Sulphur 395 Jul-Aug 2021
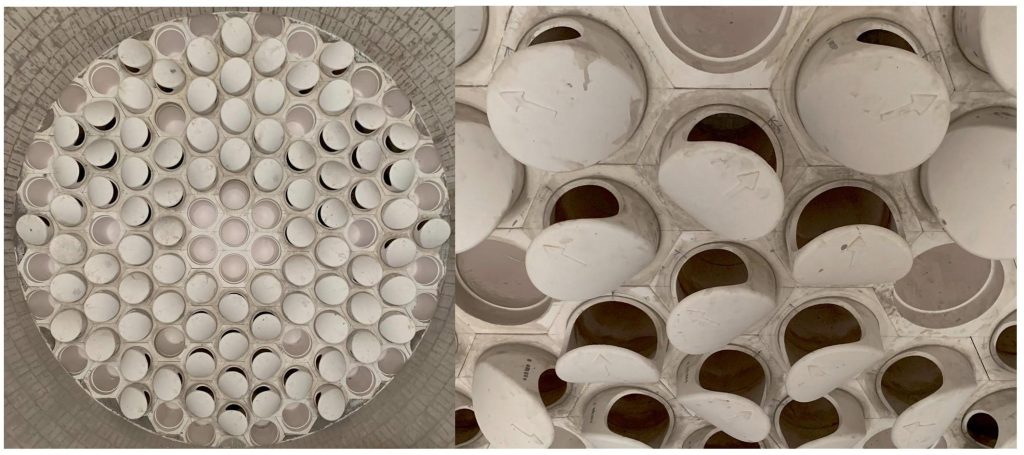
31 July 2021
Upgrading for greater efficiency
SRU THERMAL STAGE RETROFIT
Upgrading for greater efficiency
New state-of-the-art equipment has been installed in the thermal stage of one of Europe’s largest Claus SRU units. Substoichiometric firing and a furnace designed with CFD calculations and a modern compact boiler system design based on detailed heat engineering and FEM calculations were key to the success of the retrofit. P. Foith of CS Combustion Solutions reports on the retrofit and how the novel combination of a CS low pressure swirl burner, additional mixing using a VectorWall™ and a new waste heat boiler design achieved the desired results.
A successful retrofit was recently completed at a 700 t/d Claus plant in Germany, overcoming the problems of poorly operating existing equipment in the existing thermals stage of the SRU unit. The original burner, reactor and waste heat boiler all had issues.
The original burner at the site was a multi flame burner with low pressure drop on the Claus gas side. Due to construction issues the burner had undefined mixing between the air and Claus gas, the flame stability during start-up and lower load cases was poor and there was corrosion due to gas condensation. In the original design there was a ceramic block for each individual flame (48 flames) with undefined mixing of oxidation air and Claus gas. The ceramic blocks was not centrical, hence the Claus gas was not evenly distributed.
Even though the original reactor was equipped with a checkerwall in the first third of the chamber it had inhomogeneous temperature distribution, hot spots damaging the refractory and problems with long burner flames as the checkerwall was positioned too close to the burner.
Besides temperature distribution, the other main purpose of the checkerwall was to improve the H2 S to S conversion, which was also not being met. The checkerwall was therefore very inefficient.
The original waste heat boiler (WHB) was a smoke tube boiler with an internal by-pass with a capacity of 75 tonnes per hour @ 36 bar(g) and 250°C. The steam drum was installed directly on the boiler. The biggest issue was welding cracking, which arose due to thermal stress caused by an inhomogeneous temperature profile. The main challenges of the retrofit were:
- process parameters upstream and downstream should not be affected (remain the same);
- only low pressure is available on the Claus gas side (high turbulence is difficult with low pressure availability);
- low pressure availability on the air side;
- high H2 S to sulphur conversion rate;
- overall size and dimensions should remain the same (reactor and waste heat boiler).
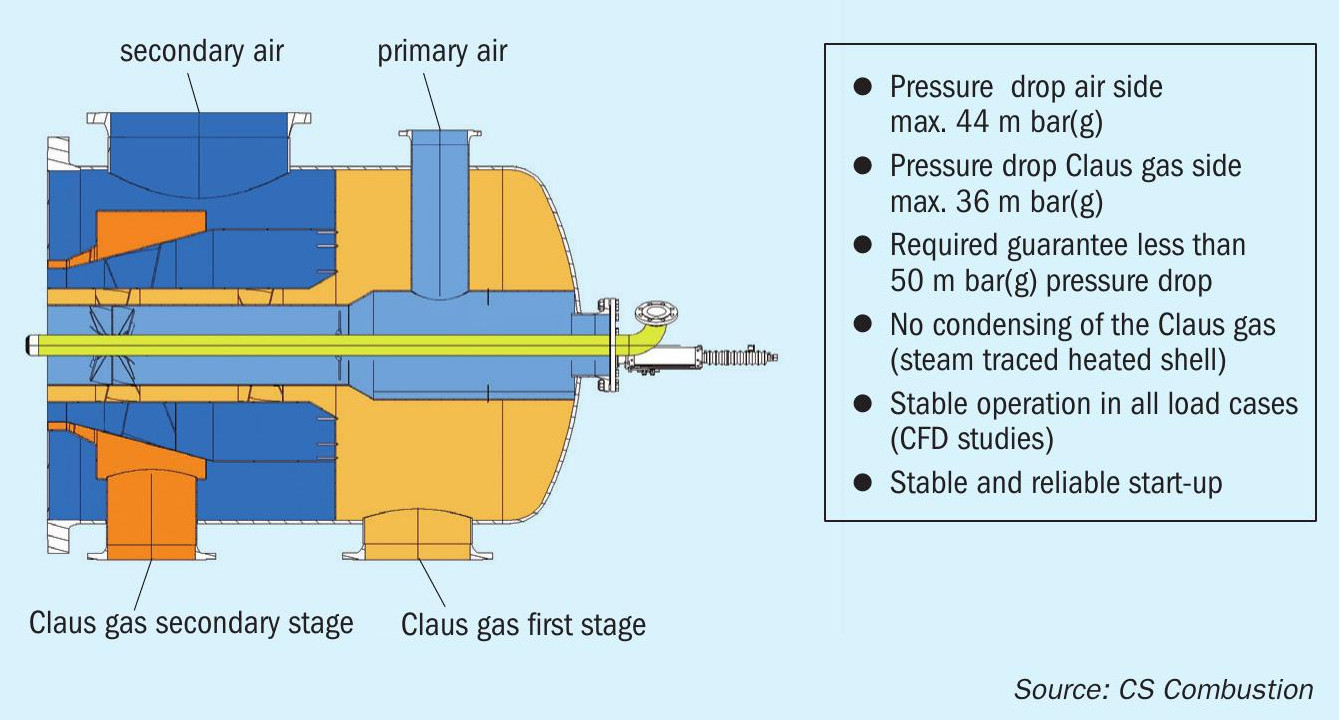
The target was for a maximum pressure drop of 100 mbar(g) through the complete unit (burner, reactor and waste heat boiler). Of utmost importance was to generate sufficiently high turbulence and mixing of air and Claus gas, despite the low-pressure availability. In addition, the aim was to get as close as possible to the theoretical maximum achievable H2 S to S conversion of 70% at these process parameters of 1,338K to meet the guaranteed conversion rate of 65%, as well as increasing the maximum sulphur capacity to 120%.
The following steps were taken to meet these requirements:
- CS low pressure swirl burner: To minimise the pressure drop over the burner and ensure proper mixture of Claus gas with oxidation air, the original burner was replaced with a low pressure double staged swirl burner, based on existing and proven CS burners (Fig. 1).
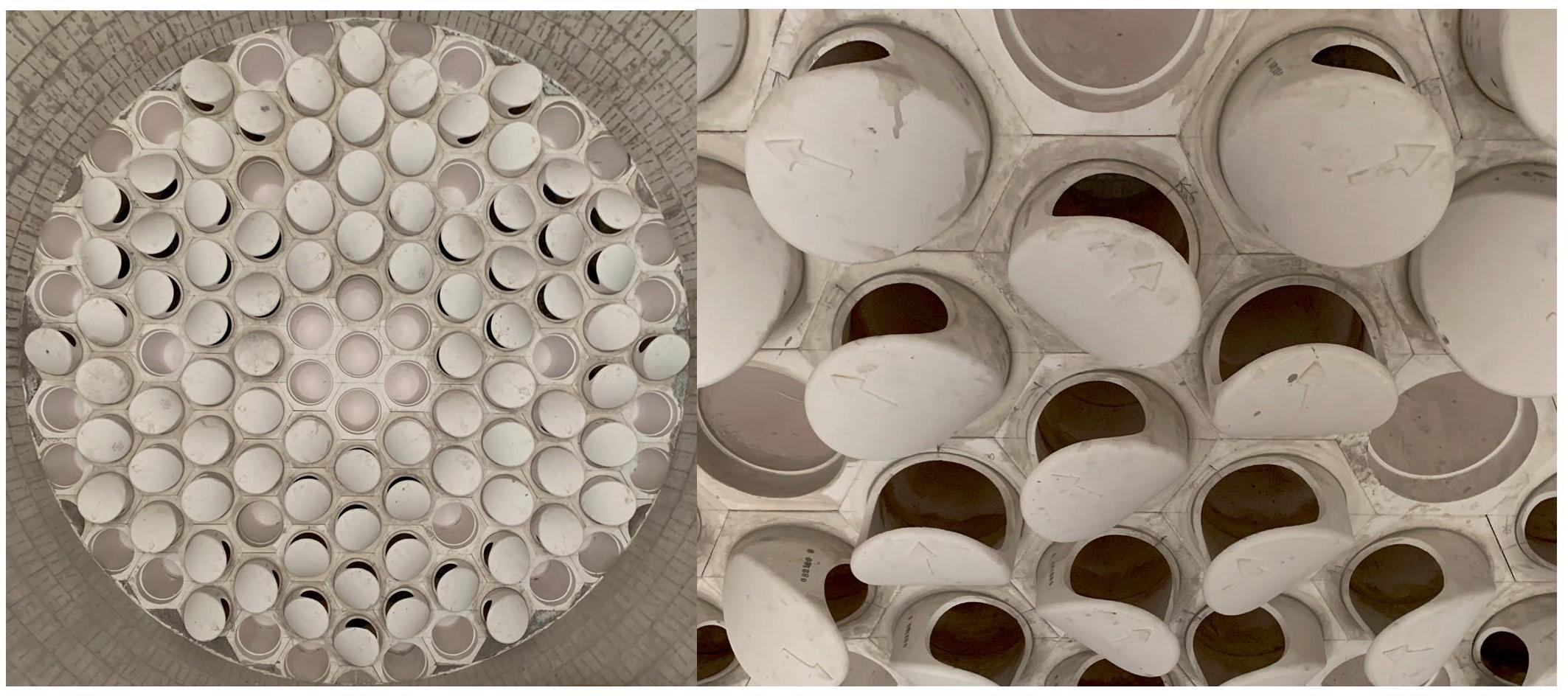
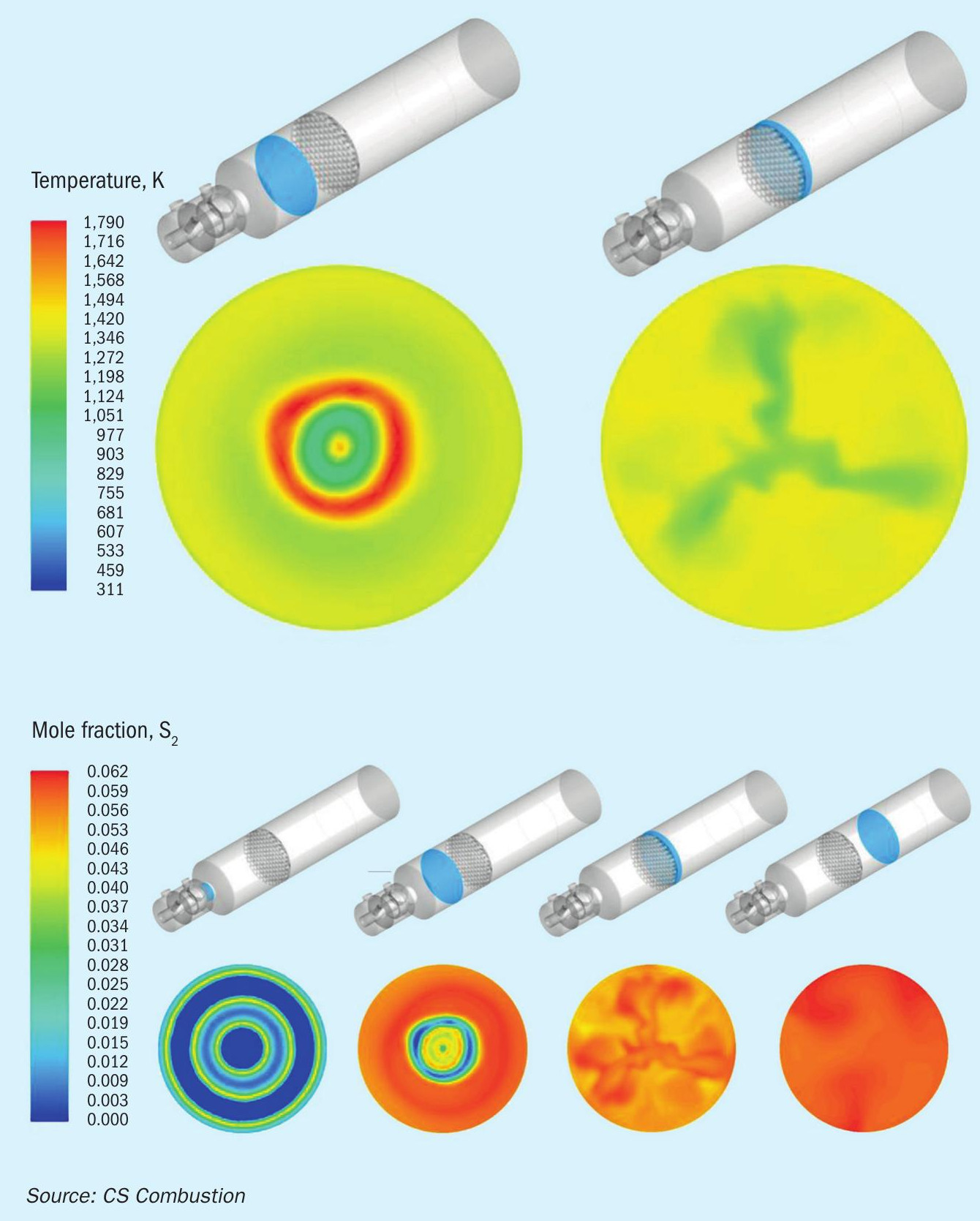
- Additional mixing section by using a VectorWall™ : The swirl and turbulence was further increased by utilising a VectorWall™ with low pressure drop (Fig. 2). The new reactor has the same dimensions as the original one but is equipped with a VectorWall™ instead of a checkerwall. The VectorWall™ generates separate mixing zones for even distribution over the entire cross section.
- New waste heat boiler and CFD analysis: A new waste heat boiler was specially designed by a partner to keep the pressure drop as low as possible. Like the original waste heat boiler, it was a smoke tube type boiler with the steam drum installed on top. The design of the heat exchangers, bypass and internal piping focused on keeping the pressure drop as low as possible, while ensuring the necessary steam capacity. Multiple CFD analyses were done to verify the design and to ensure that the guaranteed H2 S to S conversion rate of 65% or above, as well as an increase of the maximum sulphur capacity to 120% were met.
Results
The result of the retrofit was a complete new thermal process stage for a Claus plant with a sulphur output of 700t/d. The state-of-the-art design is low maintenance, has a low pressure drop throughout the overall unit and achieves a sulphur conversion of ≥65%.