Sulphur 404 Jan-Feb 2023
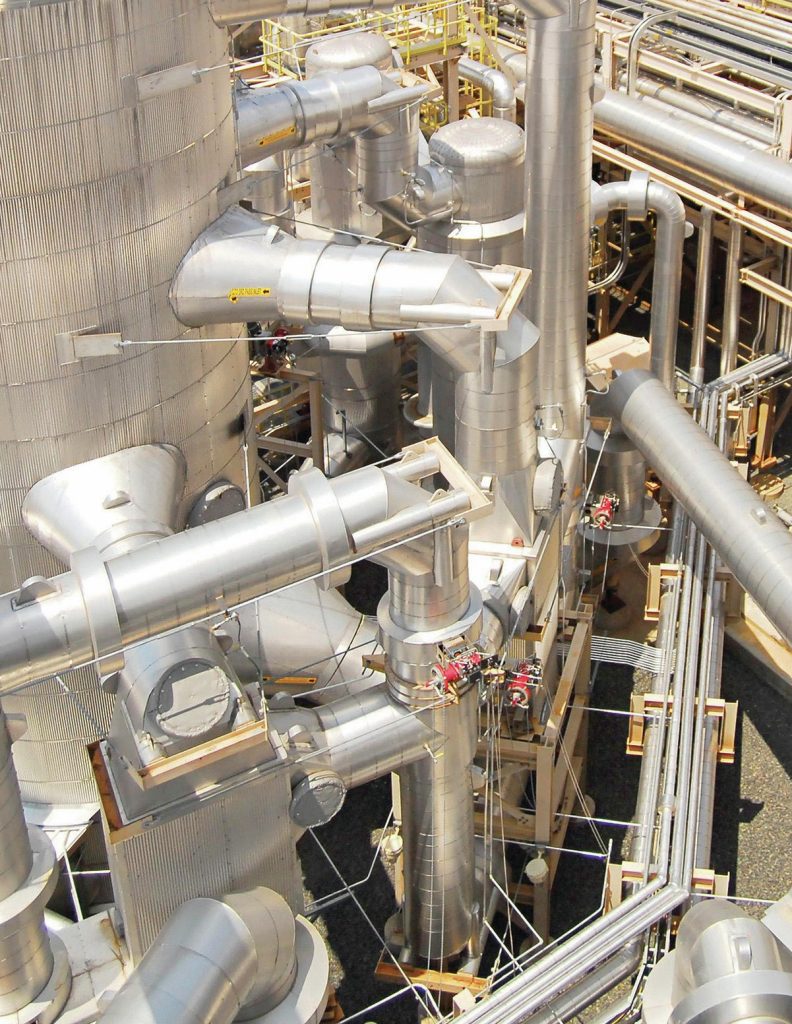
31 January 2023
Hydrogen safety in sulphuric acid plants
PLANT SAFETY
Hydrogen safety in sulphuric acid plants
Safety in sulphuric acid plants is a well-known and widely discussed topic. Industry turnover is a reality, and keeping new employees informed of hydrogen safety procedures is key to keeping plants fully operational and incident free. Walter Weiss of Elessent Clean Technologies discusses the steps facilities need to take to prevent hydrogen incidents.
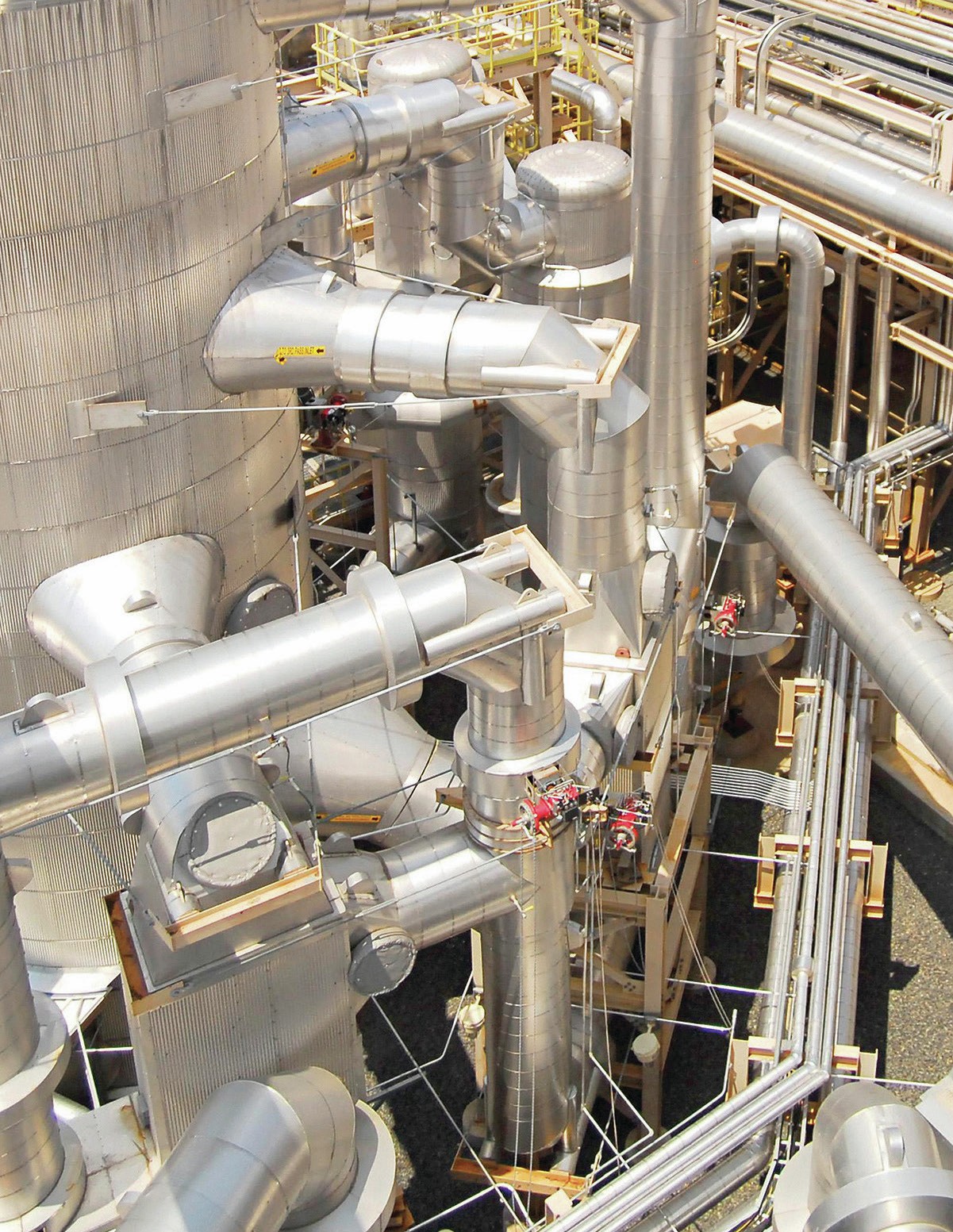
Hydrogen is a chemical element that is a gas at normal temperature and pressure. It is the lightest of all elements on the periodic table and is highly combustible. On Earth, hydrogen occurs naturally in compound form with other elements. For it to stand alone, it must be produced in different ways. In a sulphuric acid plant, hydrogen can be formed through an electrochemical reaction in which there is an exchange of electrons. The following electrochemical reaction is responsible for hydrogen formation:

In this formation specifically, the iron loses two electrons after coming in contact with sulphuric acid. This electrochemical reaction can partially be described by its two half-cell reactions involving the electron transfer as follows:
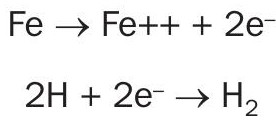
When iron loses its electrons, also known as its oxidation reaction, it occurs at the anode or metal surface where the acid contacts iron, nickel or chromium equipment. The hydrogen reduction reaction occurs at the cathode. In a sulphuric acid plant, the cathode is in the bulk solution. Electrons are able to move more freely in the bulk solution because of its conductivity, so the transfer of electrons occurs more easily. Acid with weaker strength has higher conductivity, and the higher the acid conductivity, the more rapidly the reaction can take place. Fig. 1 shows the classical electrochemical cell in simple form.
In sulphuric acid plants, the strong acid system is made up of a variety of steels, which are made primarily of iron. A plant’s design and operation govern the acid condensation from the gas phase and maintenance of the right acid concentration in the liquid phase within the sulphuric acid plant environment. Corrosion is minimised if this is done properly, and corrosion is the culprit in hydrogen evolution which left unattended can result in reduced plant safety. That said, there are always certain baseline levels of corrosion and hydrogen evolution that occur on a continuous basis. But with stringent concentration control, this level of hydrogen generation in comparison to the gas flowrate is insignificant and almost undetectable. Generally speaking, the majority of plant operators are not aware of its presence.

The impact of process technology changes
Since the 1970s, advances in process technology have been made to address evolving EPA requirements. Some of these changes are directly related to the surface area of steel within an acid plant. Over the last several decades, the relative surface area of steel within an acid plant has increased. The introduction of new flow schemes and new equipment design has led to the creation of high points where hydrogen can collect if not continuously removed. While these industry changes have made significant improvements to acid plant operations, they have also generated a new set of risk concerns and requirements which require operator attention.
As previously noted, corrosion from condensation in sulphuric acid plants leads to the generation of hydrogen. When metal surfaces come into contact with weak acid, it can increase the corrosion rate of the metals by several orders of magnitude, and as corrosion rates rise, the risk of hydrogen generation becomes greater. Over time, increased rates of hydrogen can lead to gas bubbles forming in the acid. When the hydrogen gas bubbles move through the acid, it disturbs the passive oxide or sulphate film that builds up on surfaces containing sulphuric acid which further accelerates corrosion rates within the plant.
Limiting corrosion
Within the plant environment, there are acceptable rates of corrosion that occur within relatively small concentration ranges and temperature changes. However, it is important to implement procedures to ensure that rates of corrosion do not rise. Equipment and piping must be kept within their prescribed operating window to keep corrosion rates low. Proper monitoring and attention to instrumentation maintenance is paramount for leak detection around equipment, like acid coolers that have water and acid on opposing sides of metal tubes, vulnerable to corrosion. Responding to acid leaks as quickly as possible is essential in minimising equipment damage and hydrogen generation. Not only will the water rapidly dilute acid outside the desired concentration range for the acid cooler materials, but additional heat will also be generated. Because acid dilution produces heat and corrosion rates increase with rises in acid temperature, corrosion rates intensify drastically in the event of an acid cooler leak.
Similarly, the loss of acid system concentration control caused by a control loop failure or an upstream steam system leak, can cause corrosion rates to intensify. Here again, the best course of action includes quick detection and then rapid separation of the water source from the acid and swift de-inventory of acid plant equipment. Corrosion rates should subside, and hydrogen generation should return to more acceptable levels immediately upon removal of the weaker acid from the system, and the system is re-inventoried with circulating strong acid.
Noting that the above describes acid plant incidents which likely entail full attention from the plant operators – draining, isolating, purging, cooling, etc. – attention to simultaneous generation of hydrogen can be readily overlooked without proper training and drills for these operators.
Preventing hydrogen ignition
The elements needed for a fire, which happen to be the same as those needed for an explosion, are a fuel, an oxidant and an ignition source. The difference between a fire and an explosion lies in where these elements meet. An explosion occurs when the fuel and oxidant are mixed in a confined space.
Hydrogen is a very effective fuel, and it is extremely buoyant and diffusive. In order for it to ignite at its lower explosive limit (LEL), the energy required is very low, nearly undetectable. Under normal circumstances, in a plant with adequate air circulation, hydrogen will flow normally through the plant with the bulk gas and be carried out the stack in low concentrations. However, in a stagnant plant, or plant with little air flow, it is possible for hydrogen to accumulate in high points like the tops of acid towers. Because hydrogen is diffusive, it mixes well with process gases which contain oxygen. Normal process gases like NO2 , NO and SO2 can take part in the reaction resulting in a reduction in the LEL and increase in the energy release. Once hydrogen builds up to a value exceeding its lower explosive limit of 4% (or less), an ignition source will start a fire. As already mentioned, an ignition source will cause an explosion if these elements are located within a confined space, and there are many confined spaces within an acid plant. Also worth noting, the ignition source required for initiating hydrogen combustion in air is infinitesimally small – such as static charges associated with droplets.
Continued operation of the main compressor in the acid plant while the operators respond to the incident will help reduce hydrogen concentrations by maintaining proper air flow. This will also help minimise the confined space risk factor. That said, if the main compressor is shut down, either by intent or by interlock, the risk of fire and explosion increases significantly. Thus, a key to maintaining hydrogen safety measures includes maintaining air flow to purge the plant.
Over the last decade or so, there have been an average of one or two hydrogen explosion incidents per year, occurring almost entirely when the plant has been shut down. The energy release at the LEL concentration is significant enough to cause damage to important plant equipment which can cause extensive down time and severe repair costs.
When planning for a shutdown, purging the plant to flush out the hydrogen should be at the top of the to-do list. Other preventative measures include installing high point vents in accessible locations and opening those vents after purging the plant to aid in the release of hydrogen that continues to form. Using automated valves is also recommended to speed response time and to distance workers opening valves from the explosion potential. Additionally, isolating equipment, draining acid and water from equipment and rapidly reacting to concentration or temperature upsets can help minimise hydrogen generation. Some final measures to help reduce the occurrence of a hydrogen incident include ensuring effective concentration controls, dilution water interlocks and process alarms.
Conclusion
While plants are designed to minimise all potential risks related to hydrogen, accidents still happen. It is imperative that facilities take steps to proactively prevent hydrogen incidents, such as:
- drilling emergency procedures;
- conducting operator training focused on hydrogen awareness;
- reconsidering the presence of hydrogen for general work or hot work permitting; l implementing a mechanical integrity programme;
- conducting routine turnaround inspections and equipment repairs;
- replacing equipment prior to a failure;
- carefully monitoring process conditions.
Maintaining sulphuric acid plants by safely starting up, operating and shutting down are key to minimising the presence of hydrogen, thus minimising the risk of a hydrogen incident.