Nitrogen+Syngas 372 Jul-Aug 2021
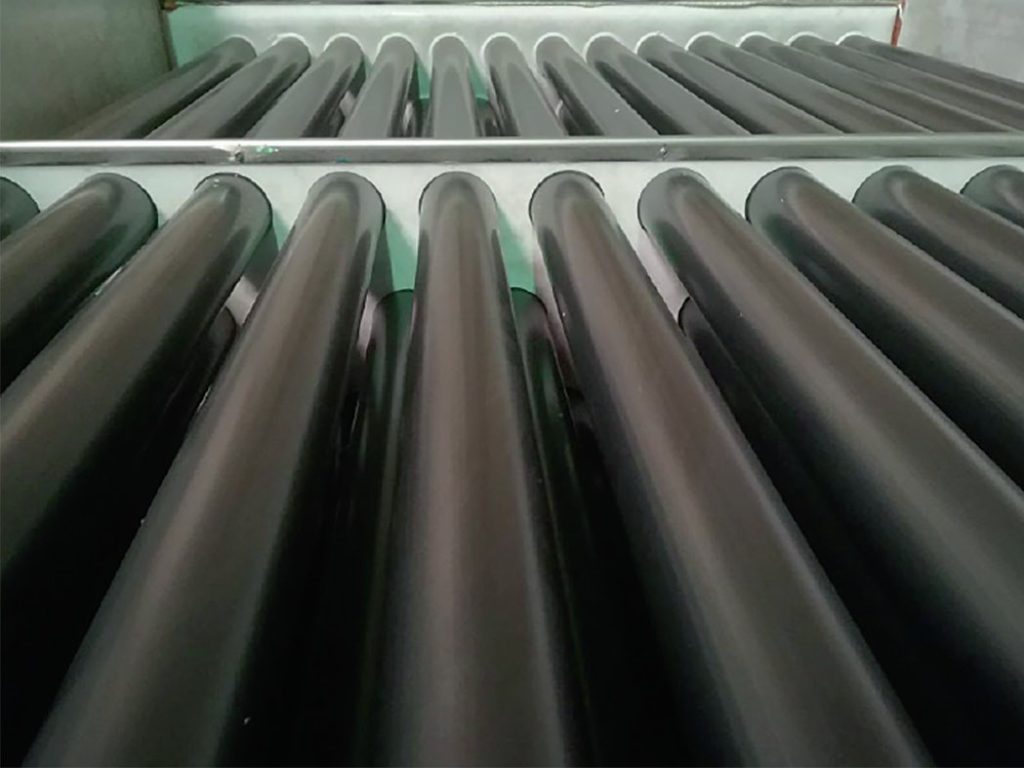
31 July 2021
New heat exchanger allows operation below the acid dew point
HEAT RECOVERY AND CO2 EMISSIONS
New heat exchanger allows operation below the acid dew point
To comply with stricter stack emission obligations, industries are required to recover more heat from flue gas and to clean it before it can be discharged into the atmosphere. J. Kitzhofer of APEX Group discusses the challenges and limitations of the majority of current heat recovery systems and reports on a new family of acid resistant tubular and plate-type heat exchangers developed by APEX Group that overcomes these problems. The new heat exchangers are resistant to dew point corrosion. The heat transfer elements are constructed from an acid resistant polymer composite with high thermal conductivity, allowing the design of new trouble-free heat recovery systems and the upgrade of existing systems to meet heat recovery and stack emission targets.
The current penalties imposed on greenhouse gas emissions are incentivising various industries to recover more heat from the flue gas and to clean it before it is discharged into the atmosphere. Heat recovery typically aims to increase the overall efficiency of the process by preheating the combustion air, which has a direct effect on reducing harmful emissions by reducing fuel consumption. Lowering the flue gas temperature is also an important factor for the overall efficiency of flue gas cleaning systems.
Industries have introduced new processes and are improving existing techniques at an accelerated pace with the objective to achieve clean air for a green environment for present and future generations. Industries which rely on fossil fuels have not been exempt from these developments. Although those industrial processes are already highly optimised for the reduction of emissions, there is still room for improvement. One area for improvement is the use of the remaining heat and the cleaning of the flue gas from hazardous components (e.g. SOx or CO2 ).
A key limitation in the use of heat coming from fired heaters is found in the heat exchanger, in between the fired heater and the stack, namely the air preheater. The maximum extractable heat from the flue gas is typically defined by the minimum heat transfer surface temperature maintained above the acid dew point of the flue gas. Air preheaters are sometimes operated below the acid dew point, causing corrosion issues. Precautionary measures can be taken to extend the lifetime of the air preheater on such occasions, such as through expensive glass or polymer coating techniques applied to its sensitive metallic parts. Constant operation below the acid dew point will however cause severe corrosion issues for economical heat exchangers constructed from metallic materials. Emerging technologies for cleaning the flue gas like wet flue gas desulphurisation (WFGD), mercury recovery or post combustion carbon capture require operating with flue gas temperatures below the acid or water dew point.
Constant operation below the acid or water dew point requires a heat exchanger constructed from acid resistant materials at an affordable cost. Polymers are a category of materials that offer resistance to acids. However, the drawback of most polymers is their low thermal conductivity and the consequent thin wall thickness required for efficient heat transfer. This drawback results in a lower mechanical strength of heat transfer elements. A polymer composite overcoming this drawback is PPS-GR.
Acid condensation and subsequent corrosion
Flue gas consists of many condensable components generated during the combustion of air/fuel mixtures, such as H2 SO4 , HCl, HF, H2 O, CO2 , SO2 . In combustion technology, the sulphuric acid dew point, which has the highest temperature of all these dew points, is traditionally known as the acid dew point.
All sulphur contained in the fuel is converted to sulphur dioxide gas during combustion in the presence of oxygen:
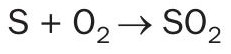
Only a small fraction of this sulphur dioxide is converted to sulphur trioxide. In the high temperature range, part of the sulphur dioxide reacts with atomic oxygen to form sulphur trioxide:
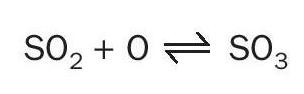
At lower temperatures, an additional part of the sulphur dioxide reacts with molecular oxygen to form sulphur trioxide:
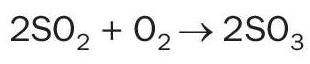
The conversion of sulphur dioxide to sulphur trioxide depends on many factors such as fuel sulphur content and composition, excess air, gas kinetics, combustion and mixing process, temperature and pressure in the system, flue gas residence time, presence of catalysts, soot, ashes, and other solid particles.

At temperatures lower than the acid dew point, sulphuric acid vapour starts to condense as sulphuric acid liquid on the surface or on nuclei. Different models for the prediction of flue gas acid dew point temperature have been reported in the literature based on empirical and semi-empirical correlations, experimental analysis, neural networks, numerical analysis, etc. The acid dew point is a function of the partial pressure of sulphuric acid and the partial pressure of water. A well-known correlation for H2 SO4 acid dew point is the one described by Verhoeff and Banchero.
Condensation of sulphuric acid
The flue gas enters the heat exchanger with a certain amount of sulphuric acid vapour at temperatures above the acid dew point. When the heat transfer surface temperature on the flue gas side drops below the acid dew point, sulphuric acid vapour condenses on this surface and builds a highly corrosive acidic film (liquid). Due to the condensation on the surface, the sulphuric acid vapour concentration of the flue gas decreases. The liquid film will grow over time. The rate of growth is dependent on the flow rate of sulphuric acid vapour, the capture efficiency of the heat exchanger and the material of construction of the heat exchanger. As soon as the flue gas bulk temperature falls below the acid dew point, sulphuric acid vapour starts to condense on solid particles (or nuclei) present in the flue gas, thus the condensation rate on the heat transfer surface decreases. A corresponding portion of sulphuric acid vapour remains in the gaseous state and is released as sulphuric acid vapour out of the heat exchanger. This is the portion of sulphuric acid vapour which determines the actual acid dew point of the flue gas at the heat exchanger outlet.
The lower the temperature of the condensate (attached to heat transfer surfaces or attached to solid particles), the more diluted the condensate is. Following the phase diagram for the binary mixture of H2 O-H2 SO4 the typical acid concentration of the condensate is in range of 80% H2 SO4 at the start of the acid condensation band down to about 50% H2 SO4 at the end of the acid condensation band.
Depending on the process operating conditions, the sulphuric acid vapour content entering the heat exchanger is divided into three distinct portions at the outlet of the heat exchanger:
- sulphuric acid liquid on the surface;
- sulphuric acid liquid on nuclei;
- sulphuric acid gas in the flue gas bulk stream.
Fig. 1 shows a typical metallic heat exchanger constructed from carbon steel which corroded due to the operation of the heat transfer surface at temperatures below the acid and water dew point. It has been observed in the field that carbon steel corrodes at a rather high corrosion rate in water-diluted acids. In such conditions, stainless steels show better performance; however, these materials also suffer greatly from corrosion due to attacks by sulphuric acid condensate at temperatures close to its boiling point at concentrations above 50 wt-%.
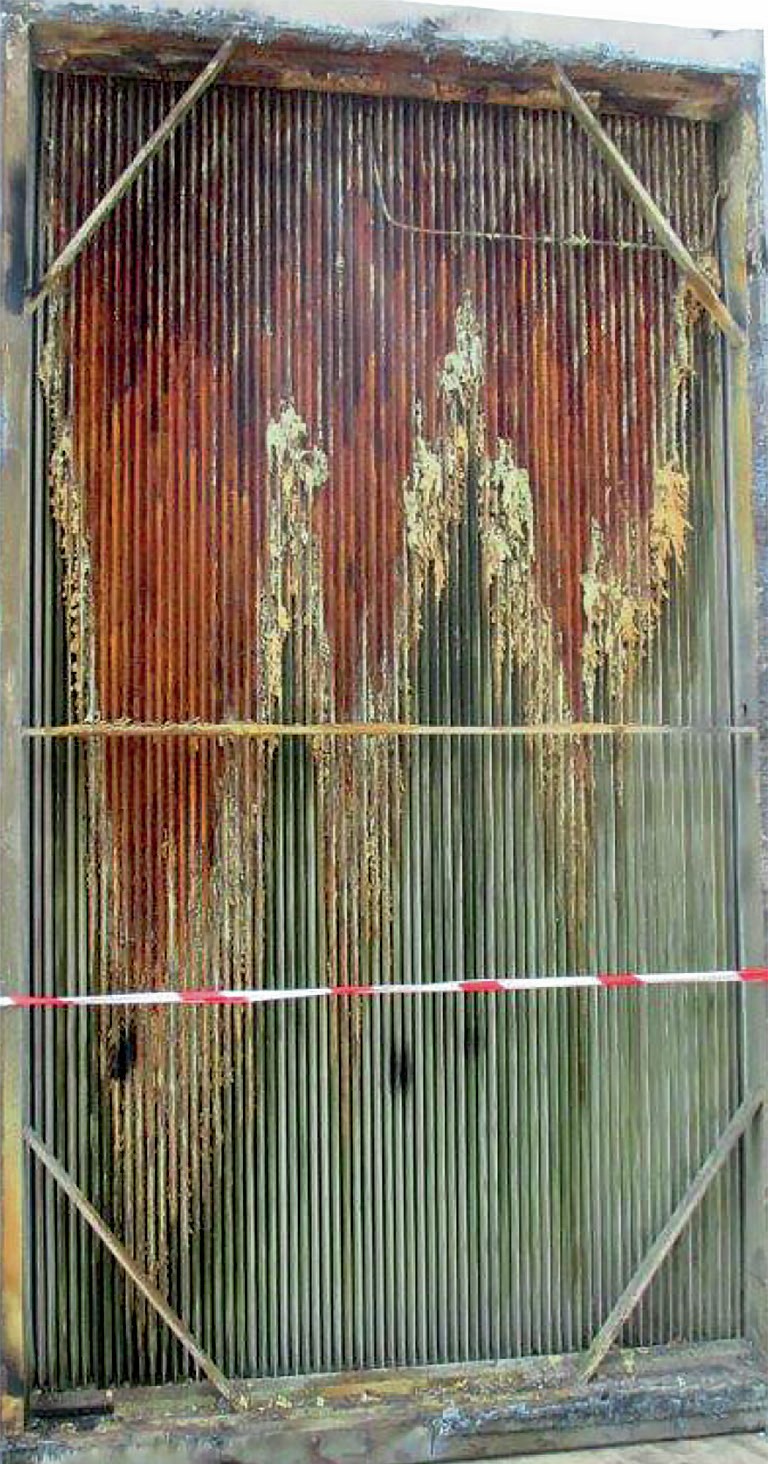
The solution
To operate heat exchangers under the previously mentioned harsh conditions, APEX Group has developed an acid resistant heat exchanger constructed from heat transfer elements made of a composite known as PPS-GR. The PPS-GR-made heat exchangers have been successfully tested in the field, in applications such as a water/gas heat exchanger in a waste incineration plant, a gas/gas heat exchanger in a heat recovery system of a steel mill plant and in a water/gas heat exchanger of a heat recovery system in a biomass power plant. The PPS-GR composite consists of 30% polyphenylene sulphide and 70% graphite (a heat conductive filler), and thus features the chemical attack resistance of polymers and thermal conductivity close to that of metals. Due to the high thermal conductivity of graphite, the heat transfer walls can be designed thicker in order to ensure better mechanical strength, while at the same time overcoming the thermal resistance of the polymer. The high thermal conductivity of the composite results from the special extrusion technology, which allows a controlled graphite flakes arrangement oriented in the direction of the heat transfer flux as shown in Fig. 2.
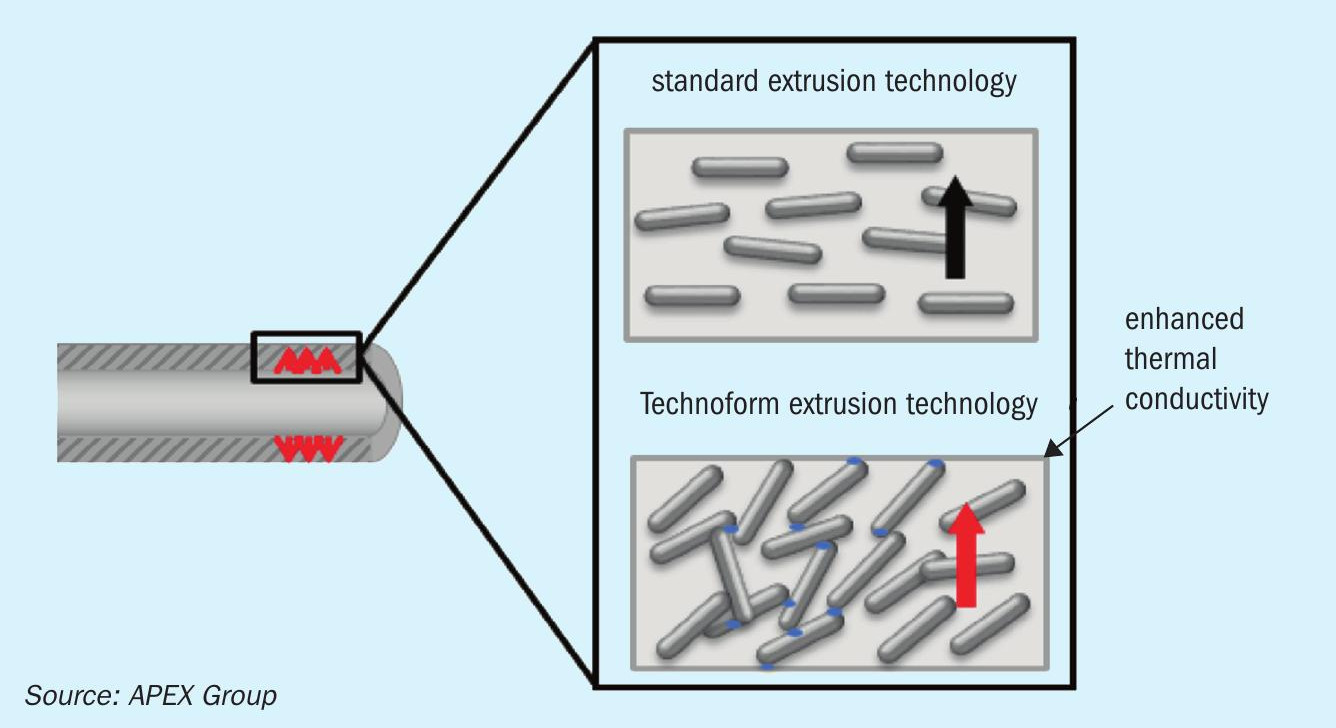
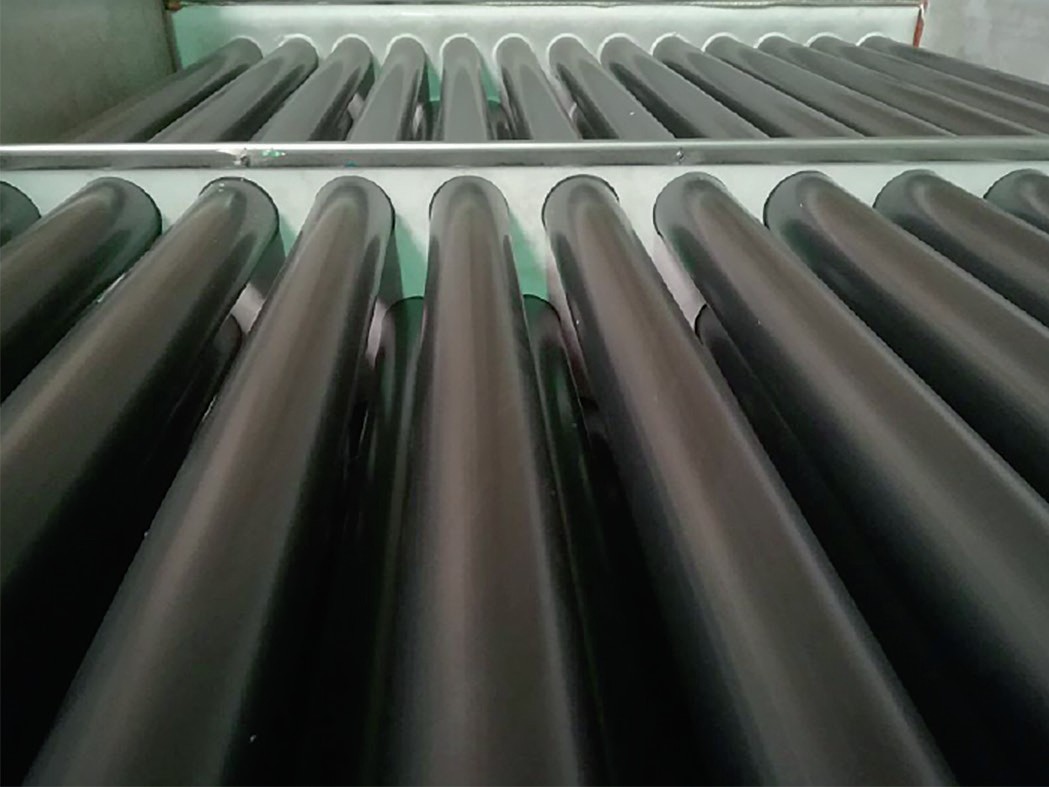
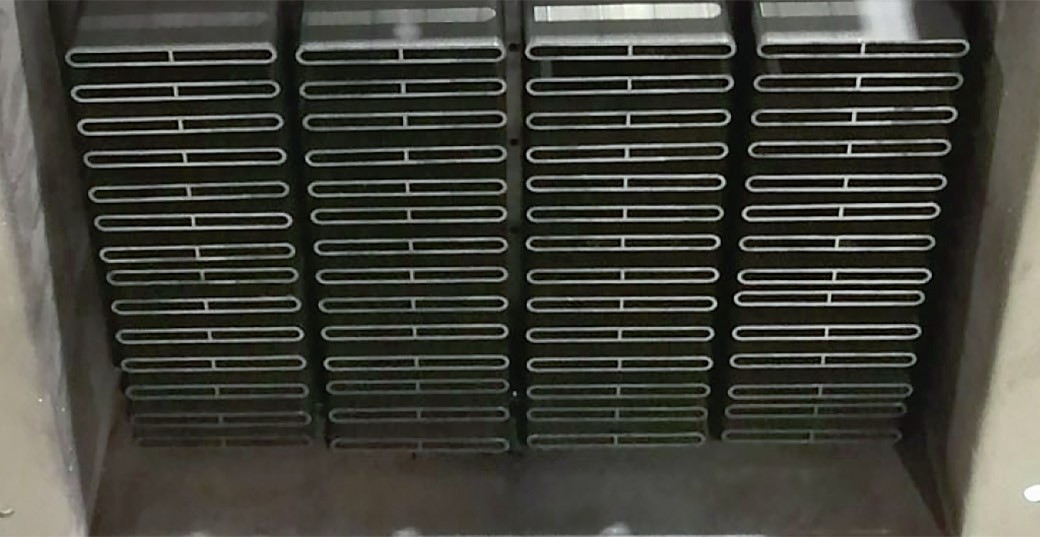
APEX Group has integrated the PPS-GR material into its tubular and plate-type heat exchanger, see Fig. 3.
The cross flow tubular PPS-GR heat exchanger (Fig. 3, left) is custom made and can be designed to the customer’s needs, e.g. in-line or staggered arrangement of tubes, variable tube diameters and variable tube lengths.
The plate-type PPS-GR heat exchanger (Fig. 3, right) is also custom made and provides an even greater flexibility in design. The heat exchanger can be arranged in cross flow, co-current or countercurrent flow (for highest thermal effectiveness), with variable process channel gaps and variable heat transfer plate thickness and dimensions. APEX Group’s well-known APEX® Free-flow Technology is integrated in the PPS-GR plate-type heat exchanger to provide operation with low fouling and low plugging tendency.
Applications
Air preheater for fired heaters
In industrial processes, heat exchanger systems are often applied as air preheaters for fired heaters, which constitute the process heart of oil refineries. For example, in syngas, ammonia, methanol and hydrogen plants, steam methane reformers (SMR) incorporate such air preheating systems. Due to the pre-heated combustion air, the efficiency of the combustion process is greatly increased. Overall, the installation of a heat exchanger as a part of a fired heater system considerably reduces the operational expenses (opex) and CO2 emissions due to a lower fuel consumption.
Fig. 4 shows three fired heater systems, with a variation in the stack temperature from 350°C to 90°C. The heat exchangers are traditionally designed to operate with minimum heat transfer surface temperature close to, but above the acid dew point (in the range of 120°C to 140°C, resulting in a stack temperature of about 150°C) to avoid condensation of H2 SO4 and as a result corrosion occurs on the heat transfer surface. Recently, driven by stricter stack emissions regulations, the air preheating system operators tend to further decrease the flue gas stack temperatures to as low as 90°C, to further increase the overall fired heater efficiency (e.g. 95.73% as shown in the example in Fig. 4) and to reduce the emissions. Flue gas temperature well below the acid dew point make the condensation of H2 SO4 on the heat transfer surface of the air preheater unavoidable. The solution to this problem can be the installation of the PPS-GR heat exchanger modules in the “cold end” of the (existing or new) air preheating systems, or as a part of any other flue gas heat recovery or cleaning system.
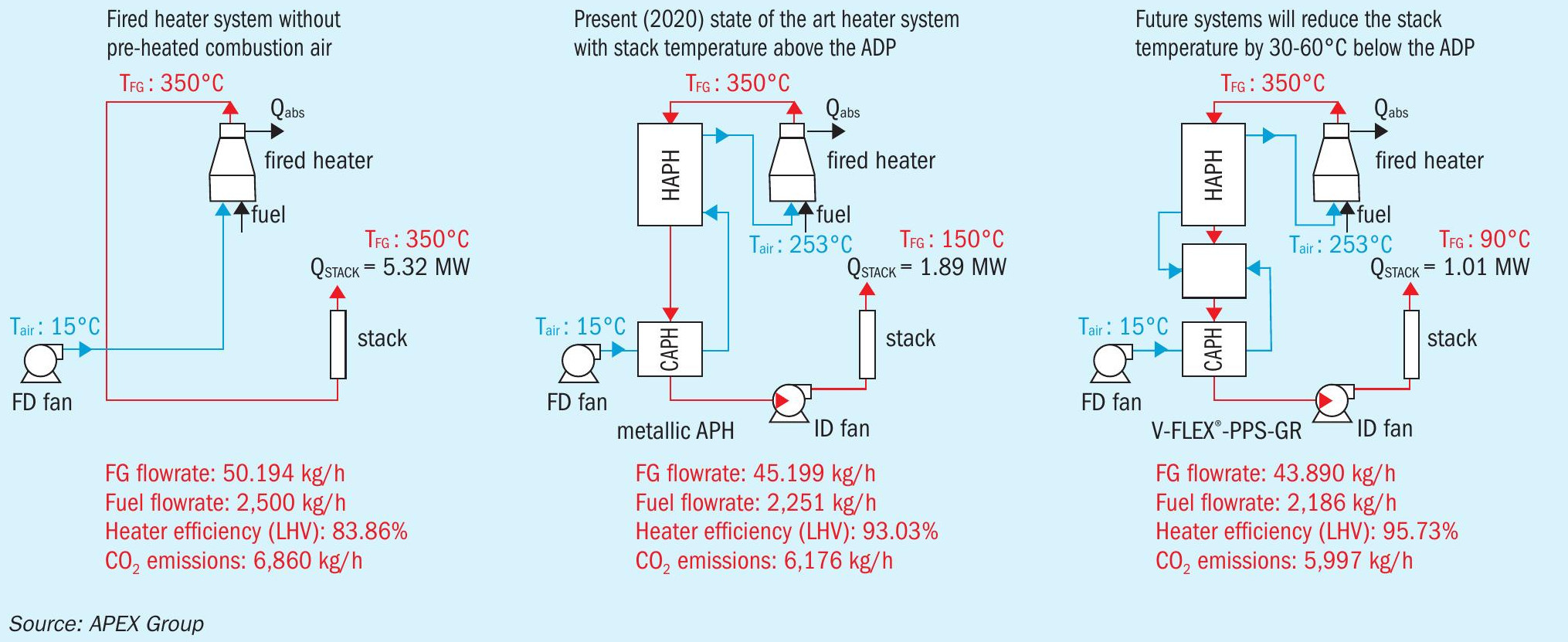
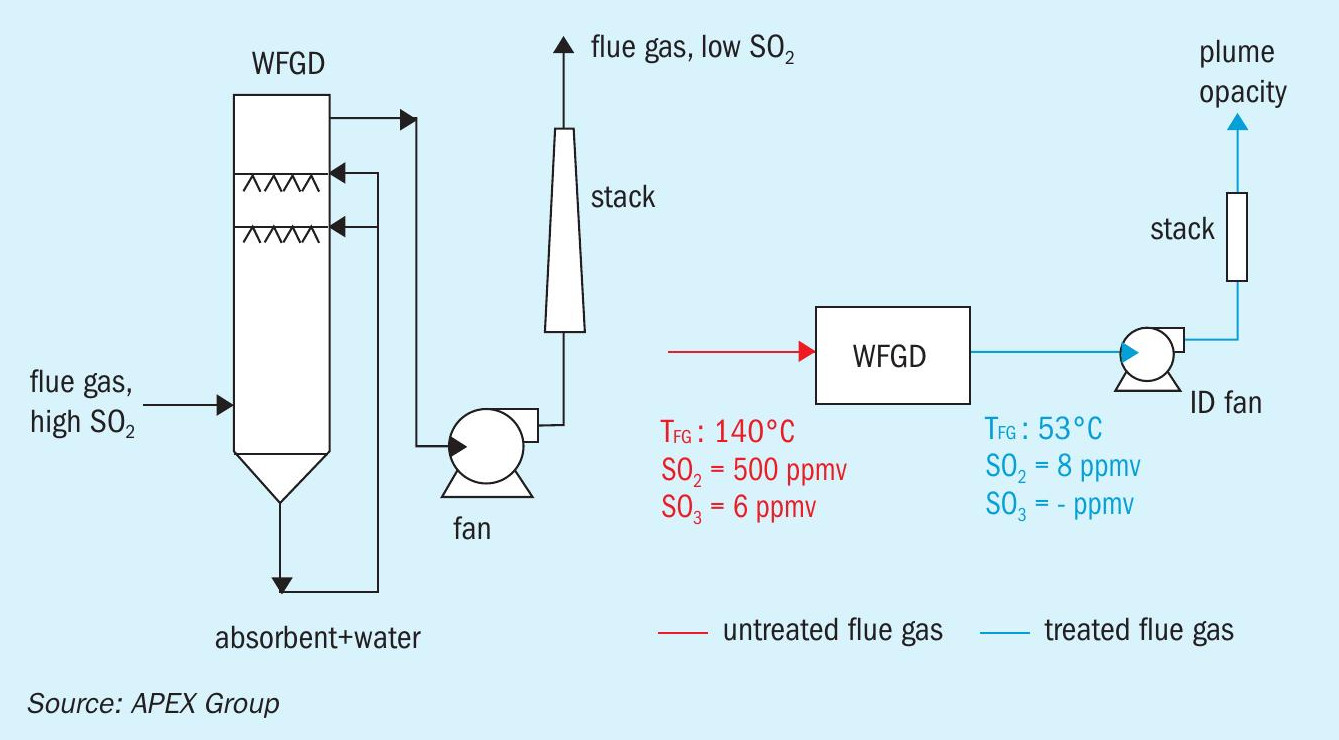
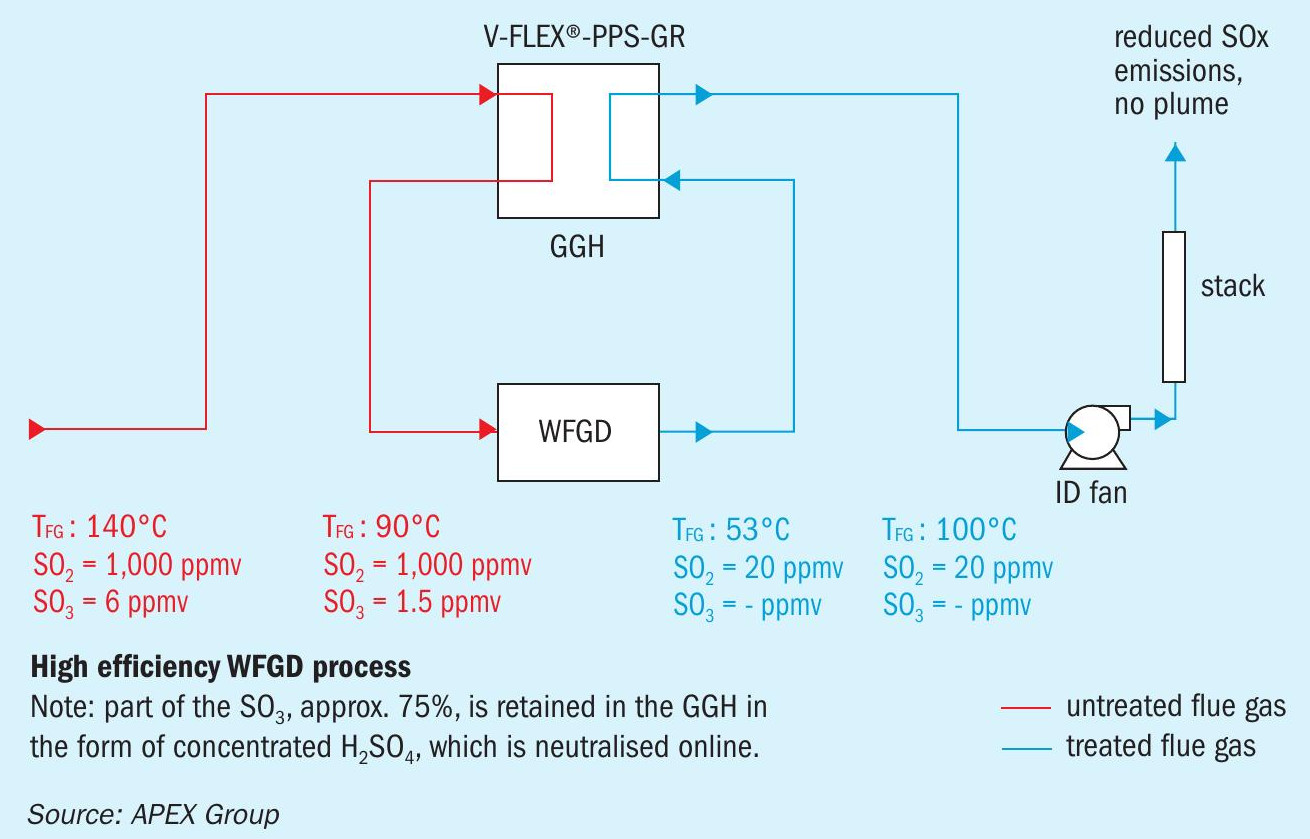
Gas-gas heat exchanger (GGH) for scrubbers
Scrubbers are used to clean the flue gas from harmful components such as Hg, CO2 , SO2 and to a lesser degree SO3 . Fig. 5 shows a wet flue gas desulphurisation unit for cleaning the flue gas from SO2 . Flue gas enters the scrubber at 140°C, above the acid dew point. Cleaning is performed by, for example, spraying a water-lime mixture, after which the flue gas with reduced SO2 content leaves the scrubber unit at 53°C.
Certain issues are known with this approach such as the required large water flow rate, formation of H2 SO4 mist due to rapid cooling and consequent flue gas super saturation which greatly limits SO3 /H2 SO4 retention in the system, and environmental restrictions with respect to the plume opacity.
The integration of a gas/gas heat exchanger made of PPS-GR composite overcomes these issues as illustrated in Fig. 6. A considerable amount of the SO3 /H2 SO4 can be retained in the PPS-GR heat exchanger and the temperature difference between the inlet and the outlet of the WFGD scrubber can be decreased, which supresses the formation of H2 SO4 mist in the WFGD scrubber itself. Furthermore, the temperature exiting the stack can be increased and thus plume formation can be eliminated. Additionally, the SO2 removal efficiency of the WFGD scrubber is increased due to the lower flue gas temperature entering the WFGD unit (Fig. 6).
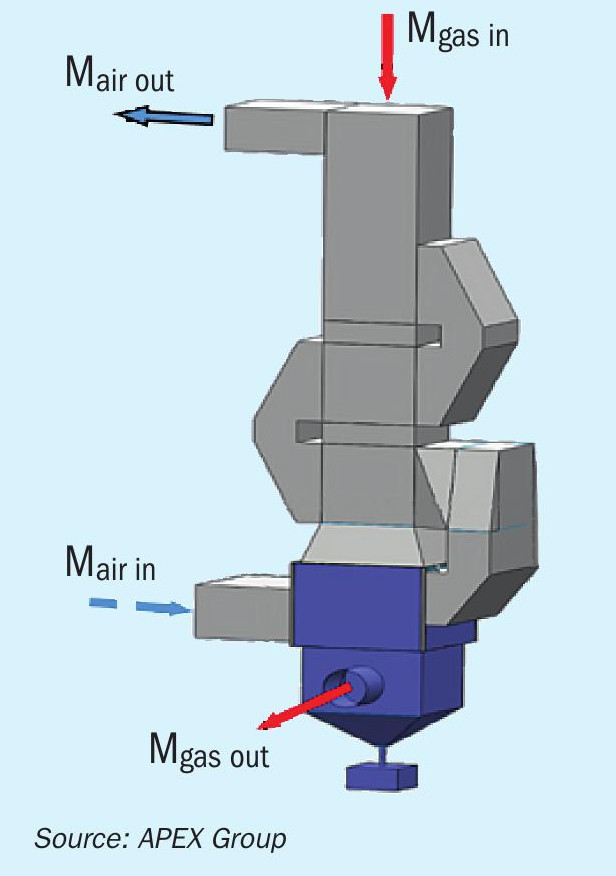
Conclusion
Current limitations in cooling the flue gas below its acid or water dew point due to consequent corrosion issues can be overcome with the use of APEX Group’s newly developed tubular and plate-type heat exchangers constructed from heat transfer elements made of the PPS-GR composite. PPS-GR presents field proven excellent chemical resistance to virtually any acid attack up to boiling temperatures, as well as good mechanical strength and thermal conductivity close to that of the metals. APEX Group heavy duty heat exchangers, capable of handling large volumes of gases, can be easily integrated into any kind of flue gas heat recovery or cleaning systems, such as air preheaters, mercury recovery, wet flue gas desulphurisation, post combustion carbon capture and similar, see Fig. 7.