Fertilizer International 513 Mar-Apr 2023
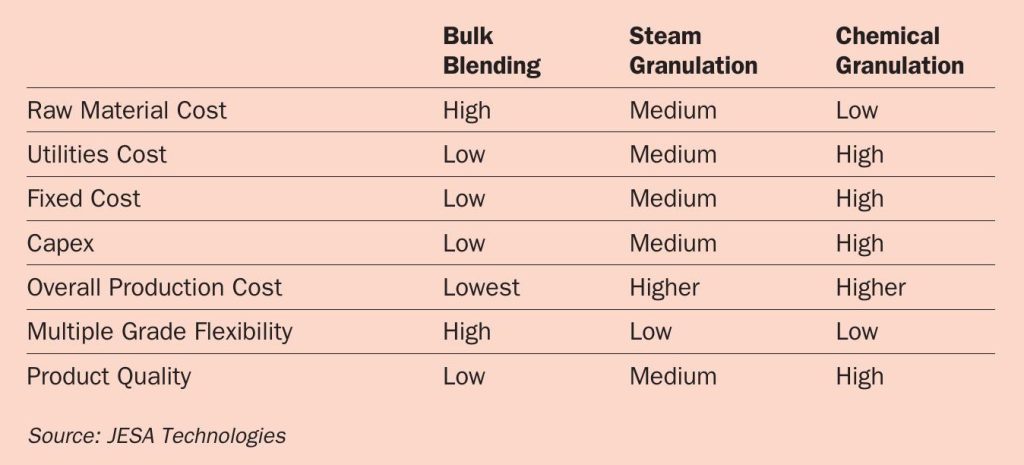
31 March 2023
Selecting the right NPK production option
PRODUCTION TECHNOLOGY
Selecting the right NPK production option
Blended and compound NPK fertilizers are a mainstay of many markets globally. We review the main production technology options.
JESA TECHNOLOGIES
NPK production: the fundamentals
NPK is a broad term covering a multitude of different nutrient formulations, each having their own process characteristics. Indeed, the term ‘NPK’ itself is a catch-all phrase given to any fertilizer that contains the primary plant nutrients nitrogen, phosphorus and potassium. Similarly, ‘NPS’ is a generic term for fertilizers that contain significant quantities of sulphur alongside nitrogen and phosphorus. They are also referred to as ammonium phosphate sulphate (APS) products.
NPK/NPS fertilizers can be produced from various raw materials via different manufacturing routes – to generate granular products containing N, P, K and S in a wide range of ratios. There are several production methods for NPKs, the main manufacturing routes being:
- Steam granulation
- Chemical granulation
- Bulk blending.
A summary of the main merits and demerits of the three NPK process routes is provided in Table 1.
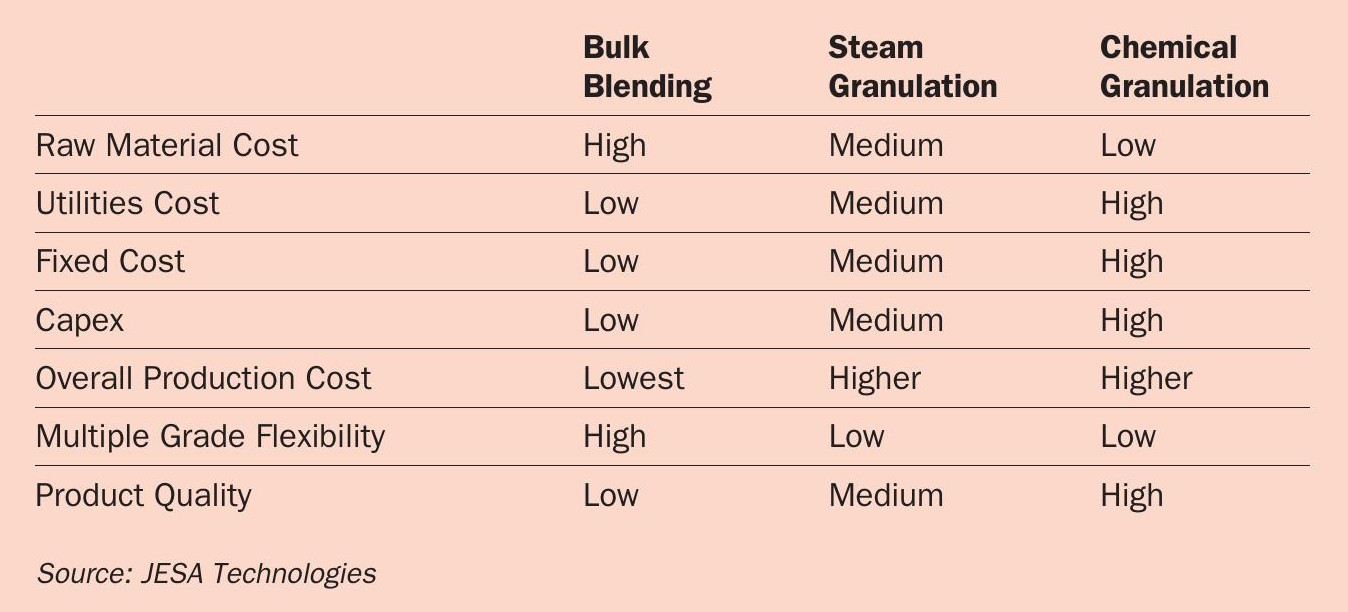
Steam granulation
In this granulation route, solid raw materials are mixed and granulated using steam and/or water. The process generates granular products through agglomeration. The addition of steam/water causes part of the solid raw materials to go into solution. This promotes the agglomeration of solids by forming crystal bridges that bind particles together.
In granulation, it is generally desirable to create end-products of between 2-4 mm in size. How efficiently these product-sized granules are formed determines the recycle ratio of the process – a ratio of 2/1 or less being usual. Product granules formed by steam granulation typically have the following characteristics:
- Fairly uniform chemical composition
- Low strength
- Poor shape
- Wider particle-size distribution.
In steam granulation, a relatively long dryer residence time is also required (typically 20 minutes). This is because, when they leave the granulator, most of the moisture is present within the interior of the granules and needs time to diffuse to the surface before it can evaporate.
Changing NPK grade at the end of a steam granulation production run can be time consuming – given that the entire plant is left full of fertilizer of the previous composition. ‘Change-over’ formulations are therefore used to speed up the switch in production from one grade to another. These exaggerate the normal feed rates required for the new grade during the changeover period. This technique can be applied when different grades of the same type of NP or NPK product are being produced. But if the production change is from an NPK product to an NP product then the only real choice is to empty the plant beforehand.
A typical steam granulation flowsheet is shown in Figure 1. This flowsheet can vary slightly, depending on the grades produced. The main variations include where to place the screening and crushing operations – either before or after the cooler – and whether to pass some of the process gases through baghouses rather than wet scrubbing.
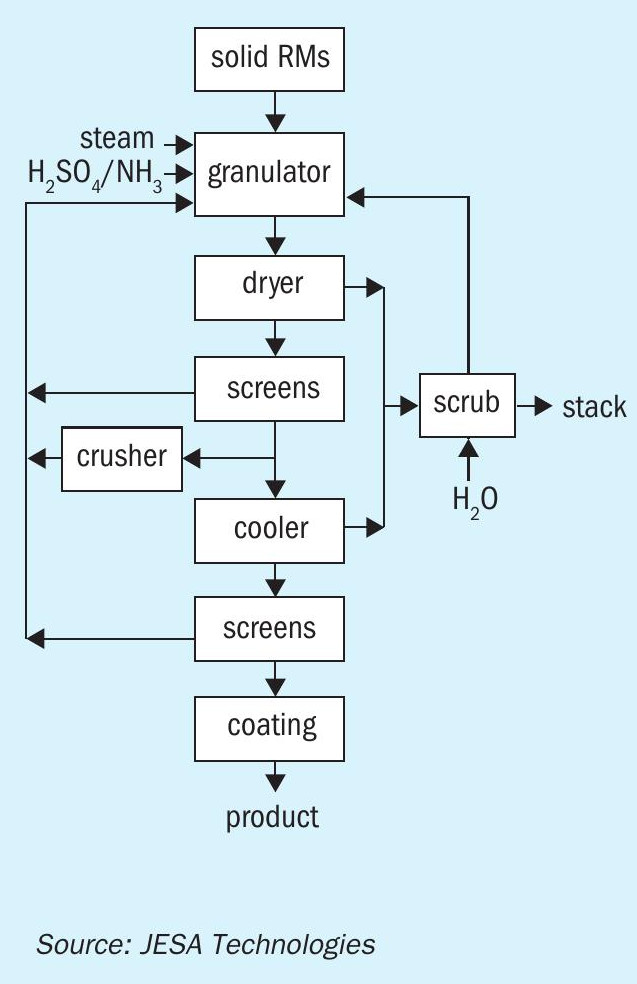
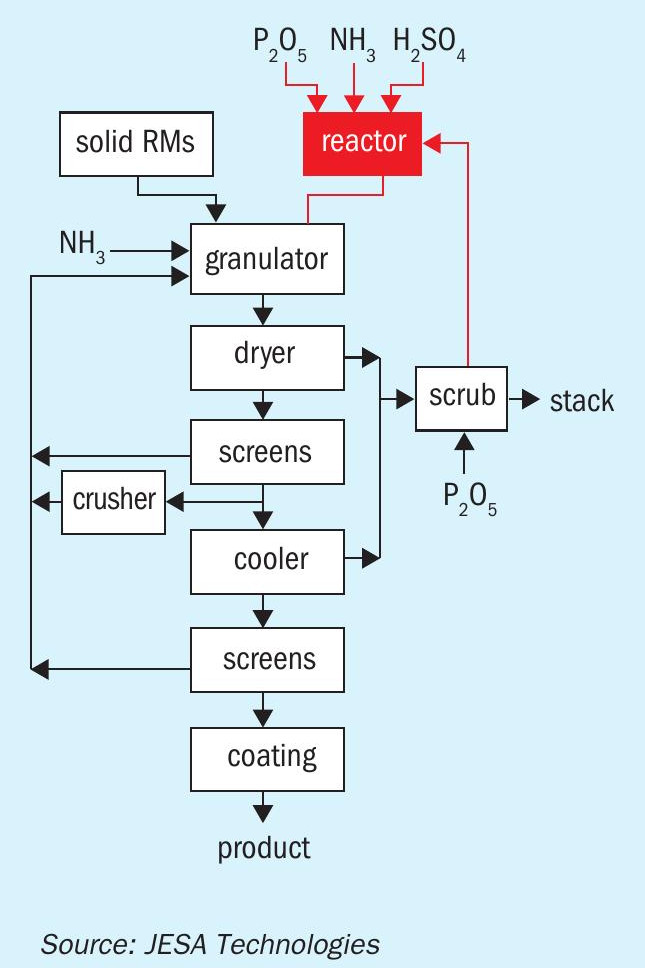
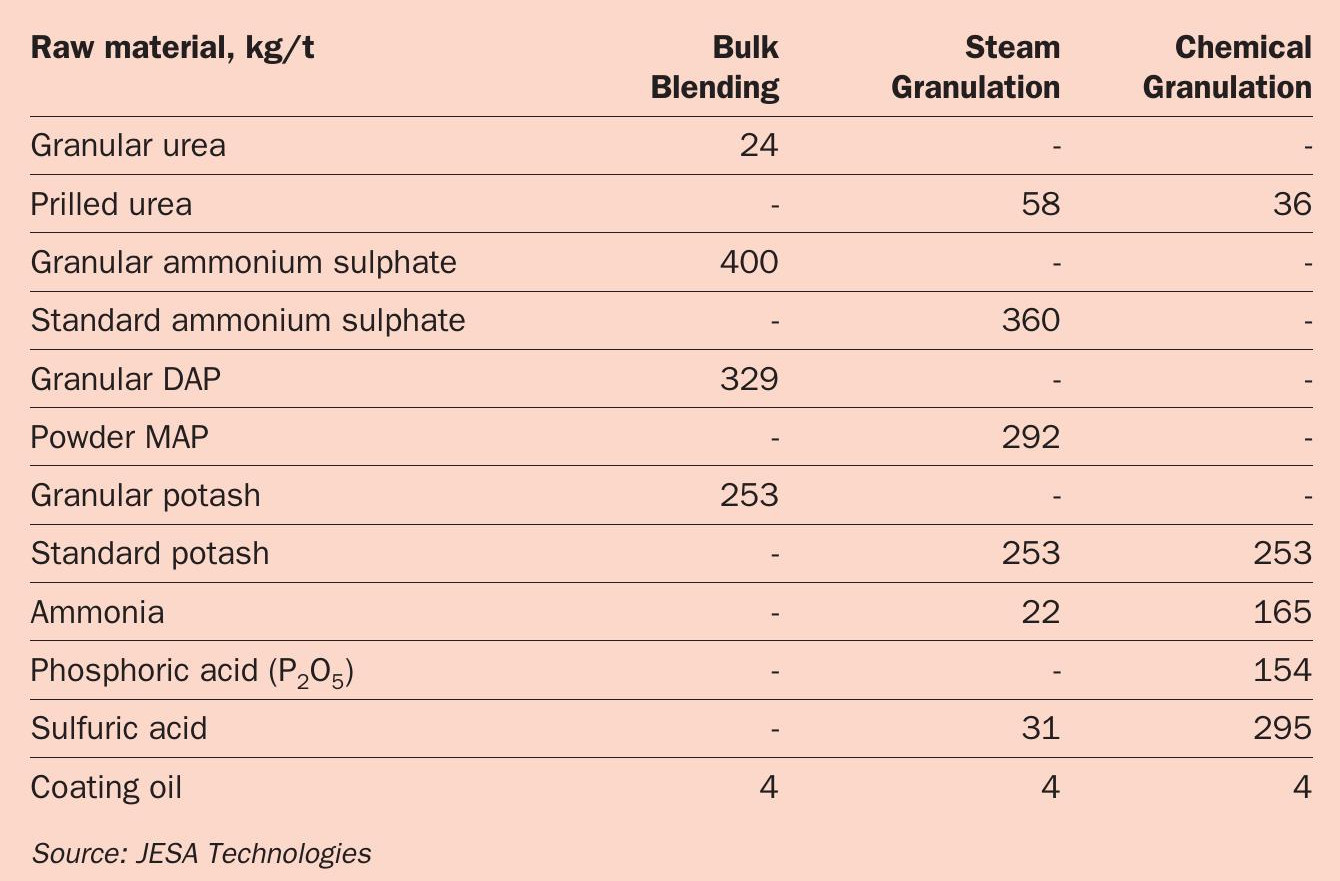
Chemical Granulation
The chemical granulation route manufactures granular products by reacting phosphoric acid and sulphuric acid with ammonia. This produces a slurry which is sprayed onto recycle material in the granulator. Solid raw materials – such as potash if NPKs are being produced – are also fed to the granulator along with the recycle. Granulation occurs partly through agglomeration but mainly by layering.
The recycle ratio in this process route is usually higher than in steam granulation – a typical value being 4/1 – and is determined by the granulator’s heat and water balance. Keeping to this higher ratio often requires the recycling of product-sized material to the granulator to maintain the correct heat and moisture conditions.
The resulting granules, as with steam granulation, are uniform in chemical composition. However – due to the layering mechanism and the higher recycle ratio – the granules formed are harder, more spherical and typically have a narrower particle-size distribution. The required dryer residence time is also shorter (typically 7–12 minutes depending on grade) as the moisture is mostly on the surface of the granules leaving the granulator.
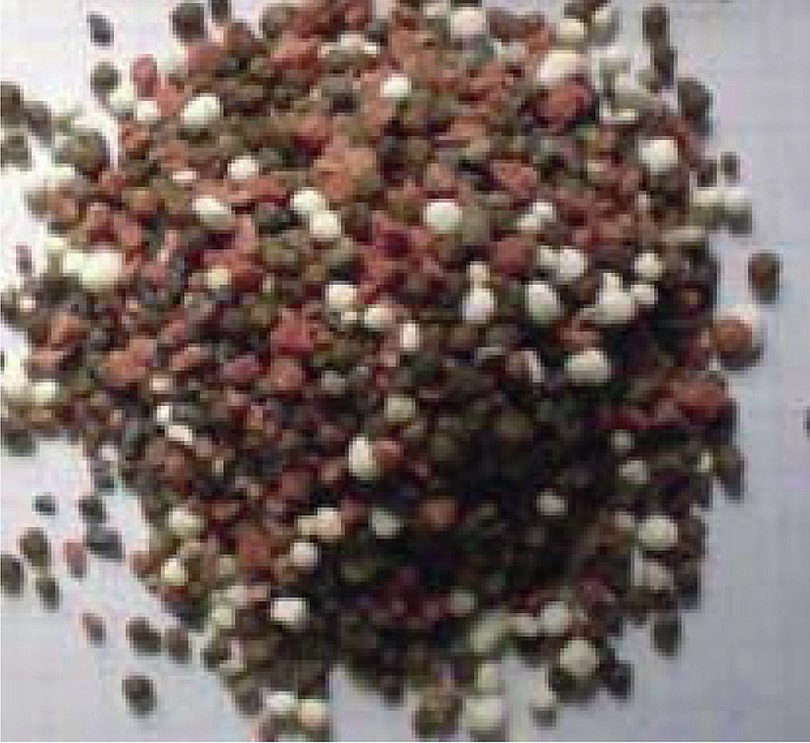
A typical chemical granulation flowsheet is shown in Figure 2. This is similar to the steam granulation flowsheet except for the added reaction stage and the use of phosphoric acid rather than water as the scrubbing medium.
Chemical granulation also faces exactly the same production challenges as steam granulation when changing between NPK and NP product grades.
Bulk blending
Bulk blending requires the mixing of dry, granular raw materials. This physical blending process is very simple and low-cost, in capex and opex terms, in comparison to the other two granulation routes.
The chemical composition of individual granules will vary according to the raw material type and their source. Granules present in bulk blends are also of different sizes, shapes and densities (see photo). Because of this, segregation can be an issue and result in the uneven field spreading of nutrients. The incorporation of micronutrients may also present a problem, although these can now be applied as a liquid coating on the surface of granules.
Raw material needs
Each NPK process route has different raw material requirements. Bulk blending, for example, requires the purchase of premium granular products. Steam granulation, in contrast, consumes predominantly non-granular solid raw materials. This route also often consumes by-products, off-specification materials, or even ‘spoiled’ substances available from nearby industries. Chemical granulation, meanwhile, uses the cheapest possible liquid chemicals as feed. These are typically generated on-site. This keeps costs low by avoiding the need to pay third parties to convert these liquid feeds into solid raw materials. The typical raw material requirements of the three different process routes in the production of 15-15-15 NPK are shown in Table 2.
Chemical granulation: product categories
Chemical granulation produces the best quality products out of all the three process routes and can manufacture these in a range of NPK and NPS grades. These include:
- Ammonium phosphate/potash mixtures
- High sulphate NP grades
- High sulphate NPK grades
- High urea content NP grades
- High urea content NPK grades.
The granulation of high and low mole ratio NPK and NP product types has been described in a previous article. (Fertilizer International 492, p57). Mole ratio measures the relative proportion of phosphoric acid and ammonia in the feed. This is an important parameter for adjusting and ‘fine tuning’ the granulation process to ensure it delivers the highest quality products at the greatest output.
EIRICH
Simple and cost-effective fertilizer granulation
Even the best fertilizers have little worth if nutrients cannot be applied to crops in the correct quantities at the right rate. This simple fact is what continues to keep the demand for granulated fertilizers high. Especially as stable, round and free-flowing granules are needed when applying fertilizers with a centrifugal broadcaster.
Granules with these characteristics can be applied optimally across the field to deliver an even distribution of nutrients over the soil.
SmartMixer – an ideal granulator
The Eirich SmartMixer is capable of mixing, granulating and coating raw materials within one single item of equipment. It operates rapidly and can granulate powdered materials in a matter of minutes (Figure 1). Chemical reactions can also be carried out within the mixer quickly and completely. In many applications, the SmartMixer combines individual processes together – enabling, for example, a homogeneous mixture to be produced from filter cake, dusts and slurries etc.
Within the mixer, water is firstly added to uniformly moisten the powder mixture. Forces of adhesion then act between the particle leading to the formation of granules. It is also possible to add binding agents or other additives to the granulating fluid – typically water – as required. The addition of a binding agent increases the strength of granules to ensure that these will not disintegrate under mechanical stress. When required, larger pellets (5-10 mm size) can also be produced using a disk pelletizer unit.
The SmartMixer combines fully-automated mixing and granulation processes in a single system. By combining individual processes in this way, Eirich can create a complete fertilizer production plant – one that is capable of continuously manufacturing fertilizers to consistently high-quality standards around the clock (Figure 2). Many straight fertilizers are used as important constituents of compound fertilizer mixes. They can also be granulated individually to improve field distribution and reduce dust formation. Examples of popular straight fertilizers include:
- Potassium sulphate (sulphate of potash, SOP, K2 SO4 )
- Potassium chloride (muriate of potash, MOP, KCl)
- Ammonium sulphate (AS, (NH4 )2SO4 )
- Diammonium phosphate (DAP, (NH4 )2HPO4 )
- Polyhalite (K2 Ca2 Mg(SO4 )4·2H2 O) etc.
The goal of granulation is to produce uniform and round granules with a target size of 2-4 mm. High throughput rates of several tonnes per hour are required for the main straight fertilizers listed above. High capacity R28 and R33 type Eirich Mixers are therefore used for this purpose. Eirich can offer a range of customised granulation processes capable of manufacturing large amounts of granular fertilizers to very high quality standards.
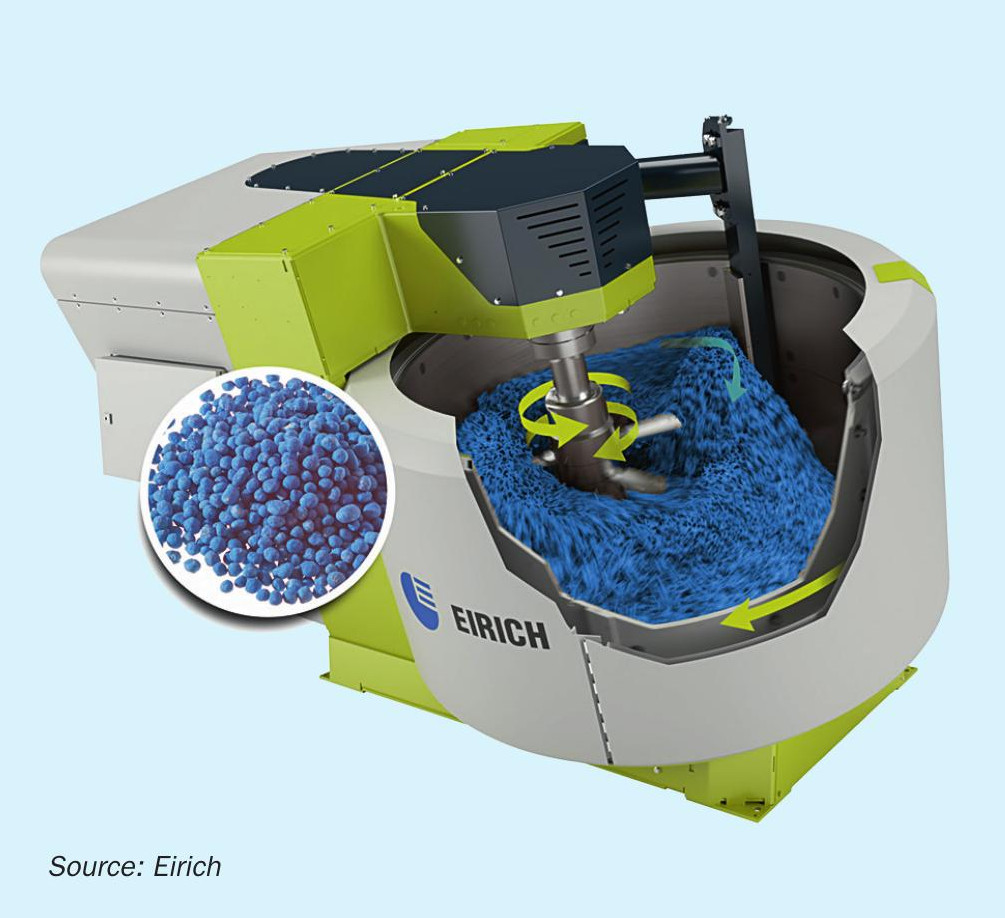
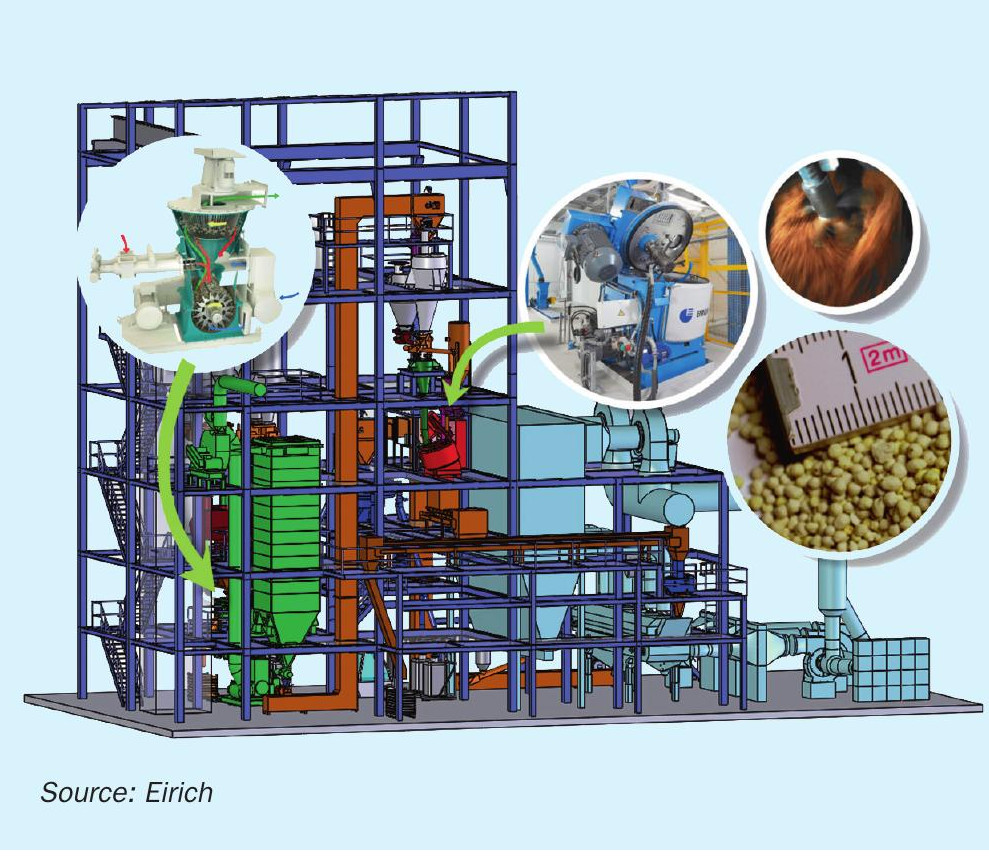
Dissolving minerals with acids
Phosphate rock can be dissolved in sulphuric acid at industrial scale to manufacture superphosphate. This process can be carried out particularly quickly and efficiently in an Eirich mixer. Dissolution in acid transforms the insoluble apatite (calcium phosphate) present into a soluble and plant available form of phosphorus. Similarly, the valuable nutrients present in other insoluble minerals can also be made more available to plants by treatment with sulphuric acid or phosphoric acid. Serpentinite, which contains magnesium silicate, is one example.
Eirich has installed a modern production plant in Paraguay which uses serpentinite to manufacture fertilizer. This plant combines a RV19 Eirich mixer with a TR36 disk pelletizer. The serpentinite rock is crushed, ground and then dissolved with sulphuric acid in the mixer. This generates a moist reaction product which readily forms granules in the disk pelletizer. The soluble end-product obtained via this process is applied as fertilizer to soils to improve the growth and yield of maize and grain crops.
Recovering valuable resources
Because they are finite, it is becoming ever more important to use all natural resources both sparingly and sustainably. For example, phosphorus – which is in high demand as a fertilizer – is contained in large quantities in sewage sludge ash. This can be concentrated and recovered by the precipi-
tation of struvite (magnesium ammonium phosphate). This can then be dried and granulated using an Eirich mixer which is capable of handling all the required process steps in a single unit.
The recovery and reuse of secondary raw materials is requiring new types of preparation processes and technologies. This is being done, for example, in Duisburg, Germany with an Eirich RV24 mixer and TR36 disk pelletizer. These produce nutrient-rich microgranules for agriculture from gypsum filter cake and other compounds such as kieserite and iron salts.
Conclusions
Energy prices and the costs of raw materials look set to rise in the future. This means that the sustainable use of finite resources will become increasingly important. Cost-effective fertilizer finishing techniques such as granulation – by ensuring that fertilizers are used efficiently – can contribute to more eco-friendly agriculture. Granulation helps ensure that plants receive the nutrients they require in the correct amounts during the growing season. At the same time, granulation also prevents fertilizer losses due to disintegration and wash-out from soils.
LANCASTER PRODUCTS
Enhanced mix-granulation in a single machine
The ability to mix and granulate in a single machine offers fertilizer manufacturers both operational and product quality advantages over traditional granulation methods.
High shear, counter-current mixers – unlike most granulation options – can rapidly mix and granulate materials in the same machine as a single-stage process. In mix-granulation equipment, such as those offered by Lancaster Products, the pan rotates in a clockwise direction, while the mixing tools rotate counter-clockwise. This design results in efficient counter-current mixing by creating the necessary shearing action within the mixing cavity.
The mixing tool’s variable speed capability achieves the desired output by enabling different sized granules and densities to be created. A wide spectrum of granule sizes – from the micron range to as large as 8-10 millimetres – are possible depending on the feed materials. Mix-granulation is completed in batches and excels at producing highly repeatable homogeneous mixes and granules (Figure 1).
Mixing and granulating in the same step in a high shear, counter-current mixer is advantageous (Table 1) as it reduces system complexity in the following ways:
- Reduced physical footprint. The continuous batch process offered by Lancaster Products requires very little square footage due to its vertical design which employs gravity for material transport.
- Operates with high moisture materials. Initial drying and subsequent milling in the manufacturing process can also be eliminated or greatly reduced as the mix-granulation process handles raw materials with up to 50 percent moisture.
- Less maintenance and energy use. The replacement of multiple machines typically found in traditional pelletising process lines with a single high shear, counter-current mixer translates into less maintenance, fewer points of failure and reduced energy usage.
- Optimised ingredients and lower operating costs. Precise batch recipes eliminate the ingredient waste that results from uneven mix distribution. Instead, much less binder and water is required because counter-current mixing technology is highly effective at thoroughly dispersing such additives throughout the main ingredients.
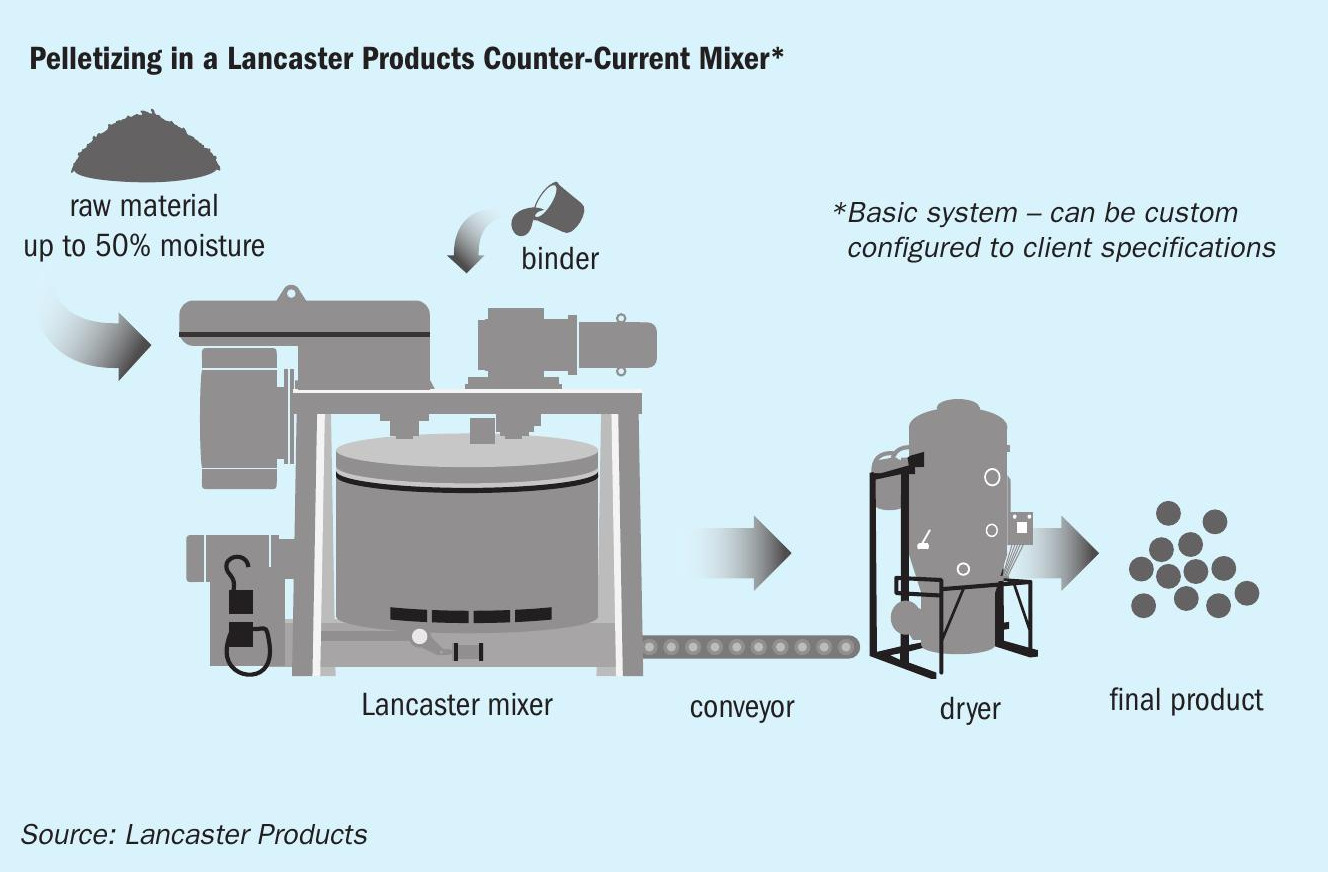
Because the pan, high speed rotor and plow are individually controlled, the mixer can create exact and repeatable conditions within the mixing cavity to produce specific products – e.g., granules of a specific size within a tight tolerance. Valuably, even slight adjustments to tooling speeds can produce different sized granules, shapes, densities, and yields. Mix-granulation also offers the following product quality advantages:
- Homogeneous pellets with improved ingredient distributions
- High yields of on-size pellets with substantially less need to reprocess off-size product
- Versatility to control pellet size and characteristics on a batch-by-batch basis.
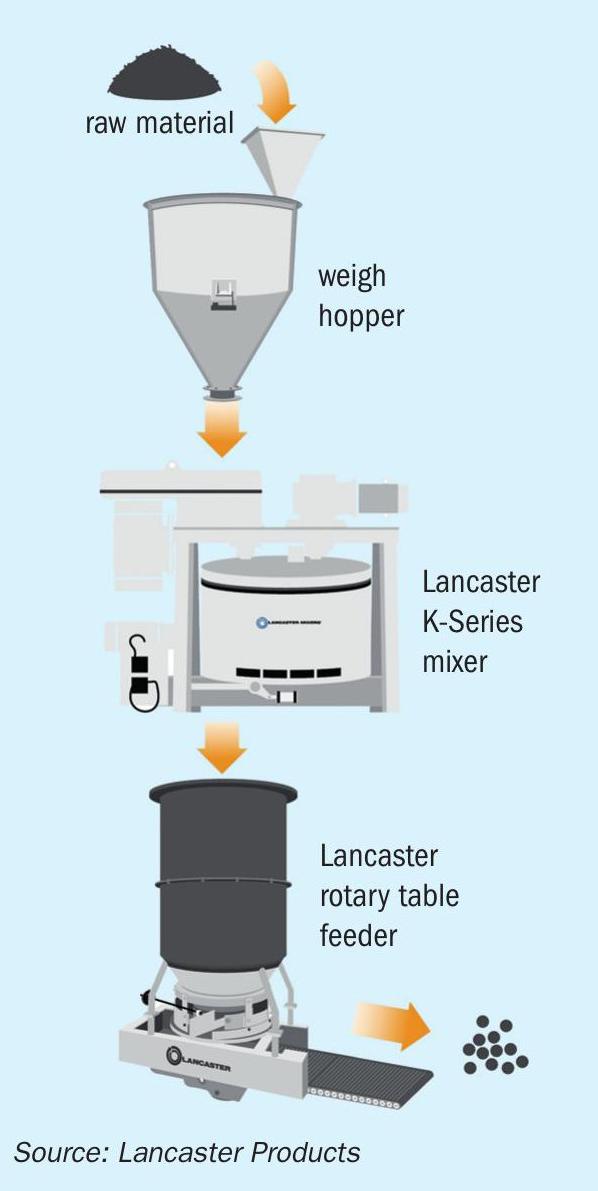
Increased throughput
Batch processing of complex fertilizers offers both greater product accuracy and high outputs. The other key advantages of a batch process are recipe optimisation and mix homogeneity. These important benefits can be realised simultaneously with the consistent throughput and high production rates of a continuous production line.
A continuous batch processing system (Figure 2) is configured sequentially as follows:
- The process begins with pre-weighed raw materials and binders
- These are delivered to the mixer via a weigh hopper
- The high shear mixer runs through a dry mix, a wet mix and then continues to a granulation cycle
- The material is then discharged from the mixer to a conveyor or table feeder – this converting the batch process into a continuous flow of materials l Parallel lines for redundancy, or systems with multiple mixers, can also be utilised to increase output capacities.
Conclusions
Simplifying the fertilizer granulation process, while simultaneously increasing throughput and lowering costs, all contribute to delivering high value fertilizer products to customers at increased profitability. Advanced technologies such as mix-granulation offer fertilizer manufacturers opportunities to achieve these objectives – by combining high shear, counter-current mixing with continuous batch processing.
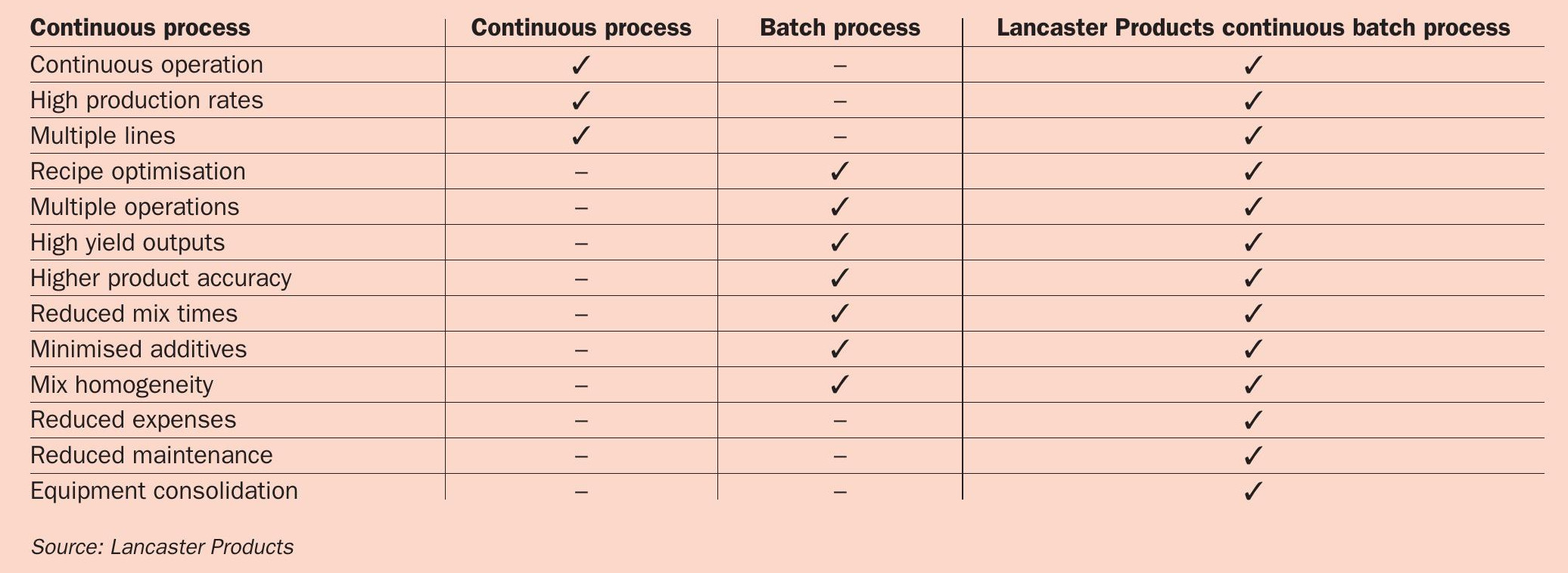
CASALE
Steam vs chemical granulation: picking the best NPK technology
Advantages of chemical granulation
Chemical granulation, using both solid and liquid raw materials, is generally recognized as the most complete NPK production method. This reflects both the nature of the chemical reactions involved and its use of liquid and solid raw materials. These process characteristics deliver excellent agglomeration by ensuring strong bonds form between components inside the granule.
The chemical granulation of NPK fertilizers uses a standard granulation loop (granulator, dryer, screen, crusher) and, unlike steam granulation, consumes liquid raw materials alongside solid feed materials. The properties of the fertilizers granules obtained are greatly improved by the chemical reaction(s) between the liquid acid (H3 PO4 and/or H2 SO4 ) and ammonia.
Chemical granulation, because it offers numerous options for selecting different raw materials, can produce a very wide range of different NPK grades (Table 1). Experience has shown that more than 200 NPK grades can be manufactured at a single plant using different liquid and solid raw materials. This is a priceless advantage as it allows NPK plant operators to respond to market demands, such as the availability of raw materials and customer requests for specific NPK grades.
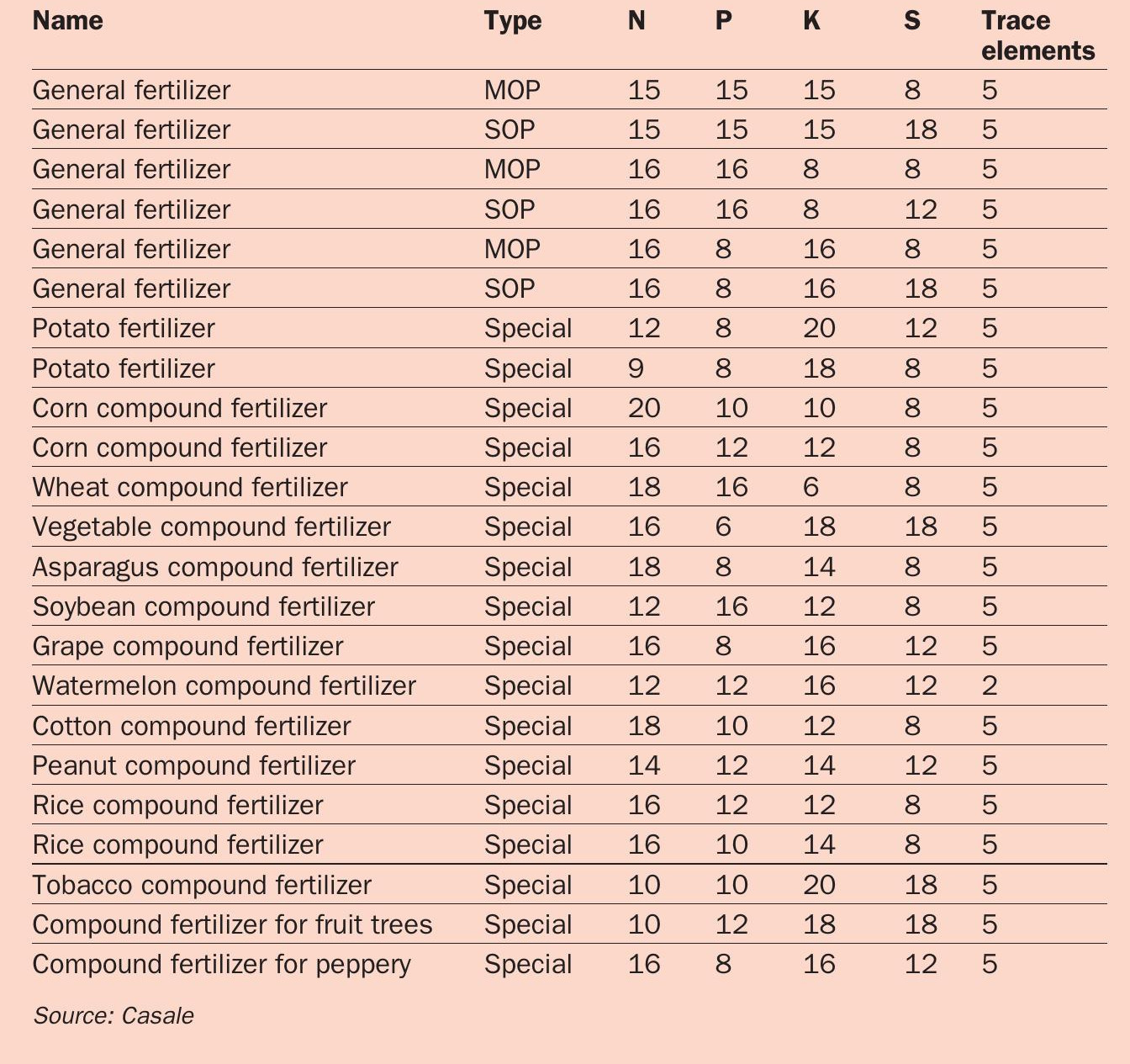
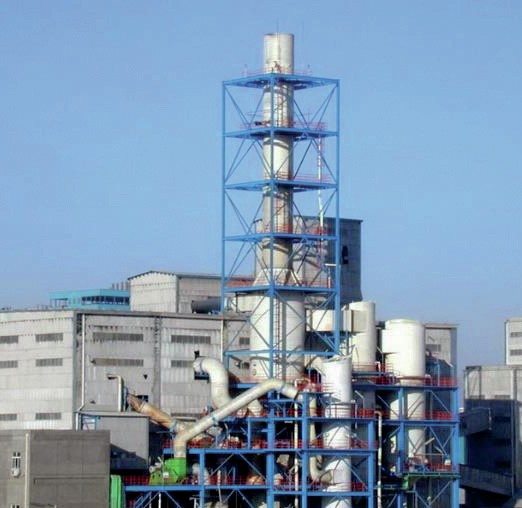
The NPK granules generated also have the best possible chemical and mechanical characteristics. The level of aggregation inside each granule, for example, is excellent due to the strong links between individual components. At the same time, the granules produced have a homogeneous chemical composition, good roundness and high crushing strength. These characteristics are ideal as they ensure the field spreading of NPK fertilizers delivers the desired mix of nutrients to the soil in a homogeneous and controlled manner.
Dual pipe reactor technology
Casale offers dual pipe reactor technology as a chemical granulation process for NPK production (Figure 1). Casale recommends this advanced granulation technology, which is based on conventional drum granulation, even when other NPK production methods such as bulk blending and steam granulation are available.
The dual pipe reactor has distinct advantages over other types of chemical granulation by providing two separate locations for reactions between H2 SO4 /H3 PO4 and NH3 to take place: l The granulator pipe reactor (GPR) l The dryer pipe reactor (DPR).
The GPR is located inside the granulator drum. This is supplied with a feed of H3 PO4 and/or H2 SO4 together with NH3 and recycled scrubbing liquor. The DPR is located inside the dryer drum and is supplied with an H3 PO4 and NH3 feed. Acid(s) can also be supplied to the scrubbing system to properly control atmospheric NH3 emissions.
This design configuration makes it possible to further widen the range of raw material choices and, consequently, increase the number of NPK grades that can be produced. It also guarantees the lowest possible production cost by adjusting the solid-liquid ratio to lower the recycle rate.
The production of any NPK grade can be targeted by selecting different raw materials such as:
- Solid and liquid ammonium nitrate (AN) and urea
- Liquid (phosphoric acid) or solid (MAP, DAP, SSP, TSP, etc.) phosphorus sources
-
Liquid or gaseous ammonia
-
Sulphuric acid
-
Nitric acid
-
Solid ammonium sulphate (AS)
- Elemental sulphur
- Micronutrients.
NPK or NP grades can be produced by either selecting or omitting a potassium source (KCl or K2 SO4 ), respectively. NP and NPK grades using different nitrogen sources, such as ammonium nitrate, urea or ammonium sulphate, can also be manufactured.
For each NPK grade, raw materials are generally selected according to market availability and cost. Operating costs (particularly recycle rate) also have an impact on raw material selection. Plant flexibility, in terms of raw materials, is therefore a key factor when it comes to the competitive production of NPK grades in response to changing market conditions.
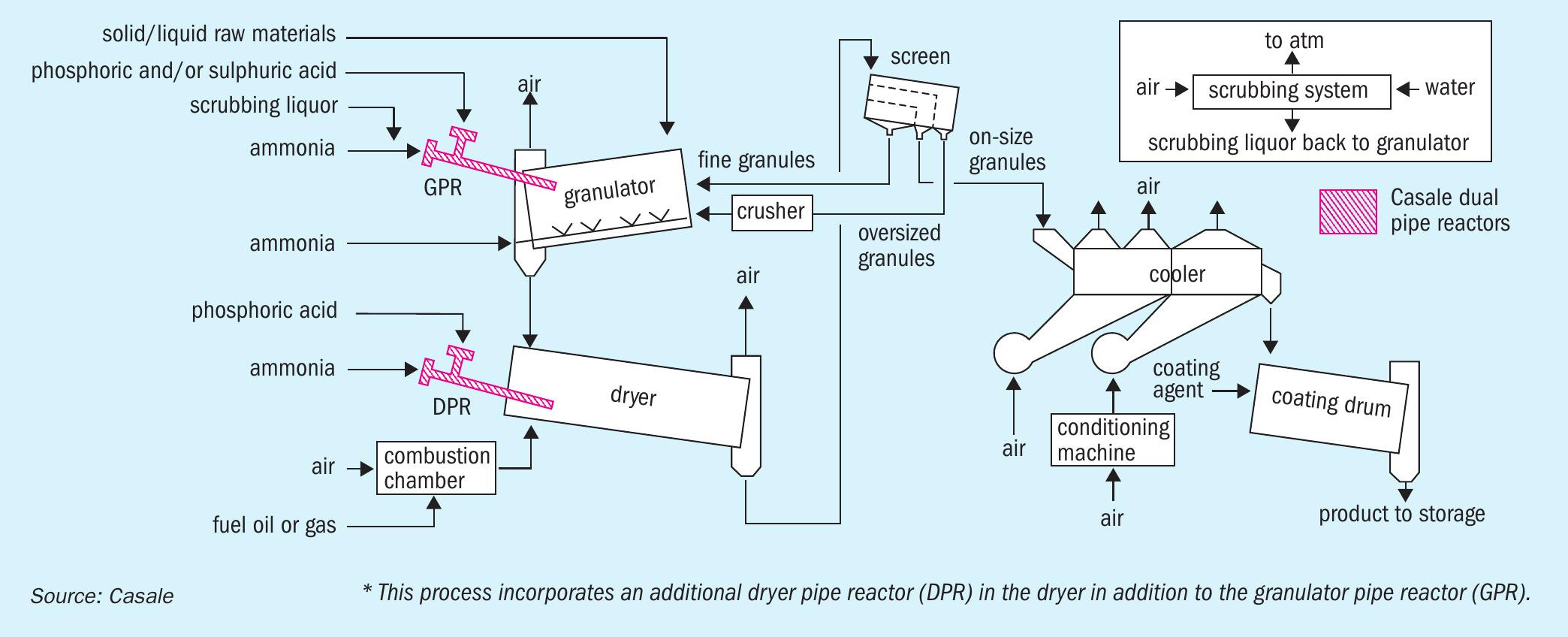
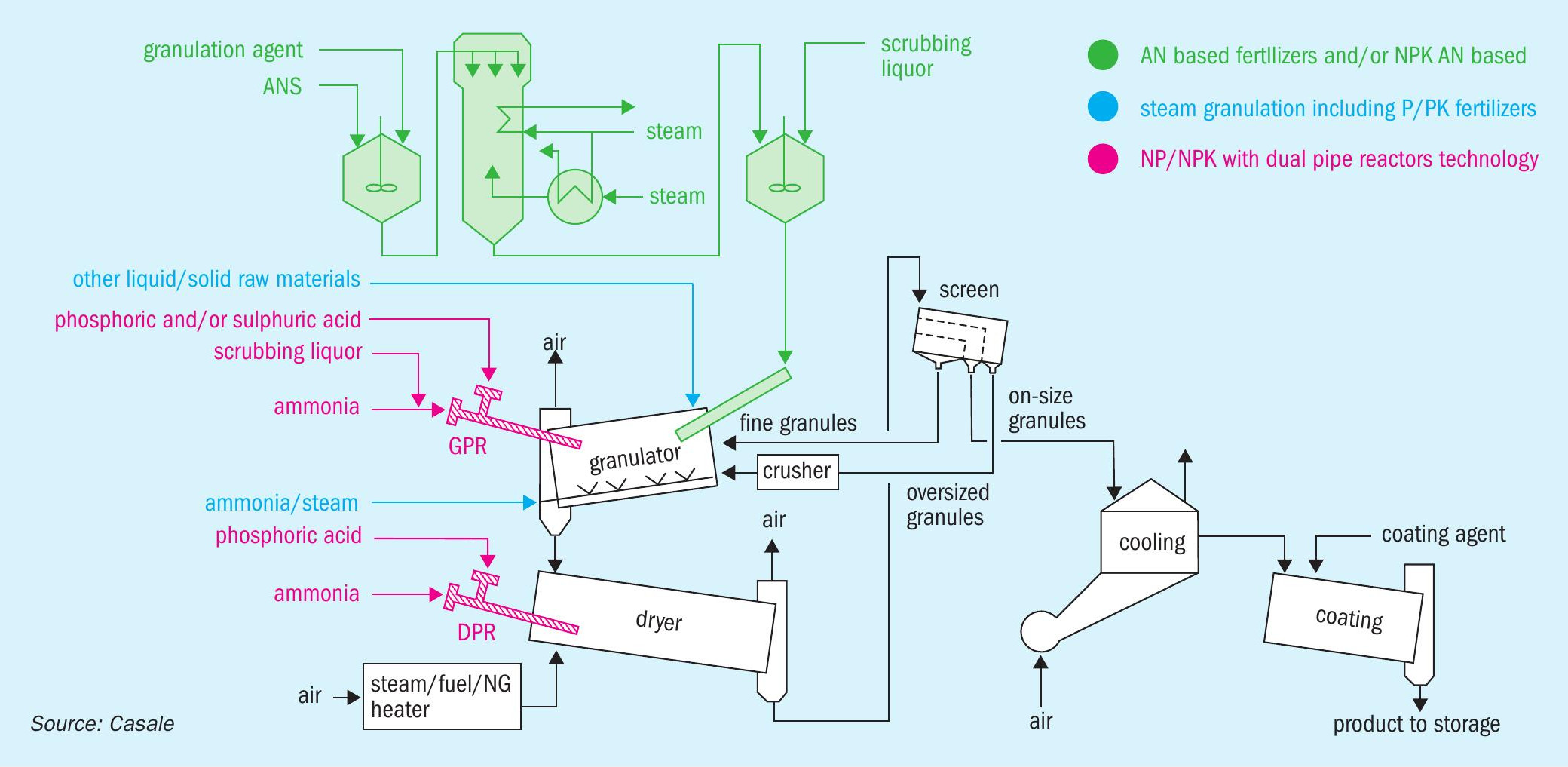
Investment and production costs
Chemical granulation is undoubtedly the best production choice for NPK product quality and offers the maximum flexibility for both raw material use and NPK product options. The selection of chemical and steam granulation should however, involve an evaluation of their respective investment and production costs.
Chemical granulation is not much different from steam granulation in terms of investment cost. Both require a complete drums granulation loop (granulator, dryer, screens, crushers). Additionally, chemical granulation requires extra feeding systems and reaction point equipment (GPR, DPR) for liquid raw materials.
The main difference in the production costs of chemical and steam granulation, however, reflect their different raw material costs. Chemical granulation requires an available supply of phosphoric acid and/ or sulphuric acid plus ammonia. Nevertheless, the consumption of acid and ammonia can be minimised for each NPK grade by adjusting the raw material selection and mix. Phosphoric acid can be used as the sole phosphorus source, for example, or in combination with other solid sources (MAP, DAP, SSP, TSP), according to availability and what is most economically advantageous.
Revamping
Because they are configured with essentially the same equipment, a steam granulation plant – if based on conventional drum granulation – can be upgraded to chemical NPK granulation by revamping with Casale’s dual pipe reactor technology.
Casale has successfully revamped several granulation plants. These have either:
- Changed production from NPKs to ammonium nitrate (AN) fertilizer manufacture
- Or upgraded steam granulation plants (e.g., from TSP granulation) to NPK production.
The integrated granulation plant
Casale is a comprehensive licensor of fertilizer production technologies with wide-ranging expertise and long-standing experience in plant design, start-up and operations. By integrating Casale process technologies (Figure 2), it is possible to design a new granulation plant, or revamp an existing plant, to produce the following wide range of fertilizers:
- AN-based fertilizers via chemical granulation
- AN-based NPKs via chemical granulation
- NP/NPKs via chemical granulation with dual pipe reactor technology
- P/PK fertilizers via steam granulation.
The production of AN-based fertilizers, such as ammonium nitrate (AN), calcium ammonium nitrate (CAN) ammonium sulphate nitrate (ASN), requires a dedicated AN solution concentration section together with a granulation agent dosing and mixing system (Figure 2, green). This is necessary to ensure proper control of ASN concentration.
STEAM GRANULATION
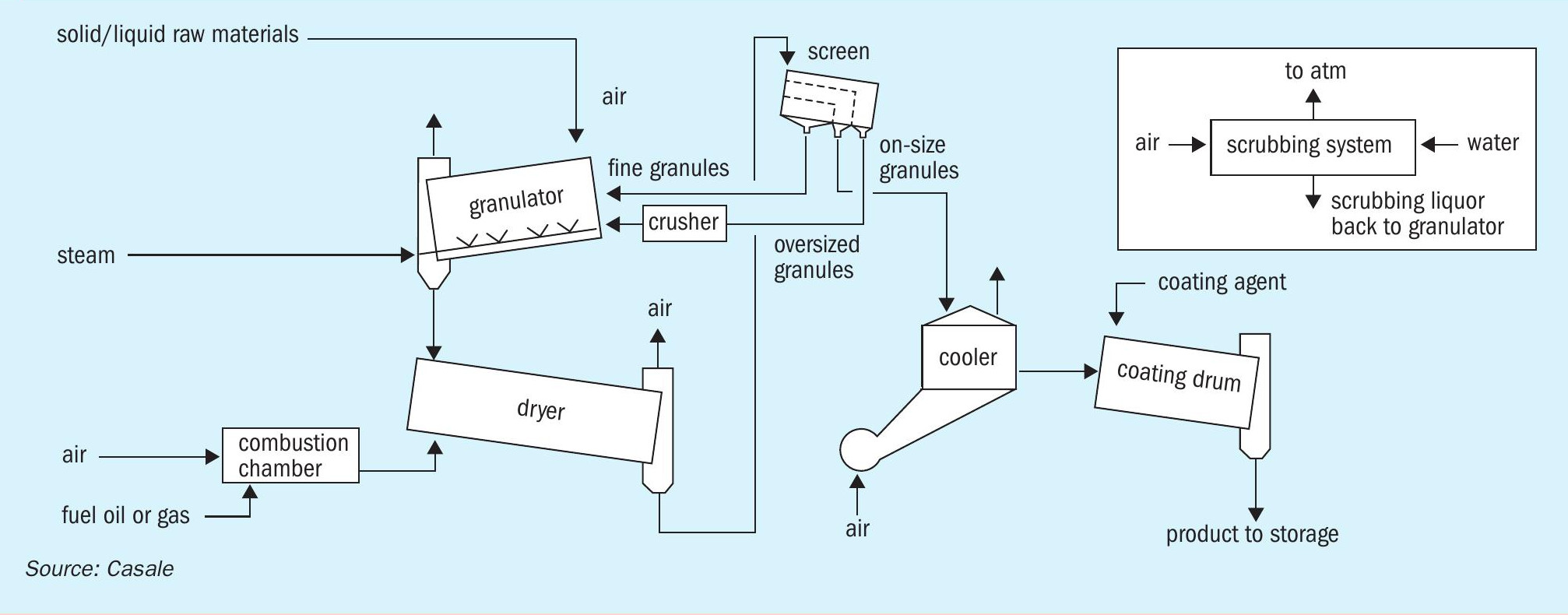
This NPK production method (Figure 3) achieves a specific NPK grade by granulating a ground mixture of solid raw materials in the presence of steam. Unlike bulk blending, steam granulation generates individual granules with the desired NPK composition. In this NPK production route, the addition of steam is used as a ‘glue’ to stick together the different raw material particles. Raw materials need to be pre-ground prior to steam granulation to achieve effective mixing and agglomeration.
The steam production method, to enable granules to form via the agglomeration mechanism, must include a full granulation loop (granulator, dryer, screen, crusher etc). The product granules obtained, although homogeneous in composition, have poor mechanical properties (crushing strength and roundness) because their different components are only held together weakly.
Not all fertilizer raw materials can be mixed and granulated using steam either, superphosphate and urea being two examples. This limits the flexibility of steam granulation by restricting both the range of acceptable raw materials and the method’s ability to produce different NPK grades.
Despite this, steam granulation still has a deserved place in Casale’s technological portfolio especially because of its ability to produce certain valuable fertilizers, particularly granular phosphates or PK grades, using only solid raw materials. Notable examples include the steam granulation of single superphosphate (SSP) and triple superphosphate (TSP).
In these fertilizer types, the only nutrients present are phosphorus or phosphorus plus potassium, while nitrogen (in the form of ammonia, for example) is specifically avoided. This means that phosphoric acid or sulphuric acid cannot be used as the ammonia necessary for their neutralisation is absent.
Casale therefore offers steam granulation as a process step in SSP/TSP powder production as follows:
- In the first step, SSP/TSP powder is initially produced in a Casale run-of-pile SSP/TSP plant by acidulating rock phosphate with sulphuric or phosphoric acid.
- In the second step, the SSP/TSP powder, with or without addition of solid K source such as potassium chloride, is granulated in a steam granulation plant.