Fertilizer International 506 Jan-Feb 2022
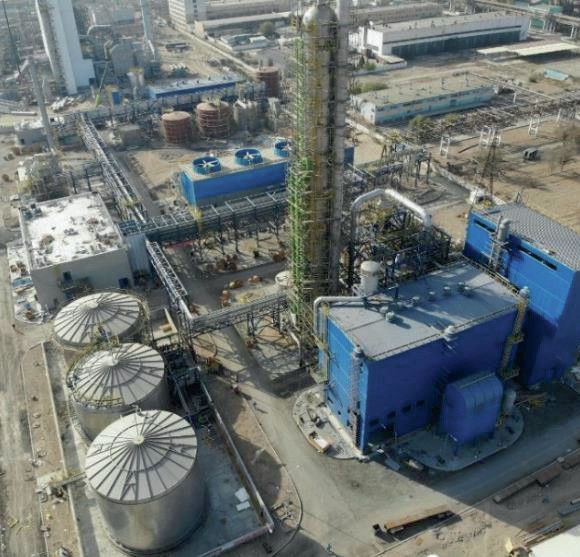
31 January 2022
Safer and sustainable nitrates production
PRODUCTION SAFETY AND SUSTAINABILITY
Safer and sustainable nitrates production
State-of-the art technologies offered by thyssenkrupp, Casale and Stamicarbon are helping make nitrates production more secure and sustainable.
Worldwide, ammonium nitrate (AN) is the second most important nitrogen fertilizer after urea (Fertilizer International 503, p29). Advantageously, it supplies nitrogen in two different forms: nitrate (NO3 -)and ammonia (NH4+ ). While crops can take up nitrate directly, ammonium acts more slowly as it needs to be converted into nitrate by soil bacteria prior to take-up. Using AN as a fertilizer therefore helps ensure that nitrogen is available to crops both immediately and over the longer term.
AN can also improve crop yields by avoiding the ammonia volatilisation associated with urea and urea ammonium nitrate (UAN). The resulting nitrogen losses contribute to pollution, affect air quality and waste resources. Indeed, ammonia volatilisation from AN and calcium ammonium nitrate (CAN) is several times lower than from urea or UAN (Figure 1). In UK wheat trials, the application of AN also achieved the best yield response (crop N offtake) and crop quality (protein content) compared to other nitrogen fertilizers (Figure 2).
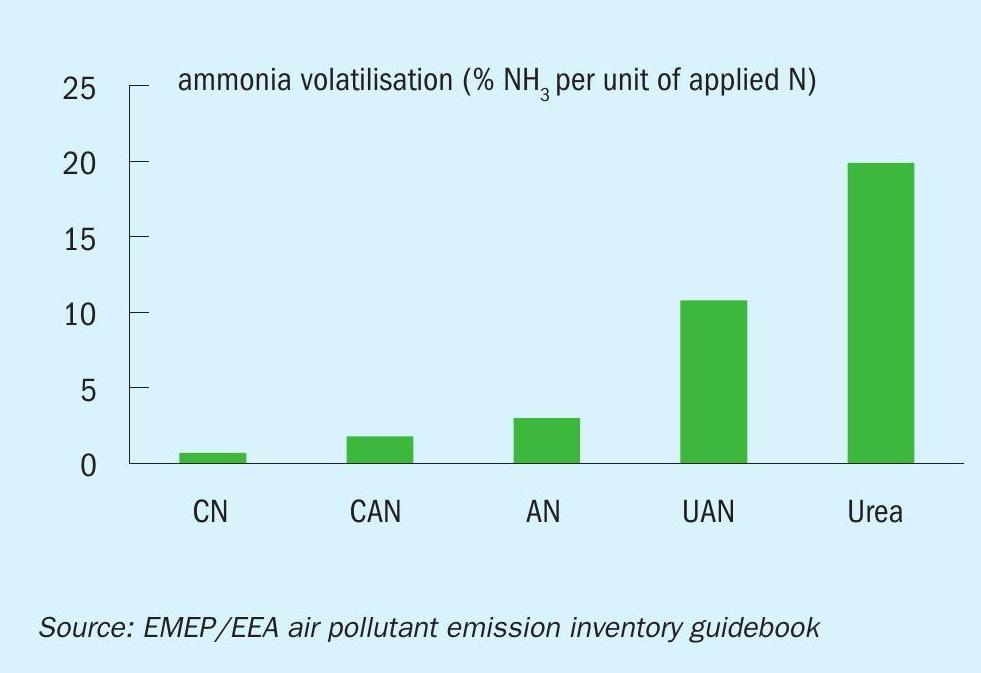
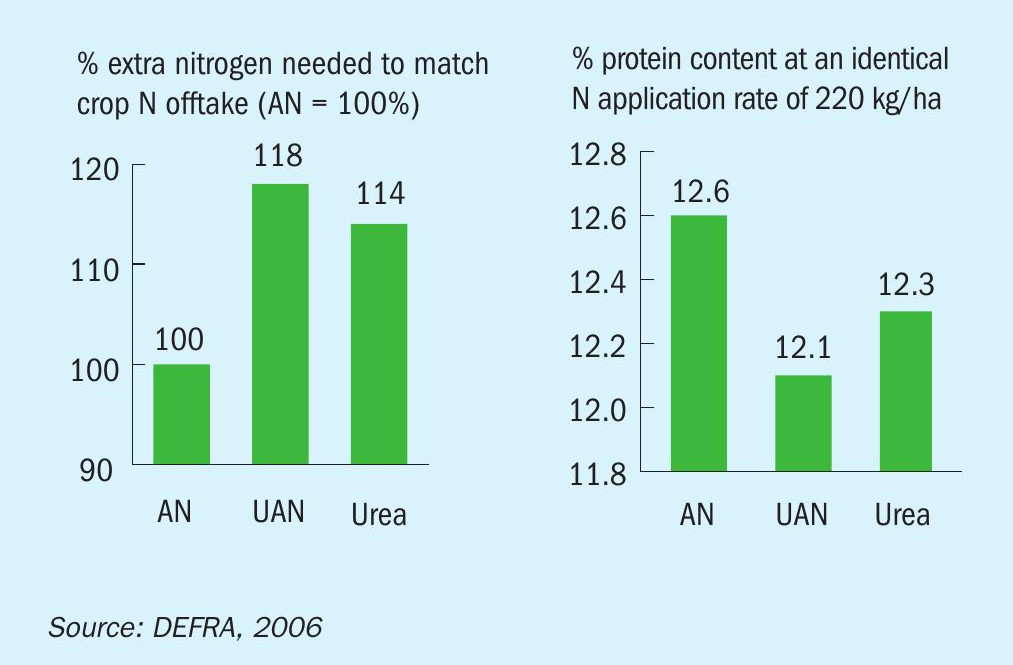
THYSSENKRUPP
Green and safe ammonium nitrate
Green technologies
By using renewable energy, thyssenkrupp Uhde (a business unit of thyssenkrupp Industrial Solutions) can design and offer a completely integrated and green fertilizer production line based on its own technologies (Nitrogen+Syngas 371, p44). These include:
- Green hydrogen production by the water-electrolysis process.
- The conversion of hydrogen to green ammonia
- Nitric acid production with the proven and most effective N2 O and NOx reduction technology (EnviNOx® )
- Ammonium nitrate production to supply granulation, prilling or urea ammonium nitrate (UAN) plants.
Green hydrogen production is based on alkaline water electrolysis technology offered by thyssenkrupp Uhde Chlorine Engineers (tk-UCE), a joint venture with Industrie De Nora. This can be converted to green ammonia and methanol or used to supply other hydrogen-based production processes such as synthetic natural gas and Fischer-Tropsch synthesis.
The subsequent use of green ammonia in nitric acid production results in a much smaller carbon footprint. Also, by partly replacing or supplementing process air with oxygen – an otherwise unused by-product of water electrolysis – the efficiency and/or capacity of the nitric acid plant can be significantly increased.
The EnviNOx® abatement system
The EnviNOx® abatement system from thyssenkrupp Uhde is effective at reducing both NOx and N2 O emissions from nitric acid plants (Nitrogen+Syngas 373, p32). This end-of-pipe technology, being installed in the plant’s waste gas stream, avoids any risk of product contamination, production losses or the fouling of equipment (Figure 3). Multiple installations in nitric acid plants worldwide have demonstrated N2 O removal rates of 99 percent or more, and come close to eliminating NOx at almost zero ppm. EnviNOx® is also a highly practical abatement method as both pollutants are dealt with in a single reactor vessel. Advantageously for operators, the installation of an EnviNOx® system will also qualify as a greenhouse gas emissions reduction project under any emission trading scheme.
The ammonium nitrate process
For AN to remain widely used as a fertilizer, what are the essential elements of safe production – and what can manufacturers do to minimise the likelihood of an accident, within their own scope of responsibility? Below, we consider some basic rules for the design and operation of AN plants.
In general, AN plant design always has a focus on safety (see box). Nonetheless, other aspects of plant operations are also important. These include:
- Flexibility in plant load
- The export of very pure process condensate
- General ease of operation, i.e. no wear and tear parts in static equipment.
How are safety considerations best combined in an AN neutralisation plant? Well, an Uhde® AN vacuum neutralisation and concentration unit (Figure 4) allows plant operators to perform the exothermic reaction between nitric acid and ammonia at a low temperature (only 145°C) well within critical on-set limits.
The precise control of both pressure and temperature possible with this unit also enables producers to generate AN solution at a constant concentration (e.g. 92 wt-%) in the neutralisation step (Figure 4, item 1). This high AN grade is achieved by flash evaporation alone without external steam supply. The vapours generated are also thoroughly cleaned and completely condensed, eliminating any possibility of nitrogen passing into the atmosphere (Figure 4, item 4). Importantly, this high nitrogen yield is delivered without permitting the system pressure to increase. Temperature, pressure and critical flows are all continuously monitored using an ESD system, while a sophisticated control system ensures that the best operating conditions are maintained.
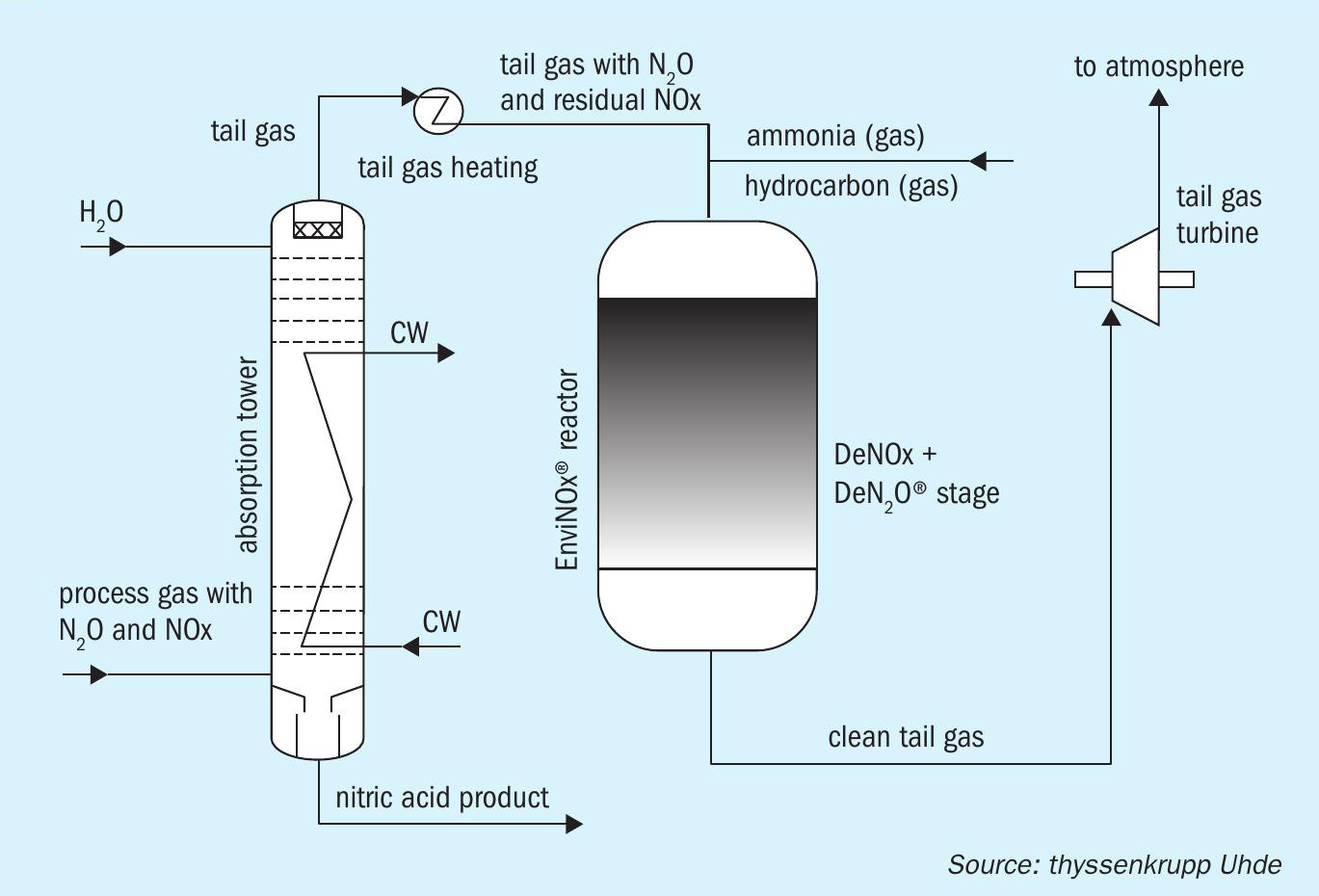
Plant safety by design
Temperature and pressure
AN decomposes via several temperature-dependent chemical reactions. Reactions that start at elevated temperatures (>180°C) are particularly problematic. These generate huge amounts of heat – and are therefore self-sustaining – and the gaseous reaction products released can cause ruptures or explosions when confined. The resulting increase in pressure, if reaction gases are contained instead of being vented, also accelerates decomposition.
The following design rules are required for production plants due to the risk of AN decomposition, its reaction chemistry and the undesirable physical consequences:
- Manufacture needs to take place at low operating pressure
- Low process temperature must be maintained
- The release of gases/vapours must always be possible
- All possible heat inputs into the system must be detected and limited.
Feedstock composition
AN is formed by neutralising nitric acid with ammonia in equal molar ratio. Yet compositional purity is very important when it comes to safety. That’s because the presence of low-level constituents such as chlorides, organic carbon and metal ions (e.g. Cu, Zn, Cr etc.) can reduce the onset temperature of AN decomposition reactions with negative consequences. Increasing concentrations of these impurities, by lowering the onset temperature, can make decomposition reactions more likely to happen and develop more quickly. Carbon, in particular, has the potential to liberate large amounts of heat when reacting with AN.
Even the presence of nitric acid itself can be undesirable if present in excess. It can also become available through the slow decomposition of AN into nitric acid even at ambient temperature. This causes the pH of AN solutions to drop and generates gaseous ammonia that needs to be vented from the system. (AN producers will all be familiar with the faint smell of ammonia close to storage vessels if these are not properly vented.)
As a result, AN plant design needs to meet the following challenges:
- Precise feedstock control
- Process monitoring
- Provisions to compensate for the natural acidification of AN solutions
- All accompanied by strict quality management of the feedstocks.
The Uhde® AN vacuum neutralisation system also runs at slightly acidic conditions as well as at low temperatures. This is the key factor for ensuring the safe control of process parameters and the lowest nitrogen slippage via process vapours. However, for intermediate storage, pH needs to be kept within an alkaline range – and is therefore adjusted downstream of the vapour separation stage under atmospheric conditions (Figure 4, item 8).
Special features
The ability to measure pH values throughout systems containing solutions of AN is an important guarantor of both safety and product quality. Uhde therefore provides a suitable and proven pH measurement and sampling system. During sample preparation, the lifetime of the pH probe is prolonged by diluting the AN solution with water to reduce the risk of crystallisation. Saturated steam is also available for flushing purposes.
The plant’s control system will automatically stop production if the pH falls below the optimal level for process control for a prolonged period. However, the plant does not need to be drained even during a shutdown as, after stopping the feedstocks, the circulation pump remains in operation allowing for a very quick restart.
Maintaining an ideal mix of the reactants, ammonia and nitric acid, inside the reactor is key to reducing ammonia losses (a critical environmental factor) and minimising spots of high nitric acid concentration (a critical safety factor). Simulations have demonstrated that the Uhde® reactor is able to keep an almost perfect flow pattern.
Valuably, in an Uhde plant both the neutralisation reaction and the concentration of the final AN melt can be performed under low sub-atmospheric pressure conditions. This means plant managers do not have to think about raising operating temperatures, so avoiding the formation and subsequent abatement of AN aerosols in the separated vapour stream. Uhde’s AN vacuum neutralisation and concentration plants are in fact free of aerosols and have clean vents – as their comparatively low operating temperature and the absence of air-swept concentrators avoids the formation of AN aerosols from the very beginning. Only leakage air from the vacuum systems (containing inert gas) is released to atmosphere.
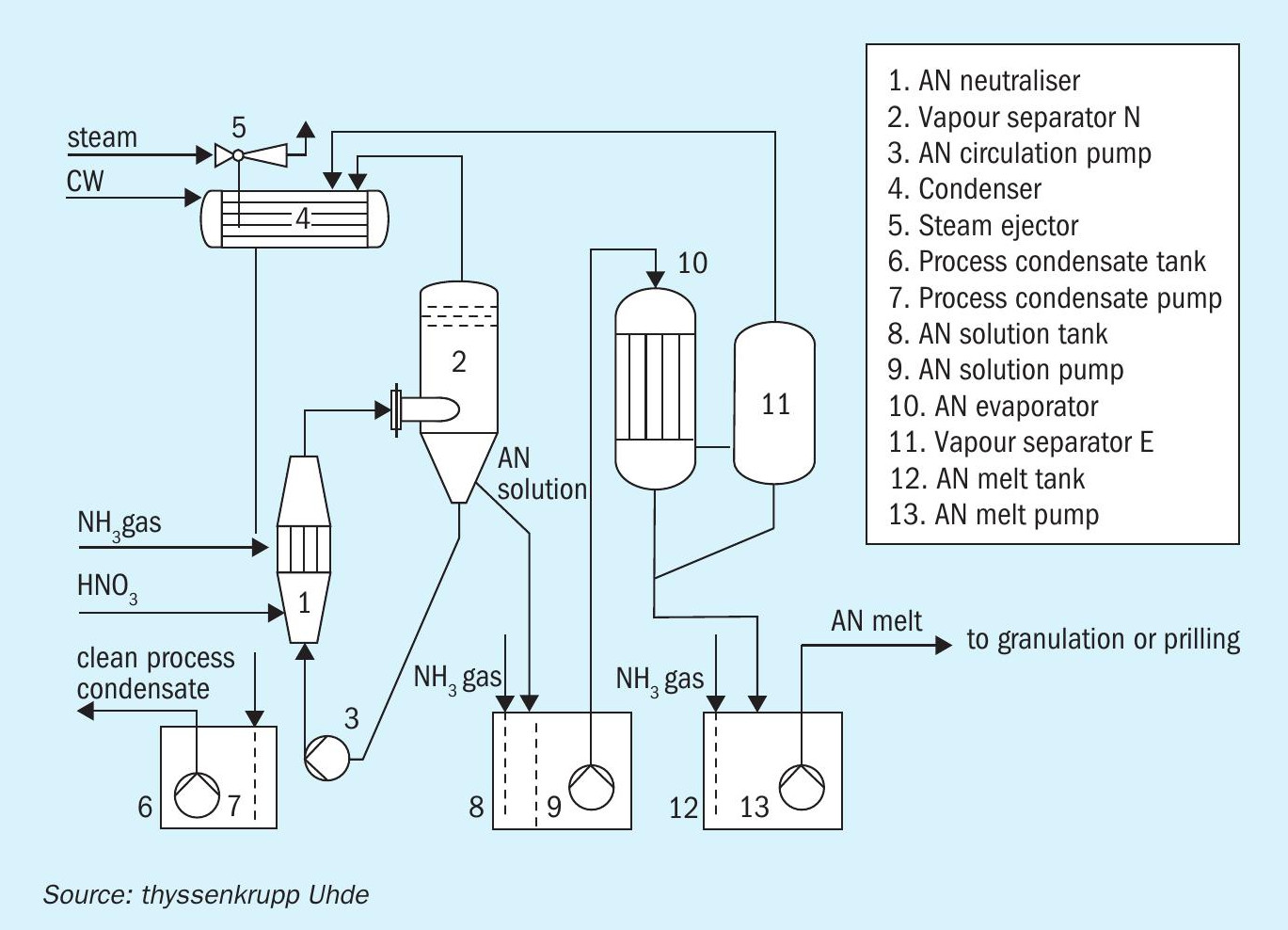
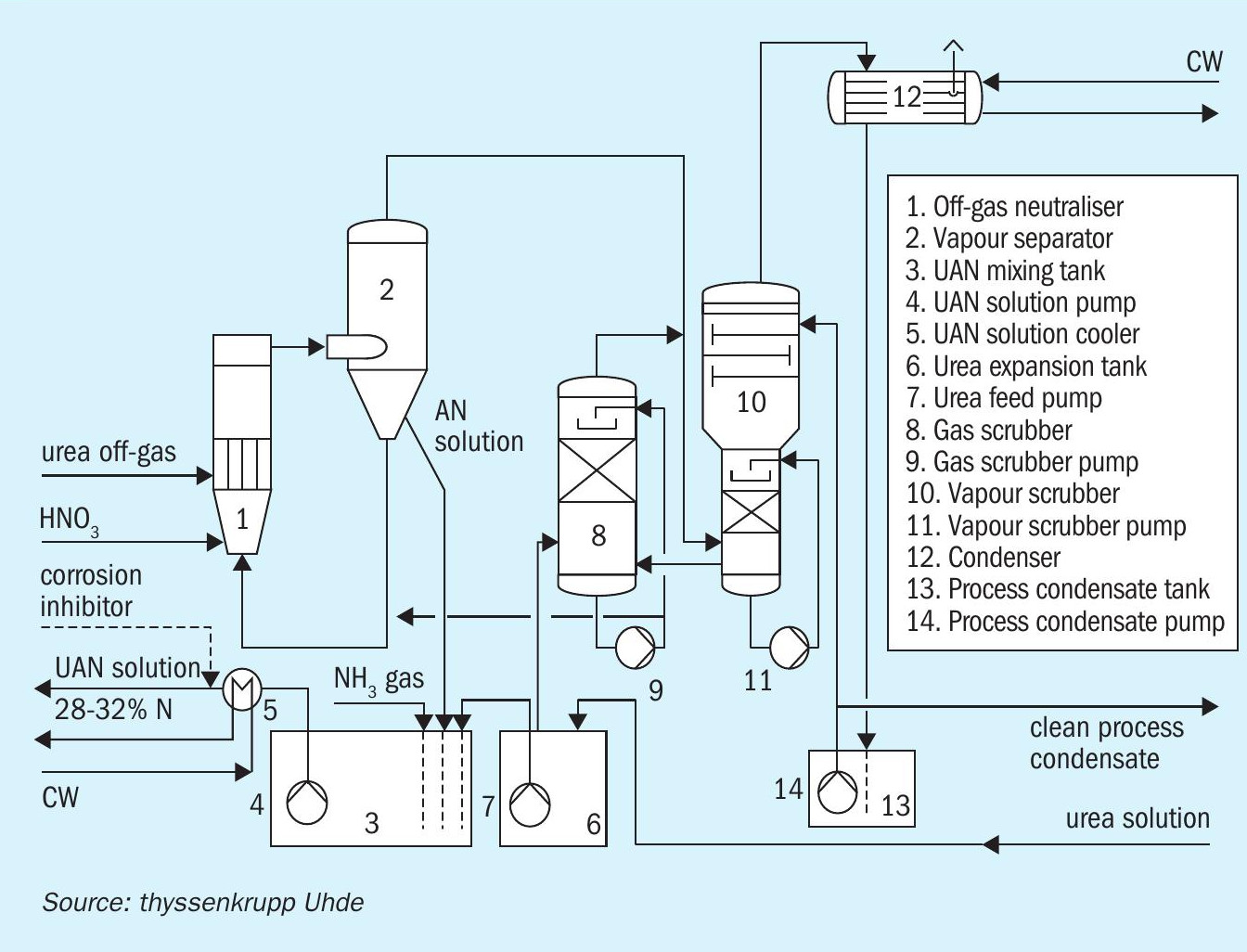
Latest developments
Combined neutralisation and concentration: In the newest development in AN technology (patent pending), thyssenkrupp has combined two vacuum units for neutralisation and concentration to form one single vapour and condensate system (Figure 4, items 4 to 7). In this system, the concentration and temperature of the final AN melt determines the overall pressure of the entire vacuum network. Vapours from the concentration and neutralisation units – although cleaned separately, under their respective ideal conditions – are subsequently merged and condensed together. This avoids the need for a dedicated condenser for the concentration unit with both stages having one common process condensate tank instead.
Urea ammonium nitrate (UAN) production: it can be commercially beneficial to feed the low-pressure, ammonia-rich off-gas from the urea plant directly to the AN neutraliser (Figure 5). However, in this configuration, the system pressure in the AN neutraliser must be lowered to cope with the pressure of the urea off-gas. This can be achieved by employing natural draft circulation instead of the forced circulation that is typical of most plants. By incorporating additional dedicated scrubbers (Figure 5, items 8 and 10), AN can be produced within environmental limits from these low pressure off-gases.
Pressure neutralisation: thyssenkrupp also offers ‘pressure neutralisation’ AN plants to customers. These operate at atmospheric pressure (in the vapour separator) or at elevated pressure, depending on project-specific requirements such as plant availability and the cost of utilities. Special attention must be paid to the system operating temperature when designing these types of AN plants. This is because of the absolute necessity to avoid reaching the on-set conditions for decomposition reactions. The proper selection of construction materials is also mandatory for these plants as the corrosion rate will increase at elevated temperatures. Pressure neutralisation is the right choice if the focus is on safety and on utility consumption (steam and cooling water), rather than investment cost, as process heat can be captured for concentrating the AN solution using reboilers.
Conclusions
The design of safe and reliable AN plants must:
- Consider lessons learned
- Follow strict internal and external standards based on experience and best practice
- While at the same time focus on the individual needs of clients.
This can be achieved by using the ‘preconfigured plant concept’ (PCPC) engineering approach. This method divides up the complete plant into functional modules. It covers all the main engineering documents for the design of a standardised plant and summarises all safety and operability information.
PCPC ensures that all design proposals are treated holistically and on a quality-assured basis. It includes key engineering information covering the plant’s process, layout, piping, static equipment and machinery. The system is both stringent – as it guarantees quality and safety – and flexible enough to allow the plant’s design to be tailor-made to match client requirements.
Although AN is a potentially hazardous substance that requires a high level of attention to safety, equally, it is a stateof-the-art fertilizer that can contribute to global efforts to reduce greenhouse gas emissions.
It is perfectly possible to produce AN under carefully selected and closely monitored conditions at plants that are designed with experience and care. In this way, significant steps towards safely manufacturing AN have been taken.
CASALE
Sustainable ammonium nitrate production
Green technologies
For several years now, Casale has been devising and bringing to market new green technologies for ammonia production. Its wide-ranging capabilities cover the design and delivery of complete green ammonia production plants including the converter and synthesis loop. Casale can also supply engineering components for other sections of the green ammonia plant, including hydrogen generation and storage. Additionally, the company has relevant complementary engineering expertise and know-how in areas such as:
- Plant digitalisation and optimisation
- End markets and uses for green ammonia
- Cracking ammonia to obtain hydrogen
- Conversion of green ammonia into nitrogen fertilizers
The Casale ammonium nitrate process
Casale’s know-how in designing ammonium nitrate plants dates back to the start-up of the first ammonium nitrate plant by Grande Paroisse in France in the early 1980s. Since then, Casale has designed more than 45 ammonium nitrate units with capacities ranging from 250 t/d to 2,000 t/d.
These plants produce ammonium nitrate solution (ANS) via the strongly exothermic reaction between ammonia and nitric acid:
HNO3 + NH3 Æ NH4 NO3
The main manufacturing goal is to optimise the process by making the best use of the energy released and obtain the highest ANS concentration possible. This is the key concept underpinning the AN2000™ pipe reactor (Figure 1), Casale’s distinctive technology for ANS. Neutralisation takes place at nearly atmospheric pressure inside this reactor – which is designed to capture and maximise the use of the heat generated to achieve a high ANS concentration.
The pipe reactor is at the heart of the overall production process (Figure 2) and the place where raw materials are efficiently mixed and reacted to produce ANS.Preheated ammonia and nitric acid feeds are mixed and fed to a specially designed tubular reactor at a pressure of 7-8 bar. Ammonium nitrate forms almost instantaneously releasing a significant amount of heat. Hot ANS flashes from the end of the pipe reactor into a separator vessel. The liquid ANS product is collected at the bottom of this separator and sent to storage, while vaporised water is released as process steam.
Design improvements
The AN2000™ pipe reactor design has undergone a series of design modifications to satisfy a range of operational and customer requirements. These improvements have maintained the reactor’s existing advantages, such as simplicity and easy maintenance, while offering the following benefits:
- Safety: this is of paramount importance in ammonium nitrate solution production. In a pipe reactor, raw materials are mixed in an extremely small space, eliminating the need for large reaction volumes which would exacerbate the consequences of an uncontrolled decomposition. Using the pipe reactor, the reaction volume required by a 2,000 t/d ANS plant is 0.2 m3 , for example, versus 20 m3 for a conventional neutraliser process.
- Low capex: the process only requires a few items of equipment and occupies a limited footprint due to its extreme simplicity. In addition, capital cost is also minimised because the process operates at atmospheric pressure.
- Start-up and shutdown: the plant can be started up from scratch to reach full capacity in less than 30 minutes, all thanks to its limited reaction zone volume. Shutdown occurs almost immediately once the raw material feed valves are closed.
Condensate purification
The AN2000™ pipe reactor process – which already has a low contaminated liquid stream due to its intrinsic design – can be easily upgraded to eliminate the discharge of waste effluent. The treatment is relatively simple: a venturi scrubber and a cyclonic column are used to remove traces of ammonia, nitric acid, and ammonium nitrate from steam released by the pipe reactor.
Casale’s Purifier Exchanger can be used for further purification without the need for an external energy source. This specially designed shell-and-tube heat exchanger is used to partly vaporise concentrated process condensates from the ammonia and nitric acid heaters. Within the heat exchanger, excess process steam flowing within the tubes is used to vaporise condensates fed to the shell side (Figure 3).
The clean vapour generated via vaporisation of the condensate contains less than 30 mg/kg of ammonium nitrate and it is eventually re-condensed in a water cooler. The remaining concentrated condensate can be recycled as make-up water to the initial scrubbing system and the nitric acid absorption towers. The clean condensate, meanwhile, can be reused elsewhere in the plant as clean water or discharged. It can also be partly used to dilute the ammonium nitrate content of the concentrated condensate recycled to the nitric acid plant.
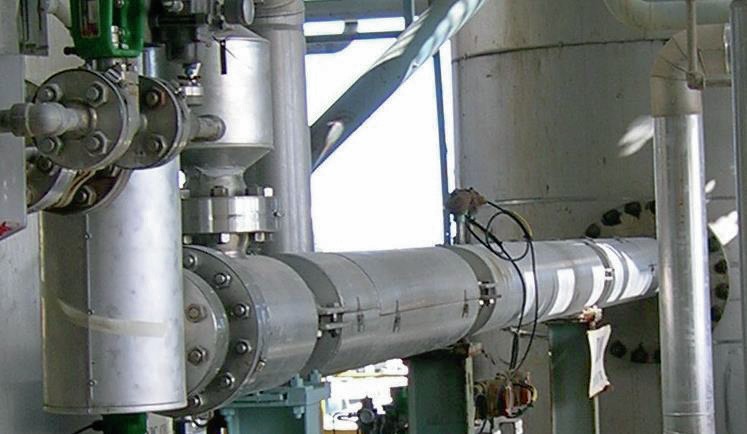
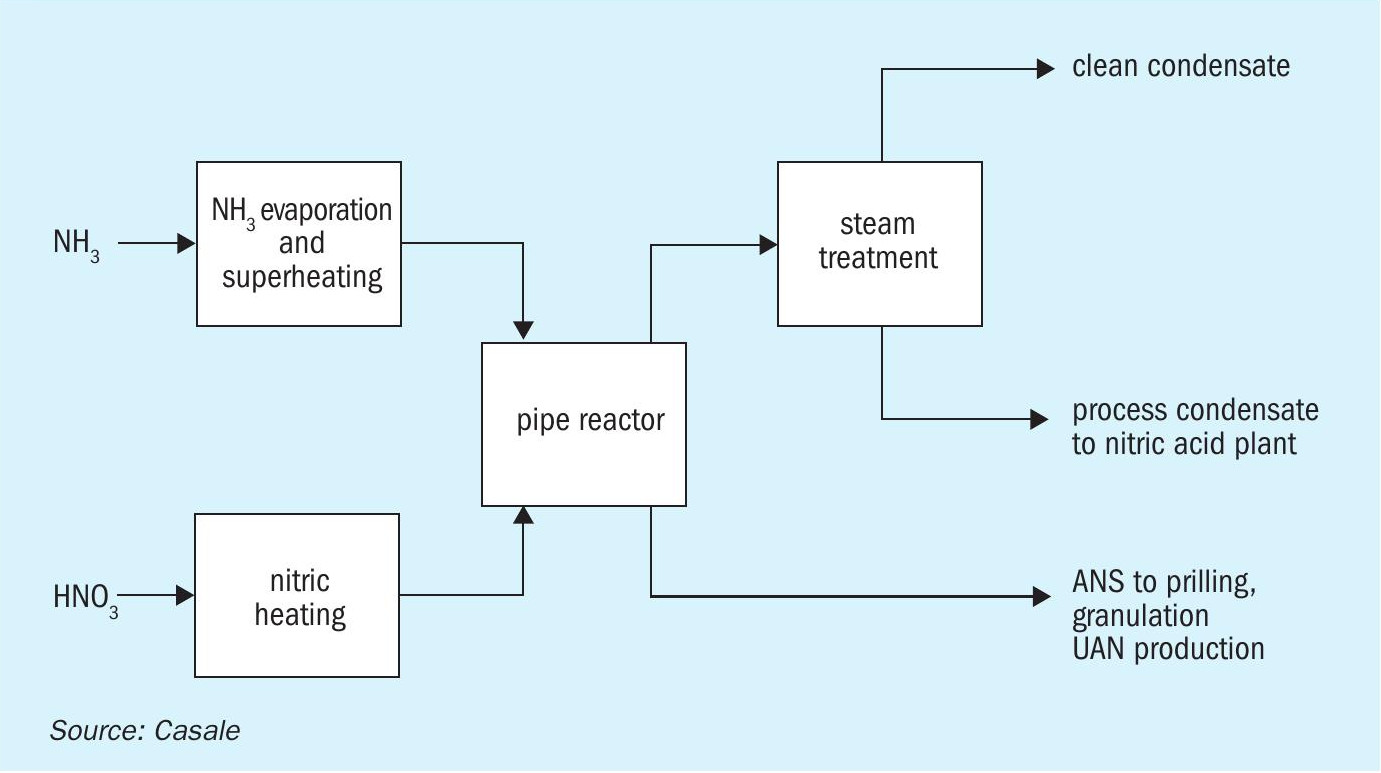
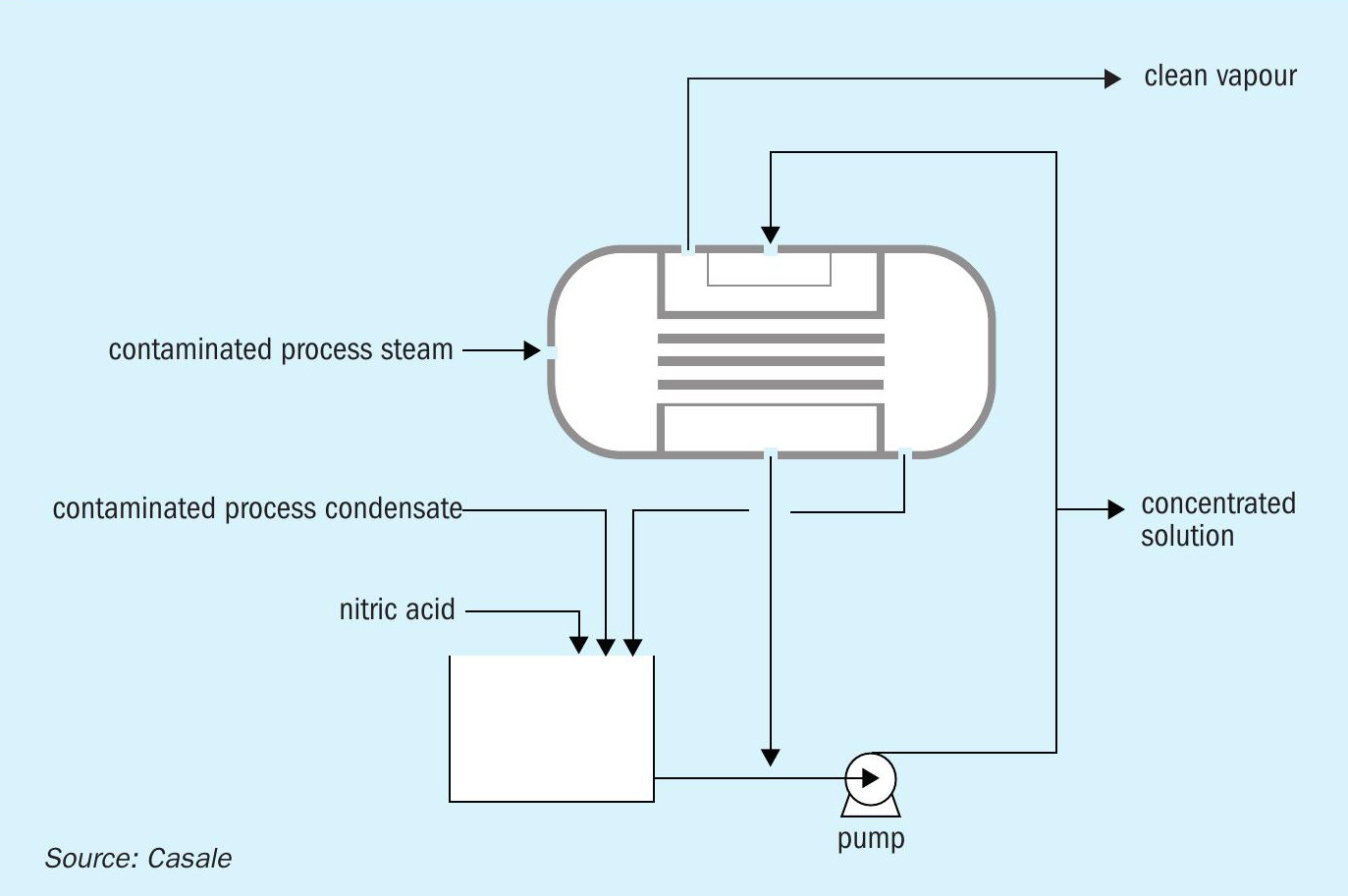
CASE STUDY: JSC Navoiyazot nitric acid plant
Casale is able to provide a complete production line for nitric acid and ammonium nitrate solution (ANS) that fully complies with the most stringent emissions and liquid waste regulations.
The following Uzbek case study illustrates how emissions reduction programmes are now being rolled out and applied – even in countries which do not impose limits on N2 O emissions currently.
In 2020, Casale completed an engineering, procurement and construction (EPC) project for a new nitric acid plant for JSC Navoiyazot in Uzbekistan (see photo). Casale’s scope of work for this dual-pressure technology unit – based on the company’s NA2000™ process – extended beyond nitric acid production to encompass all the other utilities required at the site. This included the start-up boiler, nitric acid storage tanks, cooling water facilities, demi water unit and the water treatment plant.
Casale also provided JSC Navoiyazot with an effective emissions abatement system for the new 1,500 t/d capacity nitric acid plant. This was designed to reduce emissions in line with limits specified by the client:
- NOx <50 ppmv
- NH3 <5 ppmv
- N2 O <50 ppmv.
These emissions limits go beyond Uzbekistan’s statutory requirements. Furthermore, the actual reductions achieved on completion of the project far exceeded the client’s original expectations – as the installed abatement system actually reduced N2 O and NOx emissions to below 10 ppmv and 25 ppmv, respectively.
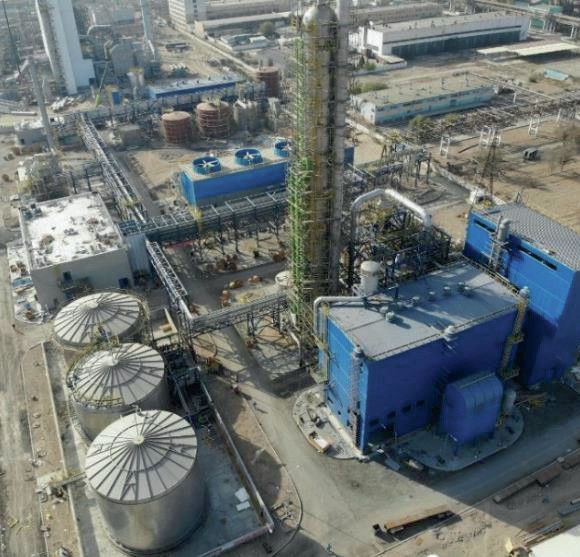
The catalytic system installed at the new JSC Navoiyazot nitric acid plant combines integrated secondary and tertiary abatement. The design of the burner basket used for secondary abatement ensures enough secondary catalyst (deN2O) is available to deliver substantial N2 O abatement underneath the gauzes. The Casale tertiary catalyst (GPRN20), meanwhile, was installed directly upstream of the tail gas expander. It operates at 430°C to ensure the decomposition of both residual N2 O from the secondary catalyst and NOx residue from the absorber. The pressure drop of the entire tertiary abatement system was limited to less than 120 mbar. Its optimised design also guarantees a proper gas distribution across the catalyst.
Special operating procedures and control loops were implemented at the Uzbek plant to achieve the emissions targets.These avoid overdosing ammonia to the tertiary catalyst and minimise ammonia slip (<2 ppmv).
Minimising ammonia slippage prevents unsafe operations by ensuring that no ammonium nitrate is formed during start-up. Additionally, NOx concentration in the tail gas is kept below the limit of stack plume visibility during both normal operation and start-up.
The proven GPRN20 tertiary catalyst used with this system has been successfully applied in similar applications worldwide – with a track record of long and trouble-free performance. Feedback after several years of continuous operation at another nitric acid plant commissioned by Casale has been extremely positive. This abatement system has recorded almost 98.5 percent N2 O conversion and NOx emissions lower than 10 ppmv.
Thanks to its remarkably high N2 O conversion, Casale’s tail gas treatment system should provide JSC Navoiyazot with a shorter return of investment due to the higher payback from carbon trading.
Casale long experience in the design of catalytic reactors for ammonia synthesis has also contributed to their successful performance in nitric acid applications, including:
- Maximum abatement efficiencies with low emissions levels
- Optimal gas distribution within the catalyst bed to ensure longer service life
- Reduced pressure drops over the reactor and minimised compressor energy loss.
The Purifier Exchanger typically generates clean and concentrated condensates at a mass ratio of 2:1, respectively. By substantially reducing the volume of liquid waste, this allows liquid effluents to be managed economically at ANS plants.
In some cases, the recycling of concentrated condensate may not be a viable option at the client’s complex, e.g., when the nitric acid plant at the site is not available, or the nitric acid produced has a dual use as raw material for both fertilizers and chemicals. These issues can be overcome by installing two Purifier Exchangers in series to double purification capacity and boost clean steam generation.
A reverse osmosis package can also be added to treat the concentrated condensate stream. These treatment options, by reducing the amount of concentrate condensate to a suitable level, allows their internal reuse in the venturi scrubber and cyclonic column. The end result is an ANS plant that produces virtually no liquid effluents.
Due to its intrinsic design, the AN2000™ pipe reactor process does not release any gaseous emissions, as the steam generated is fully condensed, either as heating steam for the raw materials, or in the Casale purifier and cooling water condenser. As a consequence, virtually no vapour streams are released to the atmosphere.
STAMICARBON
The world’s first renewable-powered nitrate fertilizer plant
Stamicarbon is developing the world’s first commercial-scale, renewable-powered nitrate fertilizer plant in Kenya. This will have the capacity to produce 550 t/d of calcium ammonium nitrate (CAN) or NPK fertilizers. This innovative plant (see photo) is being built by three Maire Tecnimont subsidiary companies – MET Development, Stamicarbon and NextChem – at the Oserian Two lakes Industrial Park, near Lake Naivasha, 100 kilometres north of the capital Nairobi (Fertilizer International 503, p9;Nitrogen+Syngas 374, p30).
The renewable power-to-fertilizer plant incorporates new Stami Green Ammonia technology (Fertilizer International 504, p20) and the company’s existing nitric acid technology. Front end engineering design (FEED) is scheduled to start later this year with construction due to follow in 2023. The new plant is expected to start operating commercially in 2025.
Efficient, reliable, compact and modular
At the heart of Stamicarbon’s novel green ammonia technology is a high-pressure ammonia synthesis loop (synloop) operating at approximately 300 bar (Figure 1). This has been customised to deliver the most efficient small-scale plant design. The synloop’s innovative design allows ammonia to condense with the cooling water, eliminating the need for a refrigerating compressor. As a result, the plant operates using just one proven and reliable electric-driven reciprocating multiservice compressor.
Stami Green Ammonia technology also offers the following key features:
- Capex efficiency
- Lean, compact, modular design
- High plant reliability with a proven track record and strong reference base
- Full compliance with environmental standards.
The minimal amount of equipment needed to operate the plant delivers a substantial capex saving – generally an important consideration for small-scale projects. Four plants are currently operating with this innovative, small-scale technology, in addition to the Kenyan project announced last year.
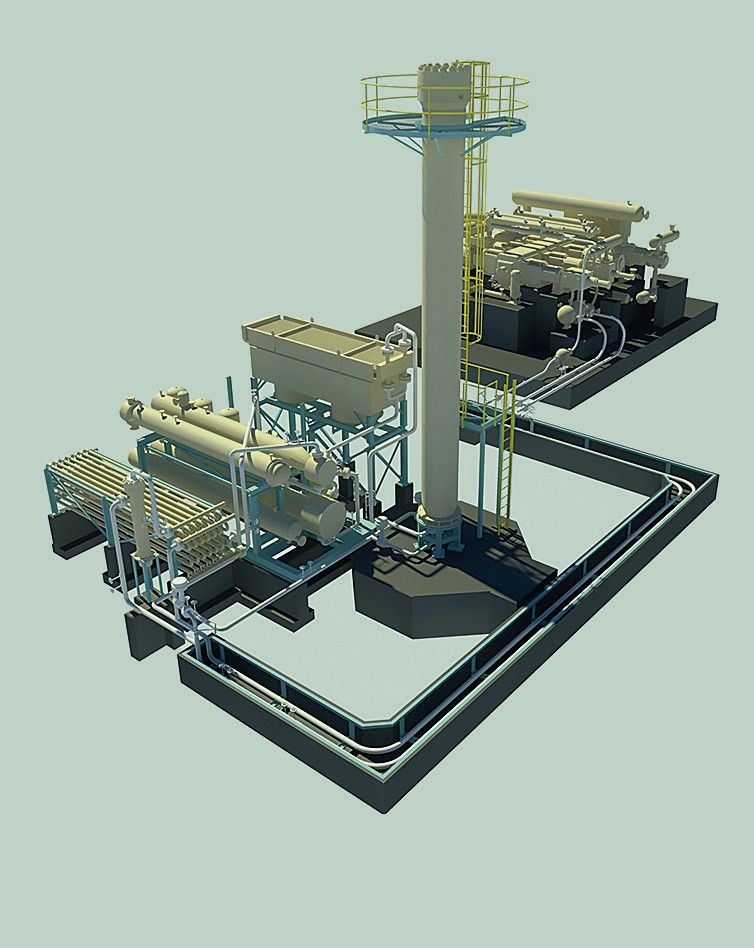
Overall, this technology package offers a viable and competitive option for the local and small-scale production of green ammonia. When used in combination with Stamicarbon’s existing urea and mono-pressure nitric acid technologies, it can produce ammonia-based fertilizers such as green ammonium nitrate and greener urea (using recycled or recovered CO2 ). By applying this same technology to blue ammonia and urea production, Stamicarbon also plans to help other industries such as steelmaking become more sustainable.
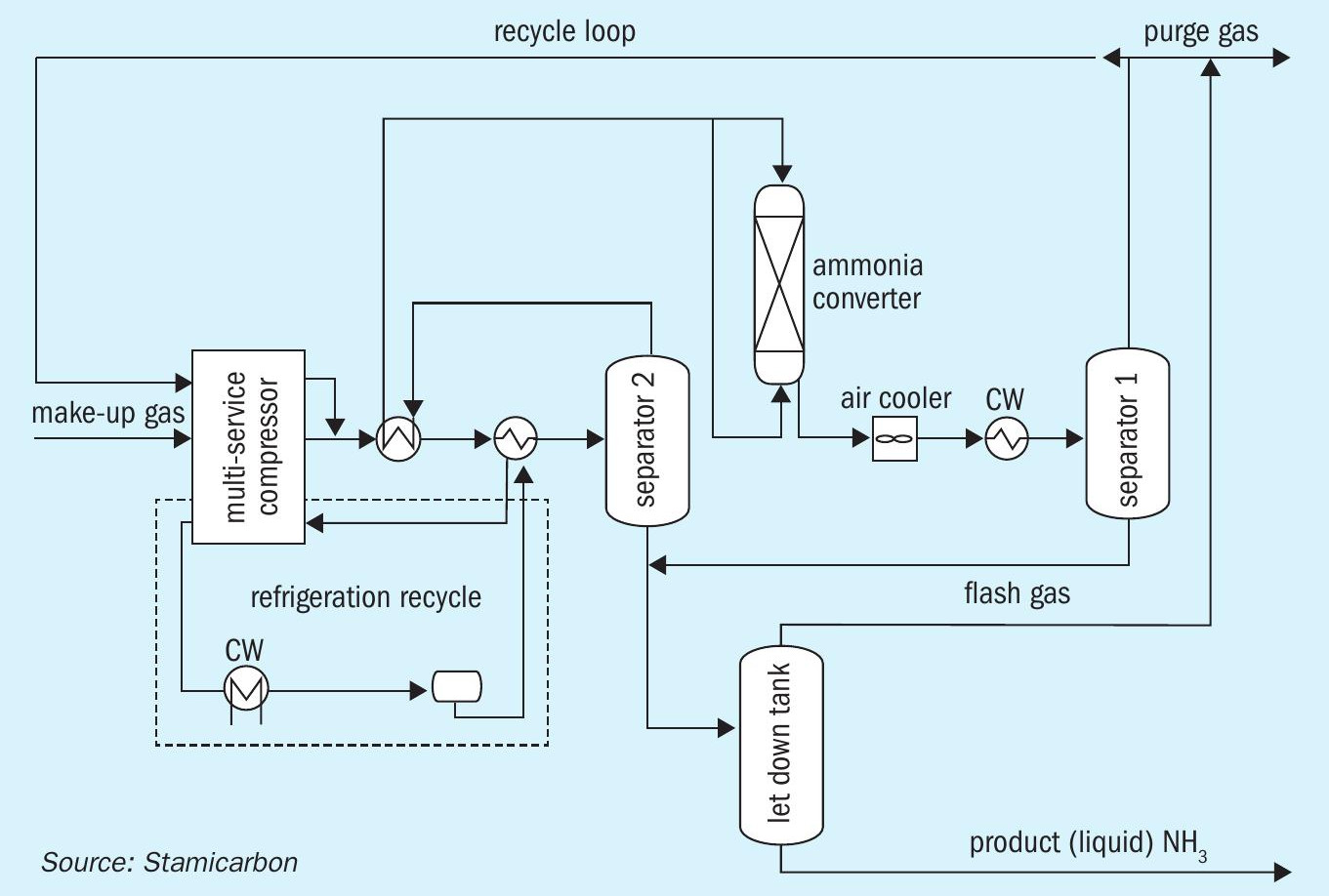
Kenyan power-to fertilizer plant project
The Lake Naivasha plant, which is located next to Kenya’s largest geothermal energy basin, will require around 70 MW of renewable power. It will also be partly powered by on-site solar electricity generation. Switching to production based on renewable energy is expected to cut carbon emissions by 100,000 t/a, compared to an equivalent gas-based fertilizer plant.
This first-of-its-kind green fertilizer plant will help secure the availability of domestically-produced fertilizers in Kenya throughout the country’s agricultural season. On completion, the plant’s production output should reduce Kenya’s import dependency for nitrogen fertilizers by around 25 percent, as well as improving domestic fertilizer affordability and availability.
Conclusions
In summary, Stami Green Ammonia technology provides a ‘futureproof’ gateway to carbon-free ammonia production and, importantly, delivers a sustainable and renewable feedstock for the production of nitrogen fertilizers. By demonstrating the viability of the renewable power-to-fertilizer concept today, this Kenyan pathfinder project is expected to pave the way for future projects and growth in green fertilizer production.