Nitrogen+Syngas 384 Jul-Aug 2023
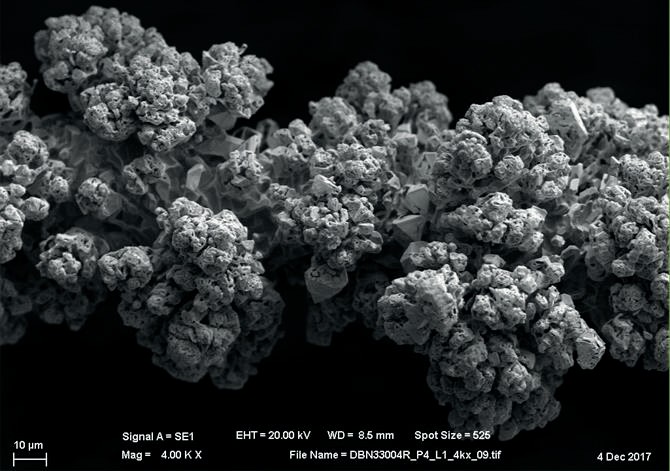
31 July 2023
Balancing cost and performance
NITRIC ACID PRODUCTION
Balancing cost and performance
Although the nitric acid industry has an extensive history dating back centuries, nitric acid production continues to be a dynamic process with bespoke system solutions necessary per plant rather than a one size fits all. Kate Cardonne of Johnson Matthey discusses strategies to balance the cost and performance in nitric acid production.
When looking at the economic challenges of nitric acid production, it is necessary to create a holistic picture of the factors feeding into the economic value of the catalyst. While one alloy may be favoured due to its extremely high conversion efficiency, it may be uneconomical due to the short lifespan of the catalyst or amount of metal lost over the course of the campaign1 . These factors coupled with the everchanging platinum group metal (PGM) market conditions are key to determining the best bespoke solution for each plant based on their operating strategy.
When designing a plant, there is an upfront decision to be made regarding the range of operating pressure, which impacts the upfront capital expenditure. This choice is guided by the cost of feedstock and energy where the plant is being built. Medium and low-pressure plants are popular in regions like Europe where feedstock and energy prices are very high, as their design maximises yield and energy efficiency and thus minimises these raw material needs. The higher initial costs are acceptable as the plant’s profitability will eventually offset and exceed the starting investment due to a greater production capacity and higher conversion efficiency while keeping operating costs low and requiring fewer changeouts. A high-pressure plant is advantageous in areas where feedstock and energy prices are low like North America because the raw material prices aren’t as constraining on design, allowing for a simpler process design with lower associated upfront investment costs. The balance comes with more frequent operational costs; as high-pressure plants have a lower conversion efficiency and thus shorter gauze campaign lengths, there are smaller production totals per campaign and more frequent changeouts. The lower cost barrier to entry warrants an opportunity for high-pressure plants to become profitable quickly2,3 . Once the decision regarding plant design is set, the resulting parameters influence the gauze catalyst design.
The fundamentals of catalyst design have not changed significantly in over 100 years, considering variables such as fluctuating precious metal prices, meaning that there is a deep understanding available when presented with these constraints to generate favourable design options. In parallel with these external factors, decisions to tailor catalyst design such as extending campaign length, improving efficiency, optimising installed PGM content or reducing N2 O emissions all present as potential solutions to these challenges.
Understanding reaction constraints
The production of nitric acid is intrinsically limited by the reaction kinetics of the ammonia oxidation process with three main products forming upon ammonia reacting with oxygen: nitric oxide (NO), nitrogen (N2 ) and nitrous oxide (N2 O). Based on typical plant operating conditions of temperatures ranging from 850–930°C and pressure ranging from atmospheric to approximately 200 psi, selectivity to nitric oxide can be 90-97% (equations 1-3).

The goal is to manipulate the operational conditions, as well as the catalyst design, to maximise the selectivity towards NO while minimising the unwanted byproducts. Depending on the reaction conditions, excess ammonia can further react with the nitric oxide and produce additional nitrogen and nitrous oxide, which reduces overall plant efficiency and increases environmental emissions.
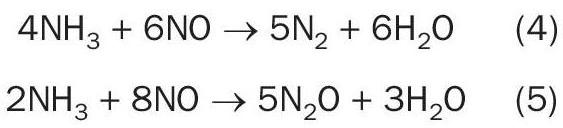
The selectivity weighs greatly on the selected alloy composition, with platinum-rhodium alloys regarded as the industry favoured class. Their combination of low in-situ metal loss and high conversion efficiency in comparison to pure platinum wires over the course of a standard campaign length allows the plant to run at a higher temperature taking advantage of the increase in selectivity to nitric oxide4,5 (Fig. 1). By further investing in the design of the catalyst pack through wire diameter and gauze layer arrangement, the catalyst design can be tailored to achieve even higher production numbers.
Catalyst design
When considering any changes to a gauze design, a fundamental understanding of the metal utilisation and movement within the pack is essential. The top section of the gauze is the location of primary interaction between the ammonia feed and the catalyst. Based on the reaction selectivity, nitric oxide is favoured by a short reaction path through the gauze pack; therefore, it is ideal for the majority of the ammonia to react within the first few layers of the pack4 . Excess ammonia deeper in the pack can result in further formation of unwanted byproducts, nitrogen and nitrous oxide. By reacting as much ammonia as possible towards the top of the catalyst pack, there is limited opportunity for byproduct production through direct ammonia oxidation or through the reaction of ammonia with nitric oxide (equations 4 and 5)5 . These byproducts not only reduce overall plant efficiency, but N2 O has the added impact of potentially breaching emissions legislation, both very costly outcomes.
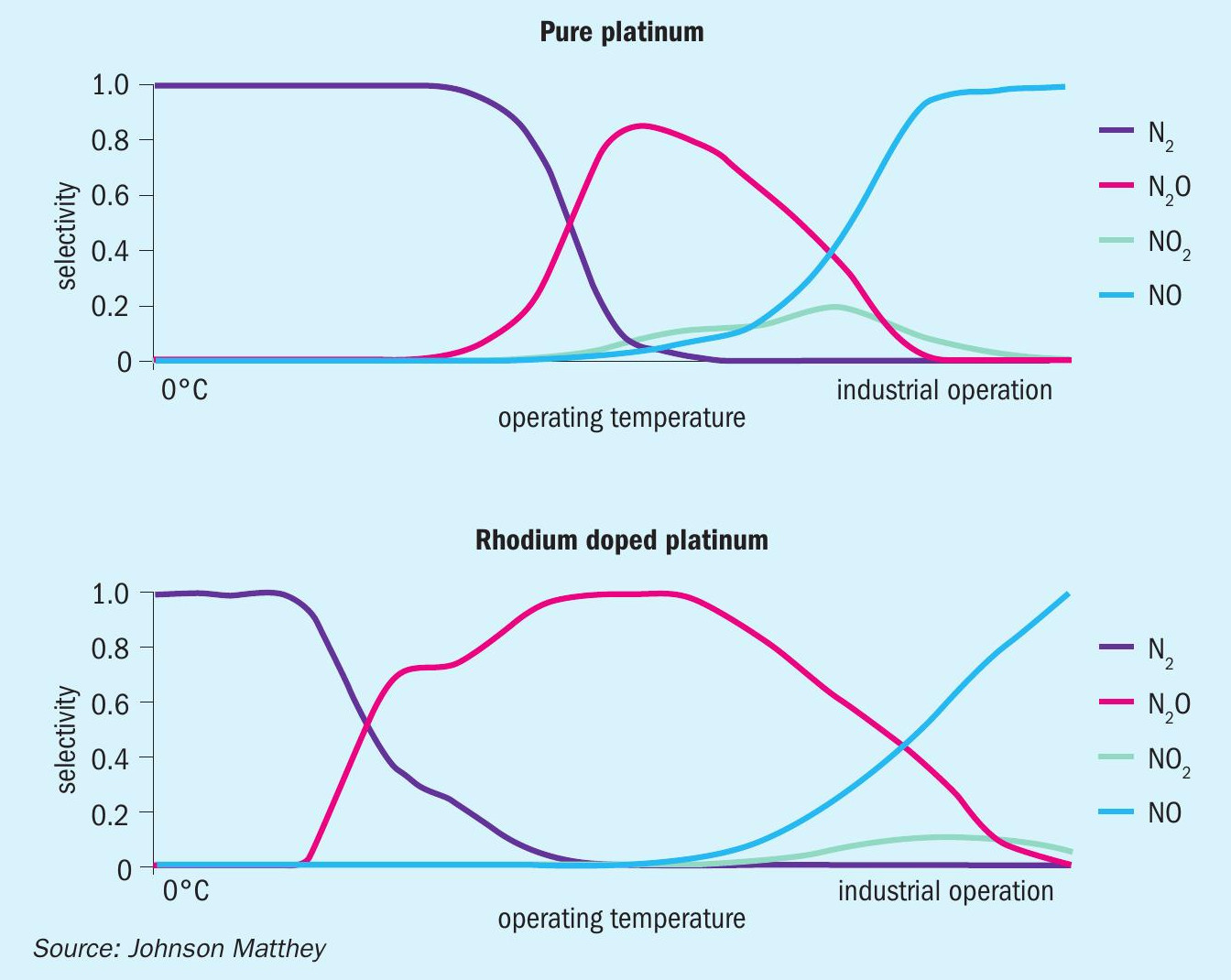
When the gauze is installed, the PGM wire surface restructures and forms cauliflower structures, which greatly increase the catalyst surface available for ammonia oxidation. The additional surface area from the cauliflower formation allows for a high conversion efficiency at the start of the campaign. As these cauliflowers begin to break off, the conversion efficiency decreases and signals the near end of the campaign. The reaction then continues to travel further down the pack, so several catalyst layers are specifically left at the bottom of the pack to react with the ammonia passing through5 . Because of the overall gauze performance, campaign lengths can be extended where maintenance schedules allow5,6 . There is an essential balance when designing a catalyst pack between installing too few layers, allowing for ammonia slip, and installing too many layers, resulting in a very heavy pack that increases selectivity towards further NO reduction and byproduct formation (equations 4 and 5).
Based on this knowledge, Johnson Matthey has created a “flex pack” catalyst design in which the top 25-30% of the 1,000 900 800 gauze pack is changed to a thicker wire, but the overall nominal weight is maintained. This thicker wire diameter acts as an increased concentration of PGM at the top of the pack where the bulk of the reaction is occurring, thus increasing the initial number of active catalytic sites2,5 . This design allows for increased conversion efficiency and/or longer campaign lengths, with some lower layers left in the bottom of the pack to minimise ammonia slip. The thicker wire also aids in the overall goal to design for no ammonia slip through the catalyst during normal operation. In comparison to a standard pack, there is a significant increase in ammonia conversion in the top few layers of the pack (Fig. 2)4 . Redistributing the catalyst weight in a gauze pack allows excess layers towards the bottom to be removed, yielding the additional economic benefit of either maintaining or reducing the amount of precious metal required, as well as decreasing process related metal losses5,7 .
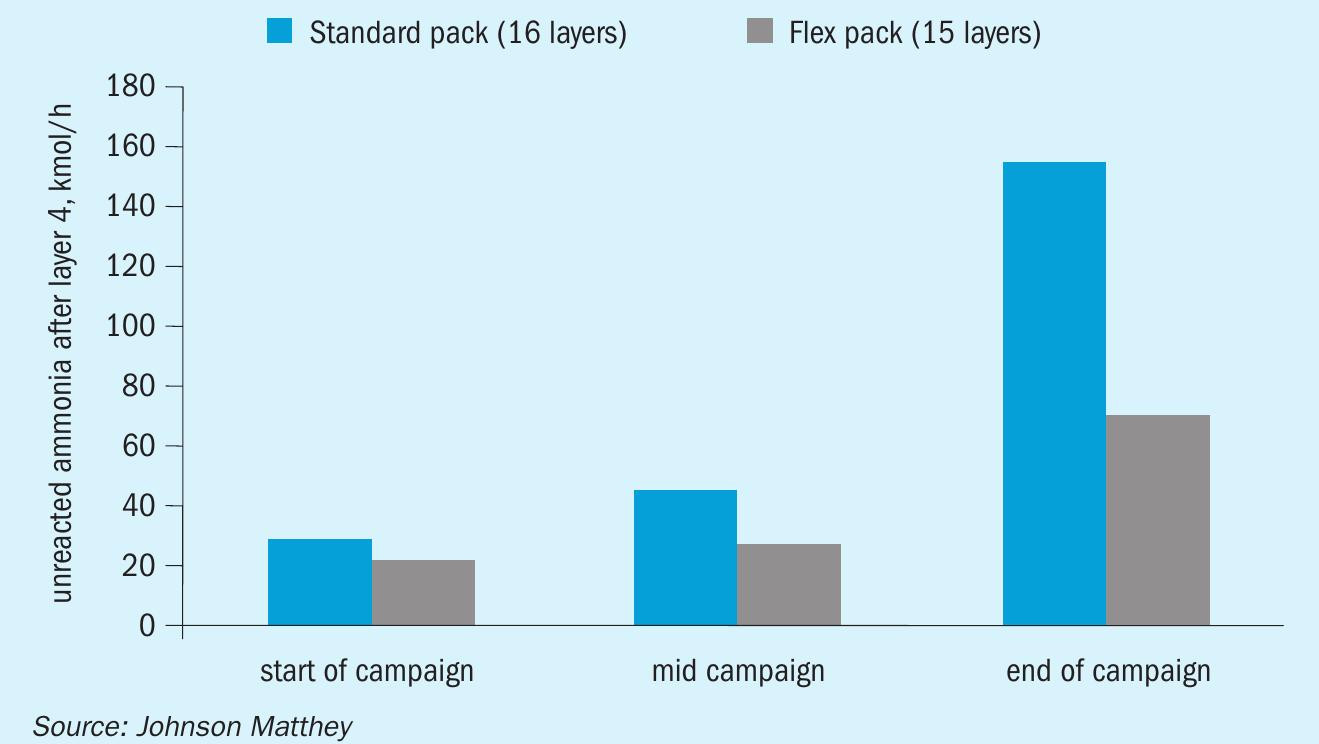
Campaign lengths
Extending campaign lengths is a goal of many producers due to the associated increase in yield and decrease in production cost. Nitric acid plants tend to land in one of two categories for determining their campaign length: either campaign lengths are predetermined based on a maintenance schedule or plants have no set date for changeout in place. Instead, these plants opt to monitor their conversion efficiency with the goal to run for as long as effectively possible based on their plant-specific threshold3 . In areas where ammonia feedstock costs are low, the plant can run at a lower efficiency than plants running in areas where feedstock prices are significantly higher. Overall, the industry tends to favour maintenance shutdown campaigns, as they limit any unplanned decrease in process yield or increased metal loss.
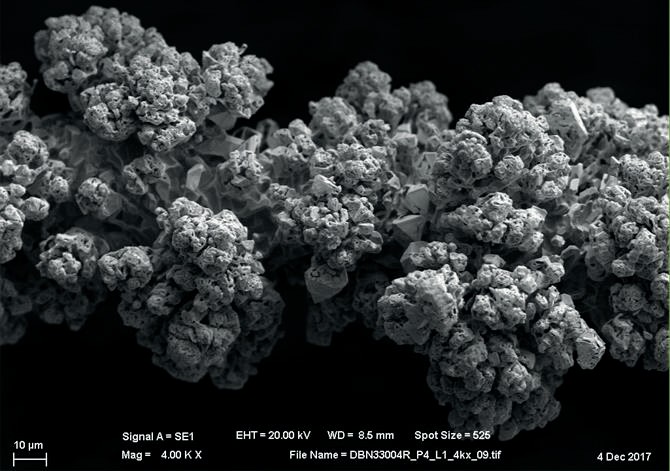
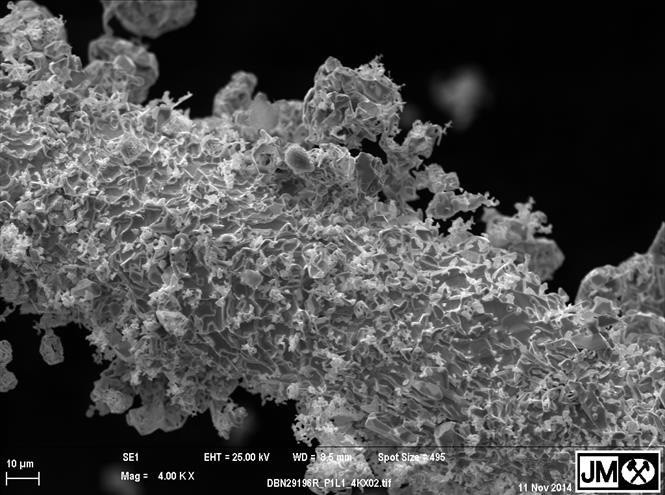
Maximum campaign lengths have continued to increase throughout the years with innovations in gauze design, now generally sitting at approximately 90-120 days for high-pressure plants and up to one year for medium-pressure plants before the catalyst needs to be changed out based on performance5 . The longer a gauze campaign can be extended, the less often the investment of a new gauze needs to be made; therefore, the economic benefit of high-pressure plants transitioning from running four 90-day campaigns per year to three 120-day campaigns is apparent.
Metal losses
Metal losses place a constraint on the campaign length, as plant efficiency notably drops once over 50% of the PGM is lost and consequently warrants a changeout5 . The addition of rhodium will reduce the overall metal loss from the pack, as these alloys see a reduction in platinum volatility compared to pure platinum (Fig. 1)5,7 . During a standard gauze campaign, the wire surface restructures to form high surface area growths, referred to as ‘cauliflowers’, which are beneficial in that they yield high selectivity to NO, but also result in PGM, particularly platinum in oxide form, to be lost to the gas stream. This standard rate of metal loss is only expedited by increases in pressure and nitrogen loading.
Thicker wire
Thicker wire diameters have also been noted to benefit plants that experience a high number of shutdowns or trips throughout their campaign. During a plant trip on a typical gauze with standard wire diameter, the cauliflower structures can be damaged and break off, eliminating the additional surface area that maintains the acceptable conversion efficiency and thus adds to the campaign length (Fig. 3). With the thicker wire, the additional density of PGM on the wire surface allows for the wire to restructure the cauliflowers again after the initial ones are lost, therefore maintaining campaign lengths following shutdowns6 .
N2 O abatement
As previously stated, within the nitric acid production process, there is potential for side reactions to occur based on selectivity in which byproducts form. The one of primary concern for the nitric acid industry is nitrous oxide (N2 O). This greenhouse gas has a global warming potential in the region of 300 times that of carbon dioxide due to its long atmospheric lifetime, posing as an environmental threat and also decreasing production yields8,9 . While government sanctioned emissions limits have been set in certain parts of the world like Europe and Asia, there has been a noticeable trend in an increased sense of corporate responsibility, with companies looking to voluntarily reduce their emissions. Either way, reducing these kinds of emissions is only gaining more traction on the global stage with the heightened awareness of climate change.
Reducing N2 O within the catalyst pack can be done with either of two main strategies: suppressing N2 O generating side reactions from the start or increasing the amount of N2 O decomposition. Based on catalyst design, the first method has already been addressed as the optimum catalyst design will have heightened selectivity for NO and create as little byproduct as possible. Primary abatement reduces the amount of N2 O formed within the gauze pack during the ammonia oxidation step8 . Methods of N2 O decomposition are more popular solutions due to their overall effectiveness, lower cost and easier installation process, with the other methods referring to different points in the nitric acid process where the N2 O is destroyed.
Secondary abatement
Secondary abatement utilises a catalyst product to decompose N2 O immediately below the gauze just after it has been formed. While the gauze sits as close to the gas entry point as possible within the basket, the abatement catalyst sits directly below the gauze near the gas exit point; this allows for increased residence time of the gas in the burner and thus increased time for the N2 O decomposition reaction to occur8 . Any uncertainty surrounding secondary abatement tends to be around the associated pressure drop that comes with replacing the standard supports with catalyst, which can be vetted for its impact on production on an individual plant basis to determine their pressure drop tolerance.
Johnson Matthey markets a Yara catalyst product for secondary abatement, YARA 58-Y1, which consists of pelleted active cobalt aluminate supported on a cerium oxide substrate. Secondary abatement is considered the most cost-effective method of N2 O abatement, as there is typically no major modification of the reactor required. Therefore, the catalyst can be readily placed in the basket with low to no capital expenditure. The installation of this catalyst has shown no effect on ammonia conversion while also potentially providing up to 90% N2 O abatement emission reduction8 . This significant savings brings the opportunity to obtain GHG emission credits under the Climate Action Reserve programme.
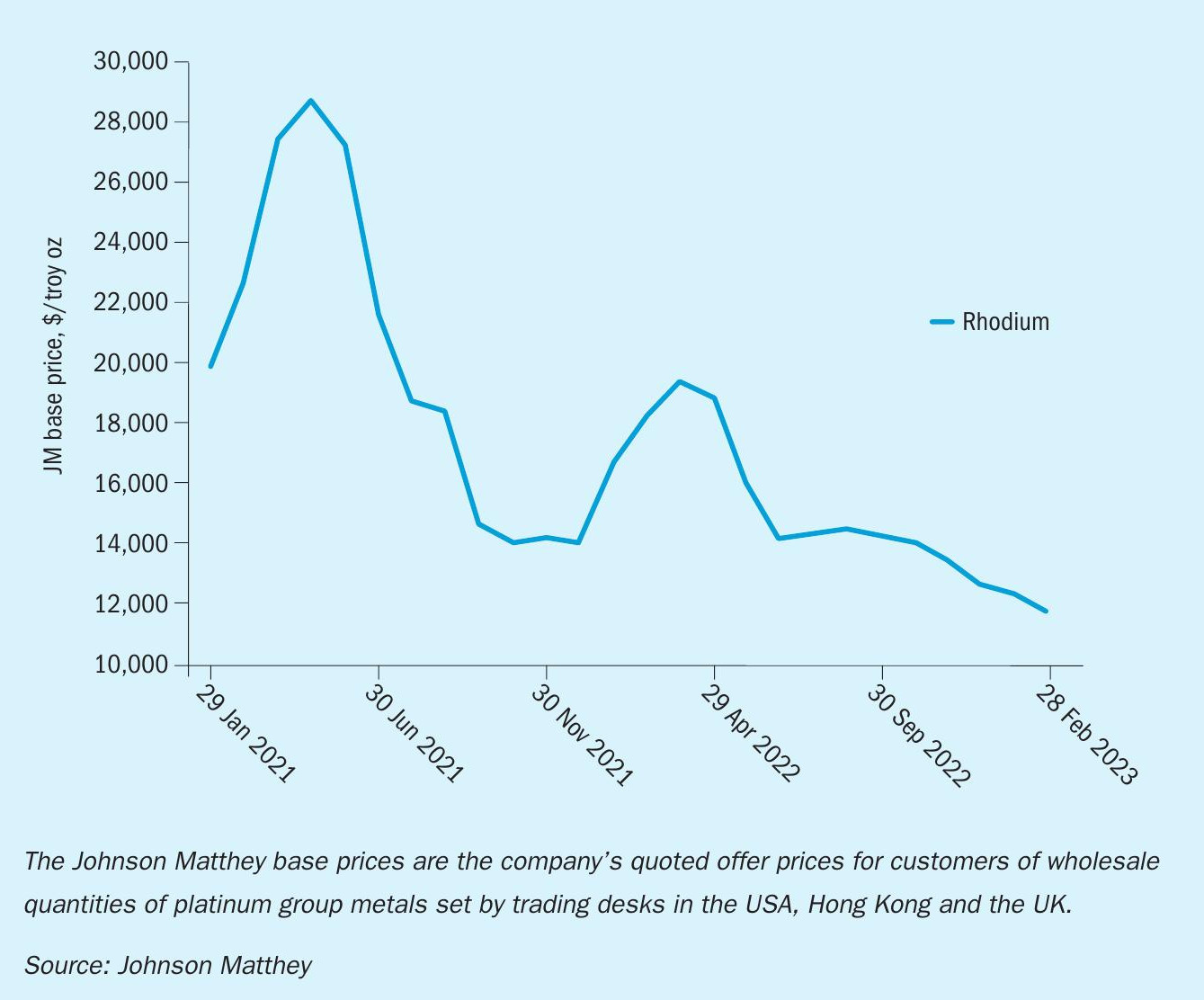
Tertiary abatement
Tertiary abatement is considered a reduction process in which the N2 O is removed from the tail gas in a separately installed catalytic reactor located after the absorption column.
Although a tertiary option could yield abatement levels as high as 98%, the cost associated with creating and installing the new vessel is much higher than other abatement options. Tertiary systems typically require plants to increase their stack gas temperatures after the absorption step in order to guarantee appropriate burn off of N2 O emissions and reach expected abatement levels. The degree to which these gases can be reheated could be a limiting factor. While all nitric acid plants should have a tail gas heater, depending on its design, age and size, the necessary reheat temperature for desired abatement may not be achievable2,8 .
Case study: rhodium pricing
Platinum is the key element in nitric acid gauzes due to its ability to withstand operating conditions and remain in its metallic form. Although the platinum-rhodium alloys performed well and satisfied production needs, their overall economic benefit came into question with the surging rhodium prices over the last three years, particularly in the spring of 2021 (Fig. 4). With rhodium prices rising above $25,000 per troy ounce in spring 2021 and peaking just under $29,000 per troy ounce in April 2021, metal pricing greatly impacted the operational spend for precious metal gauze users and will continue to do so10 .
The dynamic PGM market with its changing prices is an economic factor influencing the pack design selected. The changing PGM prices for some nitric acid plants create difficulty when trying to balance contributing factors such as cost and conversion efficiency.
Nitric acid plants have manipulated their designs to maximise either production efficiency or campaign length while minimising the amount of rhodium required in their gauzes, as even a small reduction in the amount of rhodium required can greatly reduce the cost of the total pack and thus reduce the cost of nitric acid production4 . Two of the key factors impacting the optimisation of catalyst design are burner efficiency and metal loss rate. A range of 0-5% rhodium within the alloy has been identified as the most effective alloy class that balances these variables2 . Shifting from 5% to 3% rhodium in the alloy allows for cost savings via a reduction in installed PGM value11 . This option was deemed popular with higher pressure plants (>100 psig) as well as plants running at lower temperatures, which are highly susceptible to rhodium oxide poisoning5,11 .
Conclusion
The key to a high achieving nitric acid plant is balancing performance goals with economic constraints. The optimal gauze design not only considers alloy selections and catalyst distribution throughout the pack, but also the plant’ s operating strategy and external economic pressures like the PGM market and ammonia cost.
References