Sulphur 400 May-Jun 2022
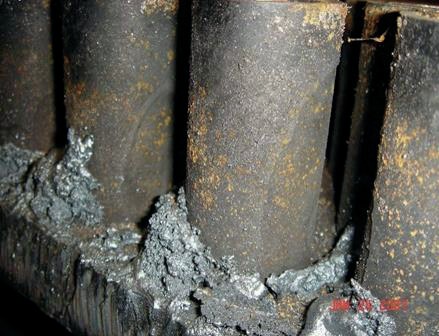
31 May 2022
Detecting water-related issues in sulphur recovery units
SRU UTILITIES
Detecting water-related issues in sulphur recovery units
Most inspection personnel are familiar with the symptoms of process-related issues; however, they often lack an understanding of the root causes of water-related issues. In this article L. Huchler of MarTech Systems and E. Nasato of Nasato Consulting provide insight about early warning signs of common water-related failures in steam generators and sulphur condensers, proactive monitoring practices, practical operating strategies, options for corrective actions, reminders about robust water-side design and reminders about the challenges of prematurely destroying evidence by prioritising cleaning over diagnostic efforts during turnaround activities.
Processing natural gas and refining sour crude creates a sulphide-laden waste stream. The sulphur recovery unit (SRU) processes this waste stream, creating a commercially valuable commodity, sulphur, and allowing the plant to conform to environmental discharge regulations. In the past, operators of SRU systems focused on process-side improvements in energy efficiency and production capacity. The current focus is addressing water-related failures in the waste heat boiler (WHB) and the sulphur condensers with a goal of eliminating water-related failures. The objective of this article is to define the warning signs of water-related failures in steam generators and provide options for corrective actions. Many of the risks and warning signs of water-related failures described in this article are relevant to waste heat boilers and process condensers in other refining processes and other industries such as petrochemical, fertilizer and inorganic chemicals.
A particular concern is the increase in the frequency of failures of the sulphur condensers (low pressure steam generation ~50 psig (350 kPag)) as compared to the WHB (higher pressure steam generation of minimum 250 psig (1750 kPag)). This trend is consistent with the use of high purity reverse osmosis (RO) permeate or 100% condensate for make-up water. In theory, the use of RO permeate will increase the water-side efficiency of all of the high pressure steam generators; however, in practice, this change usually results in poorer control of the boiler water chemistry and a higher risk of corrosion and iron deposits. In the lower pressure sulphur condensers, this higher purity make-up water appears to correlate with chronic failures such as flow-accelerated corrosion (FAC) and/or dissolved oxygen corrosion.
The water-side related failures in both high pressure WHBs and low pressure sulphur condensers are each unique with regards to specific needs for water chemistry and flow related boiler feed water distribution and steam removal. The high pressure WHB is more susceptible to water-side issues related to system fouling and thus failures related to high temperature sulphidation and high temperature metal failure. The low pressure sulphur condenser failures are not susceptible to high temperature process gas related issues since the typical process gas operating temperature is below the carbon steel limit of 650°F (343°C) but is a result of water quality issues related to items such as oxygen concentration, pH and/or FAC phenomena.
The greatest challenges for early detection of water-related issues are the lack of understanding of the warning signs and the lack of real-time operating data as compared to the process side. Often the first evidence of water-related issues is a failure or poor inspection results. As plants have increased throughput and upgraded water pretreatment systems, they have inadvertently increased the risk of lost production from water-related issues.
Early warning signs of water-related failures
Obtaining early warning signs of water-related failures requires effective monitoring practices. Most plants monitor several parameters in the boiler feedwater (conductivity, pH, total hardness) and the waste heat boiler and sulphur condenser water (conductivity, pH, alkalinity, concentrations of water treatment chemicals) at least once per day and measure a subset of these parameters on the other shifts. Based on these data, operators make adjustments to the chemical feed pumps and/or the blowdown flowrate. Boilers have long time constants; operators must learn the optimal frequency and degree of adjustments.
The chemical supplier routinely measures the same parameters as the plant and may routinely measure additional parameters such as silica and iron in the boiler water. However, few plants, or water treatment specialists, routinely measure the boiler water in the condensers because most plants lack installed sample coolers on each condenser. And some plants will not allow the use a portable sample cooler, citing the safety issues of the cooling water flooding the area near the sample location. The minimum sampling frequency for condensers is annually to detect problems and after turnaround to properly reset the blowdown flowrate. Plants that have high purity feedwater may find that all of the blowdown control valves are oversized, either due to poor design or due to an upgrade of the water pretreatment system. Plants should consider requesting an exception for a temporary installation of a portable sample cooler to control the sample temperatures to 77°F (25°C) to protect the condensers from corrosion.
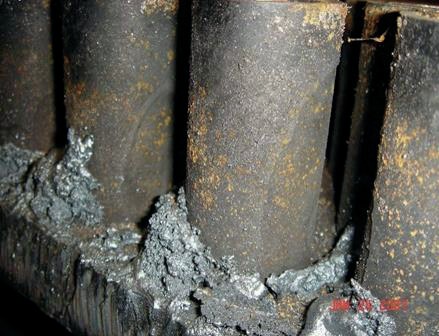
There is another, more common monitoring issue: poorly performing sample coolers. The higher the temperature of the water samples, the lower the accuracy of the test result. Water temperatures that are high enough to “flash” (evaporate a portion of the sample) will have even lower accuracy. SRU systems that use high purity make-up usually have rather small specification ranges for boiler water parameters, increasing the risk of flow-accelerated corrosion (FAC).
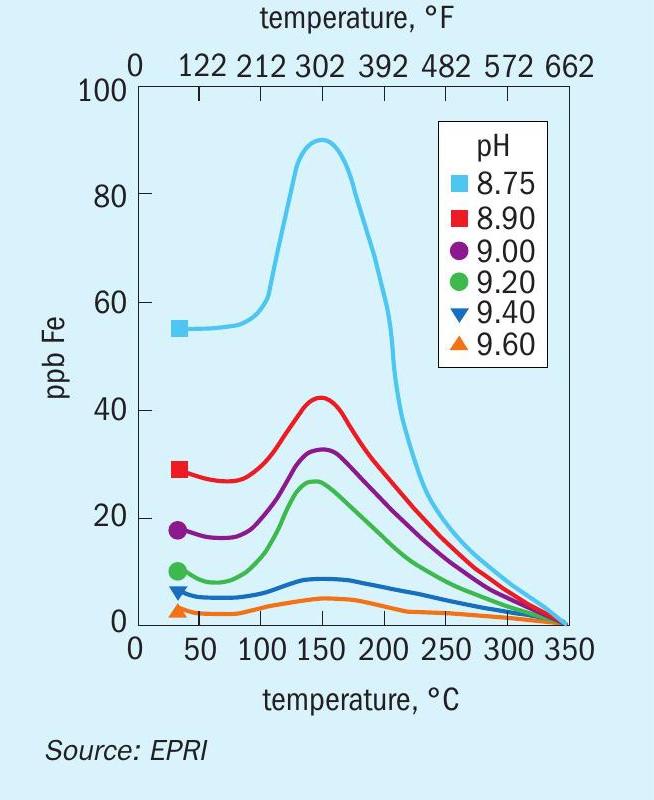
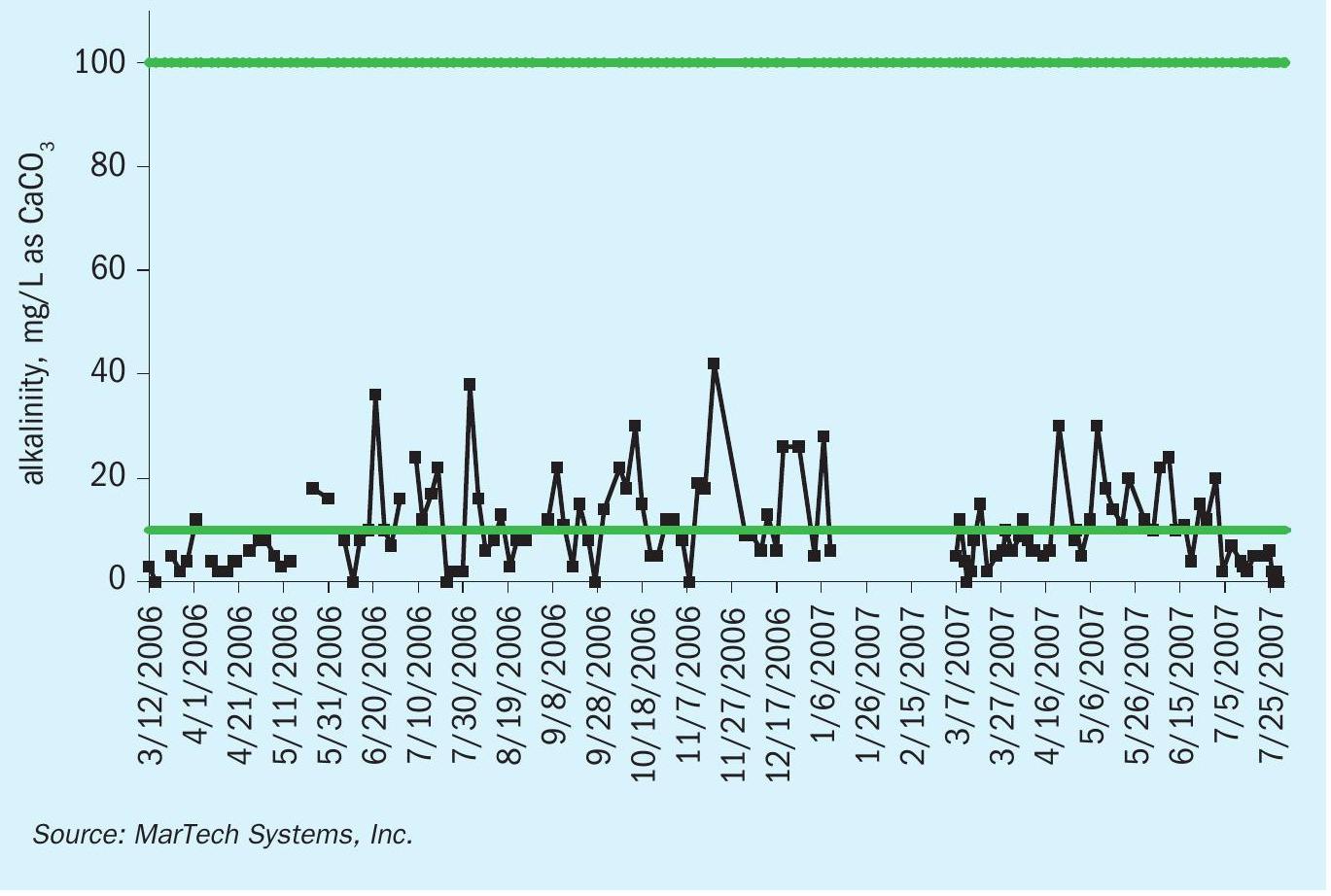
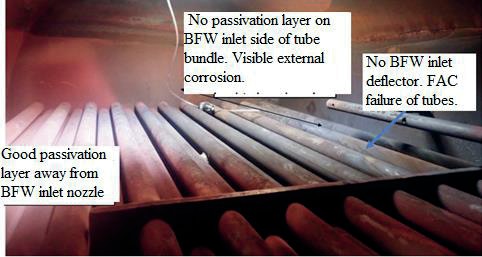
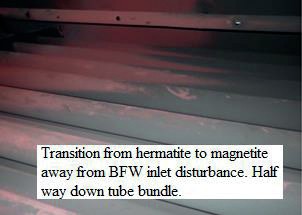
Practical operating strategies
High purity make-up water
Plants that use 100% condensate or have replaced sodium zeolite softeners with reverse osmosis units create a risk of FAC. FAC requires three conditions: high purity water (i.e. low alkalinity and/or reducing conditions), high local velocity (e.g. turbulence), and high temperature.
Fig. 1 shows the inlet tubesheet of a 50 psig (345 kPag) horizontal sulphur condenser. The semi-circular pattern of corrosion is FAC damage due to high turbulence, low OH alkalinity and locally higher heat flux than the original equipment manufacturer (OEM) specifications for this SRU.
High concentrations of the oxygen scavenger chemical create a reducing environment, increasing the risk of single-phase FAC. Feedwater inlet piping and areas adjacent to internal baffle supports are especially vulnerable to dissolution of the magnetite layer and erosion of the carbon steel substrate that eventually leads to a localised failure. Fig. 2 shows the effect of a rudimentary boiler feedwater (BFW) inlet deflector (first tube on the right-hand side, with holes) that compromised the circulation pattern, creating a highly turbulent stream of low alkalinity BFW that caused corrosion of the top row of adjacent tubes.
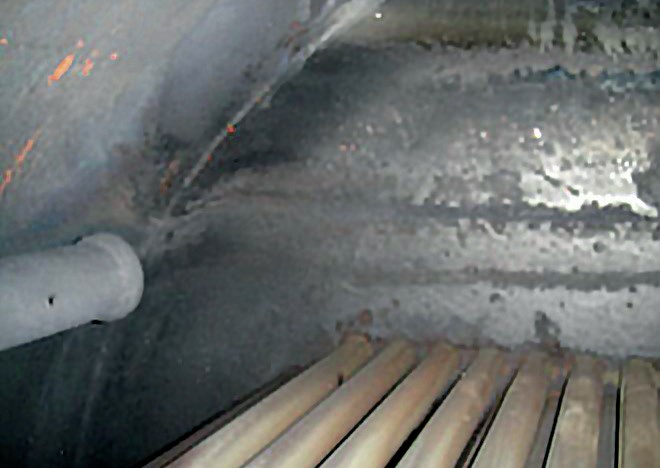
Downstream of the BFW inlet, as the low alkalinity BFW mixed with the boiler water; Fig. 3 shows the impact of lower localised turbulence and higher alkalinity: the metal surface transitions from red-coloured hematite (damage from FAC) to gray, protective magnetite. Replacing softened water with RO permeate as make-up always creates a risk of corrosion. These risks include failure to accurately feed caustic and/or phosphate to compensate for the low alkalinity (low pH) and buffering of RO permeate, and poor modulation of the blowdown flowrate due to oversized control valves.
Research confirms that there are three conditions that determine the rate of iron dissolution (i. e. generalised corrosion): reducing water chemistry, aqueous pH and the temperature of the tube surface. Fig. 4 shows that the maximum solubility of the protective magnetite, Fe3 04 , peaks at 300°F (149°C) and a pH of 8.75. In other words, the maximum magnetite solubility is the minimum stability of the protective oxide layer. Consequently, SRU sulphur condensers that operate at a nominal pressure of 50 psig (350 kPag) with a saturated steam temperature of 298°F (148°C), are highly susceptible to FAC failures. SRU sulphur condensers that have BFW with low alkalinity (i.e. low pH – “off the graph in Fig. 4”) are especially vulnerable to FAC.
Water treatment experts often cite ASME Guidelines as a source of specification limits for boiler feedwater and boiler water chemistry. However, while ASME Guidelines show specifications for total alkalinity, there are no specification limits for OH alkalinity (the only kind of alkalinity in high purity water).
For SRU systems that have high-purity BFW, the assumption that the specification limits for total alkalinity are suitable is incorrect. The footnote for the specification limits for total alkalinity for steam generators operating at or below 600 psig (4,200 kPag) drum pressure assumes the use of high-alkalinity BFW:
“Maximum total alkalinity consistent with acceptable steam purity. If necessary, should override conductance as blowdown control parameter. If makeup is demineralised quality water and boiler operates at less than 1,000 psig (6,900 kPag) drum pressure, the boiler water conductance should be that in table for 1,001-1,500 psig (6,900-10,300 kPag) range. In this case, the necessary continuous blowdown will usually keep these parameters below the tabulated maximum values. Alkalinity values in excess of 10% of specific conductance values may cause foaming.”
This footnote focuses on the risks of excessively high alkalinity. A review of the historical alkalinity in condenser FAC failures (Fig. 5) shows that the problem is exceedingly low OH alkalinity. The challenge is to determine the minimum safe specification limit for OH alkalinity in SRU systems using high purity make-up.
One approach to determine a safe minimum specification limit is to review the ASME guidelines for total alkalinity for “moderately high pressure” steam generators 600 to 1,000 psig (4,200 to 6,900 kPag) because the total alkalinity in steam generators that use high purity make-up is OH alkalinity. These “moderately high pressure” steam generators often have high purity make-up but, unlike higher pressure steam generators, do not require sophisticated water treatment programs (coordinated or congruent pH-phosphate, oxygenated treatment or AVT). Experience has shown that moderately high pressure steam generators with high purity make-up water can operate reliably with a free OH alkalinity water treatment program. A conservative recommendation for OH alkalinity specification limits for SRU systems is 75 to 150 mg/L as CaCO3 .
Poor control of condenser water level
The proper water level in the condenser is above the top row of tubes just above the elevation of the blowdown collection lateral (Fig. 6); this operating condition maximises heat transfer and system reliability. Close inspection of the tubesheet in Fig. 6 show three horizontal marks, indicating three historical water levels.
The water level near the top of the tubesheet is too high; it is likely that carry-over occurred due to the small steam-disengagement space. The middle water level is the correct elevation that allows the blowdown collection lateral to collect a sample of the most-highly concentrated boiler water: just below the interface of the steam and boiler water. The lowest water level is the setpoint required to provide a sufficient amount of space for steam disengagement to avoid carryover. Obviously, this setpoint required that the plant disconnect the blowdown collection lateral, resulting in a non-representative boiler water sample.
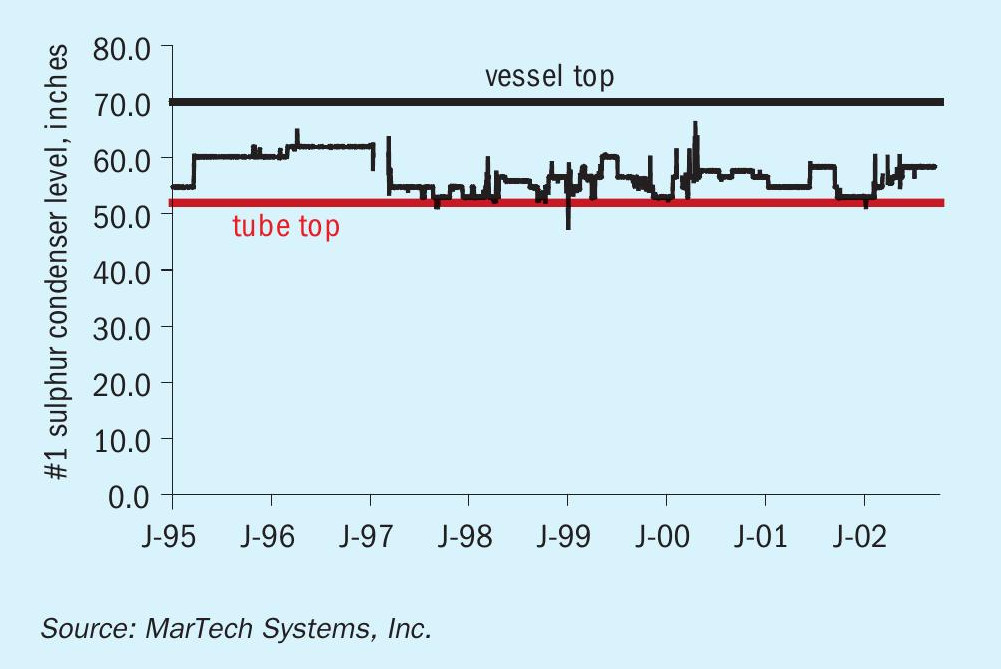
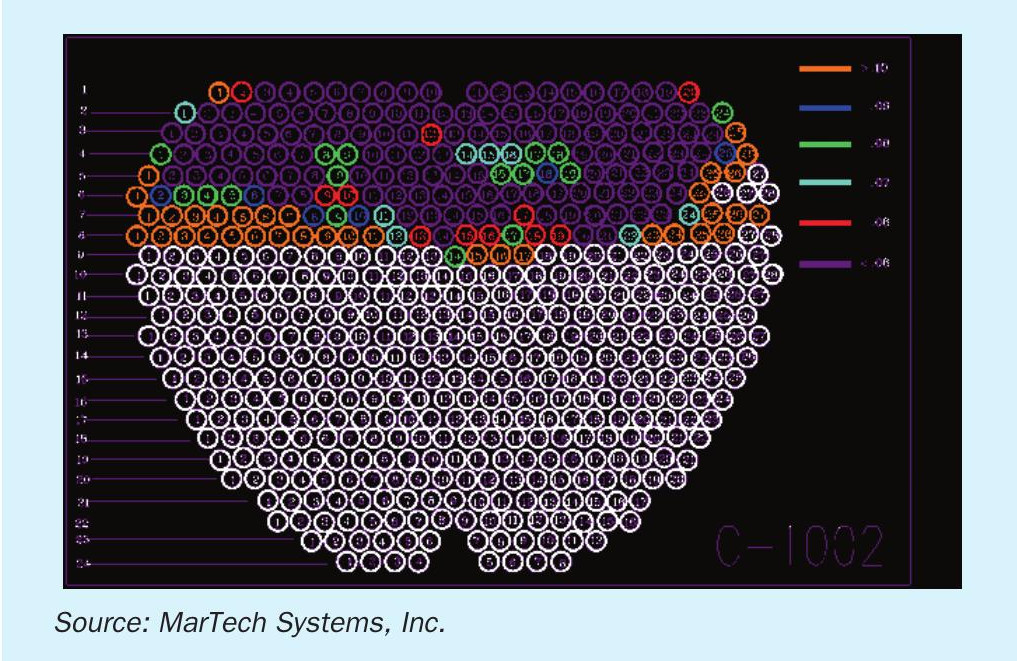
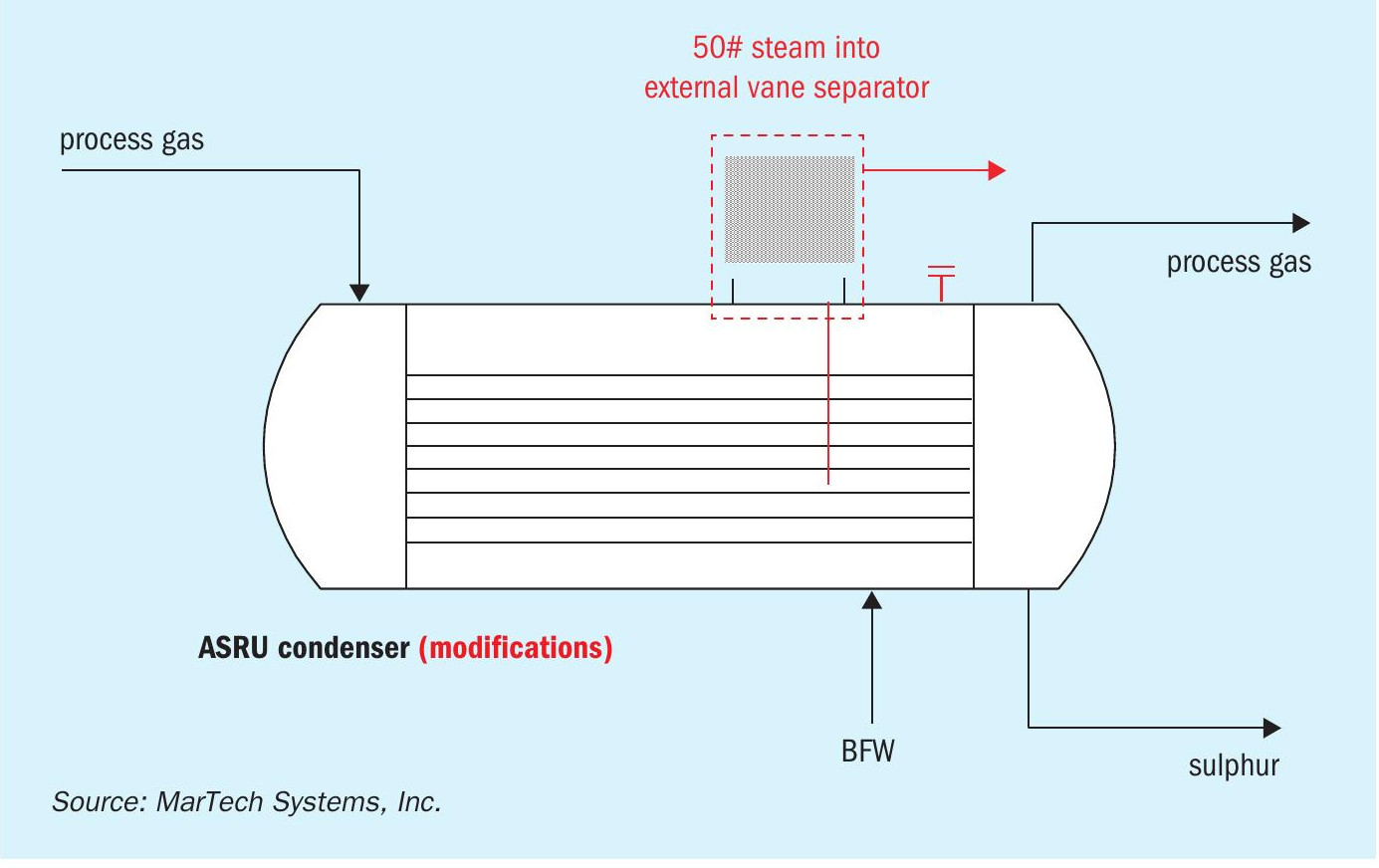
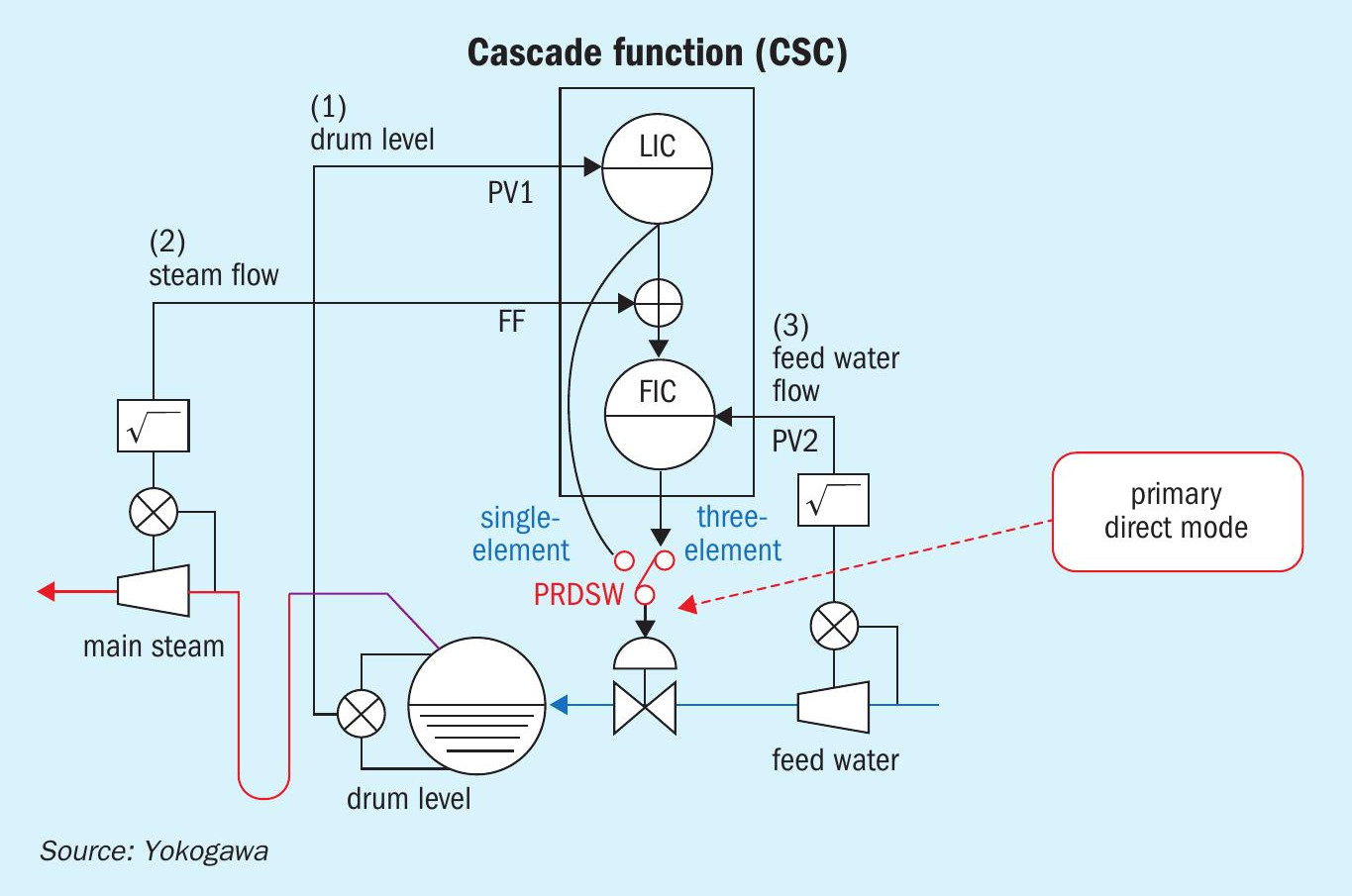
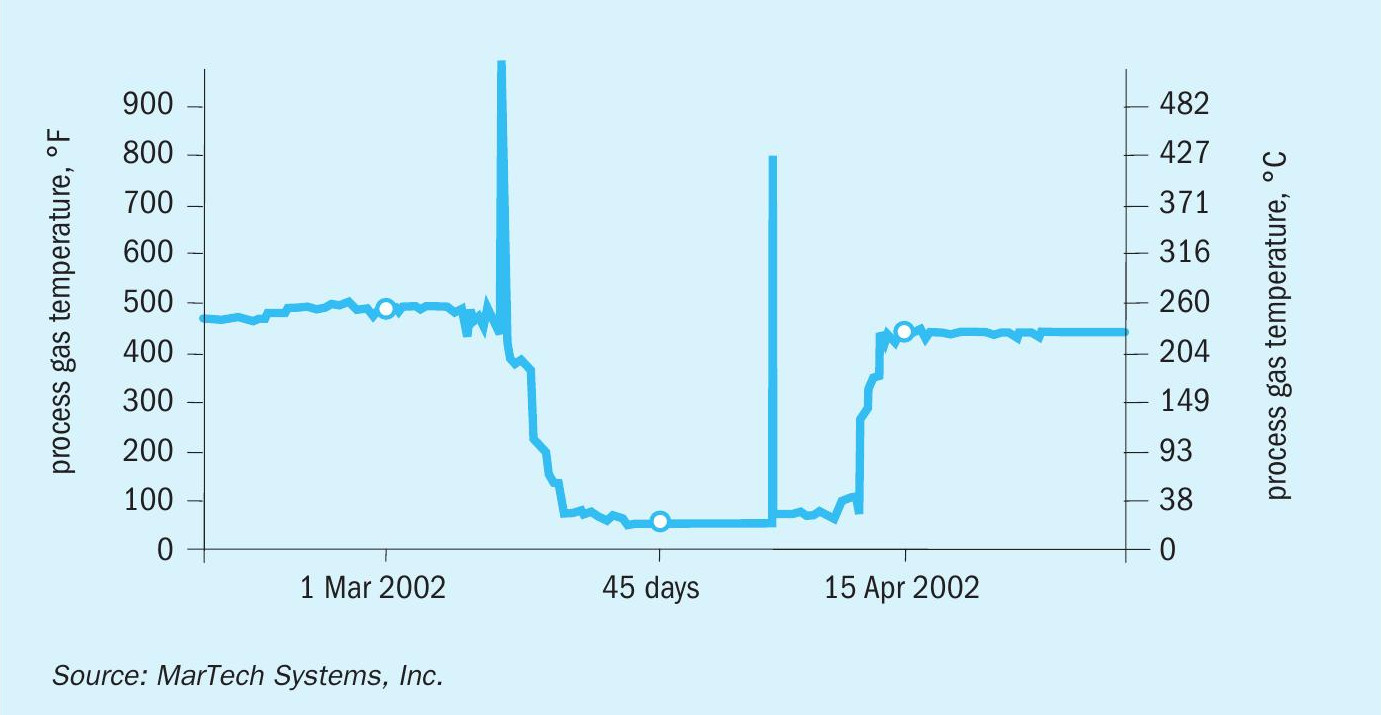
Fig. 7 shows that at this low water level setpoint, the tubes were, for the most part, below the steam-water interface, but significantly below the elevation of the (disconnected) blowdown collection lateral. The optimal water level is at the top of the (disconnected) blowdown collection lateral, approximately six inches (15 cm) above the top of the tubes.
Fig. 8 shows the results of the eddy current inspection that detected thinning, generalised corrosion, in all of the tubes in the top eight rows. The reason that there was corrosion on these tubes is likely due to the process design. Sulphur condensers operate as waste heat boilers, transferring heat from the process side to generate steam. Condensers generate steam using natural circulation; the concentration of steam bubbles is the lowest at the 6 o’clock position and the highest at the water-steam interface. Consequently, the heat transfer rate, or cooling effect, of water is much more efficient than a mixture of water and steam. In other words, the lower water level changed the “steam concentration gradient” and compromised the heat transfer efficiency and accelerated the process-side corrosion in these top rows of tubes. Note that the purple colour indicates tubes with the thinnest walls and the orange colour indicates tubes with least corrosion. The white colour indicates tubes with the thickest walls.
Solving the control issues for condenser water level are difficult and usually require an outage. This plant reviewed the design basis for steam disengagement space and determined that, even with low-alkalinity boiler water, the OEM design was not consistent with typical condenser configurations. At the next turnaround, the plant installed external steam separators and reconnected the blowdown collection laterals (Fig. 9).
The accuracy of the level control system may be a contributing factor for poor level control. Fig. 10 shows a highly instrumented system.
Poor shutdown procedures
Shutdown and start-up activities have much greater temperature and other excursions than steady state operation for all process units, but especially for waste heat steam generators. Fig. 11 shows the temperature of the process side for a 45-day period that included an outage. The plant replaced the petroleum feedstock with natural gas to condense the residual sulphur on the process side, especially in the catalyst bed.However, the plant had no defined procedure for the water-side operation. When the plant stopped the boiler feedwater pumps, the temperature increased to approximately 1,000°F (540°C) as seen in Fig. 11. Figs. 12, 13 and 14 shows circular marks around an area of localised corrosion at the 6 o’clock location of the tubesheet. The mass of the tubesheet retained heat for a longer time than the thinner condenser tubes and transferred that heat to the portion of the tubes adjacent to the tubesheet. There was no natural circulation in the stagnant boiler water, trapping steam at the 6 o’clock position at the tubesheet. Steam has a lower thermal conductivity than water, resulting in very high metal temperatures that caused rapid corrosion (“steam-side burning”).
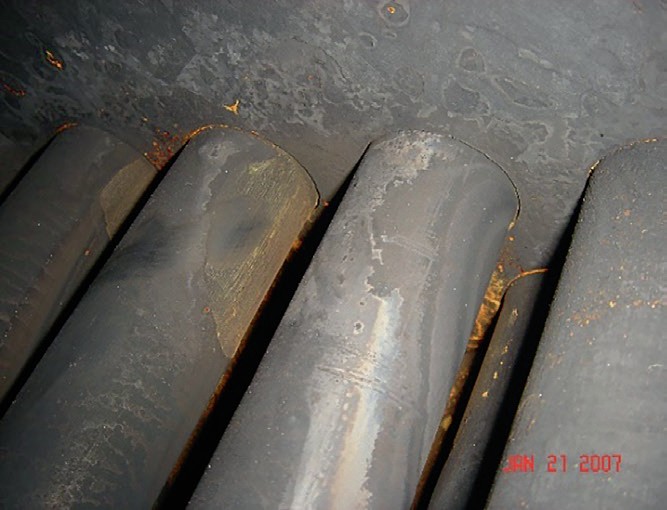
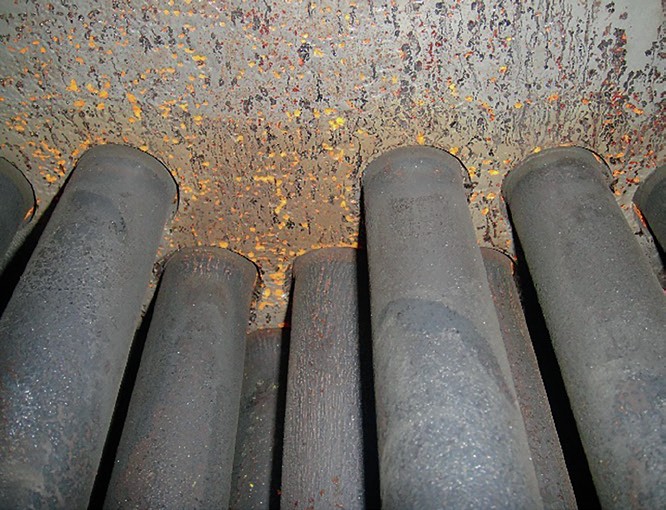
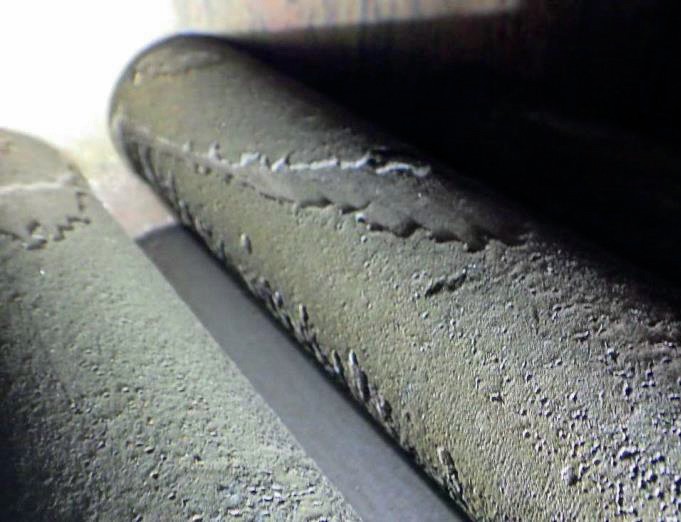
The plant may have delayed draining the water from the condensers or close the vents after shutdown, allowing atmospheric oxygen to saturate the boiler water. The tubes cooled more quickly than the tubesheet; the residual heat in the tubesheet resulted in oxygen pitting (Fig. 13). Oxygen pitting can also occur on the tubes (Fig. 14) during shutdown.
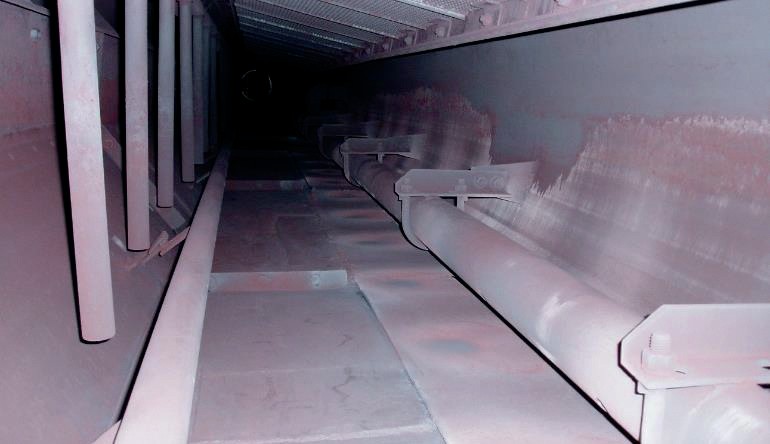
The obvious solution is to develop, and implement, an effective shutdown procedure. This shutdown procedure uses a powdered volatile corrosion inhibitor (VCI). There are several different VCI liquid and powder products. All of the VCI products use amines that have a very low toxicity and have no restrictions for discharge to the POTW (sewage treatment plant). There is no need to rinse the WHB and condensers before returning the units to service. Like neutralising amines, VCI amines are compatible with boiler water chemicals and will be present in the steam. The volatile components are amines that are compatible with neutralising amines for corrosion control in steam/condensate systems.
Powdered VCI amines control corrosion in two ways: first, the powder dissolves in any liquid water, reacting with the dissolved oxygen and preventing the water from corroding the carbon steel surface. Second, the powder sublimes, becomes a vapour, and reacts with the water vapour.The feed rate of VCI powdered products depends on the volume of the vessel.
This basic framework of a shutdown procedure is:
1. Replace the acid gas with natural gas or hydrogen to reduce the temperature on the process side and precipitate the sulphur, especially in the catalyst bed.
2. When the process side temperature decreases below 300°F (207°C), open the vents on the waterside of the WHB and condensers. Immediately open the drains to remove as much water as possible and allow the residual heat to “dry out” the water side.
3. As soon as practical, or when the process side temperature is below approximately 100°F (38°C), lay-up the water side by feeding a powdered volatile corrosion inhibitor (VCI product) into the drains and/or the vents. After completing the VCI application, close all of the vents and drains.
Robust water-side design
The proper design and location of the boiler feedwater (BFW) inlet and the continuous blowdown system can have a dramatic effect on the circulation in both the boiler and the condensers. Take for example the most rudimentary design of a BFW inlet, where a transfer pipe ends a few inches beyond the penetration of the wall of the pressure vessel, with a 90 degree turn to direct water along the longitudinal axis.
If the location of the boiler water sample is very close to the BFW inlet, the BFW will “short-circuit”, and the blowdown will not be representative of the boiler water quality. The consequence of this design error is that the plant will not be able to properly control the chemistry of the boiler water, increasing the risk of corrosion.
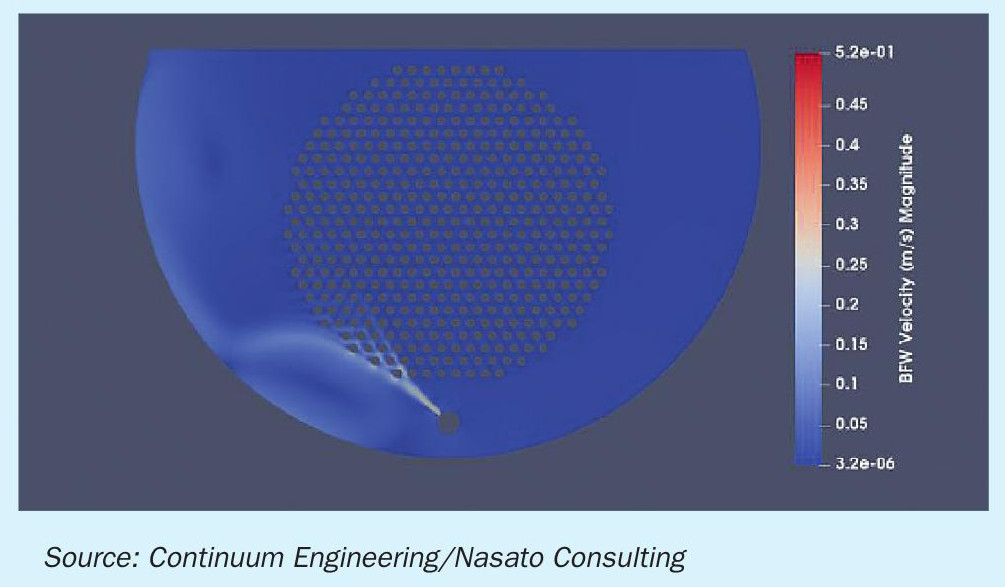
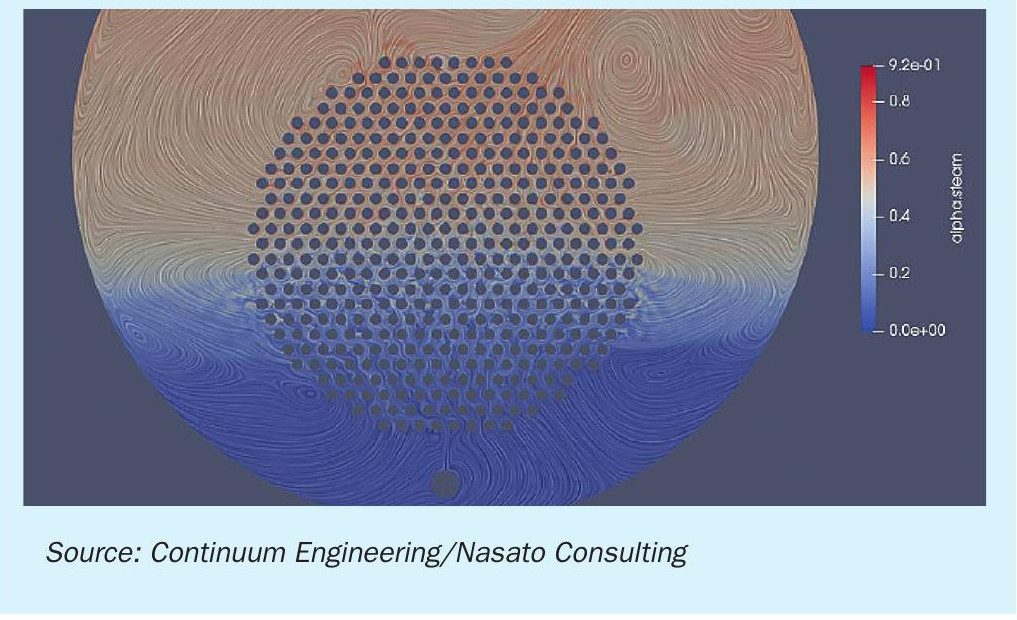
Fig. 15 shows the proper design of a BFW inlet lateral; this BFW inlet lateral is in a coal-fired boiler. However, the design of this BFW lateral is appropriate for the bottom of the kettle-style waste heat boiler, waste heat boilers and condensers. A properly designed BFW inlet distributor reduces the risk of localised areas of inadequate water circulation, off-spec water chemistry and steam blanketing in both the WHB and the condensers.
Fig. 16 shows a computational fluid dynamics (CFD) model showing the impact of a mis-aligned BFW inlet distributor in a condenser: the velocity profile and the circulation pattern compromises the heat transfer efficiency. SRU condensers are designed to operate with natural circulation that allows the steam bubbles to rise and disengage at the water-steam interface. Introducing the colder BFW at the wrong location compromises the circulation, the heat transfer efficiency, and the steam generation rate.
Fig. 17 shows a CFD model showing the velocity profile of a properly aligned BFW inlet distributor in a condenser. Proper disengagement of steam bubbles is critical to optimise the steam production rate and minimise carryover.
Confirming the process capability for blowdown based on the feedwater quality and ensuring consistent and accurate level control can reduce the risk of corrosion and fouling of heat transfer surfaces and steam blanketing, tube-thinning, carry-over and compromised continuous blowdown flow.
Priorities during turnaround
The industry continues to expand the timeframe between scheduled turnarounds. Historically, it was common to have annual turnarounds and thus known design or systemic problems were fixed in-kind. However, the modern trend is to expand the timeframe and thus reliability has become paramount. The design and operation of the process side appears to be better understood than the utility side and in particular water-side chemistry, operating practices, and good design practice. Turnaround intervals now vary between four and six years. Inspections during turnaround are important for all boilers; however, they are especially valuable for waste heat steam generators because they provide diagnostic information about the operation and integrity of the water side. Typically, the priority for inspection of the water side is much lower than the process side, creating a risk that the plant will reduce the scope or eliminate inspections of the water side.
A borescope can provide qualitative visual information about the condition of the heat transfer surfaces, the location(s) of the steam-water interface, and integrity of the inlet distributor and the blowdown collection laterals in the WHB and condensers. The water-side borescope inspections of the WHB and the sulphur condenser should be a critical turnaround activity.
Eddy current testing is especially important for “up-rated” SRU systems (i.e. operating at higher than OEM throughputs) and SRU systems that have high purity feedwater because eddy current test results provide information about tube thinning and pitting corrosion. The most important eddy current inspection is the top two rows of tubes (first 6 inches/15 cm) at the inlet of the low steam pressure generating sulphur condensers to confirm the condition of the heat transfer surfaces (e.g. presence of corrosion) and the tubesheet (e.g. off-line dissolved oxygen pitting).
Conclusion
Detecting water-related issues in the SRU requires understanding the warning signs during operation and the options for corrective actions. Reducing the risk of water-related issues requires a multi-faceted approach. The foundation of risk management is operational:
- implementing proactive monitoring practices (gathering the right kind of data, at the right frequency, properly interpreting the data, and implementing the right corrective actions to ensure consistent compliance to the specification limits for water chemistry)
- following practical operating strategies such as strict control of the water level. A third aspect to manage risk is to advocate for a high priority for waterside inspections during turnarounds.
The most challenging to minimise risk is to ensure robust water-side design, especially in operating units, to ensure that components such as inlet distributors, blowdown collection laterals, and blowdown control valve sizes are consistent with current best engineering practice and are matched to the BFW and boiler water quality.
References