Sulphur 402 Sept-Oct 2022
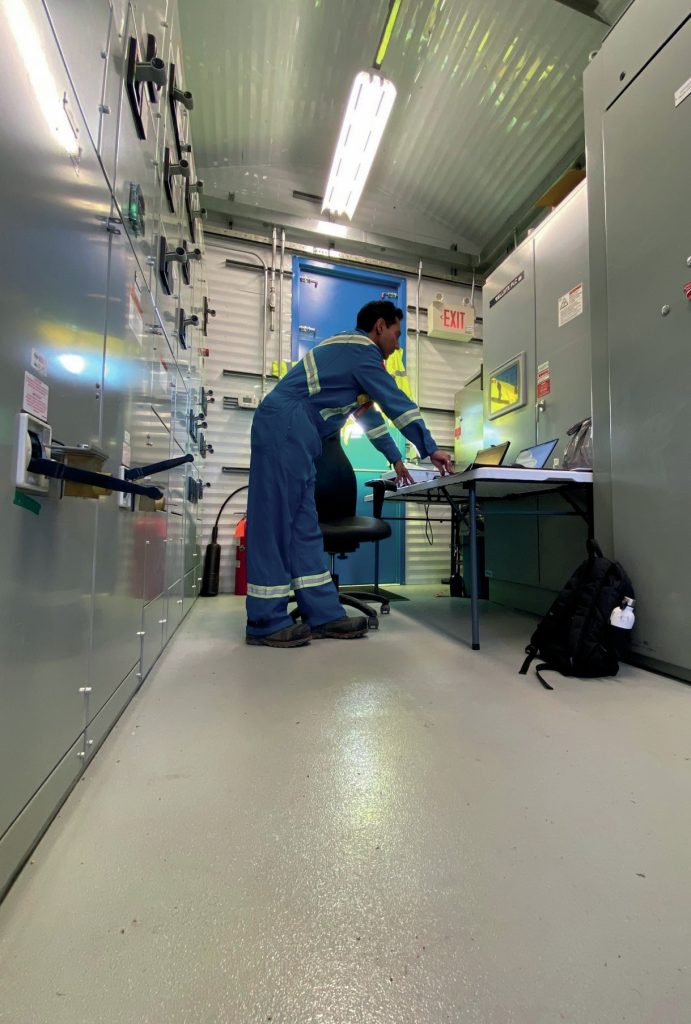
30 September 2022
Automation is great until it isn’t
SRU TROUBLESHOOTING
Automation is great until it isn’t
Inshan S. Mohammed of Sulfur Recovery Engineering shares lessons learned from a recent SRU shutdown assistance programme involving an error with the tags used within the BMS system installed on a direct-fired reheater.
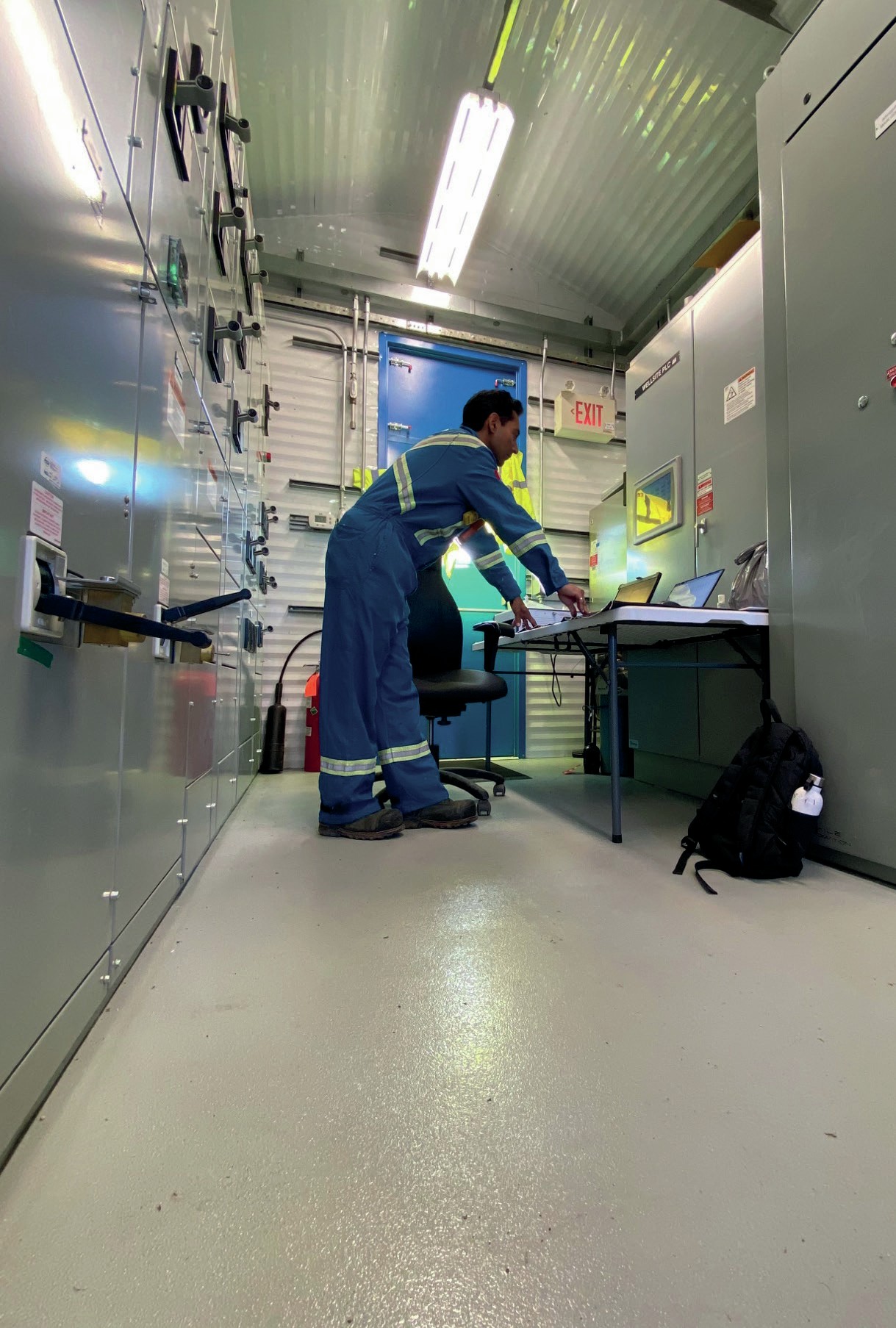
When sulphur recovery units (SRUs) were first introduced, the eloquent two to three stages of condenser, steam reheater, and catalytic converter that are present in today’s systems were not commonplace. There were varying reheat methods such as hot gas bypass, gas-gas exchangers and direct-fired reheaters also known as auxiliary burners. These latter reheat methods were commonly fired with acid gas as the fuel source. With the increased processing of sour gas in Alberta, Canada during the 1970s timeframe, a number of facilities were designed and built with acid gas auxiliary burners. At that time, starting these burners would have been done with a flame front generator, but due to their very poor reliability and performance, in most cases, simply a flare on the end of a piece of pipe, or some other similar rudimentary way, was used to light the incoming acid gas. With the introduction of distributed control systems (DCS) and an increase in safety awareness, these rudimentary methods are no longer considered safe. In addition, changes to the Alberta Safety Code, forced plant operators to install burner management systems (BMS) on these auxiliary burners. For many locations these operating companies are going through their first turnaround with their BMS-enabled auxiliary burners.
In recent years there have been significant improvements in SRU instrumentation, especially with respect to the SRU main burner and auxiliary burners. The burners have instrumentation that is critical to the safe and reliable operation of the SRU with certain components such as flame detection, and ignitor systems that are included in the SRU shutdown system and burner management system. Although safety is a critical consideration, it is only one of many considerations when designing a burner management system. Critical design considerations include reliability of the hardware and software BMS equipment, and ease of operation and maintenance. Once the BMS has been designed and installed correctly, a very critical step is the training of operations and maintenance personnel, functional testing of the BMS and, tuning of the burner control loops. Field checkout of logic and functionality is critical for all aspects of the BMS operation for start-up, scheduled and unscheduled shutdown, and normal operation.
The first step in conducting a turnaround is to conduct a proper shutdown of the SRU. Sulfur Recovery Engineering (SRE) refers to the main three steps as (1) the fuel gas sweep, (2) the air purge, and (3) the cool down as these names better imply the conditions through which the SRU is subjected. In the first step, the residual sulphur within the process equipment and within the catalyst pores must be removed. In SRE’s experience, the quality of the fuel gas sweep has a direct effect on the length of time of the remaining steps of the shutdown. One main challenge is channelling through the catalytic reactors – process gas which no longer travels over the entire cross-sectional area of the catalyst bed due to inadequate flowrate and/or a blockage of a portion of the bed which is typically solidified sulphur. In sulphur plants operating at turndown conditions, as in Alberta with lower quality acid gas, channelling of the catalyst is commonplace. Industry best practice includes conducting a heat soak for typically 48 hours prior to the start of the shutdown. Typically, in a gas plant setting, acid gas is slowly replaced with fuel gas while the inlet raw gas has been cut and the remaining acids are stripped from the amine. Under natural gas, the burn stoichiometry (i.e., the amount of air present with the natural gas) within the main burner must be maintained at 95% to ensure no adverse effects. When firing at near stoichiometric conditions the composition of the fuel gas or natural gas must be known and remain constant. That is where a clear distinction between fuel gas and natural gas exists. Natural gas is normally of fixed and known composition while fuel gas can be made up of almost any mix of constituents, hydrocarbons and non-hydrocarbons. Not knowing the exact composition of the fuel gas runs the risk of either firing with excess oxygen, resulting in potential sulphur fires, or firing with significantly deficient oxygen, resulting in soot formation. The effects of a sulphur fire are quite clear. The formation of a significant amount of soot will result in heat exchanger fouling, catalyst damage and the soot will reduce SRU capacity Mitigation of both of these extremes is normally done with the observation of the flow meters; ensuring that the air is approximately 9.5 times higher than that of the natural gas, or with the BMS inputting a ratio of 9.5 into the setpoint controller. However, errors in flow measurement can result in an incorrect burn stoichiometry. For this reason, SRE relies on oxygen analysers as a secondary assessment.
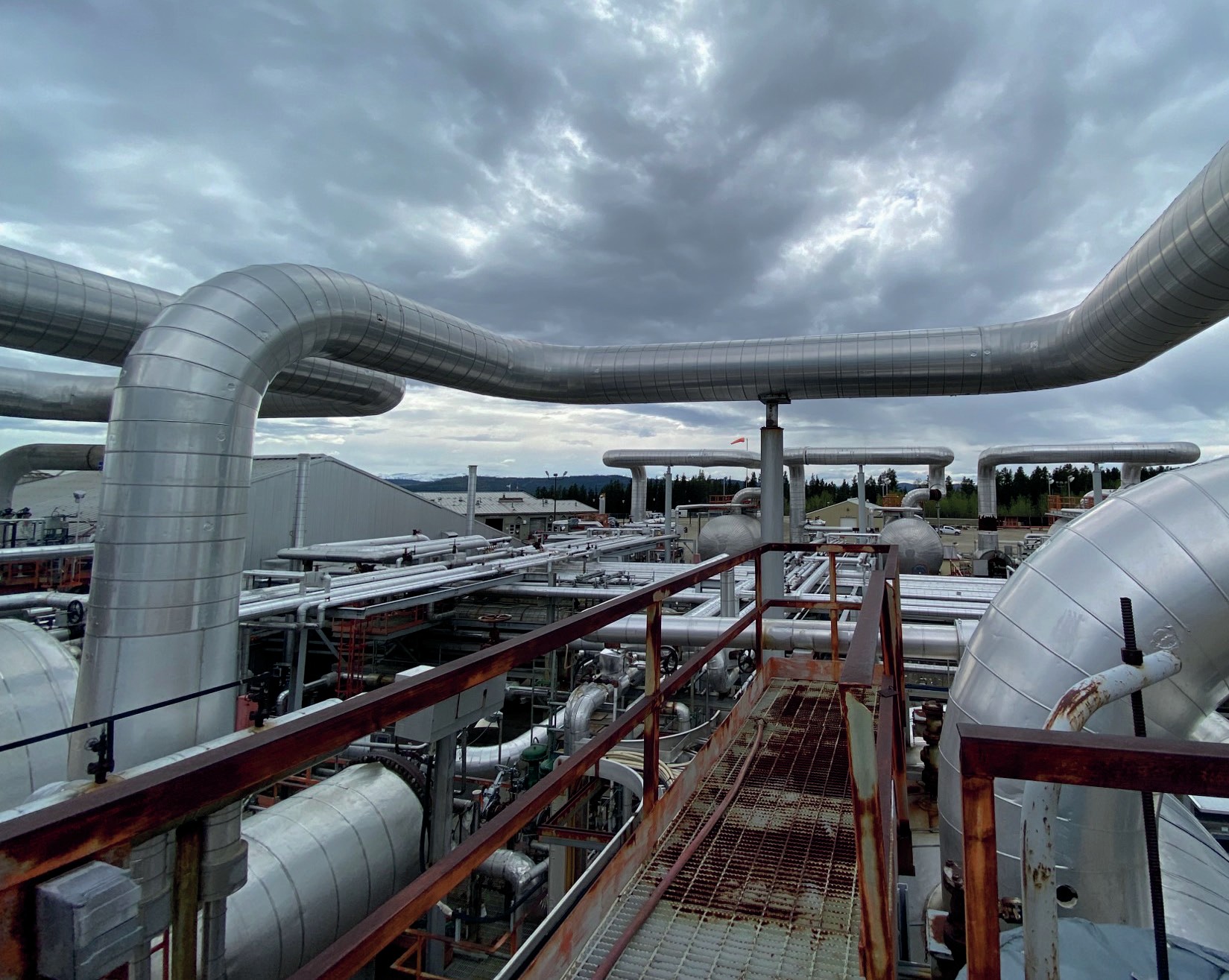
SRE helped one of its clients with conducting its SRU shutdown and an issue with the BMS system was identified as a potential hazard. Here, during the initial setup of the shutdown – switching over to natural gas in the main and auxiliary burners – an initial ratio of 9.8 of air to natural gas was used. SRE’s initial oxygen measurements indicated a very low reading from auxiliary burner 2 (approximately 50 ppm) with no signs of soot formation. Operations was informed to increase the ratio on that burner and there were slow increments of residual oxygen at its outlet: 100 ppm, 150 ppm, and 300 ppm. When reviewing the ratio controls for auxiliary burners later in the shift, it was noted that the ratio for auxiliary burner 2 was much higher than the other two. Upon closer review of the BMS, it was found that an incorrect tag was being called for the flow rate of air. This combustion air tag was not corrected and was one of the dummy tags that was installed. One positive outcome was that throughout the shutdown, no soot formation was observed from the downstream sample point. So, without SRE’s residual oxygen measurements, operations would have assumed that the 9.8 ratio setpoint would have equated to the right burn stoichiometry for the fuel gas burn, the consequences of which may have jeopardised the shutdown.
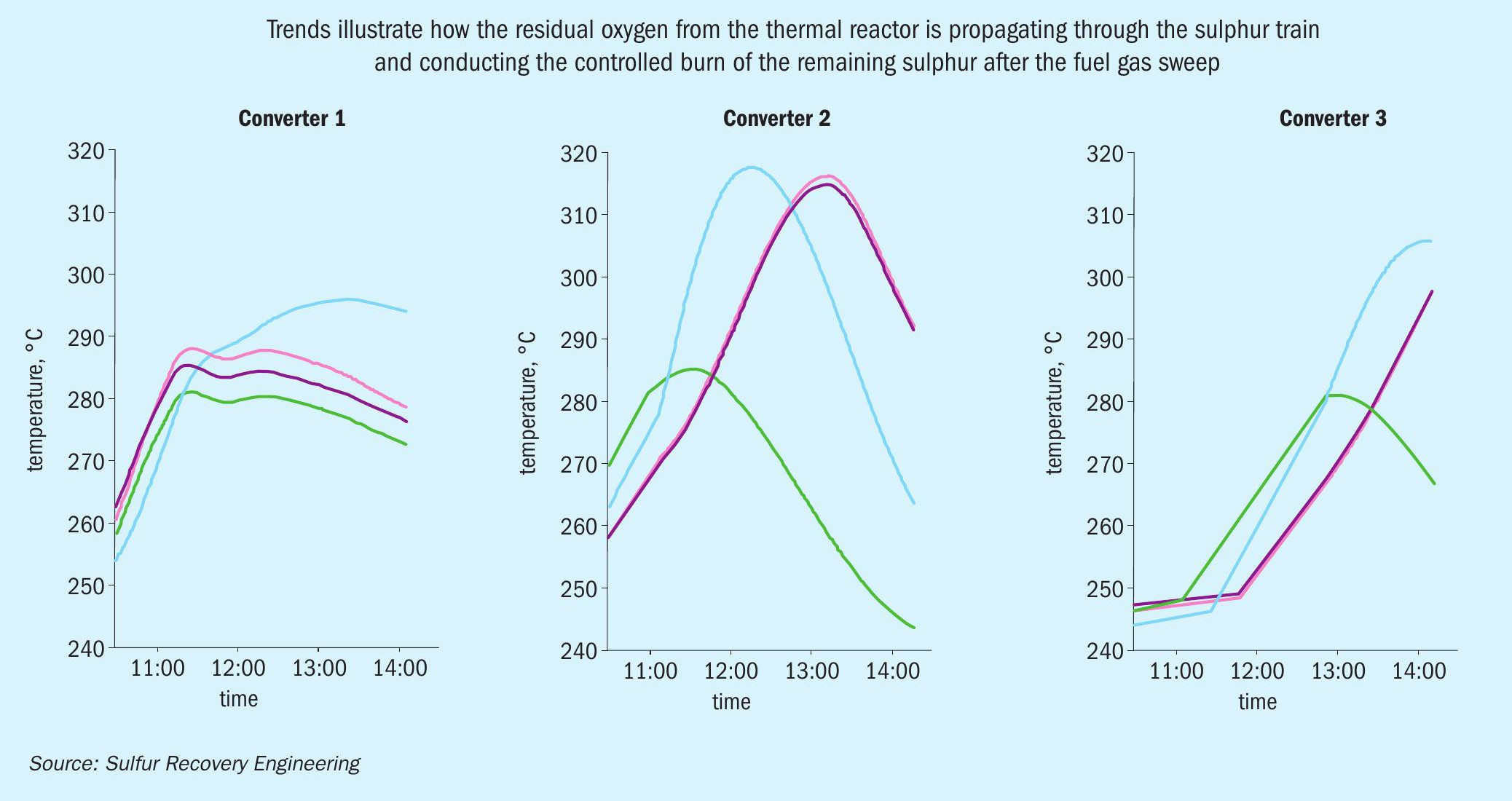