Sulphur 405 Mar-Apr 2023
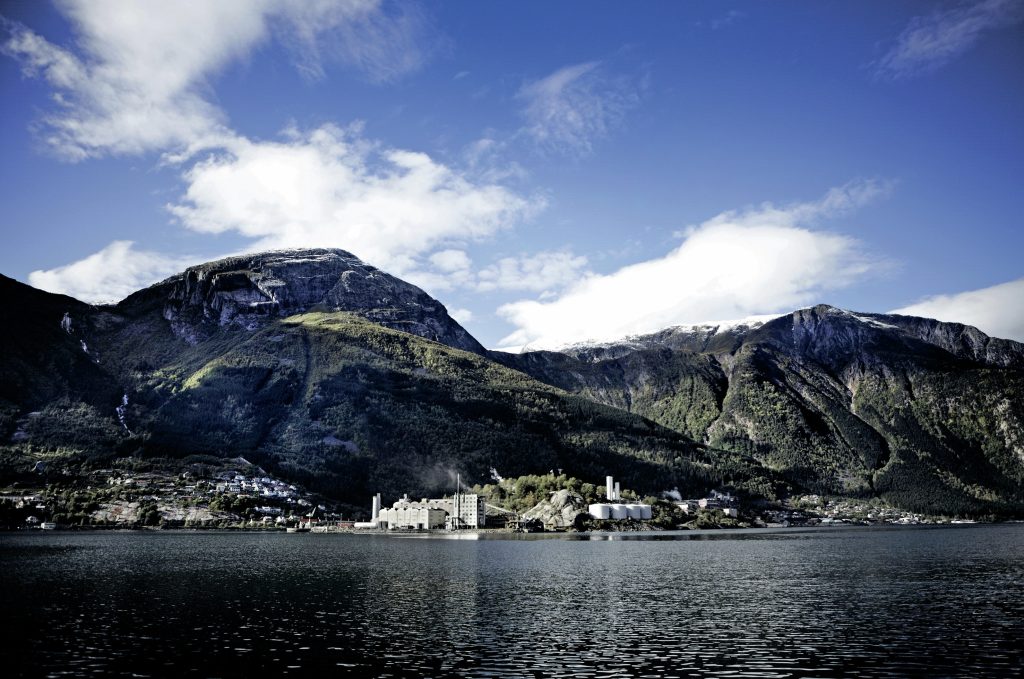
31 March 2023
Sulphuric acid plants as a source of carbon free energy export
ENERGY EXPORT FROM ACID PLANTS
Sulphuric acid plants as a source of carbon free energy export
The sulphuric acid process is virtually carbon free and, as such, it is important to consider the energy requirements of the associated industrial complex before deciding upon what form the energy should be exported from the acid plant. In this article, Stefan Braeuner, Stefan Mohsler and Anne Mohsler of Metso Outotec use case studies to exemplify the need to fully analyse the local conditions at site before a decision is taken on a specific flowsheet.
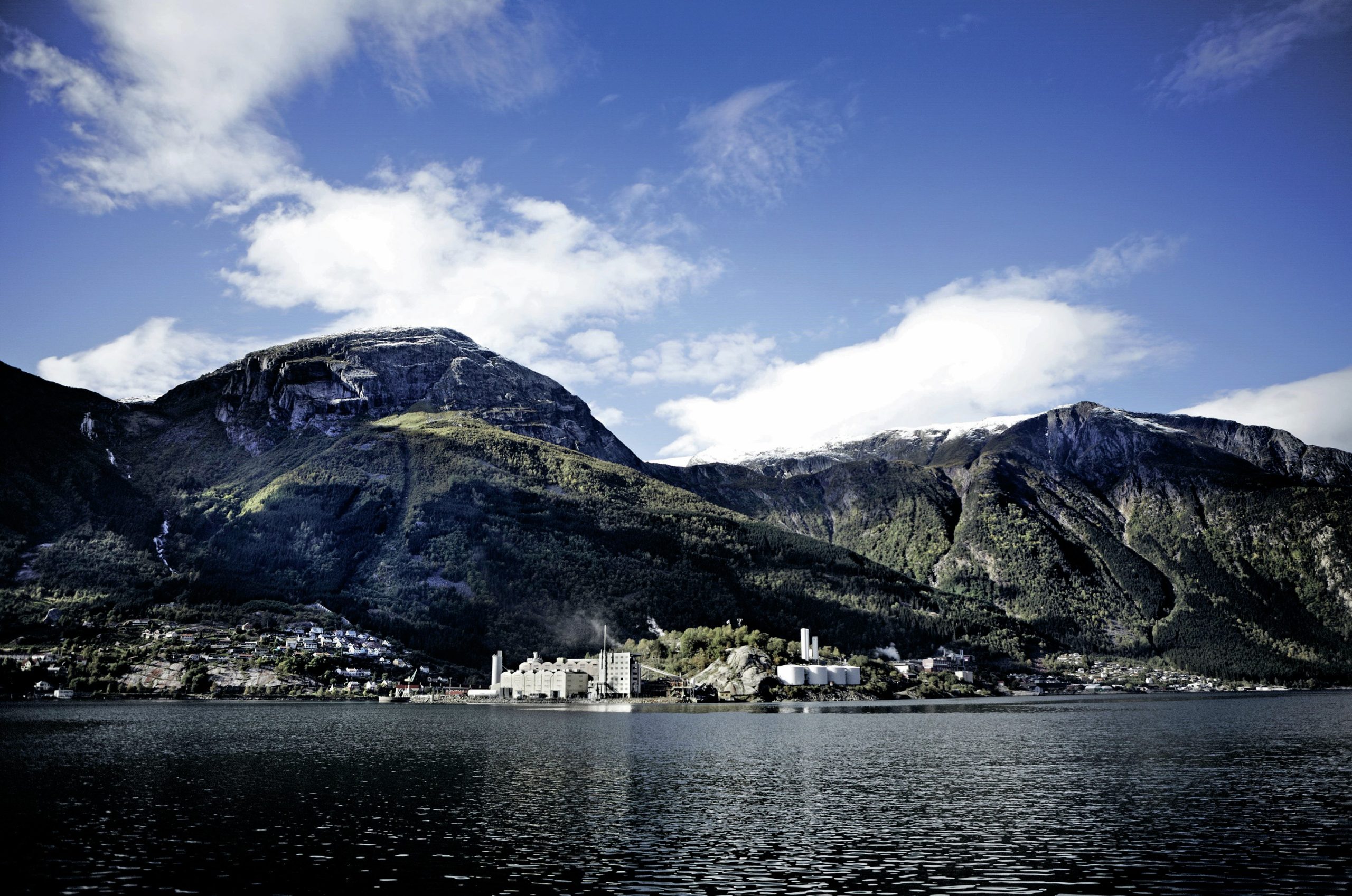
First, some home truths regarding sulphuric acid plants as a source of carbon free energy. In general, sulphur burning sulphuric acid plants can be considered virtually carbon free in their entirety. This is also the case for the complete metallurgical value chain – in other words, the pyrometallurgical process (smelter/roaster), gas cleaning and associated sulphuric acid plant. In all that we strive for in the industry, it has little to do with carbon!
It is therefore important to consider what form of ‘carbon free’ energy best suits the specific needs of the upstream/ downstream operation and not just consider that maximising steam generation to produce electrical power as the one and only solution for an acid plant complex. For example, payback for an optimised, high efficiency turbogenerator set and associated infrastructure in a country where abundant hydropower is available at low cost must be investigated for its economic sense. The aim might not be to maximise the export of electrical energy, but rather produce just enough for the plant’s own needs and thus remove the reliance on external power sources.
Surplus energy can then often be used as, for example, heating steam in processes for drying of ores or other sections requiring heat input. The same consideration needs to be given to low level heat available in acid plants, as such heat can on one hand be transformed to low pressure steam with significant additional equipment or recovered as hot water for applications such as phosphoric acid pre-concentration or district heating with a much lower level of investment intensity and added complexity within the acid plant.
Beside these fundamental considerations there is a need to consider details in plant design to improve operational KPIs such as specific energy or water consumption. Here a critical review of initial investment versus operational cost needs to be carried out. Furthermore, the impact of digitalisation in supporting operational KPIs is not yet fully visible today and first initiatives show promising results.
In the following pages, a number of existing metallurgical acid plant references are presented as case studies that have, for a number of site-specific reasons, chosen ‘carbon free’ energy export related solutions to suit their specific operational requirements.
The common denominator of all the projects is that specific technologies for the particular needs of the overall plant complex have been introduced, supporting the overall operational KPIs.
Case 1: MP steam export
Metso Outotec is currently delivering a copper smelter complex, with scope including flash smelting, flash converting, gas cleaning and Lurec® technology. This smelter complex will process 1.7Mt/a copper concentrate.
The sulphuric acid plant, based on the proprietary Lurec® technology, has a number of distinct features that have been proven in operating reference plants and can be considered particularly sustainable and indirectly mitigate significant CO2 emissions:
- Thanks to the off-gas composition originating from the flash smelting furnace (FSF)/flash smelting converter (FSC) combination, the acid plant processes approximately 300,000 Nm3 /h of gas at 17% SO2 in a single process train and ultimately produces some 5,500 t/d of sulphuric acid – the largest single train acid plant in the world.
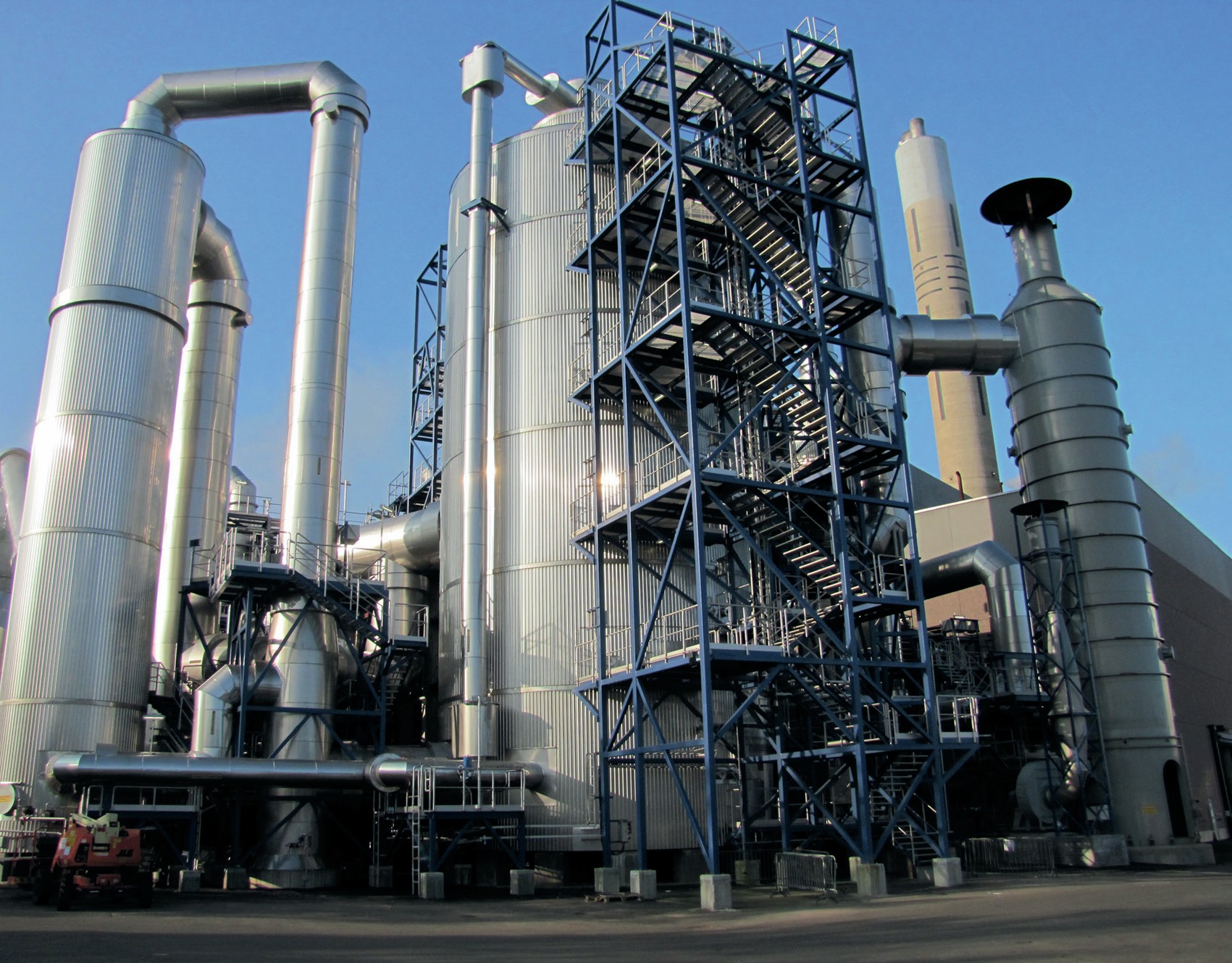
- The Lurec® technology enables the gas to be processed in a single acid plant, leading to a significant reduction in plant footprint, equipment size and scope of supply, civil works and plant erection. Although no calculation has taken place to estimate the inherent CO2 savings, this may well be significant.
- Due to processing a reduced but higher SO2 strength gas stream, significant savings in specific energy consumption and cooling water can be achieved.
- SO2 emissions are reduced by approximately 40% based on utilising the Lurec® concept versus two conventional acid plants.
- Furthermore, the plant is expected to export around 75 t/h medium pressure steam at 24 barg, which was considered the most valuable energy export format for the copper complex as a whole. This steam is used for copper concentrate and matte drying, thus allowing the high pressure smelter steam to be utilised for power generation.
Case 2: Excess heat utilisation
A further example of utilising the excess heat of the sulphuric acid plant is exemplified at Boliden’s Harjavalta plant.
As already presented at the Sulphur + Sulphuric Acid Conference in 2018, the acid plant processes an offgas volume of approximately 149,000 Nm3 /h @ 14% SO2 from various sources including a Ni FSF, weak acid thermal decomposition and partially from two Peirce Smith converters and one Cu FSF. The 2,400 t/d plant includes a five-bed converter enabling compliance with SO2 emissions of 100 ppm, as well as a modular NOx removal system.
Boliden’s carbon free energy export requirements were for steam and hot water to export into their existing infrastructure, namely:
- 25t/h steam at 38 barg is produced from the exothermic reactions around the five-bed converter HX configuration. The boilers are arranged directly after bed 3 and 5 to keep their outlet temperatures higher than in conventional layouts; this is to gain an extended lifetime especially under fluctuating operating conditions.
- The reactions in the IAT and FAT as well as the DT are also exothermic, leading to a temperature rise of the acid. The heat from intermediate absorption is removed via a shell-and-tube type acid cooler which is operated in a closed loop water circuit. With such a system, power plant water is safely heated up from 55°C to 92°C which yields 37 MW under design flow conditions. The heat from the other sources is not utilised. A trim cooling is installed for operating conditions when there is no demand for hot water.
Case 3: Additional heat recovery from the sulphuric acid circuit
Whilst the first two examples focussed on efficient use of heat from the gas phase, Eti Bakir’s integrated fertilizer and metals recovery complex in Mazidagi/Turkey additionally recovered the heat from the sulphuric acid circuit.
Back in 2013, Eti Bakir was considering how to balance the following issues into a viable business case:
- to build a combined fertilizer and metals processing facility at one location;
- energy production from the various unit processes would also provide a degree of self-sufficiency for the integrated plant complex;
- intent to produce 20% of Turkey’s fertilizer needs indigenously;
- a fertilizer complex capable of producing the fertilizer requirements for the whole of the Harran Plain.
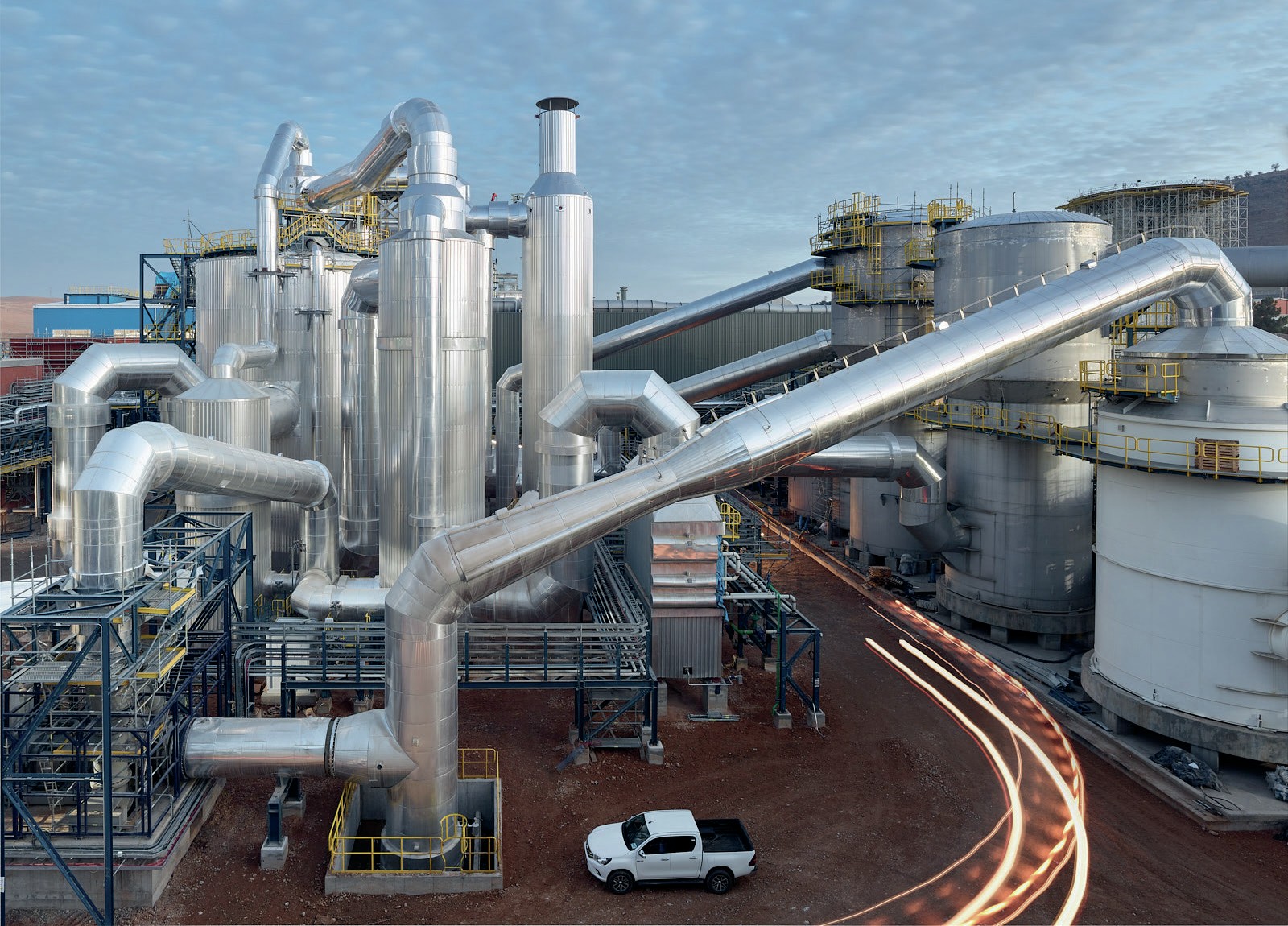
The project was presented in detail at the Sulphur + Sulphuric Acid Conference in 2019 and involves steam raising capability of the complete pyrite roasting value chain (roaster-gas cleaning-acid plant) which enables 33.5 MW of electrical power to be produced, enough to cover the needs of the entire metals complex (some 16.5 MW), as well as exporting a further 17 MW to the external electrical grid.
The sulphuric acid production of 2,080 t/d is quite conventional with an acid quality requirement of As <0.1 mg/kg acid, Hg <1 mg/kg acid and plant emission of <2 kg SO2 /t acid. The sulphuric acid plant has one distinct feature, namely the recuperation of low-pressure steam (via the HEROS™ process). In a metallurgical acid plant with interdependencies of upstream and downstream demands, it is critical that interruption of production is minimised.
Case 4: Sustainable operation
The relevance of sustainable operation operation is depicted in this case study, namely Boliden Odda’s Green Zinc Project in Norway.
In December 2021, Metso Outotec secured a contract with Boliden for the expansion of the current Odda site where they plan to increase their annual production capacity of zinc metal from 200,000 to 350,000 tonnes. The project is called Green Zinc Odda, and its energy consumption is based on fossil-free energy. Metso Outotec scope of delivery includes roasting and off-gas cleaning solutions and a sulphuric acid plant. Metso Outotec will also supply hydrometallurgical equipment and technology for calcine leaching, solid liquid separation, solution purification, as well as process and plant engineering and site services. Plant commissioning is anticipated to take place in summer 2024.
The roaster/gas cleaning/acid value chain will produce approximately 50 t/h superheated steam in total. Extracted low pressure steam is used for internal processes and also routed to further consumers within the Odda facility. With the installed turbine generator unit, which can be operated in island mode, 10 MW of power is generated. Depending on the roaster feed, the acid plant processes some 74,800 Nm3 /h of offgas, produces 817 t/d of sulphuric acid monohydrate and reaches best in class SO2 emissions of less than 20 mg/Nm3 .
The Boliden website quotes as follows, “The expansion enables Odda to almost double the zinc production [whilst] reducing the carbon dioxide intensity by 15% from already a world record leading position. Most of the facilities will be expanded alongside we will modernise our processes, increasing digitalization and automation.” and Metso Outotec is deservedly proud to be part of this leading-edge initiative in the industry.
Case 5: Brownfield acid plant retrofit
Beside such greenfield cases, where the design can be optimised from the get-go, there are many instances of brownfield acid plant requiring significant retrofits to maximise operational KPIs.
A copper smelting complex, commissioned in the 1970s with a capacity of 40,000 t/a of copper from concentrate, has undergone several expansions and technical modifications in the interim period and the production level is currently around 300,000 t/a of copper. Nowadays, the smelter uses an Outotec flash furnace, Peirce Smith converters, anode furnace, an electrolytic copper refinery and three sulphuric acid plants, and produces 1,000,000 t/a of sulphuric acid.
The addition of the heat recovery system in one of the acid plants drastically increased the efficiency of operation. High-grade heat, which used to be dissipated to the atmosphere, is now recovered as superheated steam and turned into carbon neutral, additional electricity in copper complex’s power plant. The superheated steam now produced at the heat recovery system at a pressure of approximately 40barg is sent to the power plant turbine for electricity generation. The average steam generation amounts to around 9 t/h, depending on the SO2 gas strength fed to the plant.
Further reductions in energy consumption were achieved by the no longer required cooling fan, reduction of heat transferred to the acid and the reduced pressure drop of the plant. Although the plant flowsheet complexity has increased, the operation of the plant has not.
Safe operation of the heat recovery system was considered from design to execution and operation of the project. Rather than ignoring the possibility of a leak, the rapid detection by online moisture measurement as well as strict monitoring of critical process parameters were considered a first priority. Together with the well-trained staff of the copper complex, this has resulted in a trouble free and efficient operation.
Summary
When considering what form of energy is exported from a sulphuric acid plant, the above case studies exemplify the need to fully analyse the local conditions at site before a decision is taken on a specific flowsheet. One size does not fit all.