Nitrogen+Syngas 372 Jul-Aug 2021
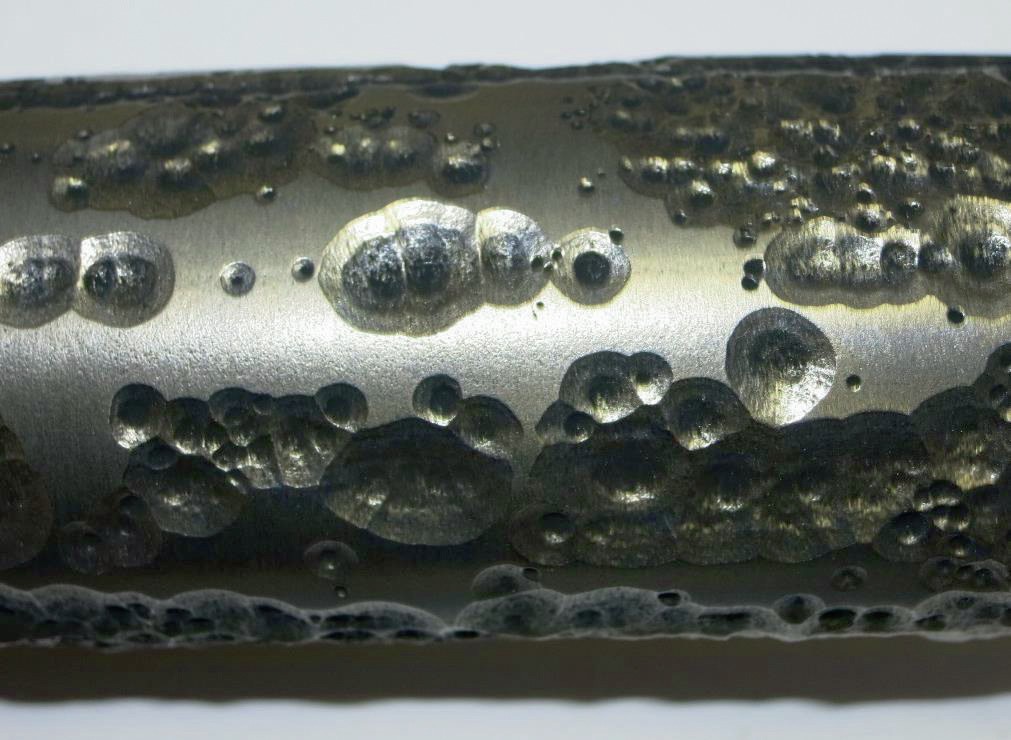
31 July 2021
Intelligent material design
METAL DUSTING
Intelligent material design
T. Hentrich and B. Nowak of VDM Metals provide an overview of the development of VDM® Alloy 699 XA, a new generation, metal dusting resistant alloy, available in a wide range of product forms, for demanding applications in the chemical process industry.
Pressure equipment such as vessels, piping and their accessories, assemblies and other safety equipment is strictly regulated throughout international markets. In addition to achieving certification for the quality assurance system in compliance with the European Pressure Equipment Directive (97/23/EC), these requirements have also helped to gain a deeper understanding of customers’ needs through the material development process for all product forms and probably following the production steps too.
As an integrated manufacturing producer VDM keeps all major production steps in-house – a vital prerequisite for a robust and stable manufacturing process, based on the knowledge that the quality and safety of construction goes back to the metallurgy and even beyond, to management and quality of raw materials. The results of these efforts are: maximum purity, homogeneity, reproducibility and optimum further processing characteristics of metal products.
VDM Metals offers high performance materials in the main semi-finished product forms plate, sheet, strip, rod, bar, wire and additionally as powder. These various product forms exhibit excellent fabricability into vessels, heads, trays, tubes, pipes, fasteners, fittings and flanges, etc. which are subsequently manufactured into the different pieces of equipment required by the chemical industry as pressure vessels, reactors, columns, heat exchangers and filters.
The constantly increasing requirements of the petrochemical industry regarding efficiency demand the application of new materials in diverse product forms. The big challenge is the combination of high-temperature corrosion resistance and workability. Workability is an important factor, not only for end-users in case of maintenance work, but also for material producers for further processing because availability on schedule is also an important “material property”. Additionally, due to the global trend for CO2 reduction or neutrality by production processes in the chemical process industry, an intensification of production conditions to achieve greater process efficiency causes an occurrence of different corrosion types.
For many years, customers in the petrochemical industry have reported a particular problem in their plants, known as metal dusting. This type of corrosion occurs, for example, in hydrogen, ammonia, methanol and synthetic fuel production plants. For affected companies, metal dusting typically results in increased maintenance costs or running processes less efficiently.
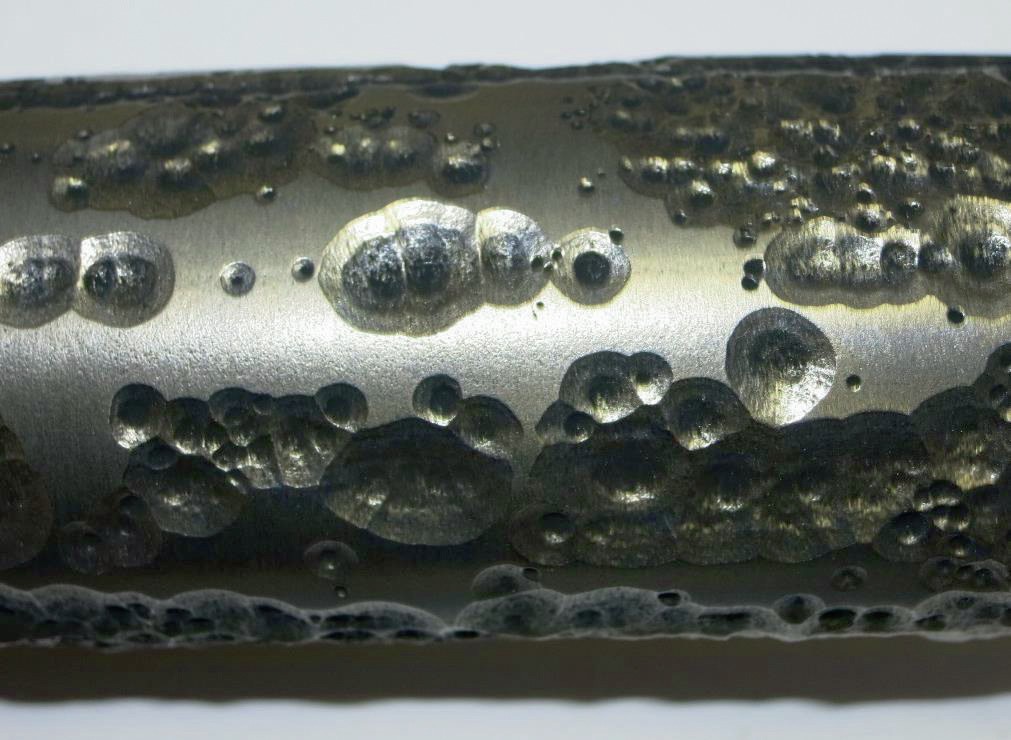
Metal dusting can be highly detrimental. It is a high-temperature form of corrosion damage in iron, nickel or cobalt alloys, which are exposed to a carbon-bearing atmosphere with a carbon activity greater than one (i.e. mixtures of CO, H2 , H2 O and CO2 ) typically between 500°C and 800°C. CO from the gas atmosphere reacts at the metallic surface to form atomic carbon, which diffuses into the metal. The metal supersaturates in carbon and decomposes into a mixture of graphite, carbidic, oxidic, and metallic particles (“metal dust”). The corrosion attack takes place by the formation of pits (see Fig. 1), but general attack is also possible.
In many traditional designs, the process parameters that could lead to metal dusting were avoided due to safety requirements as well as the lack of “ideal” material for these applications. “Ideal” material means a good combination of corrosion resistance, creep properties and workability (possibility to produce seamless tubes as well as good weldability). A well-balanced chemical composition is crucial for achieving this combination of properties.
A lot of research work has already been done in order to understand the influence of the chemical composition of wrought alloys on resistance to metal dusting1 . It is related to the ability of the alloy to form a protective oxide scale on its surface that should be dense enough to delay the diffusion of carbon. Therefore, a high Cr, Al or Si content improves the resistance of an alloy against metal dusting. Reducing the Fe content is also beneficial.
However, a high Si content could decrease weldability properties.
Furthermore, the influence of the microstructure and the surface conditions and treatment such as machining, pickling and grinding on material behaviour under metal dusting conditions was investigated and reported as important influencing parameters2 .
The workability of new and existing alloys is also important. In some applications, it is required to use seamless tubes and/or complicated thick wall welded constructions. For these needs, it is important to assure good hot and cold workability. Expansion and extrusion processes during tube production involve high temperatures and high strain rates. It is therefore crucial that alloys show good ductility at high temperatures. Generally, tube production also includes a metal working process with high deformations at room temperature, such as cold pilgering. New alloys must therefore withstand the required deformations without failure.
The design and control of the whole tube manufacturing route, hot and cold forming processes, solution annealing treatment, finishing operations and inspection procedure, is essential to obtain final tubes with an optimised microstructure and surface quality, which guarantees the optimal mechanical, oxidation and corrosion properties. In this sense, it is very important to achieve a microstructure free of undesirable precipitates, with an adequate and homogeneous grain size, and to avoid depletion of these chemical elements that enhance metal dusting resistance, such as Cr and Al, at the tube surface.
Good weldability under argon is a necessary property for the realisation of complex constructions, but also for additive manufacturing processes (new parts or repair jobs).
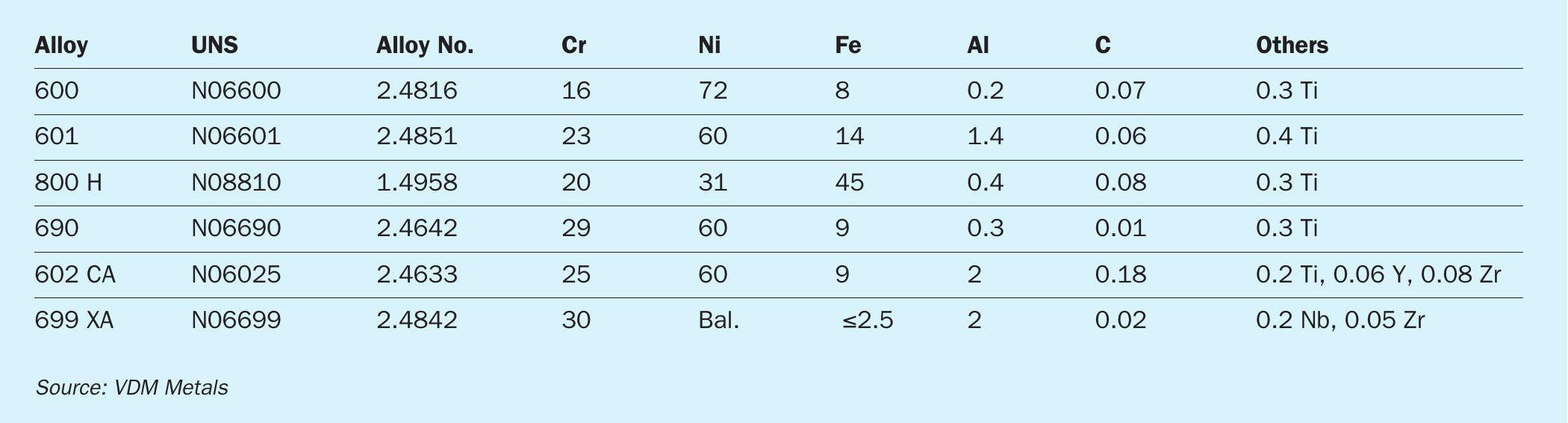
Based on the abovementioned aspects and wide material expertise, VDM Metals started the development of a new alloy especially for application under metal dusting conditions. In addition, benchmark alloys for each requirement were determined and used to compare the results achieved during the development process. In order to meet the needs of its customers the following requirements for alloy development were defined:
- higher metal dusting resistance than Alloy 602 CA;
- creep strength at least as good as Alloy 601;
- room temperature ductility better than Alloy 602 CA, in the range of Alloy 601 to produce seamless tubes;
- good weldability (under argon) similar to Alloy 601.
Table 1 shows the nominal composition of tested alloys in weight percent.
In 2012, a patent application (author: Dr H. Hattendorf, from VDM Metals R&D department) was finally filed for a new type of nickel-based alloy with approx. 30% Cr, 2% Al and less than 2.5% Fe.
In 2013, the laboratory phase for the new material Alloy 699 XA was successfully completed. The improved metal dusting resistance of the new alloy was experimentally confirmed by a significantly longer incubation time, i.e. the period until the first pit attack by metal dusting.
Further optimisation and the necessary preparations for large-scale tests followed. In 2015, the first large-scale batch was melted, from which tube feedstock and forged bars, sample sheets of various thicknesses and welding rods were produced at VDM Metals. In 2016, seamless tubes made of VDM® Alloy 699 XA were successfully produced at Tubacex in Spain.
Tubacex Group, as a leading multinational company devoted to the production of seamless tubes in stainless steel and high-nickel alloys, is constantly working on improvement of technological processes and product quality. This approach helps customers from different industry areas to meet strongly increasing process requirements. Due to their chemical compositions with a high content of nickel, chromium and aluminium to impart superior characteristics, high performance materials, such as Alloy 699 XA, are more complex than standard stainless steels to process. Tubacex Group possesses long-term experience in manufacturing tubes of special alloys and assures a robust production process. During the most critical steps on the tube production route, such as piercing, extrusion, cold-pilgering and solution annealing, the required process parameters are carefully defined and controlled.

Both the strict control during the manufacturing process and the optimisation of the final surface quality, guarantee high-quality Alloy 699 XA tubes with successful performance in service.
The main goal of this development was the design of an alloy that is highly resistant to metal dusting. The methodology and detailed sample description of the metal dusting test rig at Netherlands Organization for Applied Scientific Research (TNO) in Eindhoven has been reported in previous papers3,4 .
A temperature of 600°C was chosen to investigate corrosion resistance, since at this temperature the metal dusting attack is most severe. In order to test material performance at close to industrial conditions, and due to the understanding that the total pressure has a significant effect on the severity of the metal dusting attack3 , a high pressure of 20 bar was used for the whole test duration. Long-term exposures were run using the so-called gas 2B (see Table 2). This is a gas with a high carbon activity used by TNO to rank very high metal dusting resistant alloys. The entire test conditions are more aggressive than expected in common industrial application in order to prove a worst case scenario. Moreover, customers’ exact process conditions are strictly confidential and cannot be used as an example for investigation conditions. After each exposure of about 125 hours the test was paused, the samples were cleaned ultrasonically, examined for pits and optical documentation was taken.
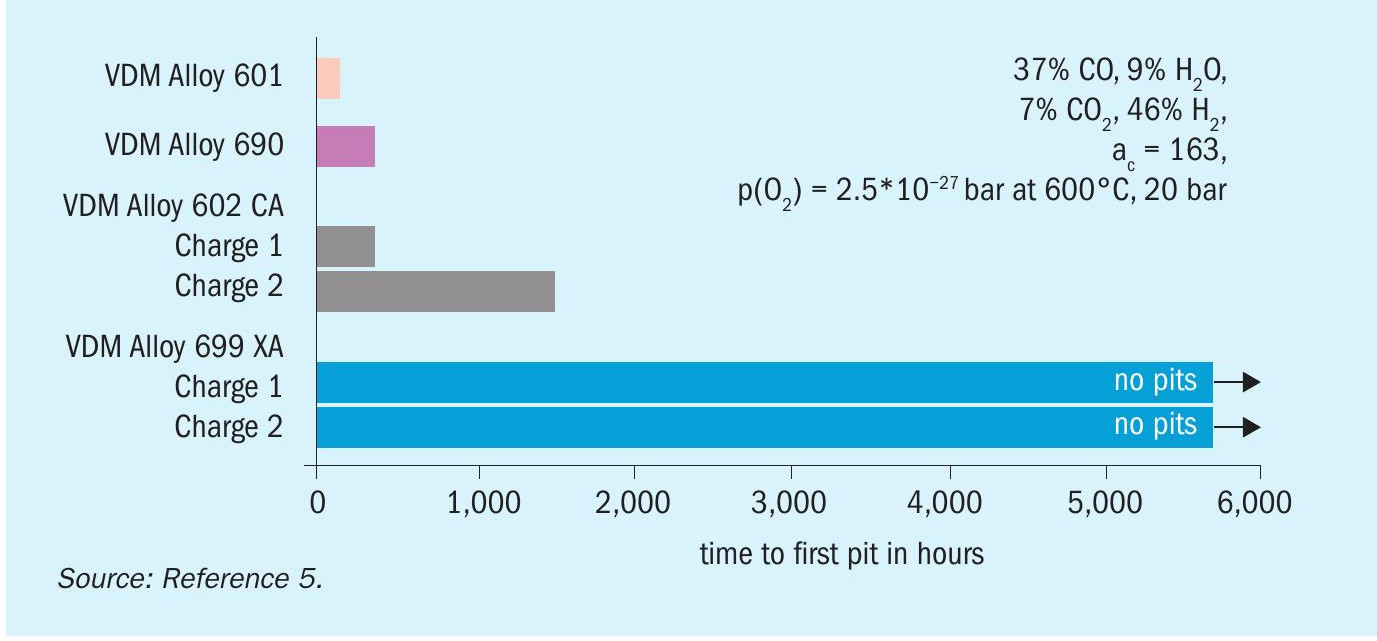
Fig. 2 shows the time to first pit, no matter where it forms (on the surface or edge of the specimen) for the different materials and Table 3 shows pictures of alloy samples after the appearance of the first pit or at the end of the exposure time5,6 . The sample of Alloy 601 shows many pits after the first test stop at 123 hours. The number of pits after this short time proves that this material is not suitable for use under severe metal dusting conditions due to a Cr and Al content that is too low and a Fe content that is too high.
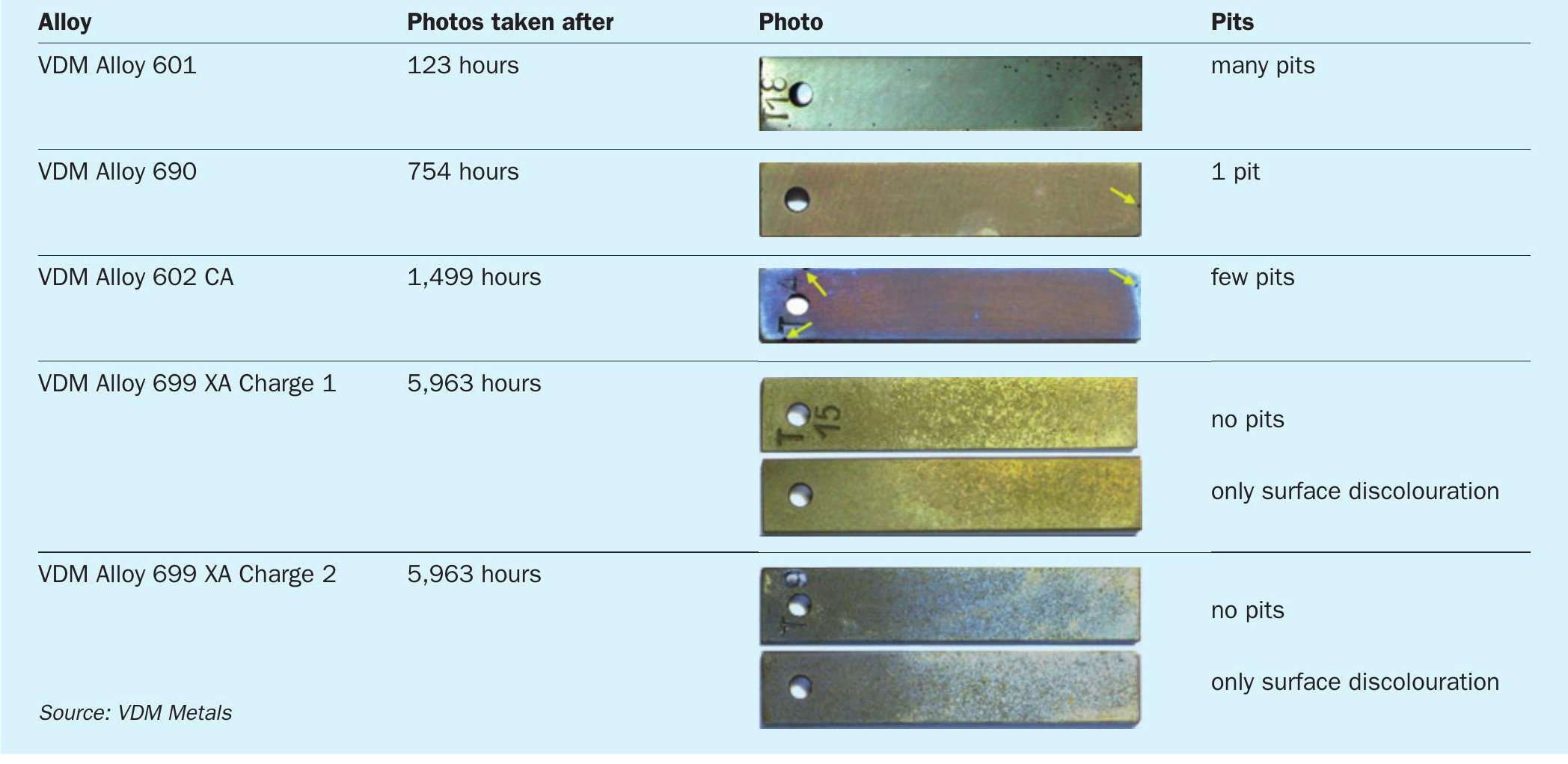
Alloy 699 XA, as a low Fe material with a Cr + Al content ≥30 wt-%, shows no pits and no attack on the surfaces or edges up to 5,693 hours (many different specimens with a slightly different chemical composition, but all within Alloy 699 XA specification were tested in the same experimental setup). Based on this remarkable test result, the goal of the first requirement “higher metal dusting resistance than Alloy 602 CA” was clearly achieved.
Mechanical properties
Balanced mechanical properties of the material over the whole temperature range is another important aspect for successful alloy application. Components as well as the whole construction should be able to withstand the thermo-mechanical load over the whole lifetime.
In general, high temperature mechanical properties compete against workability in metallic materials. All of the mentioned alloys in this article are wrought or rolled alloys and undergo cold and/or hot deformation treatment during production. During the deformation process some small defects after melting and remelting like pores are closed and hence beneficial microstructures and homogeneous grain sizes are realised. This is only possible if the deformation of the material is feasible without cracks or damage due to its too high mechanical strength and low ductility at room as well as high temperatures. While the focus for the development of most wrought Ni-base alloys has generally been on processing properties such as workability and weldability, the development of materials that are highly resistant to creep for very high temperature application (close to the alloy melting point) has primarily concentrated on end-part performance. Consequently, some manufacturing steps such as production of seamless tubes are not available, for example, for wrought Alloy 602 CA. These factors were the main drivers when defining the requirements to meet the balance between mechanical properties and workability:
l usability of a new material;
l creep strength at least as good as Alloy 601;
l room temperature ductility better than Alloy 602 CA, in the range of Alloy 601, to produce seamless tubes;
l good weldability (under technical pure argon) similar to Alloy 601.
The most important mechanical characteristic for application in CPI at high temperature is creep resistance. Non-interrupted uniaxial creep tests in tension with strain measurement were done on solution annealed samples from a forged bar for Alloy 699 XA. Creep tests on annealed tubes of Alloy 699 XA were also performed during the alloy development project. For the reference alloys, Alloy 601 and Alloy 600, interrupted creep tests were carried out on samples from solution annealed hot rolled plate.
The data on Alloy 699 XA, Alloy 601 and Alloy 600 were analysed according to the Larson-Miller approach. C=18 was used in the Larson-Miller parameter P based on data for Alloy 602 CA.

In Fig. 3 lines are shown for the mean value, the mean value –20% and the mean value +20%. Fig. 3 confirms, that the second requirement “creep strength at least as goo as alloy 601” has been achieved.
Another important aspect are mechanical properties at room temperature due to its influence on production processability. For Alloy 699 XA, tensile tests were performed at room temperature on bar and plate as well as on tube. All samples were solution annealed. The ranges of the results are shown in Table 4. This shows that the third requirement “room temperature ductility better than Alloy 602 CA, in the range of Alloy 601 to produce seamless tubes” has been achieved.
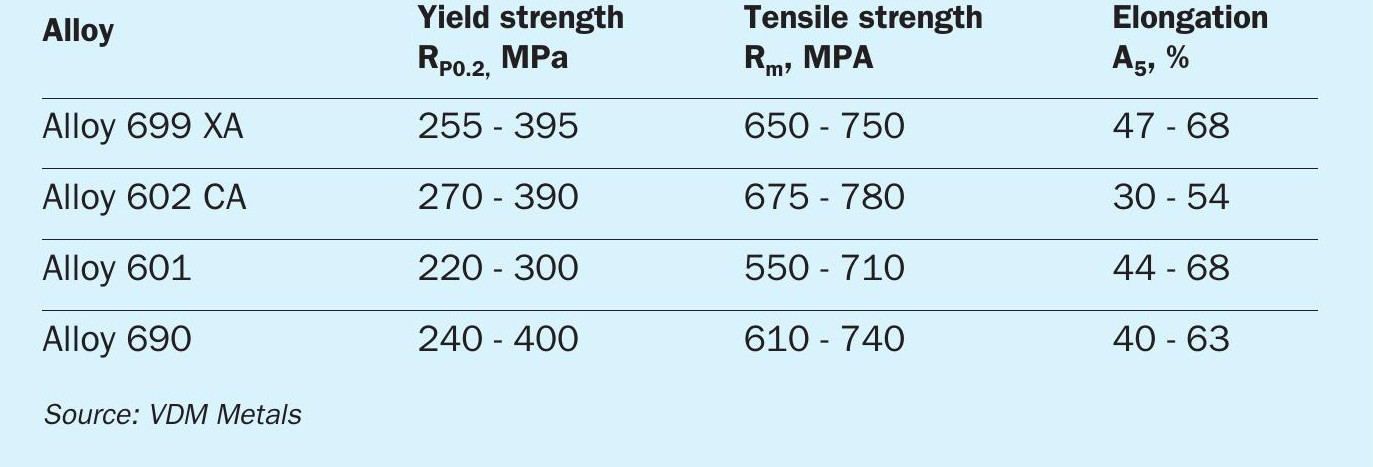
For the successful introduction of a material into the market, the weldability of an alloy is an essential requirement for complex parts and in case of repairs.
Plates of Alloy 699 XA of 16 mm thickness were welded with gas tungsten arc welding method (GTAW) with 2.0 and 2.4 mm rod under argon using matching filler metal. Afterwards a welding procedure test according to DIN EN ISO 15614-1 was successfully performed. Fig. 4a shows a macroscopic picture of the weld and Fig. 4b a microstructure of the weld, i.e. the heat-affected zone can be seen. Hence, also the fourth requirement “good weldability under argon” was also achieved.
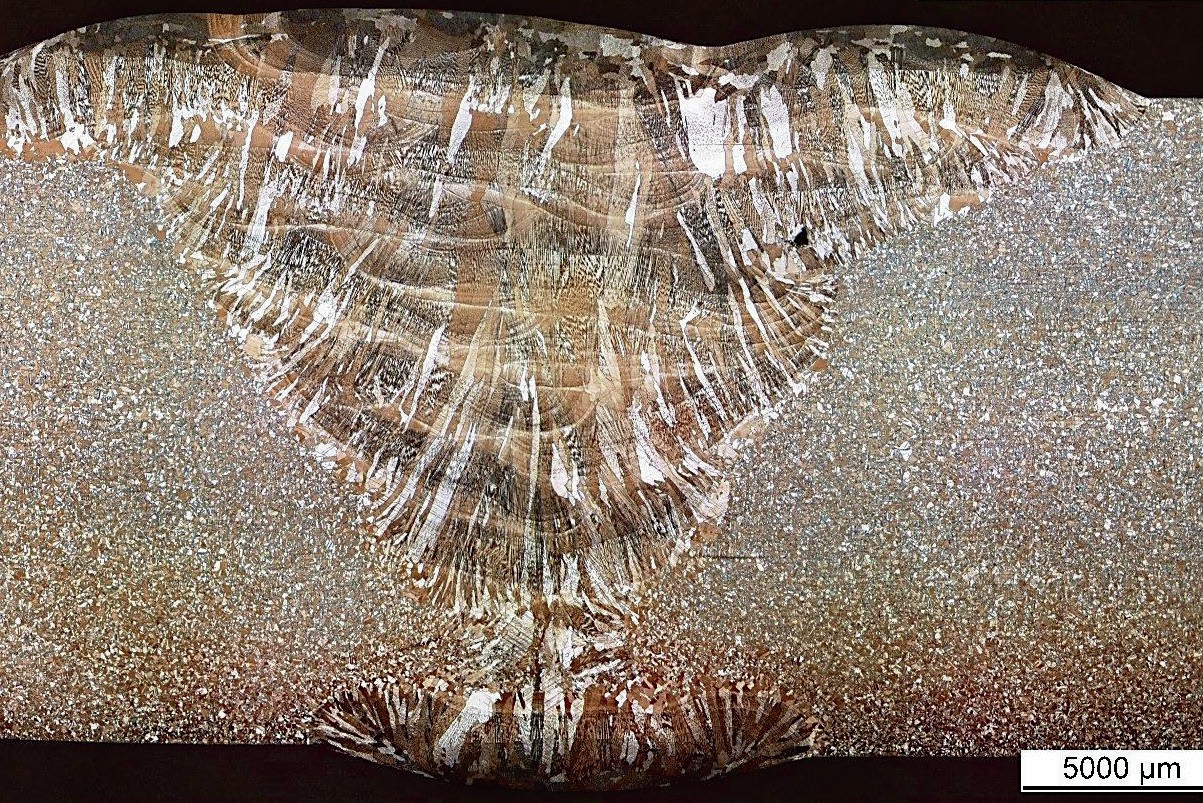
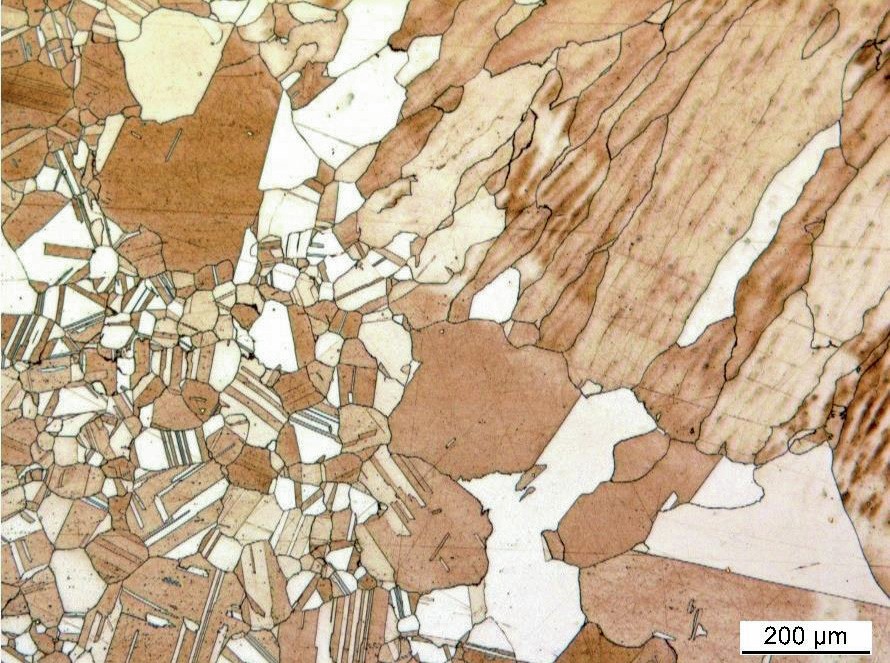
Alloy 699 XA for additive manufacturing (AM)
Since Alloy 699 XA shows an excellent combination of high temperature corrosion resistance and weldability, this alloy should be considered as ‘ready-to-use’ for AM. During a current powder project outstanding results were achieved: crack free, as well as uniform microstructure, even in complicated design parts, and good mechanical properties in an as-built condition, as well as in annealed condition (see Fig. 5).
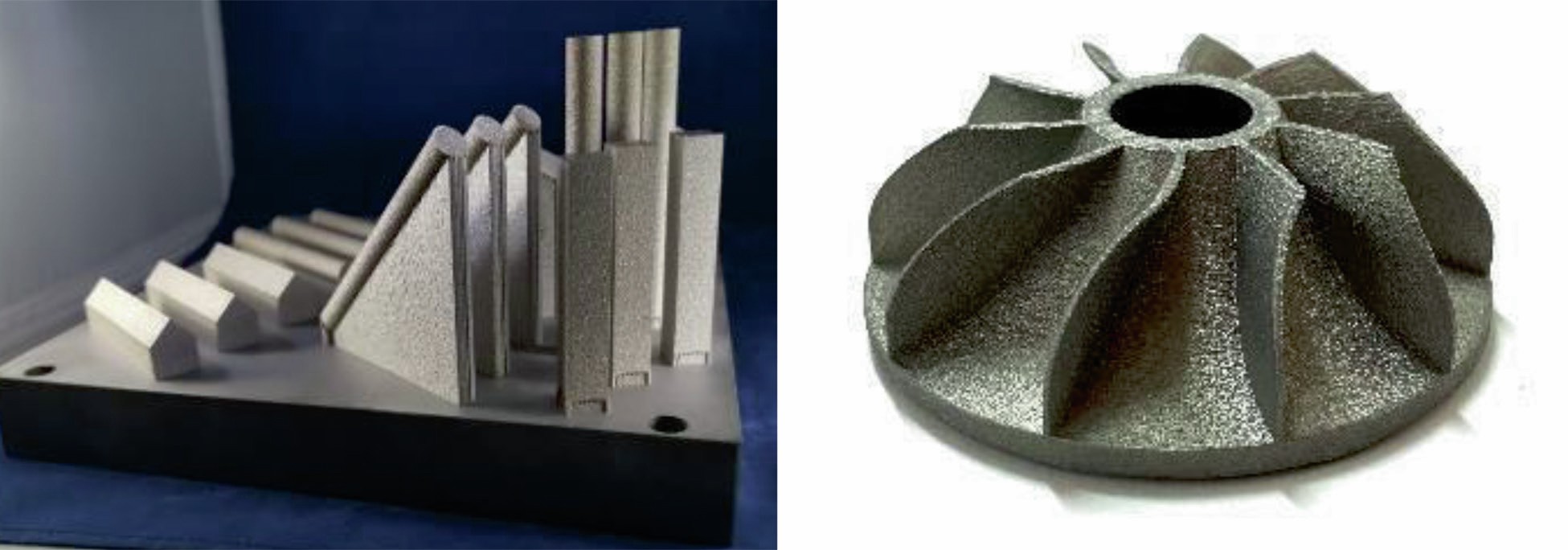
Acknowledgement
The authors thank Dr Heike Hattendorf for alloy development, endless technical discussions as well sharing passion and inspiration.
References