Sulphur 406 May-Jun 2023
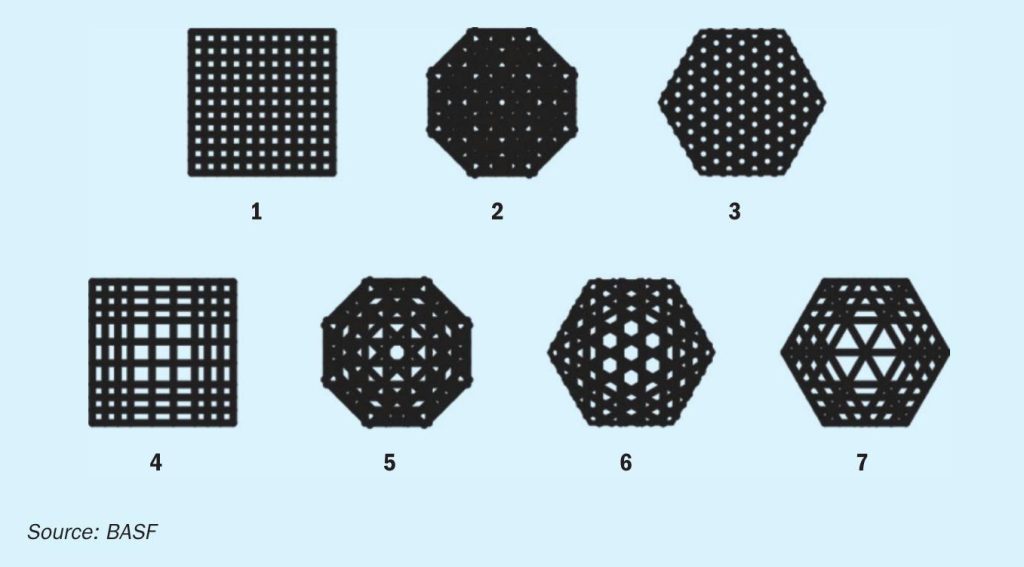
31 May 2023
A new era in catalyst geometric shape selection
3D-PRINTING TECHNOLOGY
A new era in catalyst geometric shape selection
BASF is challenging traditional catalyst shapes and performance relationships by introducing a radically new shaping concept resulting in materials with step change properties and performance. This innovative concept using 3D-printing technology is applicable to a wide range of reactions in the chemical industry and BASF is using sulphuric acid catalysts as the pilot to pioneer new ground.
BASF has produced sulphuric acid for various industrial applications since 1866 and has been producing catalyst for the sulphuric acid process since the early 20th century. A first patent for a vanadium pentoxide catalyst was granted to BASF in 1913. Today, BASF operates six sulphuric acid and 13 sulphonation plants with inline SO2 oxidation units worldwide, all using BASF’s in-house catalyst technology, with world class plants operating at emission levels below 50 ppm SO2 . The last 15 years have brought new challenges such as tighter emission regulations and cost pressure to the sulphuric acid market. This has led to BASF being on the forefront of cutting-edge research into one of the oldest catalysts of the portfolio.
In alignment with the new strategy of BASF, sulphuric acid producers and their needs are even more in focus, driving improvements in catalyst technology. BASF works directly with customers to make sure customers achieve the best performance under the specific design and operation conditions of their reactors. This is enabled through BASF’s state-of-the-art testing facility and analytics combined with more than 150 years of research and experience.
New extruded shapes
The production of sulphuric acid catalysts is generally conducted by extrusion of a precursor paste to yield shaped catalyst bodies. The extrusion process not only defines the shape of the catalyst bodies, but also impacts other crucial properties such as pore structure and mechanical stability of the catalyst. These properties are also related to the fluid properties of the precursor paste in the extrusion device. The extrusion process has to cope with pastes of varying composition for different catalyst types. Fluid properties of precursor paste and control of the entire extrusion process are strongly determined by the specific design of extrusion dies. In particular, the detailed design of the internals of the dies has a significant impact on quality and capacity of extrusion. This becomes an immediate challenge when entirely new shapes for a catalyst family are to be extruded and new dies have to be found.
Continuous progress through a commitment in extrusion technology has been key for successfully turning a lab idea into an established and reliable commercial product. With the help of BASF’s Technology Verbund, with in-house competence on computational fluid dynamics (CFD) and metal powder 3D-printing technology, it was possible to develop and optimise dies for extrusion devices in a short time period. This is evidenced by an international patent family filed by BASF on extrusion dies for catalyst production1 .
In 2016, BASF reaped the benefits from years of catalyst development launching the Quattro geometry with O4-115 Quattro being the first sulphuric acid catalyst2,3 leading to 5-8% increased plant capacity in the first commercial application. Many additional customers have chosen the Quattro geometry since, all benefiting from performance improvements. With the completion of the Quattro family in recent years, sulphuric acid production has been raised to a new performance level. The question arising from this accomplishment was of course, whether the limit of catalyst shaping had been reached or whether there was any possibility to further improve sulphuric acid catalyst shape geometries to surpass the performance benefits of the Quattro range.
A step change in performance with 3D-printing technology
Due to the significant limitation of geometric flexibility, it is necessary to move away from standard line extrusion processes in order to a achieve higher performance via larger pore sizes, higher surface areas, and lower pressure drops. Each and every variation in the geometry requires a new extrusion mould, a process that significantly increases equipment and labour expenses for its implementation. Moreover, standard extrusion methods are not capable of being extended to more complex geometries due to their limitation to formulate continuous channel designs. Therefore, new ways of producing catalysts needed to be found to overcome the limitations to reach these goals. A new way of producing elaborate geometries with dedicated purposes is already established for plastic material parts, metal powders and even construction materials through the use of 3D-printing technologies. 3D-printing has the outstanding benefit that the shape and geometry of the desired part can be precisely designed based on the final material requirements and virtually any design is possible. Novel geometries can be designed and optimised in silico with the help of computer-aided design programs, and subsequently printed allowing fast iteration cycles to optimise shape geometries. As the need for mould production and optimisation is entirely bypassed, 3D-printing offers unique benefits for catalyst design and production4 .
In addition to the benefits of 3D-printing already mentioned, the printing process itself is similar to the extrusion process. In analogy to extrusion, the 3D-printed material consists of active material which is mixed with additives such as binders and rheology modifiers. The paste is also extruded by pressure and heated to generate the final structure, but on a smaller scale. This has the significant benefit that the chemistry of the catalyst material as well as the post processing can be kept similar to the standard extrusion process.
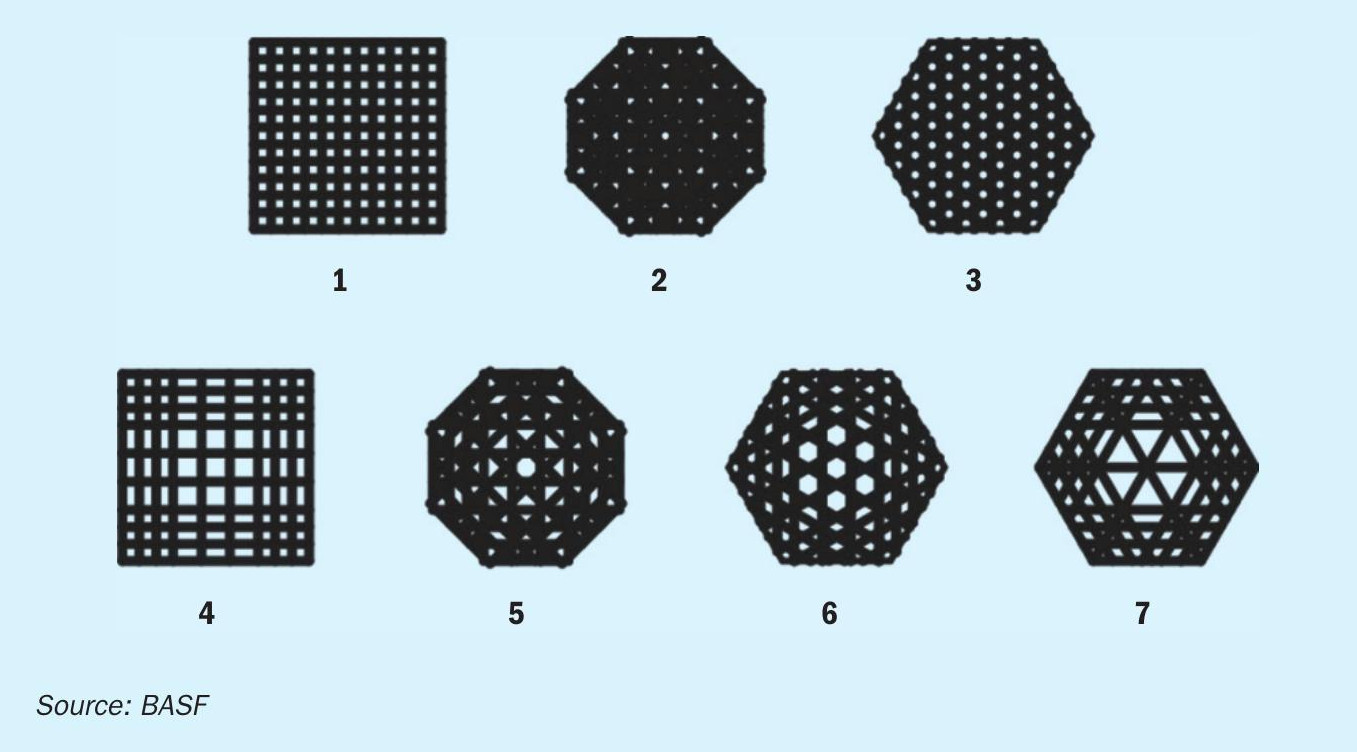
With the introduction of its X3D™ technology, BASF has launched a new range of 3D-printed catalysts that are custom designed to significantly improve performance in their dedicated application processes. This article focuses on O4-115 X3D™ , a sulphuric acid catalyst produced by 3D-printing and already implemented in three commercial sulphuric acid plants5 .
X3D™ technology development
Based on the good experiences with CFD and computer tomography (CT) scans of catalyst beds during the development of the Quattro catalyst, the target was to further harness these technologies in order to improve the catalyst shape geometries. Despite good results in the early stage, it became clear that most of the key features, such as activity and surface area cannot be improved with standard extrusion techniques while maintaining the material strength. A new way of catalyst production was required which was able to decouple these intrinsic features of a catalyst from each other. 3D-Printing technology was identified as the most suitable tool to overcome these limitations, as mechanically stable structures can be produced in virtually every imaginable shape5,6 .
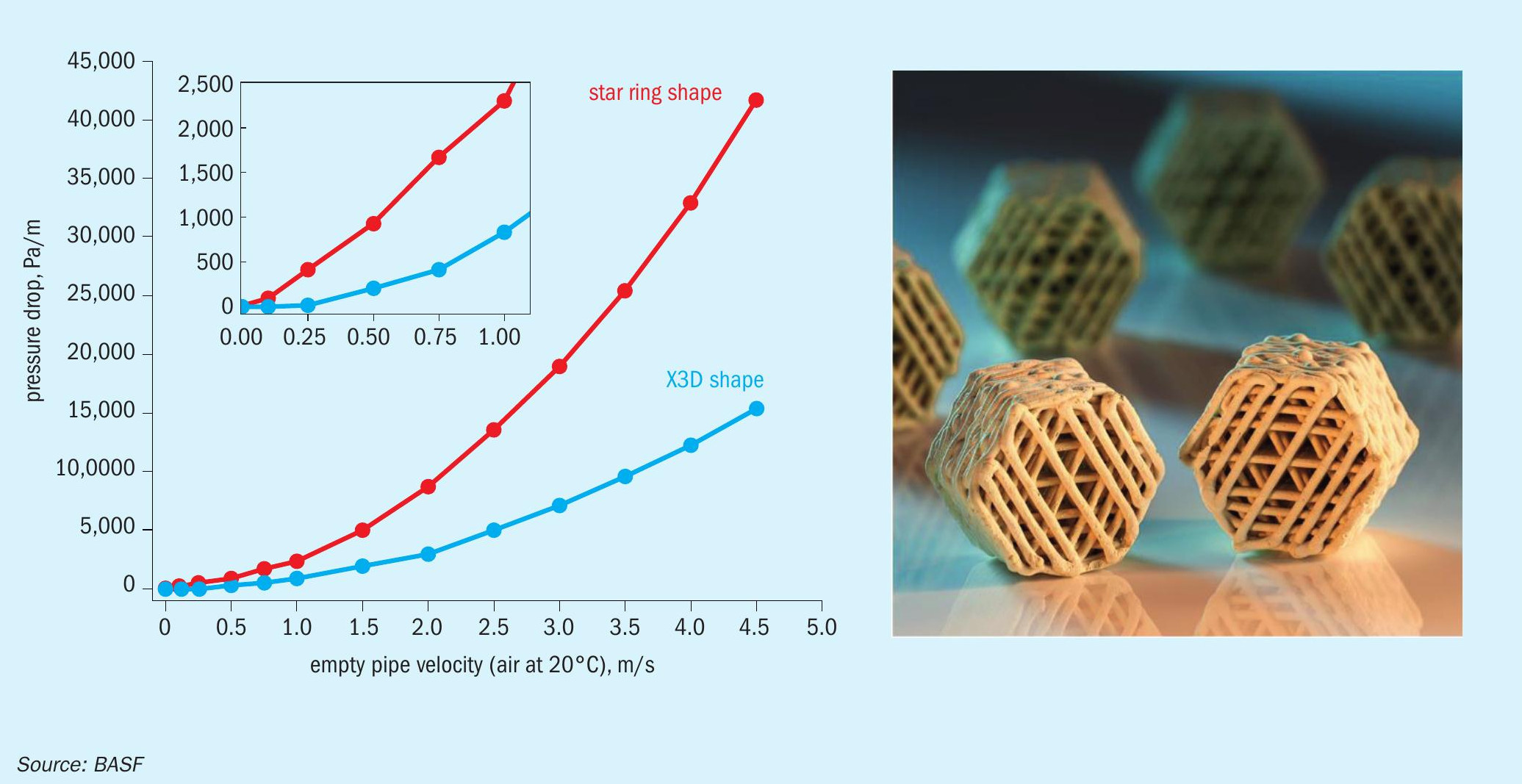
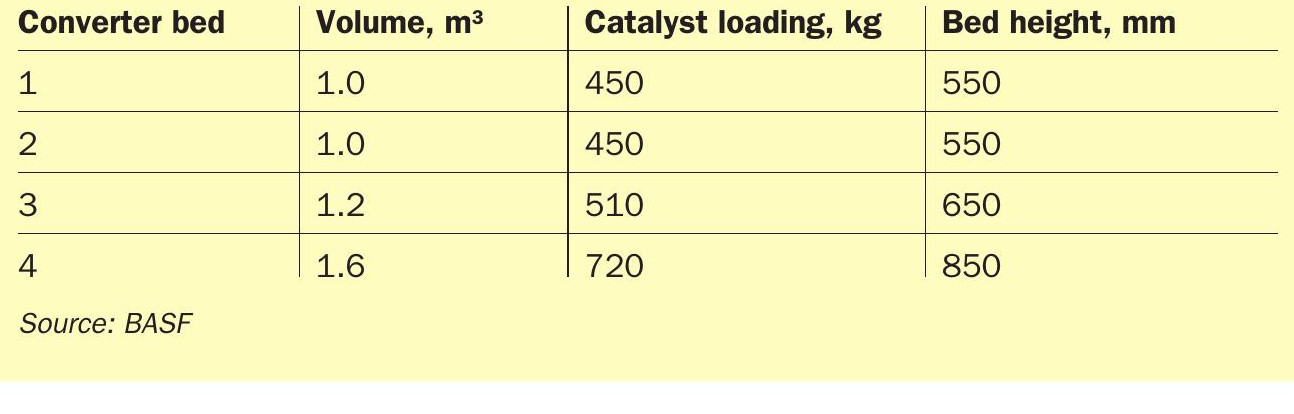
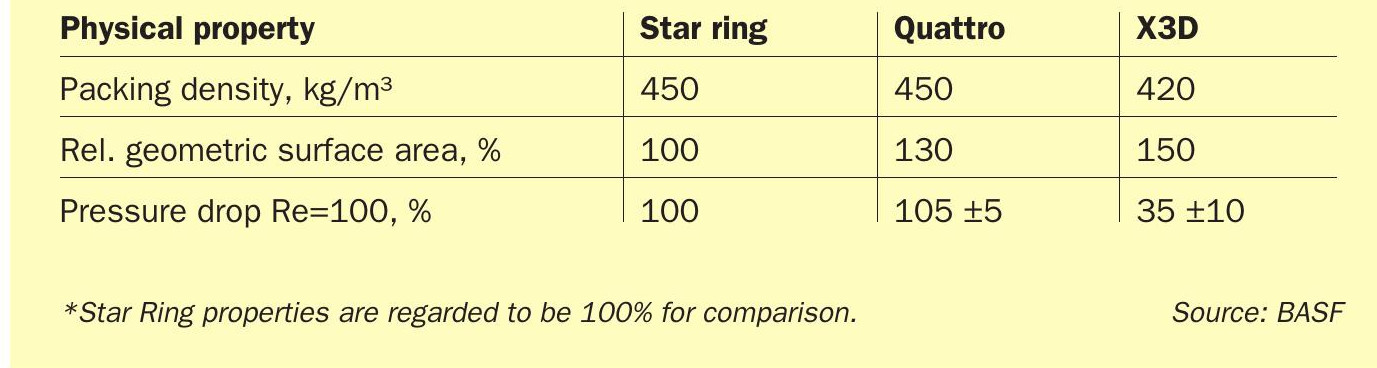
Following the decision to use 3D-printing, entirely new catalyst shapes were designed and assessed in silico using CFD and other simulation tools prior to any shape being physically produced. Based on these calculations7, 8, 9 , seven geometries were identified which can significantly surpass the geometric surface area of standard extrudates (Fig. 1).
The new shape geometries were 3D-printed in a test trial using the same catalyst paste that is used in the BASF production facilities and were subsequently evaluated in order to find the best design fit for the applications as a sulphuric acid catalyst. Catalyst shape geometry 7 (Fig. 2 right) was chosen to be the most suitable candidate for a commercial trial, as this shape geometry incorporates a high geometric surface area and mechanical stability. Moreover, shape geometry 7 displayed a significant benefit in contrast to the other shapes, a significantly lower theoretical pressure drop (Fig. 2 left).
As displayed in the graph in Fig. 2, the simulated pressure drop of the X3D™ catalyst obtained from the CT scans is 66% lower when compared to standard extruded star ring shape geometry. This is an outstanding achievement, as no extruded sulphuric acid catalyst could achieve such a low pressure drop.
When comparing the three catalyst shape geometries (Table 1), the benefits of BASF X3D™ catalyst is clearly visible. The transition from standard extrusion processes to 3D-printing afforded the design freedom for significantly higher geometric surface. Moreover, the X3D™ catalyst design offers a way to decrease the packing density of the catalyst by 7% from 450 kg/m³ to 420 kg/m³ and significantly decrease the pressure drop by 66% compared to star ring geometry. In comparison to Quattro, the X3D™ shape geometry offers a 15% higher geometric surface area, which will also reflect in an increased activity of the catalyst providing even higher performance.
First commercial trial
Throughout the development of the X3D™ catalyst technology, it became clear that the new geometries had a significant impact on the pressure drop. This benefit of decreasing the pressure drop can help SO2 converters with capacity limitations due to the pressure drop. When BASF was approached by the technical team of BASF Care Chemicals for the catalyst exchange of a sulphonation unit in 2018, after initial discussions it soon became apparent that the implementation of a custom designed O4-115 X3D™ catalyst would be an excellent fit to improve the situation of the plant. As sulphonation units operate at higher pressures, a decrease in the pressure drop results in a direct benefit for the plant due to a decreased blower power output and therefore immediate energy cost savings. The internal BASF sulphonation converter became the first commercial reference for O4-115 X3D™ using 3D-printed sulphuric acid catalyst in October 2019.
The facility of BASF’s internal reference is a sulphur burning 4-bed single-absorption sulphonation plant with a sulphur burning rate between 330-480 kg/h with normal operation around 400-420 kg/h. The feed gas has an O2 /SO2 ratio of 2.14. The catalyst O4-115 X3D™ was installed in the third bed. 510 kg of Cs-promoted catalyst were exchanged with 510 kg of O4-115 X3D™ . The target of the trial was to test the impact of the X3D™ catalyst on the pressure drop in bed 3 and the overall converter, as well as the performance benefit with respect to the SO2 scrubber which is used to remove any unreacted SO2 before the emission of the off gas, while maintaining the same sulphur burning rate as before the changeout.
Catalyst installation
This plant was selected based on the relatively small size of the converter beds when compared to a standard sulphuric acid plant. The BASF internal reference plant has a converter diameter of 1,800 mm, and the beds are described in Table 2.
The catalyst was filled by the same method that is used when filling star ring catalyst into the converter, where the technician responsible for the filling can stand on top of the catalyst inside the converter without crushing the shape geometries. This further illustrates the strength of the O4-115 X3D™ monoliths (Fig. 3).
Performance overview
In contrast to typical sulphuric acid reactors which operate at relatively stable reaction conditions, SO2 converters used for sulphonation plants need to adjust the production rates of SO3 based on the demand for products from the sulphonation unit. As a result, measuring the pressure differences and the conversion of the catalyst under comparable conditions was a challenge. The data presented in the following section is therefore displayed as average values collected over a certain day and the fluctuations indicate a change in the production rate.
One of the results from the catalyst filling which is clear and undisputable is the decrease in pressure drop across bed 3. As predicted earlier in this report by the CT scan, the pressure drop of the catalyst is 75% lower than a standard catalyst (Table 3).
To date, the catalyst has been in operation for almost three years to the full satisfaction of the customer. As displayed in the graph in Fig. 4, there has been no significant increase of the pressure drop in bed 3 throughout this period and it is currently at 4 mbar.
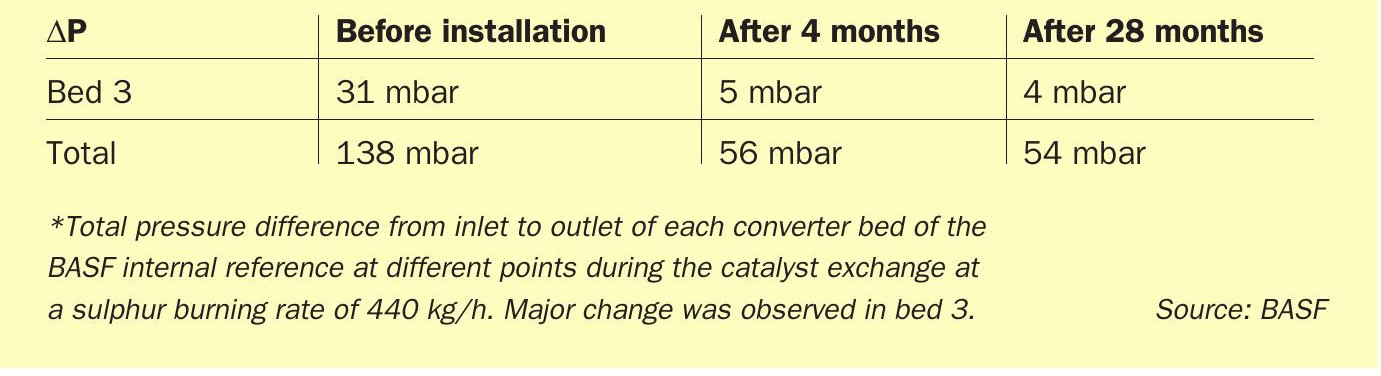
The consumption of 50% NaOH solution in the gas scrubber was used in order to assess the conversion benefit of the X3D™ catalyst. As displayed in Fig. 5, a significant increase in overall conversion could be detected from the decrease of NaOH solution consumption from the point when the new 3D-printed catalyst was implemented.
Using this measure, the SO2 conversion prior to the changeout was approx. 97.7% which increased by up to 1.3% to almost 99% after the implementation of O4-115 X3D™ . This is a significant increase in conversion for a single absorption unit and contributes significantly to the cost savings, as 20% to 45% less NaOH 50% solution is required to scrub the off-gas from remaining SO2 .
Economic benefits
The above-described outcome of the installation of O4-115 X3D™ in the third bed, namely a significant decrease in pressure drop and reduction in the NaOH consumption had a tremendous effect on the variable manufacturing costs. With the 3D-printed catalyst in place, significant cost savings have been made on a monthly basis over the last years (Table 4).
A total cost saving of 6% per month in energy costs and 20% per month for NaOH 50% solution demonstrates the potential of BASF’s new X3D™ catalyst technology. To BASF’s knowledge, this is the first sulphuric acid catalyst shape geometry obtained by an extrusion process which is able to achieve these benefits.
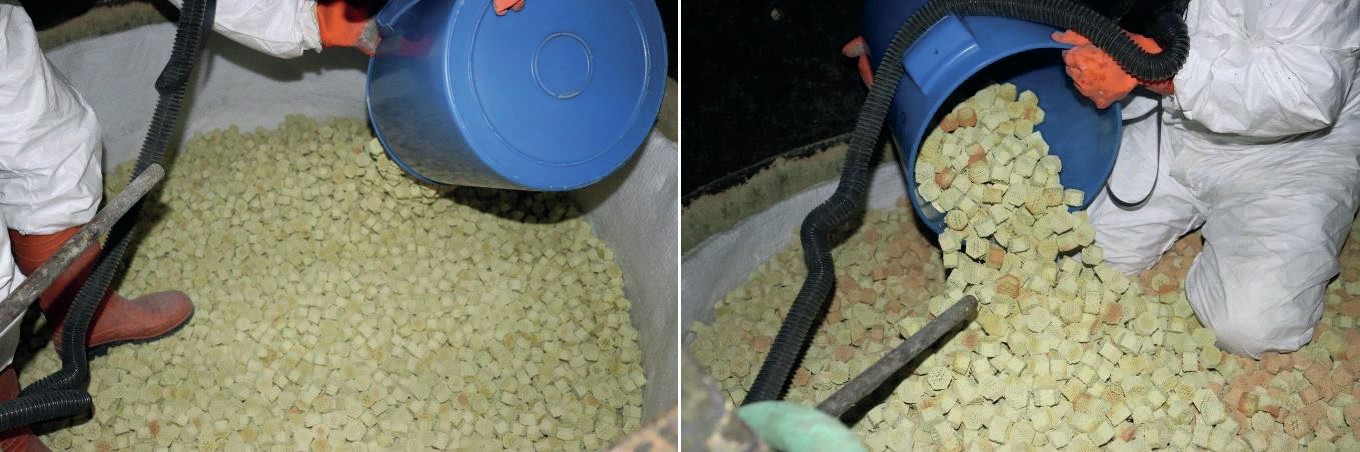
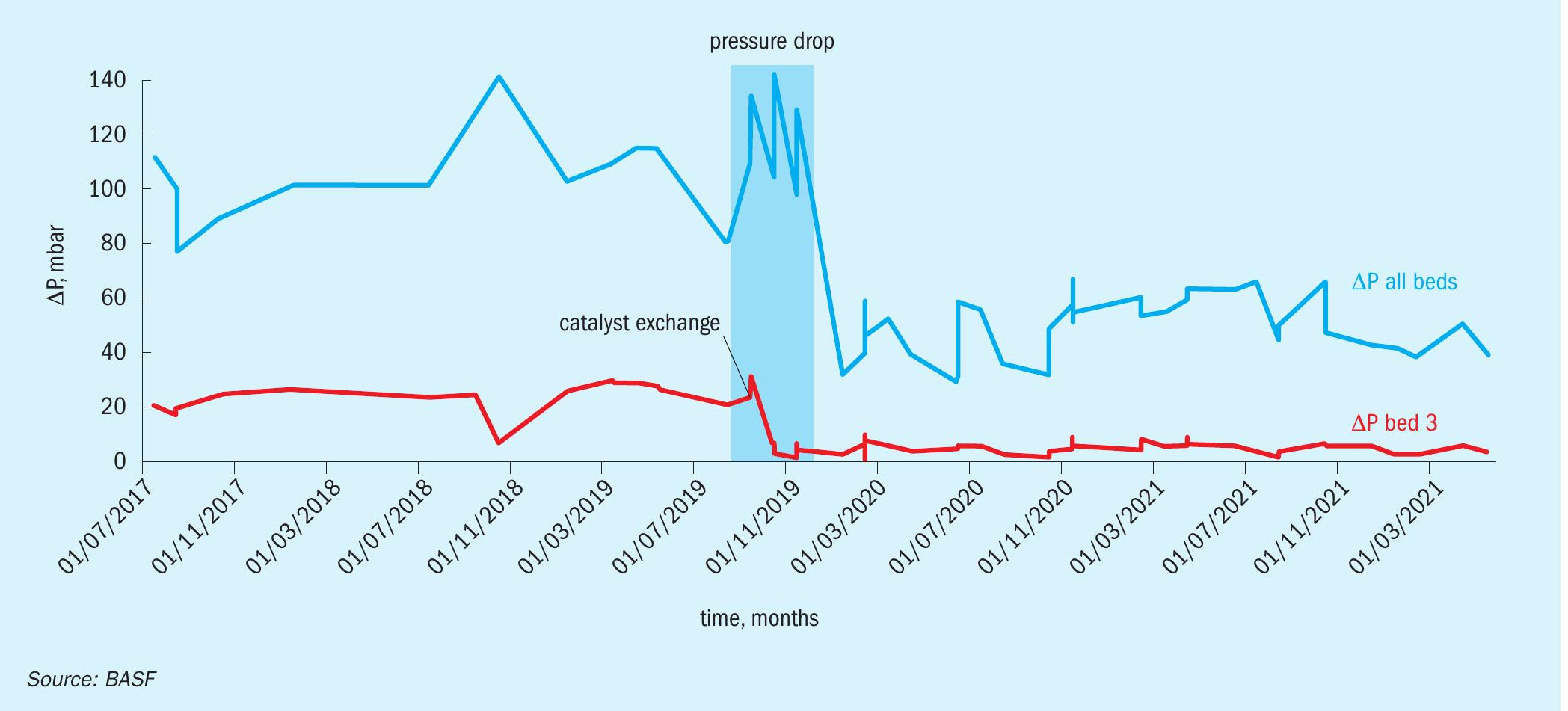
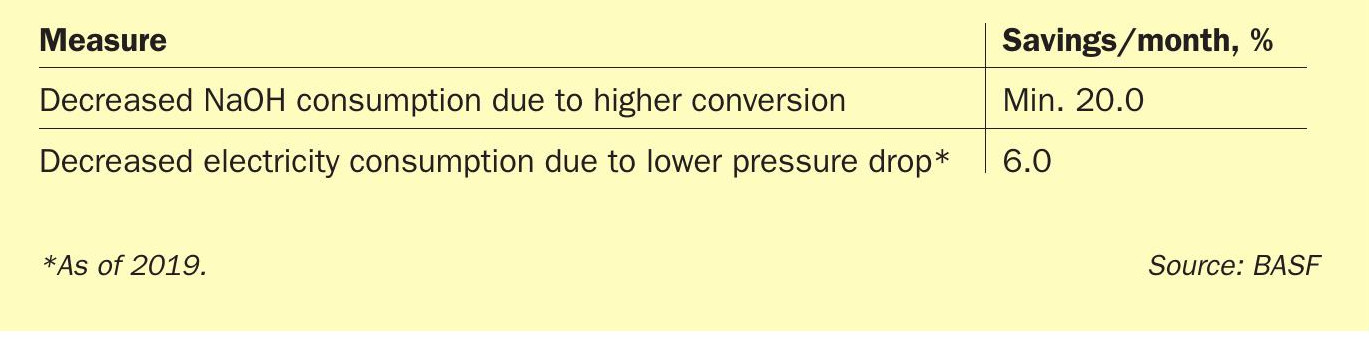
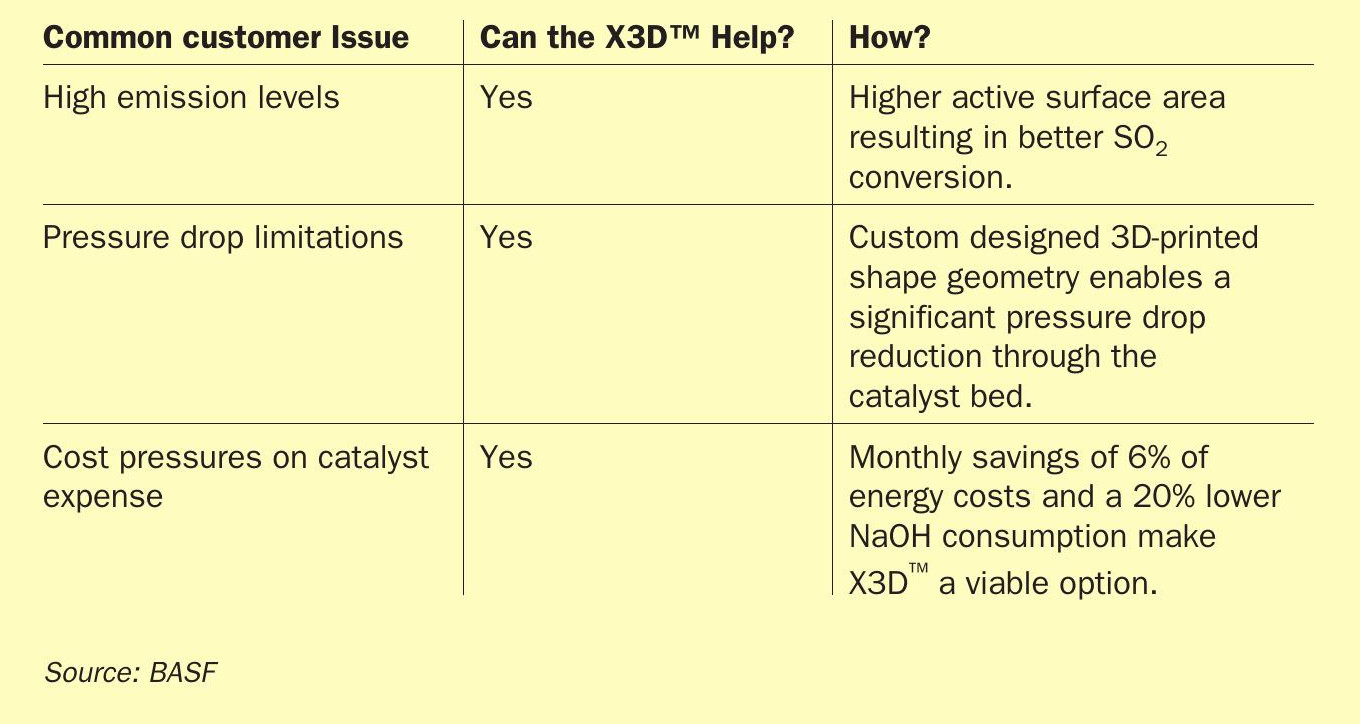
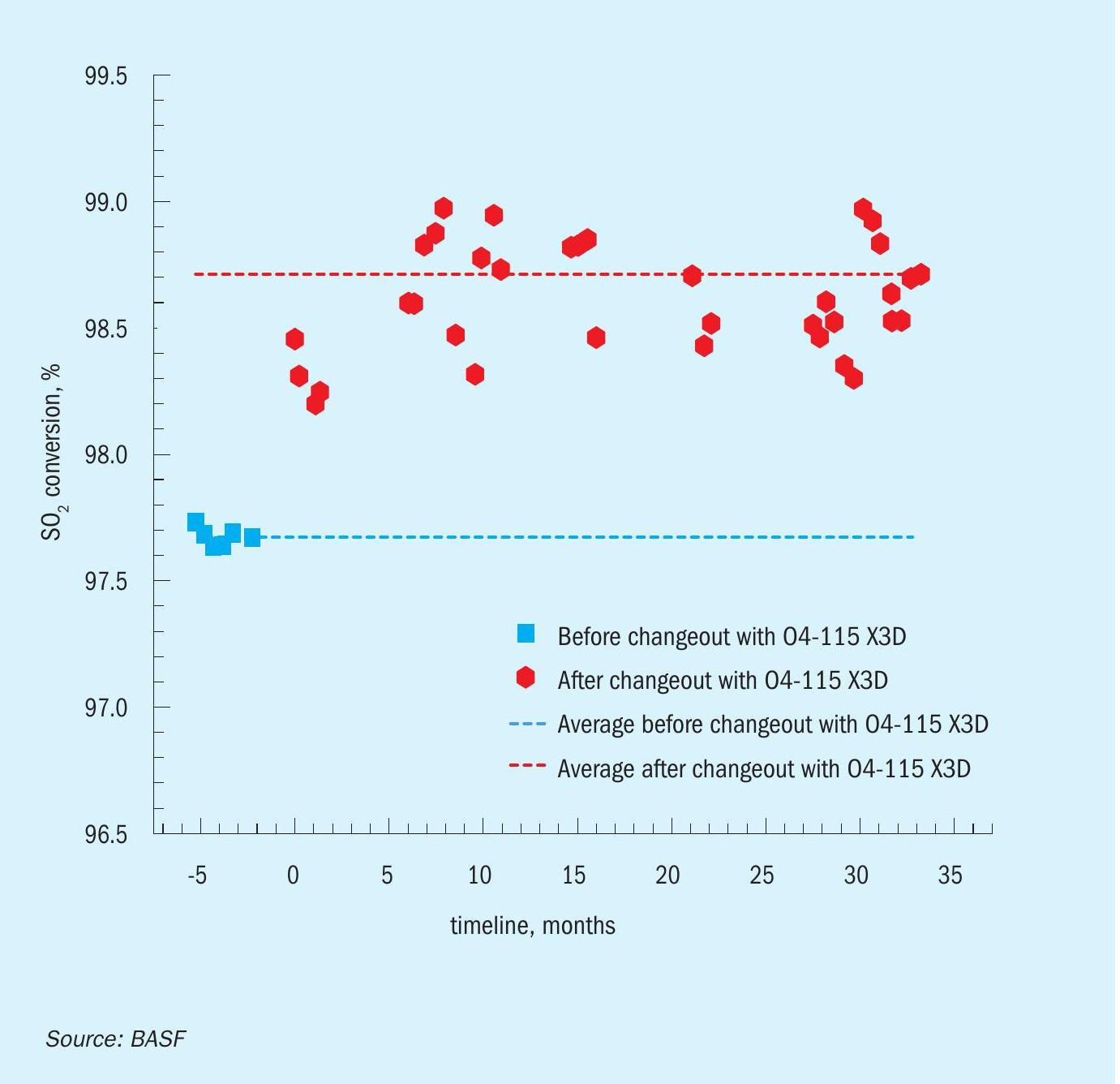
In summary the key benefits of the commercial reference at BASF are:
- 74% decrease in pressure drop in bed 3;
- 35% decrease in total pressure drop;
- 6% decrease in energy costs;
- 1.3% increase in SO2 conversion;
- at least 20% decrease in consumption of NaOH 50% solution.
Conclusion and next steps
Table 5 shows how X3D™ can help with common customer issue.
Through continuous improvement, BASF has met its goal of producing a step change in catalyst activity and pressure drop decrease. The use of 3D-printing technology to produce a commodity catalyst, such as sulphuric acid catalyst, was not regarded as economically worthwhile before. However, with the introduction of the X3D™ catalyst technology, BASF has displayed the benefits in a commercial unit and the cost savings for the customer when the catalyst is employed. The outstanding results obtained from the first reference plant from 2019 onwards has already led to two further implementations of X3D™ catalysts in commercial converter units.
Furthermore, the X3D™ catalyst can be used to meet a variety of needs of a sulphuric acid producer. Due to the flexibility in catalyst design, the catalyst shape geometry can be custom tuned and manufactured to precisely meet the desired requirements. This will not only lead to better performing sulphuric acid units, but opens up the way for new converter designs in future, providing a higher efficiency and a decreased environmental impact.
References
Acknowledgement
The authors would like to thank Hakan Uener, Carlo Masia, Fred Borninkhof, Till Blum and Mauricio Grobys for their support during the realisation of this project.