Nitrogen+Syngas 380 Nov-Dec 2022
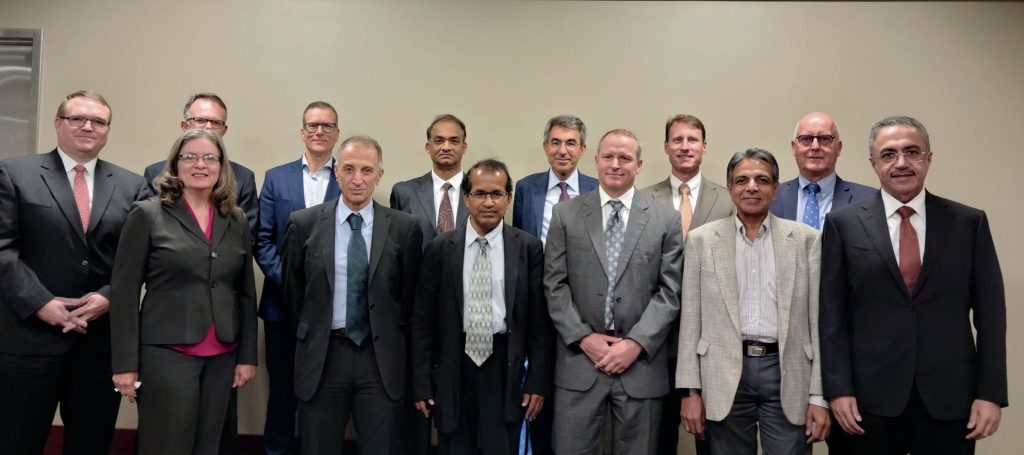
30 November 2022
2022 AIChE Ammonia Safety Symposium
CONFERENCE REPORT
2022 AIChE Ammonia Safety Symposium
Venkat Pattabathula, a member of the AIChE Ammonia Safety Committee, reports on the American Institute of Chemical Engineers’ Safety in Ammonia Plants and Related Facilities Symposium, held at the Hyatt Regency in Chicago, USA, on 11-15 September 2022.
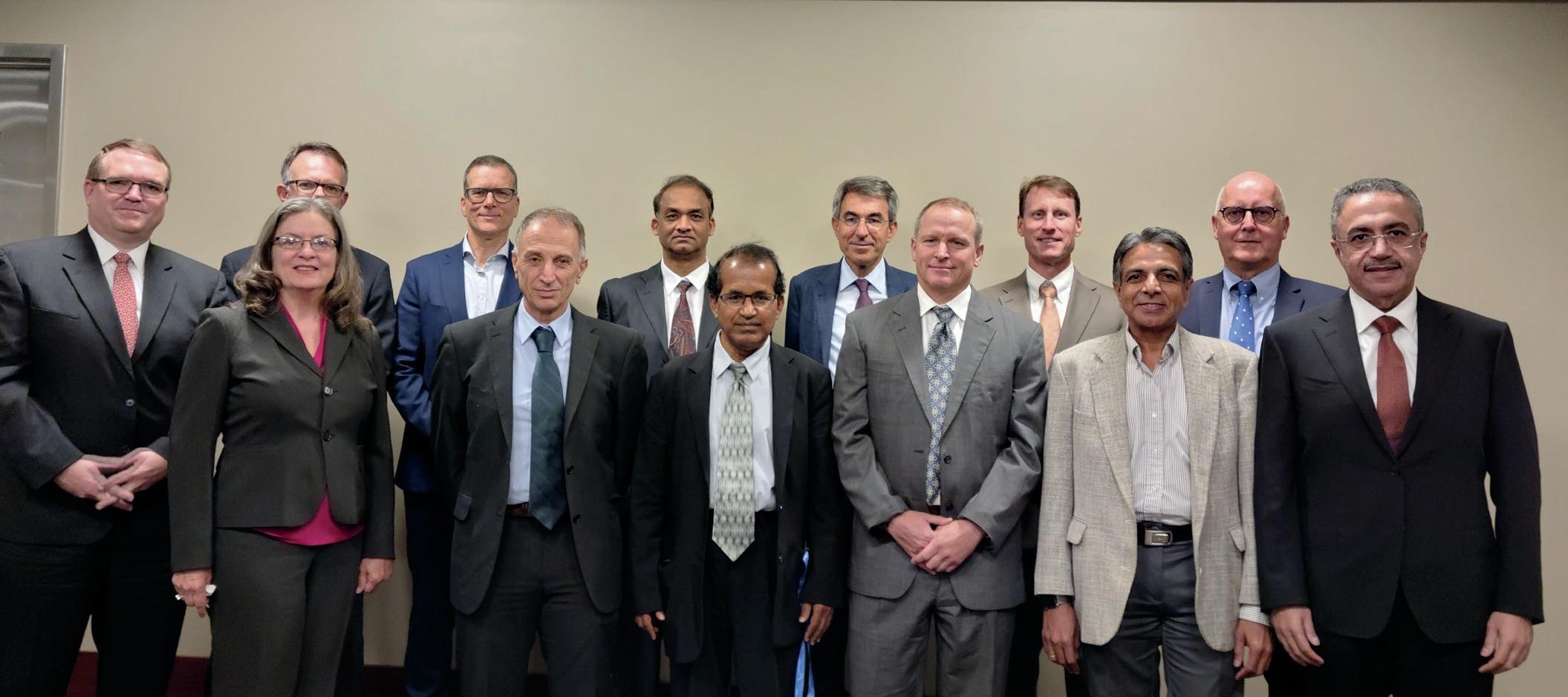
Front: Ahmed Esmael Rahimi (Qatar Fertiliser Company), Seshu Dharmavaram (Air Products), Marc Gilberston (East Dubuque Nitrogen Fertilizer), Venkat Pattabathula (SVP Chemical Plant Services), Mohamad Noueiri (Yara), Dorothy Shaffer (BakerRisk). Back: Svend Erik Nielsen (Haldor Topsoe A/S), Taylor Archer (Clariant), Federico Zardi (Casale SA), Umesh Jain (KBR), Harrie Duisters (OCI NV), Klaus Noelker (thyssenkrupp Industrial Solutions AG), Eugene Britton (CF Industries). Not Pictured: John Mason (Nutrien), John Brightling (Johnson Matthey), Ashutosh Shukla (FFI).
The Ammonia Safety Committee is dedicated to improving the safety of plants that manufacture ammonia and related chemicals, such as urea, nitric acid, ammonium nitrate, and methanol. The conference’s objective is to improve the safety performance of the ammonia industry. This is achieved by sharing information on incidents, safety practices, and technology improvements in presentations and open discussions.
Attendees who participated in the Symposium included plant managers, production managers, safety managers, process/reliability engineers, and everyone responsible for the safety and performance of ammonia plants or handling facilities. Worldwide experts discuss the latest advances in safe production and use of ammonia, case studies, and lessons learned at these symposiums. From 11-15 September 2022, about 375 engineers from more than 30 countries and 100 companies attended the AIChE’s 66th Annual Ammonia Safety Symposium held at the Hyatt Regency in Chicago.
Ammonia as an energy carrier
This year’s keynote speech, Technical, Social and Safety Aspects of Ammonia as a Carbon Free Energy Carrier” was presented by Tobias Birwe of thyssenkrupp Industrial Solutions (tkIS). Tobias said that of the 180 million t/a of ammonia produced every year, around 80% is used for fertilizer production, and around 20 million t/a is globally traded. But new uses are coming, particularly ammonia as an energy/hydrogen carrier. Social and commercial drivers include the objective announced by EU and G8 leaders to reduce greenhouse gas (GHG) emissions by 80% below 1990 levels by 2050. Over the coming decade, non-hydropower renewables capacity is expected to grow by just over 1,400 GW, totalling 2,770 GW, and the cost of solar and wind power has seen an 80% decrease over the past decade. Recent subsidy-free offshore wind bids in Europe close to or below $20/MWh have been seen. Since 2010, the cost of electrolysis has fallen by 60%, from between $10-15/kg of hydrogen to as low as $4-6/kg today. President of the European Commission, Ursula von der Leyen, has warned China and other large fossil fuel producers to find a way to price carbon at home or risk being hit by the EU with a planned CO2 tax on imports. The World Bank expects carbon pricing to be at least in the range of $40-80/tCO2 e by 2020 and $50-100/tCO2 e by 2030 to deliver on the Paris Agreement targets.
Ammonia is an ideal hydrogen and energy carrier. Hydrogen liquefies only at extremely low temperatures: -253°C, and this consumes up 40% of the energy bound in the hydrogen. Ammonia liquefies at around -33°C and has a higher energy density than hydrogen (by volume): 33% more energy. Renewable ammonia will either come from blue (carbon capture and storage coupled with conventional reforming technologies) or green sources, the latter using the electrolysis of water via renewable energy. However, greenhouse gas (GHG) accounting will be crucial, measuring the carbon emissions that contribute to a company’s or entity’s carbon footprint, including both direct and indirect carbon emissions.
On the energy side, ammonia can be co-fired in fossil power stations, though it faces challenges in burning slower than other fuels and being more difficult to ignite, as well as generating NOx. Tests have been conducted, in particular in Japan, mixing ammonia with coal in power plants, This requires only minor changes to existing power plants. In coal-importing countries, power stations are also often located at sea, ideal also for ammonia import. Plants have some experience with ammonia handling due to its use in the SCR unit for NOx removal.
Looking to the future, it will be possible to develop gas turbines for ammonia or ammonia/natural gas mixtures. This requires a larger combustion chamber and can be a difficult match if the variation of mixing rates is foreseen. In existing gas turbine power stations changes of fuel also changes the heat recovery balance. But a demonstrator 100% ammonia gas turbine was tested in 2016 in Japan. Mitsubishi Power is now developing a 40-MW class ammonia turbine derived from its H-25 series for industrial use and power generation, and is targeting commercialisation “in or around” 2025.
Fuel cells for hydrogen are commercially available but expensive and requires the intermediate step of cracking traded NH3 to H2 and N2 . Residual NH3 has to be removed to generate 99.97% H2 . Ammonia fuel cells could solve this problem.
Finally, ammonia has been suggested for internal combustion engines for ships. Ongoing developments include co-firing with methane, light oil, etc with NOx removal by ammonia SCR. Developers include MAN Energy Solutions and Wärtsila, supported by European Union funds. They are targeting a commercially available engine by 2024; later also retrofit packages for existing engines. A breakthrough in the marine sector is expected to lead to progress in the development of ammoniafueled propulsion engines for other purposes such as cars.
As a hydrogen carrier, ammonia must be ‘cracked’ to decompose at elevated temperature with a catalyst. It can replace fossil energy or feedstock sources if ammonia is not an option. However, there are inherent inefficiencies in converting hydrogen into and then back from ammonia.
SAFETY INCIDENTS
The key safety-related papers were:
Catastrophic failure of primary reformer due to mixed feed crossover piping rupture
Catastrophic failure of an ammonia plant primary reformer occurred due to a mixed feed cross-over piping longitudinal weld seam failure. This weld seam failure was the direct cause of an initial loss of primary containment that induced a reverse flow condition, resulting in the complete failure of other major components throughout the reformer. This paper presented the sequence of events and associated root causes that failed the mixed feed cross-over piping. Learnings were shared as the potential exists for other operators to have a similar type of failure.
Failure of the primary reformer mixed feed cross-over piping was the direct cause of the first loss of primary containment. This induced a reverse flow condition which exposed the reformer components to temperatures above their design limits to the point of failure. The mixed feed cross-over piping failure mechanism was determined to be hot/solidification cracking during fabrication due to incorrect weld geometry. This, in addition to the piping, creep expected for this piping system, resulting in a significant reduction in the expected life of the piping, which resulted in premature failure.
The following actions were recommended following this incident:
- Implement additional NDE requirements for new pipe procurement to improve inspection confidence.
- Perform NDE on existing plant piping operating within the creep region to ensure serviceability.
- Conduct an engineering review of the reforming section to determine the need to enhance the safeguards in this plant section, including mitigation against reverse flow.
- Conduct a review of all piping in elevated temperature and pressure services to identify the use of similar material in similar services and evaluate on a case-by-case basis.
Primary reformer air-steam coil alloy 800HT tube failure
This paper discussed the inspection and failure analysis findings and the effects of creep and high-temperature degradation on the alloy 800HT air-steam coil tubes in a primary reformer convection section. The recommendations, including planned replacement opportunities, were discussed. This paper included the benefits of proactive process monitoring, which indicated a leak in the air-steam coil before the turnaround. It further highlighted the importance of conducting destructive testing within turnaround scope in aging facilities to determine the root causes of failures.
The integrity of convection coil tubes is vital to the continued operations of primary reformers. It is very important to schedule and conduct inspections of these tubes during turnarounds to ascertain their integrity. Alloy 800HT has proven to be an excellent material for this service; however, this material is susceptible to creep and high-temperature degradation over a prolonged period. Aging facilities should plan for replacements based on inspection and metallographic examination results.
Ammonia release during ammonia import activity
On July 21, 2018, an incident occurred at an ammonia import facility that resulted in the accidental release of ammonia vapour. A thorough investigation identified the causes of the incident, which resulted in the quick connect/disconnect coupler disconnecting from the ship manifold flange, releasing approximately 1,000 kg of ammonia. Thankfully no one was injured, but the incident provided key learnings for the industry on safeguarding against similar future incidents.
A combination of factors led to the failure of different safeguards in the ammonia import process, resulting in the accidental release of ammonia vapour.
This incident has highlighted the importance of the following items: refresher training; procedural checks throughout the job cycle; preventative maintenance is designed in conjunction with the OEM, and project design reviews utilising human factors analysis.
Key lessons learned included:
- Hazards relating to all aspects of the unloading process must be identified, controlled and understood by all personnel involved.
- Maintenance strategies must incorporate all manufacturers’ specifications.
- All procedures created for the use of specific plant equipment must be completed by competent personnel with in-depth knowledge of the equipment and in conjunction with the manufacturer’s operating manual and specifications.
- All personnel involved in high-risk activities must be regularly verified as competent to perform those tasks.
- Critical equipment involved in high-risk tasks should have hard controls installed to prevent assumptions or mistakes and to prevent the system from progressing in an uncontrolled state.
Methanator temperature runaway results in a fire
In the 1990s and early 2000s, at least two known methanator runaways in North America resulted in equipment overheating and loss of containment. The particular incident addressed in this paper is one of those two. It occurred during the start-up of a hydrogen plant while reducing a fresh charge of methanator catalyst. Piping in the methanator circuit overheated, resulting in a large fire. Although this incident occurred almost three decades ago, it underscores the importance of having and following well-written procedures, safety instrumented systems, layers of protection, and risk awareness.
It is extremely important to maintain and follow written procedures covering potential safety scenarios to ensure appropriate safety systems and safeguards are functioning correctly. It is important to have clear written procedures which cover unusual situations and recognize safety risks. The procedures at the time of this event did not include the causes and effects of high liquid levels in the V-308 product hydrogen knockout pot or high-pressure drop in the C-303 absorber. There was also no discussion of the catalyst reduction requirements in the start-up procedure written for standard plant start-ups. The operating procedures were revised to include clear guidance for these situations.
It is also important to follow written procedures. In this case, the NMP solvent was not checked for water content to verify that it was low. More importantly, the methanator was not bypassed when the outlet temperature rose above 850°F (454°C).
This incident also emphasised that safety instrumented systems are needed to safeguard against high-risk scenarios. To protect against methanator runaways, hydrogen plants are now equipped with highly instrumented trip systems that quickly bypass the methanator on high bed temperatures using a voting system. Previous technical papers presented at this Symposium have discussed methanator trip systems in detail.
Finally, safeguards that are in place need to be checked to ensure they are functioning properly. In this case, the CO2 analyser incorrectly displayed false low CO2 concentrations. Layers of protection are important. In this case, the second layer of protection would have been to manually sample and analyse the gas to verify it contained less than 2% CO2 before feeding it to the methanator.
The Dakar ammonia accident
This incident is detailed in a separate paper in this issue.
Next year’s Symposium will be in Munich, Germany, 20-24 August.