Sulphur 404 Jan-Feb 2023

31 January 2023
Sulphur recovery in the energy transition
ADVANCED SULPHUR RECOVERY TECHNOLOGY
Sulphur recovery in the energy transition
In the current energy transition era, the oil and gas industry is focusing on lowering its carbon footprint while generating green energy resources such as blue hydrogen. In this article, Thomas K. Chow, Marcus Weber and Denny Li of Fluor Solutions/Goar, Allison & Associates, L.L.C. demonstrate how SRU/TGTU plants within sour gas facilities can facilitate the capture of CO 2 and generate H 2 by implementing advanced sulphur recovery technologies.
In an effort to suppress current dramatic global weather changes, scientists and policymakers around the globe are advocating and striving to minimise the use of fossil fuels and maximise the use of “green” energy resources. The oil and gas industry is also doing its part in focusing on lowering its carbon intensity footprint while also investigating the use of alternative green energy resources such as hydrogen. Undoubtedly both carbon capture and hydrogen generation processes that are commonly pursued are capex and opex intensive; however, there is an opportunity to accomplish some of these tasks cost effectively via advanced sulphur recovery technology and processes.
Sulphur recovery units associated with sour natural gas facilities must contend with unique operational challenges associated with the acid gas feed produced from a sour gas facility. Compared to typical refinery acid gas, the acid gas produced from a sour gas plant is typically leaner in H2S with higher concentrations of CO2 ; various hydrocarbons; and benzene, toluene, ethylbenzene, and xylene (BTEX). Higher reaction furnace temperatures are necessary to totally destruct the BTEX and hydrocarbons; however, the lower H2S concentration in the acid gas makes it difficult to achieve the desired flame temperature without co-firing with fuel gas or utilising oxygen-enriched air.
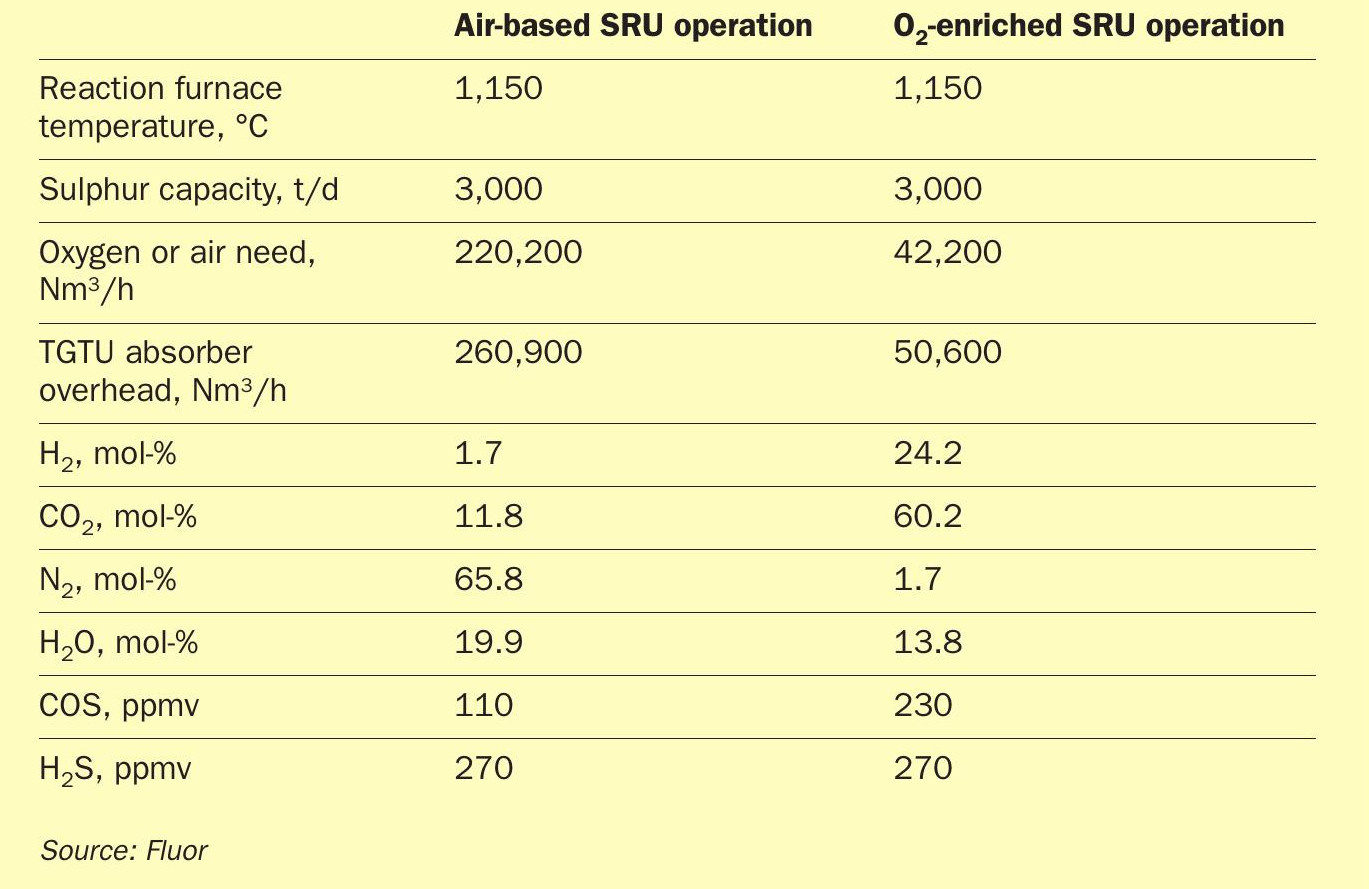
The use of high-level oxygen enrichment in the SRU presents an opportunity in terms of CO2 capture and H2 production in any facility but is especially well suited for SRU/TGTUs in sour gas plants for the following reasons:
- There is already a relatively high concentration of CO2 in the feed that will pass through to the Claus tail gas.
- Any hydrocarbons in the acid gas feed are converted into CO2.
- Oxygen-enrichment elevates the amount of H2 produced in the reaction furnace from side reactions and eliminates additional presence of undesired nitrogen.
As shown in Table 1, the tail gas treatment unit (TGTU) absorber overhead stream of an SRU converted from air-based operations to high-level oxygen is heavily concentrated with CO2 and H2 and minimum nitrogen.
In this article, Fluor discusses the results of case studies investigating how a high-level, oxygen-enriched SRU within sour gas facilities can be optimised to facilitate an owner’s CO2 capture goals and H2 generation potential.
Oxygen enrichment and COPE II process
Oxygen enrichment is the utilisation of a purer source of oxygen molecules that replace all or a portion of the nitrogen molecules within the combustion air in the reaction furnace and thus reduce the volumetric gas flow in downstream SRU/ TGTU equipment. As a consequence, the design processing capacity of an existing SRU/TGTU is increased proportionally or sizes for equipment of a new SRU/TGTU can be reduced compared to those of an air-based Claus operation. A dedicated oxygen production unit (OPU), like an oxygen VPSA, could be employed to deliver the oxygen source of typically 90-95% purity. Alternatively, oxygen from a cryogenic air separation unit (ASU) could be utilised if high capacity is needed at the facility. Currently over 400 operating Claus SRUs worldwide effectively utilise various levels of oxygen enrichment.
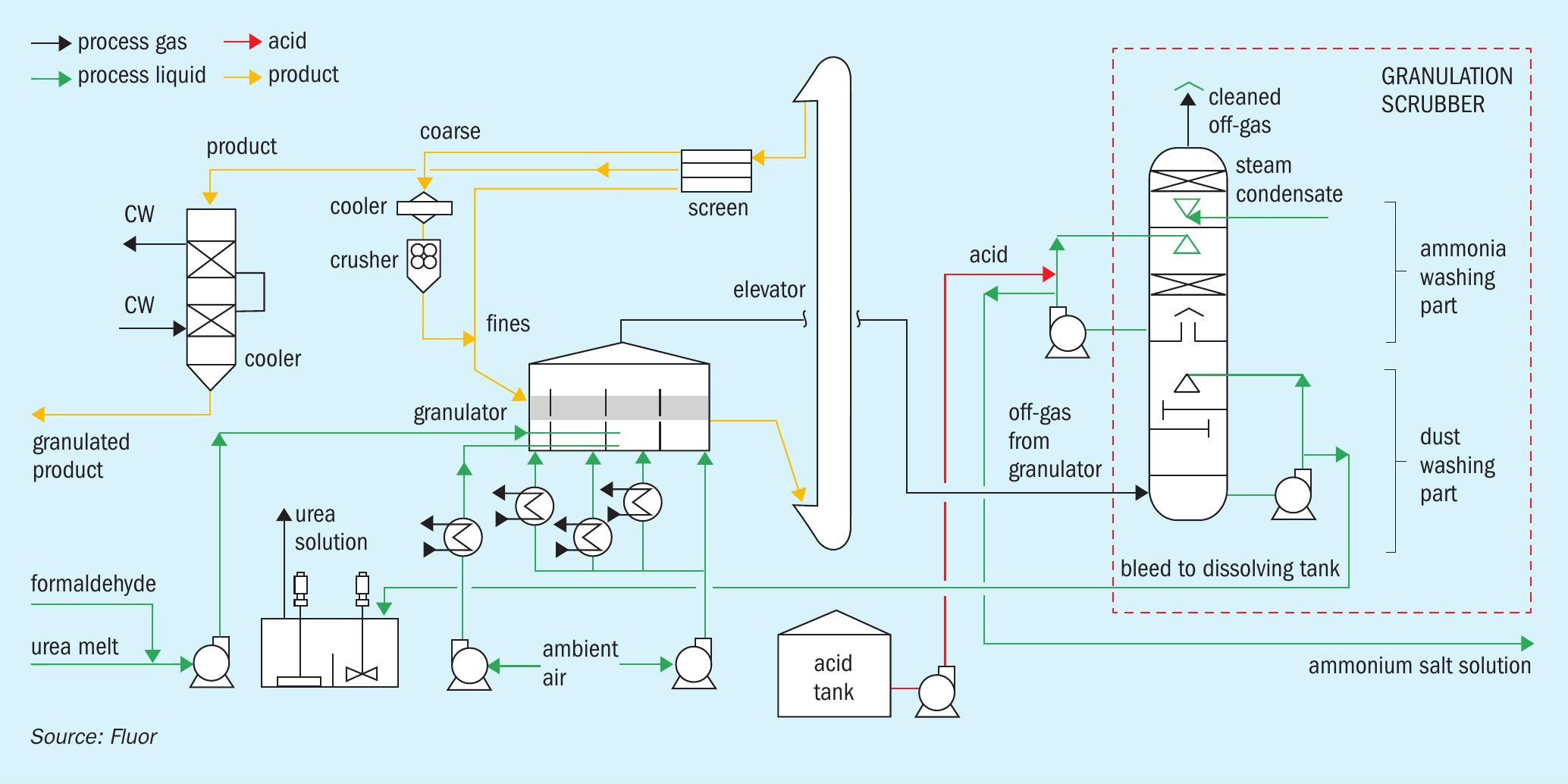
In existing SRU equipment, increases in the oxygen enrichment level correspond to higher capacity increases. Low-level enrichment in the 21-28% oxygen concentration range yields an increase of 25-30% of design capacity, medium-level (28-45% enrichment) yields increase of 50-70% of design capacity, and high-level enrichment (up to 100%) yields increase up to 150% of design capacity 1 . Oxygen enrichment levels can be manually adjusted by an operator to accommodate the processing capacity needs of the facility from original design capacity up to the desired revamped capacity.
With the lower diluent (nitrogen) content in the oxidant, the exothermic combustion reaction results in a higher temperature in the reaction furnace. One benefit of the higher furnace temperature is the assurance of the destruction of ammonia and BTEX which require minimum temperatures of 2,450°F (1,350°C) and 2,000°F (1,100°C) respectively 2 . Destruction of ammonia and BTEX is essential as these components can form ammonia salts and carbon deposition that causes plugging in piping and Claus catalyst deactivation. The primary concern with the increase in furnace temperature is that the operation could approach the design temperature limits of the refractory. Typically, existing equipment design limits will determine the allowable oxygen enrichment level.
Implementation of Fluor/GAA’s COPE™ II Technology allows for higher levels of oxygen enrichment to be utilised while remaining below refractory design temperature limits of the reaction furnace (thermal reactor) refractory. A portion of the SRU process gas from the outlet of the first sulphur condenser is recycled back to the reaction furnace burner by way of the COPE ™ II recycle ejector. The recycled process gas is mostly inert which helps to reduce the furnace temperature. The ejector is simple to operate with medium-pressure steam, adjustable for different oxygen enrichment levels, and has a small footprint compared to a blower or compressor (Fig. 1).
Fluor has developed a patented process that leverages the COPE ™ II Technology to produce high purity CO2 from the SRU, named the Oxygen Enhanced Claus CO2 Recovery Process (OEC2 RP). This process requires near 100% oxygen enrichment to ensure low nitrogen content in the Claus tail gas3 . The Claus tail gas would be treated in a hydrogenation-amine tail gas treating unit (TGTU) to remove the residual sulphur compounds.
The overhead from the amine absorber would comprise primarily CO2 , H2 , and water. Depending on project goals, the H2 could be recovered as by-product or oxidised to generate high-pressure steam and CO2 dehydrated to obtain a high purity CO2 product stream.
Case study objective
Fluor’s OEC2 RP implemented with COPE ™ II Technology was evaluated in a recent study for the Middle East region. The objective was to optimise hydrogen production and produce a high purity CO2 stream for sequestration from an SRU/TGTU in a large-scale sour gas facility. Optimisation studies were performed on the COPE recycle and the reaction furnace operating temperature.
Case study parameters
The basis for the case study is as follows:
- sulphur recovery unit capacity is 3,000 t/d of sulphur;
- two-stage Claus with a hydrogenation/ Flexsorb TGTU;
- amine acid gas feed:
– CO2 22.16 mol-%
– H 2 S 69.22 mol-%
– H2O 8.23 mol-%
– COS 0.0003 mol-%
– hydrocarbons 0.17 mol-%
– BTEX 0.16 mol-%
– mercaptans 0.06 mol-%
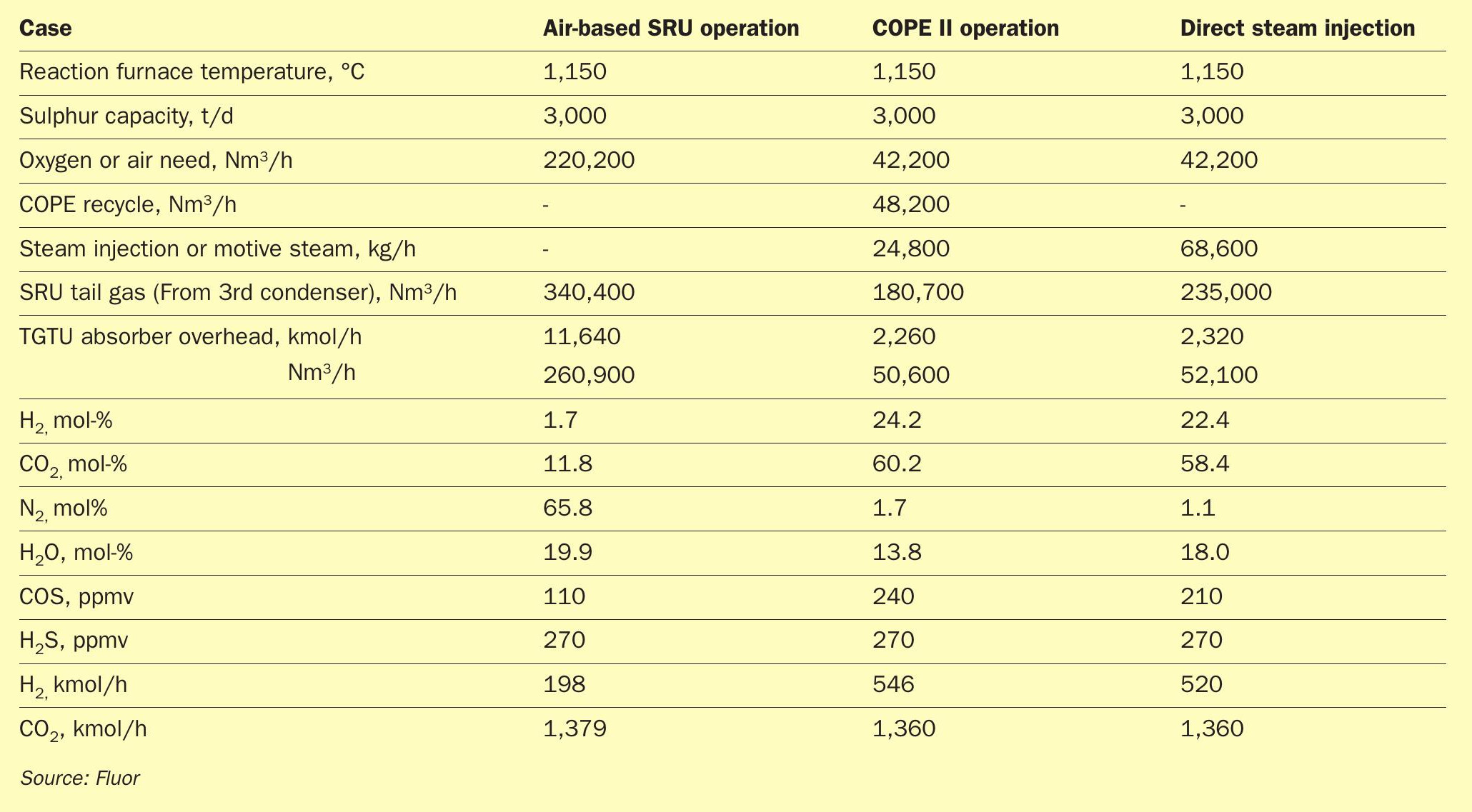
- oxygen purity of 98 vol-% utilised as the oxidant in the reaction furnace to minimise ingress of nitrogen diluent;
- TGTU Flexsorb performance targeted 270 ppmv H2S on the absorber outlet to meet the CO2 product specification.
Case study 1: Optimisation of recycle media for hydrogen production
A simulation case study was undertaken to ascertain the effect of the composition of the recycle gas on the amount of hydrogen produced. The COPE recycle is typically a mixture of steam from the ejector and various gases from the SRU/TGTU process of which CO2 is the primary component since N2 is minimised in this study case.
Hydrogen has been known as a valuable product, especially in this “green” energy era. An evaluation of H2 production in the reaction furnace was then performed. Since general observation indicates that steam not only lowers the reaction furnace flame temperature but also enhances production of H2 , an investigation was carried out by replacing the COPE recycle gas with a pure steam injection as the temperature moderating medium to the reaction furnace.
As shown in Table 2, the steam injection model showed a two-fold increase in the amount of steam injected into the reaction furnace compared to the steam required for the COPE II recycle ejector to maintain the same temperature in the reaction furnace. Additionally, unconverted steam in the process was carried downstream until being condensed in the TGTU direct contact condenser. This steam increases volumetric flowrate by 30% resulting in larger SRU and TGTU hydrogenation equipment. The large opex associated with the increased steam injection along with the larger equipment make the “steam-only” option uneconomical considering the COPE II benefits and slightly higher H2 production. However, this presents an option for manipulating the desired amount of H 2 production by increasing the amount of steam injection in an optimisation case if maximisation of H2 production is desired by a client. Such an option helps to eliminate the need for installing a capex intensive hydrogen production unit.
Case study 2: Reaction furnace operation for hydrogen production
A second case study was undertaken to evaluate the effect of the reaction furnace temperature on the amount of hydrogen produced in the SRU. While a minimum of 2,000°F (1,100°C) is required in the reaction furnace for BTEX destruction, a higher operating temperature can be achieved through reduction of the COPE recycle flow. A higher operating temperature has an effect on hydrogen formation. While the upper reaction furnace temperature limit in this evaluation is set at 2,650°F (1,455°C) to protect the reaction furnace refractory, the operating temperature in the reaction furnace without COPE recycle was slightly lower than this limit, at 1,425°C, due to the lean acid gas feed.
As shown in Table 3, the lower the reaction furnace temperature is brought down, the amount of H2 produced specifically in the reaction furnace rises. However, the lower reaction furnace operating temperatures benefit in H2 production is negated at the tail end of the sulphur plant as H2 and CO2 are brought to equilibrium in the hydrogenation bed.
Additionally, the higher operating temperature is not favourable in terms of the CO and COS formation in the reaction furnace. While the hydrogenation reactor can reduce the CO and COS because it promotes water-gas-shift and hydrolysis reactions, the residual amounts from the higher reaction furnace temperature cases still may exceed certain stringent tail gas specifications.
Ultimately, there is little benefit in controlling the reaction furnace temperature in regard to influencing the H2 production. The reaction furnace temperature should be set higher rather than lower to minimise the COPE II recycle requirement.
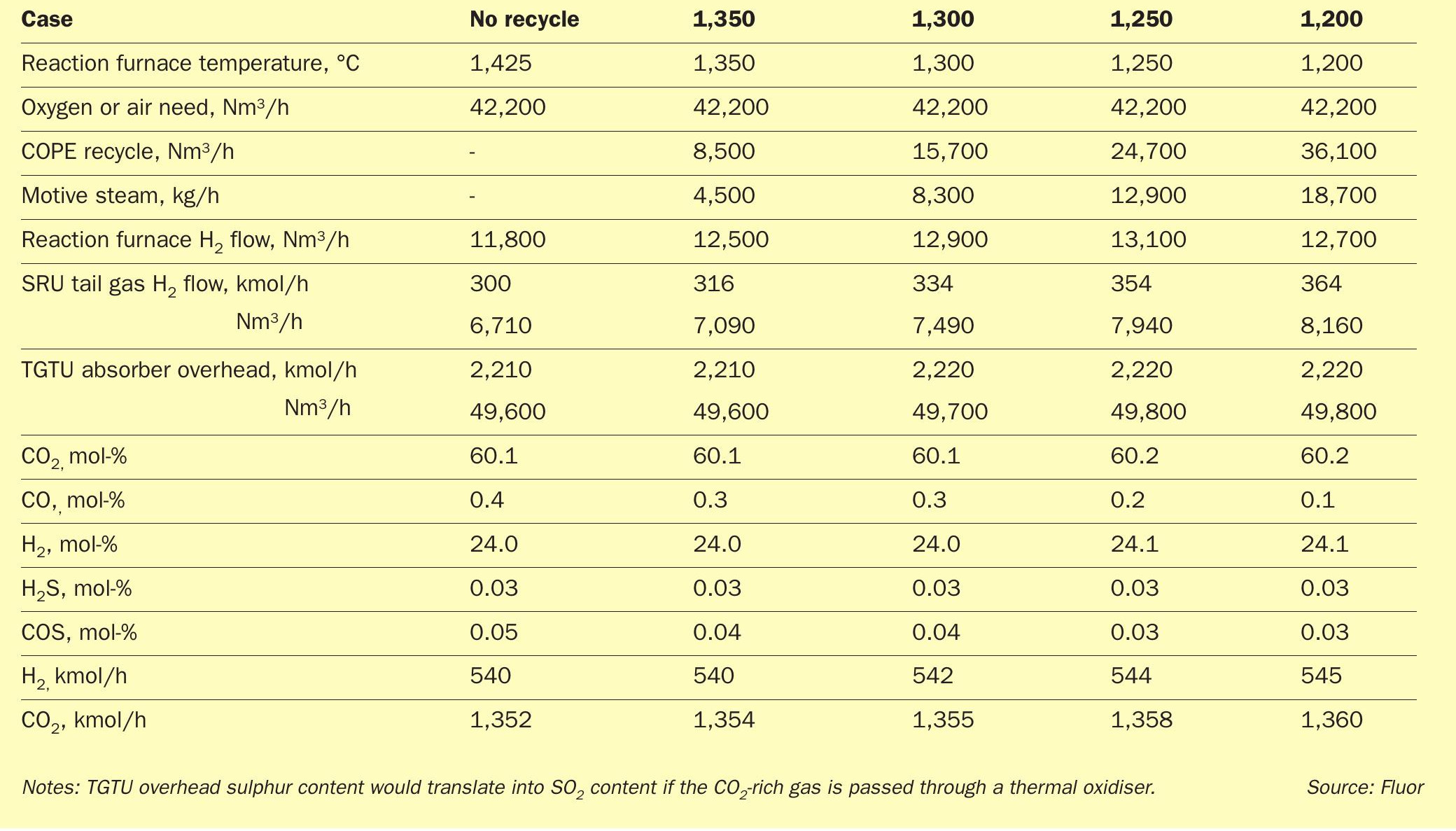
Economics
Fluor recently completed an evaluation comparing OEC2 RP with post-combustion CO2 capture of incinerator stack gas at a large Middle East sour gas plant. The evaluation indicated that the ROM capital cost (capex) of an amine-based CO2 capture system producing a similar CO2 stream to OEC2 RP was 75% more. While there was significant capex savings, the evaluation also showed that the OEC2 RP had a high operating cost (opex) primarily because the oxygen to the SRU was treated as an operating cost. If the oxygen is readily available, the economics would favour OEC2 RP much more. (Table 4)
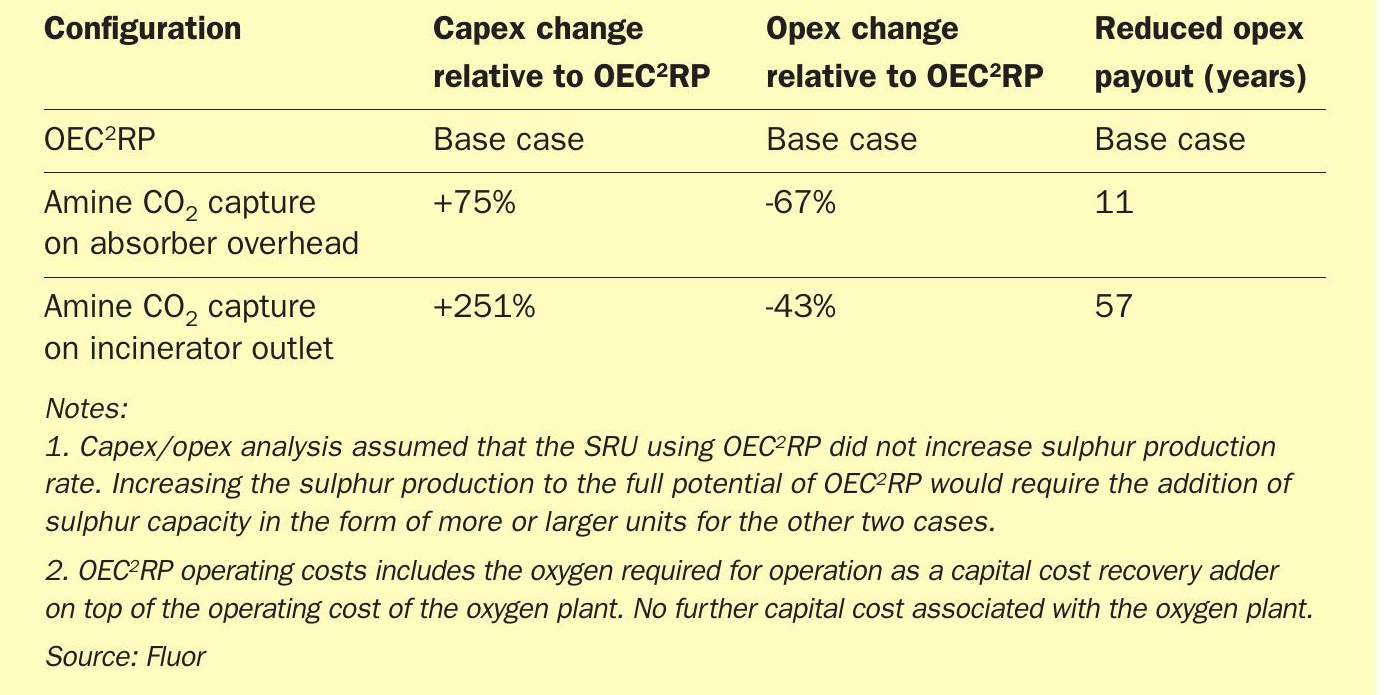
The evaluation showed the payback period for negating the capex savings provided by OEC2 RP against the higher operating cost for an amine-based CO2 capture was over ten years.
Conclusion
An ever-increasing percentage of the capital expenditures of many major corporations in oil and gas are planned around the “energy transition” of the world. Carbon capture and hydrogen are key cornerstones of that transition. Fluor has leveraged commercialised technologies in the form of OEC2 RP to facilitate the upgrading of a SRU into a platform for future H2 production and CO2 capture. With the patented OCE2 RP and the carbon capture technologies within its portfolio, Fluor can readily assist its clients with their plans to reduce their carbon footprint and realise the benefits of some “free” H2.
References