Fertilizer International 501 Mar- Apr 2021
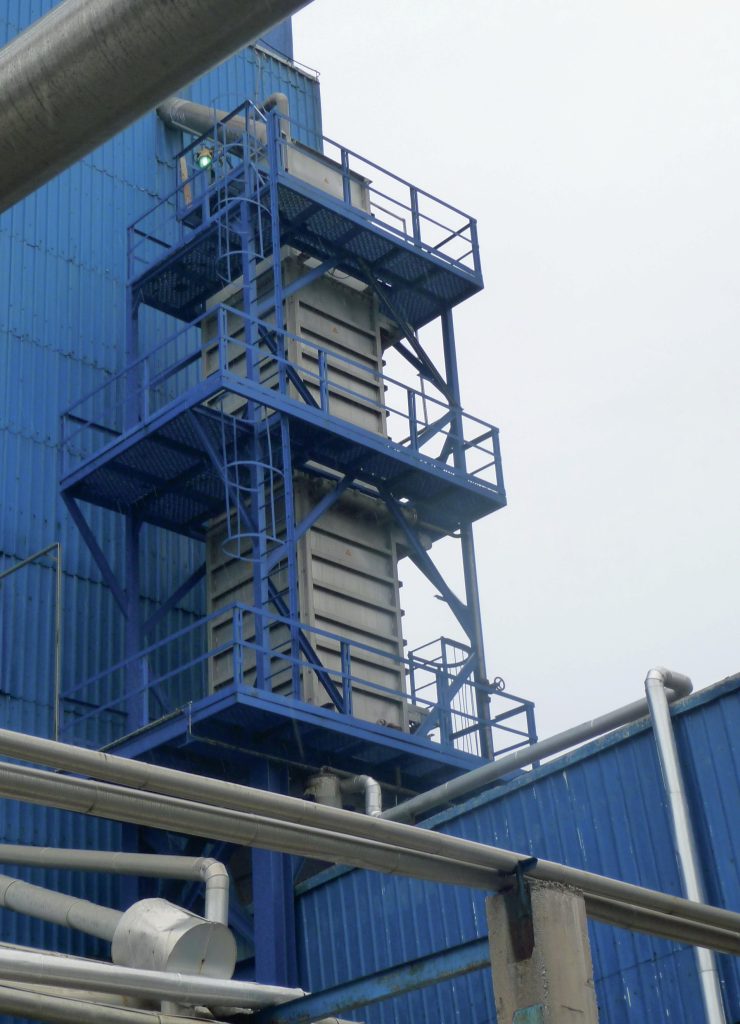
31 March 2021
Greener cooling makes better products
FERTILIZER COOLING TECHNOLOGY
Greener cooling makes better products
An industry-wide push for greater environmentally accountability is driving the need for improved fertilizer cooling methods. Not only is indirect cooling technology more environmentally-friendly, says Igor Makarenko of Solex Thermal Science, it also provides fertilizer manufacturers with a better product.
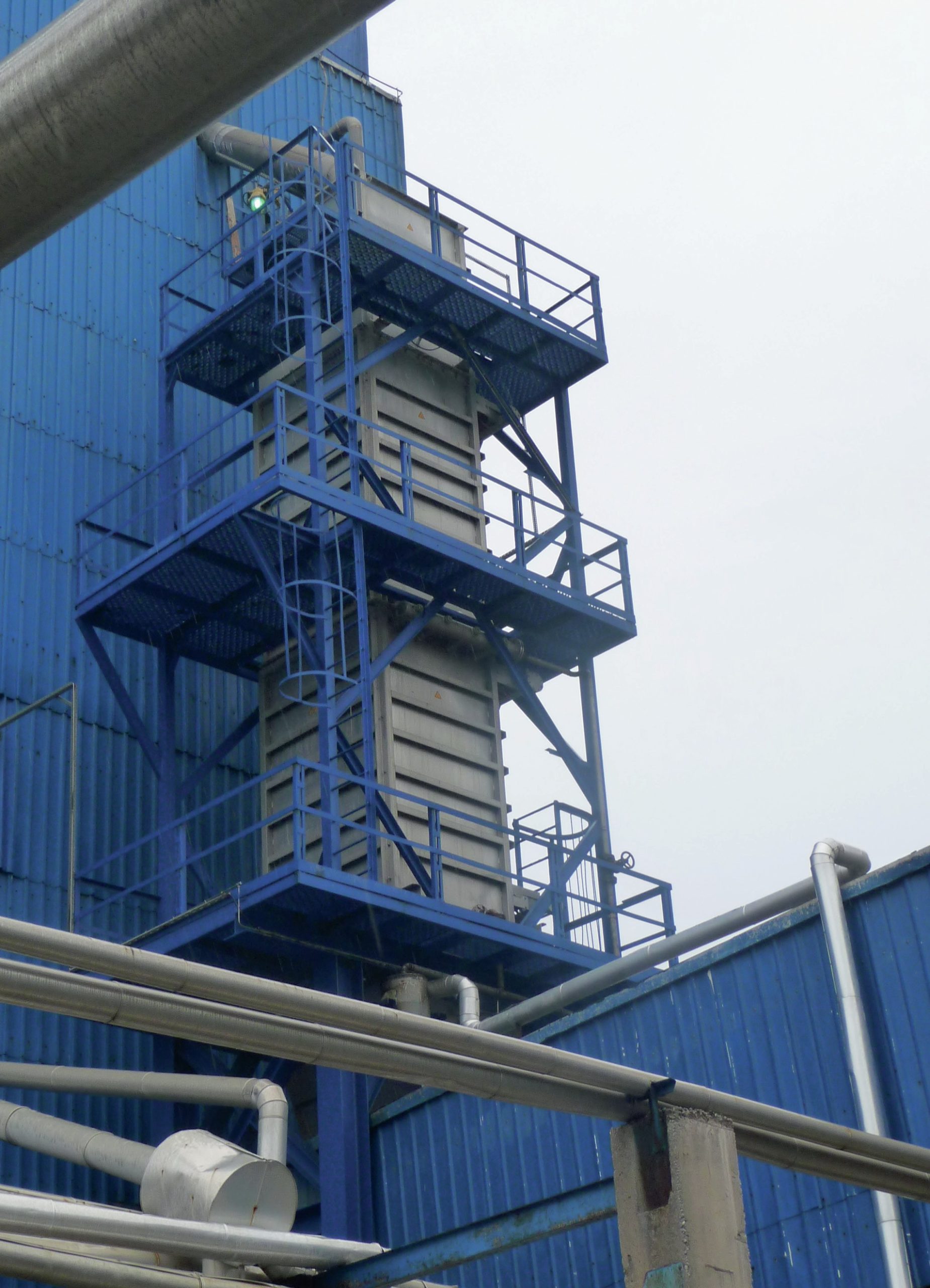
With environmental, social and corporate governance (ESG) rising up the business agenda, the fertilizer industry is taking an increasingly holistic approach to product stewardship. Creating more efficient fertilizer production processes that support sustainable food systems and mitigate climate change have become a particular priority.
The International Fertilizer Association’s first-ever Global Stewardship Conference in New York in 2020 demonstrated how sustainability has become a major priority and business imperative (Fertilizer International 495, p10). Attended by the industry’s top flight from around the world, last year’s IFA event placed ESG centre stage. In particular, the conference emphasised the need for fertilizer producers to innovate by embracing energy and water efficiency, low-carbon production methods and emissions-reduction technologies.
Such sentiments were echoed in a recent IFA member survey. More than 75 percent of respondents said growing environmental regulation will have some impact on their businesses – with the highest concerns coming from North America, West Asia and Europe.
A focus on cooling
With growing awareness of environmental responsibilities and the need to optimise processes, the industry is focused on four entwined issues:
- Emissions reduction l Improving operational practices and efficiency
- Revamping/reconfiguration of existing plants to maximise production output
- Maintaining product quality.
Inevitably, this has also shone the spotlight on the cooling stage of fertilizer production – an essential process step and key precursor to fertilizer storage and transport. However, traditional cooling equipment, such as rotary drums or fluid beds, have been hampered by their need for high volumes of air. These large air flows subsequently require the use of costly scrubbing equipment and incur considerable energy and maintenance costs. Traditional cooling equipment installations are also accompanied by other challenges such as product quality concerns (e.g. attrition) and limited throughputs (e.g. planned rate reductions).
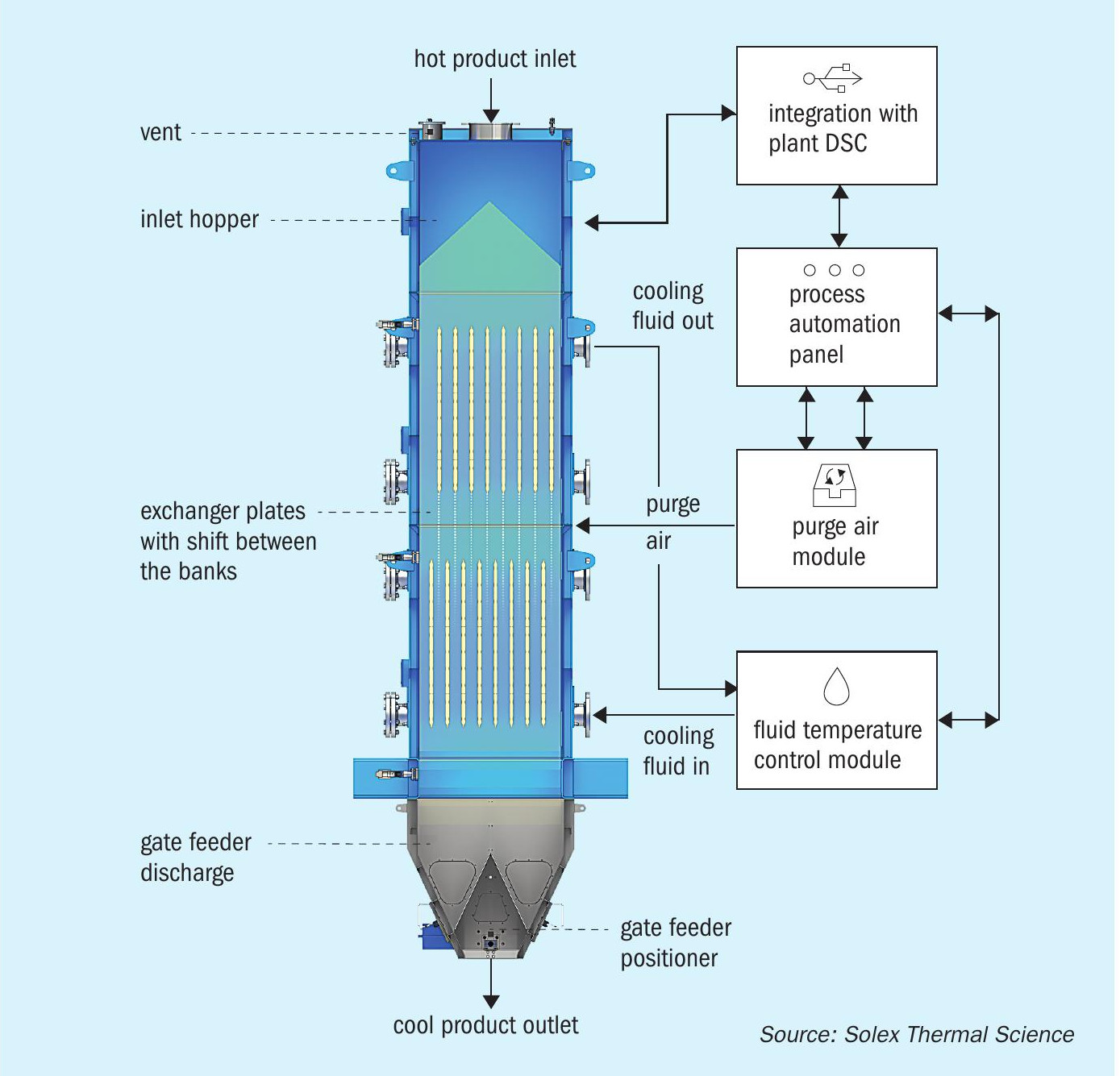
Plate-based vertical heat exchangers (Figure 1), in contrast, have emerged as a valued mainstay within the fertilizer industry. The technology offers a way to improve production and product quality, at lower capital and operating costs, while also reducing the environmental footprint of production plants.
Plate-based vertical heat exchangers are a form of indirect cooling technology. Their design harnesses the science of mass flow and combines this with high thermal efficiency. First deployed more than 30 years ago, this type of equipment has been successfully used to cool the full spectrum of currently-produced fertilizers. That includes different size products – from fine crystalline to granulated and prilled products – as well as different fertilizers types such as urea, ammonium nitrate and calcium ammonium nitrate (AN and CAN), diammonium phosphate and monoammonium phosphate (DAP and MAP), NPKs, ammonium sulphate (AS) and potash.
In the following discussion we’ve broken down indirect cooling technology into four categories:
- Overcoming water quality and water usage challenges
- Operational cost reductions – particularly for energy
- Installation cost savings
- Product quality improvements.
This provides a better understanding of how the technology works and, importantly, how it helps deliver on the industry’s current need to reduce its collective environmental footprint while simultaneously improving operational efficiency.
Addressing the water quality and usage challenge
Unlike traditional direct-contact types of cooling equipment, such as fluid beds and rotary drums, plate-based vertical heat exchange technology (Figure 1) relies on water to cool the fertilizer instead of air.
In simple terms, the technology functions as follows:
- The fertilizer flows under gravity through vertical banks of stainless-steel plates, while cooling water passes through the plates to cool the material by conduction.
- Water is circulated through the plates in counter-flow for enhanced thermal efficiency.
- This absorbs the heat from the fertilizer by cooling granular solid matter as it moves slowly down through the tower.
The benefits of utilising water instead of air as a fertilizer cooling medium are highlighted in the sections below. Yet sourcing that water – and doing so economically – can still pose challenges for many fertilizer producers around the world.
Industry concerns around water scarcity and quality were revealed by IFA’s most recent member survey. An overwhelming majority of respondents (87%) specified that water scarcity will have a severe impact on the fertilizer industry moving forward, while nearly three-quarters (74%) said deteriorating water quality is a further concern.
The adoption of cooling equipment that incorporates closed-loop water systems is one way of addressing these challenges. That’s because in open-loop water cooling systems, while water might be available in the required volume, it can present quality challenges, e.g. high-chloride content or general cleanliness. If water quality becomes compromised in such systems, it will damage or foul the heat transfer equipment over time. To prevent this happening, plant operators need to factor-in the operating costs of treating water prior to introducing it into the fertilizer cooling process.
In other operational circumstances, the volume of water required for open cooling systems might not be available on-site or is too far away or too costly to bring in. Costs can be prohibitive, for example, if plant operators need to install costly pipe bridges, insulation and even heat tracing to supply the water to the heat exchanger.
In open-loop systems, the return of water from fertilizer cooling equipment to the plant’s main water circuit is another issue. This adds extra load on cooling towers and, by reducing their capacity, can compromise process performance elsewhere in the plant.
Generally, accessing water for open-loop cooling systems can be difficult due to the quality and cost considerations described above. It is not surprising, therefore, that many plant operators are moving to closed-loop water cooling systems instead, especially when these offer other advantages such as improved operational sustainability.
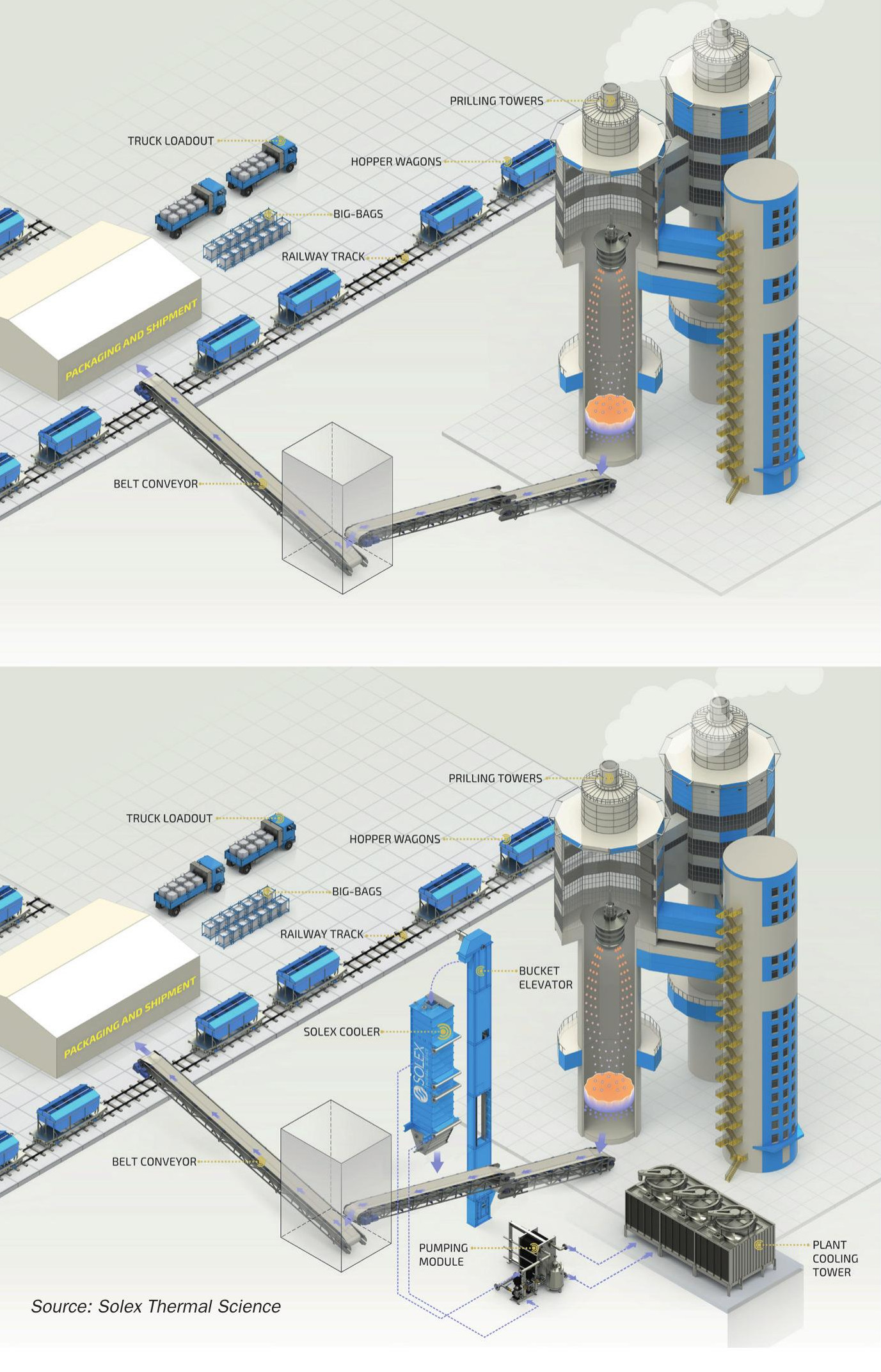
This is true of plate-based vertical heat exchange technology which, notably, incorporates standalone and self-contained closed-loop water systems. These operate as secondary water circuits, thereby isolating the plate exchangers from the plant’s primary cooling water supply.
Beneficially, these separate closed-loop circuits also allow fertilizer plant operators to regulate water quality and temperature before allowing it into the cooling exchangers. In doing so, the system maintains a steady water temperature profile without being affected by other operating conditions in the plant. A consistent cooling profile in the plate heat exchanger, in turn, helps ensure consistent fertilizer quality.
Closed-loop water modules operate on a standalone basis. This means fertilizer plant operators have access to completely independent systems that do not require any additional plant instrumentation. Importantly, such systems do not take water from other plant circuits. Neither do they load cooling towers with returning warm water. Instead, the heat load of returning cooling water is removed via one or more standalone cooler units. Meanwhile, the water is consistently clean and doesn’t require make-up supply.
In cases where the process requirements for the finished product temperature are close to ambient, plant operators can also include chillers in their water temperature control modules. The circulation of output water through the chillers provides a boost to cooling capacity, when needed, helping to maintain circulating water temperature. The cooled water, once it reaches the regulated temperature, is then sent back into the module and eventually the exchanger.
Chillers offer plant operators two benefits: they eliminate the need to supply additional cooling water and avoid placing extra heat load on the plant’s cooling towers. Everything is instead maintained within the closed-loop system.
Additionally, these combined systems are both flexible and efficient. Chillers only operate when needed – during the summer months, for example. This allows systems to operate using the existing plant-supplied water during the rest of the year, thereby saving on energy costs.
Closed-loop systems, due to their zero losses, can also run with the same circulation water for years.
Operational & energy cost savings
The energy required to operate plate-based vertical heat exchangers is significantly less than that of traditional fertilizer cooling equipment. Fluid beds, for example, typically require two powerful large horsepower fans: a forced draft fan to supply air to the cooler; and an induced draft fan following the scrubber. The air chiller and air pre-heater in fluid bed systems also draw additional energy.
With plate-based vertical heat exchangers, in contrast, the cooler itself places only a small additional energy load on the plant’s existing cooling water system. The associated cooling water pump, bucket elevator and purge air system, meanwhile, all have low horsepower requirements.
Compared to a fluid bed system, plate-based vertical heat exchangers operate at high thermal efficiency with a large capacity of up to 150 tonnes/hour in a single cooler. This reduces energy costs by 90 percent and typically saves 4-5 kWh/tonne.
The above calculation is based on typical operational power requirements of 1,040 kW for a fluid bed cooler for a 3,600 t/d urea plant on the US Gulf Coast. That compares with an equivalent 85 kW requirement for a Solex cooler. (The load for the fluid bed cooler is an average based on mean monthly day and night ambient conditions.)
The operating costs of plate-based vertical heat exchangers are further reduced due to the ease of cleaning and the simplicity of system maintenance. Large hinged doors on the back of the cooler give full access to the plate banks. These are configured to enable easy access for inspection and cleaning.
Cleaning is carried out by washing with water and drying with a counter-current of warm air. The exchanger can typically be washed and dried within an eight-hour period, easily fitting within a normal plant maintenance schedule.
Their design also makes it possible for single plates to be isolated or replaced, if required. Overall, operating such a simple system with so few moving parts generally minimises maintenance requirements.
Installation cost reduction
Capital costs associated with the installation of plate-based vertical heat exchangers are also lower as they eliminate the need for air-handling equipment such as fans, air conditioning units (cooling and heating), and scrubbers, as well as ancillary equipment – particularly the large-diameter ducting used to accommodate the high volume air flows necessary with other cooler types. The cooling water circulating skid that is required is relatively small and not particularly costly.
Usefully, because of their vertical configuration, plate-based heat exchangers are both compact and modular in design. This makes them easy to integrate into existing plants, and therefore ideal for revamp projects and plant de-bottlenecking/capacity increases. Furthermore, this modular design allows additional heat exchanger plates to be added easily to the existing stack, if and when increased cooling capacity is required in future.
While the final capital cost of any project is subject to many variables, several case studies have demonstrated that, in general, the installation costs of plate-based indirect cooling systems are at least 30 percent lower than those of fluid-bed cooler installations.
Maintaining product quality
It is important to ensure, whenever production output is raised, that product quality also remains high. Plate-based vertical heat exchanger technology, compared with conventional rotary drum and fluid-bed fertilizer coolers, offers several advantages in this respect – as they can help improve product quality while also reducing plant emissions.
Ensuring that products are stored and packaged at the correct temperature is an essential part of successful fertilizer production. In particular, elevated temperatures need to be avoided as, given the hygroscopic nature of fertilizers, they can quickly translate into caking during subsequent storage, packaging and bulk transportation. Caking, by compromising product quality, ultimately results in lower sales price and dissatisfied customers because of the associated product breakage and handling difficulties.
Ensuring sufficient cooling in the fertilizer plant and the proper control of product temperature can require the installation of additional coolers at granulation plants, or the inclusion of cooler units at prilling plants.
Urea prilling plants operating at their original design capacity rely on the original prilling tower design, for example, rather than a separate cooler, to cool prills to an acceptable storage temperature. That situation can change, however, when plant capacity is increased. That’s because the built-in cooling capacity of the prill tower is essentially fixed by the original design (e.g. height of the tower). An additional fertilizer cooler is therefore required to deal with the increased capacity (Figure 2).
Conventional fertilizer cooling technologies present a number of challenges when retrofitting an existing plant to increase production. Typical fluid bed or rotary drum cooler types, for example, employ large volumes of air blown directly through or across the product, as touched on earlier.
Plate-based heat transfer technology, in contrast, being based on indirect cooling, eliminates the need for large volumes of process air and therefore subsequent costly cleaning by scrubbing systems. Instead, the fertilizer flows under gravity through the cooler at the most suitable velocity, as determined using customised thermal modeling software. This ensures that the fertilizer’s residence time within the cooler – typically 10-15 minutes – is sufficient and provides even cooling.
Based on process requirements, sophisticated modelling software calculates the correct product velocity and residence time from a range of parameters including the fertilizer’s bulk density, specific heat, thermal conductivity, input temperature and flow rate. The modeling also accurately predicts how long prills or granules need to stay within the fertilizer cooler, and determines the plate spacing required to reach the desired discharge temperature.
The product’s flow rate through the exchanger is controlled using a mass flow discharge device. Fertilizer solids move through the cooler in a laminar flow pattern. The absence of any mechanical handling of particles makes the cooler ideal for soft and friable fertilizer grades.
Test results have shown that no measurable quantities of fines are generated by the product as it flows through the cooler. Indeed, the slow movement of material and gentle product handling avoids product degradation, abrasion and dust formation – the end result being the delivery of a high-quality final product.
The uniform flow of solid materials as they pass through a plate-based vertical heat exchanger, when combined with residence times, ensures an even product temperature profile at the discharge. It is these advantageous design characteristics that enable Solex fertilizer coolers to guarantee remarkably stable and uniform final product temperatures.
About the author
Igor Makarenko is Global Director, Fertilizer, with Solex Thermal Science, a Canadian-headquartered pioneer in bulk solids thermal exchange. Over the past 30 years, the company has installed more than 600 advanced heat exchangers in more than 50 countries worldwide with applications such as fertilizer, oilseeds, sugar and industrial materials.