Nitrogen+Syngas 384 Jul-Aug 2023
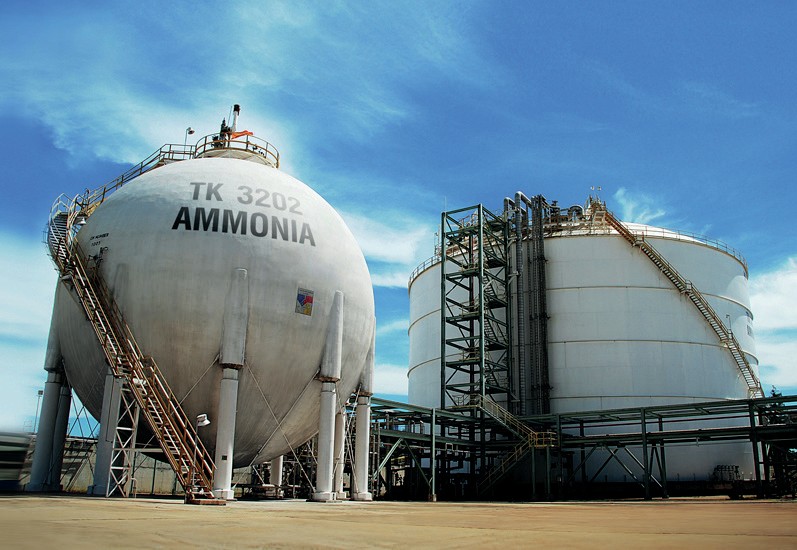
31 July 2023
Ammonia industry accidents
AMMONIA SAFETY
Ammonia industry accidents
A look at fatal incidents in the ammonia industry over the past two decades.
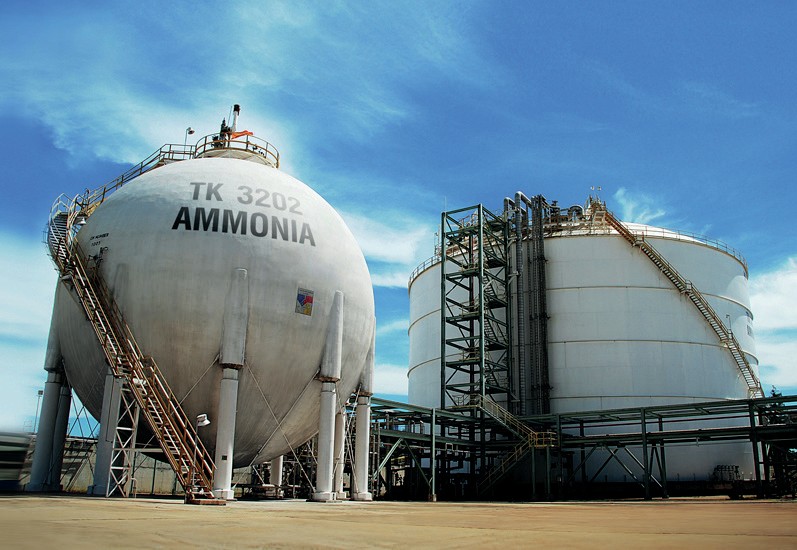
Ammonia is one of the most widely used chemicals in the world, second only to sulphuric acid in terms of number of tonnes produced per year; 185 million t/a in 2021 according to the International Fertilizer Association (IFA). However, while sulphuric acid is dangerously corrosive, it is a liquid at room temperature and pressure, whereas ammonia must be pressurised and/or refrigerated to liquefy it and make it easier to store and handle. It is also relatively toxic by inhalation. Ammonia vapours disperse quickly when released and forms dense ammonia/air clouds. Although ammonia gas can be safely vented to atmosphere during emergency situations the discharge point must be sufficiently high to prevent downwind plume hitting the ground at high concentrations. As a gas, ammonia irritates and burns the skin, eyes, and respiratory tract. Liquified gas can cause the skin to freeze, as well as permanent damage or blindness to the eyes. Inhalation of ammonia can cause severe irritation of the nose and throat, and life-threatening accumulation of fluid in the lungs (pulmonary oedema). Overall, the main recorded causes of fatalities and injuries during ammonia incidents is either inhalation or burns1 .
Perhaps for this reason, a significant proportion of industrial accidents involving chemicals are related to ammonia releases. Between 2007 and 2017, the US Environmental Protection Agency (EPA) reported that 72% of all chemical accidents in the Mid-west region were ammonia-related. Ammonia is used in a wide variety of industries, from manufacturing (production of plastics, fibres, and other chemicals), agriculture (as a fertilizer), and in the consumer sector as a food additive, cleaning agent, or refrigerant.
Ammonia refrigeration
While 80% of ammonia is used in fertilizer manufacturing, and only 2% in refrigeration systems, the majority of releases and accidents, in fact, occur when ammonia is used as a refrigerant. After the Kigali Amendment to the Montreal Protocol came into effect, many countries have begun exploring new refrigeration alternatives to reduce damage to the ozone layer and mitigate global warming. Due to technical and cost constraints, the use of ammonia as a refrigerant is widespread in industrial refrigeration, especially in large and medium-sized cold storage. This means ammonia is often close to less skilled or trained personnel, and monitoring of corrosion or other mechanical defects may be less thorough than at an ammonia manufacturing facility.
A 2019 survey of ammonia refrigeration incidents over the preceding two decades1 highlighted the following cases:
On 23rd August 2010, a catastrophic failure of a 12-inch suction pipe on a roof lead to a release of more than 14 tonnes of anhydrous ammonia in Millard Refrigerated Services in Theodore, Alabama. The pressure developed due to hydraulic shock also ruptured the evaporator coil inside the facility. The ammonia cloud travelled 0.25 miles across the river near the plant and affected workers and crew members on ships docked at Millard. One Millard employee lost consciousness and was injured. Nine crew members and 143 offsite contractors reported exposure. The cause was operator error in interrupting a defrost cycle during a restart after a power failure. The evaporator switched directly from defrost mode into refrigeration mode without bleeding hot gas from the evaporator coil, allowing low temperature liquid and hot gas to mix in the same pipe, causing the hot gas void to collapse as it rapidly condensed to liquid. This created pressure shock and ruptured the piping and evaporator coil.
The US Chemical Safety Board, which investigated the Millard incident, commented in its report: “We are seeing too many ammonia releases in our daily incident reviews. Though many are ‘small’ releases, a high consequence accident that causes multiple injuries to members of the public is a serious one that warrants our examination. Our team will be examining the events that led to the release and ways that the community can be better protected in the future.”
On August 31st, 2013, a leak of liquid ammonia at a refrigeration unit of plant in Weng’s cold storage Industrial Company in Shanghai killed 15 people and injured 25. Residents up to 15 km downwind in the Zhabei district reported the smell of ammonia. The cause of the accident appeared to be a pipe or valve failure.
On July 7, 2017, a faulty quarter inch valve caused an ammonia leak at Grecian Delight food processing plant in Elk Grove Village which led to an explosion. Ammonia under 150 psi pressure leaked into an 80 x 40-feet room with 20-feet ceiling and a spark led to ignition of the ammonia leading to a blast which ruptured the aluminium facade on the building and hospitalised two workers.
On August 16, 2011, an ammonia leak at the Pilgrim’s Pride Plant in Guntersville caused a fire and explosion. The fire was put out within 45 minutes and there were no reported fatalities, but the explosion damaged the plant.
Kamloops incident
Technical Safety BC has recently reported on an accident which occurred on May 26, 2022, when a crew was in the process of cutting up and disassembling two ammonia refrigeration systems at Arctic Glacier Inc. in the Mount Paul Industrial Park in Kamloops, British Columbia. Those present understood that ammonia had been previously removed from both systems. During the removal of a section of the system a valve handle was turned, resulting in a large release of ammonia. The individual
who turned the handle was sprayed by the ammonia and moved further into the building. The remaining members of the crew evacuated through a nearby open bay door. The individual who opened the valve was extracted from the building and pronounced dead following the incident. In addition to the fatality, there were multiple ammonia exposures, and a local evacuation.
The investigation found that the failure to remove ammonia from the refrigeration system prior to, or during disassembly was the primary cause of the incident. This was influenced by changes in personnel and their assigned responsibilities and misunderstood communications regarding the work completed. The investigation found that, given the magnitude of the release, a properly functioning ventilation system would not have prevented ammonia concentrations from reaching explosive limits; however, it likely would have lessened the amount of time that the ammonia concentration was combustible and therefore reduced the risk of explosion.
China
Another recent report examines ammonia incidents in the food processing industry in China2 , There were 82 ammonia refrigeration-related accidents in China from 2010 to 2020, resulting in 189 deaths and 1081 injuries (including poisoning). The breakdown of causes was found to be: human error 20.7%; equipment failure 67.1%; material deficiencies 7.3%; external factors 4.9%. Human factors mainly included improper or even illegal operation of facilities. Material factors were defective welding materials, cracked welds, unqualified insulation materials, broken blind bolts, aging flanges, corroded/aging gaskets, and detached pipe caps, with six cases accounting for 7.3% of all accidents. Equipment failures mainly related to ageing compressors and pipes, ruptured tanks and pipes, and loose, rusted, leaking or poorly sealed valves, accounting for 67.1% of total accidents. External causes were mainly due to the presence of open flames, abnormal changes in external temperature, and short-circuiting of wiring, with four cases accounting for 4.9% of all accidents.
Ammonia manufacturing incidents
Ammonia production occurs at high temperatures and pressures. As a result safety is a constant concern and for that reason most operators have comprehensive safety and maintenance regimens which make accidents rare. Potential causes of accidents include catalyst degradation/catalyst tube rupture, runaway reactions, corrosion in reformers, and potential releases from pipes or cracks. Failures can occur in process equipment, machines, control systems that can lead to an accident. Ammonia explosions are rare as the lower explosion limit of ammonia is high (LEL: 16% and HEL: 25%). The auto ignition temperature is 650°C, so ammonia is difficult to ignite. The most common accidents are leaks, with the most important aspect for minimisation of risk being prompt action to shut down the compressor.
Recent ammonia manufacturing incidents have included:
On June 14, 2013, an accident happened at the CF Industries site at Donaldsonville, Louisiana. There was a fire and explosion in one of the four ammonia plants, resulting in one fatality and injuring at least ten people. The fire was brought down in under half an hour and the plant was immediately shut down. Upon investigation it was found that the unit was shut down for maintenance and the workers were pumping nitrogen into a storage vessel. The accident occurred due to overpressure, causing the vessel to rupture.
On December 7, 2015, an accidental ammonia leak caused a fatality and injuries to personnel at Medicine Hat, Alberta. Two contractors were working to weatherproof a large ammonia storage tank and the leak happened when a piece of equipment accidentally struck the tank’s valve, releasing ammonia. Both the workers were taken to the hospital but unfortunately one of them died.
On August 16, 2016, an ammonia leak at Petronas chemical facility in Malaysia resulted in two fatalities and three injuries. The leak happened when workers were doing maintenance and were exposed to ammonia from a leaking pipeline. The cause of accident was pipeline failure but the protective equipment could have minimised risk to the workers.
On August 22rd 2016 an ammonia tank collapsed at the Di-Ammonium Phosphate Fertilizer Company Ltd. The 500 tonne tank was half full at the time. A cloud of ammonia affected residents in the vicinity, leading to nearly 200 requiring treatment and 56 hospitalised, though fortunately without fatality due to favourable winds. An investigation found that pressure gauges in the tank and the reserve tank were inoperative at the time, and the condenser, safety valves and pressure vent were also out of order. The tank was also being operated by employees who were not trained for the job.
In 2019, an ammonia tank explosion at a fertilizer facility at Ain Sokhna, Egypt killed 10 workers and critically injured two others, reportedly when the tank failed during a nitrogen purge.
Conclusions
The biggest risk in ammonia operations is leaks from equipment damaged during operations, or subject to improper operation, especially if poor maintenance has led to corrosion and weakening of structures. Though this can become explosive if it encounters an ignition source, the biggest risk is from ammonia inhalation during a release at high pressure. Leaks can be due to valve plugging or valve malfunction; defects in shaft seals, pipe flanges and valve stems; pipe failures due to corrosion, mechanical damage or vibration; and tank material failure. Engineering controls and proper maintenance regimes, proper training, and the provision of proper protective equipment are essential. The US EPA estimates that 95% of ammonia incidents can be avoided through better operator training, improved procedures, and enhanced communication of incidents and near-misses.
References