Nitrogen+Syngas 373 Sept-Oct 2021
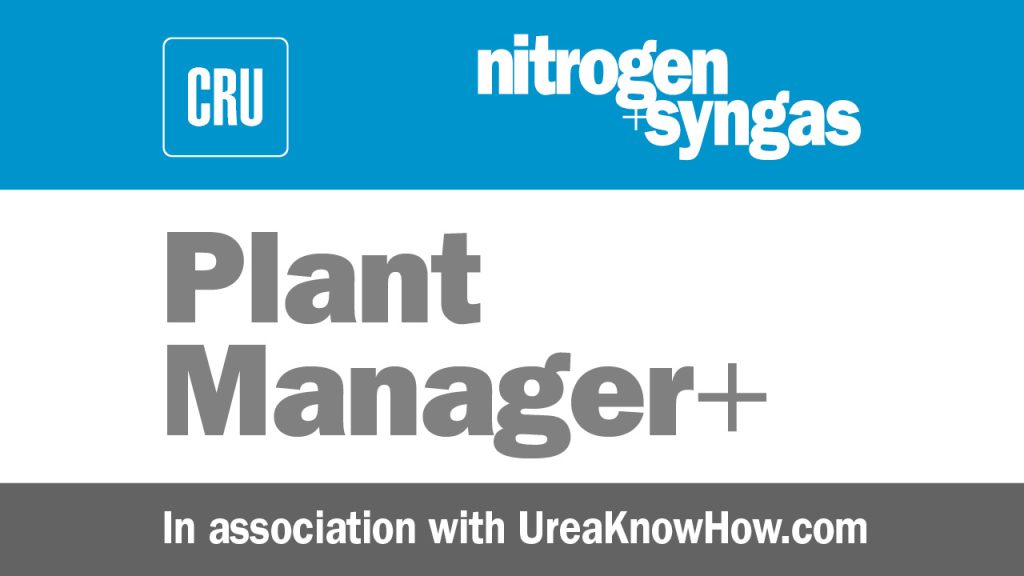
30 September 2021
Problem No. 62: Biuret build-up in the urea melter
The fact that biuret is toxic to plants has been known for a long time – since the middle of the last century. Very sensitive (pineapple, citrus), moderately sensitive (cereals, legumes) and resistant (conifers) plant species were identified. The maximum concentration of biuret in urea for each species has been established for soil application and foliar application. Most field crops easily tolerate foliar fertilization with urea, which contains 1 wt-% biuret. Potatoes and tomatoes are more sensitive – for foliar feeding of these crops, it is advisable to use urea with an admixture of biuret of no more than 0.5 wt-%. Citrus fruits and pineapples are so sensitive that biuret in urea for foliar feeding should be no more than 0.35 wt-%.
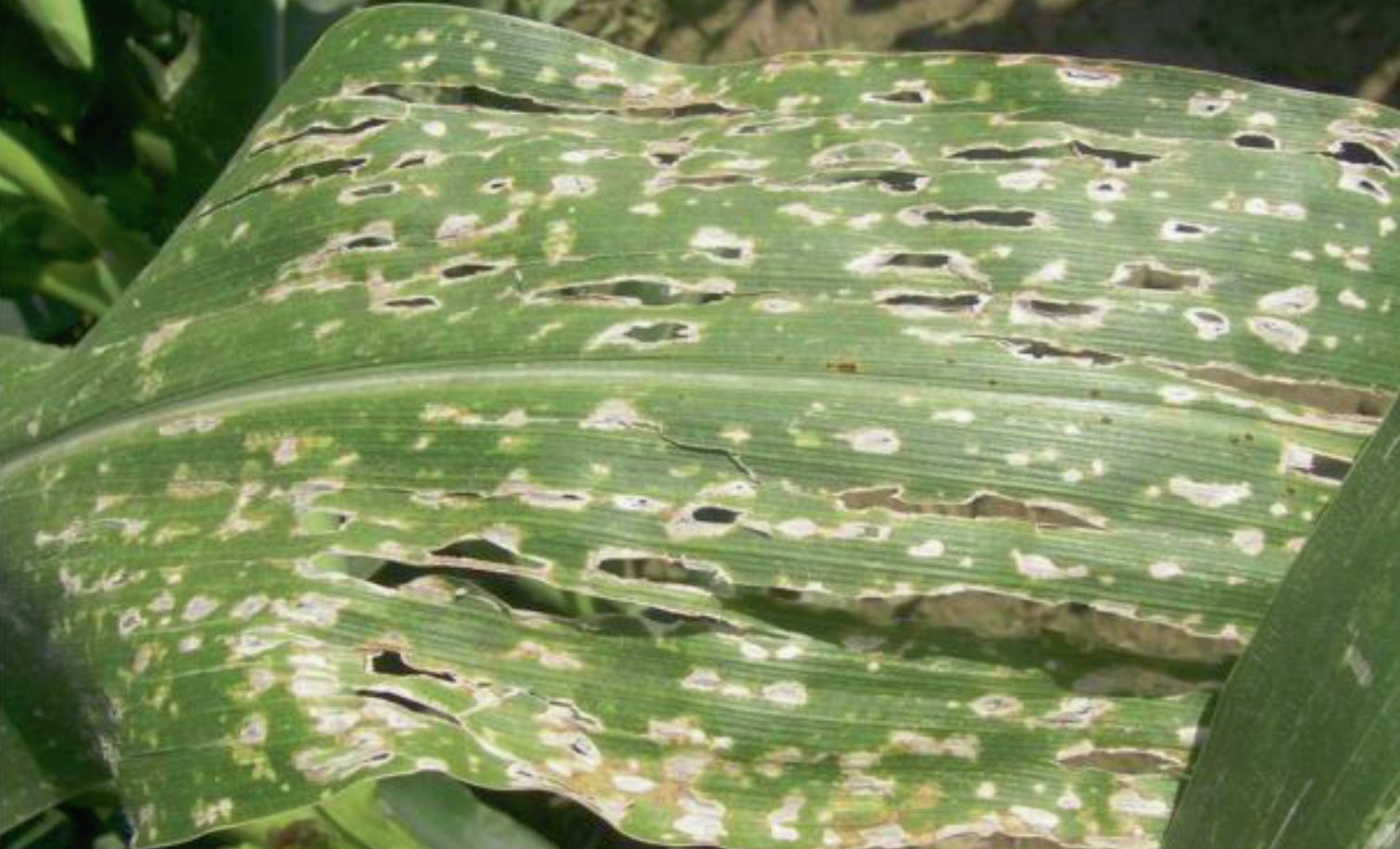
Why is biuret toxic for certain crops?
First, biuret can enter the plant through the root and/or leaf surface. Cell membranes can be permeable to biuret: a small polar molecule without lipophilic moieties can move by simple diffusion.
When entering through the root, biuret moves along the xylem to the leaves; therefore, the concentration of biuret in the aerial part of the seedlings is much higher than in the roots. The main “transporter” of biuret during acropetal movement is transpiration. In foliar application of a solution containing biuret, this substance remains in the tissues of the treated leaves and practically does not move in the plant.
Secondly, biuret enters the plant into the plant slowly: the rate of absorption of biuret is one to two orders of magnitude lower than the rate of absorption of urea. In foliar application, biuret also lags behind urea. Therefore, the symptoms of “poisoning” do not appear immediately: citrus leaves turn yellow only 3-4 weeks after the introduction of carbamide with an admixture of 0.5% biuret.
Thirdly, the biuret in the plant is preserved in its original form: plants do not have specialised enzymes to break down this substance. In orange leaves, for example, biuret persists even eight months after spraying.
Most urea plants in the world nowadays produce prills or granules with a biuret figure between 0.8 and 1.0 wt-%. In these plants urea is concentrated by means of a one or two stage evaporation section at low vacuum pressures. The low pressures lead to low operating temperatures which restricts biuret formation.
In the 1960s and 1970s of the last century, several urea plants were built which have been able to produce urea with a low biuret figure. Instead of evaporation, crystallisation technology was applied, making use of the difference in crystallisation temperature between urea and biuret.
The urea crystals produced contain hardly any biuret and some plants sell these crystals for high value pharmaceutical or food applications. However, to convert the crystals into prills or granules suitable for fertilizer application, typically the crystals are remelted and sent to a prilling tower or granulation section. The melter is the cause of some formation of biuret leading to a biuret content of some 0.3 to 0.5 wt-%.
Lance Gerdeman of Nutrien in the United States kicks of this round table discussion: We operate a crystalliser to produce low biuret prills. The unit was constructed in 1970 by C&I Girdler in Ohio, United States. The dried urea crystals are pneumatically conveyed to the top of the prill tower, pass through a cyclone separator, and fall to two parallel melters. The melters are rectangular in shape, have a bank of triangular tubes heated by 160 psig steam, and a rake to spread the crystals across the tube bank. The bottom vertices of the triangular tubes have a small gap that allows the liquified melt to flow through while preventing any crystals from passing through (see diagram below). We struggle with stagnant areas along the edges of the tube bank where the urea sits for long enough to polymerise to biuret/triuret and builds up in large chunks requiring annual cleaning. The solids are fairly insoluble in steam condensate so mechanical removal is typically required which is time consuming and hazardous (confined space entry, very challenging work environment).
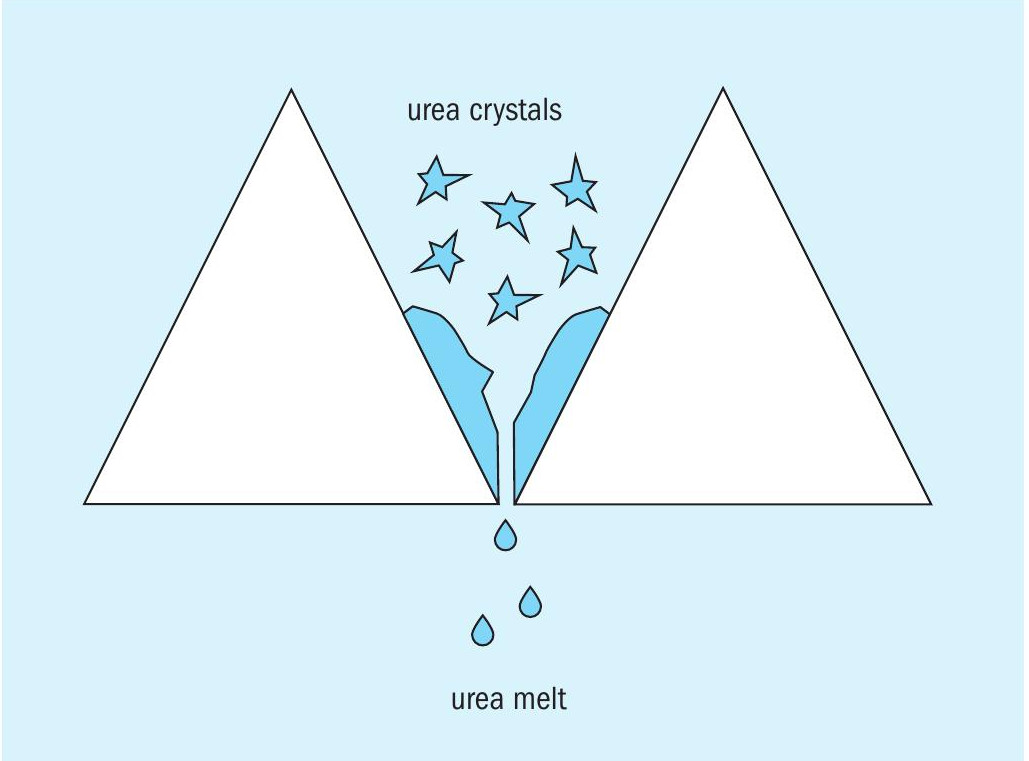
I am interested if others have experience with chemically dissolving biuret/triuret solids, perhaps to eliminate the need for mechanical removal.
I am also curious to know if others could share what type of melter technologies they are using for prill units using crystallisers?
Mark Brouwer of UreaKnowHow.com in the Netherlands replies: I know the following melters:
1. Same principle but with round tubes instead of triangular.
2. Small vessel with heater and circulating pump. You could also consider flushing with urea melt which is very effective at dissolving urea polymers
Prem Baboo from Dangote Fertilizers in Nigeria shares his valuable experiences: The biuret problem seems to be in the head tank level and outlet temperature of the melter. Sometimes the head tank level shows erratic when at maximum level. If the problem with the melter is stagnant areas, this can be rectified during a shutdown. In my opinion a melter should have no stagnant areas. I also think the biuret level can be controlled by the temperature: You are using 160 psi pressure steam, the saturation temperature at this pressure is 188°C which is very high. The temperature required for steam is 145-150°C which means 55-60 psi is sufficient for the melter. However, in case you are using a pressure let down valve in the steam line please realise the let down is isentropic expansion. The following points may be helpful to control biuret levels:
- level of head tank (minimum);
- temperature of the melter;
- melter outlet condensate should be removed with a condensate pot with control valve to maintain the level in the pot (do not use a trap);
- the stainless steel rods between the melter steam tubes (replace any eroded rods)
- the biuret may be removed in the slurry stage i.e, centrifuge into the mother liquor. Steam condensate (DM water) can be increased in the centrifuge slurry to separate the biuret into the mother liquor.
Muhamad Reda of Pupuk Kujang in Indonesia shares also his interesting views: In our old plant (Kujang 1A) using TR-CI urea process technology by TEC in Japan we have a similar case. To remove the solid biuret/triuret/urea solid during turnaround we used caustic soda (NaOH) liquid 40% concentration. We fill up the melter with steam condensate until almost full then add 3-5 t NaOH then boil it (using the steam coil inside the melter). Continue boiling with NaOH for eight hours minimum. You can boil it with condensate only before and after caustic-boiling to rinse the melter. The procedure was successful, resulting in a clean melter, ready to inspect with no need for mechanical cleaning.
This series of discussions is compiled from a selection of round table topics discussed on the UreaKnowHow.com website. UreaKnowHow.com promotes the exchange of technical information to improve the performance and safety of urea plants. A wide range of round table discussions take place in the field of process design, operations, mechanical issues, maintenance, inspection, safety, environmental concerns, and product quality for urea, ammonia, nitric acid and other fertilizers.