Nitrogen+Syngas 376 Mar-Apr 2022
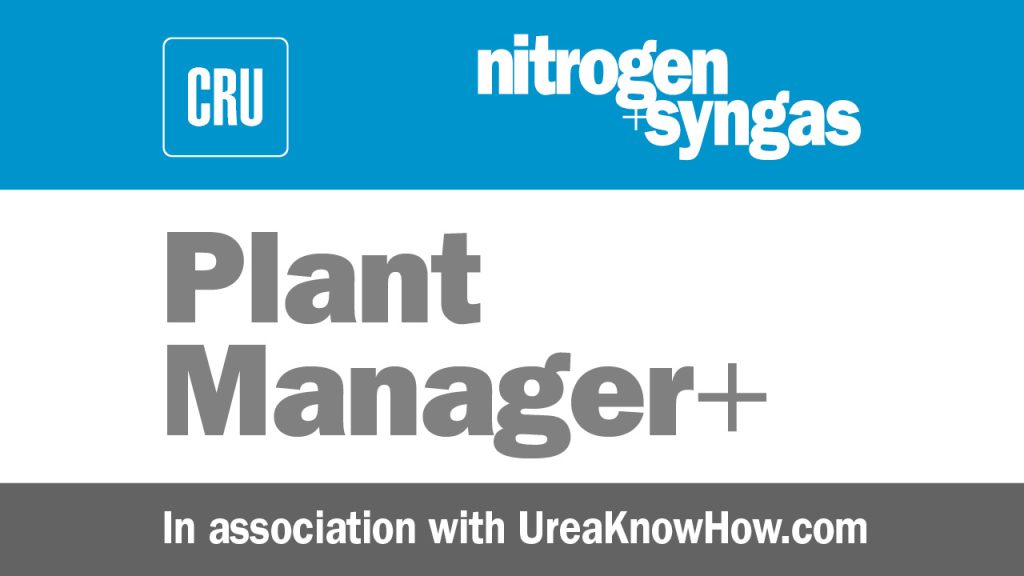
31 March 2022
Incident No. 6: Corrosion in gasket area
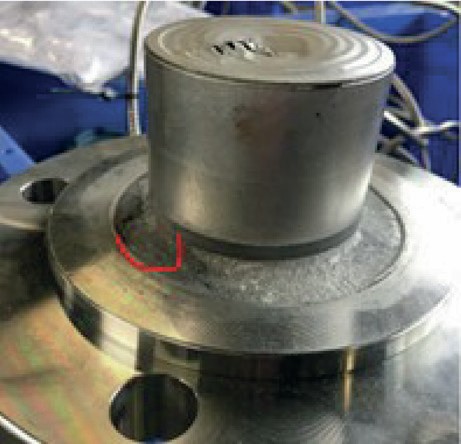
Warning signs and immediate response
Finding corrosion upon inspection during a turnaround prompted immediate replacement of the transmitter.
Causes
A chromium oxide layer should protect the material from high corrosion rates. A continuous supply of fresh oxygen should be secured at any wetted surface to assure this chromium oxide layer. Here one sees severe corrosion phenomena in the gasket area, which means that ammonium carbamate could enter between the gasket and the flange face. The oxygen in the trapped ammonium carbamate liquid will be consumed and at a certain moment instead of passive corrosion, active corrosion starts with a corrosion rate which is much higher. The chromium content of Hastelloy C276 is too low to assure a passive chromium oxide layer under these circumstances. In case a weld is applied in these areas, the heat affected zones are typically even more sensitive to corrosion.
Consequences
Potentially a leak can occur resulting in loss of containment.
A subsequent unplanned shutdown could cost >$1 million.
Prevention safeguards
1. Perform corrosion inspections during the turnaround.
2. Apply better materials like 25-22-2 (or zirconium) in these critical areas.
3. Proper gasket design, conditions, installation, and torquing are critical factors to avoid these problems.
Mitigation safeguards
In case of a leak, confirm and locate the leak, shut down the plant and drain the synthesis section as soon as possible.
Comments
Hastelloy C276 is not a suitable material for this application, typically 316L or 25 -2 2-2 is applied in these sections. When applying 316L stainless steels the gas phase should be properly traced and insulated to avoid condensation corrosion and crystallisation of carbamate. The tracing should be such that the temperature of the diaphragm is higher than the condensation temperature of carbamate at the operating pressure.
A brownish colour is normal, there could be oil or some chromium/iron oxide products from the unavoidable passive corrosion of stainless steels in carbamate solutions. In the gas phase one typically sees some blueish colour.
The damage to the diaphragm itself shown in the picture appears to be mechanical damage (external impact) or may have happened during removal of the transmitter from the process. Proper care when removing and installing these instruments is advisable.
This case study report is taken from UreaKnowHow.com’s Fertilizer Industry Operational Risks Database, FIORDA.