Sulphur 404 Jan-Feb 2023
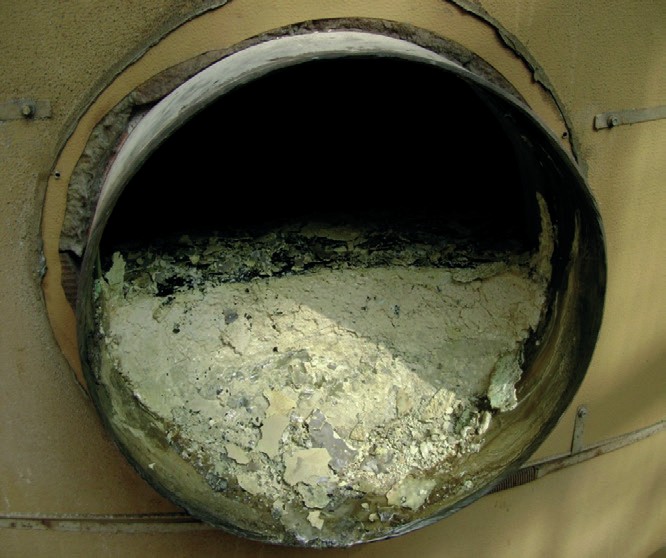
31 January 2023
Do you have a plan for a weak acid incident?
HYDROGEN SAFETY
Do you have a plan for a weak acid incident?
The world has seen a number of hydrogen explosions in double absorption plants mostly in the intermediate absorption tower (IAT). To review this increase and to determine the causes, an International Hydrogen Safety Workgroup was formed including major acid plant contractors, major acid producers, and consultants in the sulphuric acid arena. Workgroup member Rick Davis of Davis & Associates Consulting explores some of the findings.
I have been involved in the sulphuric acid industry for over 40 years and I have found the process secret. The secret is that without water the production of sulphuric acid is impossible. This is the primary reason that the process gas is dried to a very low water dewpoint using 93-98% sulphuric acid in the drying tower. This allows the use of carbon steel for most of the plant equipment. Over the years, the increase in sulphur dioxide (SO2 ) feed gas concentrations have been increasing the use of stainless steel in process equipment such as the converter. This change is not based on any corrosion consideration. Stainless steel is stronger than carbon steel at high temperatures and produces less high temperature oxidation.
How hydrogen can be generated
The workgroup has determined that the major factors causing hydrogen explosions are:
- weak acid incidents;
- failure of timely detection of weak acid conditions;
- failure to react.
There is no mystery of how sulphuric acid can generate hydrogen. I remember in chemistry lab in high school my teacher mixed hydrochloric acid and some zinc and collected the off-gas in a glass bottle and then covered the bottle lid and lit the gas with a small piece of burning wood. When the stick was introduced into the covered bottle it went poof and pop when the hydrogen ignited. The chemical reaction is:

This is the same reaction for Fe, Ni and many other similar elements, but with H2 SO4 the reaction is:

Normally, the acid concentration and temperature range routinely handled in acid plants are:
- 93% H2 SO4 , <150°F (66°C)
- 97-99% H2 SO4 , 110-240°F (43-116°C)
- 99-99.5% H2 SO4 , max. 397°F (203°C) Acid below the above range will be considered as weak acid.
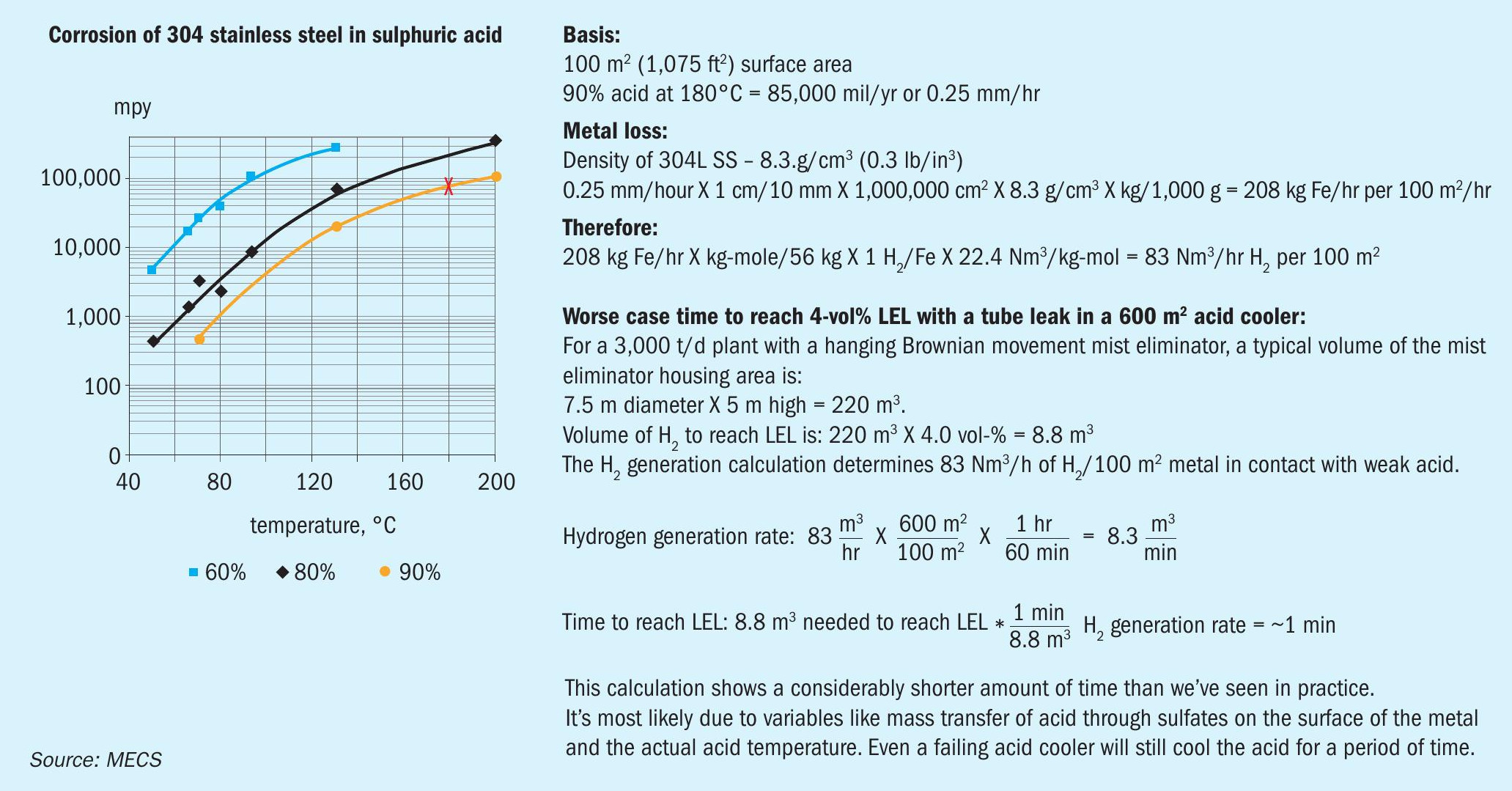
To illustrate how the corrosion of 304 stainless steel is affected by temperature and concentration, remember when water is added to concentrated acid, heat is generated. So, if you start with 93% H2 SO4 at 110°F, which is within the normal range and dilute to 90%, the temperature will increase to over 150°F. With only a 3% drop of concentration there will be an increase in corrosion and hydrogen generation.
In the scenario shown in Fig. 1, a committee member estimated how much time it takes for a weak acid excursion to lead to a hydrogen incident in a 3,000 t/d plant. The square footage of metal in contact with weak acid and time will affect the overall quantity of hydrogen generation. While this scenario most likely would not exactly match your plant configuration, it provides a scalable benchmark that illustrates the time range for hydrogen generation. Each plant must review their situation to determine standard operating procedures (SOPs) to address the actions required to mitigate the situation.
This establishes one rate of generation of hydrogen. The rate can be greater or less dependent on the actual conditions. The workgroup has reviewed incidents where the acid concentration dropped to as low as 80 wt-% H2 SO4 . In these situations the corrosion rate was greater, therefore, the hydrogen generation rate is greater.
Hydrogen will migrate to the highest point possible. Most of the incidents brought to the workgroup have occurred in the mist eliminator volume region in the interpass tower, but incidents have also occurred in drying towers and in the converter stage connected to the interpass tower.
The development of hydrogen gas is time dependent, therefore, your plant operations response should be timely. The operators must be trained with SOPs and reinforced through continuing education.
A weak acid incident can originate from the following water sources:
- High pressure steam generation components like:
– waste heat boiler (furnace and converter boilers)
– steam superheaters
– economisers
– unintentional water addition due to leaking dilution water valves during a shutdown
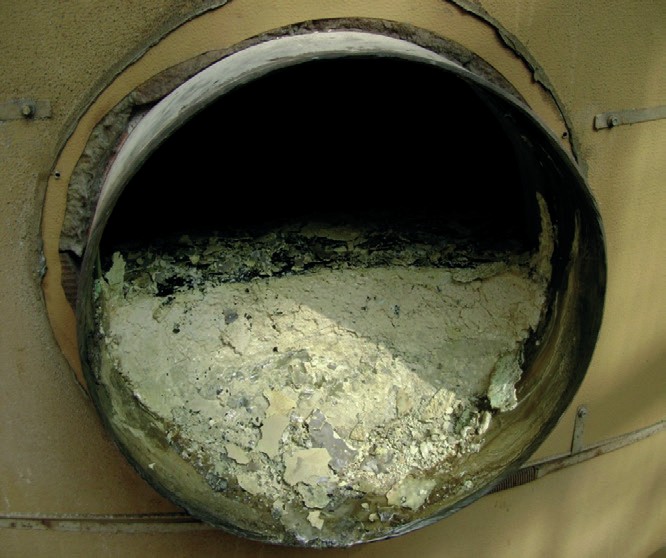
- Acid cooler issues including:
– tube leaks
– maintenance procedures
– operating procedures
Weak acid incidents detection
Steam leaks
Routine acid condensate observations from the economisers should be conducted. Routine should mean at least once per shift. Many plants with previous steam equipment leaks should consider increased frequency or additional instrumentation due to the reduced mechanical integrity of the equipment due to previous water leaks. Opening a drain valve on an economiser should produce dry white smoke. Typically, there may be a few drops of condensate. These observations should be documented and used as a point of reference for future observations.
If there is no white smoke that normally means the plant is not routinely monitoring the economiser for condensate. Sulphates and scale can gather on the economiser floor. These deposits can plug and restrict the drain nozzle as shown in Fig. 2. No smoke means the line is plugged.
Some economisers are designed with a centre point drain with a line extending to the outside perimeter of the economiser to allow access to the valve for observation and draining. Many economisers have a sidewall drain located close to the economiser floor with a short connecting nozzle.
I have seen that some plants have installed a condensate collection pot with instrumentation to detect the accumulation of condensate. These collection pots should not eliminate the need for routine drain observations plus early detection between observations.
One of the many issues the Hydrogen Workgroup reviewed was the detection of the acid dewpoint entering the intermediate absorption tower. Acid dewpoint analysers have been marketed for years to monitor the acid dewpoint for fuel fired steam boilers. The analytic equipment can provide continuous reading of the dewpoint. The application of an acid dewpoint analyser on a fuel-fired steam boiler is far different than the outlet of the economiser before an intermediate absorption tower. Two investigations into the technology for continuous monitoring of the dewpoint showed that this is not feasible. It was found to be maintenance intensive, but there is an answer.
Acid dewpoint analysers can be effective to detect sudden changes in the acid dewpoint of the process gas, but not relied on for an absolute indication of acid dewpoint. Most HP steam leaks will cause a sudden change to the acid dew-point. Leaks in superheaters may lead to an increase of acid dewpoint but may not be a sudden change. The observations at the economiser will show change. Usually, more condensate is observed.
The early detection of the weak acid incidents in steam systems in your plant should be developed into your plant standard operational procedures (SOPs) based on your plant specific configuration.
Acid coolers
Cooling water is responsible for the majority of acid cooler leaks. When stainless steel acid coolers were first introduced to the sulphuric acid industry back in in the early 1970s it was realised that controlling the cooling water quality and the tube wall metal temperature are critical for the control of corrosion. When Chemetics first marketed anodically protected coolers, they insisted that the cooling water flow must be maintained at the designed flow rate and acid temperature to the acid tower would be controlled bypassing hot acid around the cooler. There was no means or way to throttle cooling water which meant water-side fouling was minimised. Maintaining the acid pressure greater than the cooling water pressure allows for quick detection of tube leaks by monitoring the pH of the cooling water. A small acid leak will change the pH of the cooling water. There should be one pH and a conductivity probe in the outlet cooling water line of each cooler to allow for quick detection of an acid leak. Maintenance of pH probes unfortunately has not received the required priority to maintain an accurate indication in many plants.
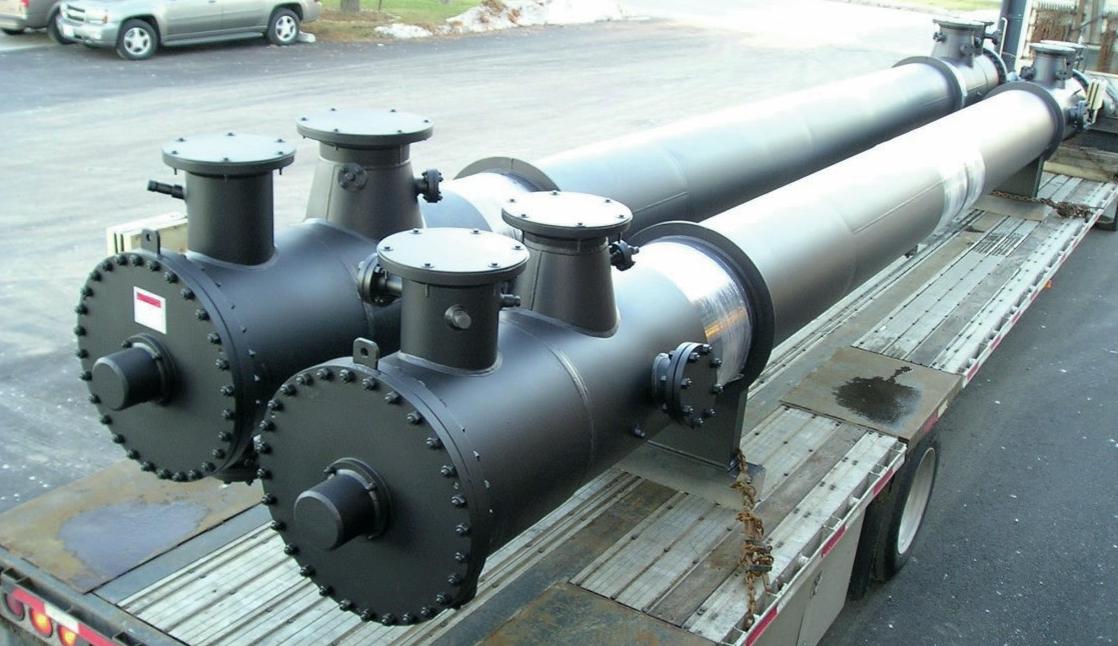
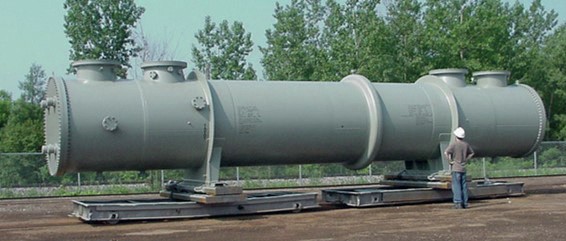
Reaction to weak acid conditions
The workgroup suggests that the plant response should be:
- timely;
- included in plant specific SOPs;
- weak acid SOPs should be written, and the operating staff should be trained and tested.
The key issues that should be included in the reaction plan are:
- maintain air flow by slow rolling the compressor to prevent the accumulation of hydrogen;
- stop the source of water;
- removal of the weak acid.
Steam system incidents
Waste heat boilers
The major cause is tube to tubesheet leaks. It has been determined that poor quality tube rolling and welding at this critical weld has been the cause of many leaks.
Economisers
The design purpose of the economiser is to reduce the sensible heat of the process gas entering the acid system to recover the energy into the steam system versus the cooling water. This requires the cooling of the process gas close to the acid dew-point. When the actual plant conditions are not as designed, condensation of acid will occur in the economiser. After several drifts away from design conditions, it can lead to tube leaks causing corrosion.
Acid coolers
The majority of hydrogen incidents reported to the workgroup were caused by tube leaks, but there has been an incident involving acid cooler washing procedures and an incident that occurred while the plant was shut down.
Reaction plan
The reaction plan should consider addressing the above issues and plant specific issues.
Steam system
Waster heat boilers
A leak in a waste heat boiler will require a plant shutdown to access. Do not shut down the blower. This will prevent the accumulation of hydrogen and that can lead to explosions. The air flow can be reduced, but not stopped.
Economisers
When a leak in an economiser is quickly detected the plant may not require a complete plant cool down. One issue the workgroup found is that many plants cannot by-pass boiler feedwater around the leaking economiser to continue to provide feed-water to a boiler exposed to the heat of a sulphur furnace. Can your plant isolate the water side of the economiser?
Waste heat boiler
Maintain air flow for plant cool down. Can air flow be maintained with steam production shutdown due to the leak?
How will the energy input to the blower be maintained? With a steam driven blower, can alternative steam production be provided in a timely manner?
Acid coolers
Early detection is required, but when detected the reaction plan should include the isolation of the water source cooling water and the removal of weak acid from the cooler. These reactions will reduce the generation of hydrogen. How will your plant do it?
Acid coolers have got larger with increasing plant capacities. The photos in Fig. 3 show how acid coolers are being designed with increased plant capacities.
The requirement to isolate the source of water and the removal of weak acid to reduce the generation of Hydrogen is very plant specific.
Some issues of your weak acid incident may include:
- Can your plant isolate each of the acid coolers from the cooling water system?
- Acid coolers are significantly larger than the original design. Can your plant drain the acid cooler in a timely matter? Are the drains and vent nozzles large enough? Do you have a location to contain the volume of acid and water?
- Are the drain valves covered with a blank flange (which take time to remove)?
Summary
Weak acid will generate hydrogen and if hydrogen accumulates, an explosive range can be reached quickly. Timely detection of a weak acid incident is essential.
Ensure that your plant has procedures (a plan) to respond to weak acid conditions as failure to plan often results in plan to fail.
Many isolation valves may not have been moved for several months or even years. Some isolation valves are not quickly accessible leading to a delay of the isolation of the water and acid system. This issue is plant specific and should be a part of the development of your SOPs review.
The International Hydrogen Safety Workgroup has written over nine articles and have made several presentations at Sulphur conferences, Sulphuric Acid Today Workshops, and at the Central Florida AIChE Clearwater conferences. If your plant has not started to plan for a weak acid incident you can find the past publications on Sulphuric Today website: www.h2so4today.com/hydrogen-safety.
If you have questions concerning hydrogen safety please contact the workgroup. My e-mail is rick@consultdac.com.