Sulphur 400 May-Jun 2022
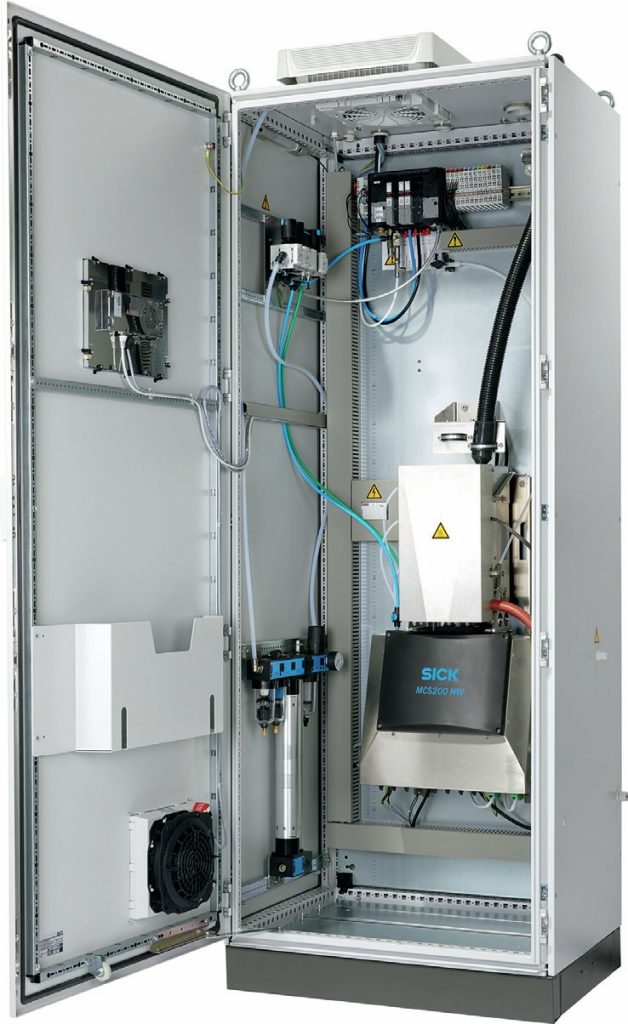
31 May 2022
Enhanced emission monitoring from sulphur recovery units
EMISSIONS MONITORING
Enhanced emission monitoring from sulphur recovery units
The trend for multicomponent analysis of emissions from sulphur recovery units is becoming more widespread. David Inward of Sick reports on a recent field trial to test the suitability of a hot extractive infra-red analyser for this application. In addition to reliably measuring and reporting emissions to air, the analyser is also capable of contributing to reducing overall tail gas emissions by supporting enhanced optimisation of the thermal oxidiser.
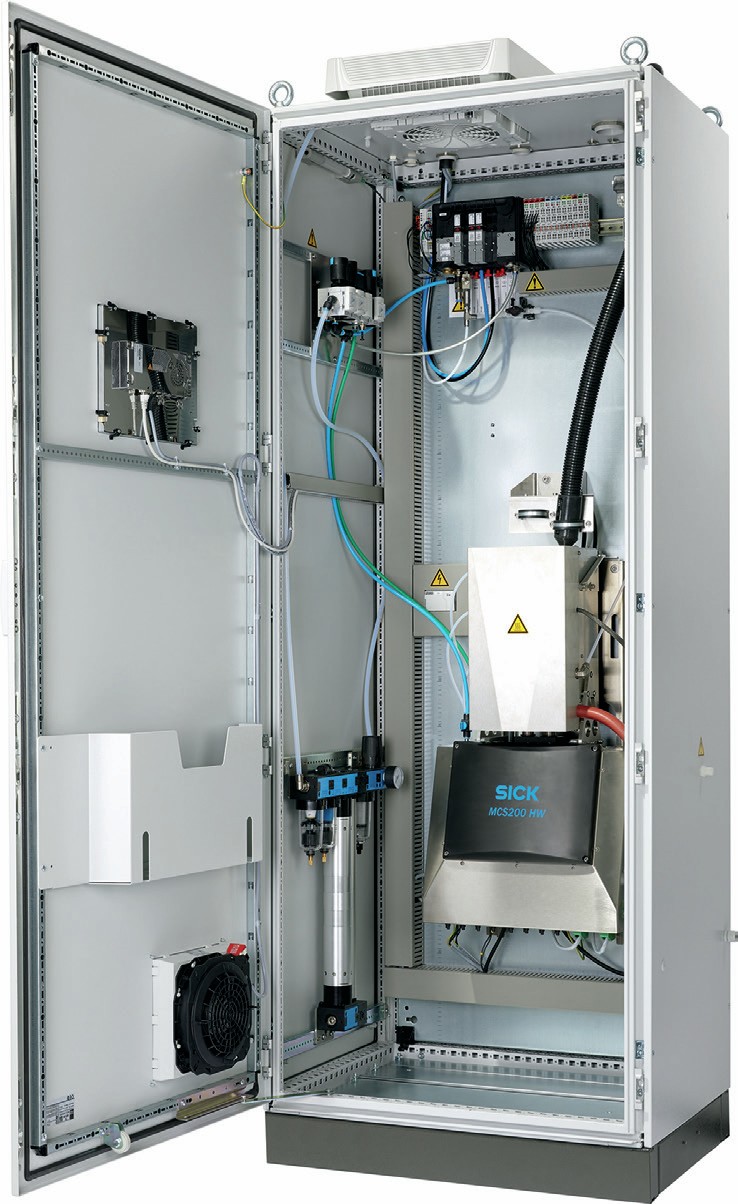
Recent trends in reporting emissions to air from sulphur plants increasingly require additional components to be measured beyond just sulphur dioxide (SO2 ). Emission limit values for both carbon monoxide (CO) and oxides of nitrogen (NOx) are now also defined for operators in the Middle East, following an equivalent trend in other parts of the world. Quantifying the mass emission of carbon dioxide (CO2 ) as a greenhouse gas is also coming increasingly into focus across the globe.
Adding more components to the emission monitoring scope from the sulphur recovery unit raises demands for an application already known to be difficult due to the unique nature of the tail gas. The presence of traces of elemental sulphur coupled with that of acidic species (SO2 /SO3 ) means that any cooling of the flue gas can result in severe blockages in the sample system or damage to sensitive optical parts.
Applying a hot extractive multi-component infra-red analyser avoids the need to cool the sample gas and so avoids these problems. The infra-red photometer is able to measure all the necessary components, even covering the new requirements.
Reporting requirements
Emission limit values are always referred to standard measurement conditions.
This requires correction to standard temperature and pressure, dry basis (i.e., at 0 vol-% water vapour) and to a defined oxygen concentration (typically 3 vol-% O2 in the case of the sulphur recovery unit).
Therefore, as well as the pollutant concentrations CO, NO, NO2 , SO2 , and CO2 , the analyser must be also able to measure oxygen (O2 ) and water vapour (H2 O).
Monitoring the mass emission of gases such as SO2 and CO2 needs to be coupled with an in-situ flow measurement and so fits an analysis technique measuring in the natural raw tail gas condition, so without water vapour removed.
System design
The MCS200 HW analyser is based on a hot extractive design base, featuring only four elements (Fig. 1).
A sample probe with heated filter element connects to a heated sample line. The heated sample line connects directly with the hot extractive infra-red analyser. The sample is drawn through the analyser by means of a heated ejector pump. The entire sampling chain is maintained at 200°C. This avoids any cold spots, which would result in deposition of elemental sulphur or condensation of corrosive acidic aerosols in the sample system and analyser optics.
The system is fully certified according EN 15267 & is available in an Ex protected version according ATEX & IEC.
Hot wet extractive multicomponent IR analyser field trial
To prove the suitability of a hot extractive infra-red analyser, Sick AG commissioned a test system on an SRU tail gas stack at a European refinery.
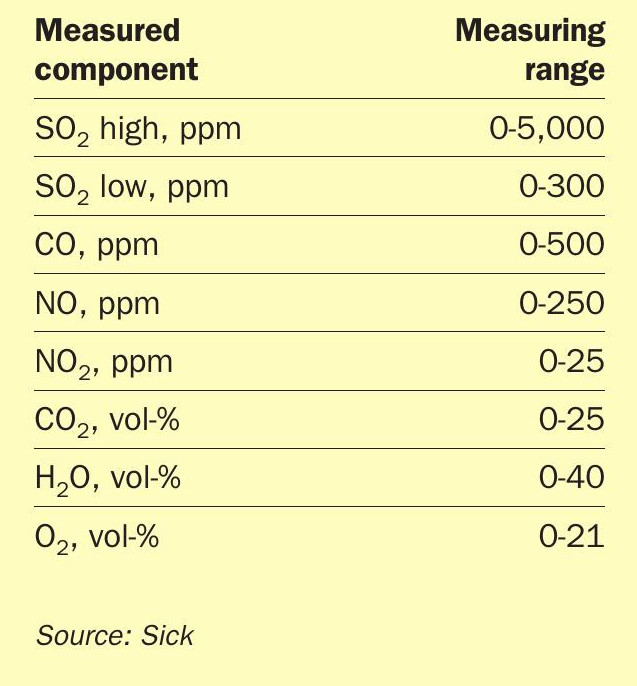
The trial analysis system was commissioned in February 2019 and operated for 11 months until January 2020 and was then replaced by a permanent installation.
The original MCS 200 HW analyser configuration is shown in Table 1.
Based on experiences gained in the field trial, the SO2 high range was increased from 0-5,000 ppm to 0-15,000 ppm. This was necessary to cover short term SO2 spikes during process upset conditions.
Similarly, the CO range was increased from to 0-500 ppm to 0-1,000 ppm.
Interesting to observe was a clear relationship between high SO2 events, triggered by a sudden increase in the H2 S concentration flowing to the thermal oxidiser, and the efficiency of CO oxidation in the thermal oxidiser.
It could be established that variability in the thermal oxidiser temperature, resulting from fluctuations in the H2 S feed concentration, created CO spikes at moments when the thermal oxidiser temperature was reduced.
Summary
The MCS 200 HW hot extractive infra-red analyser has proven itself to be a reliable, low maintenance solution capable of measuring all components needed as the basis for reporting emissions to air from the sulphur recovery unit.
Beyond the fundamental task to reliably measure and report emissions to air, it is also capable of contributing to reducing overall tail gas emissions by supporting enhanced optimisation of the thermal oxidiser.
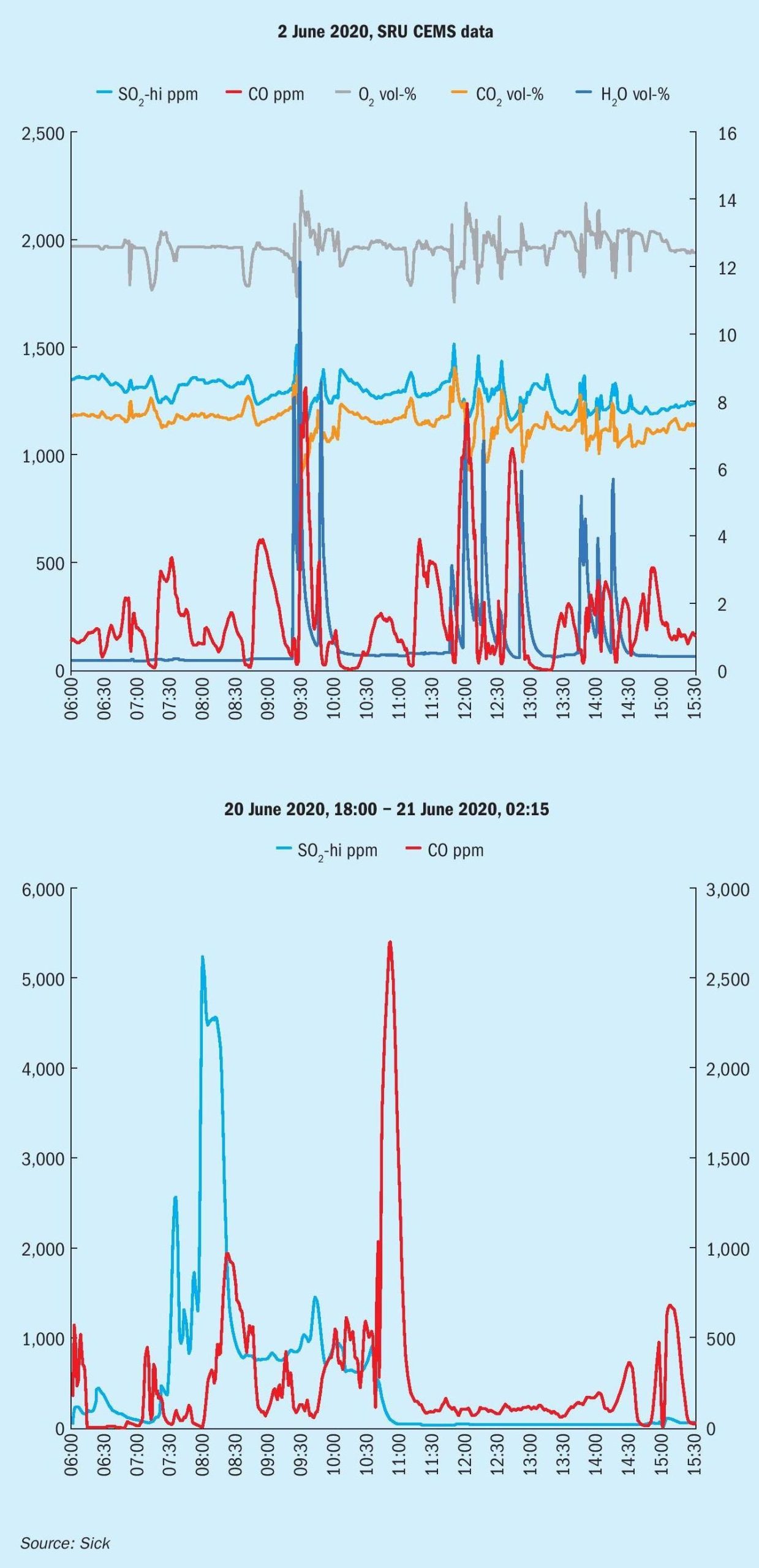