Sulphur 401 Jul-Aug 2022
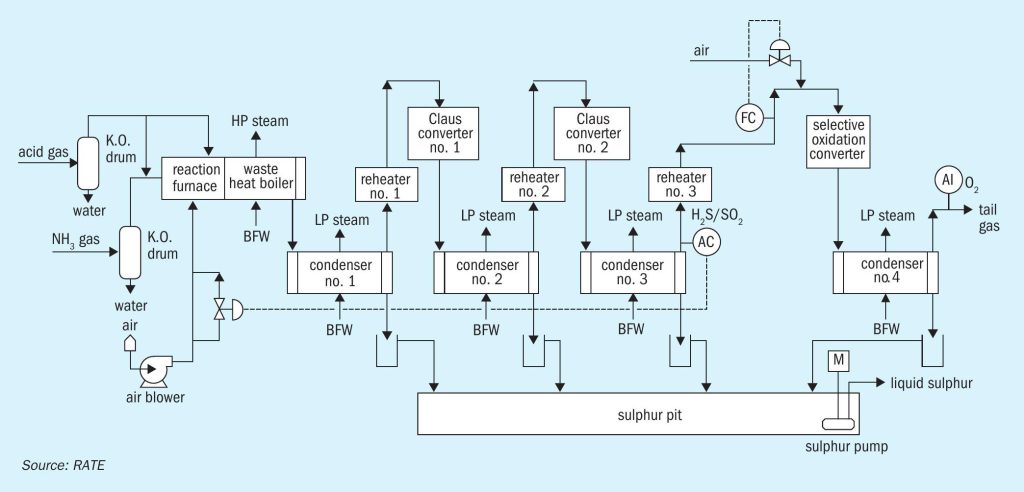
31 July 2022
Advanced catalysts meeting the need for stricter regulations
SRU CATALYSTS
Advanced catalysts meeting the need for stricter regulations
M. Rameshni and S. Santo of Rameshni & Associated Technology & Engineering (RATE USA) report on advanced catalysts for increasing the sulphur recovery efficiency of new and existing sulphur recovery units to meet stricter environmental regulations.
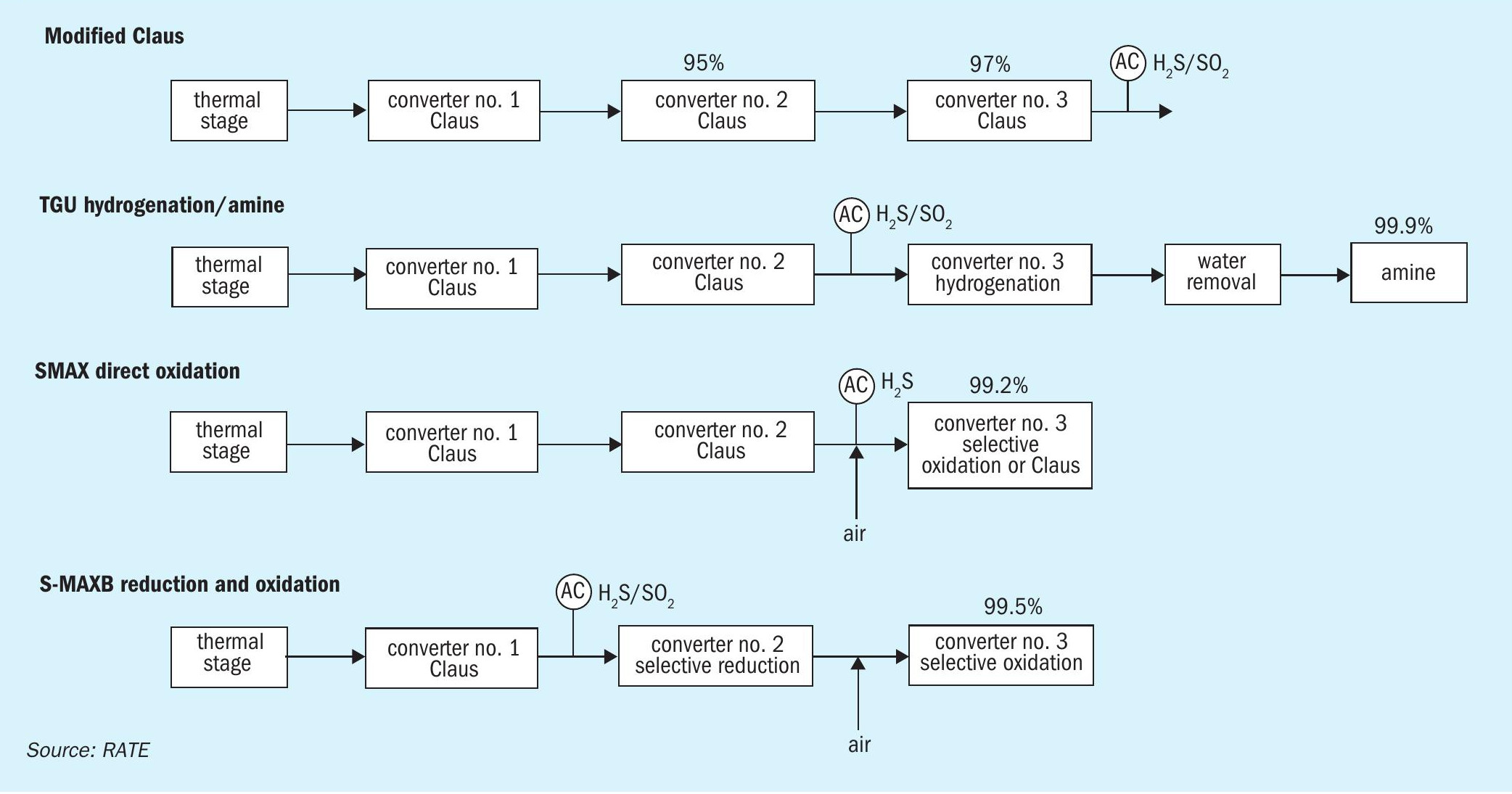
The US and Europe are required to meet SO2 emission limits ranging from 250 ppmv to less than 50 ppmv depending on the local regulations. The World Bank has also set the SO2 emission limit to less than 50 ppmv for the funding of new investments which translates to a recovery of 99.99%. However, in other countries like Canada, Mexico, some of the countries in the Middle East and CIS region, especially Russia, Kazakhstan and Uzbekistan, such tight regulations are not required. A number of years ago, sulphur recovery units were designed for plants in Canada, Mexico and other locations which included a conventional tail gas treating unit after the sulphur recovery units but since there was no requirement for tight SO2 emission limits, the tail gas treating units were never built or the facility never started up their new tail gas unit as the three-stage Claus unit followed by the incineration was adequate.
In some cases, not using the tail gas treating unit resulted in severe corrosion and in some cases the tail gas treating unit was demolished. The three-stage Claus unit can meet a sulphur recovery efficiency of 95-97%. Recently, in the locations previously mentioned new environmental regulations now require them to increase the sulphur recovery to between 98.5% and 99.5%. These facilities are looking for a robust, simple and reliable solution to increase the recovery with the minimum investment, minimum shutdown period, minimum or no training and no pre-investment for recovery beyond 99.5%.
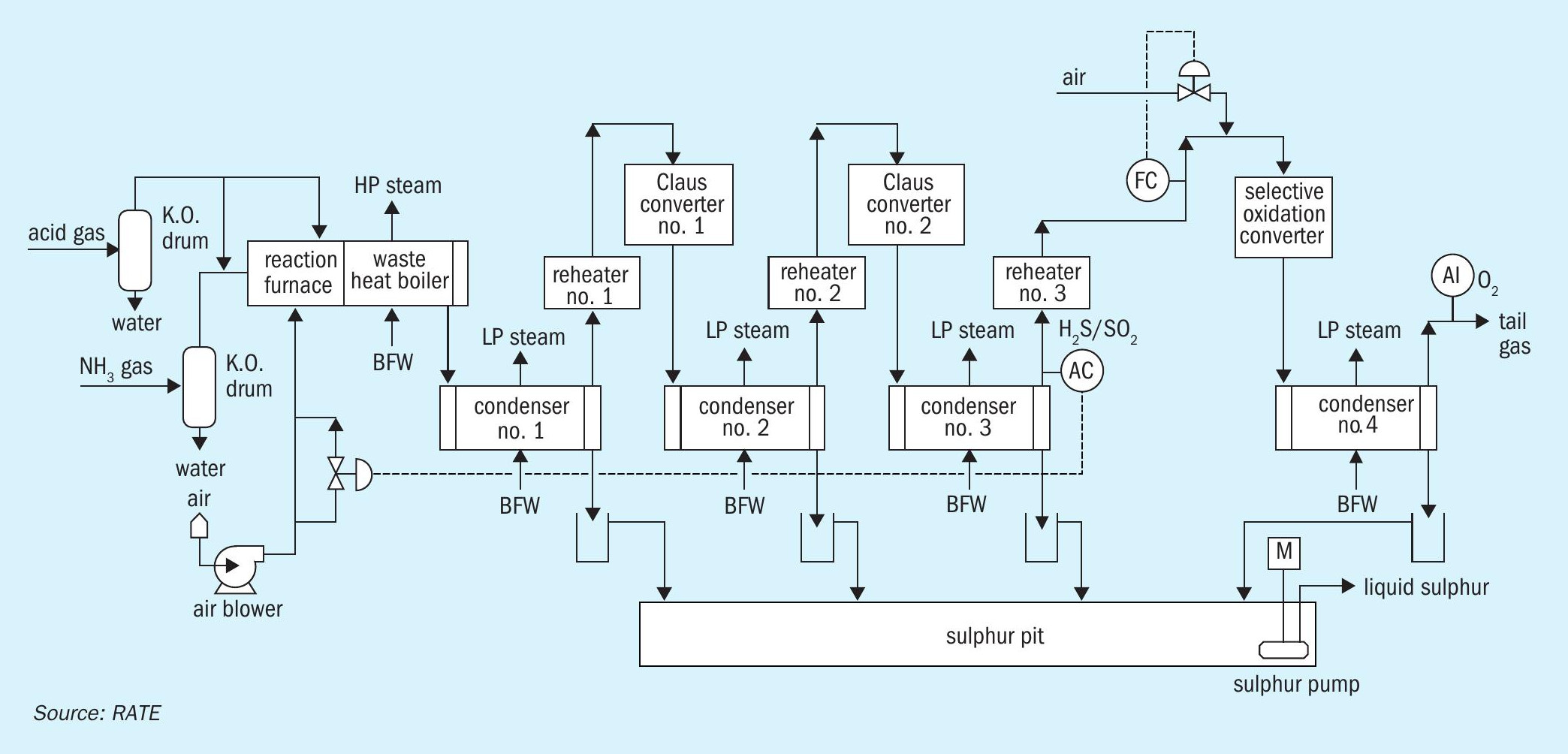
Changing the typical Claus catalysts to more advanced formulated catalysts could increase the sulphur recovery up to 99.5% and will meet such regulations with minimum modifications to the existing units as described in this article.
RATE has developed two catalysts SMAX-100 and SMAXB-100 for the selective oxidation of H2 S to sulphur and selective reduction of SO2 to sulphur.
RATE has implemented these catalysts for grass roots units and the revamp of existing sulphur recovery units in more than 20 units. This patented technology was granted by the US Patents office in 2015.
The concept of how these technologies can be implemented is shown in the block diagram in Fig. 1.
The sulphur recoveries shown in the block diagram represent the maximum achievable recovery, the ultimate recovery depends on the feed composition especially the H2 S concentration and the presence of ammonia and other impurities.
SMAX-100 catalyst
The SMAX-100 is located in the last catalytic stages of the sulphur recovery unit. A slim stream of air from the combustion air blower is mixed with the tail gas stream after the final reheater and enters the SMAX reactor. Organic sulphur species that are generated in the thermal stage are hydrolysed to H2 S in the catalytic stages and converted to sulphur in the last reactor to increase sulphur recovery. As a result, the Claus unit can be operated at the optimal H2 S/SO2 ratio, it is not sensitive to changes in H2 S/SO2 ratio, and provides process reliability, stability, and ease of the control system.
The SMAX direct oxidation concept comprises three steps:
- a conventional Claus thermal stage;
- two Claus catalytic stages;
- a selective oxidation stage that converts H2 S to elemental sulphur.
The gas from the third condenser is reheated in the third reheater, and flows to the third converter, the S-MAX reactor. Air from the combustion air blower is piped to the reactor where it mixes with the feed prior to entering the S-MAX reactor.
The remaining H2 S is reacted with O2 to form elemental sulphur in the presence of direct oxidation selective oxidation catalyst. The converter effluent is cooled in the last (fourth) sulphur condenser, before the tail gas is routed to the incinerator. An oxygen analyser located at the outlet of the last sulphur condenser is used to control the process air added to the selective oxidation converter. The tail gas stream flows to the sulphur coalescer to recover any entrained sulphur. The recovered sulphur then flows to the sulphur pit through the sulphur seal and the tail gas feed flows to the incinerator.
The direct oxidation catalyst has demonstrated its flexibility in adapting to various swings in process operating conditions, such as high and low turndown feed rates, various water content (up to 40%), and various H2 S concentrations in the feed. Under this wide range of operating conditions, the direct oxidation catalyst maintains its high activity and selectivity. The direct oxidation catalyst promotes the selective direct oxidation of H2 S to sulphur as indicated by the following reaction:
H2 S + ½O2 = 1/x SX + H2 O
Besides the main reaction, a small amount of SO2 is also formed according to the following side reactions:
H2 S + 1½ O2 = SO2 + H2 O
1/x SX + O2 = SO2
Fig. 2 shows the overall process flow diagram of the three-stage sulphur recovery unit where the last reactor contains SMAX100 direct oxidation catalyst.
SMAXB-100 catalyst
SMAXB-100 is a direct reduction catalyst that is located in the second reactor of a third-stage Claus unit or in the third reactor of a fourth-stage Claus unit depending on the desired recovery.
In order to comply with up to 99.5% recovery requirements and to minimise the investment and the capital cost RATE offers the S-MAXB direct reduction and oxidation process. This tail gas treating scheme consists of four steps:
- a conventional Claus thermal stage;
- at least one Claus catalytic stage;
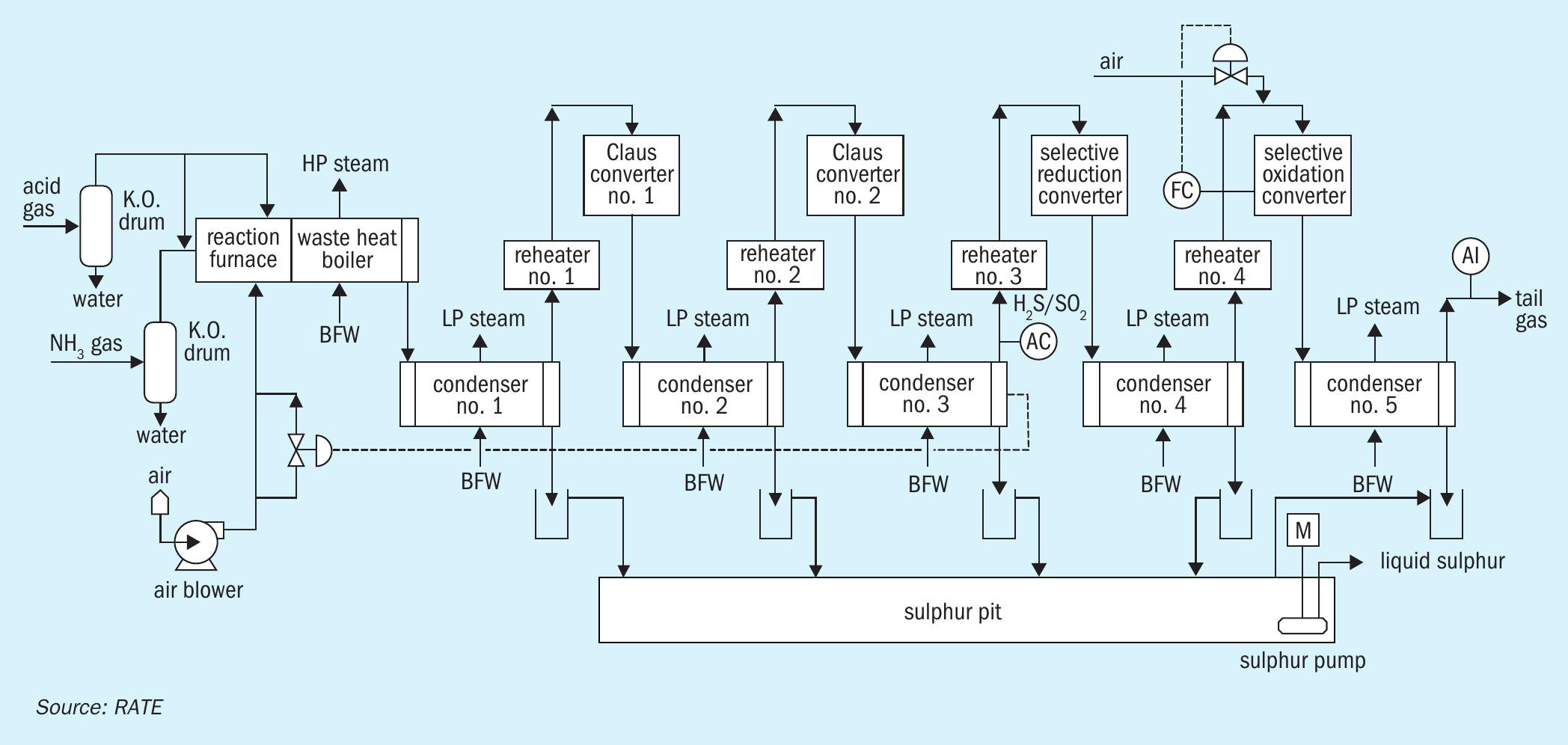
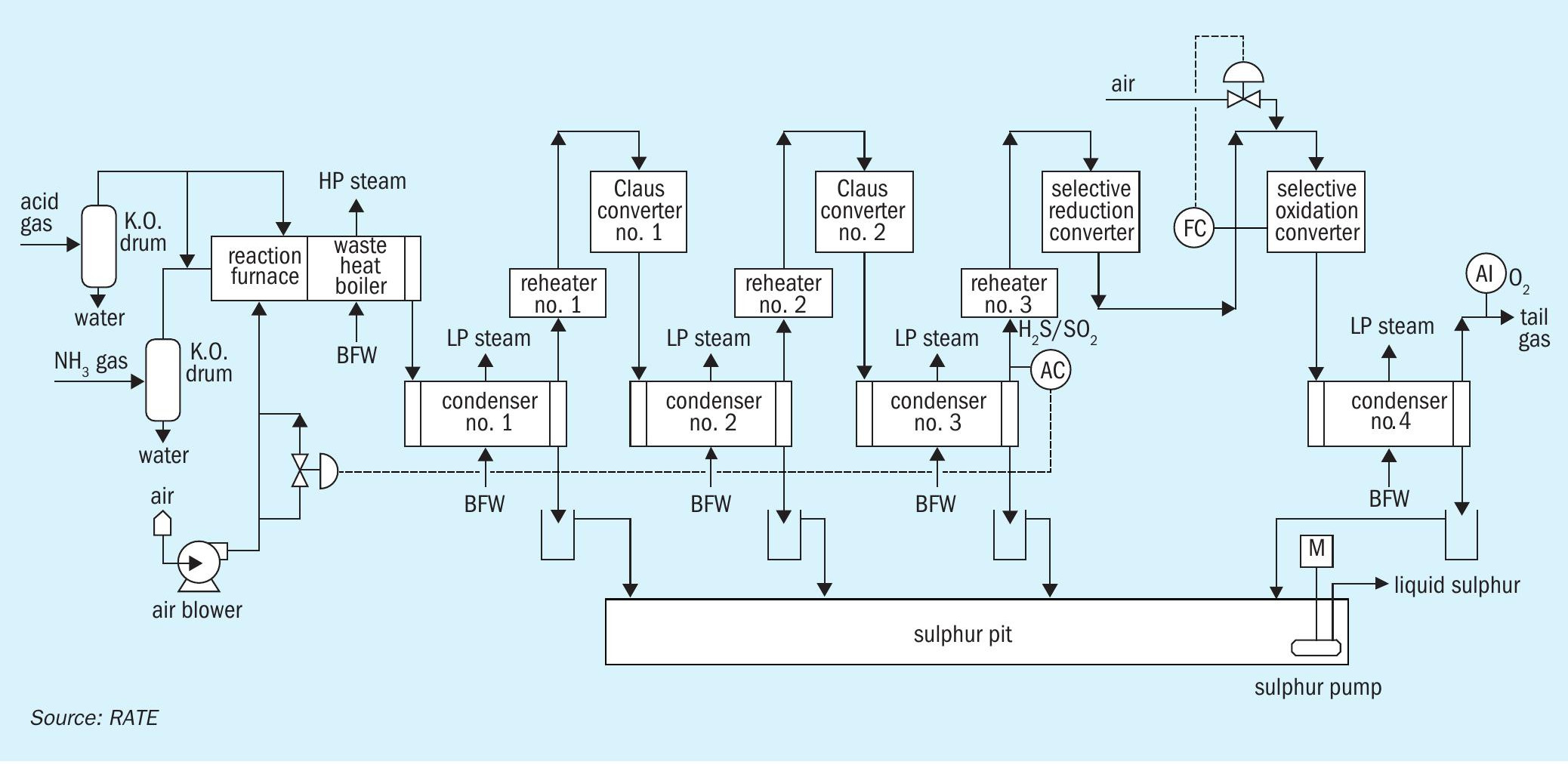
- a selective reduction stage that converts SO2 to elemental sulphur;
- a selective oxidation stage that converts H2 S to elemental sulphur.
Taking advantage of the H2 and CO produced in the Claus reaction furnace as reducing gas for the selective reduction of SO2 to elemental sulphur, no external supply of reducing gas is necessary. The description of the oxidation stage is the same as described for SMAX-100 catalyst.
Fig. 3 represents a four-Stage Claus unit where the SMAXB catalyst is located in the third stage and SMAX is located in the fourth stage.
In some cases, the third condenser and the fourth reheater after the SMAXB is eliminated as the SMAXB reactor provides an adequate temperature to the SMAX reactor (see Fig. 4). And in some cases, the SMAXB catalyst is added to the second Claus reactor and the SMAX is added to the third Claus reactor as shown in Fig. 5.
SRU revamp for increased recovery
Short descriptions of the modifications to existing SRUs in some current projects are listed below:
- Retrofitting existing two-stage Claus to 2+1 SMAX: requires adding a third reactor (with selective oxidation catalyst) to existing two-stage Claus SRU. Most of the work can be done as add-on, skid-mounted units with no need to shut down, however, tie-in of the third reactor, piping, instruments, utilities, etc. requires ≈ two weeks of unit shutdown and will improve the recovery efficiency from the current 95% to 99% or 99.1% depending on the H2 S concentration.
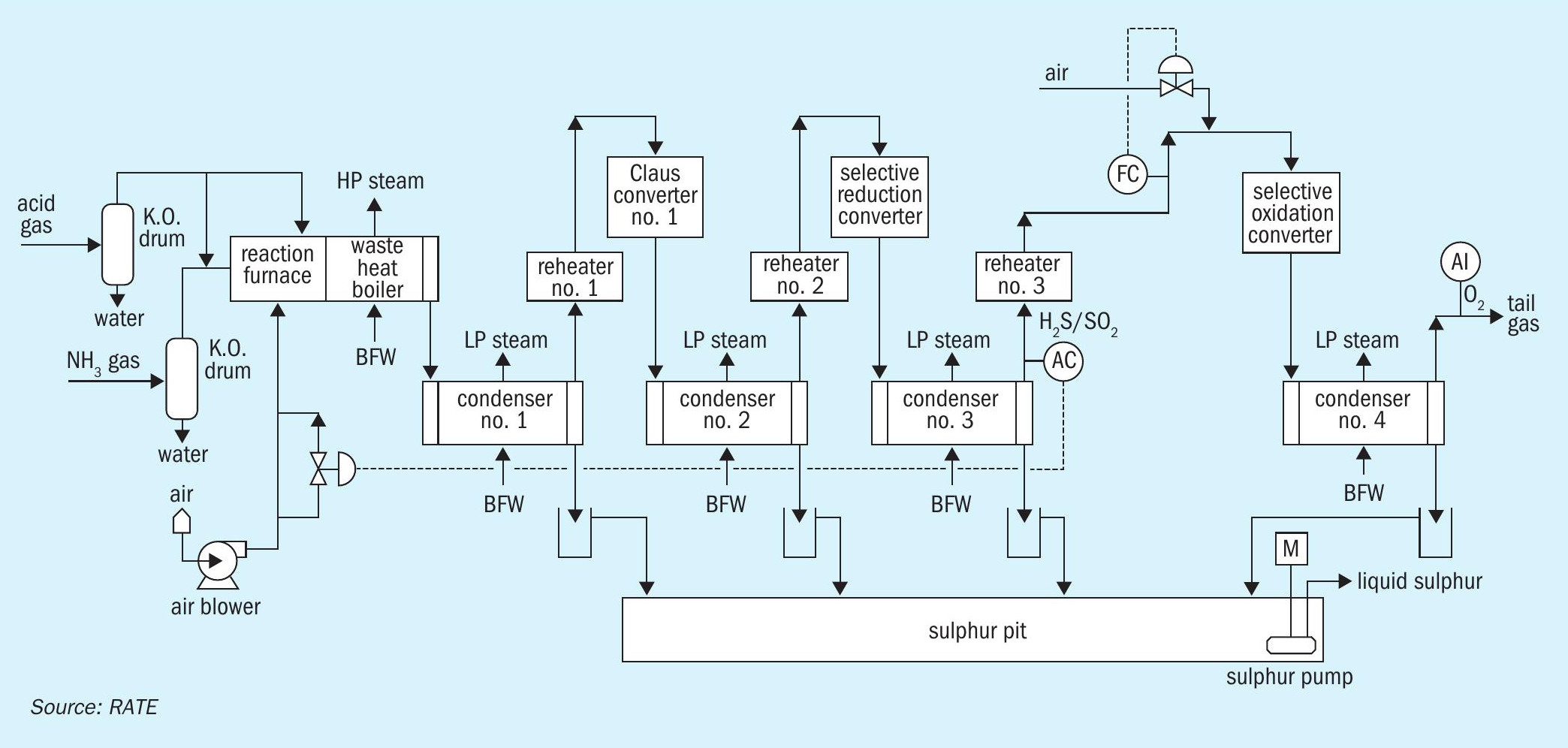
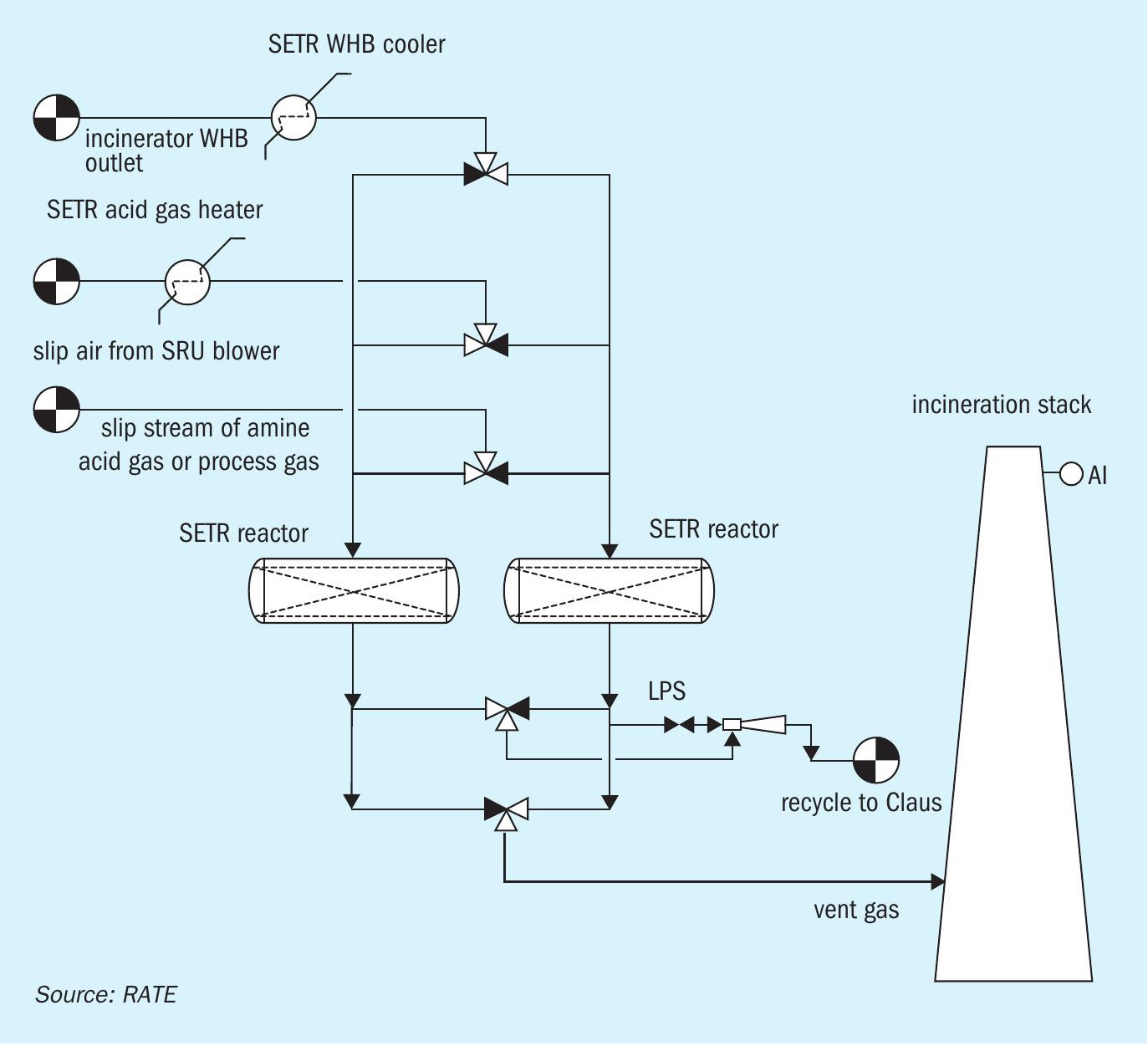
- Retrofitting existing two-stage Claus to 3+1 SMAX: requires adding a third reactor (with conventional Claus catalyst) and a fourth reactor (with selective oxidation catalyst) to the existing two-stage Claus SRU. Again, most of the work can be done as add-on, skid-mounted units with no need to shut down, however, tie-in of the third and fourth reactors and associated piping, instruments, utilities, etc. requires two to three weeks of unit shutdown and will improve recovery efficiency from the current 95% to 99%-99.4%.
- Retrofitting existing two-stage Claus to keep 2+1 SMAX: requires changing the catalyst in the second existing reactor (with combined conventional Claus + reduction catalyst) and adding a third reactor (with selective oxidation catalyst) to the existing two-stage Claus SRU (adding only one reactor and changing the catalyst in the second reactor). Again, most of the work can be done as add-on, skid-mounted units with no need to shut down, however, tie-in of the third reactor and associated piping, instruments, utilities, etc. requires three to four weeks of unit shutdown and will improve recovery efficiency from the current 95% to 99.2%-99.3%.
- Retrofitting existing two-stage Claus to 3+1 SMAXB: requires adding a third reactor (with combined conventional Claus + reduction catalyst) and a fourth reactor (with selective oxidation catalyst) to the existing two-stage Claus SRU. Again, most of the work can be done as add-on, skid-mounted units with no need to shut down, however, tie-in of the third and fourth reactors and associated piping, instruments, utilities, etc. requires three to four weeks of unit shutdown and will improve recovery efficiency from the current 95% to 99.2%-99.6%.
In all four projects listed above the pit vent stream from the sulphur pit or degassing that contains H2 S can be recycled to the front of the SRU instead of the incinerator to increase increase the sulphur recovery further. It would require more cost to recycle the pit vent stream.
The modifications required in these projects are minimal:
- if a new additional reactor is needed it can be fabricated separately, and installed during a short shutdown;
- install new (horizontal or vertical) thermowells (minimum four thermowells for four thermocouples across the height of the reactors) and relocate the existing thermowells as needed;
- replace conventional catalyst with SMAX and possibly SMAXB;
- replace the retaining grid and screens inside the reactor; l touch up the reactor refractory as needed.
SETR ADS 700 catalyst
SETR ADS 700 is an activated alumina-based adsorbent and has the same catalyst life as Claus catalyst (four to five years).
“This scheme will increase sulphur recovery efficiency from 99.5% to 99.9%-99.99%.”
SETR is another patented technology which is located after the incinerator and before the stack. The technology can be applied after any type of a tail gas treating unit, including the SMAX and SMAXB processes described earlier, in cases where the sulphur recovery needs to be increased beyond 99.5%. There is no need for the conventional tail gas treating. SETR can be added after the incinerator and before the stack.
The main difference is that sulphur is recovered and recycled back to the SRU. Caustic treatment generates a waste stream but there is no waste stream from SETR. This scheme will increase sulphur recovery efficiency from 99.5% to 99.9%99.99%.
Retrofitting an existing two-stage Claus to one of the configurations in Figs 2-5, SMAX/ SMAXB plus SETR can achieve the ultimate sulphur recovery or zero SO2 emission.
Fig. 6 represents the SETR process where the catalyst is supplied through RATE.
Summary and conclusions
RATE has developed two catalysts to increase the sulphur recovery from 95% up to 99.5% by using SMAX -100 and SMAXB100. These catalysts can be used in new or existing sulphur recovery units with no size limitation. The life of the catalysts is the same as Claus catalysts, four to five years.
For sulphur recovery efficiencies of greater than 99.5%, RATE has developed the SETR ADS700 catalyst and process which can be added after the incinerator and before the stack.
Sulphur recovery depends on the feed compositions and is evaluated on a caseby-case basis.
All three catalysts including the process schemes are patented technologies, licensed by RATE as part of the technology licensing.