Sulphur 396 Sept-Oct 2021
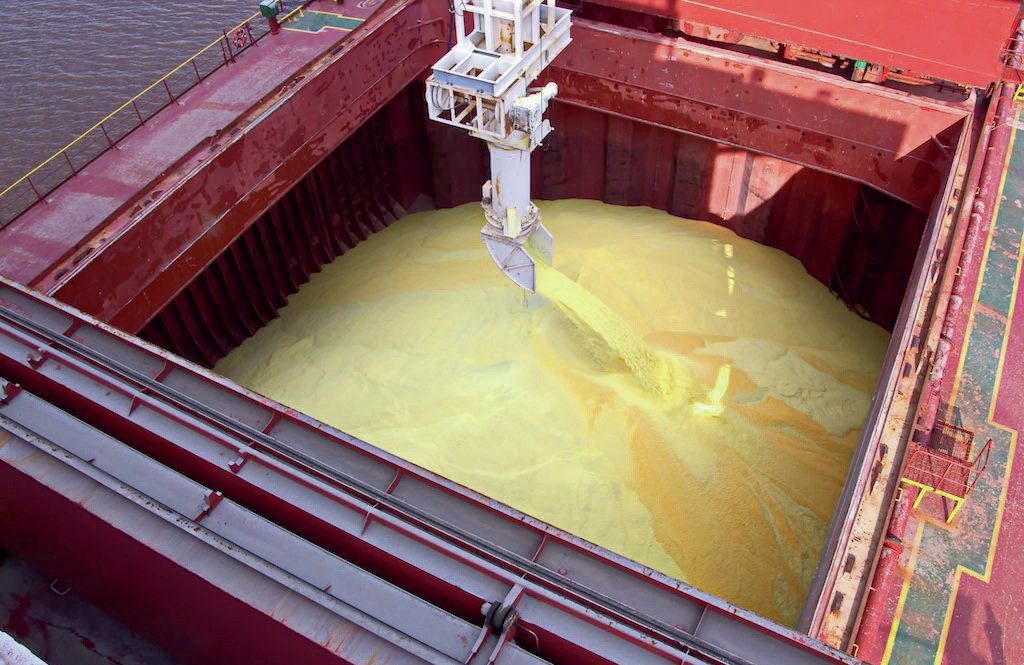
30 September 2021
Sulphur dust control
SULPHUR DUST
Sulphur dust control
Dealing with sulphur dust is an operational challenge for sulphur forming plants and sulphur storage and handling facilities.
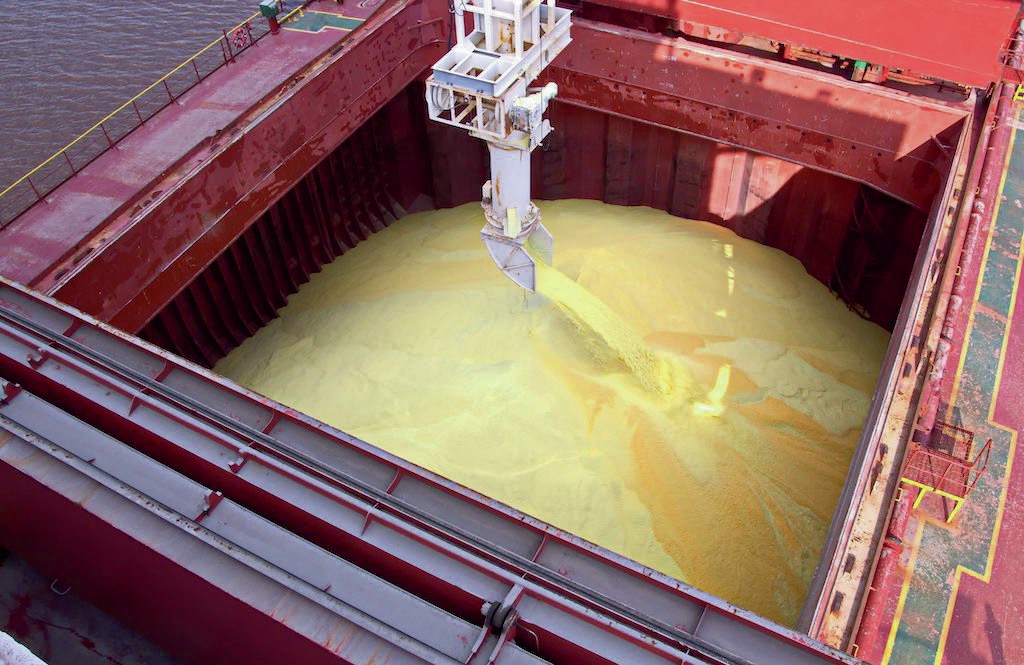
The major threat involved in handling solid sulphur is dust. Dust can be created during the processing or transport of sulphur, or sometimes due to sulphur sublimation in melting pits or tanks. Dust can be thrown into the air by maintenance and cleaning activities, by the transportation itself, at belt transfers and stackers, by failures of transport belts such as guide chutes overfilling, belts slipping or side travels, causing spillage and falling of sulphur. If unmanaged, these conditions can create a sulphur dust explosion hazard.
Particle size is a key determinant of the explosibility of a dust. As the particle size of the dust decreases, the available surface area increases, making it easier for the dust to burn rapidly. A fine dust will also form suspensions in air more readily and remain suspended for longer than coarser particles. A shock wave from a primary explosion will also disturb any settled dust layers in the vicinity, forming a second dust cloud, which can then initiate a much larger and more devastating secondary explosion, possibly only fractions of a second after the primary.
In order to prevent dust fires and explosions there are two basic strategies; to avoid suspensions of dust in the air, and to exclude sources of ignition.
Dust minimisation
Over the years solid sulphur has moved to less friable and dusty forms, from slated or flaked sulphur to spherical or hemispherical forms. Even so, dust can be generated when solid particles rub against each other during transfer and handling operations. It is always good practice to reduce the number of transfer points and handling steps to a minimum, and try to minimise the use of front end loaders which can crush sulphur granules beneath their wheels.
To prevent dust accumulation during storage and handling of sulphur, enclosures should be constructed with a minimum number of horizontal surfaces where dust can accumulate, and access to any and all hidden areas. Good housekeeping is a must, with inspection of and cleaning of dust residues at regular intervals.
Dust suppression
While dust minimisation and good housekeeping is essential for keeping dust levels down, dust formation cannot be prevented completely. The next step then is to suppress dust. Water can be sprayed at transfer points and load-out station; the wetted particles agglomerate to each other and to larger particles, making them more difficult to be picked up by air currents. Until the advent of dust suppressant chemicals, water was the sole means of controlling release of sulphur dust during transfer operations. However, water promotes the formation of acidity and wet sulphur corrosion. For this reason a maximum moisture content of 2% is specified in, e.g. Chinese sulphur specifications. Customers also tend to have maximum standards for water content of the sulphur, as higher water content increases the energy consumption during re-melting at sulphuric acid plants in order to evaporate the water. In general a moisture content of 1-2% is the recommended value.
The effectiveness of water for dust control is also limited by the hydrophobic nature of sulphur. This can be overcome by the use of special water-based chemical surfactants. When air is mixed with the surfactant/ water mixture, foam is generated. Foam is a very effective means of dust control, made up of small bubbles 100-200 micrometers in size. When it comes into contact with dust particles the bubble breaks, coating the particle. When several come into contact they coalesce into a larger particle and can no longer become airborne as dust. Foam suppression systems create 0.5-1.0% moisture on the specified transfer point according to the transfer rate.
Sources of ignition
It is also important to remove potential sources of ignition. Solid sulphur is a poor conductor of electricity, and can easily develop a sufficient static charge to cause sparking. For this reason, every care must be taken to prevent static electricity accumulation in areas where solid sulphur is handled.
Smoking and the use of matches must be prohibited in all areas where sulphur dust is likely to be present. Naked flames or lights and the use of gas cutting or welding equipment should also be prohibited during the normal operation of the plant.
Dust layers or clouds of sulphur are also easily ignited by hot surfaces. To prevent excessive heat build-up, all equipment should be properly and securely installed to ensure the correct alignment of rotating shafts, belt tension etc. The surface temperature of plant or machinery should not be allowed to exceed2 /3 of the ignition temperature of sulphur dust (i.e. 127°C).