Fertilizer International 515 Jul-Aug 2023
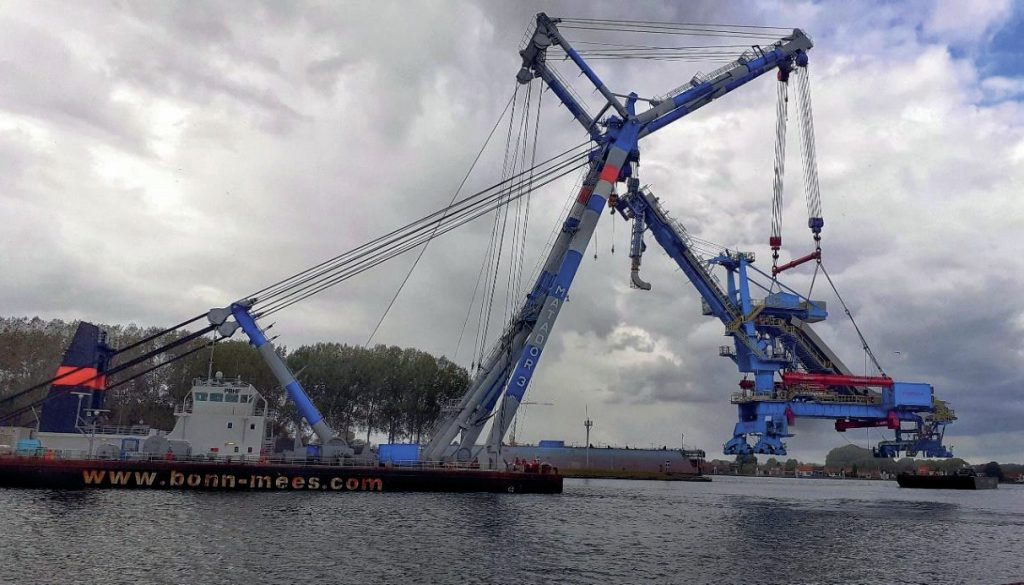
31 July 2023
Who’s who in fertilizer handling and precision blending
HANDLING & BLENDING
Who’s who in fertilizer handling and precision blending
An overview of the very latest in fertilizer handling and blending, including new contracts, company news and advances in technology.
BEDESCHI
The fertilizer handling experts
Bedeschi is a well-established supplier of crushing and handling machines for cement, steel, coal, the mining sector and other industries. The Italian industrial manufacturer moved into the marine sector 15 years ago and now offers a range of large-scale onshore ship-loading equipment. Due to its experience and know-how, the company has continued to set the standard for fertilizer bulk handling – offering turnkey solutions for every type of fertilizer.
Strong growth in fertilizer trading and shipments is expected in response to a rising global population. This will be required to meet the growing need for crop nutrients as agricultural production expands to keep the world fed and food supplies secure.
The Covid-19 outbreak negatively affected the fertilizer industry, similar to other segments of the bulk handling industry, with significant downtime during the lockdowns of 2020 and 2021. Despite this, the fertilizer market has stabilised over the last 18 months as production and demand have recovered.
The challenge when handling fertilizers is their corrosive nature and their tendency to breakdown easily, generate dust and – because they are hygroscopic – absorb water. To counteract this, Bedeschi always puts in place a range of measures to preserve the integrity of fertilizer materials. When it comes to handling machines, for example, the company uses materials that resist attack, such as stainless steel, plastic components made of glass-reinforced plastic (GRP), or high-durability paint for structural parts, since fertilizers are highly corrosive.
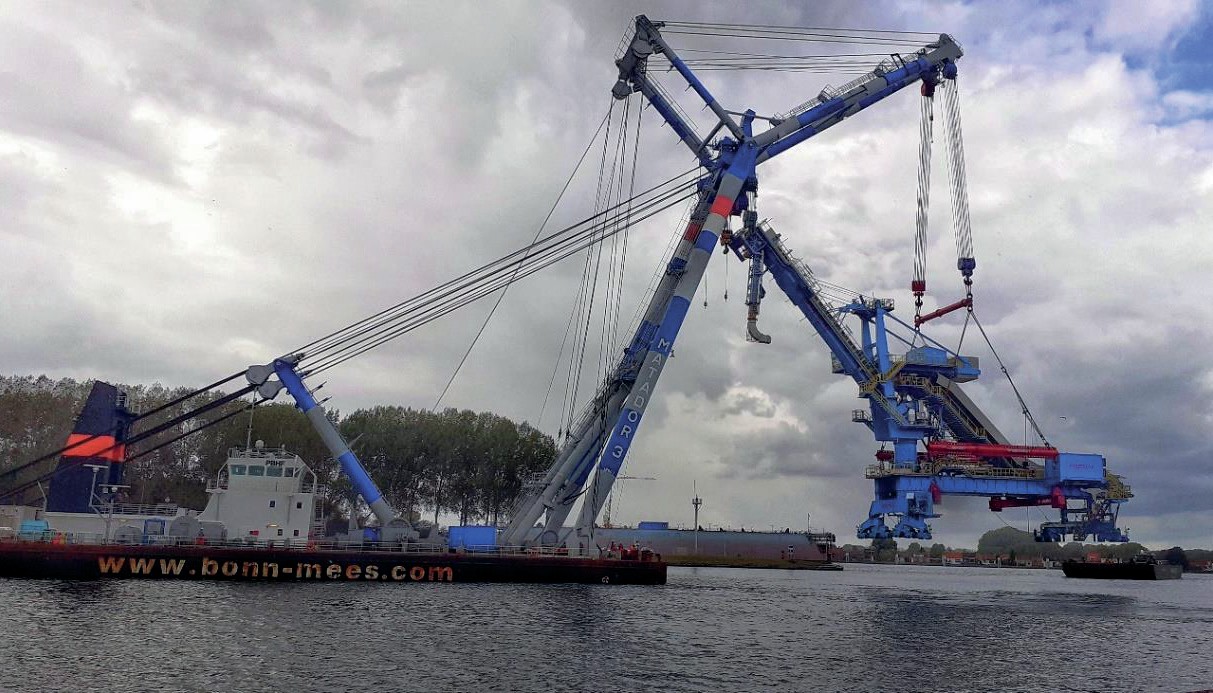
Because they break relatively easily, it is essential to guarantee the gentle treatment of fertilizer granules during handling and, by avoiding dust generation, also ensure that the highest environmental standards are being met. Bedeschi therefore pays extra special attention to loading chutes. This includes performing in-depth studies.
The company’s controlled-flow chutes, for example, are designed to keep loading speeds within acceptable values during vessel loading, and also limit the drop height to avoid degradation in cargo quality. In addition, to avoid dust generation during handling, the choice of the chute is also extremely important. For dust control, Bedeschi therefore recommends the use of pipe conveyors or enclosed conveyors and dust suppression systems, according to the cargo being handled.
Fertilizers are hygroscopic materials, as previously stated, so protecting them from water or rain is extremely important too. This is another reason why Bedeschi always uses enclosed conveyors or pipe conveyors when handling fertilizers.
Thanks to the achievements of its R&D department, and its focus on green technologies, Bedeschi can design stateof-the-art handling systems and environmentally-friendly solutions that fully meet client needs.
Bedeschi has demonstrated the quality of its fertilizer handling equipment through its long-term collaborations with industry giants such as Yara International (Fertilizer International 491, p30) and OCP Group. Notable examples of recent fertilizer and sulphur sector contracts are provided below.
QatarEnergy, Qatar
Bedeschi is to supply new sulphur-handling equipment to the NXFP sulphur project (Fertilizer International 514, p12).
This follows QatarEnergy’s award of a $600 million construction contract to the project’s joint venture partners, Spain’s Técnicas Reunidas (70%) and China’s Wison Engineering (30%) in April last year.
The NXFP project will process and extract sulphur from liquefied natural gas (LNG) for export at Qatar’s Ras Laffan Industrial City (RLIC) complex. The project’s new sulphur plant has the capacity to process around 5,000 t/d of molten sulphur.
As part of a large-scale and comprehensive supply and engineering contract with Técnicas Reunidas and Wison Engineering, Bedeschi will supply:
- Six conveyor belts with a total length of 1,400 metres with a capacity of 550 t/h, including galleries and transfer towers
- Four conveyor belts with a total length of 480 metres with a capacity of 2,000 t/h, including galleries and transfer towers
- One conveyor belt with a total length of 120 metres with a capacity of 3,700 t/h, with a gallery and transfer tower
- Two trippers with a capacity of 550 t/h
- A double arm portal reclaimer with a capacity of 2,000 t/h
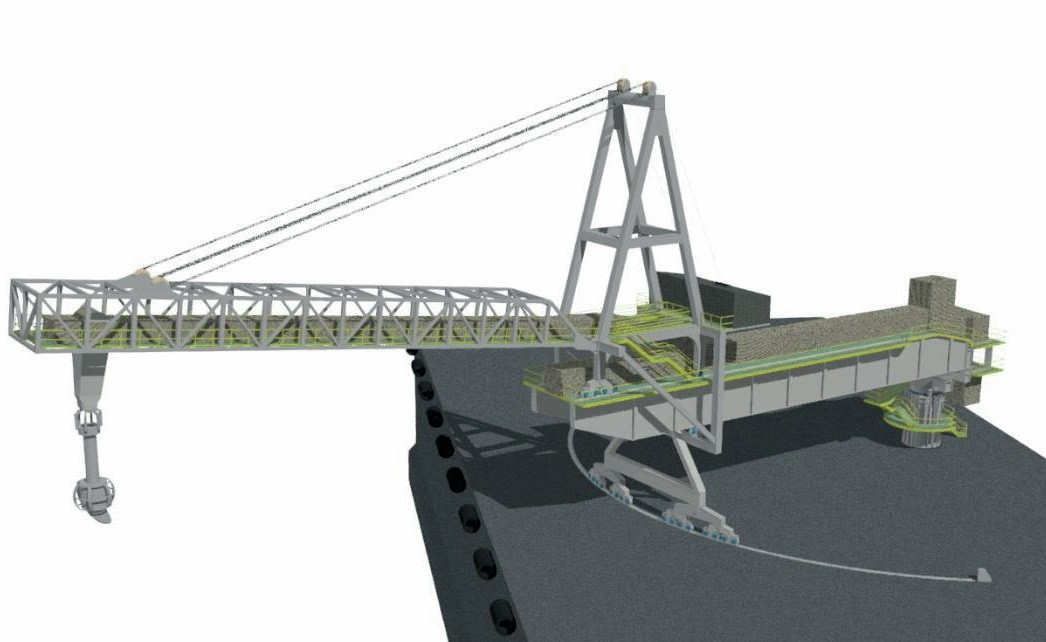
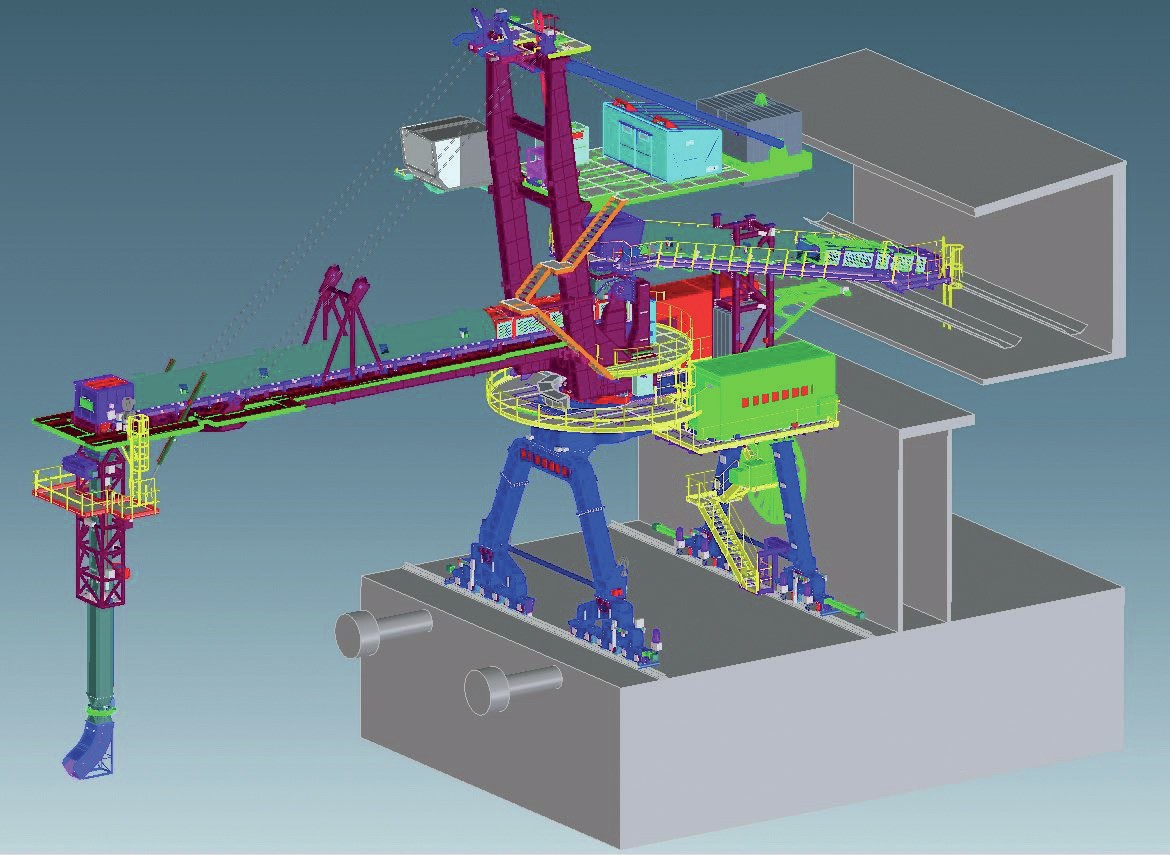
Fertil, Ruwais, Abu Dhabi
Bedeschi is supplying a new 1,200 t/h capacity shiploader for Fertil’s Ruwais terminal in Abu Dhabi (Fertilizer International 510, p10).
The tailor-made ‘luffing and slewing’ type shiploader (see schematic) will be delivered on site fully constructed. Installation of the new shiploader will not disrupt Fertil’s operations at Ruwais.
The new machine will replace the existing shiploader used for fertilizer and granular urea loading operations at the terminal. It runs on rails and uses a towed tripper to divert product from a wharf gallery conveyor onto the transfer belt that supplies the loading boom belt.
The machine’s design, engineering and construction are all based on Bedeschi know-how and have been customised to meet Fertil’s requirements – with the specific design and performances characteristics developed jointly with the client’s technical team.
OCP, Phosboucraa, Morocco
Phosphate production giant OCP has awarded long-term partner Bedeschi a new engineering, procurement and construction (EPC) contract for its Phosboucraa production complex, 30 kilometres from Laayoune (Fertilizer International 511, p11).
Bedeschi will supply three new automated bulk handling and storage systems with a combined annual capacity of 300,000 tonnes. Two of these will handle fertilizers for export while the other will handle imported sulphur.
The bulk handling equipment installed at Phosboucraa as part of the contract will include three trippers, three reclaimers, and six conveyor belts with a capacity of up to 2,000 t/h. These items are similar to those already supplied and installed by Bedeschi at OCP’s massive Jorf Lasfar phosphate complex in Morocco (see photo below).
The new contract is of strategic importance to OCP and its development plans for the country’s ‘southern axis’.
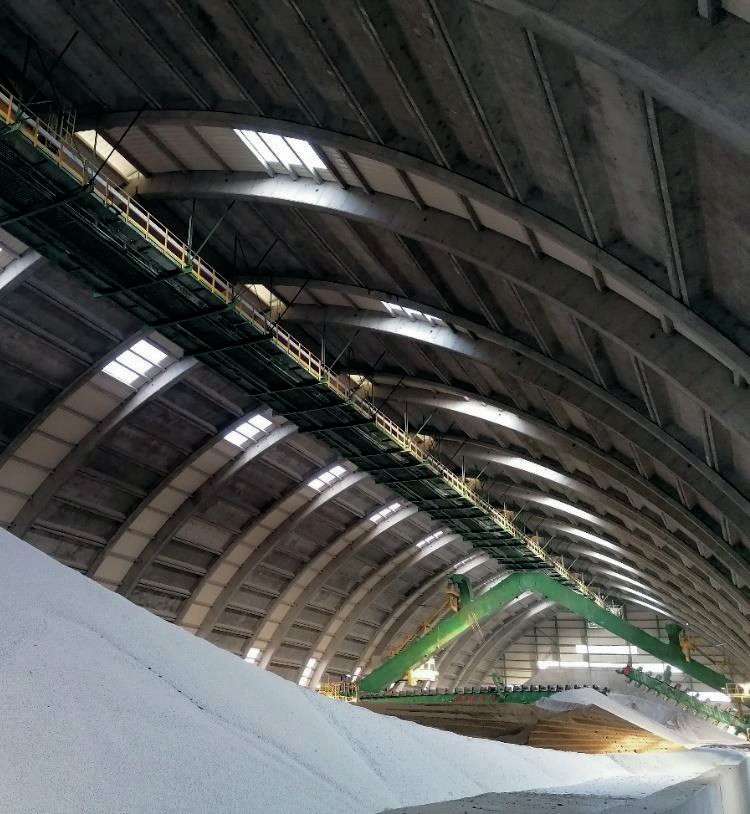
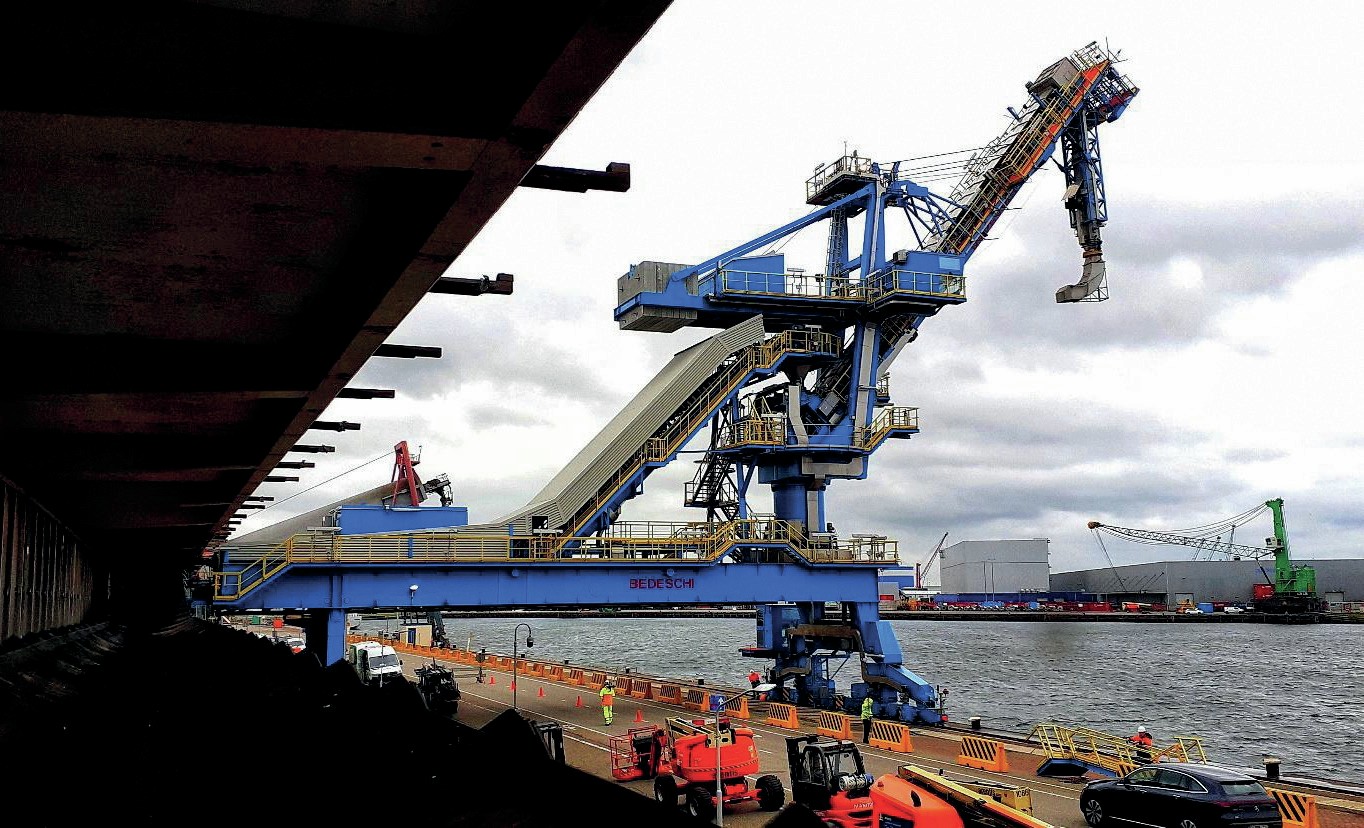
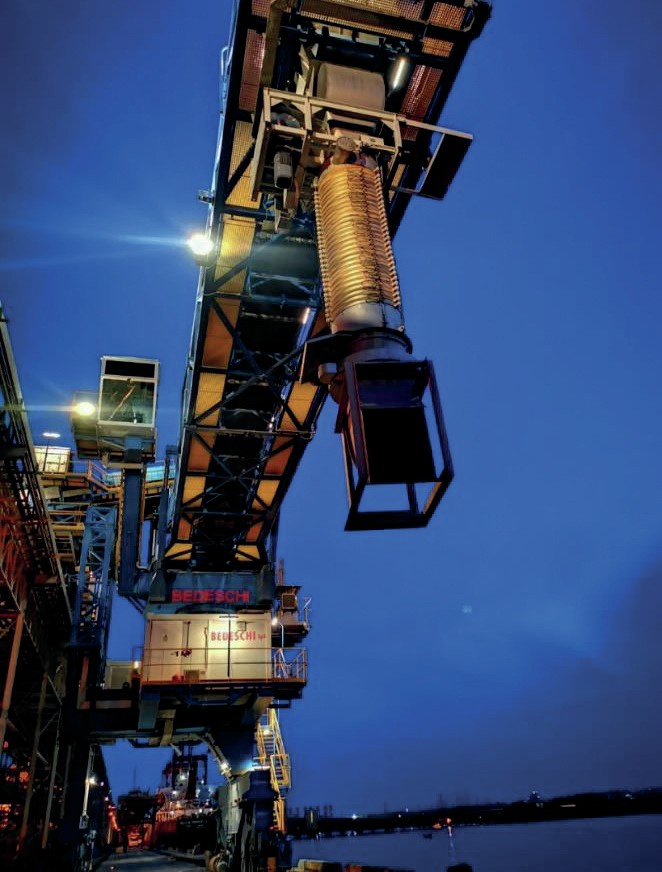
PT Petrokimia Gresik, Indonesia
Bedeschi has fulfilled an order with PT Petrokimia Gresik to supply a 1,000 t/h shiploader (SHL 25/1400) for use at the company’s Demarga jetty, Gresik, Indonesia. This is now operational (see photo) and loading NPK and NPS fertilizers onto vessels of up to 30,000 dwt size.
The order was signed with Barata Indonesia, a local engineering company responsible for civil works at the jetty including the structural steelwork for the shiploader. PT Petrokimia Gresik has previously selected Bedeschi as its supplier for circular storage and longitudinal storage units at the Demarga site. These were fitted with PAL PD portal scraper reclaimers.
Yara, Sluiskil, the Netherlands
Bedeschi recently installed a shiploader to handle urea at Yara’s Sluiskil plant in the Netherlands. Sluiskil is a major fertilizer production complex and the largest manufacturing site for ammonia and nitrate fertilizers in Europe.
The complex comprises of three ammonia plants, two nitric acid plants, two nitrate granulation plants and two urea plants, one for prilling and the other for granulation. The complex is located close to Antwerp with direct access to the North Sea.
A new slewing shiploader (SHL 28/1200) with a 600 t/h design capacity was manufactured by Bedeschi to efficiently load urea onto barges and shipping vessels under heavy duty conditions. The shiploader was recently transported from Mammoet’s quay to Yara’s quay at Sluiskil, travelling 1.5 kilometres in just 15 minutes using Matador 3, a floating sheer-leg (see main photo).
The sandwich conveyor installed at Sluiskil is the project’s main technological innovation. This high angle conveyor consists of two belts placed one on top of the other and gently conveys material inside an enclosed channel. The sandwich conveyor is positioned on the main gantry and runs along the high 40 degree incline between the jetty gallery level and the shiploader boom (see photo). This type of conveyor offers the following advantages:
- The ability to cope with a large change in slope over a small distance – overcoming the limitations of the maximum incline angle of conventional conveyors
- Improvements in environmental safety as the transported material is completely enclosed between two belt loops
- Its design and geometry makes spillages or dust emissions to the atmosphere highly unlikely.
The shiploader is now fully operative (see photo).
Bedeschi has a long history of cooperation with Yara, having previously installed:
- A 250 t/h capacity urea shiploader operating in France
- A 500 t/h capacity shiploader handling various fertilizer types operating in Italy
- A 500 t/h urea shiploader operating in Germany.
SACKETT-WACONIA
A focus on precision blending
Established in the United States 125 years ago, Sackett-Waconia has a long track record in the design and manufacture of fertilizer handling, blending and process equipment. The company, which was purchased by PVS Chemicals in April 2022 (Fertilizer International 508, p10), specialises in customised systems designed to match individual customer requirements.
Sackett-Waconia’s blending systems and equipment can be found throughout North America and around the world. Its robust equipment is engineered specifically for the rigours of the fertilizer industry and is designed with a long service life in mind. The company specialises in designing and supplying complete systems for:
- Terminals
- Fertilizer blending, granulation and compaction
- Superphosphate production
- Coatings, both powders and liquids
- Water-soluble fertilizer blending.
“Sackett-Waconia blending installations can be found throughout Africa, the Americas and Oceania.”
Sackett-Waconia delivers safe, reliable, and efficient equipment with advanced automation to customers worldwide. The company’s overall goal is to promote the sustainable use of fertilizers – through balanced nutrient use and better nutrient use efficiency – while maintaining production speed and never compromising on safety.
Sackett-Waconia offers many system designs and blending options to suit the varied requirements and locations of its customers. These range from tower blending systems, with in-floor reclaim systems and overhead storage, to its Precision Horizontal Blending system. The company’s systems combine certified, static weighments with high-quality, high speed blending and, says Sackett-Waconia, have a greater accuracy than comparable declining weight or volumetric-based blending equipment.Sackett-Waconia’s current focus is on advanced and automated Precision Fertilizer Blending® (PFB) systems. These are offered in two options:
- AccuBlend™ systems: These incorporate NTEP certified weigh hoppers, arranged horizontally, precise PLC-controlled dosing, and blending using either an HIM 2.0 precision mixer or orbital blender.
- Precision Fertilizer Blending® (PFB) tower systems: These offer an effective way to reduce the overall footprint of the blending system, and can vary in capacity from 90 ton mini towers to larger towers with 300+ tons of overhead storage capacity. The company’s flagship line of towers featuring the HIM 2.0 precision mixer and Smart Blending™ system.
The consistent, accurate and precise blends (NPKs plus micronutrients) produced by the company’s equipment provide a balanced mix of nutrients to match soil-specific nutrient requirements. Sackett-Waconia blending installations can be found throughout Africa, the Americas and Oceania. Three recent projects are highlighted below.
AccuBlend system for Loyder, Sao Paulo, Brazil
Brazil’s Loyder, part of the Essere Group, has commissioned a new 64,500 square foot (6,000 m2 ) fertilizer plant. This is dedicated to the production of enhanced effit ciency fertilizers and innovative products that improve plant resistance to abiotic stress.
Loyder placed a contract with our local Sackett do Brasil team to design and build an AccuBlend system with controls and automation – firstly at their Olimpia site, Sao Paulo, and then at nine other follow-on locations. An all-stainless Accu-Blend with an HIM 2.0 precision mixer was chosen as the model for all 10 locations. This system has an overall bagging output of 60+ tons per hour, as specified by the customer.
Project specifications at a glance:
- Facility Size: 64,500 square feet
- Blending System: AccuBlend System with controls and automation
- Blender: HIM 2.0 precision mixer
- Capacity: 60+ tons per hour in 50 kg or 1,000 kg bags.
PFB Tower for Cargill in Alberta, Canada
Cargill’s new plant in Camrose, Alberta, Canada, features the latest in Sackett-Waconia blending technology paired with high-speed receiving and wholesale operations. The system receives from rail or truck and transfers materials via belt conveyor and bucket elevator to a tripper conveyor. This configuration provides maximum filling within the bins. For loadout, the Precision Fertilizer Blending Tower® is fed by an in-floor reclaimer. The materials are then conditioned before being loaded into the overhead storage.
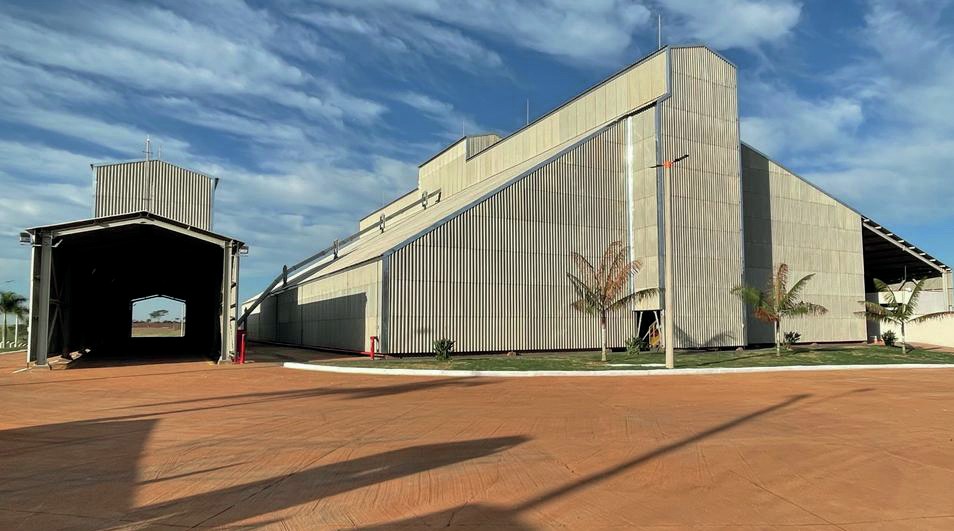
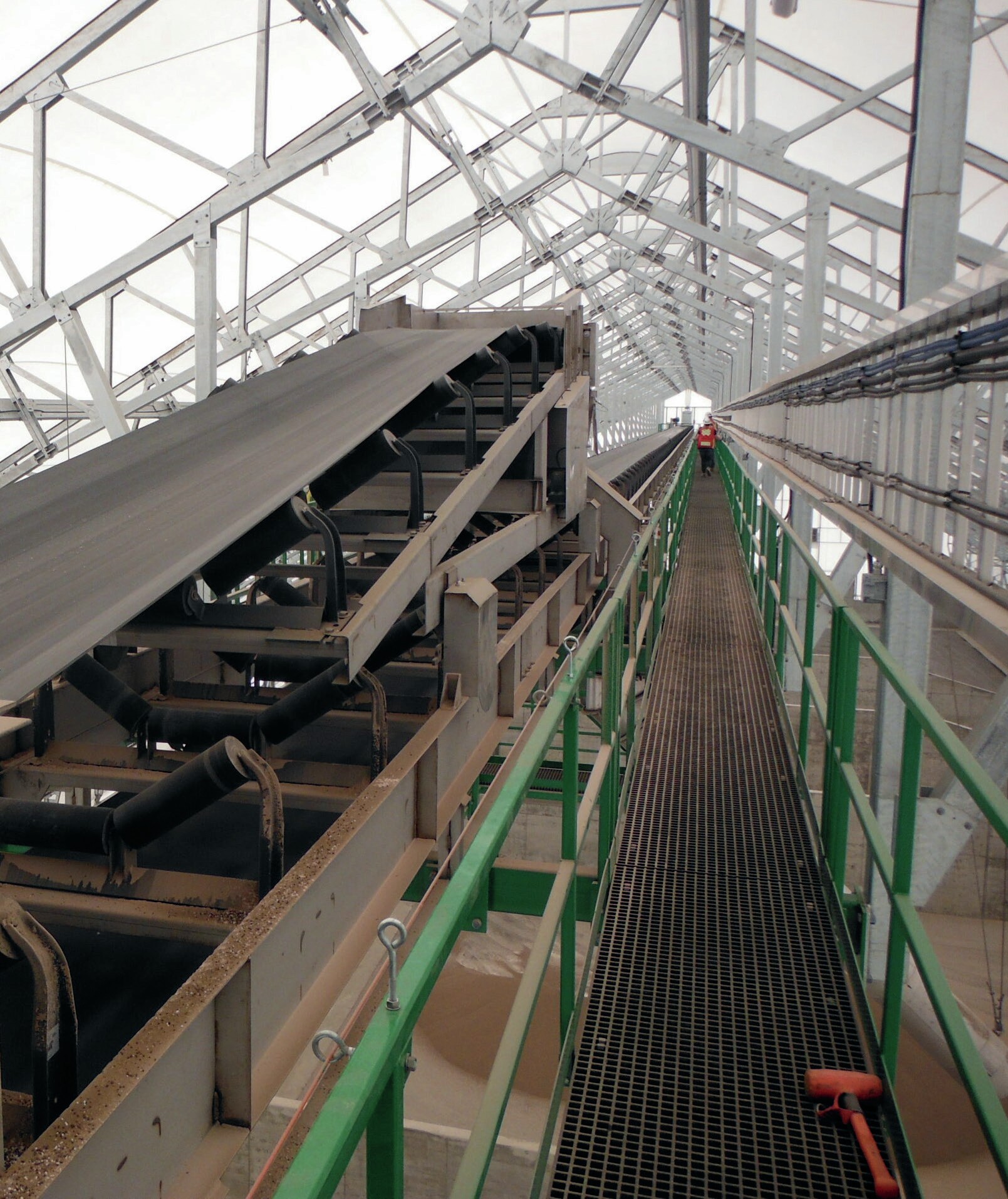
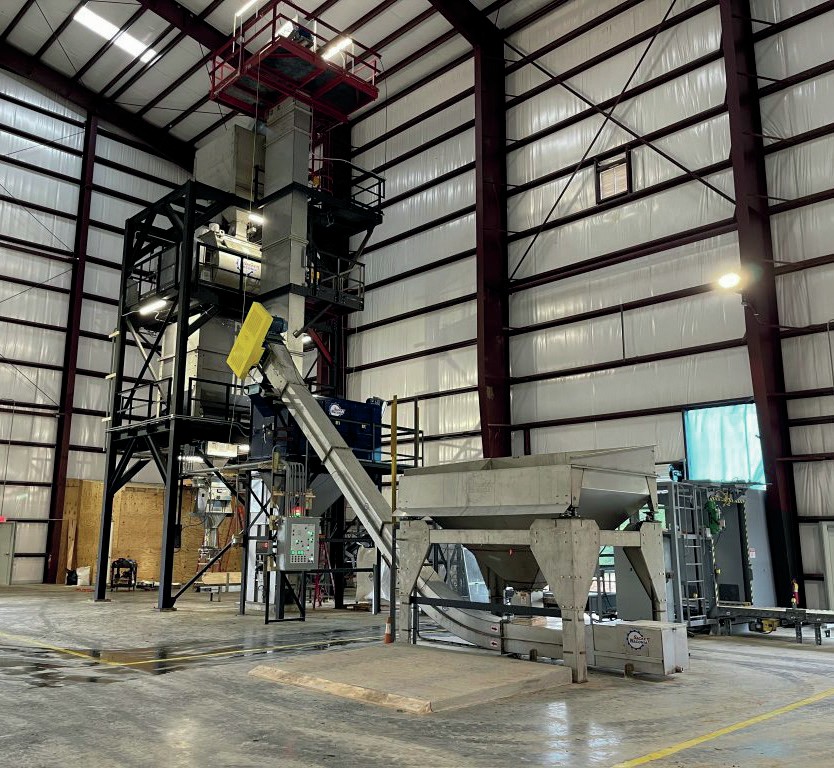
The Camrose plant was designed for high-capacity operations while, at the same time, keeping the blending accuracy to an exact formula to support 4R Nutrient Stewardship and nutrient use efficiency. Project specifications at a glance:
- Receiving System: 750 (+/-) tonnes per hour rail and truck receiving
- Blending System: PFB Tower with multiple loadout options operating in blend or wholesale modes
- Storage: 275 tonnes capacity overhead, in 12 bins (8 macro and 4 micro), and 4,100 tonne capcity wholesale bins
- Blender: 4.5 tonne (5 ton) HIM 2.0 precision mixer
- Handling capacity: 275 (+/-) tonnes per hour via 4 tonne batches
- Discharge: to trucks.
Compact PFB Tower for Beaty Fertilizer in Cleveland, Tennessee
Beaty Fertilizer purchased their first compact PFB tower from Sackett-Waconia in 2016. The company has since upgraded this, along with their receiving system, and added a second compact tower. The installation of the original tower raised operational capacity and led to a large improvement in product quality. The resulting uptick in business allowed Beaty Fertilizer to invest in an additional second tower – effectively doubling the company’s blending capacity.
The new system is completely built from stainless materials and features a HIM 2.0 precision mixer. Beaty also chose an upgraded screener to increase system speed, together with expandable dosing that incorporates an NTEP certified weighing system.
PFB towers are designed to ensure the highly accurate individual weighing of materials and provide superior blending. These design characteristics support 4R Nutrient stewardship by ensuring the nutrient content of blended products – the ‘right source’ – fulfils customer specifications as closely as possible.
Project specifications at a glance:
- System: PFB Tower with expandable feed and pre-screening
- Storage: 10 ton weigh hopper
- Blender: HIM 2.0 precision mixer
- Discharge: To bagging
- Receiving System: 200 tons per hour, rail and truck.
EMT
Rising to the challenge of global project delivery
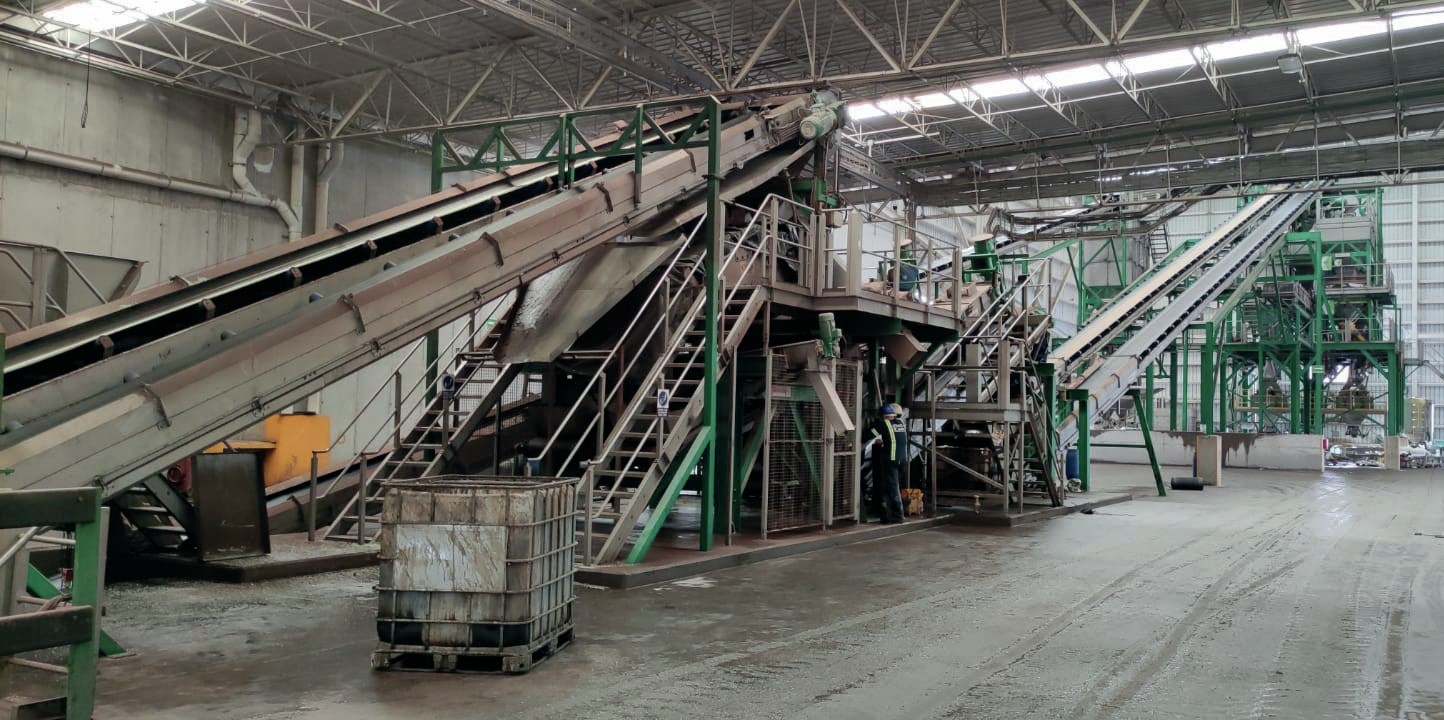
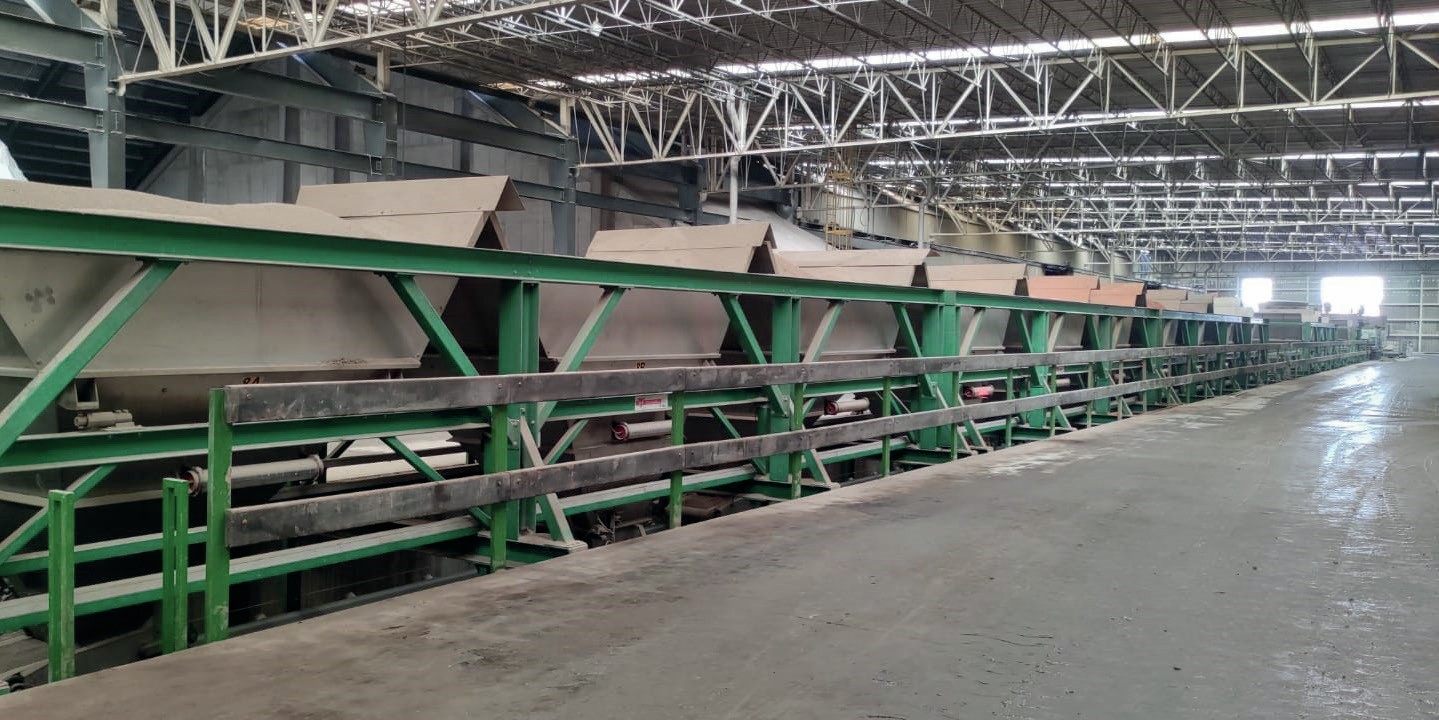
Netherlands-based EMT is one of the world’s largest fertilizer blending and bagging equipment producers. In recent times, the company has successfully delivered a variety of projects worldwide in highly challenging circumstances.
Each project came with its own unique set of hurdles that needed to be overcome.
These included:
- A project that needed to install one of the longest fertilizer blend units in the world.
- A project that needed be delivered to a site almost exactly on the opposite side of the world.
- A project that needed to be fully mechanically engineered and tailor-made to fit into an existing warehouse.
EMT successfully overcame all of these challenges and, consequently, these project installations are now fully operational. In this article, we highlight three of their outstanding recent projects. These illustrate how EMT is able to put its 35 years of turn key factory experience into producing solutions that can help you with your project.
ISAOSA, Topolobampo, Mexico
EMT installed a state-of-the-art fertilizer blending factory for ISAOSA (Insumos y Servicios Agrícolas de Occidente S.A.) at the port city of Topolobampo in the Gulf of California, Mexico. Impressively, this is one of the longest fertilizer mixing lines in the world.
The completed machine is designed to operate at a capacity of 300 tonnes per hour and is more than 200 metres in length. This high capacity is achieved by running two lines in parallel. This ensures the blend quality is near perfect and also allows the machine to be filled by multiple front-loaders simultaneously.
In line with the latest advances in fertilizer treatment, a liquid inhibitor is applied as a direct coating to urea prior to blending. Initially, a conditioner is added to break up any lumpy urea material before the liquid is added via an injection point installed directly into a blending screw. By weighing both the urea conditioner and the inhibitor, the flow of both liquids is constantly monitored and adjusted to ensure the treatment of the end-product is exactly as required.
The complete blend line is computer controlled and can easily be operated with one operator from the central office. With this new machine line, ISAOSA can triple its annual production capacity to 300,000 tonnes.
Ballance, Whangarei, New Zealand
EMT has also installed a large mixing, bagging and bulk truck filling plant at Ballance’s Whangarei Hub in New Zealand. This involved delivering, unpacking, assembling and then commissioning the contents of 15 high-cube, 40-foot long shipping containers on the other side of the world.
EMT installed a 17-hopper Weighcont blending machine for Ballance. This consisted of nine weighing hoppers each fitted with a specifically designed double-dosing cone that met the low input height of the existing equipment.
These double hoppers are filled using a large bucket shovel. The product assigned to these double hoppers is dosed with two dosing belts, ending up on a central conveyor.
As well as the nine double hoppers, EMT installed eight additional single hoppers with a single dosing belt. These are filled with product from big bags or from small bags weighing 25-50 kg.
The plant’s central conveyor belt transports materials to a coarse sieve where lumps are removed from the product stream. These are broken down to the correct size by a lump breaker to ensure no product is lost.
After being conditioned this way, the product is transported to two parallel truck loading lines. These bulk-load the product into 48-tonne double-trailer trucks. These carry 24 tonnes in the first trailer with an additional 24 tonne trailer behind.
Both trailers are fully filled using a movable transport system located above the trucks. Alternatively, the product can be placed in big bags or small bags for onward transport to the farmer or distributor.
The decision to select EMT’s Weighcont blender for the Ballance project was driven by the need for accuracy, efficiency and consistency in the mixing process – while still maintaining a high tonnage throughput of up to 250 tonnes per hour.
Atena, La Rochelle-Ceddex, France
As well as delivering on challenging large projects, EMT was recently tasked by Atena with resolving its intricate handling and blending needs and translating these into a practical functioning machine line. Taking these difficulties into consideration, EMT went on to successfully install a state-of-the-art fertilizer production line for Atena at La Rochelle-Ceddex, France, in the first-quarter of 2023. This machine line consisted of three parts:
- The urea coating-line
- The NPK-line
- The central blend and discharge line.
The urea-line starts with a 10.5-tonne weighing hopper equipped with a conditioner that breaks oversize material down to less than 15 millimetres. This line is flexible and can either screen-out dust or bypass this screening stage entirely and transport material direct to the coating unit instead. Within this unit, coating liquid is added to raw materials via the coating screw. The resulting product is then conveyed to the transport line.
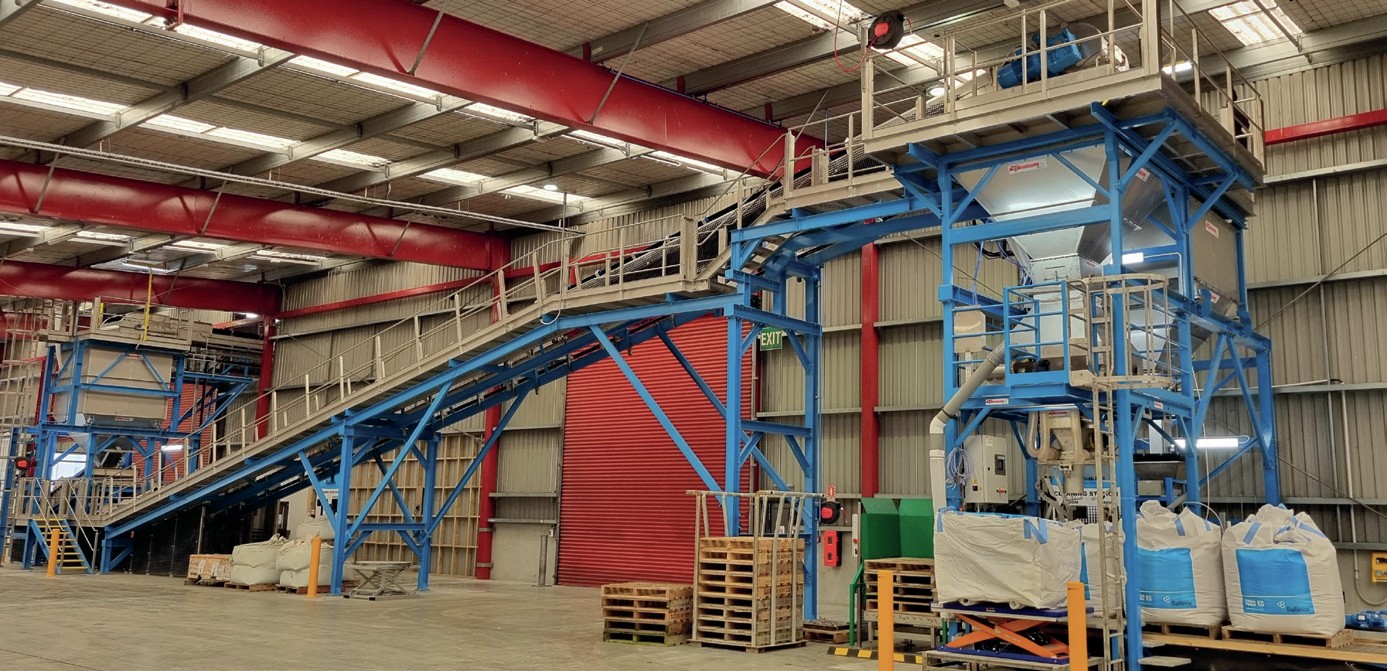
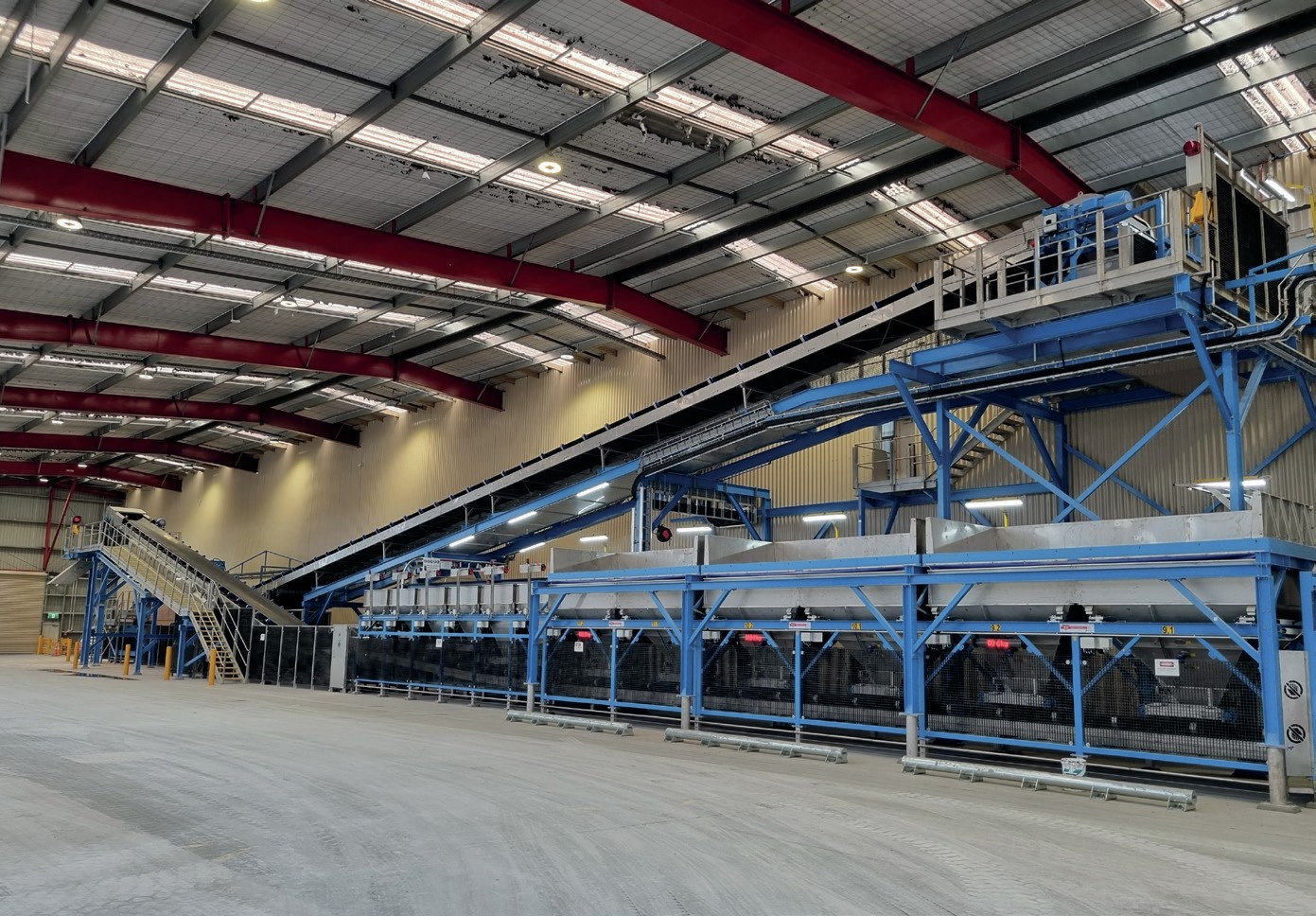
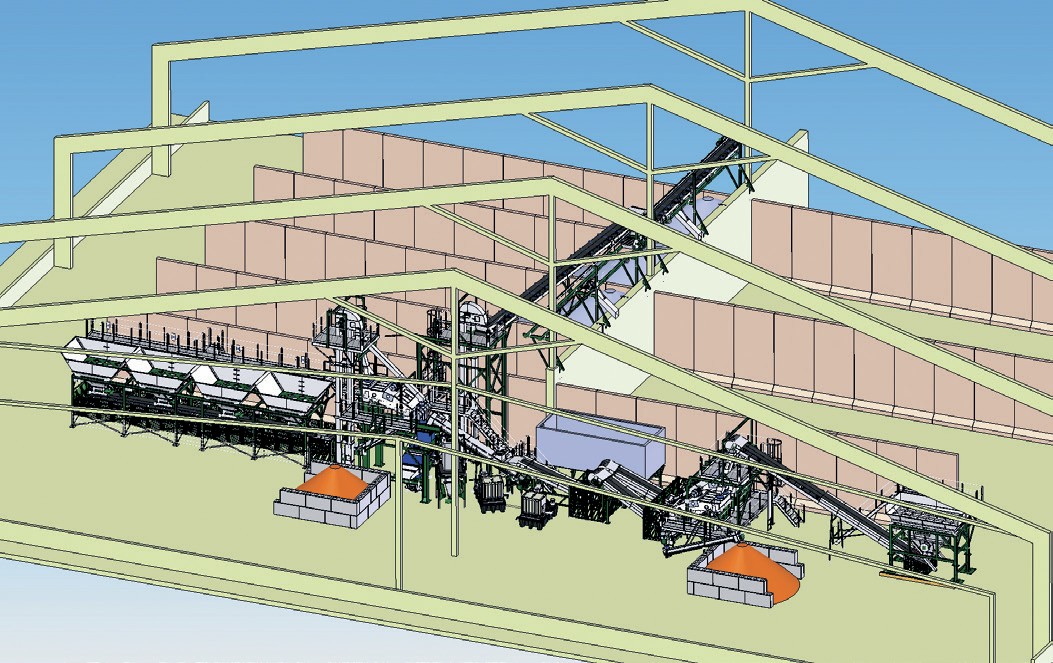
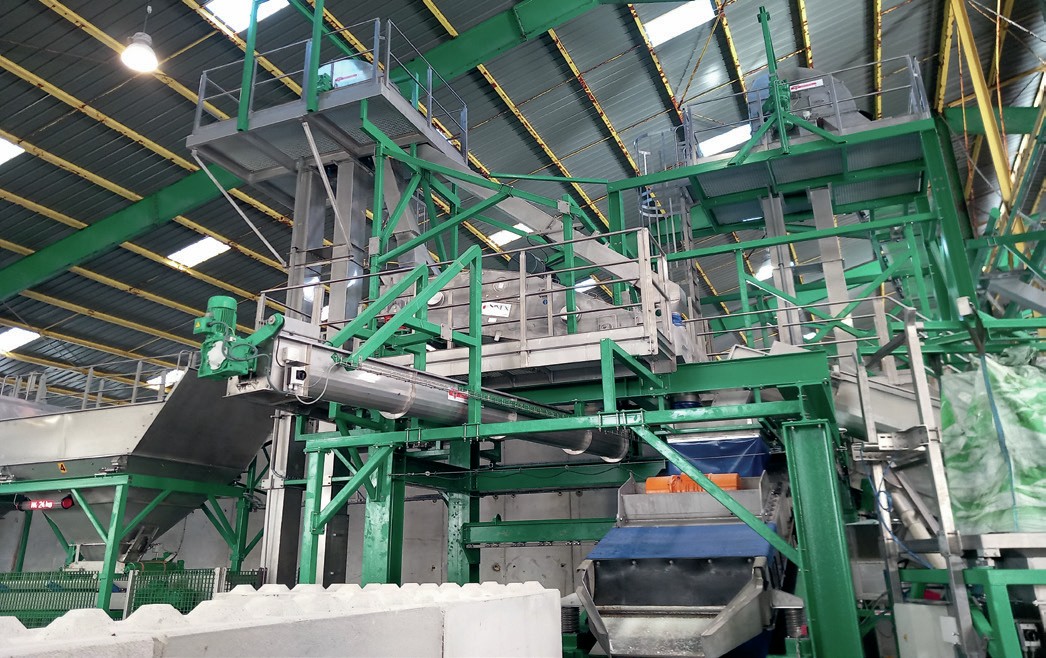
The NPK-line starts with a four-hopper Weighcont blender. This transports material to an elevator where it is then directed to one of two lines: material is either screened for fines or instead bypasses this stage and is discharged directly onto the coarse screen.
Both NPK lines merge again on arrival at the coarse screen and are fed into the blending screw where powders or liquid can be added to the total blend. The final product is lifted by a second elevator onto a conveyor. Here, it is either distributed to the bulk bays, or to a bagging line located 70 metres ahead in the middle of the warehouse.
At EMT, we know that many factors must be considered with this type of fertilizer blending plant – particularly the characteristics of the raw materials and the required specifications of the final product. For the Atena project, these factors required the installation of two different treatment lines, this being necessary for coating one product before mixing the final blend.
As well as this, delivering the required capacity is crucial when designing production lines. For this project, for example, a double screen setup was chosen to enable the urea line to achieve the desired capacity of 120 tonnes per hour. With a double screen arrangement, the plant can operate at higher capacity as the screen is no longer a bottleneck in the process.