recommends an individually tailored approach, given that every ore is different.
“While flotation systems are necessary when recovering ore, making them more sustainable and energy-efficient has been a challenge.”
Increasing phosphate recovery or grade through the flotation process is a balancing act, suggests Arkema-ArrMaz, as improving one is difficult to achieve without detrimentally affecting the other. Indeed, in the company’s view, a true positive shift in the grade-recovery curve can only be achieved by integrating flowsheet design with reagent formulation. Arkema-ArrMaz therefore advises developing the reagent scheme and the process flowsheet together from the outset. This holistic approach recovers more higher-grade phosphate during flotation, while at the same time consuming less energy, fewer resources and extending mine life.
The company individually formulates its standard flotation reagents according to each customer’s unique ore characteristics (Fertilizer International 480, p53). Available product lines include:
- CustoFloat® and CustAmine® anionic and cationic collectors
- CustoFroth® frothers/surfactants
- Depressants
- Defoamers
- Flocculants
- Filtration aids
- Float oils
- pH modifiers.
CustoFloat and CustAmine reagents are specially formulated to handle clays and multiple size fractions. These collectors can successfully reject carbonate and silica in clay-laden feeds, while also maximizing grade and recovering more phosphate in finer size fractions (Fertilizer International 480, p53). The end result is the generation of more tonnes of higher-grade phosphate for phosphoric acid production – which, in turn, leads to better quality phosphate fertilizer.
Modifiers
The demand for flotation reagents capable of improving selectivity and recovery during phosphate ore processing is becoming more widespread, as high-grade deposits have become depleted. The use of additives to modify fatty acid collector systems is one area where significant advances have been made in recent years. These secondary collectors/modifiers – typically anionic or non-ionic surfactants – have a critical effect on flotation performance, especially in acidic reverse carbonate flotation.
Since the mid-1990s, BASF Mining Solutions has developed and introduced a range of non-ionic modifiers in mineral processing applications. These are marketed as safe, biodegradable and non-toxic alternatives to alkylphenol ethoxylates (APEOs) and nonylphenol ethoxylates (NPEOs). The range includes Lupromin FP A 105, a non-ionic modifier for standard fatty acid collectors. This modifier is recommended for the direct flotation of both oxidised and un-oxidised igneous phosphate ores, and has been shown to improve selectivity and increase recovery compared to conventional APEO modifiers (Fertilizer International 480, p53).
Depressants
Phosphoric acid and its derivatives have long been used as depressants for apatite in phosphate flotation. Although an effective reagent, dosage levels are normally quite high (1-5 kg/t), making the use of phosphoric acid a costly option. This depressant is also usually sourced from downstream phosphoric acid production, leaving less P2 O5 for onward fertilizer manufacture.
Nalco Water recently trialled a new depressant reagent which, says the company, should help phosphate process engineers maximise P2 O5 recovery and increasing profitability. Test results show that the new reagent can cut phosphoric acid dosage requirements by as much as 50 percent, and increase phosphate recovery by as much as three percent, without any decline in concentrate grade (Fertilizer International 480, p53).
Further reading
A more comprehensive introduction to phosphate floatation flowsheets and reagents can be found in our March/April 2017 issue (Fertilizer International 480, p53). Flowsheet, equipment and reagent options were also discussed in our March/April 2020 magazine (Fertilizer International 495, p44).
References