Sulphur 398 Jan-Feb 2022
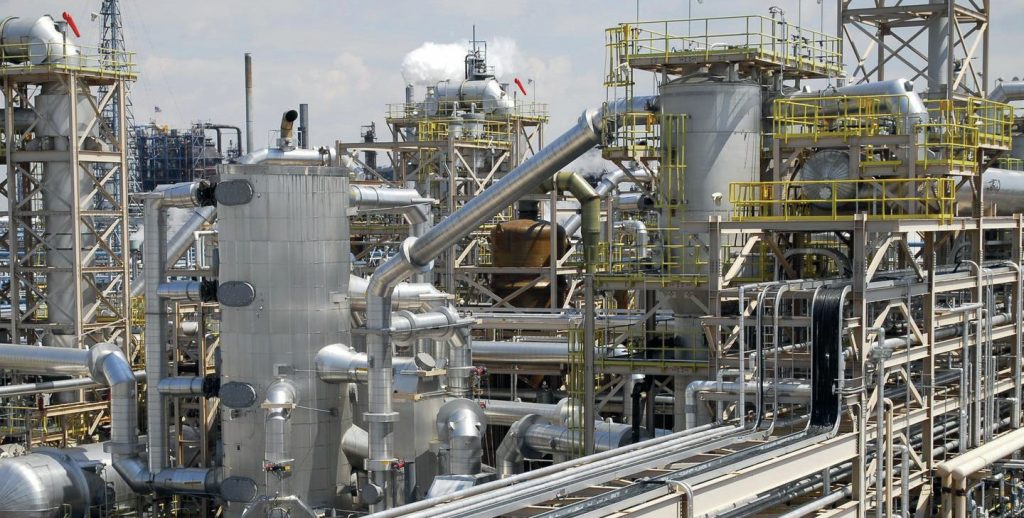
31 January 2022
Sulphuric Acid News Roundup
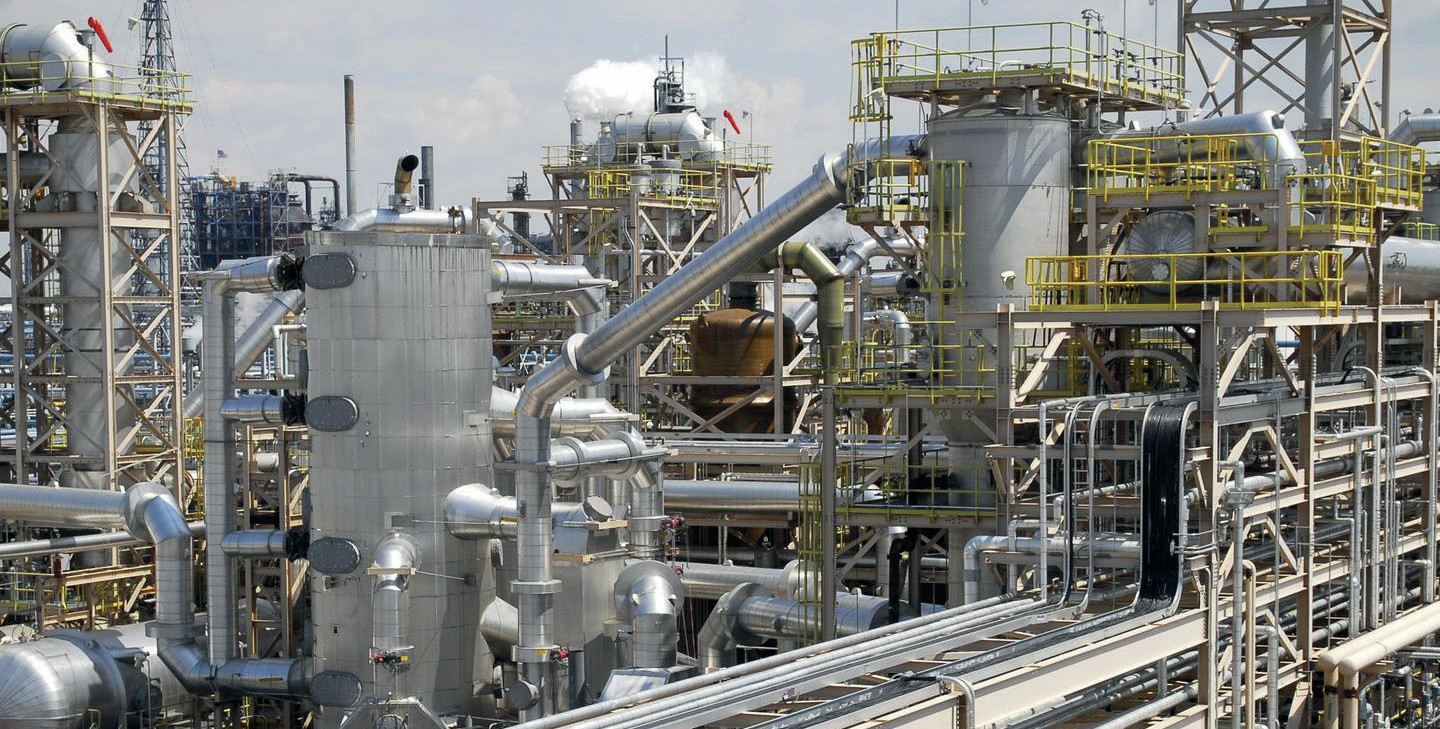
DuPont sells Clean Technologies business
DuPont has agreed to sell its Clean Technologies business for $510 million to an international private equity consortium, comprising BroadPeak Global, Asia Green Fund and The Saudi Arabian Industrial Investments Company (Dussur). The new, independent company has been named Elessent Clean Technologies and will be a global leader in process technologies to drive sustainability and carbon neutrality in the metal, fertilizer, chemical and oil refining industries. Elessent retains exclusive rights to the technologies, expertise, products, and services including: MECS® sulphuric acid and environmental technologies, BELCO® scrubbing technologies, STRATCO® alkylation technology and IsoTherming® hydroprocessing technology. Derived from the words “element” and “essential,” Elessent says that it will help customers produce, optimise or separate essential elements every day, creating clean alternatives to traditional industrial processes to minimise the impact on the environment while enabling our customers to produce essential elements critical to everyday life.
The sale is part of a restructuring of DuPont following the merger of its nutrition and biosciences unit with International Flavors & Fragrances (IFF). DuPont’s executive chairman and CEO Ed Breen said: “DuPont today is a premier multi-industrial company, well equipped to drive organic growth and expand our businesses through select and targeted mergers and acquisitions.”
“We are excited about what the future holds for us as a standalone company,” said Elessent CEO, Eli Ben-Shoshan, “The strong global expertise of the Group will accelerate our mission to deliver the technology and tailored solutions our customers need to more efficiently produce cleaner products for the world.”
FINLAND
Smelter shut down by slag explosion
Swedish mining and metallurgical company Boliden says that nickel production at its Harjavalta smelter in southwestern Finland has been stopped due to a slag explosion that was the result of a process malfunction in the nickel electric furnace slag tapping system on December 24th. The company said that no one was injured as a result of the explosion and that the main damage is in the mechanical construction and the slag tapping system. Boliden added that production in the nickel line has been stopped and is estimated to be offline until mid-January. According to the company’s statement, estimates on the impact on earnings lost due to the lost production and repair costs is $11 million.
Boliden Harjavalta is the only nickel smelter in Western Europe. It produced 770,000 tonnes of sulphuric acid in 2020.
Metso Outotec to divest its Metal Recycling business
Metso Outotec has signed an agreement to divest its Metal Recycling business line to an affiliate of Mimir, an investment company based in Stockholm. The closing of the transaction is expected to take place during the first half of 2022. The parties have decided not to disclose the value of the transaction. The business sold to Mimir includes the brands Lindemann and Texas Shredder. The business will change name in conjunction with the divestment and operate globally under the Lindemann brand, with headquarters in Düsseldorf, Germany. Its current approximately 160 employees will transfer to the new company in connection with the transaction. The net sales of the business totalled e77 million in 2020.
“We are delighted that going forward, the Metal Recycling business will continue to implement its strategy together with the new owner Mimir. As an established standalone company, its full focus will be on the metal recycling markets and customers,” says Piia Karhu, Senior Vice President, Business Development and Metal Recycling business line at Metso Outotec.
AUSTRALIA
Feasibility study for large scale sulphuric acid plant
SNC-Lavalin says that it has been commissioned to undertake a definitive feasibility study for Verdant Minerals Pty Ltd on their Ammaroo Phosphate Project in Australia’s Northern Territory. SNC-Lavalin will provide engineering and procurement services to assess the feasibility of a 4,500 t/d sulphuric acid plant which will be part of a fully integrated mine and downstream processing facility to produce ammonium phosphate fertilizers. The company says that the planned sulphuric acid plant will utilise MECS® technologies to minimise SO2 emissions, making it more sustainable in the longer term. MECS® Heat Recovery System technology will also be used to recover medium pressure steam from the sulphuric acid plant, providing the majority of energy requirements for the site and removing the need to have additional sources of energy. This will maximise energy efficiency while reducing the overall facility’s reliance on energy supply from external sources and overall lessen its carbon footprint. Initial development of Ammaroo could produce in the order of 2 million t/a of phosphate concentrate, with further downstream processing resulting in 500,000 t/a of merchant-grade phosphoric acid for domestic and global markets, according to Verdant.
“We are proud to be working with Verdant Minerals on this project to develop a world class sulphuric acid plant as part of its major new mine and processing development, ensuring the long-term sustainability of its operations,” said Patrick Sikka, Vice-President, North America, Mining & Metallurgy at SNC-Lavalin.
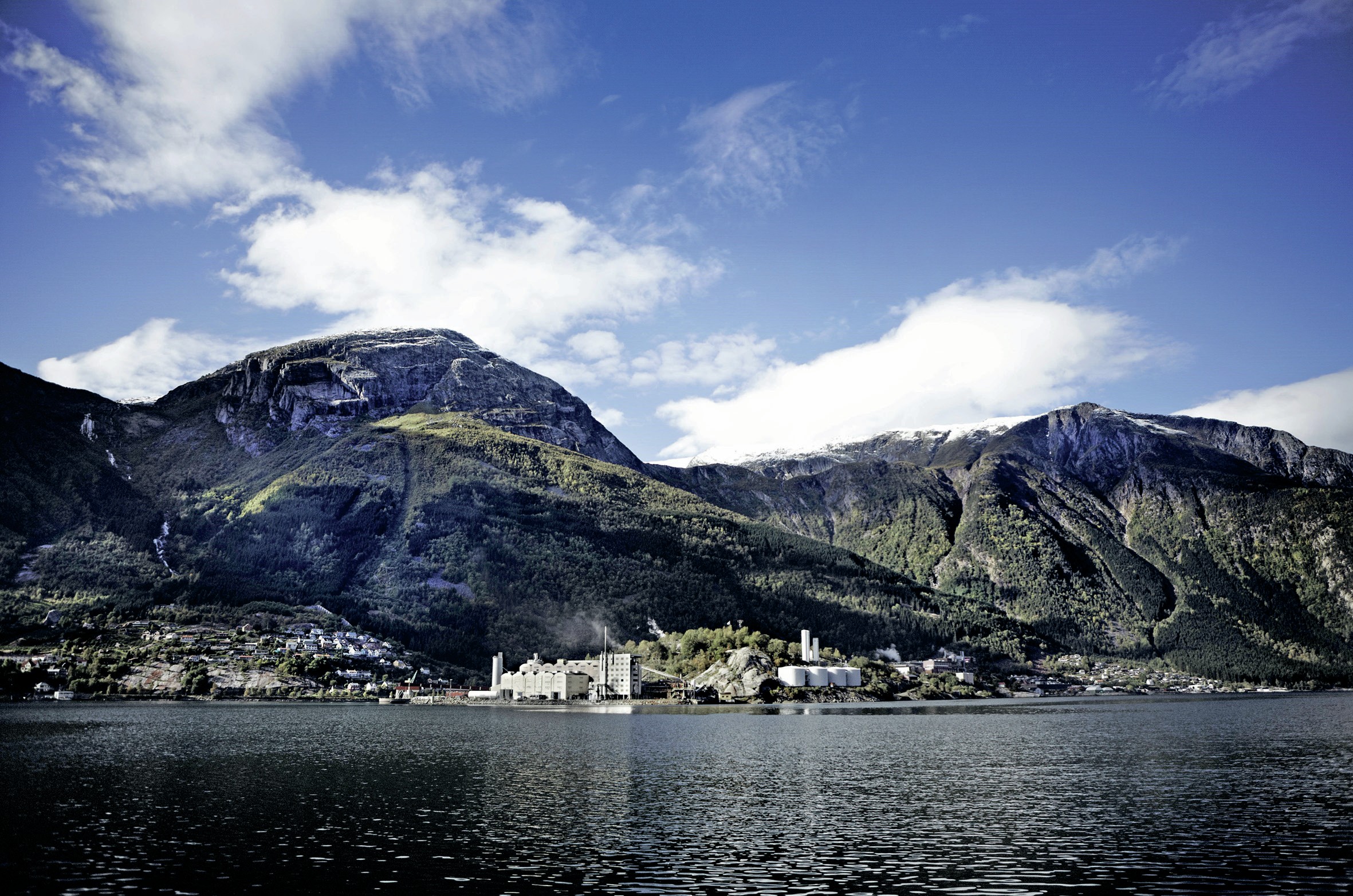
NORWAY
Metso Outotec to license acid plant for zinc smelter expansion
Metso Outotec has been awarded a e150 million contract for the delivery of key technology to the Boliden Odda zinc smelter expansion in western Norway. Boliden Odda is planning to increase its annual production capacity of zinc from 200,000 t/a to 350,000 t/a. Several by-products will also be produced. The project is called Green Zinc Odda, and its energy consumption is based on fossil-free energy. Metso Outotec scope of delivery includes roasting and off-gas cleaning solutions and a sulphuric acid plant. Metso Outotec will also supply hydrometallurgical equipment and technology for calcine leaching, solid liquid separation, solution purification, as well as process and plant engineering and site services. Metso Outotec deliveries will take place in 2022-2024. The company says that its zinc processing technologies consist of several proprietary ‘Planet Positive’ solutions which enable efficient zinc and by-product recovery from a wide range of primary zinc raw material. In the roasting process, even electrical power is produced as a by-product.
“We are very happy for being trusted with this order. The Green Zinc Odda project paves way for more sustainable zinc production and is yet another important milestone in the many years of collaboration between Boliden and Metso Outotec,” says Jari Ålgars, President, Metals business area at Metso Outotec.
INDONESIA
First production from HPAL project
China’s Zhejiang Huayou Cobalt says it has achieved its first trial output of nickel and cobalt mixed hydroxide precipitate from its PT Huayue project on Sulawesi. Zhejiang Huayou is operating the project in partnership with Tsingshan Holding Group and China Molybdenum Co. PT Huayue is designed to produce 60,000 t/a of nickel and 7,800 t/a of cobalt per year using high-pressure acid leach (HPAL) technology. Huayou also has a 20% stake in a larger HPAL project in Indonesia, while another Indonesian HPAL scheme, led by GEM, is targeting start-up in 2022.
Contracts awarded for copper smelter
After the October 2021 groundbreaking ceremony for PT Freeport Indonesia’s new copper smelter at the Special Economic Zone Java in Gresik, a second new copper smelter project is also progressing as PT Amman Mineral Industri (AMIN) has recently finally signed contracts with two major contractors to build AMMAN’s new 900,000 t/a copper smelter and precious metal refinery in West Sumbawa, Tenggara Province. It means that Indonesia will soon have three copper smelters – PT Smelting Gresik, which has been operating as the single domestic smelter since 1996, plus the new Freeport and AMMAN smelters.
The contracts were signed between AMIN and China Non-Ferrous Metal Industry’s Foreign Engineering and Construction Company (NFC) as well as PT Pengembangan Industri Logam in December 2021. NFC will be the main contractor supplying materials and equipment for the copper smelter. The technology and patented equipment for the project will be procured from prominent original equipment manufacturers around the globe, including MECS for the gas cleaning and sulphuric acid plants.
NFC’s President Qin Junman, said: “As one of the top international contractors, NFC has successfully completed numerous projects, including copper smelters with the latest technology. We are confident that we will build this project into a world-class one with the help and support from the government, AMMAN, and our partners. During the Covid-19 pandemic, the project will be very challenging. However, we want to ensure that all necessary resources are available for smooth, successful, and on-schedule project implementation.”
Tsingshan starts producing nickel matte
China’s Tsingshan Holding Group says it has officially started producing nickel matte in Indonesia for electric vehicles. The company is making matte from stainless steel raw material nickel pig iron (NPI) and nickel sulphate, an alternative route to battery-grade nickel to the high-pressure acid leach (HPAL) process which is also aiming to be used by Tsingshan and several other companies in Indonesia. Tsingshan said in March 2021 it planned to sell 60,000 tonnes of matte to Huayou and another 40,000 tonnes to CNGR within a year of first production.
RUSSIA
Nornickel expects Sulphur Programme completion in September
Nornickel says that it has made significant progress with delivery of large-scale equipment as part of its Sulphur Programme in Norilsk. The programme includes an investment of over $4 billion to capture emissions at the Nadezhda and Copper plants with intermediate production of sulphuric acid with a high rate (>99%) of sulphur dioxide recovery. As of the beginning of December 2021, more than 700 tonnes out of the planned 7,000 tonnes of various equipment items had already been installed at the site. The assembly of ball mills at the calcium hydroxide production section that will make the powder for this important solution is currently underway. The sulphuric acid generated as part of Nornickel’s metallurgical operations will be recovered and neutralised using the calcium hydroxide solution (‘milk of lime’) to produce gypsum.
Contractor Velesstroy has already installed the largest section of the ball mills; a drum weighing 28 tonnes. Heat exchangers for the sulphuric acid production section – the biggest project units, weighing over 200 tonnes each – are expected to arrive at Dudinka Port soon. In the near future, the company says that it plans to complete thermal envelopes at the slaked lime and sulphuric acid production sections. Plans for the next three months include the construction of building frames and thermal envelopes at three other key facilities of the Nadezhda Metallurgical Plant.
“The list of equipment is extensive and includes chemical, mechanical and process units. They come together with a wide range of auxiliary systems, from ventilation to water supply and water treatment. This will be the most advanced facility to be launched within the Sulphur Programme. We are planning to complete the full process cycle, including start-up operations, in September 2022,” said Pavel Zhigulin, Senior Manager of the Sulphur Programme Project Management Office at Nadezhda Metallurgical Plant.
SOUTH AFRICA
Start-up for Elandsfontein phosphate plant
Kropz says this it has achieved a major milestone with the first introduction of phosphate ore to the beneficiation plant at the company’s Elandsfontein mine in South Africa. Team is now ensuring that alle front end circuits are balanced and running stably. The flotation circuits will then be commissioned and the reagents added in due course for the production of the first concentrate. Commissioning activities will transition into full scale ramp-up of the mining and beneficiation plant over the coming six months. Mining activities commenced in October 2021, and significant volumes of ore are available to support the commissioning ramp-up.
CEO Mark Summers said: “The introduction of ore to the processing plant reflects the successful culmination of the construction phase and signals the commencement of the next chapter in the Company’s development. I would like to express my gratitude and appreciation for the tireless efforts of all of those involved in reaching this milestone safely and on time, despite the many challenges that the past two years have presented.”
Transnet has provided the Company with a draft port access agreement to support the long-term export of Elandsfontein’s phosphate rock through the port of Saldanha. First phosphate rock exports from Elandsfontein are expected in Q1 2022.
PHILIPPINES
Sumitomo increases share in Coral Bay Nickel Corporation
Sumitomo Metal Mining Co., Ltd. (SMM) says that it has reached an agreement with Mitsui and Sojitz for the purchase of shares in the Coral Bay Nickel Corporation. Sumitomo is buying Sojitz 18% shareholding in the company, as well as the 18% owned by Mitsui subsidiary Mitsui & Co. Mineral Resources Development (Asia) Corp. (MMRDA), at a total cost of $164 million. The purchase will take SMM’s share in the company from 54% to 90%. The remaining 10% of shares are held by the Nickel Asia Corporation. Based on the assumption that all necessary permits and approvals are acquired, the sales of the shares are planned to be completed by the end of January 2022.
Coral Bay is a major nickel high pressure acid leach (HPAL) plant, and began commercial operations in 2005.
CHILE
Project for copper tailings treatment
Researchers at Chile’s Pontifical Catholic University are working on a project called Tailings to Construction Materials (T2CM), which aims to transform copper tailings into high-quality polymers and cements. The project is part of BHP’s Tailings Challenge and is backed by DITUC, a research centre; Melon, a leading cement company; Eral, an engineering firm; the Paris Geo-polymer Institute; and Noracid, a manufacturer of sulphuric acid. T2CM’s goal is to transform all tailings produced at a given operation into usable components for buildings by using cleaning/extractive processes to recover copper and molybdenum as well as sulfuric acid. As well as reducing the accumulation of tailings, the process would also drastically reduce the almost one tonne of CO2 that is released into the atmosphere per tonne of cement produced using conventional techniques. It involves transporting fresh tailings to a nearby or on-site treatment facility, fine grinding and particle size classification of the tailings for surface activation, as well as rougher sulphide flotation to obtain a desulphurised material and a sulphur poly-metallic concentrate. The sulphur-enriched material is then separated into copper sulphide and a pyrite fraction by flotation, and the pyrite-enriched concentrate goes to a roasting step for sulphur removal and sulphuric acid production. Finally, the iron oxide desulphurised material is used to develop construction materials.
TUNISIA
Tunisia records major phosphate export boost
Tunisia’s National Institute of Statistics says that the country’s monthly trade deficit narrowed to $467 million in November 2021. Partly this was explained by a fall in imports of oil, gas and raw materials, in spite of a 20% increase in capital goods imports. But it was helped by a major increase in exports from the mining, phosphate and derivatives sector of 51% for the month. In particular, exports of phosphoric acid to Algeria were up by 90%.