Nitrogen+Syngas 383 May-Jun 2023
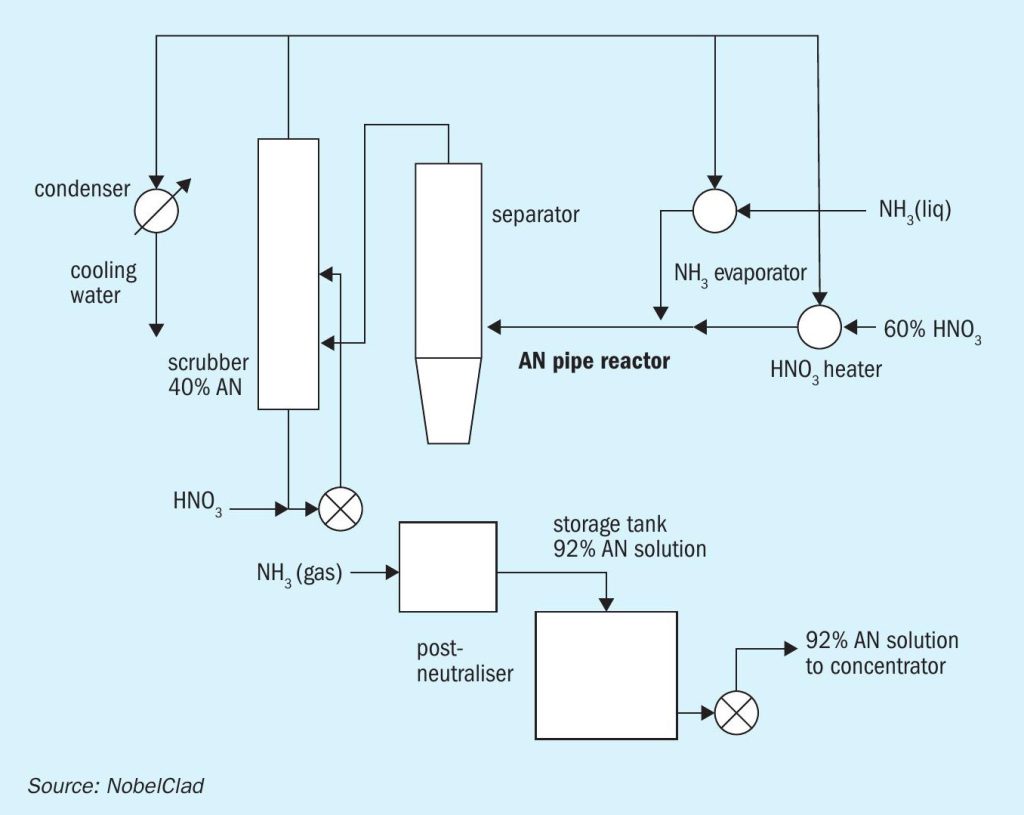
31 May 2023
Improving the lifetime of AN pipe reactors
AMMONIUM NITRATE
Improving the lifetime of AN pipe reactors
Pipe reactors in ammonium nitrate plants suffer from short lifetimes due to serious corrosion and erosion issues. A new solution from NobelClad could provide a unique opportunity to address the problem faced by licensors and end-users in the pipe reactors of ammonium nitrate plants. The NobelClad solution provides higher safety and reliability standards and less downtime and maintenance leading to an attractive payback time.
Often seen in the production of inorganic fertilizers, a pipe reactor is an acid-base reaction vessel that uses reaction heat as the primary method of drying. This process reduces the burden on the dryer and can significantly decrease plant energy costs.
The pipe reactor accepts phosphoric acid, sulphuric acid or nitric acid in one side of the pipe, and gaseous or liquid ammonia is sparged into the reaction chamber. This results in either ammoniated phosphate, sulphate or nitrate, a hot “melt” of superheated product1 . The contained heat of the reaction contributes to the heat requirement for moisture removal of the granulated material. This reduces the dryer fuel requirements for the plant.
Pipe reactors are popular equipment items in several ammonium nitrate (AN) process technologies. Ammonia gas reacts with heated nitric acid releasing heat which evaporates a significant part of the water fraction leading to a concentrated ammonium nitrate solution. Fig. 1 shows the flow scheme of the Grande Paroisse (now Casale) AN process.
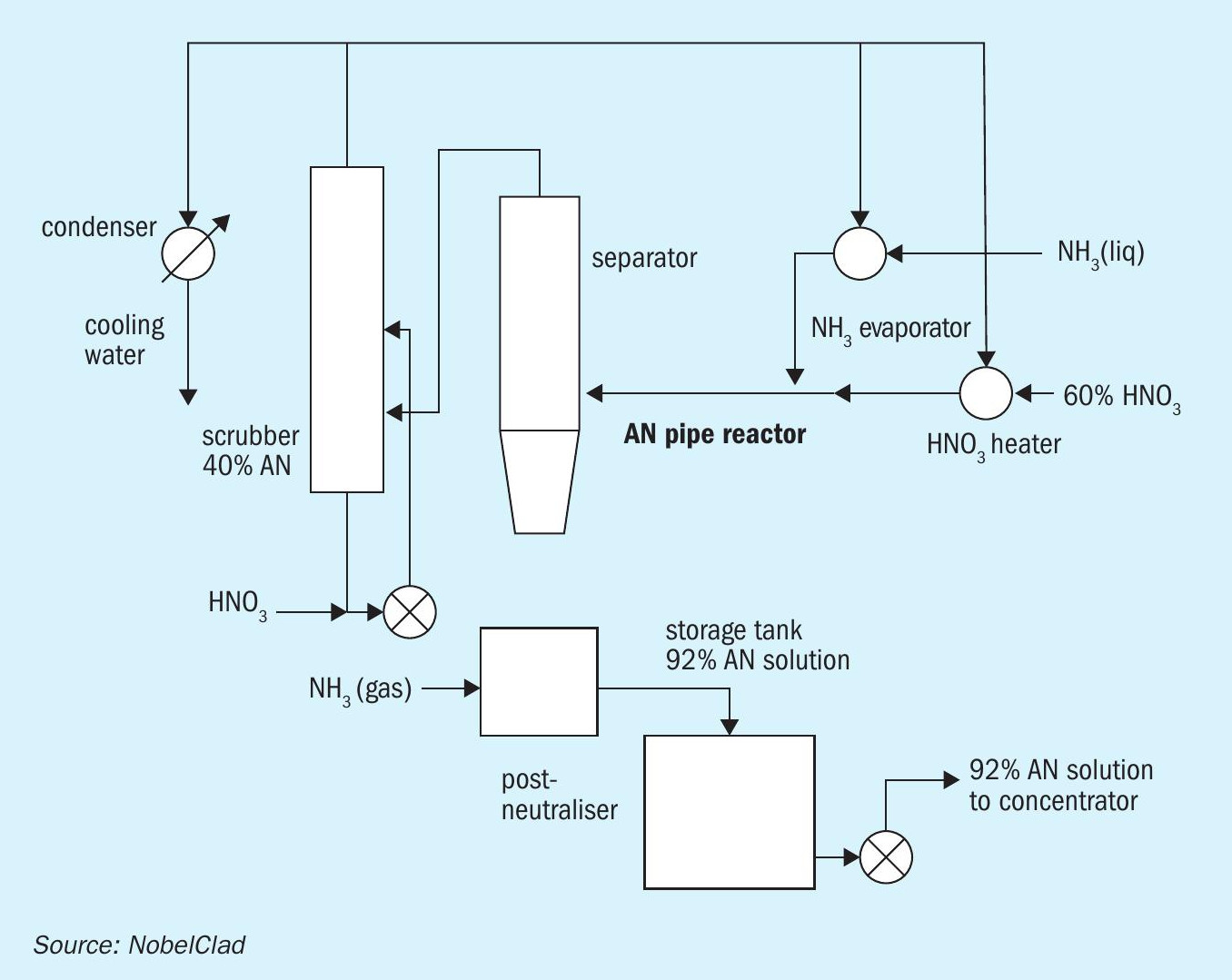
The ammonia flow rate is measured in the liquid phase and then the ammonia is vaporised and superheated up to 90°C. Heat is provided by the condensation from process steam generated by the neutralisation reaction. Hot gaseous ammonia is fed into the pipe reactor.
The nitric acid flow rate is measured and controlled through ratio control related to the ammonia flow. Nitric acid is heated in a heat exchanger fed with process steam to increase the ammonium nitrate concentration.
The instantaneous reaction starts as soon as nitric acid and ammonia are mixed and goes on all along the pipe reactor. Pressure decreases from the reactor head (4~7 abs. bar) to the separator tank (~1 abs. bar). At the pipe reactor outlet, the ammonium nitrate solution (ANS) and process steam are split in a separator.
The ANS flows by gravity from the separator tank into the buffer tank where a small flow of gaseous ammonia is fed to automatically adjust the pH of the solution.
Pipe reactor issues
A main advantage of a pipe reactor is its operating flexibility, it can be operated over a wide capacity range. For example, the pipe reactor in Fig. 2 was designed for a capacity of 1,650 t/d and has been operating within a range of 700 and 2,000 t/d. This range is achieved by one single pipe reactor (DN 200 mm – length 9 m).
However, in the stainless steel 304L pipe reactor, corrosion at a rate of approx. 12 mm/year takes place in a zone of approximately one metre in length, close to the nitric acid inlet.
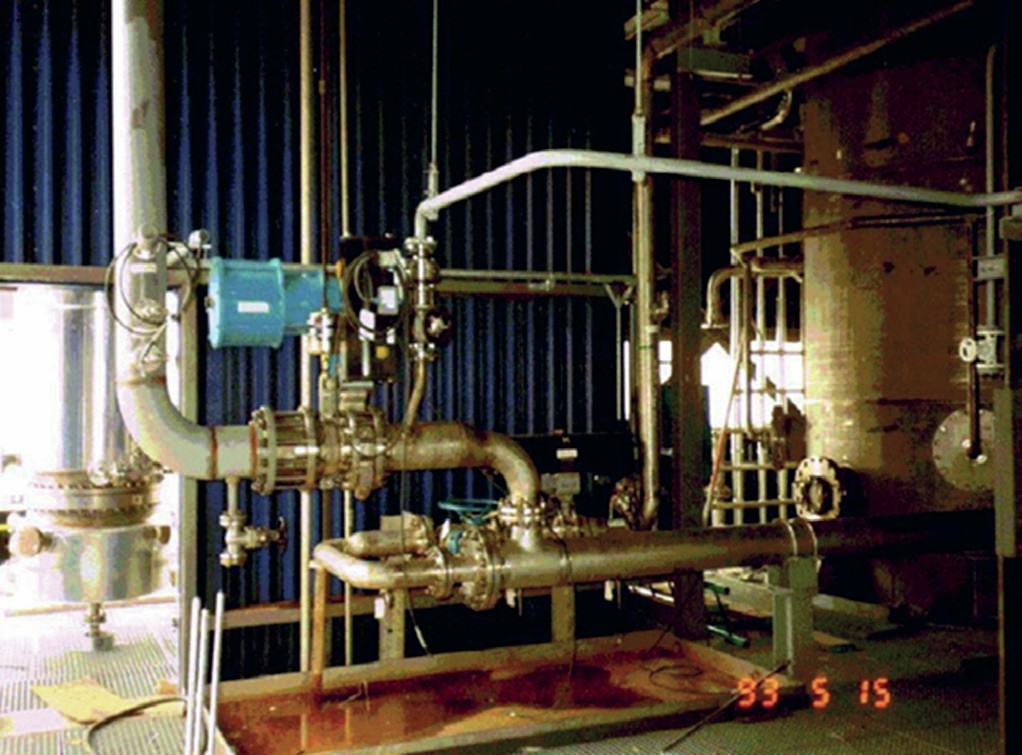
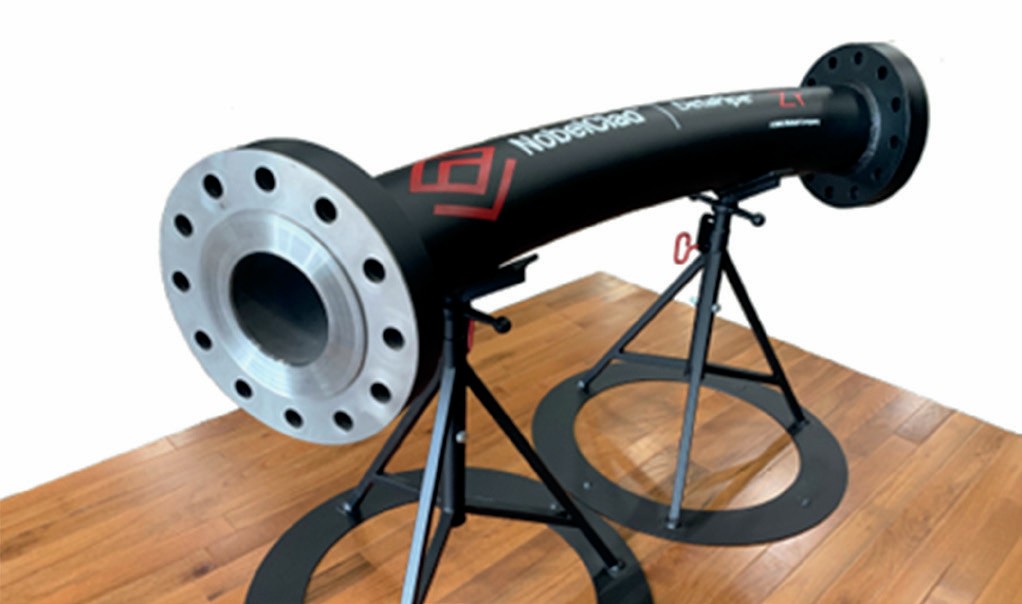
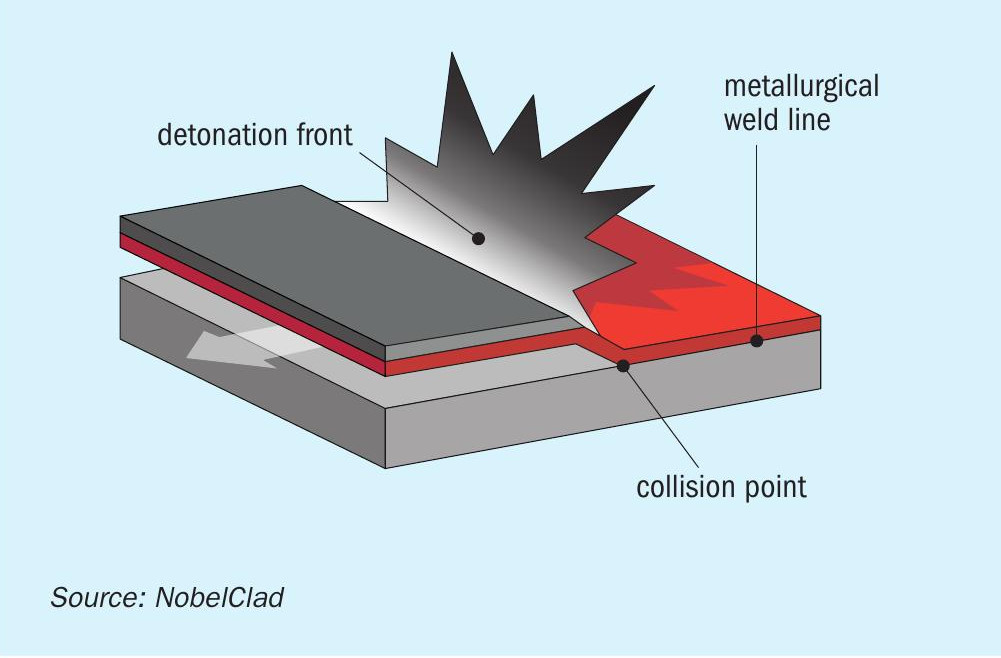
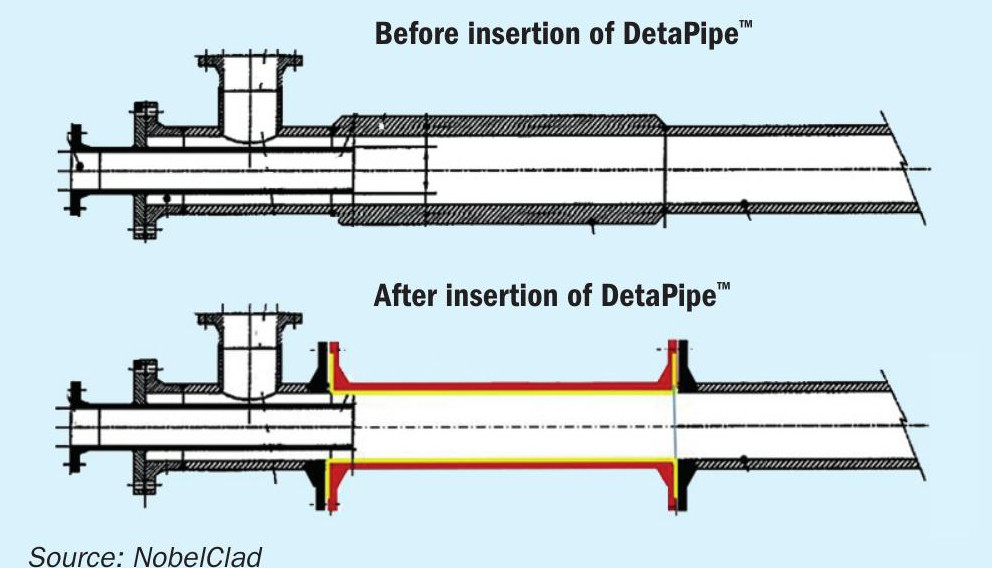
Besides possible erosion phenomena, the following corrosion mechanism is likely to happen in this turbulent environment: The already heated nitric acid plus the exothermic heat developed from the reaction between ammonia and nitric acid creates alternating wet-dry zones (condensation and re-evaporation).
The anodic reaction is:
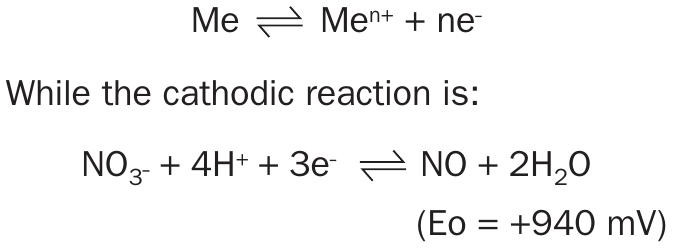
In these alternating wet-dry zones, dichromic acid will be formed and the above cathodic nitrate reduction reaction will be overruled by:

The higher equilibrium potential of this redox reaction will shift the corrosion potential further in the trans-passive area of the polarisation curve leading to high corrosion rates of stainless steels.
With the target of better corrosion resistance, titanium has been used for these pipe reactors. A passive layer of titanium oxide provides corrosion resistance. However, if this protective layer is broken, the exposed metal surface will oxidise, and the resulting combustion process can be highly exothermic. Therefore, care is needed when considering titanium for this application. To establish the safety of using titanium for nitric acid spargers, appropriate testing or assessment has been carried out by several companies, but details of such work do not seem to be available in the open literature for nitric acid reactions. Special care is advisable when urea off gases are used as a source of ammonia. The presence of contamination with incompatible substances such as iron should be avoided2 . Besides the above-mentioned safety risks, titanium pipe reactors also show a limited lifetime of six months maximum as the corrosion resistance of titanium in nitric acid concentrations is limited to 40-60%3 .
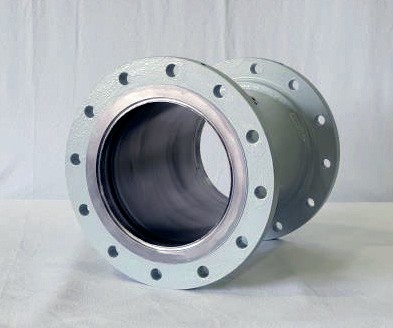
Solutions
Grande Paroisse has operating experience of more than five years in two of its own plants (now owned by Agrofert, earlier Borealis). In these plants, the corrosion zone of the pipe reactor is made of SS 304L, but is also fitted with an internal lining. Those pipe reactors can operate for more than two years without any corrosion issues.
In the DSM-Agro (now OCI) plant, it is preferred to maintain the equipment as simply as possible, and every six months the pipe reactor is changed and repaired.
NobelClad, a DMC Global Company, headquartered in Colorado, has been approached by some end-users looking for a better solution. NobelClad is an industry leader in explosion welding (EXW), commonly called explosion cladding, which is a solid-state welding technology for the manufacture of large clad metal plates, which are sold under its trademark DetaClad™ . The technology was discovered around 1960. Explosion clad products are used extensively, worldwide in the manufacture of corrosion-resistant process equipment as well as other bi-metallic applications. The cladding metal alloy can be selected for optimum corrosion performance. The base metal alloy can be specified to optimise strength, fabricability, and cost. The high strength, durable explosion weld allows for the construction of chemical process industry equipment exhibiting the beneficial features of both4 .
Fig. 3 shows the general arrangement of the plates during the welding process. The distance of the gap is one of the crucial elements in explosion welding, helping to determine the angle of impact, the velocity of impact, and the consistency of the jet5 . DetaClad™ has been extensively used in fertilizer and chemical plants (such as urea, nitric acid, purified terephthalic acid, acetic acid, polycarbonate, and chlor-alkali to name a few), as well as refinery, LNG, geothermal, and nuclear applications.
NobelClad has recently launched a revolutionary reactive clad metal product known as DetaPipe™ . It is a mechanically clad pipe product. DetaPipe™ will be manufactured to B31.3 specifications which will assist the piping engineer when designing a piping system. Considering this is mechanically clad, NobelClad performs gripping force tests, like oil and gas industry standard API 5L. In addition, test spools have been tested at 200 bar and 225°C.
Fig. 4 shows DetaPipe™ Zr, a pipe spool clad with zirconium. The pipe spool, from flange face to flange face, is fully clad with zirconium inside carbon steel. This pipe spool can also be clad with titanium. DetaPipe™ can be fabricated with either ANSI flanges, compact flanges, or seal ring hubs. DetaPipe™ is currently being offered in straight lengths up to 9 m and elbows.
NobelClad can produce pipe spools currently from 6 inch to 30 inch NPS, however flexibility exists to downsize or upsize these dimensions by a few inches depending on the application and business viability.
To solve the corrosion issues in the earlier discussed pipe reactor, NobelClad proposed using a DetaPipe™ Zr spool along with flange faces made with DetaClad™ Zr. NobelClad can produce the entire length of the pipe reactor with Zr mechanical cladding, however, considering the cost benefits, the solution proposed included replacing only the section subject to maximum corrosion and erosion. Of all the corrosion-resistant metals, zirconium or tantalum are highly resistant to all forms of corrosion which include crevice corrosion6 . The NobelClad solution for pipe reactors in AN plants reduces flange connections by providing a single construction piece (Fig. 5).
Recently, NobelClad installed a tantalum test spool for a chlor-alkali application (Fig. 6) and is further working to develop tees and reducers.
Conclusions
Pipe reactors in ammonium nitrate plants suffer from short lifetimes due to serious corrosion and erosion issues. NobelClad’s DetaPipe™ coupled with its highly used and recommended DetaClad™ solution could provide a unique opportunity to address the problem faced by licensors and end-users in the pipe-reactors of ammonium-nitrate plants.
NobelClad’s DetaPipe™ provides new opportunities for mining, fertilizer and other chemical applications. End users and licensors are encouraged to contact NobleClad to jointly test sample spools for critical applications.
References