Sulphur 399 Mar-Apr 2022
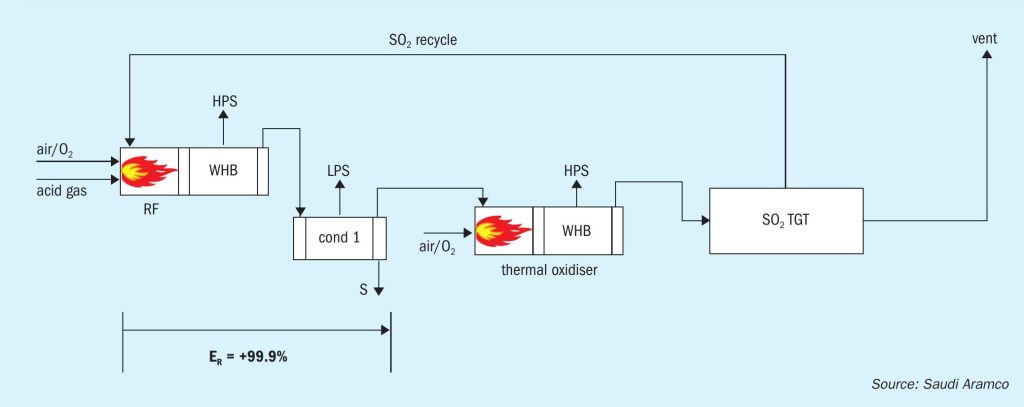
31 March 2022
Simplified sulphur recovery technology
SULPHUR TECHNOLOGY
Simplified sulphur recovery technology
A new cost-effective alternative sulphur technology, providing a simple and robust process to achieve an overall sulphur recovery efficiency of 99.9+% is being developed by Saudi Aramco. J. P. O’Connell and I.A. Alami of Saudi Aramco discuss the new technology, its benefits and current stage of development.
The emission regulations for sulphur dioxide (SO2 ) continue to become more stringent with time, which is placing more pressure on the refineries and gas plants to increase the recovery efficiencies of their existing sulphur recovery units (SRUs). In many countries around the world, this equates to either upgrading an existing facility or designing a grassroots SRU to be able to achieve an overall recovery efficiency of 99.9+% on a daily basis. This typically results in adding a tail gas treatment (TGT) unit behind the Claus plant, which increases the cumulative recovery efficiency from between 95 to 98% to the required 99.9+%. The addition of the TGT requires major capital investment and significantly increases the operating costs of the SRU. It is for these reasons that a cost-effective alternative for achieving a sulphur recovery efficiency of 99.9+% will always be a welcome addition to the existing choices of sulphur technologies.
SSRT
The basis of the new Saudi Aramco Simplified Sulphur Recovery Technology (SSRT) is the deletion of the traditional Claus and TGT catalytic stages. Each catalytic stage includes a reheater, a catalytic converter/reactor and a condenser/cooler. The new SSRT technology, therefore, represents a reduction in equipment of three heat exchangers (i.e., two Claus condensers and one TGT cooler), three catalytic beds (i.e., two Claus converters and one TGT hydrogenation reactor) and three reheaters (i.e., two Claus reheaters and one TGT reheater). These deletions result in savings in both capex and opex.
The front end of the SSRT configuration includes a thermal stage consisting of a reaction furnace connected to a waste heat boiler (WHB), followed by a single condenser for removing the sulphur product. The process gas from the condenser is further processed in a thermal oxidiser (TOX), which converts all sulphur compounds, i.e., H2 S, COS, CS2 , sulphur vapour, and entrained liquid sulphur, to SO2 . There is a second WHB downstream of the thermal oxidiser that generates additional HP steam.
The cooled flue gas from the TOX/WHB is then processed in a regenerable SO2 TGT unit, which allows for absorption and recycle of the SO2 back to the reaction furnace. Currently, two commercialised regenerable SO2 absorption technologies are available. These units include a direct contact condenser, absorber, and regenerator.
Oxygen enrichment can be utilised in both the reaction furnace and the thermal oxidiser.
The patented SSRT process (Fig. 1) takes advantage of the fact that typical conversion of H2 S to elemental sulphur in the Claus plant reaction furnace ranges from 50 to 75%. The remaining sulphur compounds that would normally be converted to elemental sulphur in the downstream traditional Claus catalytic converters and H2 S in the TGT hydrogenation reactor are, instead, sent directly to the TOX for combustion to SO2 . Due to the quantity of combustible sulphur compounds remaining in the condenser tail gas stream, no fuel gas is needed in the TOX to maintain normal operating temperatures.
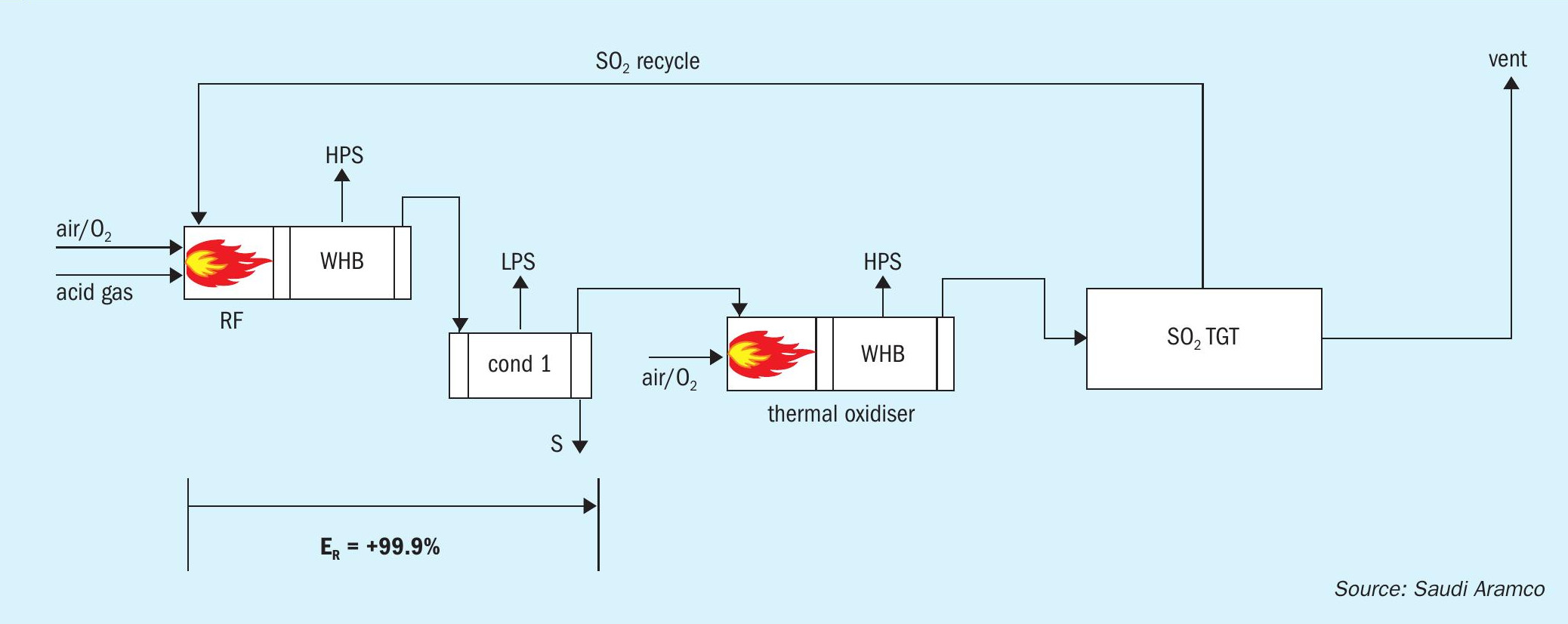
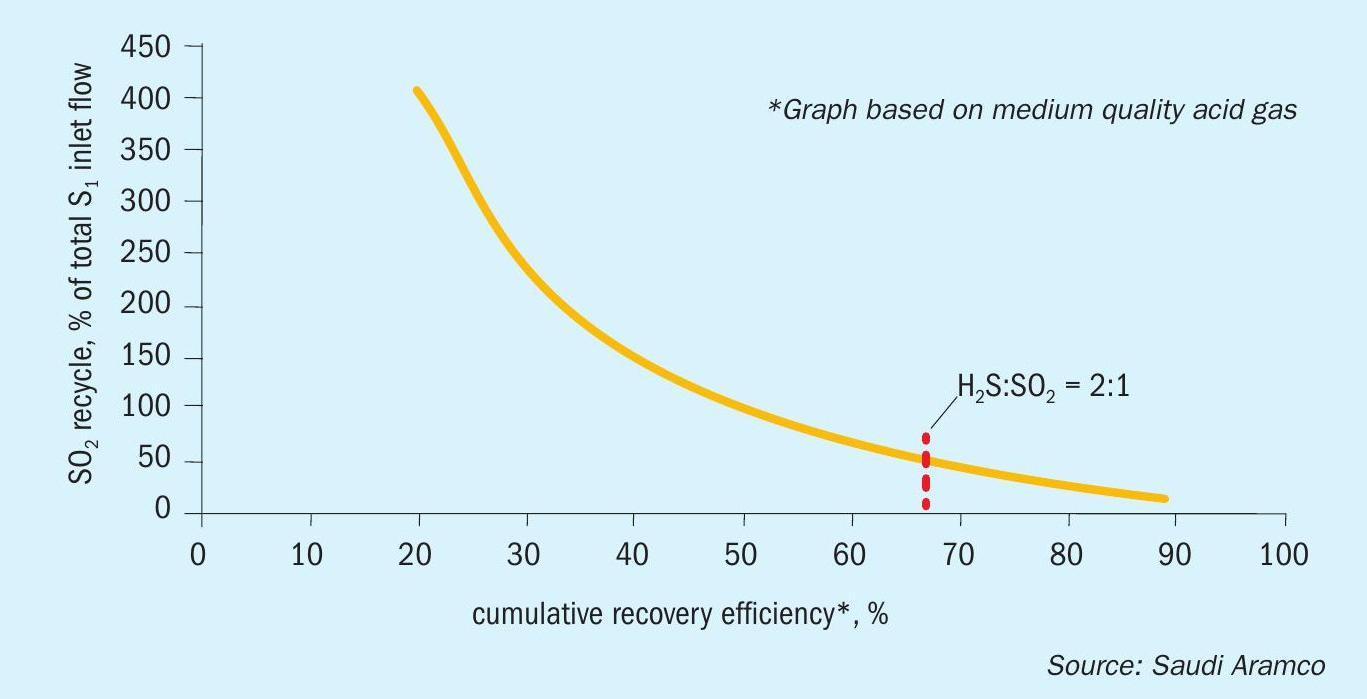
It is not immediately apparent how overall recovery efficiencies of 99.9+% can be achieved when there is only a thermal stage for the Claus reaction to occur. The explanation is in the differentiation between unit conversion efficiency of the thermal stage and cumulative conversion efficiency based on the amount of equivalent inlet sulphur in the feed gas streams. For example, if the feed stream contains 100 mol/h of H2 S and the SO2 recycle is 50 mol/h, and the condenser produces 99.9 moles of S1 equivalent, the unit conversion efficiency is 99.9/(100+50) = 66.6%, while the cumulative conversion efficiency is 99.9/100 = 99.9%.
It should be noted that the sulphur degassing unit liquid feed stream may have an H2 S content as high as 700-1000 ppmw, which is higher than the traditional value of approximately 300 350 ppmw, due to the liquid sulphur being in contact with a high H2 S concentration process stream in the condenser and should therefore be designed accordingly.
Thermal stage Claus reaction
The SO2 that is recycled to the reaction furnace takes part in the Claus reaction to produce elemental sulphur. What is not well known, regarding the reaction furnace, is that the reaction of H2 S and SO2 at typical reaction furnace temperatures, i.e., between 1,000°C and 1,350°C, is slightly endothermic2 . The SSRT process therefore requires co-firing of fuel gas to sustain the required temperatures for the Claus reaction to proceed, while ensuring that all acid gas contaminants are adequately destroyed. The industry rule of thumb for achieving acceptable BTEX and NH3 destruction is 1,050°C and 1,250°C, respectively, along with an adequate reaction furnace residence time, high intensity main burner and combustion chamber checker/HexWall.
Process stoichiometry
In order to optimise the Claus reaction in the SSRT reaction furnace, the traditional H2 S:SO2 ratio of 2:1 must be maintained. Process simulations of the SSRT with high SO2 recycle quickly revealed that this can only be maintained if the reaction furnace conversion efficiency is greater than 66.7%. If the reaction furnace does not obtain a minimum conversion of 66.7%, the H2 S:SO2 is forced below 2:1 and a downward “spiralling” effect in conversion efficiency is observed involving higher SO2 recycle rates and a corresponding requirement of higher fuel gas flow to maintain reaction furnace temperatures. This has an exponentially negative effect on both capex and opex.
This phenomenon therefore limits the use of the first patented SSRT configuration to SRUs that process a high quality acid gas stream, i.e., refineries. Due to the kinetic limitations of the reaction furnace, coupled with the requirement of fuel gas co-firing, reaction furnace unit conversions of >66.6% cannot be expected to occur with low to medium quality acid gas feed streams (i.e., acid gas feed streams with < 50 mol-% H2 S).
Fig. 2 illustrates how the SO2 recycle rate increases as the reaction furnace conversion efficiency goes down for a medium quality acid gas. The curve extends past the 66.6 % reaction furnace efficiency to illustrate the effect of the “Extended Thermal Stage” technology in the second SSRT patent (see next section).
Extended Thermal Stage SSRT
To alleviate the limitation of acid gas quality for the application of the SSRT process, and the continued desire to eliminate all traditional Claus catalytic stages (i.e., reheater, catalytic converter, and condenser), an additional new technology has been incorporated and patented. The new SSRT technology takes advantage of the Gamson-Elkins relationship that reveals the Claus reaction equilibrium is favoured by cooling from reaction furnace conditions to WHB outlet conditions2 . This relationship is implemented in the “SSRT with Extended Thermal Stage” patent via a small non-traditional catalytic section at the outlet of the WHB that allows for an increased conversion efficiency via the removal of only heat (see Figs 3 and 4). This can be accomplished by extending the outlet section of the WHB to allow for the addition of a small catalytic “zone” having a gas hourly space velocity (GHSV) of 3,000 to 9,000 h-1 .
The small catalytic zone could be designed as a plug flow reactor since pressure drop is not a major concern due to the limited equipment in the SSRT configuration. Therefore, the catalytic zone could take the shape of an extension of the WHB from three to six metres in length that includes a “caged” zone of typical alumina/titania catalyst, with multiple rows of thermocouples. Titania is recommended due to higher COS and CS2 hydrolysis rates and longer lifecycle.
[Note: Alberta Sulphur Research Limited (ASRL) pilot tests proved that equilibrium, with respect to the Claus reaction, could be achieved under these conditions3 . Should a catalyst change-out be required, Saudi Aramco employs an N+1 design philosophy for their SRUs to avoid acid gas flaring (i.e., an entire spare SRU).]
By adding a catalytic zone in the outlet section of the WHB, low thermal stage conversion efficiencies of between 20 and 50% (i.e., from poor quality acid gas streams) can be “pushed” to between to 70 and 90%. This allows for the ratio of H2 S:SO2 to be maintained at 2:1 and minimises the SO2 recycle, which in turn minimises the amount of fuel gas co-firing required (i.e., conversion efficiencies above 66.6% allow for some of the H2 S in the acid gas to be combusted to SO2 ). The “SSRT with Extended Thermal Stage” therefore allows any type of acid gas quality to take advantage of its minimised process configuration.
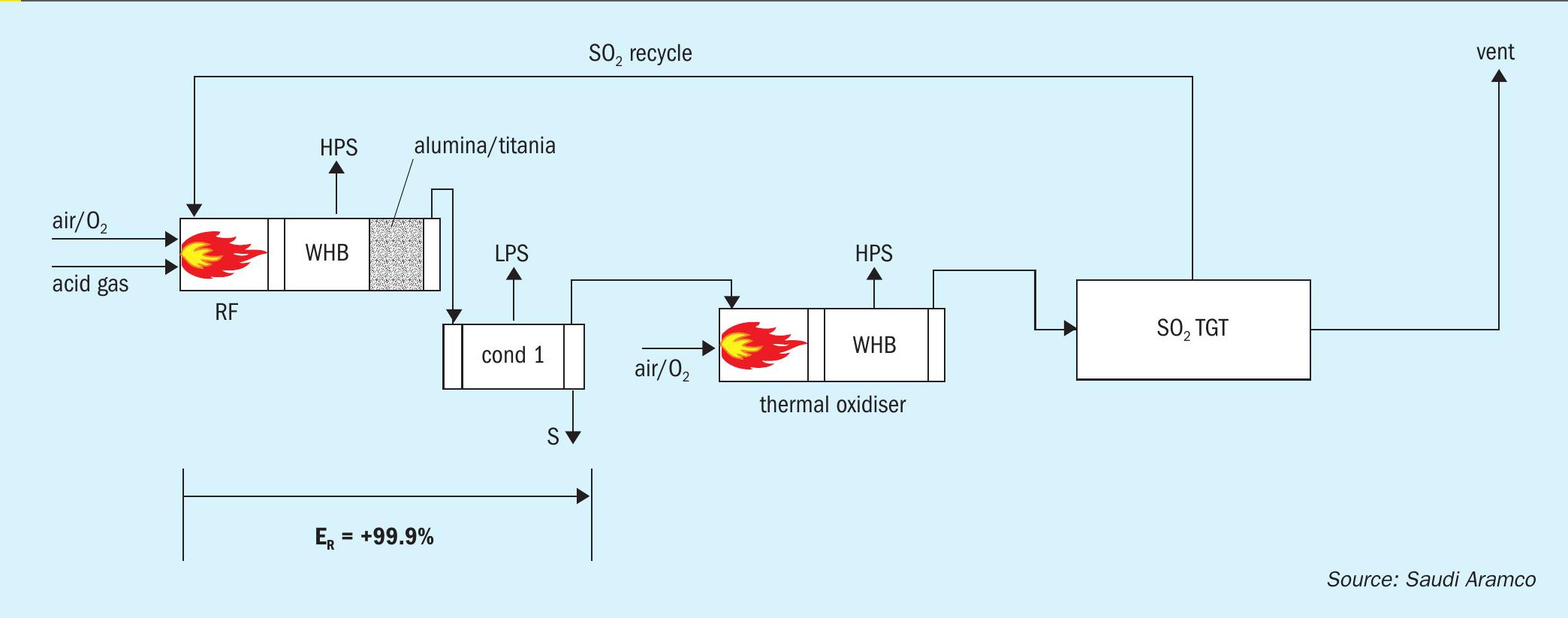
Pilot study
A pilot study of the SSRT thermal and catalytic stages was conducted by ASRL to prove the front-end kinetics for both the reaction furnace and the catalytic section3 .
The tests proved the viability of the high SO2 recycle for an ultra-lean acid gas (i.e. 20% H2 S) and a typical refinery amine and sour water stripper (SWS) acid gas feed composition (i.e. 80% H2 S and 8% NH3 ). The following critical parameters were used during the bench-scale tests:
- reaction furnace temperatures of 1,050°C for ultra-lean acid gas tests;
- reaction furnace temperatures of 1,250°C for refinery acid gas tests;
- reaction furnace residence times of 0.75, 1.0 and 1.5 seconds;
- BTEX concentration of 1,000 ppmv in acid gas feed streams;
- 40% O2 enrichment employed;
- gas hourly space velocities of 3,000, 6,000 and 9,000 h-1 for catalytic section;
- titania catalyst in catalytic section;
- maximum bed temperature of 315°C for catalytic section.
The pilot test results are summarised in Tables 1 and 2.
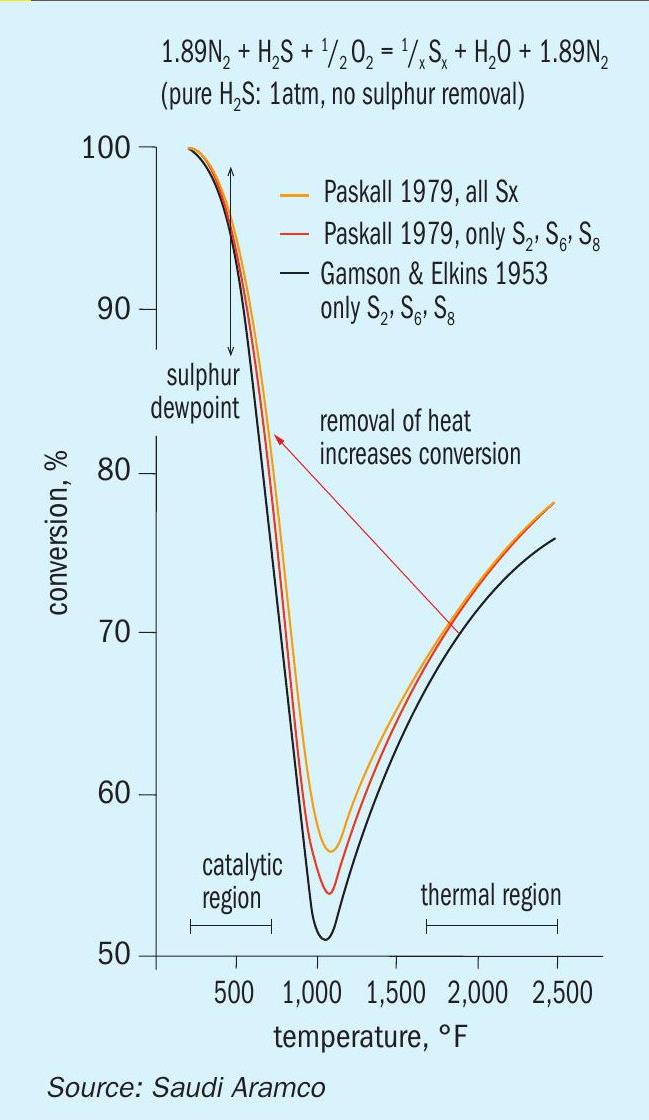
A full-scale demonstration plant is planned to prove scale-up and operational simplicity of the SSRT process. A successful demonstration will allow for deployment of the technology in new greenfield SRUs for Saudi Aramco as well as licensing the technology internationally.
Advantages of SSRT
There are many advantages of the SSRT process compared to the conventional 2-stage Claus with reduction absorption TGT:
- Significant reduction in capex and opex.
- Elimination of all traditional catalytic stages and the operational and equipment issues associated with this equipment.
- Simplicity of control and operation. Thermal stage conversion is not overly sensitive to fluctuating air demand (i.e., air demand versus conversion curve is “flatter” than at higher conversions).
- Fast response to process upsets due to placement of the tail gas analyser at the outlet of the condenser (i.e., feedback dead time of seconds rather than minutes). Less panel operator intervention is required during upsets.
- All COS and CS2 produced in the reaction furnace, and not hydrolysed in the extended WHB catalytic section, is combusted to SO2 , which is recycled and recovered. In the reduction absorption TGT, COS residuals cannot be avoided.
- SO2 and sulphur breakthrough from the hydrogenation reactor in the reduction absorption TGT can cause severe operational issues and damage to the quench tower internals and piping as well as the downstream amine absorber. These issues are eliminated by using regenerable SO2 TGT technology.
- All sulphur-containing vapor from pits, drums, degassing systems and liquid sulphur storage tank vents can be processed in the TOX, which is much simpler than recycling these streams to the reaction furnace.
- Untreated sour fuel gas and flash gas can be processed in TOX since all sulphur compounds will be combusted to SO2 and recycled to the reaction furnace for recovery. This is not the case for an SRU with a reduction absorption TGT unit where any sulphur compounds being processed in the TOX will result in SO2 emissions.
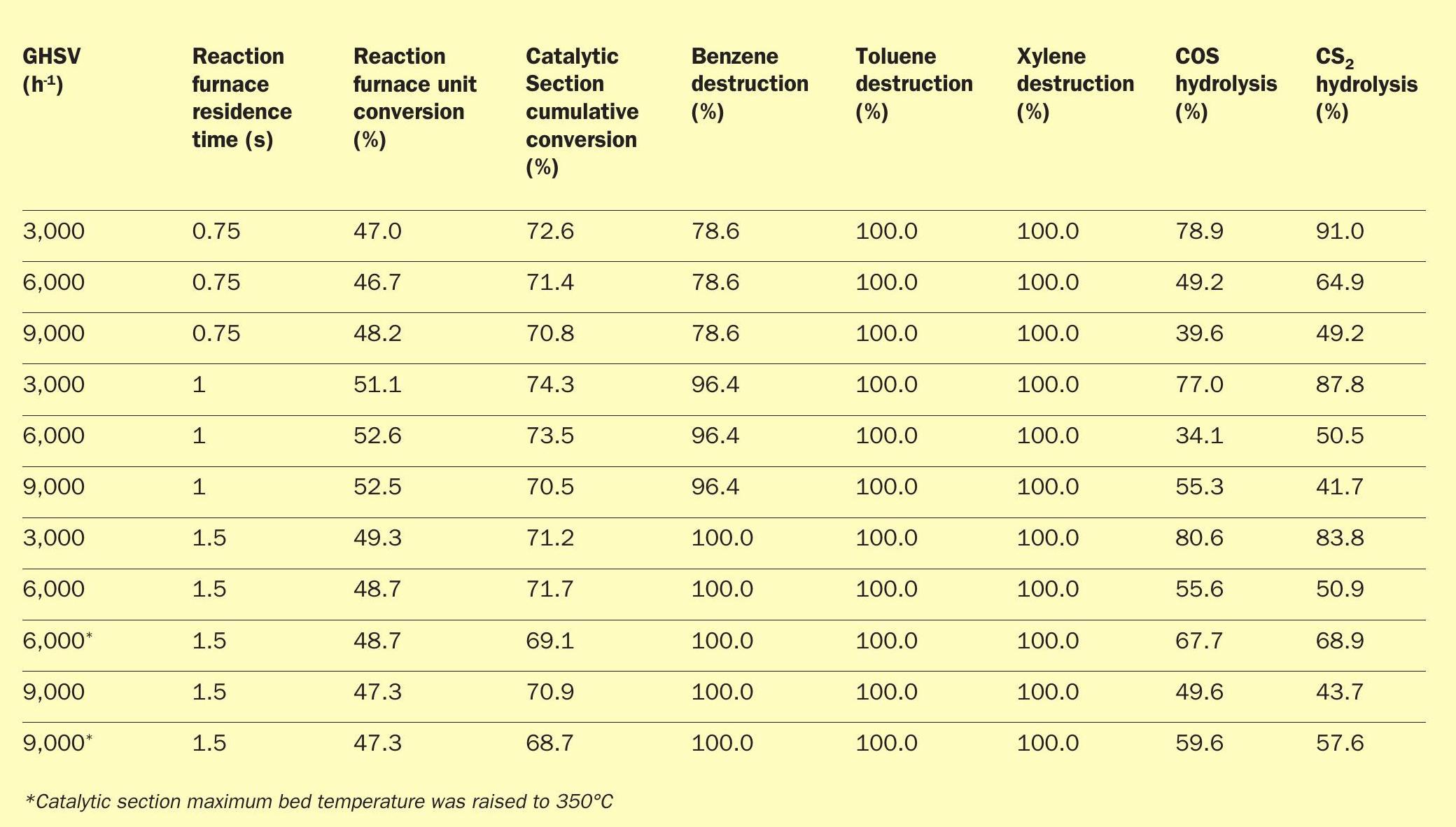
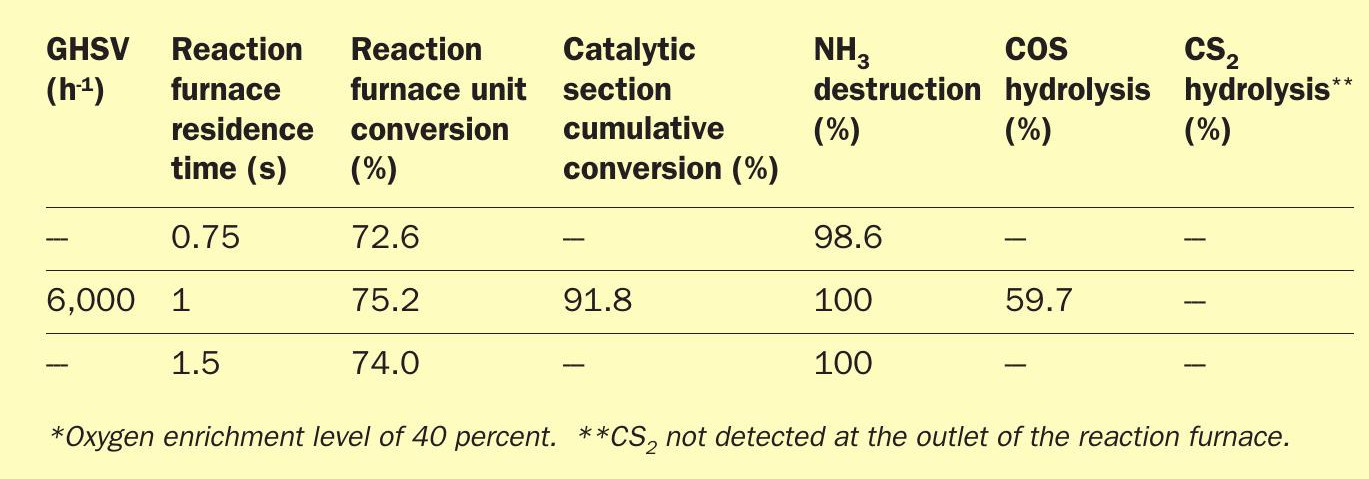
- Due to the reduction in equipment, compared to the traditional Claus/TGT plant, the required acid gas feed pressure at the SRU battery limit for SSRT can be significantly reduced. This will allow for upstream gas treating regenerators to operate with lower back pressures, which will result in lower reboiler duty, i.e., energy optimisation.
- The footprint of SSRT is significantly smaller than the traditional 2-stage Claus with reduction absorption TGT.
- 100% O2 enrichment technology can be used in SSRT with high acid gas quality feed streams without the need for additional reaction furnace temperature control technology, which must be used for traditional Claus plants.
- Start-ups and shutdowns are greatly simplified and can be accomplished in 24 hours.
- The vent stream from the SSRT TGT is CO2 , with a small amount of O2 and is ready for sequestration without the need of an additional low pressure amine system.
Conclusion
Saudi Aramco’s Simplified Sulphur Recovery Technology (SSRT) technology offers the industry a new cost-effective process that is both simple and robust, and capable of maintaining an overall sulphur recovery efficiency of 99.9+%.
Along with innumerable process advantages that have been listed come various other tangible/intangible benefits such as reduced tube-to-tubesheet failures in the condensers, elimination of extended fuel gas sweep procedures for shutdowns, drastically reduced turnaround length (i.e., testing and inspection), elimination of “channelling” in Claus converters during high turndown scenarios, and elimination of all process reheaters.
References