Sulphur 407 Jul-Aug 2023
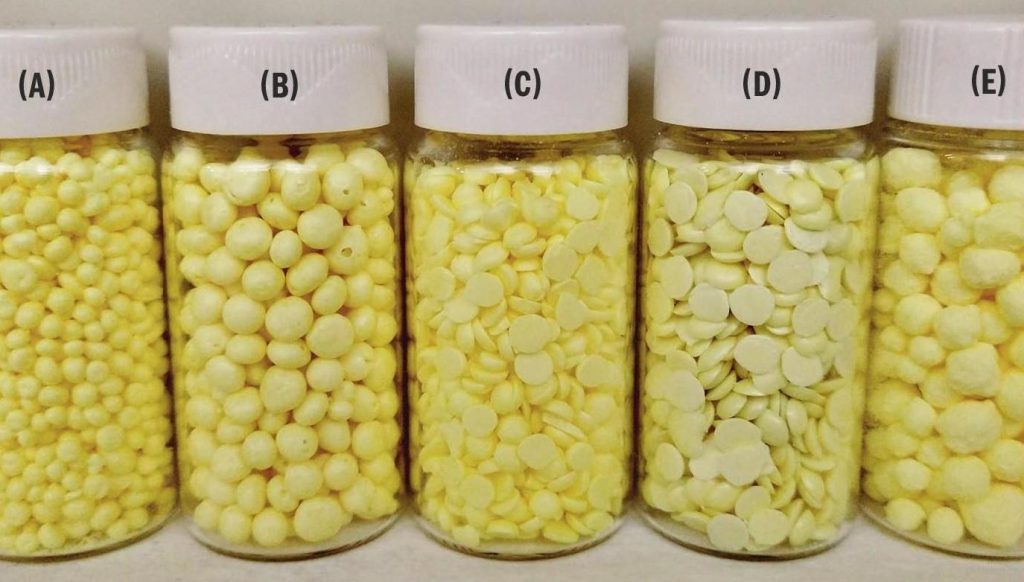
31 July 2023
The age and friability for different forms of elemental sulphur
SULPHUR PROPERTIES
The age and friability for different forms of elemental sulphur
Aged sulphur products can be friable and fragile, which can lead to sulphur dust during handling. Because sulphur dust can lead to dust explosions and excessive wet sulphur contact corrosion, shipping and handling specifications for the safest products are used by producers, shippers and consumers to limit dangerous incidents. Metastable polymeric sulphur in the solid product limits friability and is rarely cited as a measured quantity within sulphur specifications, but often discussed when explaining best handling and forming practices. In this article, ASRL discusses why sulphur tends to be friable and explores several measurements cited in many specification documents, with the purpose of focusing on several modern solid forms. In addition, the measurement of total and extraneous water is explored.
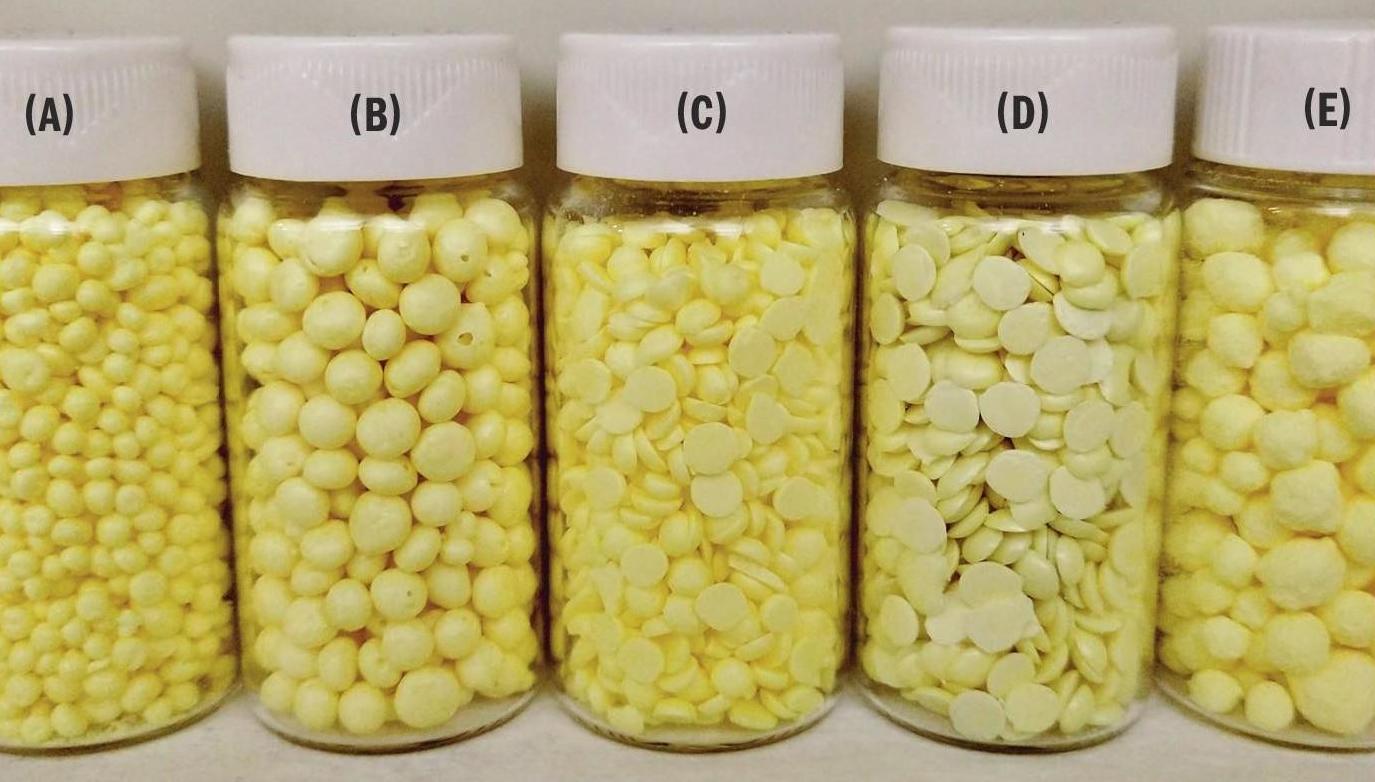
Commercially produced sulphur is available in the form of pastilles, granules or prills. To ensure production of a high-quality formed product, several properties are of interest to producers and consumers, such as H2 S content, friability (fragility), water content, porosity, etc. As discussed by many authors, sulphur’s properties change during the initial forming of the product, aging of the product and might differ depending on the use of degassed or non-degassed liquid sulphur. With controlled batches of commercial air prills, commercial granules, commercial pastilles, lab formed water prills, and lab formed pastilles (Fig. 1), ASRL has been following several properties during aging to improve the understanding of optimum handling and forming practices.
Upon solidification and further cooling, solid S8 transforms from monoclinic solid crystal structure (β-solid) to an orthorhombic crystal structure (α-solid) at T < 95.2°C (203°F)2,3 . Note that the monoclinic form can be kinetically stable below 95.2°C for some time; therefore, it is important to recognise that the solid β-α phase transition may not occur immediately during the formation process and some crystal transition may occur during handling or storage. The transition is exothermic and will exhibit a maximum thermodynamic temperature halt at T = 95.2°C, i.e., if heat is not taken away or if the transition begins at a warm temperature, the internal temperature of a sulphur stockpile could reach 95°C upon transformation. For this and other reasons discussed later, it is important to store solid sulphur at cooler temperatures (T< 50°C).
While the orthorhombic solid is thermodynamically favourable during shipping and handling, this form naturally contains internal shear stress due to changing the crystal unit cell angles from 96° to 90° during the solid β-α phase transition (see Fig. 2)3-6 . Note that if the unit cell angles remained the same during the transition, a density change (volume reduction) would not cause shear stress, thus it is not entirely correct to assume that the density change alone induces solid fractures in solid sulphur particles.
The overall consequence of this transition is that pure S8 (as an α-solid) can be very brittle or friable, which leads to extraneous sulphur dust and fines during product handling. This dust can lead to dangerous and explosive situations. The presence of polymeric sulphur (Sµ ) helps to bind and support these stressed shear planes (crystallite disconnects); thus, most forming and handling processes aim to insure some polymeric sulphur content in the product for safety reasons. Note that sulphur specifications rarely include a polymeric sulphur content, which is a critical value.
ASRL and others had previously shown that sulphur with a lower Sµ content results in a higher occurrence of fines when subjected to Stress Level II testing9,10 . Because Sµ is not thermodynamically stable in the solid sulphur phase at elevated temperature, a warmer solid can lead to conversion to S8 , whereas at colder temperatures the polymeric sulphur is kinetically stable for very long periods of time.
S8 + Sµ ➝ S8 (1)
There are multiple questions which can be asked when determining why a solid sulphur product could contain low levels of polymeric sulphur, including:
- How fast was the sulphur quenched from liquid to solid temperatures?
- How cold was the stockpiling temperature of the solid?
- What temperature (and time) was the solid sulphur stored at prior to shipping/analysing?
- Was there any extraneous dissolved chemical left in the sulphur before forming?
- Was the liquid sulphur degassed?
- What temperature was the liquid stored at prior to forming the solid?
In 2020, the first part of this study assessed the last two questions and concluded that fully degassing sulphur (with zero dissolved H2 S; see Fig. 3) did not significantly alter the polymeric content of the liquid sulphur1 , suggesting that over-degassing will not compromise product strength, as long as degassing catalysts do not remain in the product. Here polymeric sulphur is measured 100as the CS2 insoluble fraction, S 10μ , if carbon content and ash are 0 low1 . While degassing H2 S is beneficial for safety reasons and over-degassing may lead to excess SO2 emissions, there is little reason to believe that degassing will improve the quality (strength) of a sulphur product. Thus, H2 Sx in solid sulphur is not necessary. In fact, several of the products investigated in this study were completely free of dissolved H2 S.
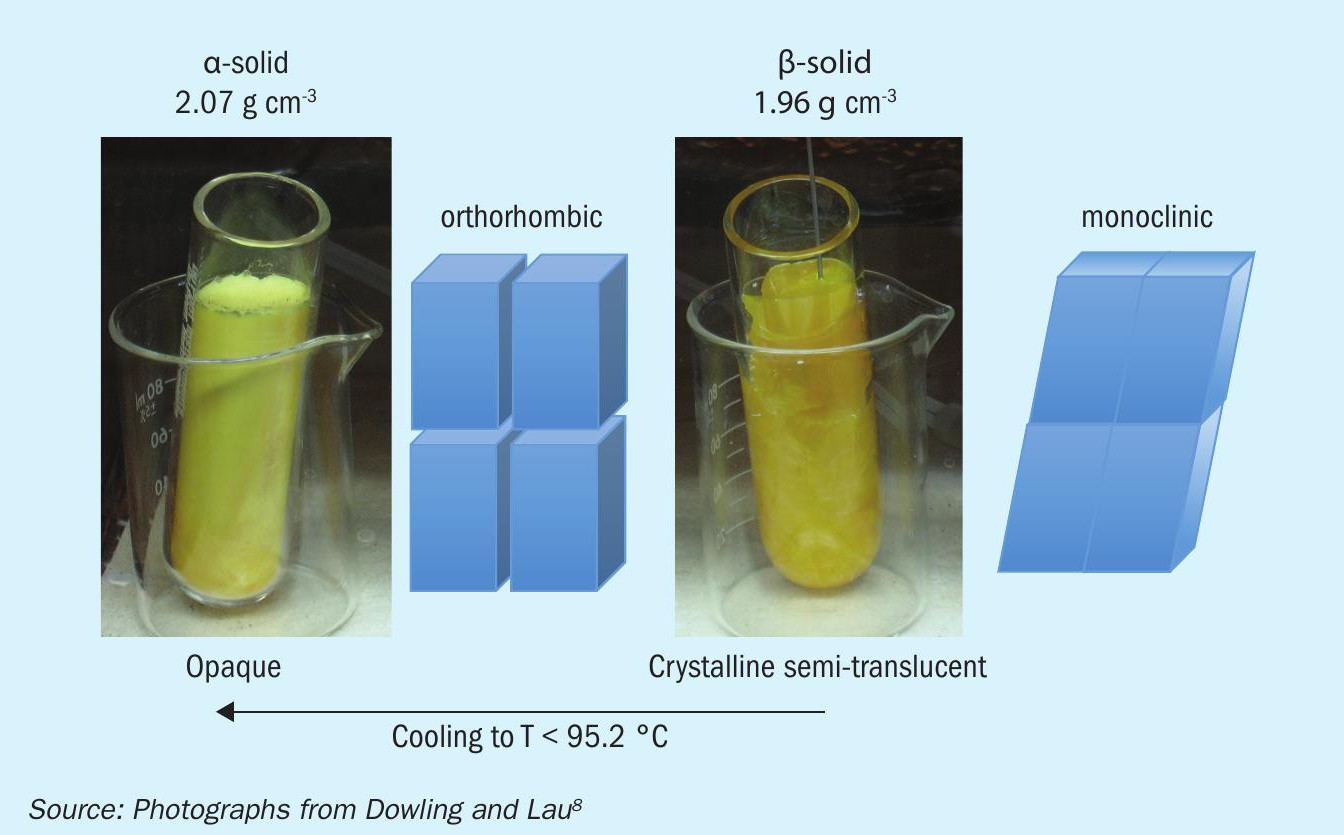
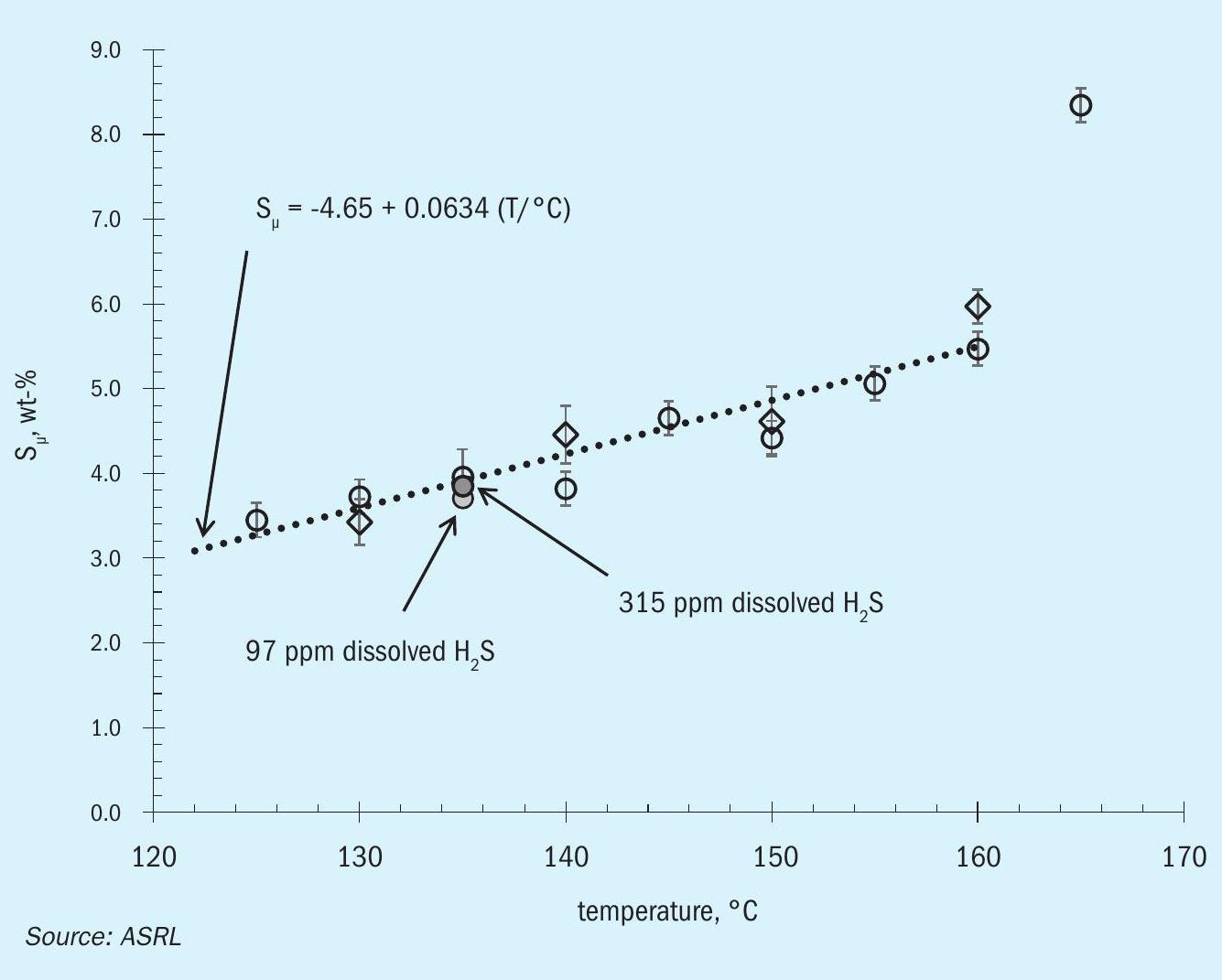
A previous ASRL study also concluded that liquid sulphur storage temperatures between 125 and 160°C do not significantly influence the polymeric sulphur before forming the solid. The current study is an attempt at answering the other questions and aims to quantify the polymeric sulphur decay after solidification and over time. Finally, ASRL took a brief look at the water content of formed sulphur, where two types of water can be measured.
In order to produce formed prills within the laboratory, ASRL developed its own lab-scale wet forming process. Similarly, ASRL recently commissioned an IPCO Rotoform MI pastillation system to allow for production of small batches of lab-scale pastilles. ASRL also studied field samples of granulated sulphur, pastilles and air-prilled sulphur. While these various forms of sulphur are not directly comparable to each other in terms of morphology, they are all considered premium products and studying their properties allowed ASRL to determine what factors may have an impact on product quality during storage and aging.
Sulphur forms
Commercial sulphur forms
The two main commercial sulphur forms used in this study were (C) Rotoform pastilles obtained from the Shell Shantz Gas Plant (> 99.993% purity by combustion) and (A) air-prilled sulphur from the Keyera Strachan Gas Plant (> 99.995% purity by combustion)1 . Note that these materials were seven and four years old respectively and infra-red (IR) absorbance showed no detectable dissolved H2 S or hydrocarbon in the melts. Additional testing was also performed with (E) commercially produced granules obtained from the Waterton Complex. This product was approximately one month old when used for this project.
(B) Laboratory wet forming
The lab-scale wet forming process consisted of a custom machined sulphur pot (~5 L), sulphur delivery line (1 /8 -inch stainless steel) and a circulating water reservoir (~63 L). The sulphur pot, and delivery line were wrapped in resistive heating ropes and insulation. The water in the reservoir was circulated using a Fluval® SEA CP3 Circulation Pump, and ca. 0.5 g of sodium dodecyl sulphate was added to the reservoir prior to forming to prevent surface aggregation. The sulphur pot was pressurised to p ≈ 20 psig with nitrogen, to facilitate sulphur flow through the1 /8 -inch delivery line (see Fig. 4).
Prior to the forming step, a portion of the liquid sulphur was allowed to flow through the delivery line and was directed to a waste collection container to allow for temperature stabilisation of the delivery line. Molten sulphur flow was then stopped briefly, and the outlet of the delivery line was positioned at < 1 cm from the surface of the water. The sulphur pot outlet valve was manually controlled to ensure that the sulphur was emitted as continuous individual droplets (ca. 2 drops s-1 ). The water circulation allowed the molten droplets enough residence time to completely solidify before hitting the base of the reservoir. At the end of the process, the valve was closed, and the product was collected and allowed to air dry prior to analysis.
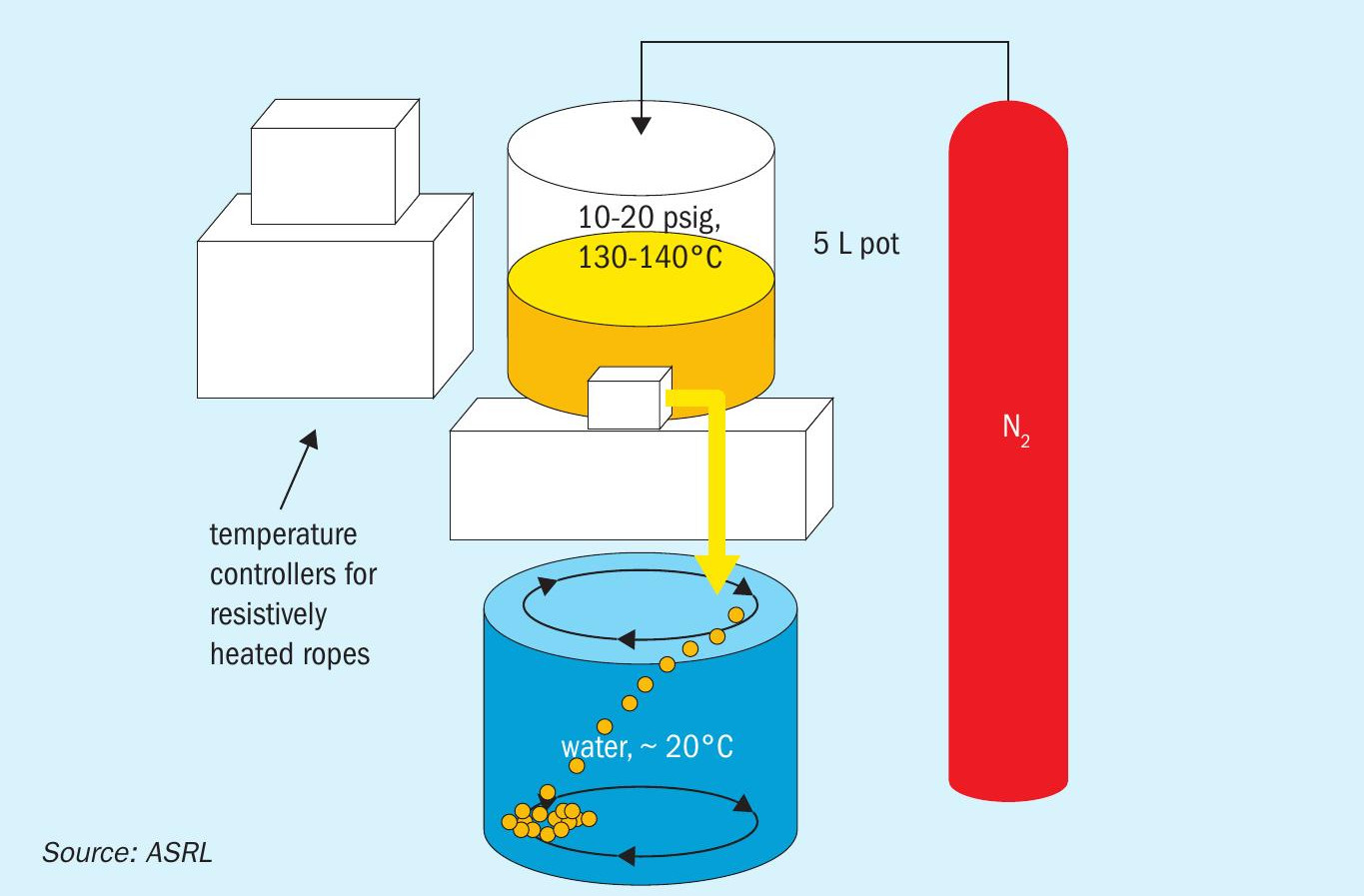
(D) Laboratory pastillation
The lab-scale pastillation process setup consisted primarily of a bespoke sulphur pot (~39 L) and a newly commissioned IPCO Rotoform MI lab-scale pastillator (see Fig. 5). The sulphur pot utilised a countercurrent heat exchange system via heated silicone oil, supplied from a LAUDA® Proline P18 heated circulating bath. Once loaded with solid sulphur, the vessel lid was hermetically sealed to prevent the escape of sulphur vapours.
The sulphur vessel was connected to the Rotoform MI system via a1 /2 -inch stainless steel braided delivery line. The delivery line and flange connections were resistively heated via heat ropes to prevent sulphur solidification and cold spots. The rotating sulphur outlet drum on the Rotoform MI was heated by a heated silicone oil loop supplied from a VWR® 1136D heated circulating bath. The Rotoform MI system was principally comprised of a steel belt conveyor system and a rotating sulphur outlet drum, set at 10.3 m min-1 and 13.6 m min-1 speeds, respectively. Cooling water was sprayed underneath the stainless-steel belt to speed up solidification of the molten product as it moved down the conveyor line.
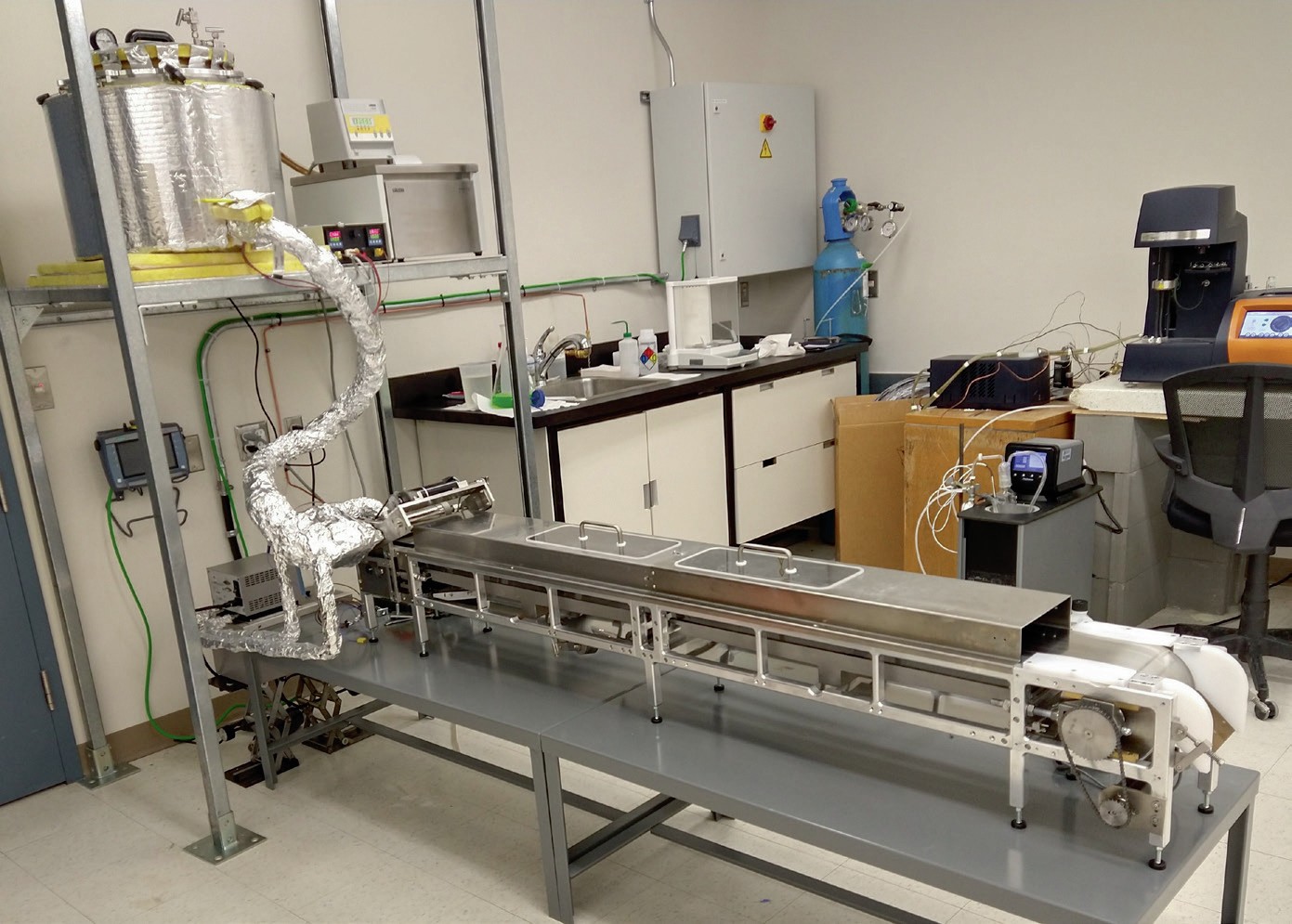
The outlet valve of the sulphur pot was slowly opened while the rotating drum spun, with an operator controlling the valve until the product had a consistent size/ shape. The uniform product was then collected for analysis.
Sulphur properties testing methods
Sµ content
Polymeric sulphur content was determined as CS2 insoluble sulphur by dissolving ca. 10 g of sulphur sample in carbon disulphide, followed by filtering the solution through a pre-weighed medium (10-15 µm) 30 mL sintered stemless Pyrex funnel. The funnel was then dried in a vacuum oven and weighed again to obtain the weight of insoluble Sµ material. Note that the first part of this study confirmed that no detectable amounts of other CS2 insoluble impurities were present in the stock sulphur1 .
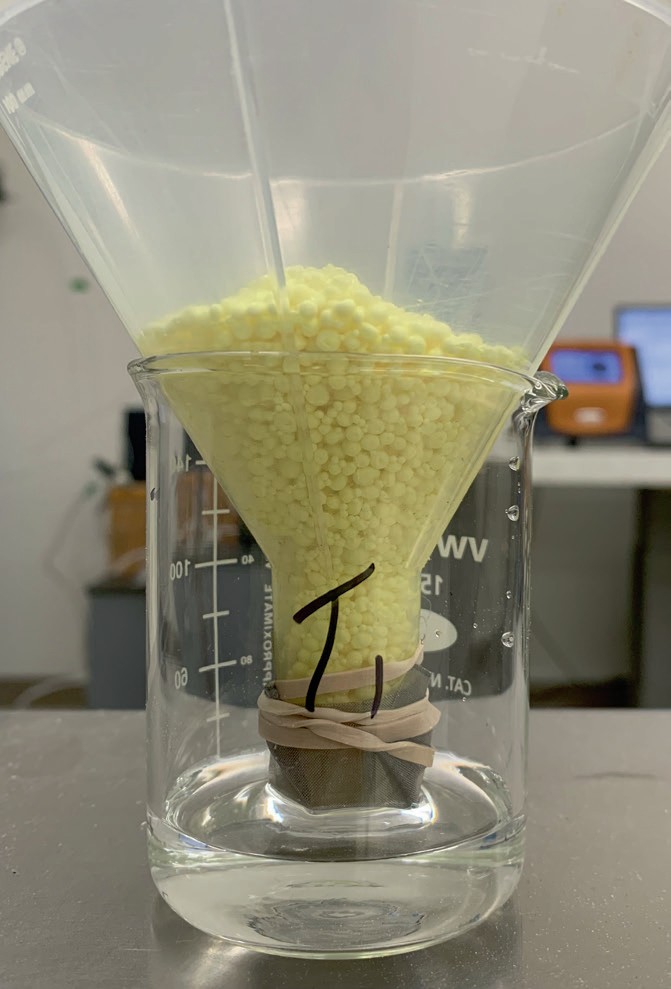
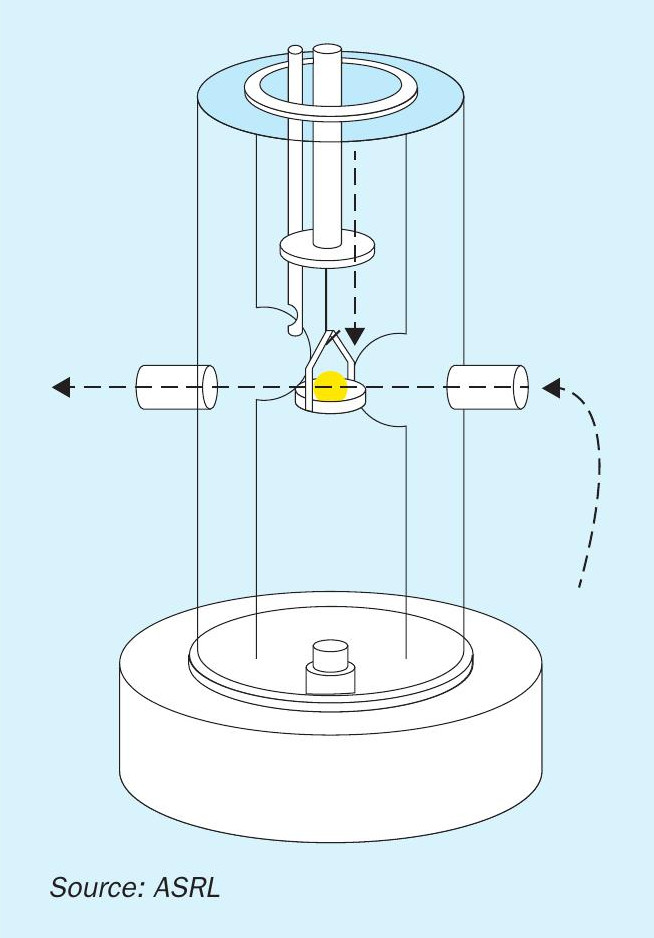
Sµ decomposition
For tests requiring holding sulphur at a certain temperature to investigate Sµ decomposition within the formed solid product, ca. 1.3 kg sulphur was loaded into a Bruker 450-GC oven. It was then heated to the target temperature (50-100°C) for the desired time. Sµ content was then determined after quenching to room temperature.
Interstitial water retention (15-minute drainage)
To determine the interstitial water retention of sulphur forms, a mass of ca. 20 g of sulphur form was loaded into a 125 mL beaker and covered with water. The mixture was allowed to sit for 30 min and was then transferred to a pre-weighed beaker-funnel system with a metal mesh (150 µm) occluding the funnel’s outlet (Fig. 6). The mixture was allowed to drain for 15 minutes into the beaker. The resulting wet sulphur was then transferred into a pre-weighed crystallising dish and weighed to determine the water retained by the sulphur form.
Thermogravimetric analysis (TGA)
A TA Instruments TGA 55 apparatus was used to determine if internal water was occluded within the sulphur product (Fig. 7). A single sulphur form was placed on a 100 µL platinum pan at 25 to 30°C, followed by a temperature ramp at a specified heating rate (2.5 to 25°C min-1 ) until it reached a temperature of 145 to 150°C. A dry helium gas purge rate of 30 mL min-1 was used.
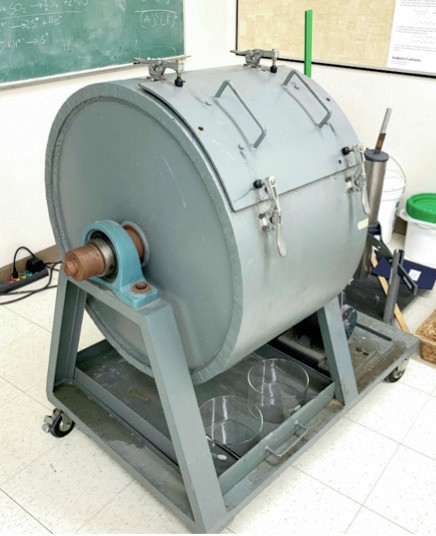
Surface area and porosity
The Braunauer, Emmett and Teller (BET)11 specific surface areas and Barrett, Joyner and Halenda (BJH)12 pore size distributions for sulphur samples were determined via N2 physisorption at -197°C on a Micromeritics 3Flex Surface Characterization Analyzer. The samples were degassed ex-situ at room temperature conditions and in-situ (T = 30.0°C) under vacuum to remove volatile species prior to analysis.
Particle size distribution
To determine the particle size distribution for a sulphur sample, ca. 1 kg of formed sulphur (produced at least 20 days prior) was loaded into a pre-weighed sieve stack (>4.75 mm, >2.36 mm, >1.18 mm, >0.600 mm, >0.300 mm, <0.300 mm) on a Retsch AS200 Sieve Shaker apparatus. The apparatus sieved the sample for 20 minutes continuously at a 40% amplitude. The sieves were then reweighed to determine the particle size distribution of the sample.
Stress level II (SLII)
To determine the extent of breakdown of a sulphur sample via a Stress Level II Test, a pre-weighed mass of sulphur (ca. 1 kg) was loaded into a large iron rotating drum (76 cm diameter) equipped with an internal protruding baffle (9 cm) and fully rotated 40 ± 1 times (Fig. 8). The resulting sample was then scrupulously collected from the drum to minimise product loss. The sample was then loaded into a pre-weighed sieve stack (>4.75 mm, >2.36 mm, >1.18 mm, >0.600 mm, >0.300 mm, <0.300 mm) on a Retsch AS200 Sieve Shaker apparatus, using the same procedure as before.

Results and discussion
The sulphur industry in general, recognises several tests to determine if a sulphur form is of sufficient quality to be used by customers. The pass/fail criteria are not universal but are in large, inspired by the Sulphur Development Institute of Canada (SUDIC) recommendations from 1978. Typically, criteria include shape, size, size distribution, friability, bulk density, compaction breakdown, angle of repose, moisture content and chemical purity. Additional specifications are often negotiated between different parties when trading sulphur. These typically specify the maximum concentration of different impurities, for example, ash, carbon, hydrogen sulphide, arsenic, selenium, tellurium, water, acidity, chloride, etc.13 . While only a few of these parameters were studied within the current project, they provided valuable information. Interestingly enough, CS2 insoluble or polymeric sulphur content is rarely specified or discussed despite our understanding that polymeric sulphur is required for sulphur strength and dust mitigation.
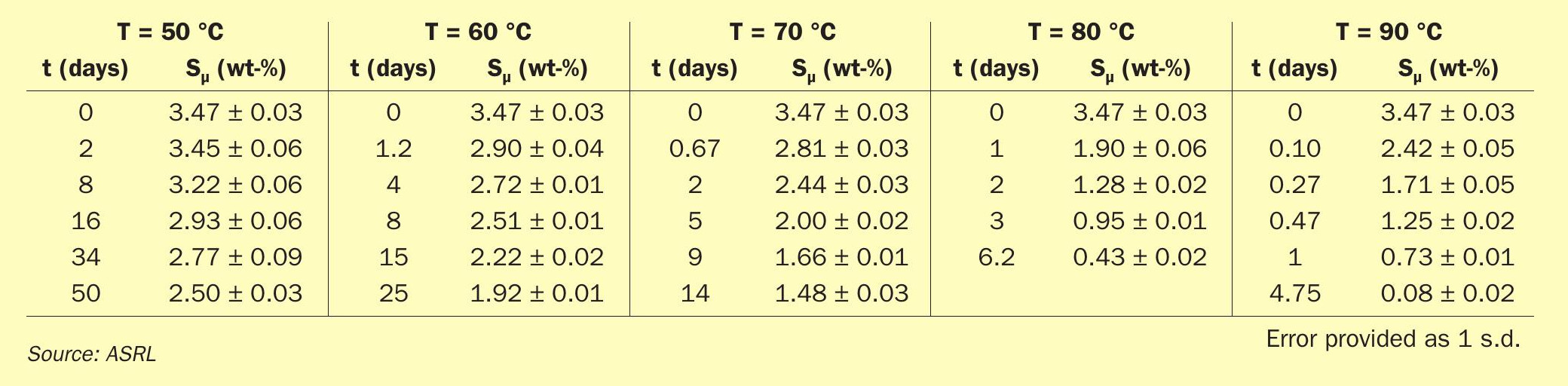
Initial sulphur fines
Initially, the different forms of sulphur used in this study were tested for particle size distribution, as this is one of the tests that is typically quoted to determine if a form is a premium product. This test was performed on each form, prior to any heat treatment. Results are shown in Table 1.
The 1978 SUDIC specifications state that a premium product should contain < 0.1 wt-% of fines (< 300 μm). Most forms tested met this specification regarding fines. Note however, that the commercial pastilles contained marginally more fines, with 0.38 wt-%. 0.38 wt-% is still far below the 5% sited by SUDIC for the minimum specification. The fact that the laboratory version (custom pastilles) contained only 0.03 wt-% fines seems to suggest that this form may also meet the specification when freshly produced but that perhaps, through handling the sample, it had degraded further. Later results will show that these pastilles produced virtually the same quantity of fines, following SLII stress tests.
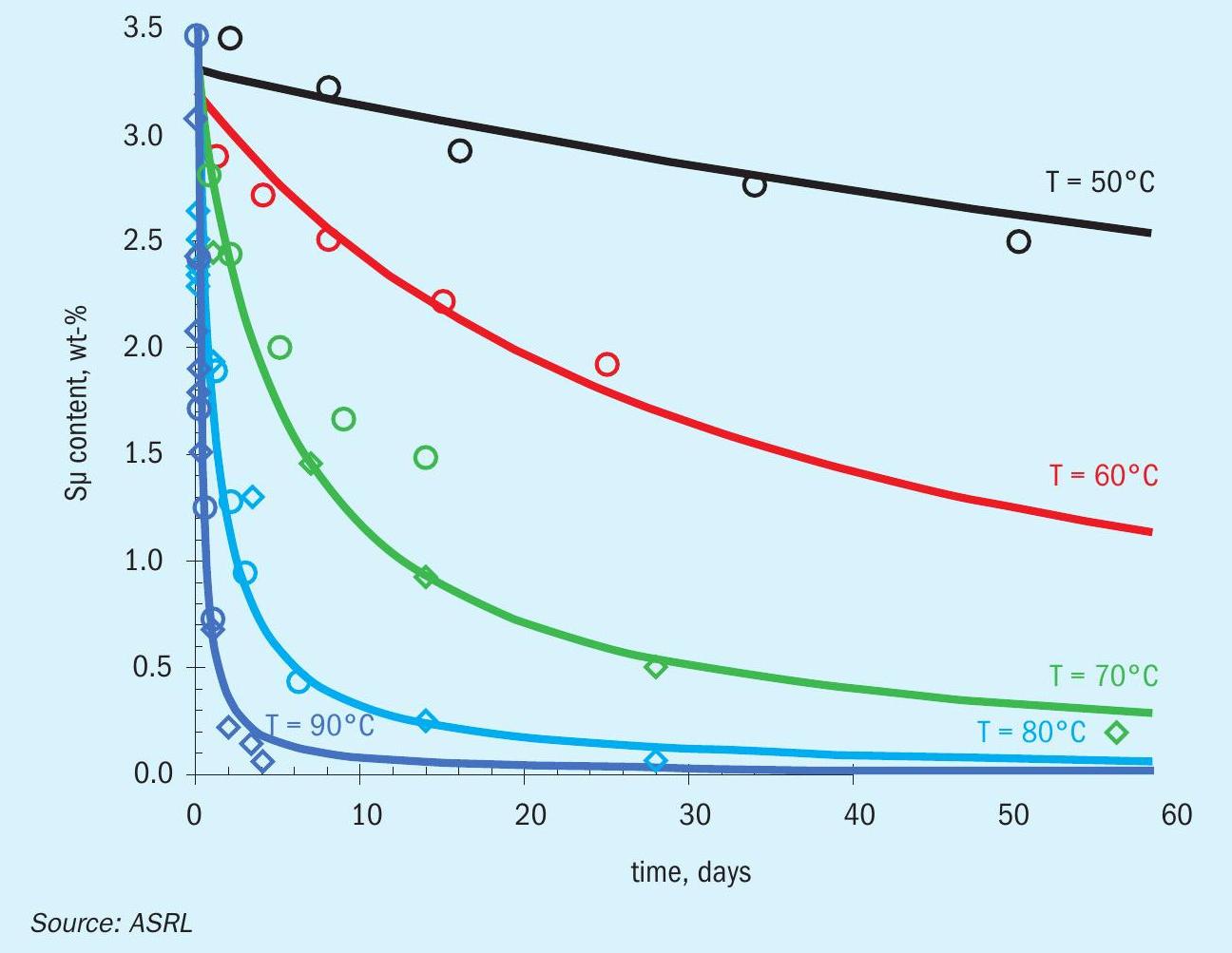
Polymeric sulphur decay
As discussed in the introduction, the friability of elemental sulphur and its propensity to form dust should be significantly affected by the amount of polymeric sulphur retained in the product (Sµ as a CS2 insoluble wt-%). Polymeric sulphur serves to bind crystallites which undergo stress due to the monoclinic to orthorhombic crystal transition. ASRL showed previously that the liquid storage temperature before forming a product has little effect on the retained polymeric sulphur in the formed solid; however, ASRL also knows that warm solid sulphur can lose its polymeric sulphur over time.
In order to get a clearer understanding of how fast polymeric sulphur would deteriorate when solid sulphur is stored at higher temperatures, ASRL measured the Sµ content for commercial air prills at T = 50 to 90°C (Fig. 9 and Table 2). Fig. 9 also includes data from Dowling and Wan, where their data at 70 and 90°C complement the new data reported in table 2. Dowling and Wan were investigating sulphur block storage, which would suffer the same polymeric decay; however, friability would be more important for block integrity. ASRL found that the formed sulphur still contained Sµ > 3.4 wt-% after more than 4 years of being stored in our laboratories (ca. 20°C), which indicates that sulphur can maintain its important polymeric binder for a very long time, provided that the storage temperature is cool enough.
Fig. 9 shows that orthorhombic sulphur stored above 50°C shows significant loss of polymeric sulphur over time, where warmer storage temperature shows a more significant rate of decay. The decay of polymeric sulphur shown in Fig. 9 has been fit using the global data and an exponential decay (shown in solid lines within Fig. 9):
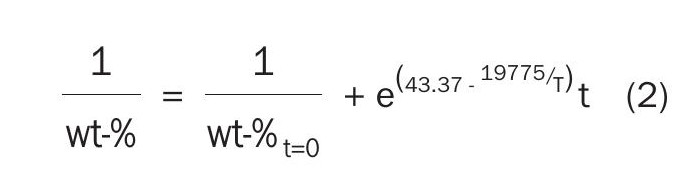
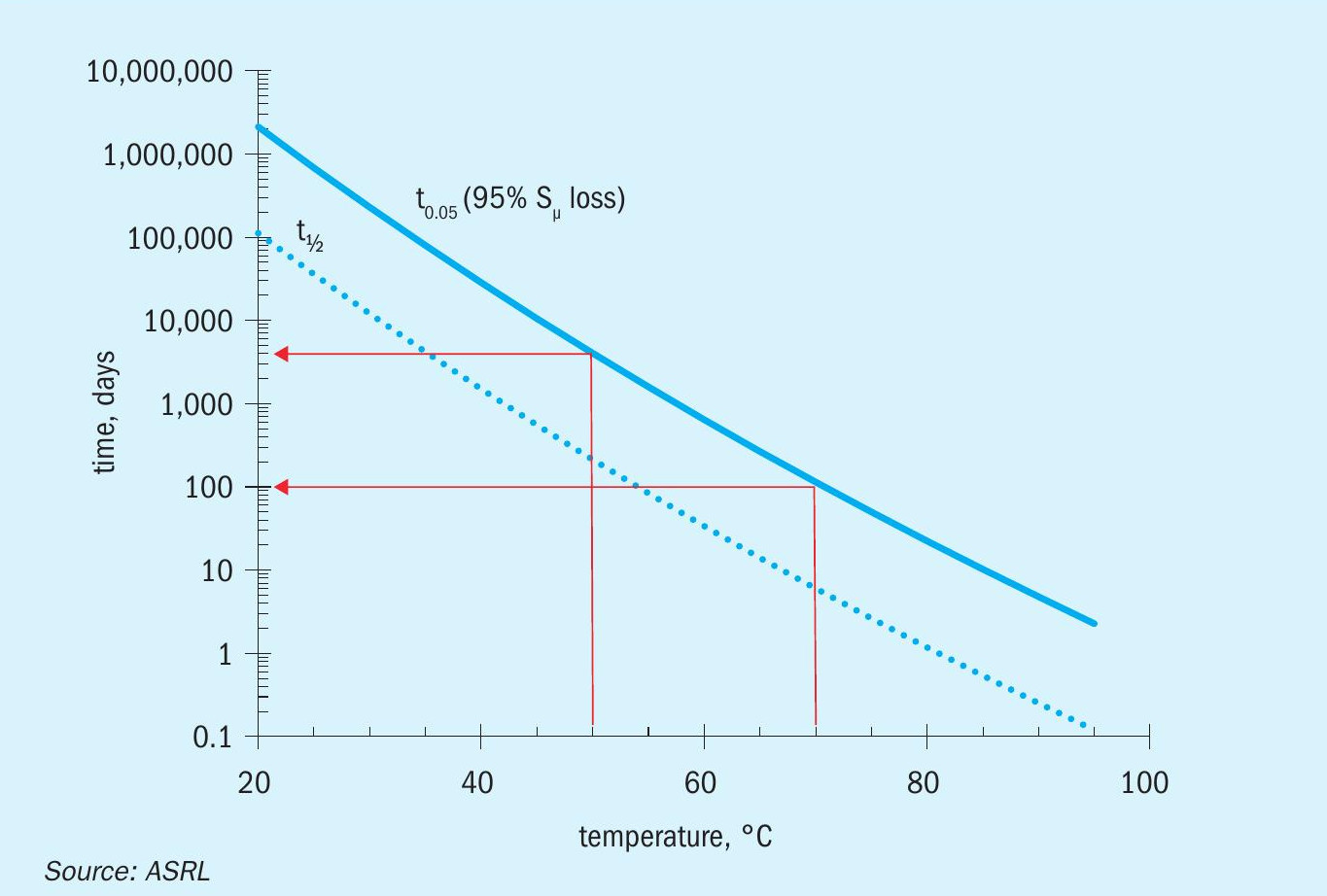
In Equation 2, the temperature, T, is in units of Kelvin and time, t, is in seconds. Using this equation, both the half-life, t0.5, or when one expects to lose 95% of the initial sulphur, t0.95 can be calculated. These times versus the temperature are shown in Fig. 10. Using Fig. 10 for a storage temperature of 50°C, one can see that 95% of the polymeric sulphur will be lost after approximately ten years; however, at a nominal storage temperature of 70°C, 95% of the polymeric sulphur will be lost at approximately 100 days. 90°C storage temperatures would result in less than half of the initial polymeric sulphur in less than seven hours and less than 5% of the initial polymeric sulphur in five days.
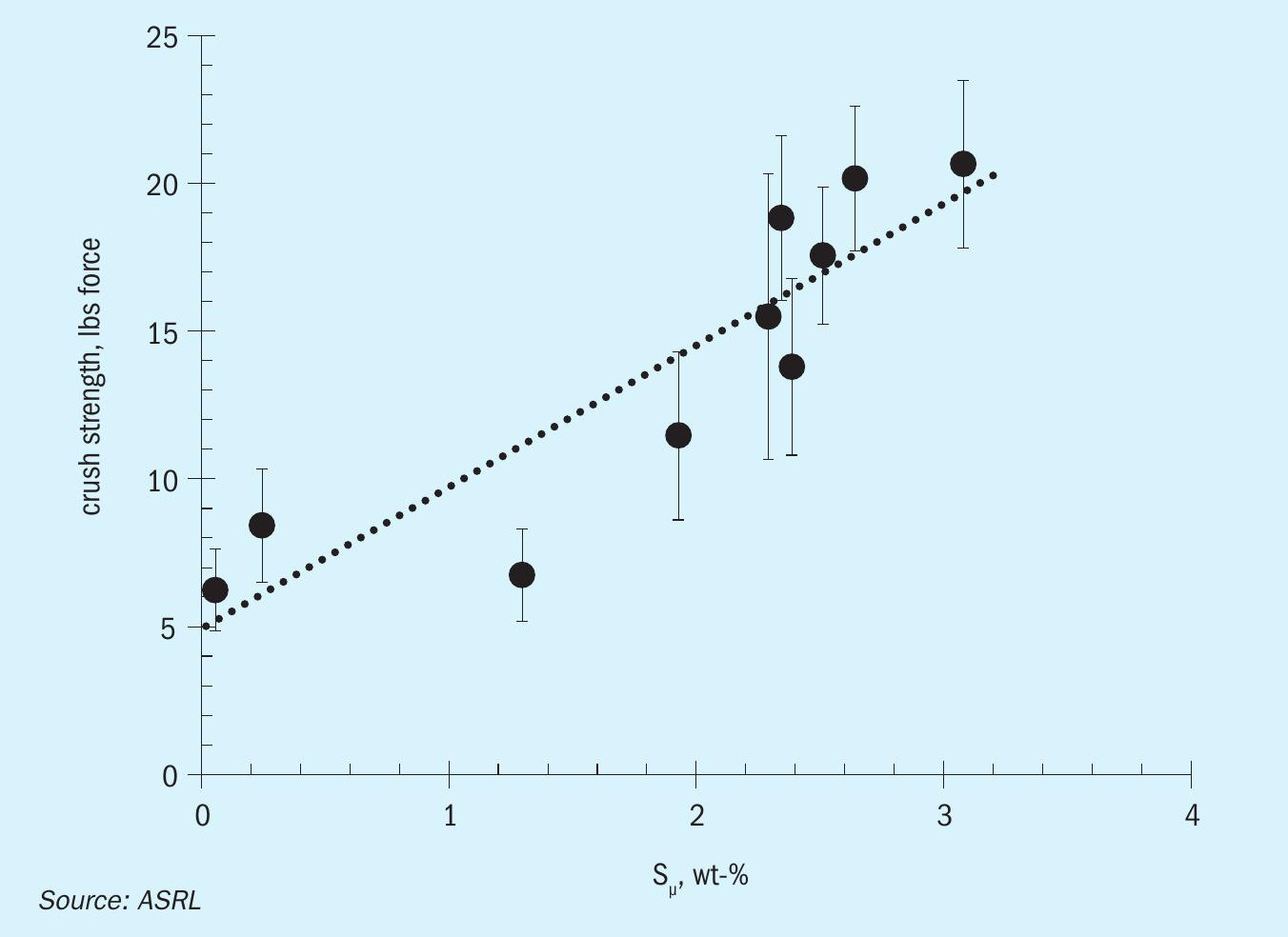
To make matters a little more complicated, sulphur initially solidifies by crystalising in the monoclinic form. The monoclinic form can persist for some time below its thermodynamic transition point of 95.2°C2 . If sulphur products were to be piled up before this transition occurred,the exothermic transition would spontaneously heat the interior of the stockpile (to a maximum temperature of 95°C).This form of sulphur appears translucent and orange, versus the opaque and yellow orthorhombic form. ASRL also measured the decay of polymeric sulphur in the supercooled monoclinic form, by heating to 100°C (converting to monoclinic) and then cooling to 90°C (metastable monoclinic). The rate of decay was ten times faster than in the orthorhombic form.Thus, monoclinic sulphur could lose 95% of its polymeric sulphur in ten days at 70°C or 12 hours at 90°C. Thus, there are two issues with stockpiling sulphur in its monoclinic form: (1) it could self-heat if the heat from the exothermic phase change can’t be removed and (2) the polymeric sulphur will decay much faster if the heat is not removed. Another added issue is that monoclinic sulphur products may tend to agglomerate.
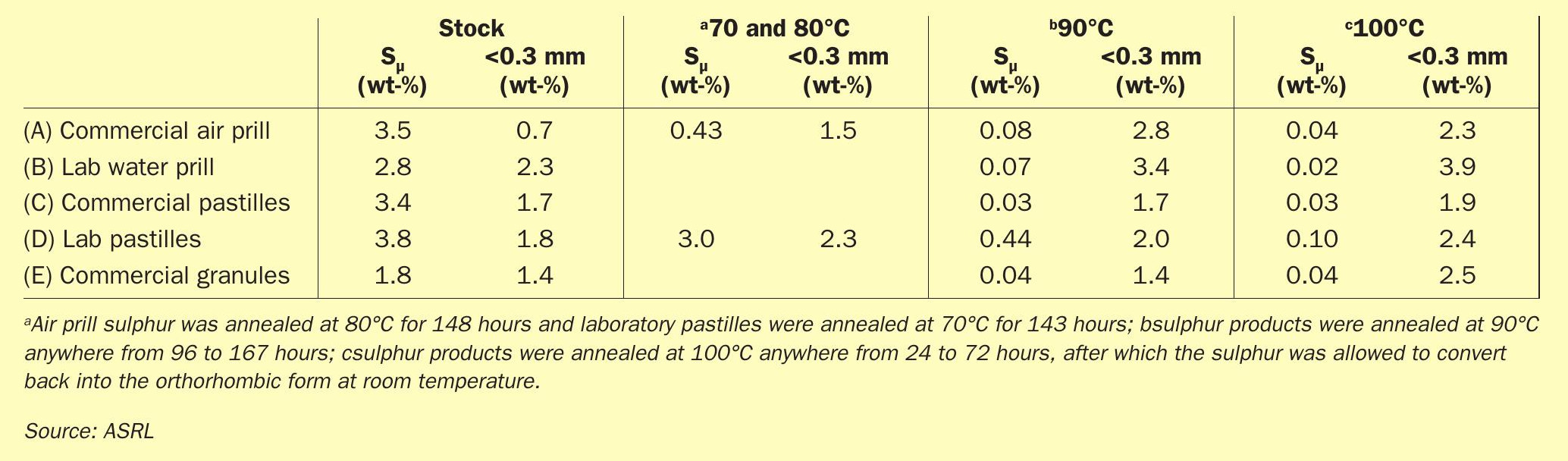
Based on the previous calculations, storage temperatures at 50°C (internal stockpile temperature) or less still provides a cold enough environment for polymeric sulphur to persist for years. If sulphur forms are initially handled in the monoclinic form (translucent and slightly orange), then the heat from the solid transition will need to be monitored or removed (through perhaps smaller piles and/or aerial fans).
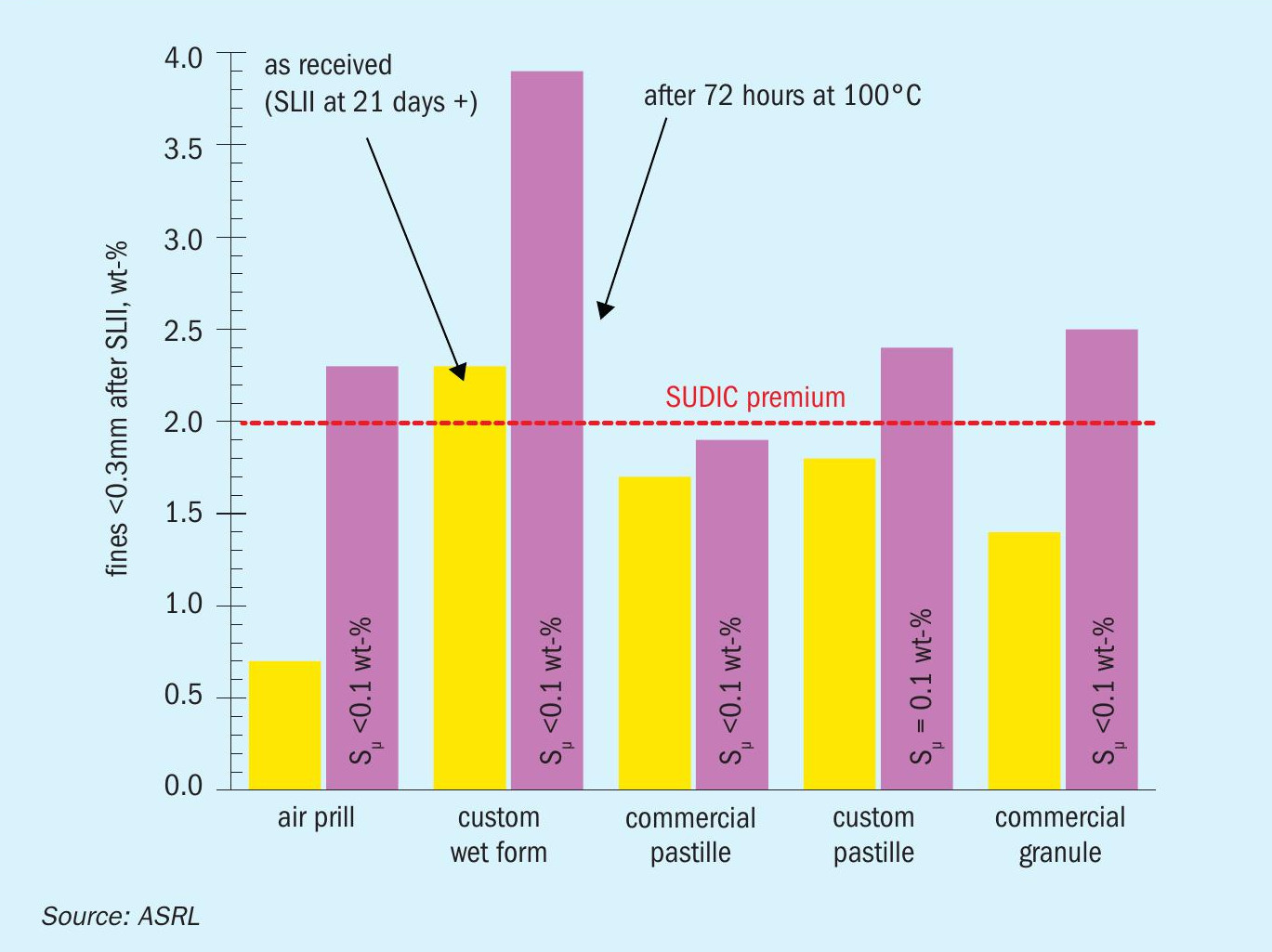
Friability, strength and dust
Dowling and Wan (2012) previously showed that the crush strength of sulphur was correlated with the polymeric content (Fig. 11)14 . Their study focused on formed sulphur blocks, where laboratory sulphur slabs were tested for compressive strength using a load cell. ASRL attempted to measure the crush strength of the various sulphur products using the same load cell apparatus; however, the apparatus can only measure one prill or pastille at a time and the results are not reproducible. The variability in morphology of the products requires other methods. ASRL has commissioned a bulk crush strength apparatus to be reported to ASRL member companies in a future report.
Single prill or pastille crush strength is not a specification that is typically reported, likely because the results are inconsistent and not directly comparable between different sulphur forms. In this study ASRL sought to show that Sµ has a significant impact on formed sulphur quality via the Stress Level II test, which is a more traditional test for sulphur product friability. Results are shown in Table 3. To obtain different concentrations of Sµ , the sulphur forms were held at 70, 80, 90 and 100 °C for various lengths of time.
The SUDIC specifications mention that for premium sulphur products, fines following the SLII test should be < 2 wt-%13 . Based on the results in Table 3, all tested forms would have met this criterion, except for the ASRL custom wet form which could not be considered a premium form as it produced 2.3 wt-% fines. A closer look at the fines results from Table 3 show a soft correlation between polymeric content and produced fines. Fig. 12 shows a comparison between the SLII fines for the non-annealed sulphur products (high polymeric content) and the fines produced from product which was annealed at 100°C (low-polymeric sulphur). The annealing at 100°C and nearly complete removal of polymeric sulphur resulted in a failure for all but one of the sulphur forms.
While it can be seen that the SLII fines increase with reduced polymeric content, it is noted that the SLII test is not as sensitive as one might expect for modern sulphur products. When SUDIC and other groups were looking into SLII test fines to assess sulphur products, slate sulphur was still commercial. It was these forms which were severely failing the SLII test, whereas all the modern forms perform quite well. In terms of laboratory time and reproducibility, it might be easier to measure and report polymeric content in the future, where all products with > 0.4 wt-% polymeric sulphur passed the SLII test. A more precise target for polymeric sulphur may be revealed in future bulk crush tests.
Finally, while sulphur storage temperature, solid phase and polymeric content must be considered to reduce the risk of dust, handling practices are just as important.
It was also decided to investigate the effect of the presence of different amines on Sµ and SLII test performance. Amines are often used to breakdown polysulfane bound H2 S as degassing catalysts; however, it’s well known that too much amine or not allowing amine to evaporate will compromise the product. While ASRL could dose the sulphur feed for the laboratory pastilles with amines, it was difficult to determine the actual amount in the liquid sulphur before forming. ASRL chose to assume that all the amine put into the feed vessel resided in the liquid sulphur. 12-14 ppm of MEA, MDEA and morpholine did not change the polymeric content or the SLII fines. 100 ppm of morpholine in the elemental sulphur resulted in no polymeric sulphur; however, the SLII test passed at 1.4 wt-% fines. Again, this may point to the SLII test as not being as rigorous for modern forms of sulphur. Future investigations might consider looking at how the polymeric content decays in the presence of an amine.
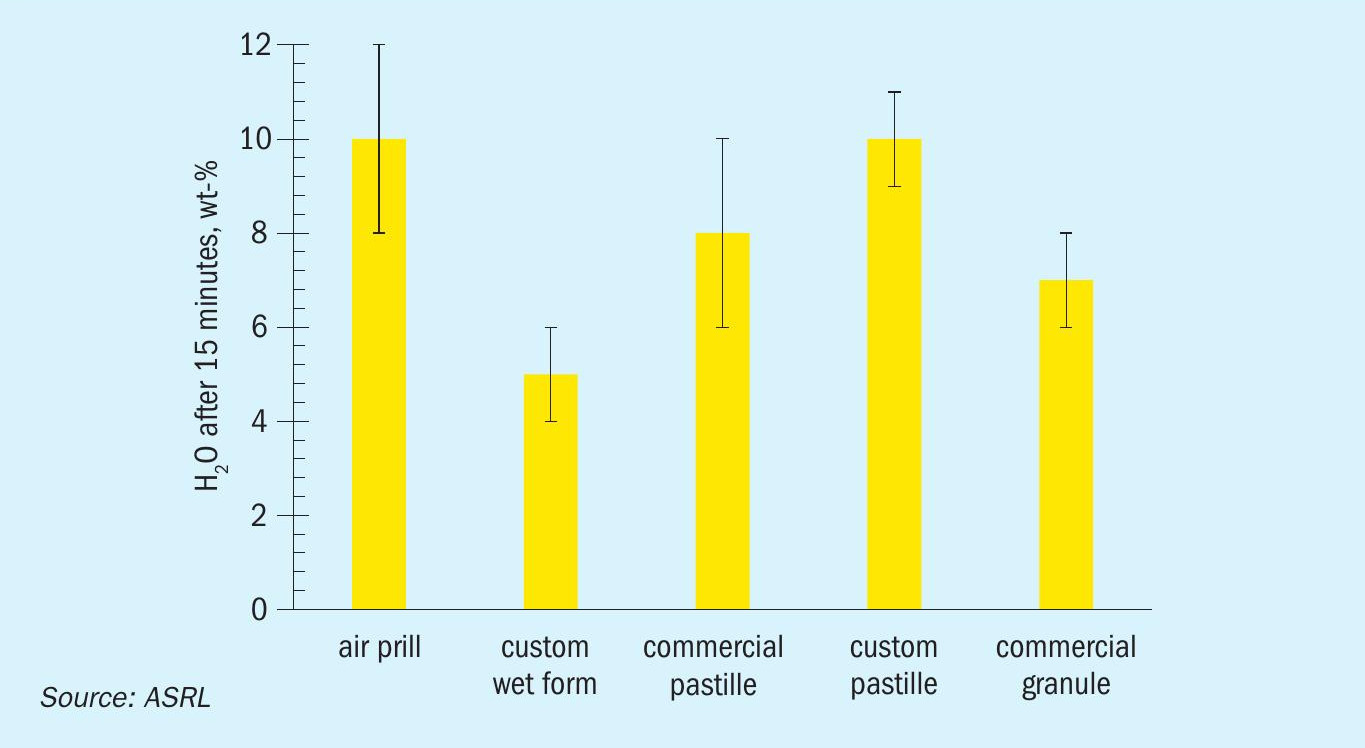
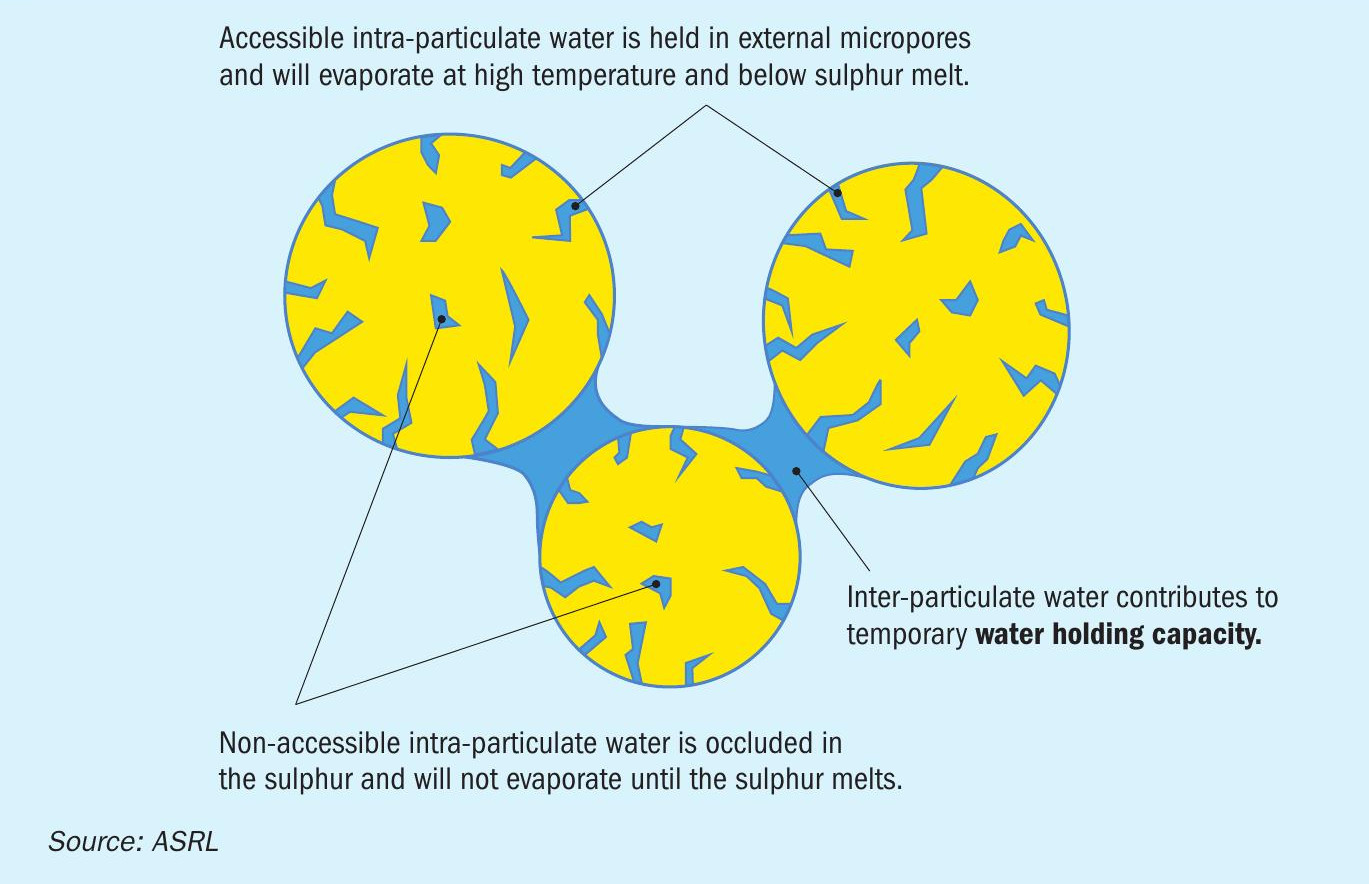
Water and sulphur products
After looking at polymeric content effects or addition of amine contaminants, the different forms were also tested for how much water remains on the particles after soaking them with water and allowing drainage for 15 minutes. This can approximate to, for example, how the top of a pile of sulphur would behave after a heavy rainfall. Results are shown in Fig. 13 and reported in Table 4. Note that this test assumes that the interaction between the wall and the particles are the same as the interactions between particles and that any wall effects are negligible. The application of water is necessary during handling to reduce dust formation evolution, but this is not typically enough to appreciably increase water content. Due to the extreme nature of our test, the measured values shown in Fig. 13 for all form types are much higher than the recommendations by SUDIC (< 0.5 – 1.5 wt-%). It is important to note that the water retention test results should be viewed as the maximum amount of water that could exist within a pile of formed sulphur 15 minutes after a rainfall (see Fig. 14), whereas the SUDIC values represent an arbitrary target, aimed at lowering transport costs13 . Note that this 15 minute drainage would eventually evaporate on its own.
Each form also was tested for its internal water content after being wetted and allowed to dry, using thermogravimetric analysis. Prior to testing, each form was allowed to air dry at room temperature for a minimum of 48 hours. This allowed any external water to evaporate. The water remaining within the sulphur form can either be trapped within accessible pores or within inaccessible pores, occluded within each particle. The water within the inaccessible pores is only accessible once the sulphur particle is melted (Fig. 14). A 5 °C min-1 heating rate led to less noisy scans and provided the best sensitivity definition. The overlay of the TGA thermogram of all tested forms is shown in Fig. 15 and the data reported in Table 4.
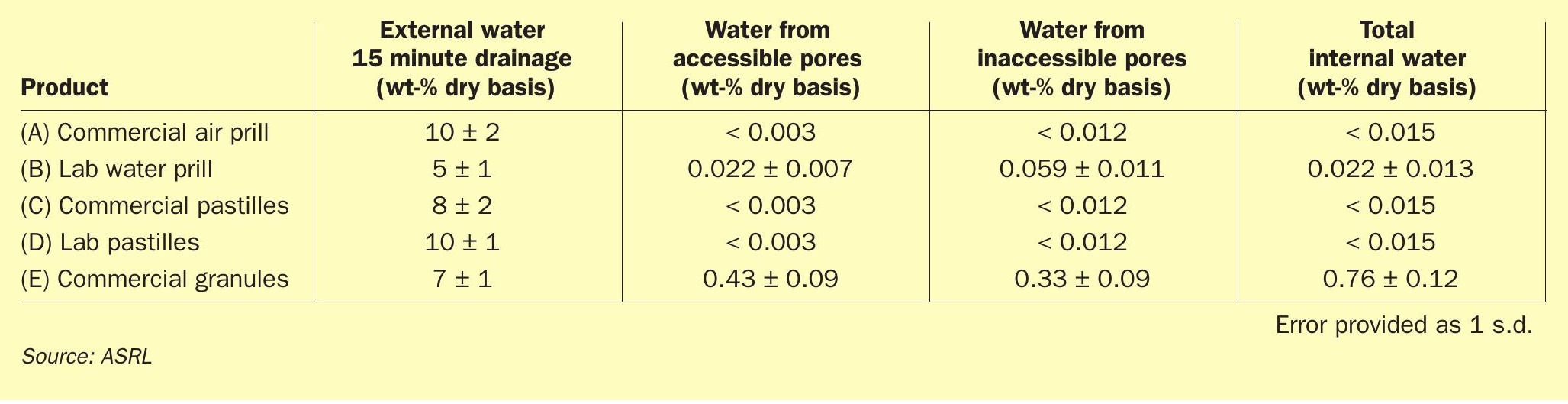
In Fig. 15 it is apparent that the commercial granule and the custom wet form curves show a different trend than the other three. This is because the water content of the other three forms is below the limit of detection for this analytical technique. The mass change at ~107°C corresponds to water from accessible pores and the peak at ~117°C corresponds to water that sits within inaccessible pores. As the sulphur particle starts to melt, water can escape, and the mass is reduced further. A similar behaviour can be seen for the custom wet form curve, although to a much lesser extent. The occluded (second type) of water is not likely a risk to transportation; however, it might result in frothing during remelt. Note that the increased mass loss near the end of the thermogram is due to the increased sublimation rate of sulphur at higher temperatures.
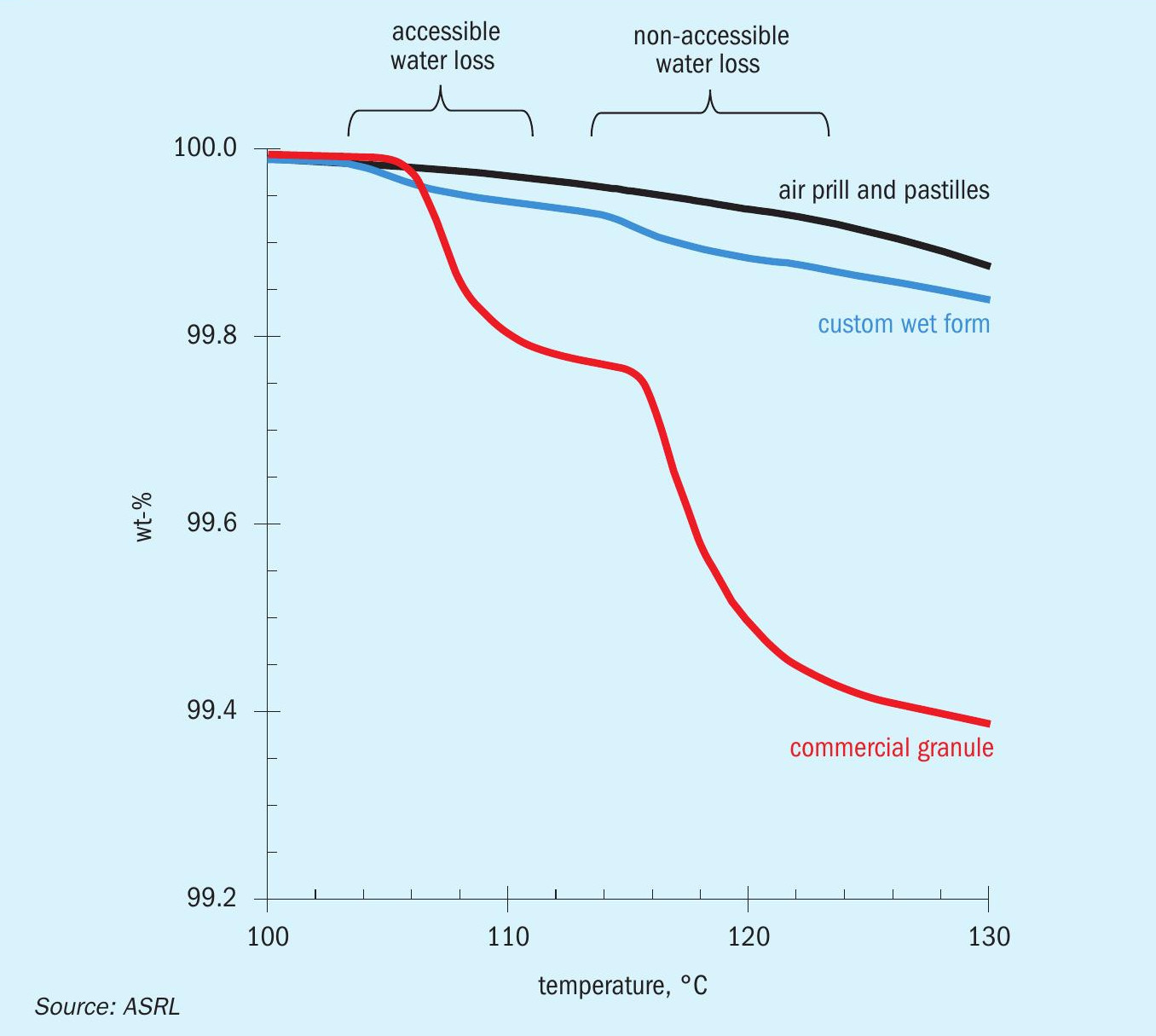
Finally, both BET surface areas and BJH pore size distributions were measured, as it was originally thought this might give insight into water holding capacity. All sulphur forms were found to have very low surface areas at 0.05 to 0.13 m2 g-1 and only a very small fraction of micropores. Note that after thermal treatment and aging, the sulphur specific surface area dropped to 0.02 to 0.07 m2 g-1 . Thus, standard and rapid surface area and pore size distributions were not a reasonable method for looking at sulphur product quality.
Conclusions
In this study, ASRL measured several properties of controlled batches of commercial air prills, commercial granules, commercial pastilles, lab formed water prills, and lab formed pastilles. These results are not meant to compare the different forms but are useful to understand how these properties may be affected by aging. All modern forms of sulphur tested appear to be premium quality with very little propensity to form dust within a SLII test unless the polymeric content of the solid form was allowed to decay below 0.4 w-t%.
Although sulphur polymeric content (CS2 insoluble) is not mentioned in the original SUDIC specifications, it was found to be a useful parameter when assessing the quality of a sulphur form. In particular, loss of polymeric sulphur can lead to excessively friable sulphur and a moderate failure of the SLII test for premium specification. At 20°C, the concentration of Sµ was determined to remain constant for several years but at 90 °C, freshly formed sulphur can lose over 90% of its Sµ content in less than two hours. It is thus important to cool formed sulphur adequately, to avoid a reduction in crush strength and an increase in fines production. Piling sulphur while hot or before it has transitioned into its orthorhombic form many lead to further polymeric sulphur decay. The delayed transition may cause self-heating within the stockpile (up to 95°C), which will exacerbate the polymeric sulphur decay, in addition to likely leading to product agglomeration. When troubleshooting low quality sulphur product, measuring the Sµ content would likely provide valuable information.
It was previously determined that liquid sulphur storage temperatures do not significantly influence the final product (assuming solid products are rapidly quenched). Degassing also did not alter the polymeric content of the liquid sulphur, suggesting that over-degassing will not compromise product strength, as long as degassing catalysts do not remain in the product. In addition, the latter suggests that, while degassing H2 S is beneficial for safety reasons, there is little reason to believe that degassing will improve the quality (strength) of a sulphur product.
ASRL looked at the maximum water retention after sulphur was saturated with water and allowed to drain for 15 minutes, where no differences were noticeable between forms. In addition, internal water content was found to be below the limit of detection for all tested forms, except for custom wet form and granules. Completely melting the sulphur reveals how much occluded water can be retained, where occluded water may lead to frothing upon remelting the product downstream.
References