Nitrogen+Syngas 384 Jul-Aug 2023
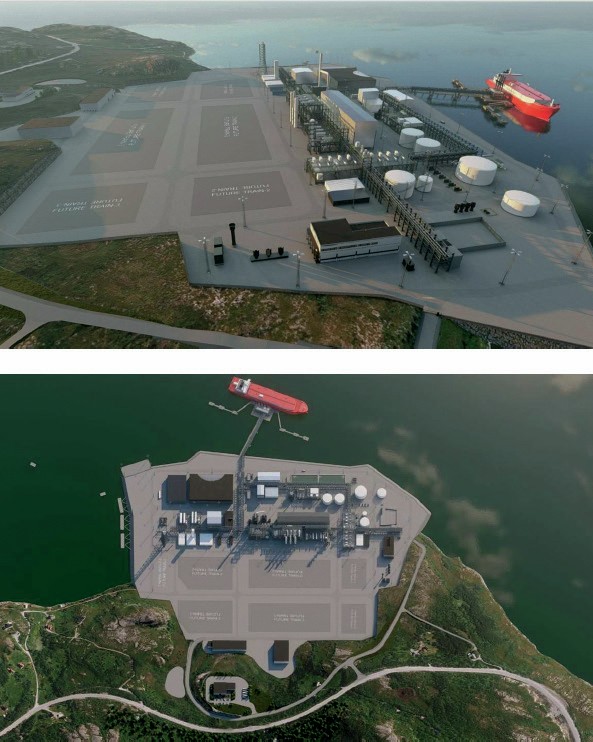
31 July 2023
Barents Blue Ammonia project
LOW CARBON AMMONIA
Barents Blue Ammonia project
Horisont Energi has the aspiration to develop the most carbon and energy efficient blue ammonia plant in the world, an environmentally friendly plant with a focus on sustainable solutions. This article describes the main features of the Barents Blue Ammonia project, such as 99% carbon capture rate target, a high degree of modularisation, winterisation, infrastructure for ammonia and CO2 management and the provision for future expansion.
Barents Blue Ammonia project
Horisont Energi, an independent Norwegian energy company, is developing a large-scale blue ammonia complex in Finnmark, Norway, (Fig. 1), exploiting the favourable combination of feedstock gas availability, cold climate conditions which allows higher process efficiency, and proximity to offshore CO2 storage.
In 2021 Saipem started work on the concept study for the Barents Blue Ammonia project and was subsequently awarded the extension of the engineering services, currently ongoing, to optimise the overall complex by integrating the process, utilities and offsites.
The plant
Topsoe’s SynCOR Ammonia™ process, which is based on autothermal reforming (ATR), was the technology selected for the Barents Blue Ammonia project.
ATR is emerging as a promising application for the new generation of large-scale ammonia plants and is well referenced in other syngas applications, e.g., methanol and gas-to-liquids. The first large-scale ammonia project based on SynCOR Ammonia™ is currently under execution by Saipem.
For blue ammonia there is an inherent advantage in the use of ATR; most of the natural gas is used as feedstock and the CO2 generated in the reforming section can therefore be easily captured in the conventional CO2 removal unit, while only a small portion is used directly as fuel, eventually resulting in reduced CO2 emissions to the atmosphere. As a consequence, the CO2 capture rate achievable without modifications to the process scheme (i.e., simply conditioning and storing the captured CO2 ) is higher for the ATR than for the steam methane reformer (SMR) which is typically in the range of 80-88%. Taking into consideration the capture rate, an ATR-based plant is inherently a blue ammonia plant and does not require post-combustion CO2 capture from the flue gas. To further improve the capture rate, among various alternatives, it is convenient to use off-gas from the syngas purification along with purified syngas recycled as fuel in the fired heater, without excessive oversize of the front end, as depicted in Fig. 2.
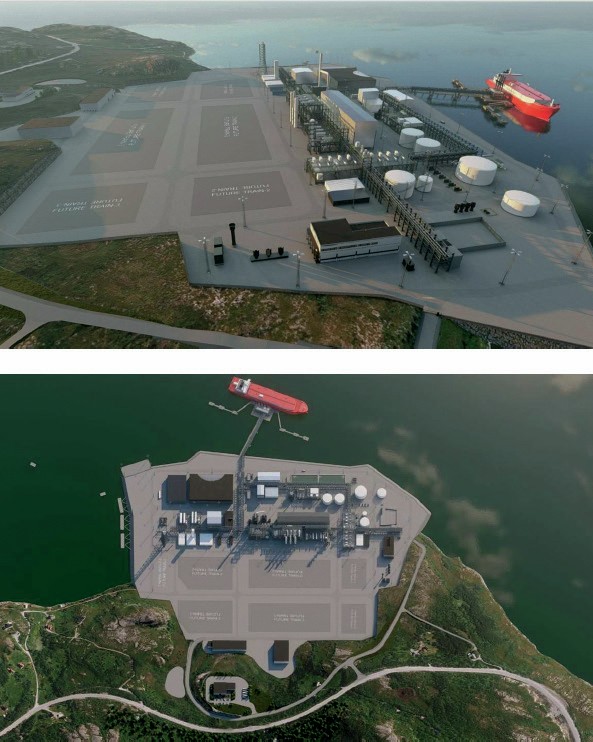
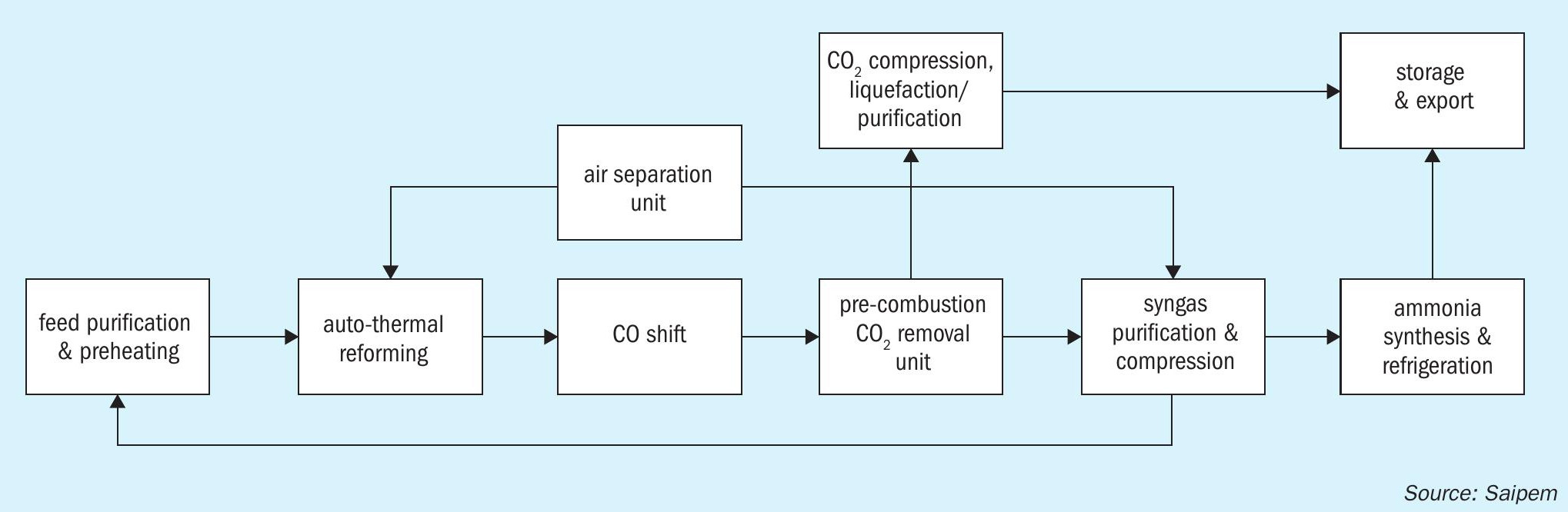
The integration of the utilities with the ammonia plant, and in particular the optimisation of the steam and power network, is a key element in the design of the overall complex.
Extensive use of electrical over direct steam turbine drivers increases the overall efficiency of the complex. The plant electrical power requirements are mainly satisfied by internal power generation by means of steam turbine generator (STG) with limited renewable electricity from the grid.
A thorough value engineering exercise has been carried out to identify all possible opportunities to increase efficiency in normal operation: for instance, excess syngas generated in the ammonia front-end section for fuel is expanded to generate 3-4 MW electric power.
Optimisation of the efficiency has been evaluated in conjunction with other key design parameters such as reliability and operability; therefore, the plant is designed to operate without some of the energy recovery features.
In addition, the low steam-to-carbon ratio enables large-scale capacity; in fact, all the units in the plant have equipment that falls within the referenced size of operating plants or generally requiring minimum scale up.
Barents Blue Ammonia is a fully automated plant with integrated energy management; another advantage of ATR is that it is possible to maximise automation with inherently efficient and safe operation. It significantly reduces the risk of human error resulting in less lost time accidents, increasing plant availability and reducing the environmental impact of flaring caused by erroneous upset situations.
In addition to the CO2 emission, the plant is designed to minimise the overall impact to the environment with the main focus on noise, effluents and emissions (e.g. mitigation measures implemented after a dedicated noise study, DeNox system implemented, etc.).
Carbon capture rate: 99% target
Barents Blue Ammonia project will capture and permanently store approximately 2 million t/a of CO2 per ammonia train, which corresponds to the CO2 emissions generated from more than 400,000 cars.
The CO2 is captured from the synthesis gas using standard capture technology already included in conventional plants.
The CO2 emission from the fired heater upstream of the ATR is minimised thanks to the hydrogen-rich gas from the front end. The increase of the front-end size has been evaluated to be more economical and efficient than the implementation of a post combustion CO2 capture unit in the fired heater exhaust.
The selection of the most adequate process scheme is driven by both plant operating conditions and/or the use of the available utilities at site. The 99% target includes the contribution of all the other sections of the complex: utilities and offsites.
The steam generated by process heat recovery is used to drive the major compressors and to generate electric power by means of STG. With the minimum supplementary steam generated by the auxiliary boiler, which is using hydrogen-rich gas as fuel during normal operation, it is possible to close the steam and power balance, avoiding additional CO2 emission in the utilities section.
The design has also been tailored to reduce CO2 emissions during commissioning and start-up; dedicated studies have been carried out to identify a suitable design and features to also minimise CO2 emission during transient scenarios (e.g., minimising the flaring and the use of natural gas as fuel in the auxiliary boiler).
The capture rate is not the only parameter to measure the environmental sustainability of a blue ammonia project: another important parameter is the carbon intensity which takes into account not only the emissions generated in the process but also the emissions associated to the imported electricity. Maximisation of the efficiency reduces the natural gas consumption and the relevant contribution to the carbon intensity, while the availability of renewable energy from grid is essential to maintain a low overall index. According to the study performed by Saipem, Barents Blue Ammonia carbon intensity (tCO2 eq/t product) for scope 1 and 2 is 0.0169 while the benchmark for a modern grey ammonia plant in Europe is 1.694.
Winterisation
The cold climate in the region represents a challenge but also an opportunity for the project to improve the plant’s efficiency. For example, the utilities scheme uses cold sea water (8°C) as a direct cooling media for the STG condensers and a cooling water loop (13°C) provides robust plant cooling with high thermal efficiency.
The building is heated by hot water, while process winterisation is provided by electrical tracing. Where possible, waste heat from the plant is used to improve efficiency and further reduce CO2 emissions. For example, the heat pump circuit has been integrated with process streams for winterisation purposes.
High degree of modularisation
Modularisation offers several advantages in terms of safety and costs for a location where the mobilisation of huge construction manpower is not possible and/or access at site is difficult or not possible for a prolonged period such as in Finnmark.
A deep analysis of the optimum size of the modules considering logistic constraints, cost and time-effectiveness and availability of yards has been performed to optimise the strategy. As result of the investigations, the overall complex has been modularised to a large extent (>90% on total equipment count). The process sub-units fit within single big modules to minimise the hook-ups and pre-commissioning works at site.
This project has the advantage of having a location with direct access to the sea, which allows the offloading of large modules, with more than 5,000 t per module and maximum dimension of approximately 100 x 30 x 36 m (L x W x H) per module.
Infrastructure for ammonia and CO2 management
The ammonia is stored in a rock cavern physically located under the site thus enhancing safety, reducing the thermal dispersion and minimising the associated boil off refrigeration energy consumption. This provides a very efficient solution from the energy point of view. The capacity is 120,000 m3 .
Permanent offshore CO2 storage, which can be reached by pipeline or by ship has been considered. In the latter case, an intermediate CO2 storage would be required. Depending on the CO2 purity target, a purification and chilling section might have been required affecting the overall energy plant consumption. Transportation by pipeline has less strict requirements and is the base case for storing CO2 in the Polaris reservoir.
Provision for future expansion
Since the early stages of the project, possible future expansions have been duly considered. Proper design allows safe and efficient expansion even when the first train is already in operation. The optimised choice for the common utilities and offsites minimises the overall cost over the project life.
Modularisation offers significant advantages for future expansion with the possibility to replicate modules for the additional train and utility modules already designed.
Site preparation, sea water intake, raw water tank, fire tank, main electrical substation, main control room, ammonia storage, the jetty and its loading system have all been designed taking into consideration the expected overall expansion.