Sulphur 392 Jan-Feb 2021
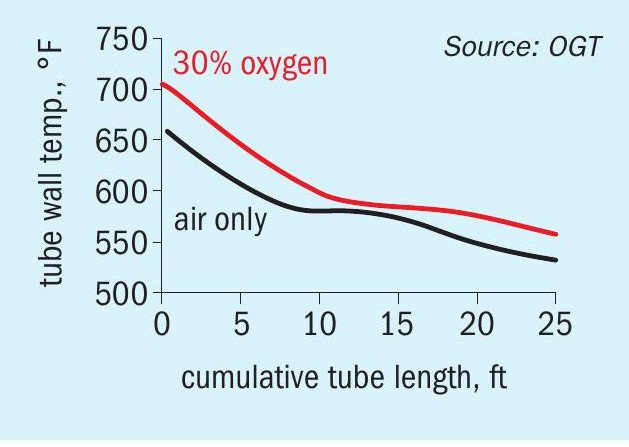
31 January 2021
SRU troubleshooting tools
SIMULATION AND MODELLING
SRU troubleshooting tools
Process and simulation models can be valuable tools when troubleshooting to solve operational issues in sulphur recovery units. Two examples are provided. In the first case study it is shown how a tuned model was useful in troubleshooting an SRU that was experiencing lower than expected recovery efficiency and apparent channelling in the first catalytic converter. In the second case study an SRU simulation tool is used to investigate sulphidic corrosion in a waste heat boiler.
SULFUR RECOVERY ENGINEERING (SRE)
The merits of tuned simulations

At one time, unit engineers were allowed to spend their time identifying problems, spending large amounts of time creating simulations, gathering data, conducting analysis of that data, calculating different variables, and then verifying their hypotheses, all to improve the operation of their units. As margins have become tighter and objectives have shifted, it is now common to see unit engineers with very little extra time, if any at all, beyond firefighting the latest issues at their facilities. Now, gaining a realistic and appropriate solution for their problems within an efficient timeframe is essential. One could argue that having a solution that is ready to solve their problems, right out of the box, could be an asset. As George Box once said, “All models are wrong, some are useful.”
SRE strives to provide that solution to its clients through tuned simulations. SRE utilises its gas chromatograph analyses to adjust the unit operations within a sulphur recovery unit created within Symmetry (a Schlumberger software). The compositional analyses of the feed streams and the inter-stage process streams are all generated by SRE engineers who collect and analyse the samples themselves to ensure complete control of the chain of custody. Ensuring accurate results is also bolstered using SRE’s GC application which analyses 33 compounds, including trace sulphurs, within a 5-minute run time. With these GC results, the thermal reactor can be tuned such that the hydrogen, carbonyl sulphide, and the carbon disulphide productions match that of the test period. Likewise, the catalytic converters are tuned to ensure the hydrolysis rates and the approach to equilibrium match the catalyst performance. Once aggregated together, the final simulation can be considered an accurate offline steady-state model of the SRU.
Using such a model can help solve some operational issues. For example, for a recent client, the facility was experiencing lower than expected recovery efficiency and apparent channelling in the first catalytic converter (Converter 1). As seen in Fig. 1, the converter temperature profile shifted dramatically between the 2019 and 2020 test periods. In between that time, there was an operational upset which resulted in an exotherm of the catalyst. After the upset, the thermocouple profile illustrated that the process gas was mainly running along the right side of the converter, as marked by the increased exotherm along that wall. The slightly lower recovery efficiency that followed suit after the upset made the operator fearful that permanent damage to the catalyst had taken place.
To troubleshoot the lower recovery efficiency and to evaluate the catalyst, SRE was brought in to conduct a performance evaluation of the SRU train. In so doing, SRE collected gas samples necessary to create the tuned SRU model. Samples must be collected across all unit operations which change the composition of the process gas. For example, samples of the inlet and outlet of the thermal reactor are required, but if there is a steam reheater in between the thermal reactor and the first catalytic converter, the inlet to the catalyst is already accounted for by the outlet of the thermal reactor. This would not be the case if the reheat method were to introduce a compositional change, like an acid-gas-fired reheater where the heat of the burn product of acid gas with air is combined with the process gas to heat it up to the desired temperature for the modified-Claus reaction. There is a compositional change across a condenser, in which the sulphur vapour drops out as liquid sulphur, but since GCs do not measure sulphur vapour or water, from an analytical perspective, the composition is the same. To make up for the lack of measurement of the condenser throughput, SRE measures the rundown for facilities with traditional sulphur seal leg look boxes. Otherwise, an assumption is needed; that the outlet temperature of the condenser is reflective of its theoretical performance. With the samples collected in duplicate for repeatability, the tuned simulation model of the SRU was created.
Typical sample points collected to create a tuned-simulation of a 3-stage Claus plant are:
- acid gases to the thermal reactor; l co-firing gas, if applicable (natural gas, refinery fuel gas, or hydrogen)
- condenser 1 outlet;
- reheater 1 outlet, if a direct fired reheater;
- condenser 2 outlet;
- reheater 2 outlet, if a direct fired reheater;
- condenser 3 outlet;
- reheater 3 outlet, if a direct fired reheater;
- condenser 4 outlet.
In reviewing the simulation data, the catalyst within the first converter was found to be fully active but the performance of the sulphur train was hindered. It was found that the hydrolysis rates had decreased from the last test period. A loss of carbonyl sulphide and carbon disulphide hydrolysis rates can be a precursor to the loss of catalyst activity. The loss of recovery efficiency was partially due to the loss in hydrolysis but was found to be mostly caused by the loss in conversion within the thermal reactor. A lower acid gas quality resulted in lower thermal conversion and the low turndown of the SRU train exasperated the reduction in performance. So, even though there were no extreme repercussions from the thermal incident, the tuned simulation model made it apparent that some damage had been done. SRE helped the client further by recommending a heat soak. This action helped to clear the channelling which was occurring and helped to regain some of the lost hydrolysis.
This example illustrates how a tuned model can be useful in troubleshooting an SRU. Further, as an offline steady state model, the model now has better predictive capabilities than the typical thermodynamic properties and can be used by the unit engineer for future troubleshooting. n
OPTIMIZED GAS TREATING, INC. (OGT)
Sulphidic corrosion in a Claus waste heat boiler
Sulphidic corrosion and thermal cycling in Claus waste heat boilers (WHB) are the two leading causes of unscheduled shutdowns of sulphur recovery units (SRUs). Sulphidic corrosion is caused by high temperatures, typically exceeding 650°F (343°C), in conjunction with hydrogen sulphide (H2 S). These conditions are especially prevalent in the reaction furnace and WHB at the SRU front-end. Metal surfaces are thermally protected by refractory lining. Additional protection is by ceramic ferrules around the tube-to-tubesheet transition joint as well as inside the first 6-12 inches (15-30 cm) of heat transfer tubing where most WHB failures occur.
Tube metal temperature is affected by the heat flux from the hot process gas through the tube wall to the cooling utility water/ steam. The hotter the tube walls, the higher the heat flux, making the heat flux of vital concern when designing a WHB or when managing changes to SRU operating conditions. Oxygen enrichment also can have a profound effect on heat flux, changing a borderline thermal condition into a catastrophic failure.
Sulphidic corrosion is generally calculated based on the widely-accepted Couper-Gorman1 curves which, at least for high heat fluxes, have been very closely confirmed by measurements made by Alberta Sulphur Research Limited (ASRL) for carbon steel. Couper-Gorman curves are also available for a variety of chromium-containing metallurgies and are generally used to assess corrosion in systems containing H2 and H2 S, typified by Claus WHBs. The Couper-Gorman curves were modified downwards by a factor of between two and three by Martens2 based on personal experience, but the original curves were subsequently validated by ASRL.
Case study
A North American refinery was considering oxygen enrichment to increase the capacity of its Claus unit. Oxygen enrichment can be a simple and inexpensive way to push more sulphur through a plant without large capital expenditure. Increasing the oxygen content of the combustion air allows part of the diluent nitrogen to be replaced with H2 S. Although oxygen enrichment has been practiced for many years, there has been a tendency for more frequent failures from the concomitantly higher operating temperatures.
Fig. 1 shows a typical three conversion stage SRU with a front-side split design on the reaction furnace, and a two-pass WHB. In addition to amine acid gas (AAG), the unit processes sour water acid gas (SWAG) with high ammonia content. As designed, the SRU operates on air only. In this instance, the WHB steam generation pressure is somewhat elevated at just over 650 psig (44.8 barg). Normally, WHBs are designed to operate in the range 300-600 psig (20-40 barg). This will be important later in the discussion.
Operating with air only
To establish a baseline, the WHB with carbon steel tube metallurgy was simulated under its present operating conditions using the SulphurPro® simulator. Sulphidic corrosion calculations based on recent ASRL research data and the Couper-Gorman plots reduced to correlations are built directly into SulphurPro® . The model provided a good picture of the heat transfer characteristics along with an estimate of the present corrosion rate in the WHB. The black line in Fig. 2 shows the tube wall temperature through the first pass of the WHB under current air-only baseline conditions.
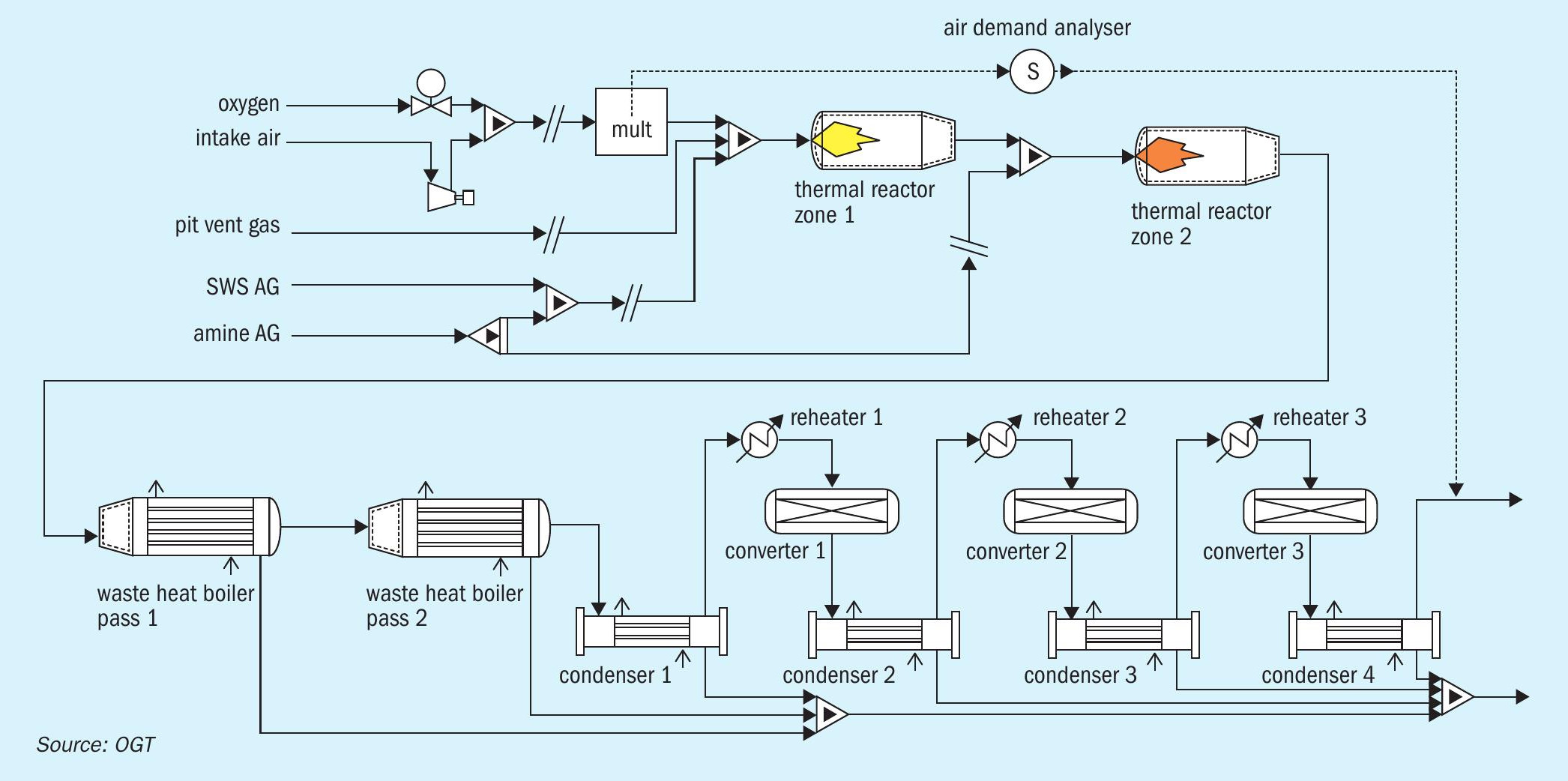
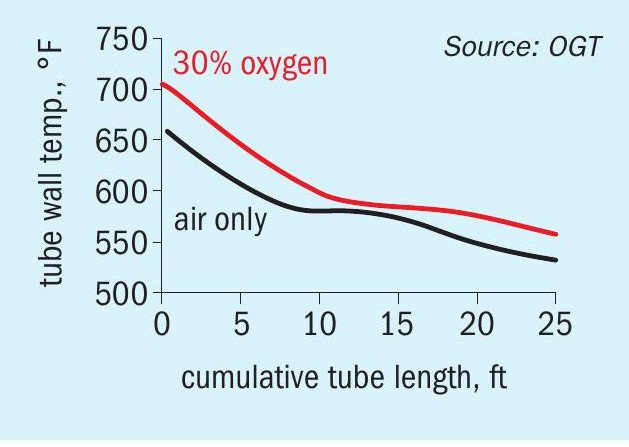
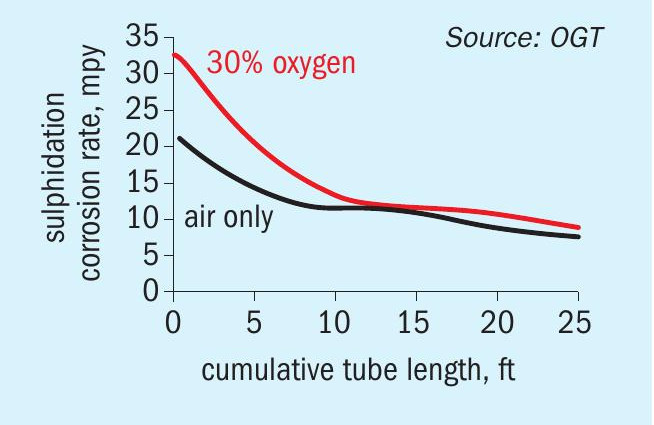
The front of the WHB (Pass 1) is where the tube wall temperature (and the heat flux) are highest. The tube wall temperature is slightly elevated at just over the recommended maximum value of 650°F. The black line in Fig. 3 shows the sulphidic corrosion rate in the first pass for the air-only base case. The predicted peak corrosion rate is just over 21 mils per year (mpy). It is somewhat alarming that even with air-only the peak corrosion rate at the front of the WHB is already twice the recommended limit of 10 mpy. With the elevated steam generation pressure the utility-side temperature is also higher so a hotter tube wall is needed to drive the heat transfer, causing the corrosion rate to increase.
Oxygen enrichment
Having established the base case, oxygen content of the combustion air was increased to 30% and the acid gas rates increased to keep the same overall hydraulic throughput in the SRU. The red lines in Figs 2 and 3 correspond to 30% oxygen enrichment. The tube wall temperature has now risen to over 700°F (371°C) at the inlet and the predicted sulphidic corrosion rate has gone to over 32 mpy. While that may not sound like a large increase, it is 50% higher than the base-case air-only operation which was already twice the recommended maximum, this in a piece of equipment liable to catastrophic failure with a high replacement cost and a potentially long lead time! Even low-level oxygen enrichment has compounded an already existing problem, producing a corrosion rate nearly three times the industry recommended maximum.
Increased sulphidic corrosion stemmed in part from oxygen enrichment, but also from the unusually-high utility-side pressure which resulted in elevated tube temperatures. The effect of utility-side pressure is to increase the predicted corrosion rate from about 11 mpy to over 32 mpy over the utility-side pressure range 150-650 psig. This may help to explain why WHB failures have become more commonplace with high-pressure steam generation, especially when using oxygen enrichment.
Summary
Even with a very modest level of oxygen enrichment and quite a low utility-side pressure it is possible for a WHB to show concerning levels of sulphidic corrosion at and near the inlet tubesheet of the boiler. When considering oxygen enrichment, the possibility of elevated corrosion must be given careful attention. It may not be enough just to lower the steam generation pressure to compensate. Oxygen enrichment can be a risky undertaking demanding assessment of multiple possible consequences. There is no substitute for a well-founded SRU simulation tool with high reliability that takes fully into account all the fundamentals of radiative and convective heat transfer, process chemistry, and the kinetics of all the reactions.
References