Sulphur 393 Mar-Apr 2021
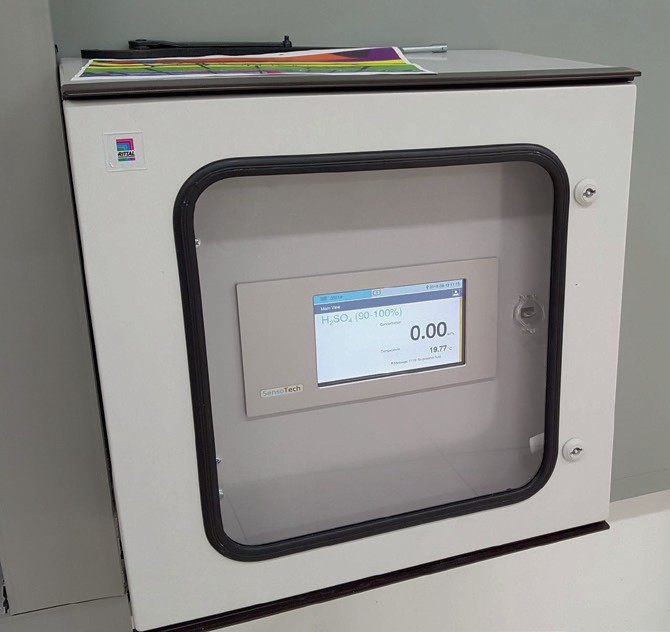
31 March 2021
Better monitoring of sulphuric acid and oleum
PROCESS CONTROL AND MONITORING
Better monitoring of sulphuric acid and oleum
Automatic identification and optimum online monitoring using sonic velocity measurements can now be used to determine the concentration of both sulphuric acid and oleum.C. Kahrmann and T. Knape of SensoTech report on a new user-friendly method of measurement providing a significant step towards automated process control.
Sulphuric acid is still one of the world’s most important industrial chemicals, used in many industrial applications and production steps. It is produced by the double contact double absorption process (DCDA) or the wet gas absorption process (WSA). Exact monitoring of the concentration of sulphuric acid and oleum in sulphuric acid plants is of great importance as it determines the quality of the end product. It is precisely this determination of the concentration that can be ideally realised by means of sonic velocity.
Conventional monitoring of sulphuric acid and oleum is carried out in many production facilities by taking samples manually. These samples are then analysed in the laboratory and a result is available a few hours later.
Advantageous of sonic velocity for process control
Determining the concentration of sulphuric acid by measuring the sonic velocity, however, offers several advantages over many other measurement methods.
Measurement principle
By emitting sound waves from a sound emitter to a receiver, the transit time of the sound wave is measured several times per second. With the measured transit time and the known distance between the emitter and the receiver, the sonic velocity is precisely determined in the electronics of the sensor. Since the sonic velocity is influenced by temperature, this must also be measured in the process liquid and its influence included in the calculation of the sonic velocity. Both sulphuric acid and oleum show excellent dependencies of the temperature-compensated sonic velocity on the concentration. The concentration can be calculated from these dependencies with the aid of a calculation model in the controller and shown on the display.
Measurement of sulphuric acid concentration
Sonic velocity is ideally suited to the monitoring of sulphuric acid concentration, providing a user-friendly method of measurement, especially in the target concentration range 80-100% H2SO4 .
Monitoring can be performed with an accuracy of up to ±0.03% and, unlike many other measurement systems, thanks to the static and dynamic temperature compensation in the LiquiSonic® system, temperature does not influence the measurement of the sonic velocity and density. It can be installed freely in the process and, compared to the density measurement method, it is less sensitive to emerging contamination in the process liquid.
Boliden confirms the suitability of sonic velocity
In Harjavalta, Boliden produces the main products copper, nickel, gold and silver, as well as by-products such as sulphuric acid. Traditionally, Boliden has used a conductivity analyser for H2 SO4 concentration measurements. At its new sulphuric acid plant, however, Boliden wanted to test something else to see if better accuracy and reliability could be achieved using an alternative technology.
The SensoTech analyser was selected due its accuracy statement and robustness. The accuracy of the first LiquiSonic® measurement was proven according to specification (0.05 wt-%) over the whole measuring span.
“All the units installed have been working fine since commissioning. The Boliden laboratory takes a control sample once a day from each line for comparison which has confirmed the accuracy. With conductivity analysers inaccuracies led to the need for many new calibrations. The reliability of the system was not at the level the operators required. Also, the measurements are almost useless when the acid concentration goes below 94 wt-%, due to the flat concentration curve of the conductive method. LiquiSonic® is in agreement with the lab references and re-calibration is no longer needed”, confirmed Jarkko Heikkilä, head of maintenance.
The first LiquiSonic® concentration analyser went into operation at the new sulphuric acid plant in Harjavalta in August 2018 to measure sulphuric acid concentration 90-100 wt-% at the outlet of the plant to the storage tank (Fig. 1).
In 2019, more units were purchased to replace conductive analysers in the old sulphuric acid plant – one at the outlet of the plant to the storage tanks, another for the feed line to the drying tower, plus one for the return line of the final absorption tower (Fig. 2).
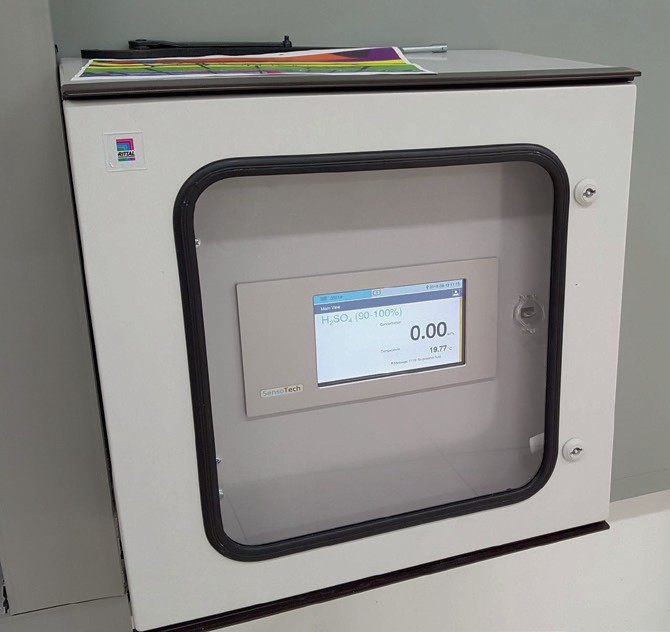
Oleum monitoring during production
Oleum is a solution of sulphur trioxide in sulphuric acid and is formed during concentration in sulphuric acid production. As soon as the sulphuric acid reaches a concentration of 100%, any further introduction of sulphur trioxide (SO3 ) is dissolved in the sulphuric acid. It is present as “free SO3 ” and is displayed as such by LiquiSonic® for the oleum range.
Oleum is also called “fuming sulphuric acid”, because in pure air the dissolved sulphur trioxide in the sulphuric acid immediately escapes. Furthermore, oleum has a strongly hygroscopic character, so that even the water content in the air causes a falsification of the initial concentration. Because they are classified as hazardous chemicals, high safety precautions must also be taken when handling them. The validity of samples analysed in the laboratory is therefore critical, even with the most stringent measures in place. Moreover, taking a sample results in a time delay. Samples have to be checked in the laboratory, which means that measurement results are only available hours later. Users can therefore only react to deviations in the process at a very late stage. Inline measurement therefore is highly recommended in technical production.
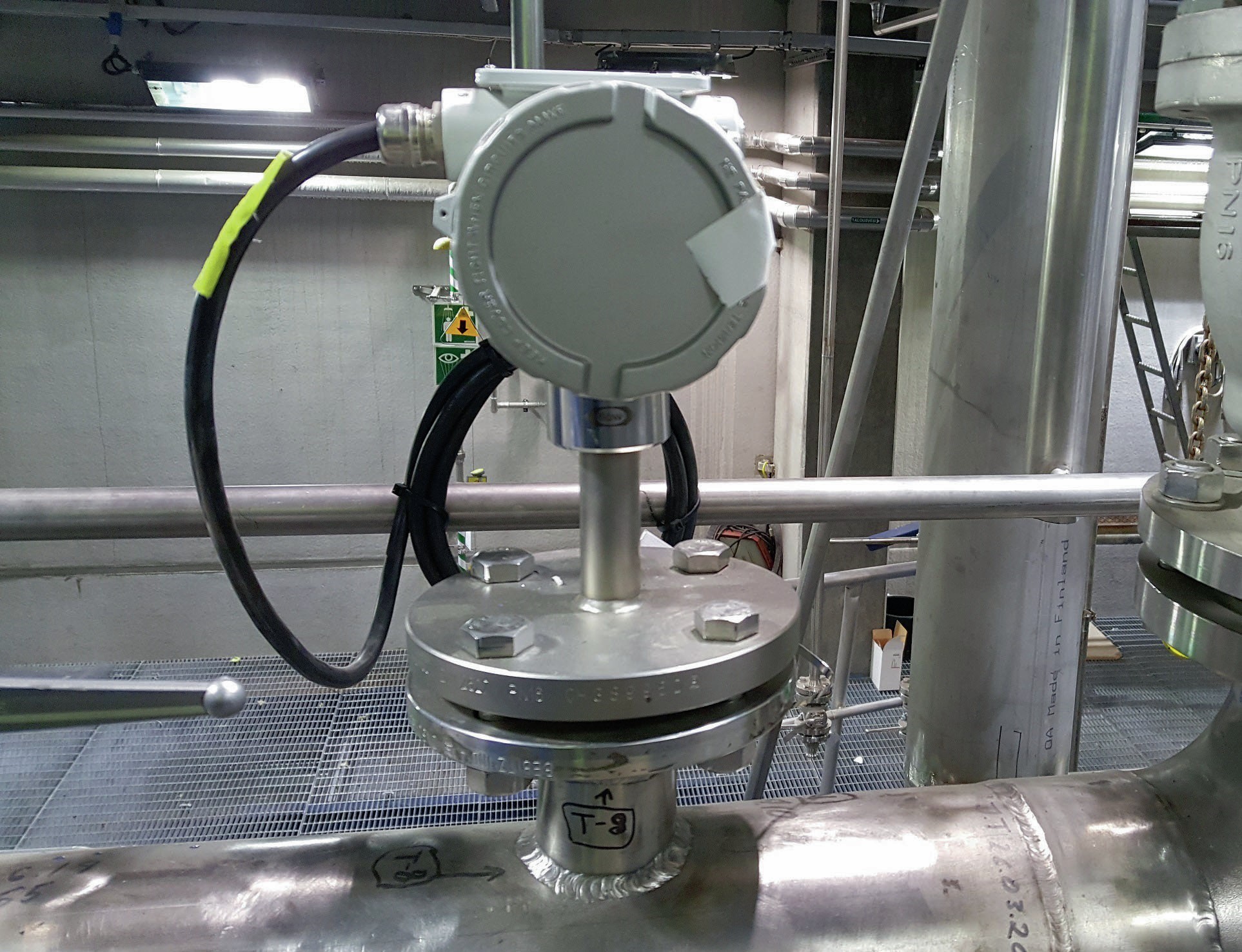
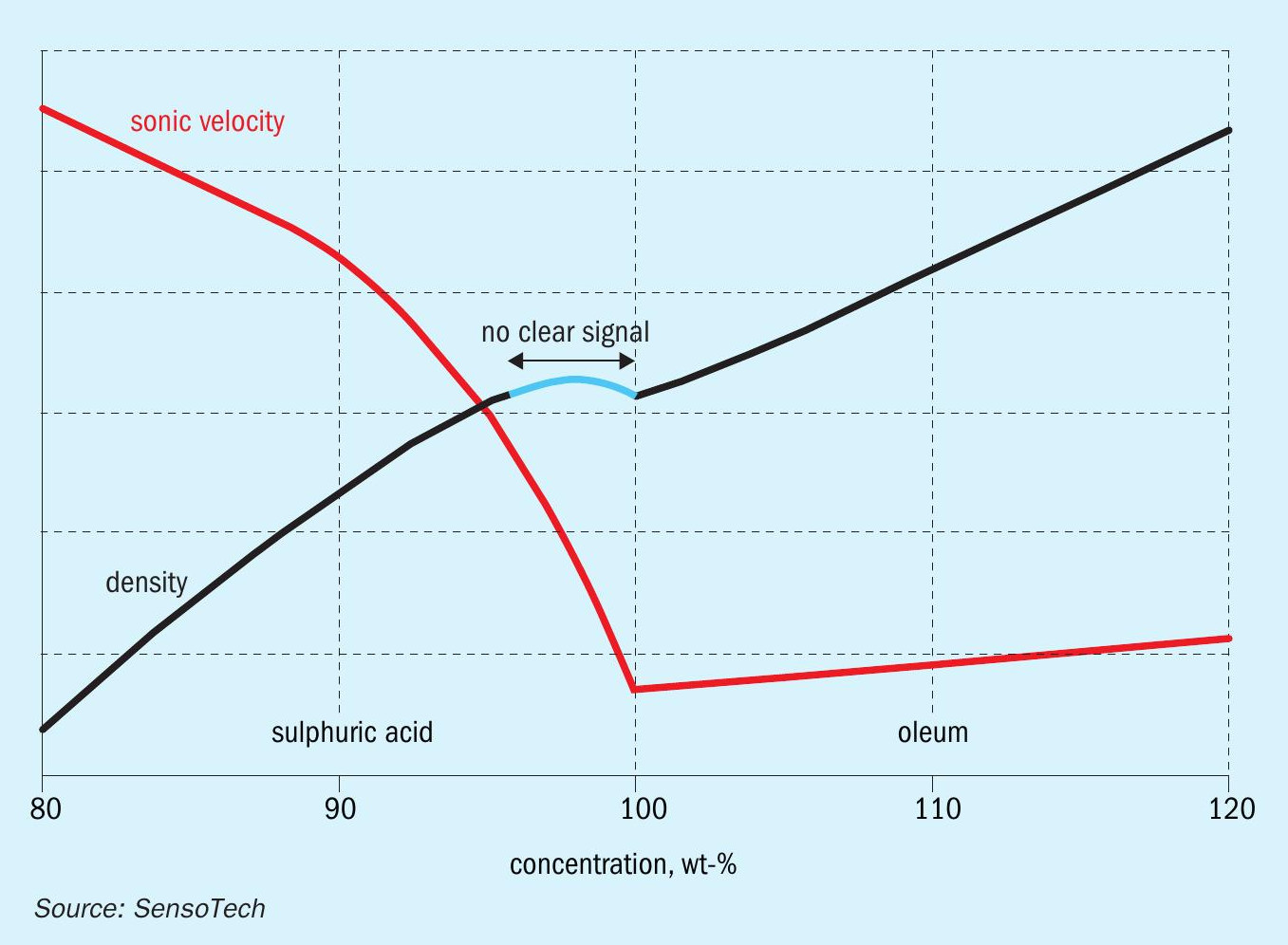
The concentration range of dissolved sulphur trioxide in sulphuric acid (oleum range) can also be monitored at sonic velocity. In the range 20-35%, a clear signal is obtained with sonic velocity measurements and thus a very accurate concentration determination. Fig. 3 shows the relationship between the concentration of sulphuric acid and dissolved sulphur trioxide in oleum and the specific sonic velocity.
Since both sulphuric acid and oleum are extremely aggressive chemicals, the sensors are made of materials that are resistant to aggressive chemicals. Thus, LiquiSonic® sensors are characterised by a long service life. For application in sulphuric acid and oleum typically Hastelloy C2000 is used.
Sulphuric acid and oleum simultaneous monitoring
Oleum or sulphuric acid usually occur independently of each other during production. Until now, it was common practice to precisely configure one analyser for a correct inline measurement. To distinguish between sulphuric acid and oleum, a second physical quantity, the density, is used. In the oleum range, this exhibits a linear dependence on concentration.
The LiquiSonic® controller uses a feature specially developed for this requirement. The detection and switching between the ranges are thus fully automated. The concentrations are determined with a special calculation model, displayed and, if desired, passed on to a process control system.
Compared to the separate inline measurement of both components, the simultaneous inline measurement has clear advantages. While the respective calculation model must be selected via the controller for individual measurements, this step is completely eliminated by using a single model. This has the advantage that concentrations, especially around the switchover point, can be determined exactly at any time. If necessary, the maintenance-free LiquiSonic® measuring system offers the possibility of adjusting the calculation model to emerging contamination, gas bubbles and other factors that interfere with the measurement. The device can thus be used very flexibly and adapted to changing process conditions.
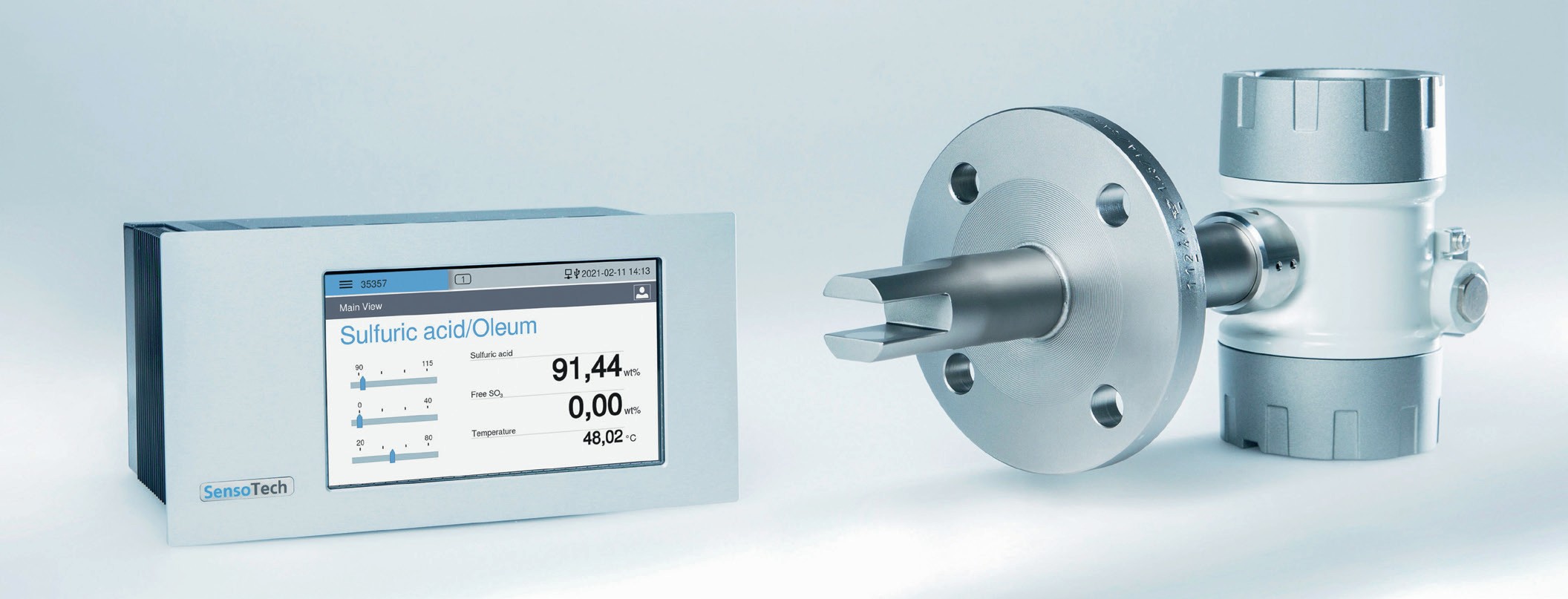
Smart process monitoring with LiquiSonic®
Especially for the monitoring of sulphuric acid and oleum, sonic velocity sensors provide highly accurate measurements. Users are thus able to optimise their process in a simple way. Continuous monitoring and documentation of quality and productivity is the basis for lean, cost-efficient and safe processes.
The LiquiSonic® measuring system from SensoTech GmbH (Fig. 4) enables monitoring of sulphuric acid and oleum with only one measuring device and without manual switching.
Automatic product recognition
Due to the different physical properties of oleum and sulphuric acid, LiquiSonic® recognises which substance is flowing through the line. While the oleum concentration shows a linear dependence on density and sonic velocity, sulphuric acid shows a different behaviour. As the concentration increases, the sonic velocity decreases exponentially, with density having a reversal point at 98%. The calculation method developed by SensoTech uses this opposite behaviour for product detection. The intelligent controller always displays the correct concentration of the current process liquid. This smart process solution thus effectively prevents misinterpretations.
Finally, in this application, the controller also provides warning messages about detected deviations in the process, which helps to improve the safety of people and the environment. The user is always informed about the current status of the process. These messages are also recorded in the automatic documentation, which saves an enormous amount of time for users and improves subsequent error analysis.
Increase safety, save resources
The simultaneous monitoring of sulphuric acid and oleum with LiquiSonic® thus revolutionises the workflow in production plants. By eliminating time-consuming and inaccurate offline sampling with the help of simultaneous inline measurement, an increase in quality assurance can be achieved immediately after installation of the measurement system. Due to the avoidance of direct contact between people and process liquid during sampling, inline measurement ensures protection of people and the environment. Automated switching between the measured process liquids provides another safe measurement. Time-delayed or forgotten switchovers between the measuring ranges, which lead to incorrect measurement data, are thus no longer a problem. The comprehensive documentation function enables longterm storage of the measurement data and subsequent analysis of the process. The data can be read out manually at the controller or transmitted directly to the process control system. Continuous data acquisition and its transfer to the process control system helps to avoid faulty batches. This enables optimum measures to be taken to adjust the process – for example, automated re-batching or manual intervention in an emergency. In this way, a purposefully controlled process sequence is realised, which maximises plant utilisation and use of resouces.
Maintenance-free measurement
Sonic velocity sensors are robust, they contain no moving parts and are ideal for use in harsh environments. The maintenance-free and long-lasting use of the sensors result in time and cost savings for repairs that would otherwise occur.
Result
The LiquiSonic® measuring system ensures optimum monitoring of sulphuric acid and oleum. Measurements directly in the line increase process reliability. Immediate warning messages ensure extremely short reaction times in the event of process deviations, reducing the required resources and ensuring improved product yields.
In most cases, the measurement system pays for itself after one year at the latest. This has convinced numerous users, including Boliden in Harjavalta, to install the system. On the one hand, this is due to the fact that the system is maintenance-free and has a long service life. On the other hand, the time savings due to inline measurements and the optimal use of resources also come into play. Monitoring takes place with no intervention in the process. Thus, the LiquiSonic® measuring devices represent a significant step towards automated process control. The sensors automate many steps of process monitoring and reduce human error.