Fertilizer International 507 Mar-Apr 2022
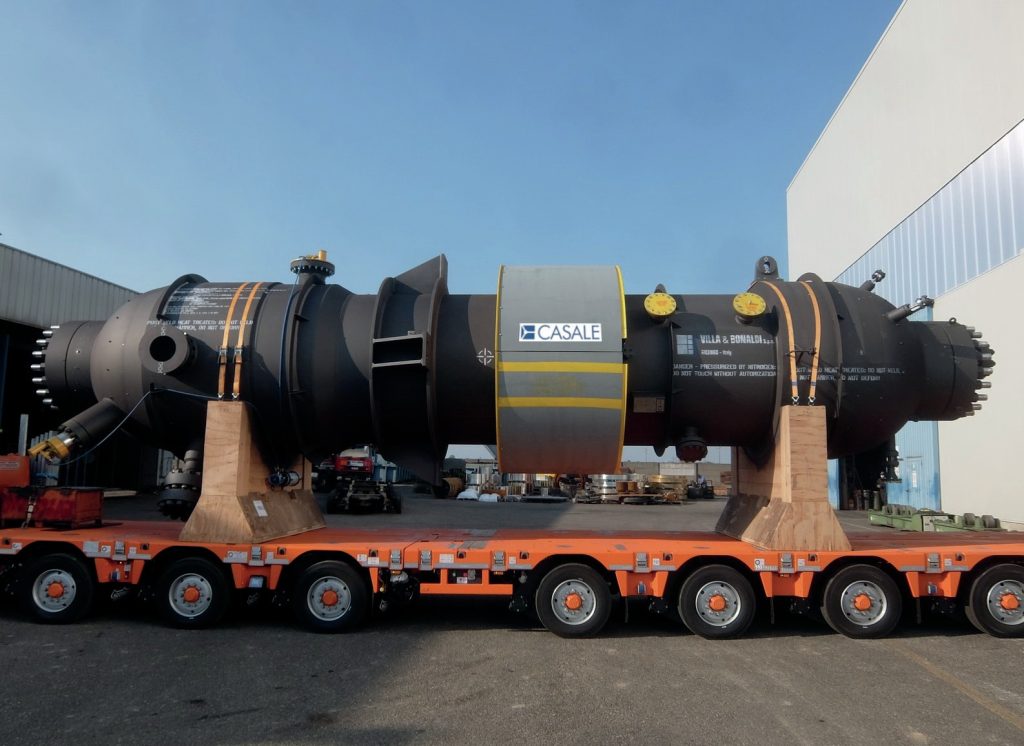
31 March 2022
Urea plant efficiency and reliability
PRODUCTION TECHNOLOGY
Urea plant efficiency and reliability
Improvements to equipment and materials are driving greater operational performance and higher efficiencies at urea plants. Recent advances are reviewed.
Operational reliability is essential for the consistent production of urea in large volumes at the lowest possible cost. This is true in both newly built urea plants and older revamped units. Safety, reliability and efficiency have therefore emerged as primary considerations in urea plant design, process engineering, the selection of materials, and subsequent operational support.
For plant operators, three main considerations are uppermost:
- To ensure profitability and market competitiveness, the operation of urea plants needs to be predictable in terms of throughput and product quality
- The production process should also be capable of achieving the highest performance with the minimum operational expenditure
- Finally, the process must comply with the newest environmental and safety regulations and be designed to meet efficiency targets.
Critically, modern urea plants operate at much harsher pressure and temperature conditions than in the past. This requires the use of superior materials designed for higher durability. Greater care also needs to be taken during process operations and maintenance work if the highest safety and reliability standards are to be maintained throughout the plant’s entire working life.
Historically, titanium and zirconium alloys have been widely used in urea plants because of their excellent corrosion resistance. More recently, super austenitic urea-grade steel has become widely adopted in critical equipment and plant components to reduce costs and further improve reliability.
CASALE
Uremium29 – a leap forward in equipment reliability
Casale, as a leading global technology licensor, brings added value to urea projects. This is thanks to its long-standing technology and mechanical engineering capabilities developed over several decades.
Casale, by improving process schemes, construction materials and its approach to mechanical design, has been able to drive down the consumption of medium pressure steam in urea plants. Urea production can also benefit from Casale’s wide range of digital services for remote monitoring and optimisation of plant operations.
The benefits of super duplex steel
Casale in a joint collaboration with its partner Tubacex has developed and extensively tested Uremium29, a super duplex material for high pressure (HP) urea service.
The introduction of super duplex steel as a construction material has brought about a leap forward in urea plant equipment reliability. Super duplex steel is distinguished by its higher chromium content and lower nickel content relative to the super austenitic steels previously used. Steel alloys with this composition exhibit superior corrosion resistance by allowing ferritic and austenitic layers to be bonded in a ‘sandwich’ structure.
The use of Uremium29, when combined with the latest equipment designs, offers great benefits in newly constructed urea plants. The same approach can be implemented at vintage urea plants too – enabling small-to-medium capacity units to remain competitive after decades of service. The goal of most owners of vintage urea plants is to prolong the operational lifetime of their facilities, and reduce their opex to help them compete with the most modern installations. This can be achieved via maintenance interventions, end-of-life equipment replacement and debottlenecking revamps.
It is important to recognise that plant performance is determined by both mechanical and process reliability. For example, reliability issues (e.g., unexpected mechanical failure, prolonged downtime or a production slowdown) at an efficient but costly modern urea plant can cause a more drastic decline in gross margins relative to a less efficient vintage plant.
Uremium29 – multiple uses and benefits
Casale has accrued a number of Uremium29 orders for critical HP equipment since this material was first introduced to the market in 2016. Its reliability and suitability was extensively investigated for a range of urea process conditions, in both stringent lab and plant tests, before being released to the market. Casale was determined to exploit the material’s superior mechanical and chemical properties to boost the life expectancy of critical urea equipment – without compromising plant efficiency.
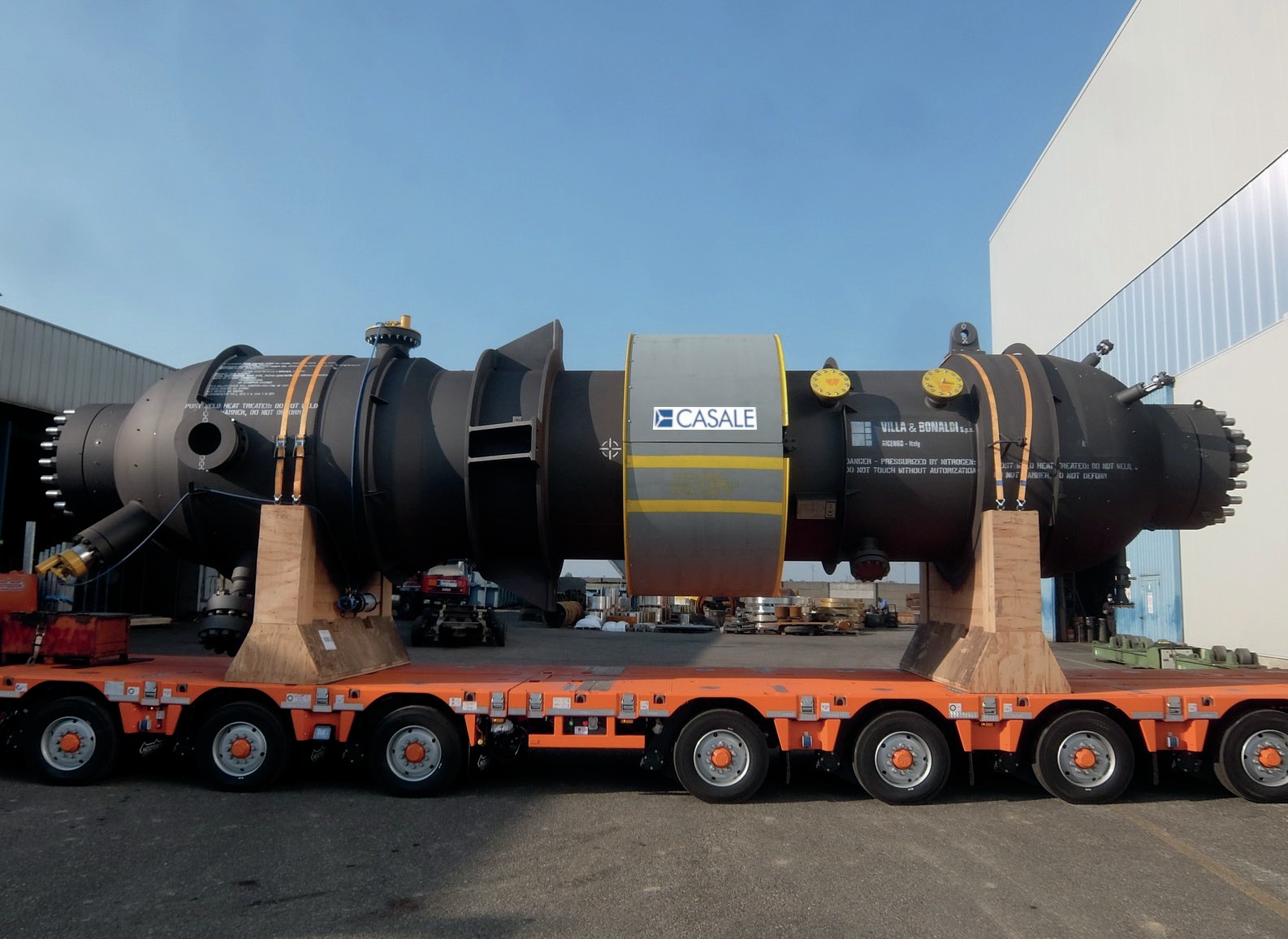
Uremium29 find its most natural use in those parts of the synthesis section of CO2 stripping plants which are in contact with process fluids. In addition to critical equipment items, it is also highly suitable for piping, fittings, control valves and the critical components of process instrumentation. Its range of applications are described below.
Improving urea reactor conversion
A major benefit of super-duplex materials such as Uremium29 is that they drastically reduce the oxygen required for passivation. In CO2 stripping plants, those parts in contact with the process fluids of the HP stripper are traditionally made of 310 MoLN steel. However, the required oxygen fraction (0.6-0.8 vol-%) in the CO2 feed has a detrimental effect on conversion in the urea reactor. The use of Uremium29, in contrast, reduces the oxygen fraction to 0.3 volume percent. This improves conversion with a corresponding reduction in medium pressure (MP) steam consumption of 2-3 percent.
Thinner, lower weight tubing
Additionally, the increased resistance to corrosion and the superior mechanical strength of Uremium29 allows thinner tubes to be used, so reducing the stripper’s overall weight. This is extremely useful when replacing vintage strippers as it makes it possible to increase the number of tubes without the need for reinforcement of the support structure and foundations.
Capacity increases
The HP stripper is frequently the capacity bottleneck in vintage urea plants. Simply replacing this with a modern stripper equipped with Uremium29 tubes can deliver moderate plant capacity increases. These tubes have a higher maximum load due to their larger internal diameter.
The same concept also applies to other critical items in urea stripping plants. Replacing a traditional 310 MoLN carbamate condenser, for example, with a new condenser equipped with thinner Uremium29 tubes increases surface area at comparable equipment weight. By generating low pressure (LP) steam at significantly higher pressure, the new HP condenser should make it possible to debottleneck downstream equipment and increase plant throughput.
Two-phase flow piping
Uremium29 is also ideally suited for process locations where two-phase liquid-gas flow and high fluid velocity may cause erosion-induced corrosion. This makes it a useful choice for two-phase flow piping, especially as a material for synthesis let-down valves which need to withstand heavy duty service for many years.
Self-stripping technology
The use of Uremium29 in HP stripper construction is not limited to CO2 stripping: the material can also be applied in self-stripping technology, also known as NH3 stripping. This traditionally relies on zirconium, titanium or bimetallic (25Cr.22Ni.2Mo + zircornium) tubes to withstand the high temperature at the stripper bottom.
In Casale’s view, Uremium29 has great potential as a replacement material in bimetallic equipment when also combined with an improved NH3 stripping process configuration. The latter involves installing a new level in the reactor top, typically by replacing the reactor cover. This separates the oxygen-containing vapour phase from the liquid phase at the reactor outlet. This is then driven to the new Uremium29 stripper bottom to provide oxygen for passivation purposes.
This new configuration is advantageous as it enables the passivation air compressors to be idled. These require frequent maintenance and can also cause the undesirable entrainment of oil into the process. This type of configuration also delivers great benefits in terms of condensation and ammonia capture capacity – by reducing the overall pressure of inert gases in the synthesis loop and ammonia recovery sections of the urea plant.
TOYO
Toyo’s approach to improving urea plant reliability
Toyo Engineering Corporation (Toyo) is a leading global engineering contractor and urea process licensor. The Japanese-headquartered company has increased operational efficiency of urea plants by developing a range of technologies for improving reliability and safety. Its innovative technology line-up includes:
- DP28W™ super duplex stainless steel
- A leak detection system
- AOCM™ (Advanced Online Corrosion Monitoring)
- IDCS™ (Image Diagnosis for Corrosion Screening).
In Toyo’s view, two recently introduced innovations, AOCM™ and IDCS™ , will enhance the maintenance of critical equipment at urea plants.
DP28W™ – an advanced duplex stainless steel
Toyo has more than 40 years of experience on the use of duplex stainless steels at urea plants. These materials enhance equipment reliability and safety due to their excellent corrosion resistance to urea-carbamate solution. Their use also reduces the amount of passivation air required.
Building on this experience and responding to industry demand, Toyo and Nippon Steel Corporation (NSC) have developed DP28W™ (28Cr-8Ni-1Mo-2W) for urea plants. This advanced duplex stainless steel can greatly improve the safety and economics of urea plants over their lifecycle. It has outstanding features in terms of composition, mechanical properties and corrosion resistance:
- Composition: DP28W™ shows excellent corrosion resistance due to its combination of the high chromium content, the addition of tungsten and a well-balanced ferrite/austenite structure. The molybdenum content is intentionally reduced to ensure good corrosion resistance in the heat-affected zone (HAZ). While the addition of tungsten compensates for the adverse effect of reduced molybdenum on corrosion resistance elsewhere.
- Mechanical properties: DP28W™ has remarkable mechanical properties compared to other stainless steels (Table 1). Its high mechanical strength, compared with austenitic stainless steels, such as 25Cr-22Ni-2Mo and 316L, is a great advantage when it comes to the mechanical design of equipment.
- Corrosion resistance: the resistance of DP28W™ to corrosion by urea-carbamate solution has been proven in commercial plants, with, for example, a lower corrosion rate than alloys such as DP12 and 316L-UG (Figure 1).
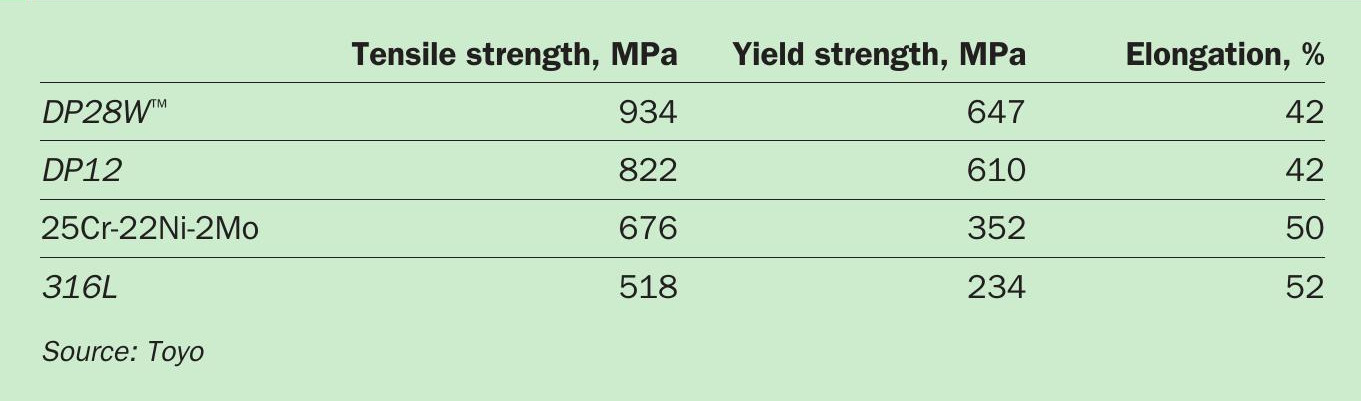
Lifetime advantages of DP28W™
DP28W™ provides advantages which contribute to the safety and economics of the urea plant throughout its lifetime. Its corrosion rate is lower relative to conventional duplex stainless steels. In particular, the corrosion resistance in the HAZ and weld metal are greatly improved. These positive features enhance equipment reliability and maintenance by:
- Prolonging the life of components exposed to urea-carbamate solution
- Decreasing maintenance frequency
- Reducing the risk of active corrosion.
Other notable operational advantages include:
- Decrease of passivation air: DP28W™ is easily passivated with less dissolved oxygen in urea-carbamate solution. As a consequence, the passivation air – which restricts operational efficiency due to lower conversion in the synthesis section and ammonia loss in the recycle section – can be reduced.
- Design allowance: DP28W™ has a higher allowable stress value and stress intensity value than austenitic stainless steels and conventional duplex stainless steels. This high mechanical strength provides a larger design allowance.
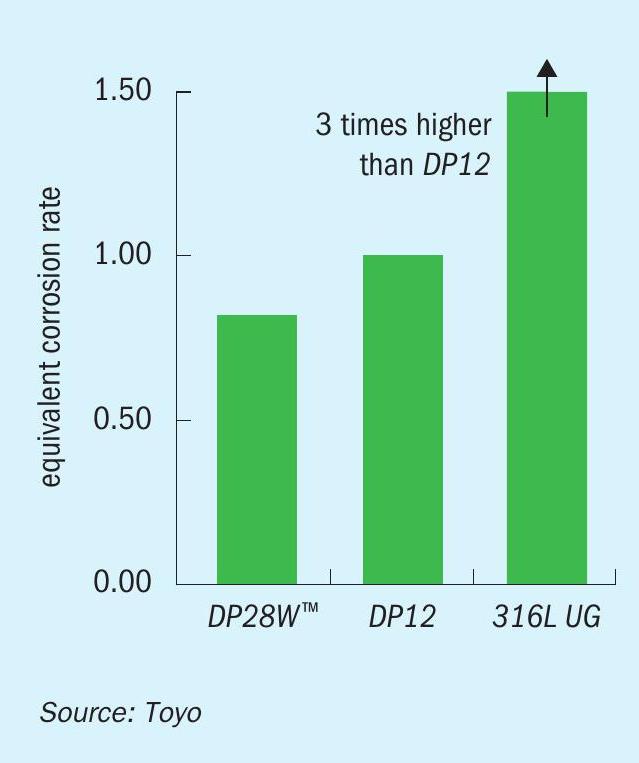
Operational experience with DP28W™
Toyo has applied DP28W™ at its urea plants since the mid-2000s with excellent performance to date. One operator, for example, replaced its existing titanium-lined urea reactor (used in the total recycle process) with a new one lined with DP28W™ . Titanium requires little passivation air even at high temperature. Nevertheless, under the same severe operating conditions (200 bar, 200°C), the corrosion rate of DP28W™ has been far lower than titanium. The new DP28W™ fabricated reactor has reduced maintenance costs by around 90 percent since it first began operating successfully in 2006. The maintenance during each turnaround has mostly involved just visual inspections with no major repairs being required to date.
Leak detection system
The internal walls of high-pressure equipment in the urea plant are lined with proper corrosion-resistant metal plate to protect them during contact with corrosive fluid. This protection is important as any leakage through the lining plate will inevitably damage the outer carbon-steel pressure holding shell.
To detect and prevent such leaks, Toyo has developed an on-line leak detection system. This detects ammonia leaking into the nitrogen gas circulating between the lining plate and pressure holding shell. This system is able to detect ammonia leakage in tiny amounts and identify the location of the defect before damage becomes severe. It improves the reliability of the urea plant and helps keep maintenance work easy and simple.
Advanced online corrosion monitoring (AOCM™ )
Assessing the real-time condition of stainless steels exposed to ammonium carbamate is particularly challenging. Toyo’s advanced online corrosion monitoring (AOCM™ ) system is, however, able to predict the condition of such equipment and piping. The system helps to ensure reliable operations and optimise plant inspection plans by providing real-time corrosion monitoring of high-pressure equipment and piping in the urea synthesis loop. For example, AOCM™ can measure the corrosion rate in synthesis piping on a real-time basis via ultrasonic testing (UT) sensors installed in the piping (Figure 2).
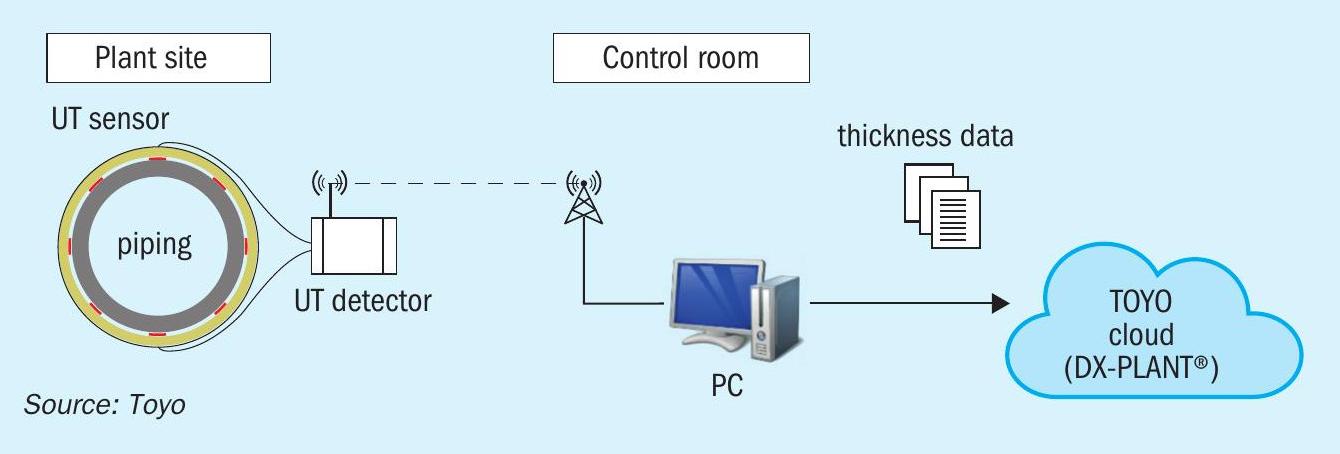
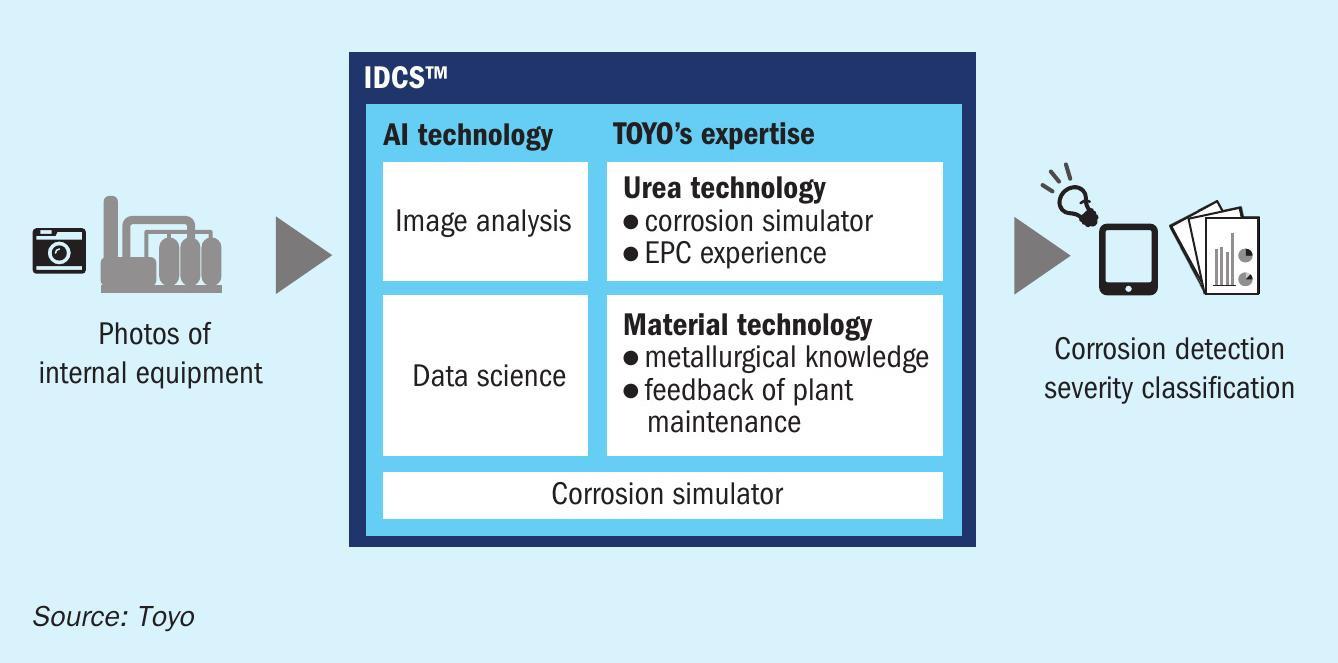
Image diagnosis for corrosion screening (IDCS™ )
Toyo’s image diagnosis for corrosion screening (IDCS™ ) system is a new way to screen and detect the corrosion of equipment internals during plant maintenance. This system uses image analysis technology and artificial intelligence (AI) to efficiently inspect equipment during plant maintenance (Figure 3). The system provides high speed and reliable analysis by combining a range of AI technologies (image analysis, data science, corrosion simulator etc.) with Toyo’s expertise. The advantages of IDCS™ include:
- Time saving and accurate visual inspections during plant maintenance
- Dependable estimates of timing for equipment repairs/replacements
- Condition-based maintenance with reduced opex.
THYSSENKRUPP INDUSTRIAL SOLUTIONS
Self-regulating pumps for higher operating stability
Avoiding biuret formation is a well-known challenge for urea plant operators. This needs to be kept to minimum to avoid generating off-specification product. Biuret forms as an unwanted but inevitable side reaction when two urea molecules polymerise to eliminate ammonia. Its formation is accelerated by three main operational factors:
- Low ammonia concentrations
- High temperatures
- High residence times.
Every urea plant generally has a few locations where all three factors occur simultaneously. In this article, we focus on the outlet of the evaporation section and the melt transfer line to the granulation unit.
Dedicated transfer pump
A dedicated pump is required to transfer the urea melt leaving the evaporation section to the granulation unit. This is needed to ensure the necessary supply pressure for the granulator spray nozzles.
This transfer pump functions at a high NPSH (net positive suction head) to cope with the boiling melt that leaves the evaporation section under vacuum conditions – with a three metre suction head being a common value. While necessary to prevent cavitation, one undesirable consequence of a high NPSH is increased biuret formation. This is caused by the higher residence time of the urea melt in the pump suction line.
To avoid this scenario, thyssenkrupp Industrial Solutions (tkIS) offers a special self-regulating pump as an option for newly built urea plants. Compared to a conventional centrifugal pump, this self-regulating pump works well independently of the intake rate, i.e., its capacity always corresponds to the intake rate, so maintaining the NPSH at a more desirable value of close to zero metres. As a consequence, the suction head – and therefore the residence time of the melt – is kept to a minimum, leading to less biuret formation. This also avoids low melt levels which can trip the urea plant.
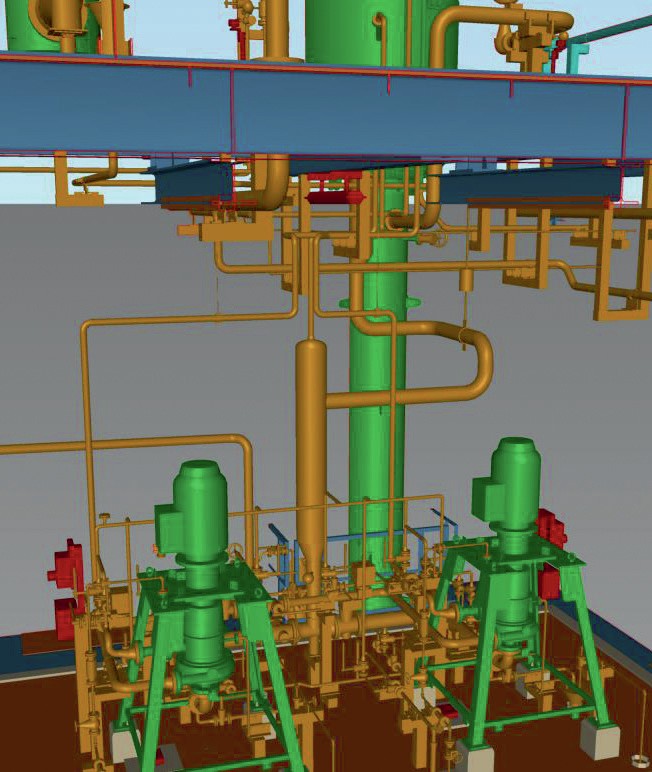
“Self-regulating pumps provide the security necessary for stable urea plant operations, especially for the downstream granulation unit.”
Unstable urea supply
A nitrogen fertilizer plant consisting of just an ammonia unit and a urea unit will normally run smoothly without significant capacity changes. In more complex plants (e.g., consisting of urea synthesis, urea granulation, diesel exhaust fluid and urea ammonium nitrate units), in contrast, changes to the urea solution and melt supply to certain units are required when their capacity is altered to generate different product volumes.
Any resulting instability in urea solution supply to the evaporation unit can be an issue for the granulation unit. In such cases, the operator needs to adjust the load to the evaporation section, and therefore the transfer pump capacity, accordingly.
Yet care must be taken when reducing pump capacity, especially when using a conventional centrifugal pump. This is because reducing centrifugal pump capacity can easily trigger the dry run protection in the suction line, causing the downstream granulation unit to trip.
Self-regulating pumps offer advantages
This scenario is, however, avoided if a self-regulating pump is used instead. The self-regulating ability of this type of pump allows its capacity to adapt, matching the intake rate, without causing a trip in the pump or the downstream process unit. Self-regulating pumps, by easily handling capacity fluctuations, therefore aid the plant operator by reducing the risk of downstream units tripping.
The elimination of layout constraints at the outlet of the evaporation section is another advantage when using a self-regulating pump. For a conventional centrifugal pump, a long line is generally needed between the outlet of the evaporator and the pumps’ suction flange, depending on the plant layout, in order to maintain the suction head. This inevitably increases melt residence time and, consequently, promotes biuret formation.
A self-regulating pump, in contrast, can be located directly below the evaporator outlet – because no specific suction head is required. The only consideration being the overall height of the pump frame and the required head space. A typical pump setup is shown in Figure 1. How close the pump can be placed to the evaporator, visible in the background, can be clearly seen.
Summary
In summary, the self-regulating pump provides security for stable urea plant operations, especially for the downstream granulation unit. This type of pump can be installed in newly built plants and during revamping. tkIS has gained a lot of good experience using self-regulating pumps in recent years, particularly with respect to efficiency and reliability. Furthermore, their use has improved plant layout, specifically the outlet of the evaporation section. tkIS holds the patent rights to install a self-regulating pump at this challenging location.
STAMICARBON
Leak detection to ensure plant safety
Ammonium carbamate – corrosion risks
Unlike the urea solutions ultimately obtained, ammonium carbamate, an intermediate in urea synthesis, is highly corrosive. Loose stainless steel liners are therefore commonly fitted to protect high pressure synthesis equipment from corrosion. Nonetheless, these liners still become thinner over time due to carbamate corrosion. They are also vulnerable to:
- Corrosion in the heat affected zones (HAZ)
- Condensation corrosion.
All of these types of liner corrosion can potentially cause ammonium carbamate to leak. A hazardous situation can then quickly arise, if carbamate-containing fluids enter the space between the liner and the carbon-steel pressure shell. Due to the risk of active and rapid corrosion of the carbon-steel pressure vessel, the urea plant needs to be shut down immediately when this happens – to keep operational staff out of danger and avoid damage to the pressure shell and the surrounding environment. Having a dependable leak detection system in place to monitor such leakages is therefore of paramount importance.
The benefits of leak detection
Stamicarbon, the innovation and license company of Maire Tecnimont Group, has designed a reliable leak detection system (LDS) that continuously monitors the lining for leakage. The system signals whenever a leak is detected.
The benefits of installing Stamicarbon’s LDS include:
- Usage of a single system for more than one piece of high-pressure equipment
- Continuous monitoring for leaks
- Detection of a gas leak of 1*10-7 STD. cc/sec is possible
- Quick response time (under 60 minutes)
- The leakage rate can be calculated
- The location of the leak can be traced
- Improves reliability of the high-pressure equipment
- Significantly lower repair costs, due to early detection of a leak
- Reduced turndown period and production losses.
Stamicarbon also provides additional services, including:
- Inspection of the current leak detection system
- Assistance with installation, commissioning, and start-up of the LDS
- Training of operators and technicians
- Troubleshooting support.
In the event of a leak, Stamicarbon can also help repair damaged equipment and carry out relining to replace corroded liners.
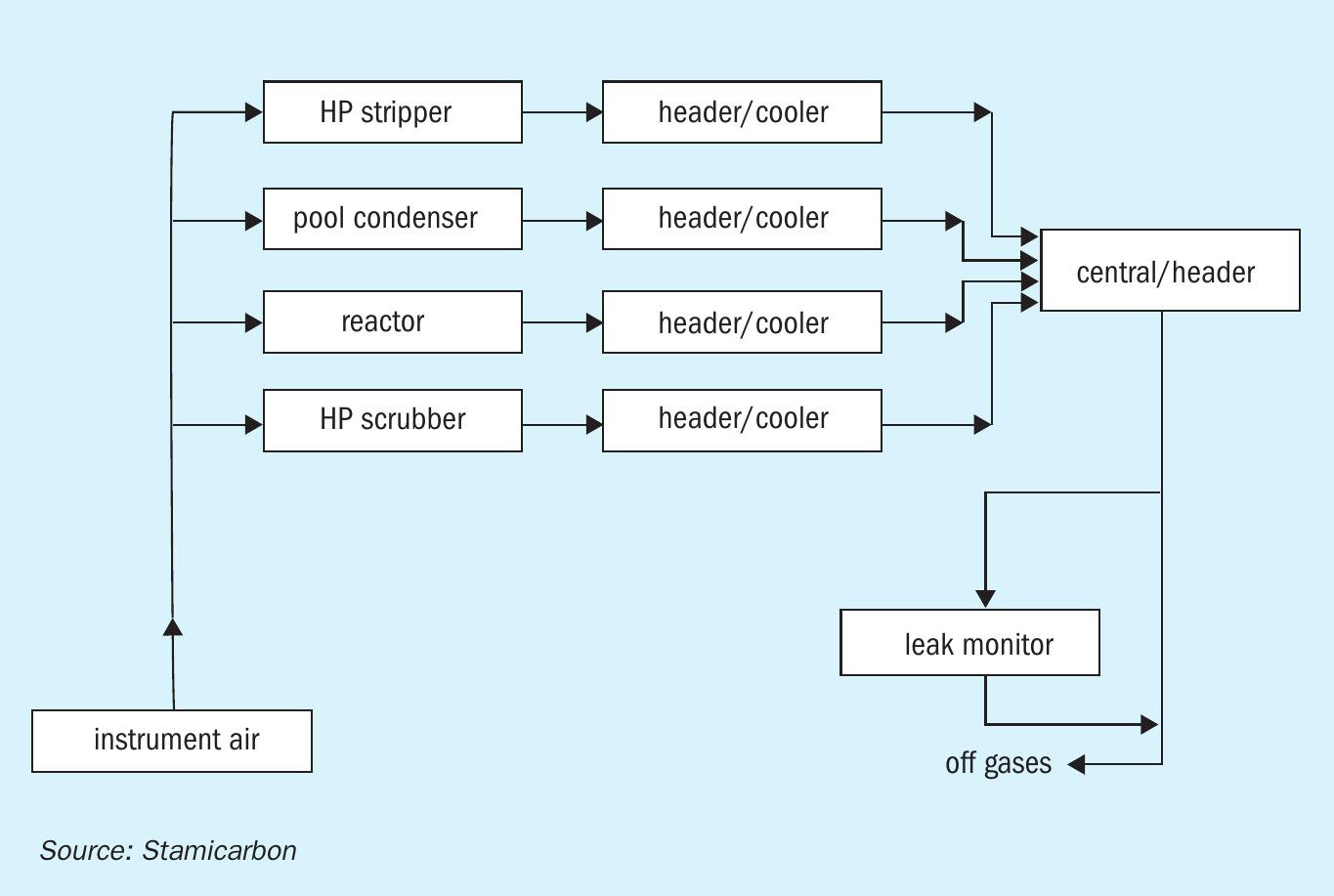
General operation and types of LDS
Leak detection systems use a gas monitor (analyser) to continuously measure gaseous ammonia concentrations. The gas monitor is connected to the annular space between the carbon-steel pressure shell and liner (together with the leak detection holes) via a header/cooler. The gas analyser detects ammonia concentrations as low as 1 ppm up to 1,000 ppm.
Stamicarbon offers leak detection systems based on three concepts:
- Pressurised-type leak detection
- Vacuum-type leak detection
- Combined (hybrid) leak detection.
Pressurised-type leak detection
The pressurised-type LDS is suitable for new high-pressure vessels. These generally have grooved passageways and at least two leak detection holes in each liner compartment.
In this system, instrument air is circulated in the gap between the liner and pressure shell (Figure 1). A pressure reducer regulates the supply of air into the system, while a safety valve prevents pressure in the system becoming too high. Tubing from each liner compartment ends in a header/cooler where the air is cooled to ambient temperature. A small part of the air is dried and fed into the leak monitor to continuously analyse for ammonia. The remaining air (off-gases) is released into the atmosphere.
The resistance met during circulation is not the same in each liner compartment. To equalize this and optimise the flow in each liner compartment, a flow meter and a control valve are incorporated into the tubing to the header (Figure 2).
Key features of pressurised-type leak detection:
- Ideal for newer high-pressure vessels with grooves (passageways) in the carbon-steel wall
- Highly reliable and accurate
- Easy to use and maintain
- Provides continuous readings to the distributed control system (DCS)
- Good diagnostics – receive proof of segment communication via a flowmeter
- Flowmeter readings immediately identify passageway blockages behind the liner – whereas vacuum-type or combined (hybrid) systems only identify these periodically
- Eliminates false alarms in tests from tube leakages caused by the entry of ambient air containing ammonia.
Vacuum-type leak detection
“During urea production, early warning of leaks is essential as they could lead to a catastrophic failure of high-pressure vessels.”
The use of a vacuum-type leak detection system is advised if there is no passageway system between the lining and pressure shell, as is typical of older high-pressure equipment (Figure 3). In this type of LDS, fluids leaking into the liner are sucked continuously into a gas monitor using a vacuum pump. Tubing from each liner compartment ends in a header/cooler where the air is cooled to ambient temperature. A small part of the air is fed into the leak monitor to continuously analyse for ammonia. The remaining air (off-gases) is released into the atmosphere.
Key features of the vacuum leak detection:
- Ideal for older high-pressure equipment which have leak detection holes but no grooves
- Highly reliable and accurate
- Limited diagnostics – needs periodic tests to check segment communication
- Continuous DCS readings.
Combined leak detection
This type of integrated leak detection system is ideal for monitoring several pieces of older and newer high-pressure equipment. The newer equipment is monitored by the pressurised system and the older equipment with the vacuum system. Both systems work independently.
LDS maintenance
It is important to commission and operate the leak detection system according to the guidelines. Pressurised systems need safeguarding at 0.5 barg pressure, for example, while the vacuum system is inherently safe. Particular care must be taken not to over-pressurise the leak detection system during commissioning and plant shut down.
Leakage detections systems must be checked on a regular basis to ensure they are functioning properly. Blockage of the LDS (e.g., due to crystallised product leaking behind the liner), by hampering leak detection, may lead to a dangerous situation. Stamicarbon does not, however, recommend using steam condensate to unblock leak detection systems.
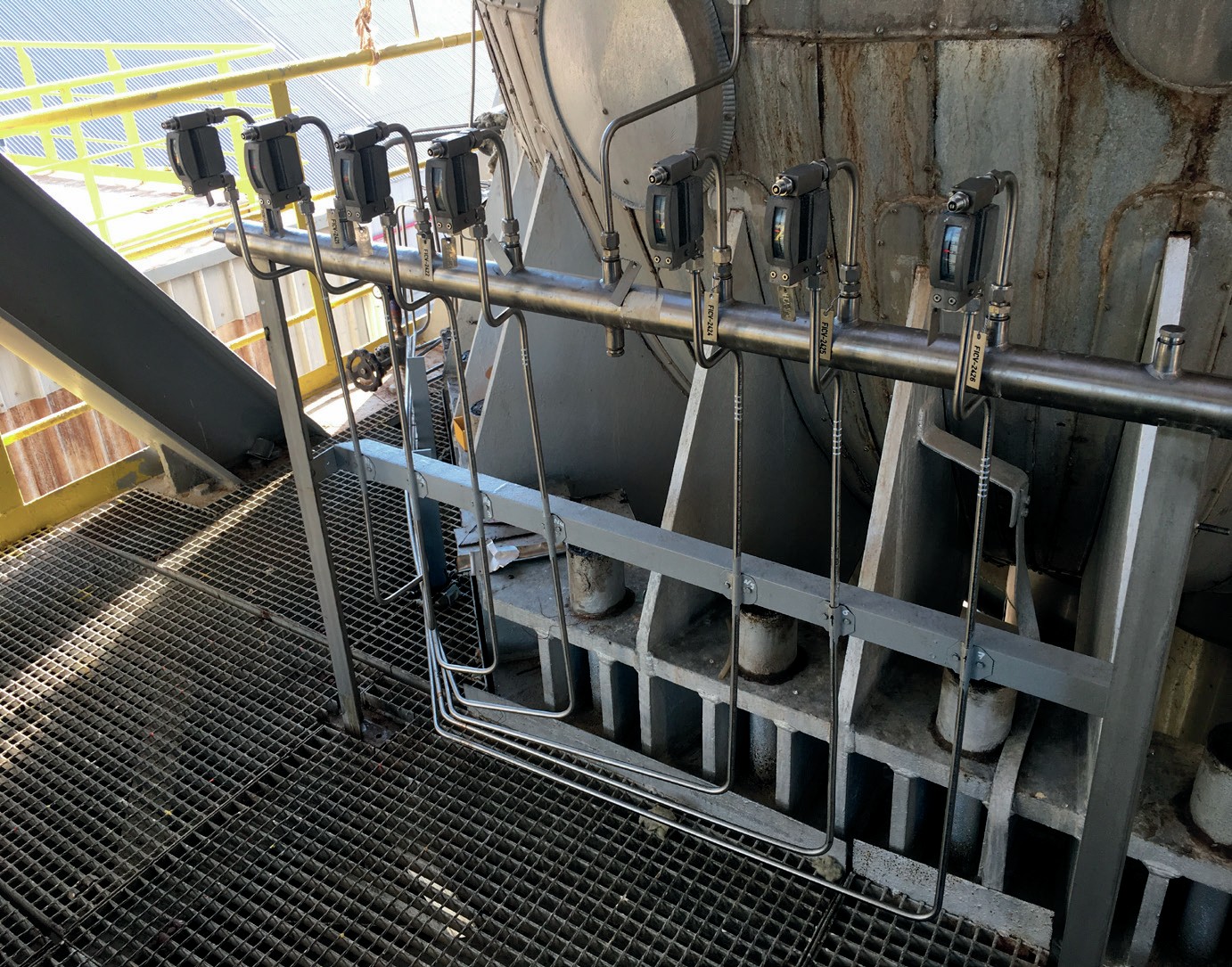
Potential leaks must be monitored closely. When a leak is identified and located, the plant must be shutdown to confirm and repair the leakage. This is necessary to avoid corrosion damage to the carbon-steel pressure shell.
Locating leaks
Within the liner compartment, leaks can be traced by searching each compartment with help of the valves on the header. When the leaking compartment is identified, the leak rate can be calculated from the ammonia content. This leak rate will determine the likelihood of finding the leak and the selection of the best method to discover it. Leaks mostly occur in liner welds and are commonly caused by welding defects such as porosities and so-called wormholes.
It is important to recognise that synthesis composition varies throughout the high pressure (HP) loop. It follows that the composition of fluid leaking through liner – particularly its ammonia concentration – will also differ from one place to another. The influence of synthesis composition on measured ammonia concentration therefore needs to be taken into account when calculating the leak rate.
Leak detection systems also need to have a quick response time. This is partly because any synthesis solution leaking between the liner and the carbon-steel pressure shell will contain urea as well as corrosive ammonium carbamate. This solution can dissociate and crystallise (as biuret or triuret) to block passageways and risks making detection impossible.
There are three recommended methods for finding a leak:
- Bubble leakage test
- Ammonia leakage test
- Helium leakage test
A bubble test is the appropriate method for bigger leaks. The pressure in the gap between the liner and carbon steel shell is increased to a maximum 0.3 barg using air or nitrogen. Leaks are then searched for by applying a soap solution on the liner welds of the suspected liner compartment. The detectable leak rate using the bubble method is in the range of 1*10-3 STD.cc/s.
An ammonia leak test is advised for smaller leaks. Air is firstly evacuated from behind the liner using a vacuum pump. Ammonia is then introduced behind the liner up to a maximum pressure of 0.03 barg. A coloured ammonia sensitive spray or paste is applied onto inspected welds. Leaks are then detected by a colour change.
In this leak test, the ability to detect small leaks depends on the ‘dwell time’ – the time taken for the ammonia to penetrate the leak. With a dwell time of 8-10 hours, for example, it is possible to detect leaks with a leak rate as small as 0.02-0.03 cc/hr.
The detectable leak rate using an ammonia leakage test is about a thousand times more sensitive compared to the air bubble test (i.e., around 1*10–6 STD. cc/s). However, a different strategy such as a helium leak test is necessary for the detection of even smaller leaks (down to 1*10–7 STD.cc/s).
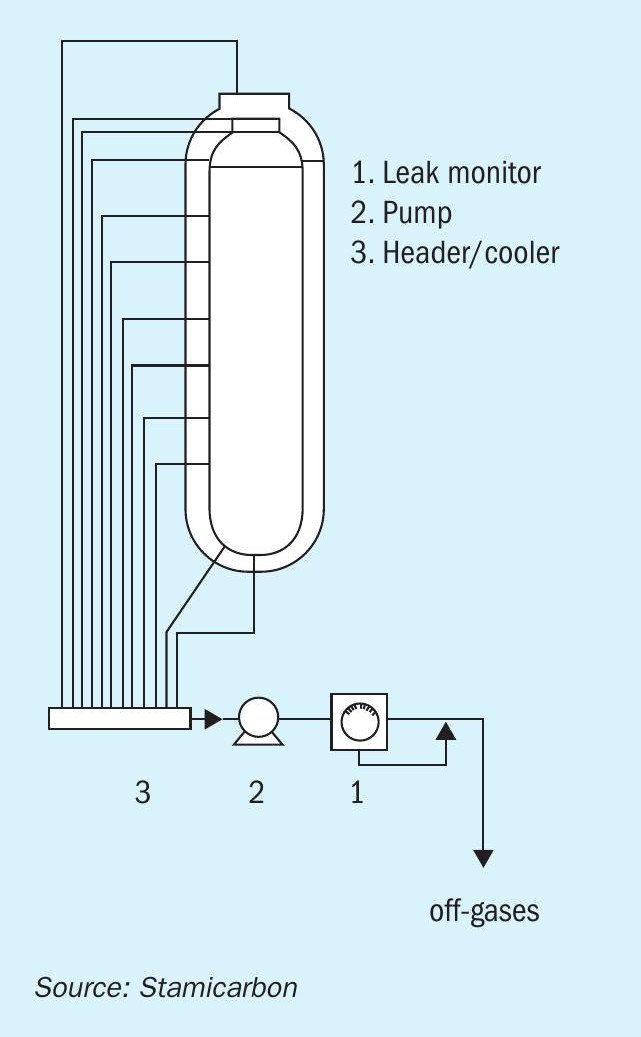
Conclusions
During urea production, early warning of leaks is essential as they could lead to a catastrophic failure of high-pressure vessels, if left undetected. Stamicarbon therefore strongly advises that a state-of-the-art leak detection system (LDS) is installed to monitor high-pressure equipment protected with a liner. These systems are valuable as they can update operators continuously on the integrity of protective liners during everyday plant operations. Stamicarbon’s LDS is reliable and, due to its ability to detect small leaks, enables plant managers to quickly find and repair leaks. Their reliability does, however, depends on correct operation and proper maintenance. The careful inspection of protective liners during normal plant turnaround also remains necessary.