Sulphur 406 May-Jun 2023
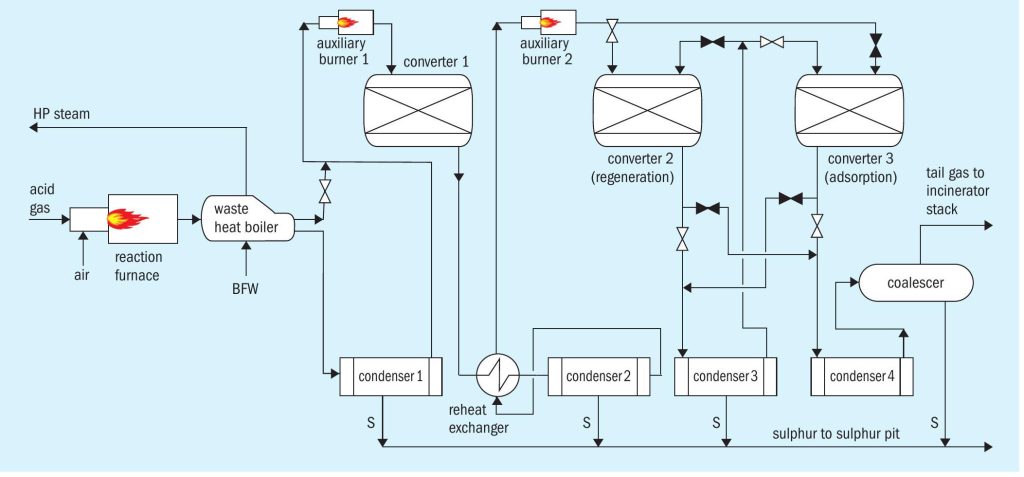
31 May 2023
Another lesson from an SRU shutdown
SRU TROUBLESHOOTING
Another lesson from an SRU shutdown
Inshan S Mohammed of Sulfur Recovery Engineering shares the lessons learned from an emergency shutdown of an MCRC sulphur recovery unit in the middle of a cold Canadian winter where temperatures can be -30°C.
Sulphur recovery units (SRUs) are designed to meet a specific set of targets given an initial set of premises such as feed flowrates, feed compositions, and environmental regulations. During the design phase, considerations are generally given to different scenarios such as varying feed quality and feed rate (turndown), as well as equipment aging and catalyst aging to help with the robustness of the design. However, start-ups and shutdowns arguably cause the most damage to an SRU through the thermal cycling of the process equipment. For facilities with poor reliability, these frequent events lead to unplanned, emergency shutdowns. This article highlights the success story of a Canadian gas plant operator surviving an emergency shutdown in the dead of winter.
A good SRU shutdown commonly involves three main steps: the fuel gas sweep of the catalyst, the controlled burn of any residual sulphur, and the cool down of the unit to ambient conditions. First, increasing the volumetric flow until limited by the available fuel gas, main combustion air blower or tempering steam ensures all of the sulphur remaining in the catalyst pores are pushed through to the downstream condenser. Second, once all sulphur rundowns are clear, then the controlled burn stage is implemented through the gradual increase of residual oxygen. Whereas in the first step the amount of oxygen is kept below 1,000 ppmv, in the controlled burn the oxygen is increased to percentage-levels while keeping an eye on emissions. Last, the cool down of the SRU to ambient conditions is completed by running blower air or via the use of nitrogen.
An emergency shutdown is any unplanned interruption of the operation of the SRU. Disruptions can be from external sources from the operating facility, such as inclement weather resulting in power loss, or internal sources, such as equipment failure.
The Main Claus Recovery Concept (MCRC) is a sub-dewpoint process by which the Claus reaction is extended to the point where the sulphur is condensing onto the catalyst. Sulphur recoveries can be extended beyond 99% of the inlet sulphur with the right configuration and design. The first converter follows the conventional mixed bed of titania catalyst, topped with a sacrificial layer of alumina catalyst. The last beds alternate between sub-dewpoint mode and regeneration mode. When the catalyst has completed its adsorption, the converter beds switch positions and then the subdewpoint bed is subjected to the hot regenerative temperature. The Canadian operator in this case study operated a 3-converter MCRC unit with a capacity of approximately 85 t/d and with acid gas direct-fired reheat methods as illustrated in Fig. 1
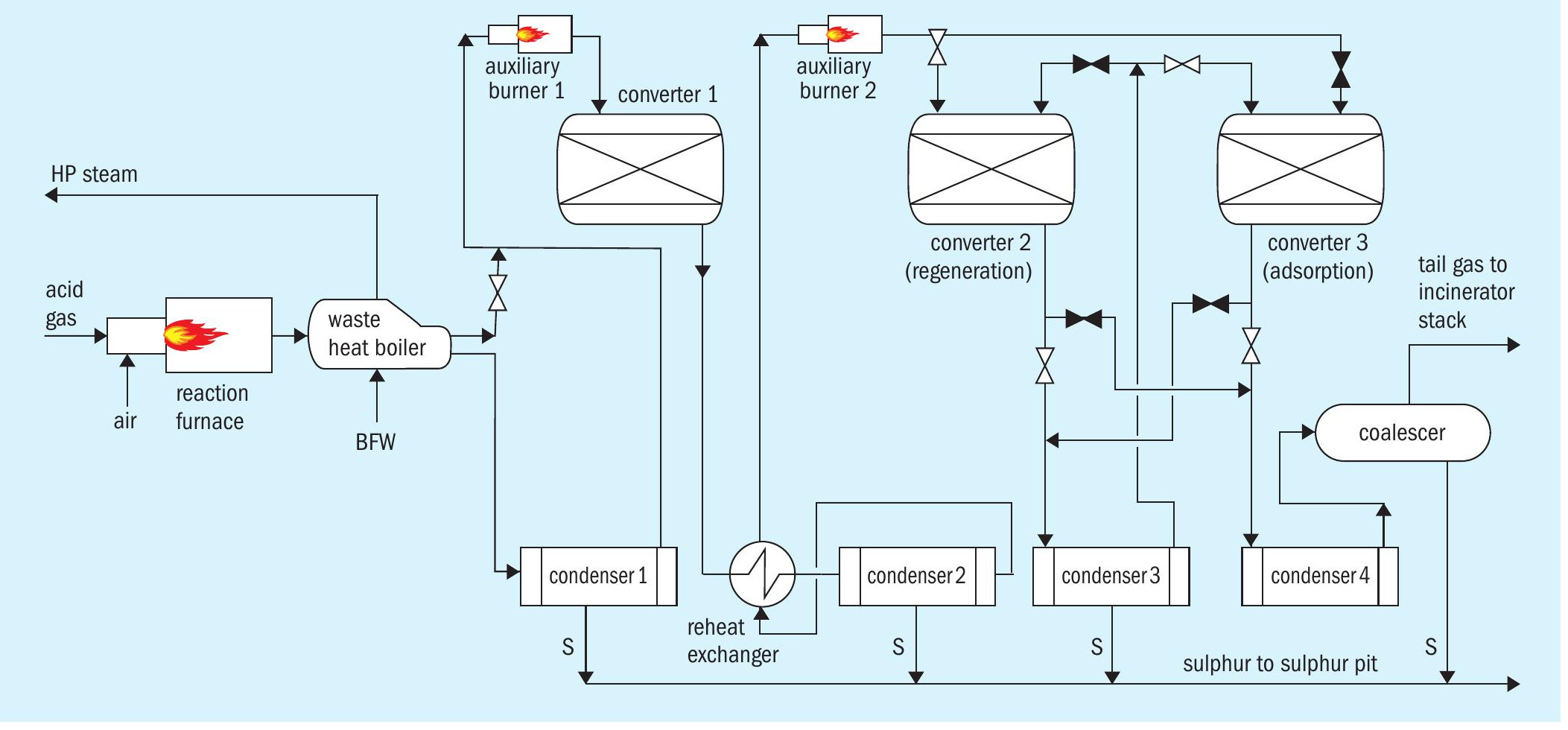
Discovery of the issue
Sulfur Recovery Engineering (SRE) was contacted after the discovery of a tubesheet failure within the waste heat boiler (WHB). Shutdown assistance was requested to ensure safe access for inspection and repair of the thermal reactor and the WHB, and to also ensure that the other unit operations (condensers, reheaters, converters, etc.) were free of elemental sulphur. There was no easy path forward for an unplanned outage in the middle of a Canadian winter.
With the tubesheet failure being found the day prior, the first day on site was kicked-off with a meeting where SRE was tasked with finding a way to manage (1) the sulphur still loaded within the MCRC converters and (2) accessing the reaction furnace and WHB for repair. The path forward was to start-up the auxiliary burners on fuel gas and use the flow from them to heat the downstream converter, switching between converter 2 and converter 3 as required. SRE was tasked with measuring the residual oxygen, the formation of soot, and the pressure at the outlet of both reheaters as well as checking for liquid sulphur flow from each of the sulphur rundowns. The thought process was to establish some flow through the unit in order to ensure communication and channelling should the sulphur solidify due to heat losses.
The next day, the thermal reactor and the WHB were blinded off from the rest of the process in preparation for the inspection work. Meanwhile, maintaining a flame in either auxiliary burner was impossible without some process gas to dissipate the heat produced by the flame. The auxiliary burners constantly tripped on high temperature. A nitrogen truck was brought in to provide this motive gas and was connected to the condenser 1 outlet sample point with an initial flow of 6 m3 /min at a temperature of 40°C.
By the third day, the nitrogen flow was increased to 10 m3 /min and the auxiliary burners were running steady. The rates of fuel gas were approximately one half of those from the previous shutdowns, which was understandable given the lack of frontend flue gas from the main burner. What was also apparent were the mixed values from the residual gas analysis and from the oxygen analyser. Here, the gas results illustrated the incomplete burn with residual methane (C1) and carbon monoxide (CO) and the analyser illustrated a percentage level amount of oxygen. There are several plausible explanations for the difference:
- vacuum condition of the process gas; l poor mixing within the auxiliar burner;
- low flow through auxiliar burner;
- lag-time between collection of the gas sample and measurement via the analyser.
Regardless of the reason, this discrepancy highlighted the need for continuous monitoring of the combustion via the various methods (analyser, gas analysis and local pressure) to ensure that the converters do not plug off. Nonetheless, there was a good amount of flow going through the two MCRC converters and the crisis of the emergency shutdown was in a manageable state.
New findings
Now five days into the emergency support, the plan was to continue to operate the modified fuel gas sweep until the repair of the leak was completed. Throughout this time, and in addition to the log items above, SRE was tasked with recording the converter temperatures (Figs. 2 and 3). Assistance was also given to ensure (1) that the process gas temperature to the MCRC converters was adequate, (2) that the condensers were outside of sulphuric acid attack, and (3) that the MCRC converters were switched at an appropriate time. The works for repairing the tubesheet and for fixing the castable refractory was estimated to be completed by the following week.
Flow of liquid sulphur from condenser 2 (sulphur within converter 1) started flow on day 5. The trickling flow was constant until day 10, when the rundown dried out. A total of five days.
The modified-fuel gas sweep of the MCRC converters and SRE’s onsite support continued through to end of day shift on day 13. During the last remaining two days, the fuel gas to air ratios for the auxiliary burners were increased to expose the downstream converters 2 and 3 to more oxygen; mimicking the controlled burn step of a typical SRU shutdown. As no sulphur fires or excessive sulphur dioxide emissions were observed, the exercise of safely shutting down the SRU without the use of the main burner was achieved.
Next steps
The Canadian operator is now tasked with completing the repairs on the WHB. Unfortunately, the number of tubes with leaks has steadily increased as each repair attempt was made and hydrotesting of the unit was completed. Once the unit is cleared to be back in service, SRE plans to assist with the safe start-up of the unit.
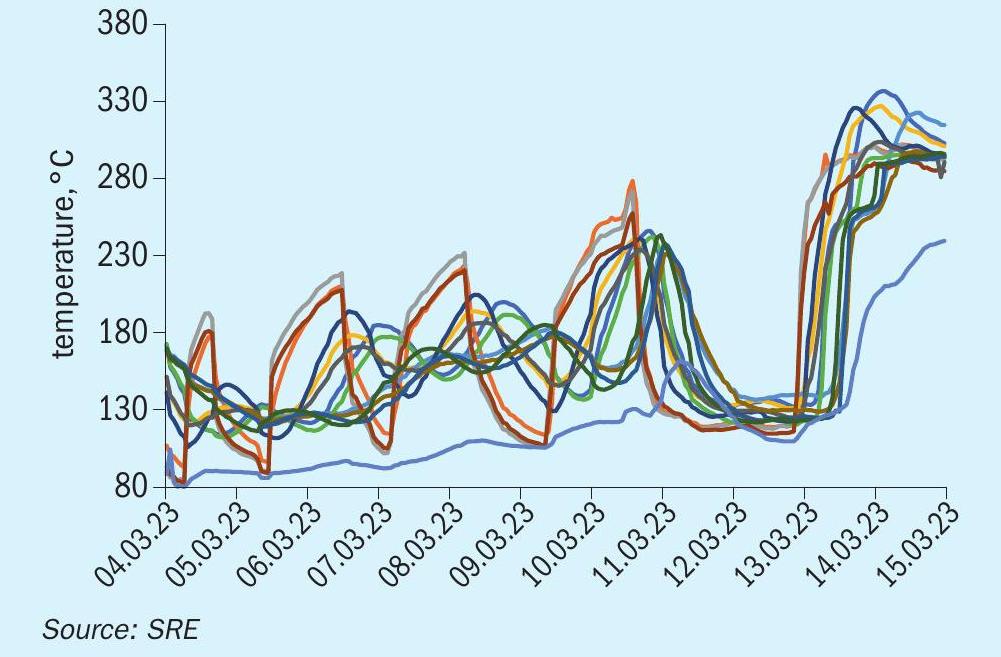
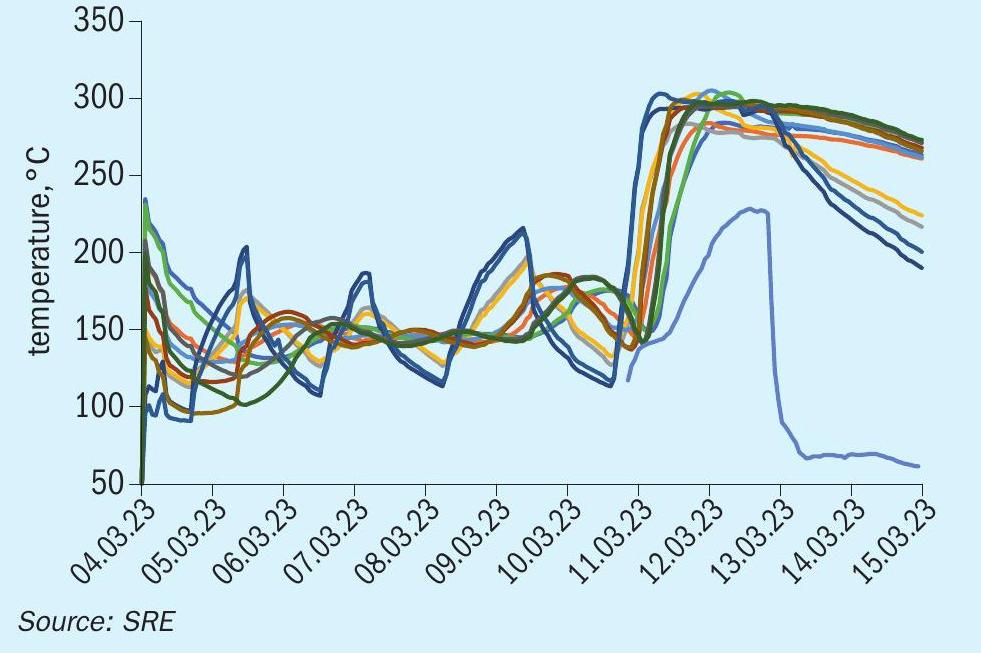