Nitrogen+Syngas 377 May-Jun 2022
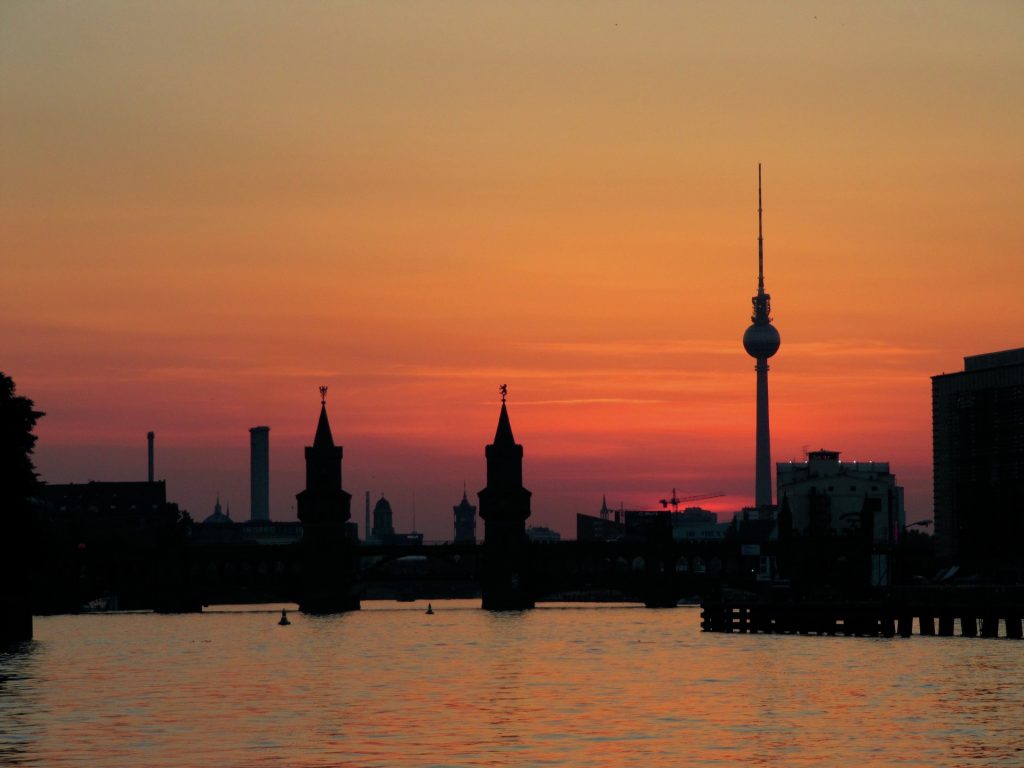
31 May 2022
Nitrogen + Syngas 2022
CONFERENCE REPORT
Nitrogen + Syngas 2022
CRU’s Nitrogen + Syngas conference returned to a face to face meeting for the first time in two years at the end of March this year.
While the current situation in China is a salutary reminder that covid remains with us, the fact that thanks to widespread vaccination we may finally be moving to living with the virus rather than simply containing it was underlined by the move back to face to face conferences. CRU’s Nitrogen+Syngas conference in the Netherlands was actually the last industry meeting that I was able to attend personally, in February 2020, just before lockdown closed in around us. This year it was back to Berlin’s unlovely Estrel Centre on the southeast side of the city for a ‘hybrid’ conference, both virtual and in person, with a packed agenda of nearly 50 papers.
Market updates
The conference began as usual with market updates from CRU’s team of analysts. Shruti Kashyap presented the gas price and nitrogen market outlook, dominated of course by events in Ukraine. The disruption to grain exports caused by the conflict has led to record crop prices, but affordability is being squeezed by higher fertilizer prices, leading to demand destruction for phosphates and potash, and switching on the nitrogen side from e.g. ammonium nitrate to ammonium sulphate. It was also possible, she said, that we could see demand destruction for nitrogen if prices remained high.
Russia represented 23% of ammonia and 14% of urea trade in 2021, two third of which had left via the Black Sea, and though the Baltic ports remained open, the OPZ ammonia pipeline across Ukraine was now closed. At the same time, gas prices had broken records in Europe, though had stabilized and were at around $37/ MMBtu when the presentation was delivered. These price levels turned Europe into a marginal producer of ammonia, ousting China from that position and leading to idling of capacity across Europe. However, with Europe setting floor prices production could be more sustainable going forward.
With 4 million t/a of Russian ammonia supply potentially lost to the market, could other producers cover this? New production is expected this year in the US, and at Ma’aden in Saudi Arabia, and there was the potential for some Trinidadian production to return. However, the price outlook is strong at least until 3Q 2022, falling as new capacity comes onstream into 2023.
On the urea side, India was still active on the spot market and new plants are coming onstream there, but imports are still rising, and urea demand could be boosted by DAP demand destruction. China was expected to keep its urea export restrictions for the time being, leading to a sharp decline in Chinese exports for 2022 – possibly to as low as 3 million t/a as the government prioritises the domestic market. In the medium term, new urea projects outweigh demand growth, especially in India and China, and excess capacity will keep prices lower, though obviously elevated in the short term by the Ukraine crisis.
Alexander Derricott of CRU explored the challenges of the fertilizer industry’s carbon footprint, including the implications of emissions tax schemes. The nitrogen industry generates on average 2.49 tonnes of carbon dioxide equivalent per tonne of ammonia produced, he said, on a par with steel or copper production. This collectively represents 1-2% of global emissions. The industry faces the challenge of cutting emissions while maintaining nitrogen output. This can be achieved by blue and green production; capturing carbon emissions or avoiding them via novel production technologies. Emissions levels are defined by feedstock, but change was coming, Alexander said, pointing to the carbon tax regimes that are now existing or coming in the EU, China and Canada, amongst others.
To complete the first morning, Kevin Rouwenhorst of the Ammonia Energy Association presented an update on ammonia’s progress as an energy carrier. He drew attention to a recent report by the International Renewable Energy Agency (IRENA) on ammonia’s use as a shipping fuel which forecast that ammonia demand for shipping could reach 183 million t/a by 2050. AEA is also working on a globally harmonised certification scheme for low-carbon ammonia to support the development of a market for low- and zero-carbon ammonia. It will quantify the absolute greenhouse gas emissions associated with ammonia production, and enable prospective producers and consumers to trade ammonia on the basis of certified, transparent, and verifiable emission reductions.
Green and blue ammonia
With green ammonia the topic of the day, the first technical session delved into that topic with presentations by several major licensors. Topsoe began, with a run through of ammonia’s advantages as a means of transporting hydrogen, as well as direct use as a fuel, especially for shipping. The break-even price remains sensitive to plant capacity; choice of electrolyser technology; cost of electricity; the EPC portion of capex, and the ammonia plant’s adaptability to fluctuating power.
Casale’s Giovanni Genova also highlighted the fluctuating power input and seasonality of operation that renewables based plants must cope with, which brings new constrains in ammonia plant design. It is necessary to analyse the dynamic of the overall system to guarantee optimal plant configuration as well as reliability and robustness for key equipment. Casale argues that its flexible ammonia synthesis loop allows optimisation of electrolyser and ammonia plant size as well as hydrogen storage, which can be a significant expense.
Deepak Shetty of Stamicarbon described his firm’s relatively new green ammonia technology, based on high pressure (300 bar) synthesis, which works well with a high purity electrolysis-based hydrogen feed. Stamicarbon is working on a 200,000 t/a renewables based plant in Kenya at the Oserian Two Lakes Industrial Park, powered by geothermal and solar energy, as well as projects in the US and Europe.
Moving to green ammonia production places different demands on ammonia synthesis catalysts as well. Julie Ashcroft of JM described ongoing technology and catalyst development work that JM has been conducting to meet the technical demands of low-pressure ammonia synthesis and low temperature ammonia cracking, including the development of KATALCO 74-1 GREEN, an ammonia synthesis catalyst optimised for operation at lower pressure, and KATALCO 27-612, a low temperature ammonia cracking catalyst, which allows for flexibility in operating temperature range for cracking and pressure range for synthesis.
Saipem’s Massimiliano Sala suggested that economics of blue ammonia production make it preferable to green for the short to medium term, and that it is possible to achieve a significant CO2 capture target with small modifications to an existing ammonia process flowsheet. Different alternatives based on available technologies such as steam reforming or autothermal reforming can be used, based on the project targets.
Biomass gasification offers another route to relatively green chemical production, and Yasuhiko Kojima of Toyo reported on work Toyo has been conducting on producing sustainable aviation fuel (SAF) using synthesis based on Velocys’ microchannel Fischer-Tropsch technology in Japan. The demonstration plant, using woody biomass, ng was commissioned in June 2020 and a regular domestic flight fuelled by the SAF was conducted in June 2021.
Decarbonising existing plants
Klemens Wawrzinek of Linde argued that in order to achieve emissions targets new green ammonia plants will not be sufficient, but existing plants must also be considered. This means carbon capture and storage – so-called blue solutions. Not only direct emissions but also indirect emissions must be considered, such as power and steam, as these significantly influence the carbon intensity of the product.
Ameet Kakoti of Topsoe presented what he described as ‘hybrid’ plant concepts, which are an important enabler for green ammonia production, revamping a plant to produce up to 10% green ammonia via coupling fuel production with power and fertilizer production could actually encourage and facilitate an increase in the scale of renewable power available, and the hybrid plant can be completely converted to 100% green production by integration of the ammonia loop and renewable technologies over time.
Dan Barnett of BD Energy Systems looked at benchmarking decarbonisation options using a computer model of the syngas plant. The path to decarbonising almost always includes exploring conventional efficiency improvements, he said, and may include the implementation of a green hydrogen package as utilities, and blue scheme improvements with carbon sequestration, each with cumulative energy improvement and decarbonisation gains. In a separate paper, BD Heat Recovery presented work conducted with Petrokemija in Croatia using pinch analysis and HEN integration as techniques for designing retrofit options for a primary reformer furnace. After replacement of an existing APH heat exchanger with an improved design and installation of an additional MP steam coil, energy savings were 0.51 GJ/t NH3 .
“In order to achieve emissions targets new green ammonia plants will not be sufficient.”
Urea technology
Takahiro Yanagawa of Toyo showcase Toyo’s new g-Urea® process, aiming at carbon neutral urea production using green ammonia made from water electrolysis, nitrogen from air separation and captured CO2 from waste flue gas or direct air capture, as well as urea production from ammonia and CO2 generated by biomass and/or municipal solid waste gasification.
Desmet Ballestra have been working on methylene urea – an intermediate in the production of urea formaldehyde resins, but also with potential use as a carrying agent for slow release fertilizers or a coating for urea granules or prills.
Another option for urea downstream production is melamine, and Casale presented their Low Energy Melamine (LEM) process with low urea melt and energy consumptions and easier integration with the associated urea plant due to the generation of anhydrous high-pressure reaction off-gas.
Materials
Stamicarbon makes valves for urea service from corrosion resistant Safurex® . Together with valve partner BHDT, the company has now developed a high pressure composite valve, using Safurex in combination with other materials. The design allows for lower and easier valve maintenance, combined with the reliability and performance at a cost-effective price. The new composite valve can also be equipped with wireless sensors for remote monitoring.
VDM Metals detailed field trials conducted at SKW Piestritz in Austria of alloys designed to show excellent resistance to metal dusting conditions as well as relatively easy weldability. VDM Alloy 699XA contains 30% chromium and 2% aluminium, and in addition to its resistance to metal dusting it also exhibits hot strength and creep properties similar to or better those of alloy 601 and a ductility at room temperature comparable to alloy 601. Dissimilar welds with Alloy 800H showed no defects in the weld zone after 18 months.
For nitric acid use, particularly resistant materials are necessary, and Sandvik described its 2RE10™ material, intended for use where there are problems with 304L type materials due to condensation or evaporation of nitric acid droplets. For process conditions, zirconium is the best choice, and Sandvik also offer a bimetallic tube with an inner layer of zirconium and an outer tube in 2RE10. If chlorides cause problems, for instance, in cooling water, SAF2304™ can be a suitable material, but for cases when a combined resistance to both chlorides and nitric acid is needed, Sanicro 28 and SAF 2906 are the best options. In high nitric acid concentrations above 80%, silicon alloyed stainless steel grades have shown the best performance. Sandvik SX™ , widely used in the sulphuric acid industry, has also performed well in strong nitric acid.
Methanol
The International Methanol Company has conducted an energy efficiency project on its 3,600 t/d methanol plant in Saudi Arabia. With the assistance of Johnson Mat-they, the target of 15% improvement in fuel efficiency was exceeded, coupled with a 25% boost to methanol production without increasing the natural gas consumption of the site.
Jens Sehested of Topsoe described his company’s research and development work in developing methanol synthesis catalysts, resulting in new discoveries on how the different components in the catalyst formulation matrix influence the performance of the catalyst under industrial conditions, and leading to a new generation of methanol synthesis catalysts.
Nitric acid
Nitrous oxide abatement remains a key concern in nitric acid manufacture. Umicore has been conducting a project conducted with thyssenkrupp Uhde focusing on the improvement of ammonia combustion efficiency in nitric acid plants and the reduction of N2 O emissions and usage of platinum group metals. The first application of a “twisted wire” catalyst shows noticeable advantages over conventional designs, including significant cost reductions and lower CO2 equivalent emissions.
Thyssenkrupp Uhde also discussed using the Organic Rankine Cycle or Kalina Cycle technology to make use of low caloric energy from a nitric acid plant, rather than dispersing it in cooling water. More than 800 kW of electrical power can be produced from the low caloric heat of a typical 1,000 t/d dual pressure nitric acid plant. It can also be used as a revamp option.
KBR’s N2 O abatement process employs a catalytic reactor upstream of the tail gas expansion unit in a nitric acid plant. At an operating temperature range of 350°C to 660°C the process achieves more than 95% removal efficiency by use of a proprietary catalyst. By operating at a higher temperature the energy efficiency of the expander is also increased,
Krastvetmet presented data from testing different catalytic systems for ammonia oxidation. Nitrous oxides may be reduced by 25-30% by changing the catalyst design at the same level of ammonia oxidation efficiency. Krastsvetmet has developed a process for single pressure nitric acid plant revamping using tertiary nitrous oxide reduction on iron exchange zeolite catalyst which removes both nitrous oxides and NOx with over 98% efficiency.
Johnson Matthey described a solution using in-burner destruction of N2 O via a ceramic catalyst developed by Yara (YARA 58-Y1) to achieve more than 90% abatement. The operating conditions immediately below the catalyst create mechanical challenges that must be overcome, as described in the presentation.
Operating improvements
Several papers tackled operational improvements to plants. Koch Engineered Solutions presented computational fluid dynamic modelling cast studies to highlight the challenges related to reformer revamping and new, stringent NOx emission requirements, as well as operational issues due to poor combustion performance or an increase in existing reformer capacity, and solutions for revamping reformers, providing guidelines for air balancing, accurate reformer CFD modelling, reformer layout, and burner design.
Alfa Laval examined the pros and cons of syngas boiler design to recover process heat, aiming to optimise process and mechanical dimensions and minimise the amount of expensive construction materials. Engro Fertilizers discussed the discovery of a hairline crack was observed on the main Natural Gas Feed Line towards the Primary Reformer at their plant in Pakistan. The site team were able to install a box to contain the leak, avoiding an expensive shutdown.
Finally, two papers from Fatima Fertilizers discussed emergency scenario planning for a vintage ammonia-urea plant, including layers of protection enhancement and an upgrade to the emergency shutdown system, as well as work on dealing with a methanator feed tube leak during start-up, tackled with assistance from Topsoe remote monitoring of the converter via their ClearView advanced monitoring tool.