Fertilizer International 515 Jul-Aug 2023
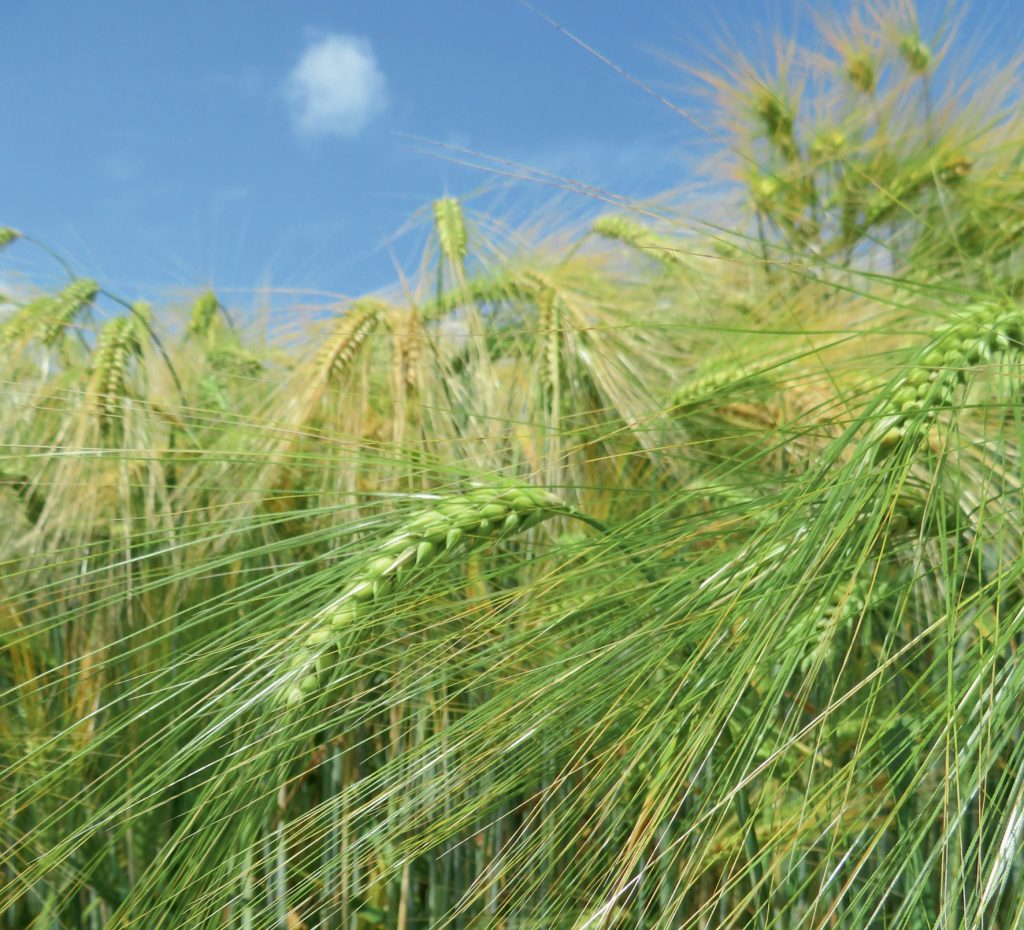
31 July 2023
Innovative fertilizer products and pioneering producers
INNOVATION SHOWCASE
Innovative fertilizer products and pioneering producers
A review of recent additions to fertilizer product portfolios and new process technologies, as innovation within the industry accelerates to decarbonise production and improve nutrient use efficiency (NUE).
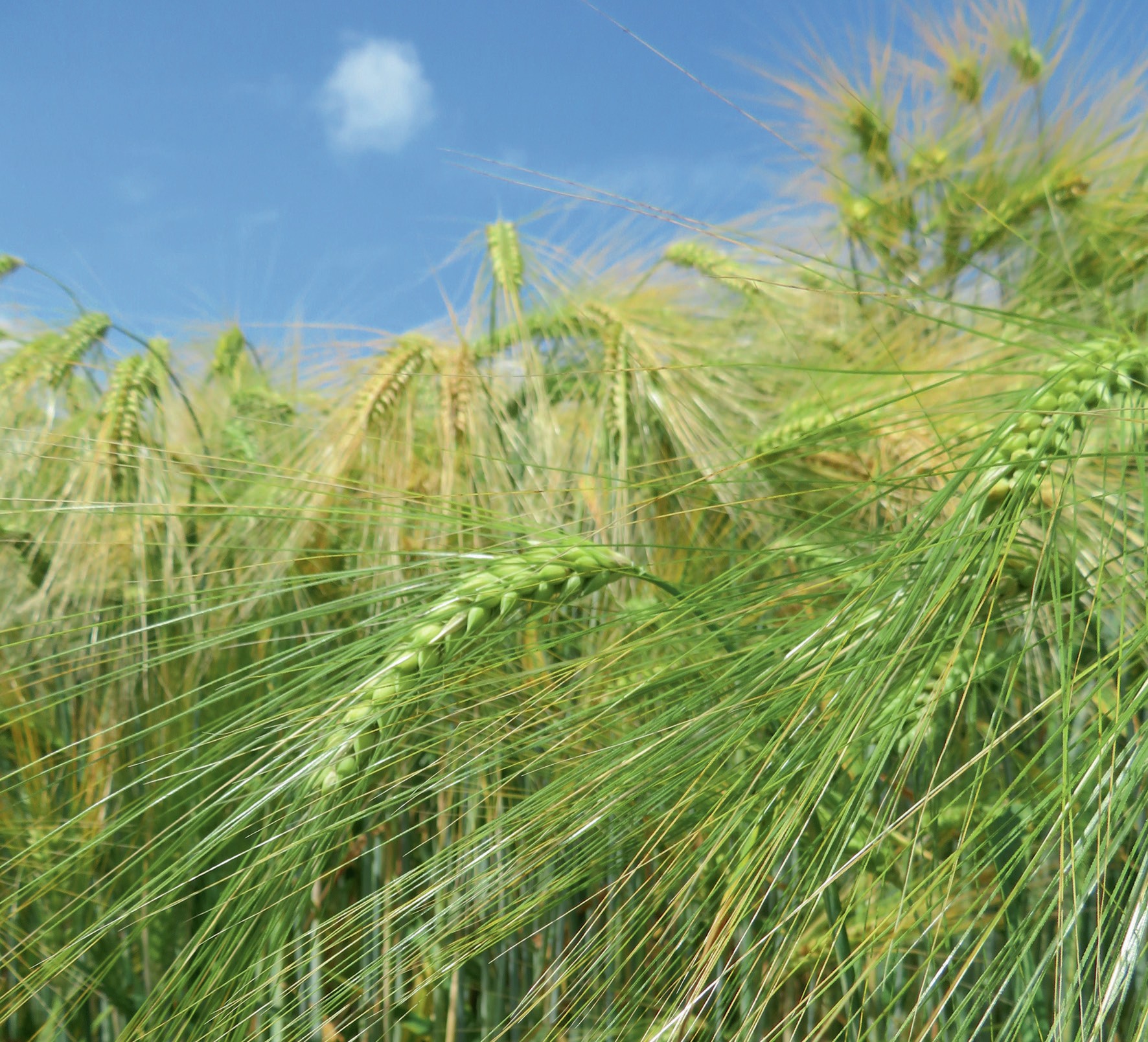
The last 12 months have been a highly productive period for fertilizer industry innovation.
In major project launches, SQM unveiled a novel iodine speciality fertilizer, while ICL introduced a controlled-release fertilizer (CRF) with a biodegradable coating. ICL also brought Nutriduo, an innovative new micronutrient product, to market in Brazil. This foliar fertilizer is enriched with selenium, magnesium and zinc (Fertilizer International 513, p24)
In India, both Coromandel International and IFFCO have launched nano fertilizers and ramped-up production.
Yara, meanwhile, has agreements in place to market and sell ground-breaking ‘green’ fertilizers. These have an 80-90 percent lower carbon footprint than their conventional equivalents.
AgTech start-ups have also come to the fore. These were showcased and given an opportunity to pitch to the fertilizer industry at CRU’s Fertilizer AgriTech Forum in Dallas last September (Fertilizer International 511, p25). One of the participants, Californian AgTech start-up Nitricity, went on to secure $20 million of investment for its sustainable and local nitrogen fertilizer production technology.
For the second year in a row, the International Fertilizer Association (IFA) also featured a dedicated start-up corner as part of the exhibition accompanying its annual conference. A prominent exhibitor was Fertipaq, a Netherlands-based company that manufactures an organic liquid sulphur fertilizer by de-sulphurising wastewater streams.
Ultrasol®ine K Plus – a new speciality fertilizer with iodine
SQM has launched a new speciality fertilizer that supplies iodine to fertigated crops. This allows growers to apply iodine as a plant micronutrient in a form that is guaranteed to be safe and at an effective science-based dose.
The newly-launched product, known as Ultrasol® ine K Plus, combines two essential plant macronutrients – potassium and nitrate nitrogen – with iodine. The product ensures that all three nutrients are applied at well-defined application rates. This makes it easy for the grower to maintain an effective and safe concentration of iodine in the root zone. As a result, Ultrasol® ine K Plus can prevent iodine deficiency in crops without the risk of excessive iodine application.
The product has already been extensively tested globally and is backed by more than 100 well-documented trials with growers. The experience of these growers has confirmed that iodine delivers distinct crop benefits – including improvements to:
- Root growth
- Above ground plant growth
- Photosynthesis
- Nitrogen metabolism
- Tolerance to abiotic stress
- Flowering and fruit quality with less fruit rot and better shelf life.
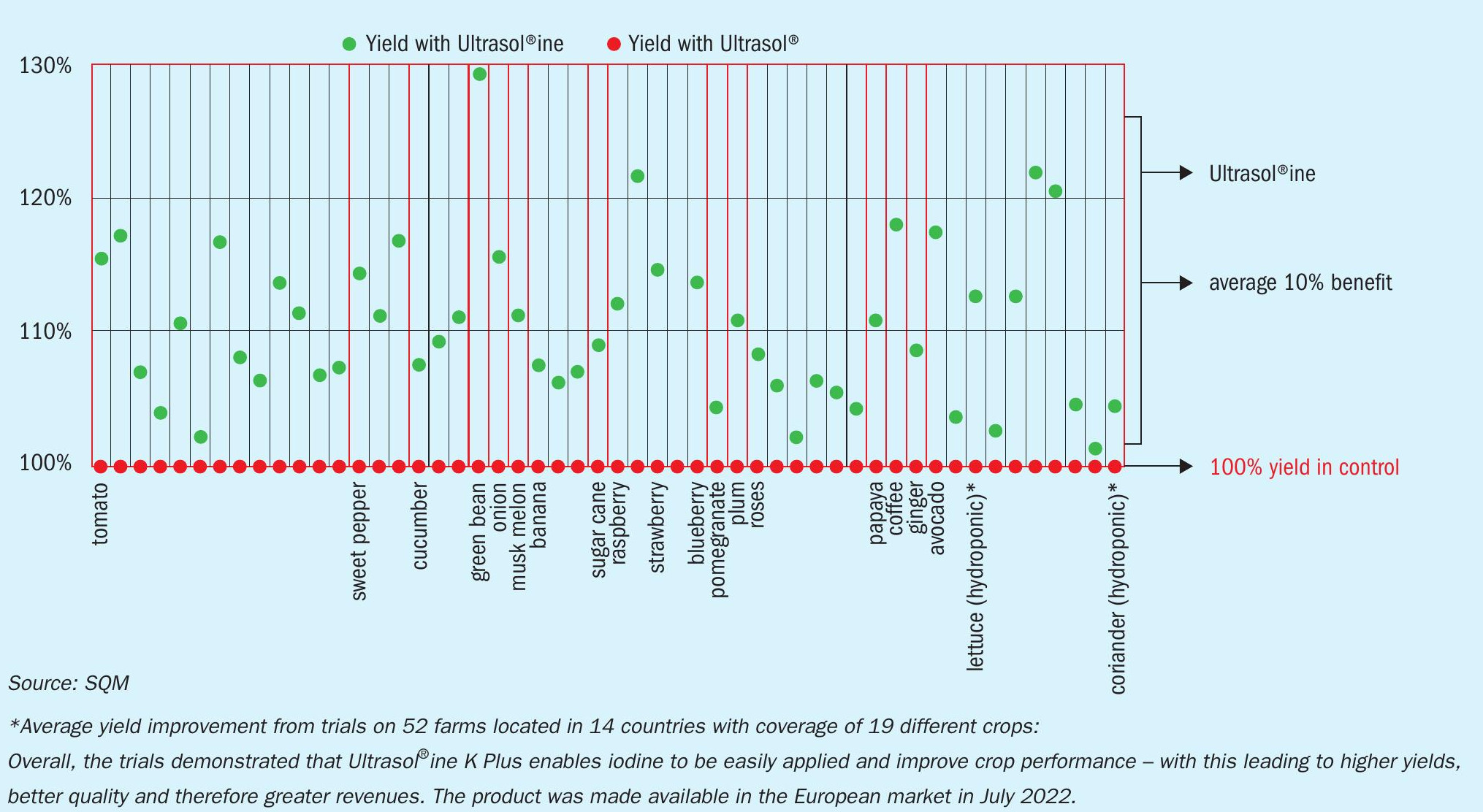
Typically, the application of iodine to crops delivers 10 percent more marketable yield (Figure 1). This is the average yield improvement from trials on 52 farms located in 14 countries with coverage of 19 different crops. These trials compared Ultrasol® ine K Plus to potassium nitrate without iodine for the same crop, on the same planting date with the same fertilizer programme. Crops included: tomato, lettuce, sweet pepper, cucumber, musk melon, sugarcane, pomegranate, papaya, banana and coffee.
Ultrasol® ine K Plus was developed in response to new information published in a landmark paper in 20211 . This highlighted the importance of iodine as an essential plant nutrient.
It has long been known that iodine is essential for human and animal health. But this paper demonstrated that plants need micro doses of iodine as well. For the first time, the presence of 82 naturally-occurring iodine-containing proteins was also identified in higher plants. Drawing on these and other findings, the researchers concluded that1 : “Results are strongly suggestive of the role of iodine as a plant nutrient.”
Subsequently, based on this compelling new evidence, iodine was mentioned as a beneficial nutrient for plants in the recently published 4th edition of Marschner’s authoritative Mineral Nutrition of Plants2 .
The potential of iodine to reduce yield loss in salt-stressed crops was also confirmed by an agronomic study last year3 . This examined the role of iodine as a micronutrient in tomato. In non-stressed plants, the presence of iodine in the nutrient solution increased plant growth and fruit yield and had a positive effect on the firmness of the fruit. In salt-stressed plants, iodine boosted overall tomato yield when applied in micromolar doses – increasing both the number of fruits per truss/per plant and individual fruit weight.
SQM has observed similar beneficial effects on strawberries grown under saline growth conditions in California. In replicated trials, the presence of iodine in the nutrient solution, by alleviating salt stress, led to greater fruit yield and fruit quality.
New biodegradable coating technology
ICL has developed a new generation of biodegradable coatings for its controlled-release fertilizer (CRF) portfolio (Fertilizer International 510, p24). The new coating technology is designed to meet the requirements of the new EU fertilising products regulation (2019/1009) and reduce the environmental footprint of CRFs. It will also help Europe’s farmers meet the requirements of the EU’s Green Deal policy.
This patented innovation, named eqo.x, coats nitrogen fertilizer granules applied to field grown crops. The technology has already been fully tested in the field – and shown excellent results in terms of ease of production, nutrient use efficiency, and reducing volatilisation and leaching losses.
According to ICL, eqo.x is one of the most important innovations and technological launches since CRFs were first introduced to the market decades ago. It is expected, once again, to shape the future of fertilization.
“We see this as a huge step forward in the use of enhanced efficiency fertilizers for the agricultural market,” comments Ronald Clemens, ICLs Global Marketing & Portfolio Manager CRF. “The biodegradable release technology will be able to reduce all kinds of nutrient losses, and combines this with all the known advantages of CRFs, such as reduced application frequency and application rates.”
He adds: “This innovation makes it possible for farmers to reduce fertilizer rates without losses in yield. In that respect, eqo.x is ahead of the present regulations and ready for future standards coming.”
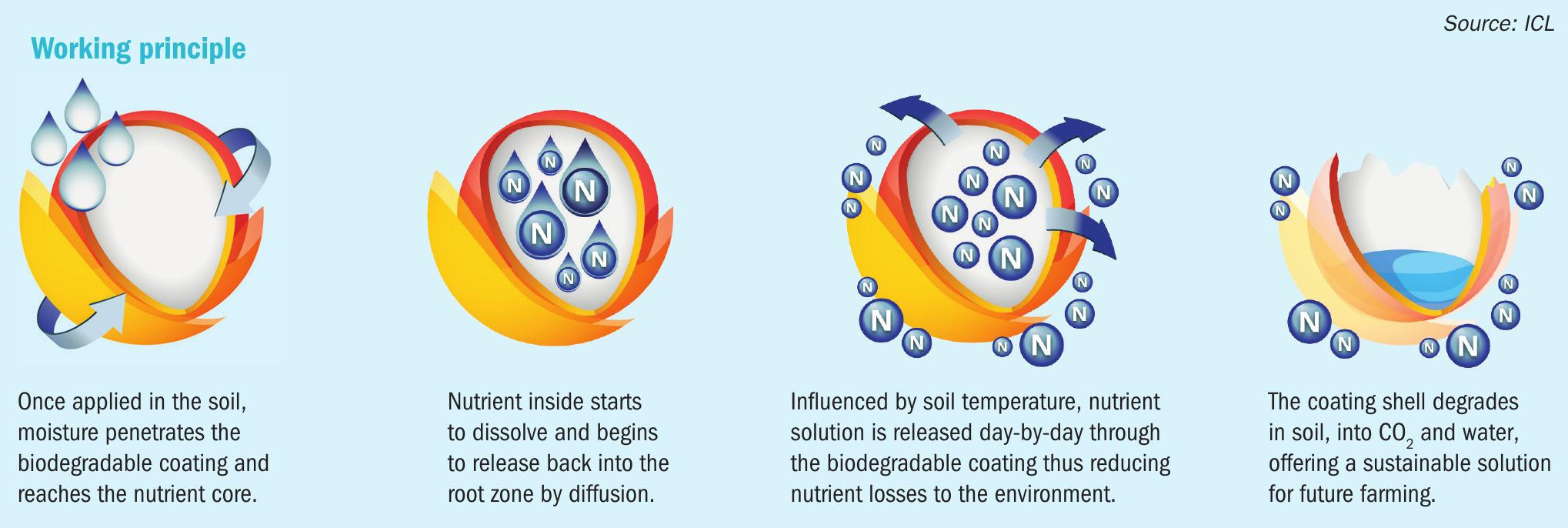
Clemens explains how the new biodegradable coating functions (Figure 2):
“Eqo.x works similar to our existing coatings. The soil temperature affects the speed of release in a similar way to E-Max coatings. That makes it easy for the farmer to use the new product, as neither the application or the performance will change.
“The new technology offers an improvement in release patterns, making CRFs with eqo.x technology even more reliable and predictable than before. And after the longevity ends, the coating shells will degrade even faster to CO2 and water, leaving no trace behind.”
Wide ranging trials with eqo.x technology have all shown an increase in NUE. This is to be expected with a CRF, says Ronald Clemens: “The technology contributes to reducing nutrient losses and improved nutrient use efficiency. It will help farmers to maximise their yields.
“We have tested in crops like potatoes, but also in very hot conditions in rice cultures where the product is fully under water. We have tested the release specifications in the lab under various temperature regimes, in water and in soil as well as under practical circumstances. In all those conditions, the nutrient use efficiency was significantly increased, giving better results than growers practice – in terms of yield, number of applications or application rates.”
ICL will start to deliver eqo.x technology to the market in its Agrocote and Agromaster formulations this year. In the meantime, the company’s R&D team is continuously working on new solutions.
“We are extremely happy that this innovation is already available now – so that we are prepared for the future,” sums up Ronald Clemens. “The next step is to move more of our coating technologies to faster degradability.”
Nitricity secures funding
Last October, Californian AgTech start-up Nitricity successfully raised $20 million as part of a ‘Series A’ capital investment round.
The fundraising round was led by Khosla Ventures and Fine Structure Ventures. Three other investors, Energy Impact Partners, Lowercarbon Capital and MCJ Collective, also participated. Nitricity has raised $27 million in total funding to date, including this new financing.
“This fundraising round brings us one step closer towards sustainable and locally produced fertilizer,” said Nicolas Pinkowski, CEO and co-founder of Nitricity. “It’s time to bring this to market. We have aggressive growth plans in motion.”
Nitricity’s innovative technology turns air and water into nitric acid using solar energy and a plasma reactor. The nitric acid generated can then be converted into a range of liquid fertilizers by combining with other inputs such as limestone, phosphate rock and potassium hydroxide.
The company’s aim is to electrify and locally distribute nitrogen fertilizer production using low-cost solar or wind power. This approach disrupts the nitrogen industry’s current highly centralised and fossil fuel reliant production model.
“This electrified technology provides fertilizer in a climate-smart nitrate form, designed for efficient application, allowing it to address greenhouse gas emissions beyond ammonia-based technologies,” said Joshua McEnaney, president, CTO and co-founder at Nitricity. “This is an opportunity to attack not just the 1-2 percent of global GHG emissions in the production, but the additional five percent of GHG emissions in the application by mitigating nitrous oxide formation. We are pushing hard to scale up and implement this solution.”
Nitricity has shown the potential of its new approach to fertilizer production at California State University’s Center for Irrigation Technology at Fresno – where it was successfully used for the fertigation of tomatoes. This demonstrated the ability of Nitricity’s system to produce and apply nitrogen fertilizers close to the end-user.
“Today’s fertilizer industry is facing the perfect storm of high GHG emissions, high fossil fuel consumption, rising costs and geopolitical disruptions,” said Rajesh Swaminathan, partner at Khosla Ventures. “Nitricity’s decentralized approach to manufacturing fertilizers using just air, water and renewables-based electricity was born out of a vision to completely transform a 100-year-old industry, and we are excited to be partnering with them.”
“Nitricity has made rapid progress since our initial investment in their Seed round,” said Allison Hinckley, senior associate at Fine Structure Ventures, a venture capital fund. “In response, we are increasing our support of the company to aid in bringing their differentiated, decarbonized fertilizer products to market in the near term.”
Nitricity is fast-tracking the development of its renewables-based technology and is aiming to make this commercially-available within two years.
Yara and Lantmännen to bring fossil-free fertilizers to market
Yara has been pioneering the introduction of green fertilizers to the marketplace. The Norwegian crop nutrient giant plans to start manufacturing these this summer.
The company signed the world’s first commercial contract to sell fossil-free fertilizers to Lantmännen, a leading European agricultural cooperative, in January 2022 (Fertilizer International 506, p8). These will be produced by Yara and marketed by Lantmännen in Sweden later this year.
The commercial deal with Lantmännen provides guaranteed market access for the green fertilizers Yara will produce using renewable energy. This should help decarbonise the food chain while offering consumers more sustainable food choices.
Yara plans to supply the market with nitrate-based fertilizers with an 80-90 percent lower carbon footprint. These carbon savings will be validated by DNV, an independent assessor.
Yara’s first fossil-free fertilizer deliveries will use green ammonia sourced from a large-scale pilot project at the company’s Porsgrunn plant in Norway. This is on track to begin commercial production in 2023. Porsgrunn will initially produce around 20,000 tonnes of green ammonia annually. This volume will then be converted into 60,000-80,000 tonnes of fossil-free green fertilizer.
Yara should be well-positioned to scale-up green ammonia manufacture in future from its portfolio of under-development projects in Norway, the Netherlands and Australia. The company is planning to convert its entire Porsgrunn plant to green ammonia within the next 5-7 years.
“We have to transform the food system to deliver on the Paris Agreement, and this will require collaboration across the entire food chain instead of working in silos,” said Svein Tore Holsether, Yara’s president and CEO. “The Yara-Lantmännen partnership is a concrete example of how this can be done.”
“With green fertilizers from Yara in place, we enable Swedish farmers to continue to be at the forefront as well as bringing sustainable food to consumers,” said Per Olof Nyman, Lantmännen’s president & CEO. “With this partnership, we can continue to meet an increased market demand for sustainable products.”
Lantmännen – through its Farming of the Future programme – has already reduced the climate footprint of wheat cultivation by as much as 30 percent since 2015. Including green fertilizers within this programme should reduce the climate impacts of cereal growing by a further 20 percentage points.
Yara has also agreed to supply fossil-free fertilizers to El Parque Papas, Argentina’s largest potato grower later this year (Fertilizer International 512, p8). Yara calculates that the use of its green fertilizers for potato crop nutrition will cut greenhouse gas (GHG) emissions at farm level by around 29 percent, versus standard fertilization practice. Green fertilizers will also reduce the overall carbon footprint of consumer snacks like potato chips (crisps) by around 5-10 percent.
“Most people probably don’t think about emissions when eating their chips. But there are huge opportunities to decarbonize snacks, if we find business models that enable each step of the value chain to contribute and to benefit. This is why the agreement between Yara and El Parque papas is important – we show that this can be done,” said Svein Tore Holsether, Yara’s CEO.
El Parque Papas is Argentina’s single biggest potato farmer. The company supplies 14,000 tonnes of potatoes to Argentinian food processors every year. These are used to produce some of the country’s most popular potato chips.
Carbon-neutral urea production
Stamicarbon has been selected as the licensor for the NeuRizer urea project (NRUP) in Leigh Creek, Australia. The site is located 550 kilometres north of Adelaide in South Australia.
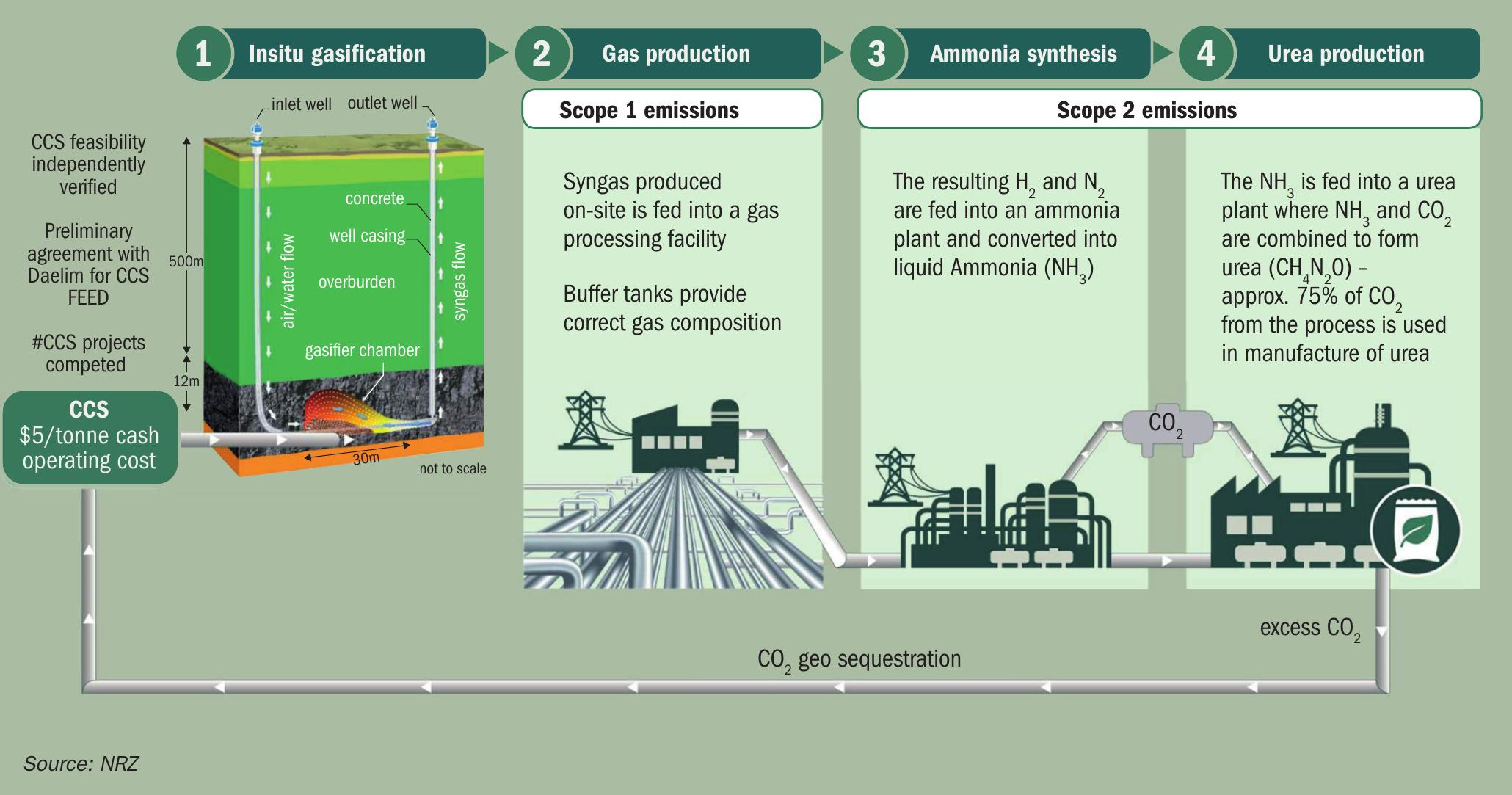
NRUP is aiming to be Australia’s first fully integrated, carbon-neutral urea production plant, having on-site availability for all the inputs (gas, power and CO2 ) required for low-carbon urea production.
KBR will provide technology licensing and engineering for the project’s 1,600 tonne/day ammonia plant. This will be based on KBR’s highly efficient Purifier® process. Stamicarbon, meanwhile, will deliver the process design package (PDP) for the project’s 2,850 t/d capacity urea melt and granulation plant. NRUP will use Stamicarbon’s Launch Melt™ flash design for the melt plant (with a pool reactor) and its Launch Finish™ granulation design for the granulation plant.
Stamicarbon’s Launch Melt™ design significantly reduces the melt plant’s steam consumption due to its high energy efficiency. Its Launch Finish™ fluid-bed granulation design also has favourable characteristics. These include low formaldehyde consumption, low dust and ammonia emissions, high product quality, and high on-stream times. Launch Finish™ also significantly reduces the physical footprint and capital cost of the plant by minimising the equipment required. Fewer equipment items also help cut maintenance costs and deliver operational savings.
Doug Kelly, KBR president, technology, said: “We are excited to provide our energy-efficient ammonia technology for NeuRizer’s flagship carbon-neutral project for the local and export agriculture markets. This project reaffirms our commitment to continuing to explore novel ways to help our clients meet their business and sustainability targets.”
Stephen Zwart, Stamicarbon’s vice president of licensing, said: “This is the first new grassroots urea capacity in Australia in decades. It is a genuinely solid project with an innovative concept that has been built from the ground up. We are proud to be contributing to carbon neutral fertilizer solutions that will help close urea supply-demand in Australia, supporting farmers and food production across the country.”
The NRUP will produce low-cost, high-quality, carbon-neutral urea using novel in-situ gasification (ISG) technology (Figure 3). Urea synthesis and production will consume a large proportion of the carbon dioxide generated during syngas production – with any excess CO2 being captured and stored underground (geosequestration).
A bankable feasibility study (BFS) and front-end engineering design (FEED) work are currently in progress and will be followed by a final investment decision (FID) for NRUP. Project start-up is currently scheduled for 2025.
India ramps up nano fertilizer production
Private sector Indian fertilizer producer Coromandel International launched a new nanotechnology-based phosphate fertilizer, Nano DAP, in June.
“We have completed around 700 field trials… to establish the efficacy of the product. It has also received regulatory clearance,” the company said in a statement.
Coromandel is setting up a new production plant to manufacture Nano DAP in Andhra Pradesh to begin supplying the market this year.
The new product was developed at Coromandel’s R&D centre at the Indian Institute of Technology, Bombay. The Chennai-based company – part of Murugappa Group – said the efficacy, biosafety and toxicity of Nano DAP was investigated prior to its launch via extensive field studies.
“Nano DAP will go a long way in driving the sustainability of Indian farms through improving nutrient uptake, lowering water consumption and minimising environmental losses,” said Arun Alagappan, Coromandel’s executive vice-chairman.
The adoption of Nano DAP should also make farm economics more attractive by driving sustainable fertilizer usage and site-specific nutrient applications, Alagappan said. He also praised the Indian government for its help.
“I would like to thank the government for its continuous guidance, extending policy and regulatory support and providing the requisite impetus for adoption of new technologies in farming,” he said.
The Indian Farmers Fertilizer Cooperative Limited (IFFCO) is also scaling-up its production of nanotechnology fertilizers. Indian government minister Amit Shah officially launched IFFCO’s new liquid nano DAP product in April.
IFFCO will sell half-litre bottles of nano DAP at INR 600, less than half the current price of an equivalent 50 kg bag of conventional DAP. It will be available to farmers from the 2023 kharif season.
IFFCO is setting up production plants for nano DAP at Kalol and Kandla in Gujarat and Paradeep in Odisha. The Kalol plant is already in production and IFFCO says it will manufacture 50 million bottles on nano DAP this fiscal year, equivalent to 2.5 million tonnes of conventional DAP. The company plans to scale up nano DAP production to 180 million bottles by 2025/26.
“The launch of IFFCO’s liquid DAP nano is an important beginning towards making India self-reliant in the field of fertilizers,” Shah said. India currently imports around 10 million tonnes of DAP annually, with more than half of this volume sourced from West Asia and Jordan.
The start of nano DAP production follows IFFCO’s launch of nano urea liquid in June 2021 (Fertilizer International 503, p20). The company is mass producing half-litre bottles of the nano urea from three new production plants – Kalol, Gujurat and Aonla and Phulpur in Uttar Pradesh.
Initially, these sites will provide enough capacity to produce 140 million bottles annually, although IFFCO plans to ramp up production to 320 million bottles per year. The company calculates that producing nano urea at this scale will be enough to replace 13.7 million t/a of standard urea production.
Currently, Indian farmers have a financial incentive to overuse urea as it attracts significantly higher government subsidies relative to other types of fertilizer. IFFCO’s new nano urea liquid, in contrast, is a much more efficient nitrogen product. Each bottle – which contains 40,000 ppm of nitrogen – delivers enough crop nutrients to replace at least one 45 kilo bag of standard commodity urea, according to IFFCO.
IFFCO believes its new nano urea product can avoid many of the environmental problems associated with the use of standard granular urea, such as nitrous oxide and ammonia emissions, soil acidification and water eutrophication. As well as cutting environmental losses, IFFCO says nano urea is more sustainable in other ways: “It will reduce the input cost to farmer. Due to its small size, the bottle can be kept in the pocket and will significantly bring down the cost of logistics and warehousing also,” the company said.
Nano fertilizers have been heralded as a potential game changer for the market, although this does hinge on their acceptance by farmers. IFFCO is therefore planning a massive nationwide campaign to demonstrate and train farmers about the usage and application of nano urea.
Harmonising crop nutrition
Nutrien has launched a new product that uses a unique technology to evenly integrate sulphur, phosphate, and nitrogen within fertilizer granules.
Known as Smart Nutrition ™ MAP+MST ® (9-43-0-16S), Nutrien says the product is one of the most efficient dry fertilizer systems on the market – due to its ability to deliver key nutrients to crops when they need it most during the growing season. It is designed to optimise crop nutrition and boost plant growth while providing a familiar handling experience.
Micronized Sulphur Technology (MST), a patented process under license from Sulvaris Inc., converts elemental sulphur into ultra-fine, evenly sized particles with an average diameter of 15 microns. Smart Nutrition ™ MAP+MST ® integrates this micronised sulphur directly into the manufacturing process for monoammonium phosphate granules (MAP) – resulting in a highly uniform distribution of MST within the MAP granule.
Crops are dependent on microbes to help make sulphur available for root uptake. They do this by oxidising elemental sulphur – which is not accessible to plants – and transforming it into plant-available sulphate. However, if sulphur particles are large, the surface area exposed for oxidation is relatively small and microbial conversion rates are correspondingly slow. In contrast, when elemental sulphur particles are small, as with MST, there is a much larger surface area available and microbial activity increases substantially. This characteristic, together with the uniform distribution of MST within every MAP granule, offers more rapid conversion to sulphate and therefore better crop performance.
Due to these microscopic-level advantages, Smart Nutrition ™ MAP+MST ® provides versatility in sulphur management and distinct benefits over sulphate fertilizer products. The oxidation of elemental sulphur is a biological process and the rate at which MST is converted to sulphate is therefore highly temperature and moisture dependent.
When soils are cold, the MST remains in elemental form and remains resistant to leaching. As soil temperatures warm, biological activity increases and starts converting the elemental sulphur into sulphate for quick crop uptake. This allows Smart Nutrition ™ MAP+MST ® to be applied in the fall (autumn) season without fear of sulphate losses. This is followed by the subsequent slow-release of plant available sulphur in the spring to match crop needs.

In US field trials, Smart Nutrition ™ MAP+MST ® has been shown to deliver an adequate supply of sulphur to crops. For comparison purposes, trial results were compared to the equivalent sulphur supply rates from the application of ammonium sulphate (AMS), a readily available sulphate-sulphur source. Results indicate that Smart Nutrition ™ MAP+MST ® supplies adequate sulphur to maximise yields, matching the sulphur availability from AMS applications, while protecting the environment from potential leaching losses.
In summary, the key benefits of Smart Nutrition ™ MAP+MST ® (9-43-0-16S) include:
- High performance across diverse crop, soil and environmental conditions
- Increased nutrient availability for quicker crop uptake
- Slow-release behaviour keeps sulphur available throughout the growing season
- Optimised for dry fertilizer storage, handling, and spreading logistics
- Safe for seeds, handling and storage.
Tuning wastewater into fertilizers
Netherlands-based Fertipaq exhibited at this year’s IFA annual conference in Prague – attracting a lot of interest in their novel Fertipaq s600 organic sulphur fertilizer and their ‘circular economy’ business model.
Fertipaq is a wholly-owned subsidiary of Netherlands-headquartered water treatment technology company Paques. The company sources its concentrated liquid sulphur suspension fertilizer from wastewater treatment plants around the globe.
The Thiopaq desulphurisation units installed at these plants biologically treat and recover sulphur from wastewaters rich in hydrogen sulphide. The sulphur produced by these installations comes from a range of different industries including pulp and paper and food and beverage companies.
Fertipaq s600 has distinct advantages over sulphur products derived from oil and gas production, according to the company. Its hydrophilic properties and very fine particle size (<20 microns), for example, ensure the product is ‘rain fast’ and oxidises easily to supply crops with the sulphur they need under difficult growing conditions.
Fertipaq s600 is a liquid fertilizer and is therefore sprayable and – advantageously – can be added to and applied alongside nitrogen solutions. Applying sulphur and nitrogen together makes sense, suggests Fertipaq, as these two nutrients are closely connected. Sulphur plays a role in nitrogen uptake, for example, and without adequate nitrogen, photosynthesis cannot take place.
In addition to its concentrated liquid sulphur suspension product Fertipaq also manufactures and sells sulphur cake, a raw material with a high dry matter content that is suitable for various agricultural and horticultural applications.
References