Fertilizer International 516 Sept-Oct 2023
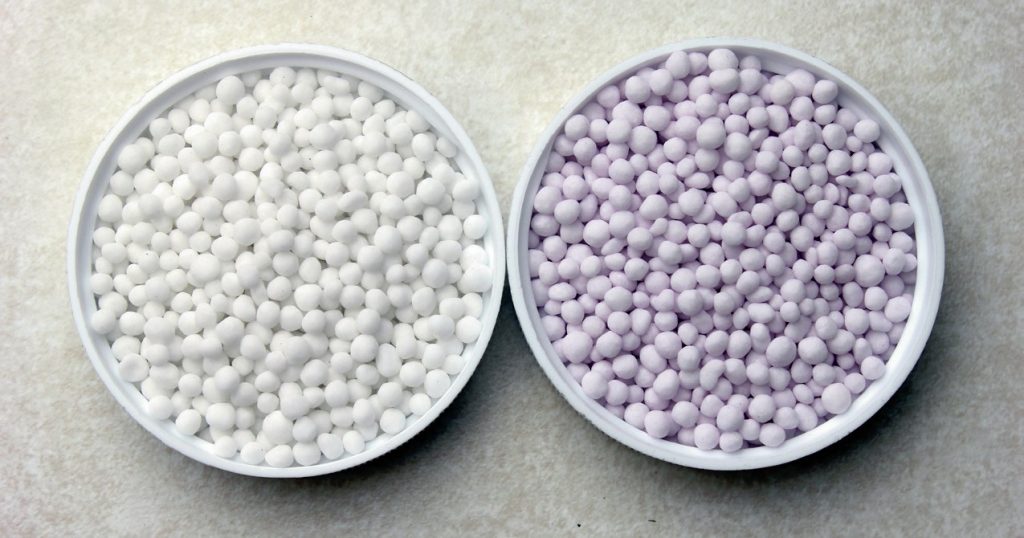
30 September 2023
Coating agents and equipment
FERTILIZER COATING
Coating agents and equipment
The quality of finished fertilizers can be maintained during transport, handling and storage by protecting the surfaces of granules and prills with coating agents. Valuably, fertilizer coatings can also be used to control the release of nutrients in the field.
HOLLAND NOVOCHEM
Future-proof fertilizer additives
Founded in 1992 by a team of experienced fertilizer additive engineers, Holland Novochem markets a long-established range of high-quality anti-caking, moisture repellents and de-dusting agents. Over the last three decades, this independent company has grown to become Europe’s leading in-depth provider of coating agents to the fertilizer industry.
Holland Novochem’s head office and laboratory are located just outside of Amsterdam in the Netherlands, while its state-of-the-art production site is strategically located on the Merwede river near the port of Rotterdam.
Holland Novochem serves fertilizer industry customers in more than 90 countries through four branch offices located across Eastern and Western Europe. The company offers an extensive range of branded fertilizer additives through its well known NovoFlow and Novodust portfolios (see box). These low-toxicity, environmentally- friendly products successfully address many of the problems associated with the production, storage and transportation of fertilizers, whether in solid or liquid form.
The Holland Novochem way
Over the years, Holland Novochem has built up a strong reference list that includes all the major global fertilizer producers. The company attributes its success to the following factors:
- Dedicated staff: building long-term partnerships with our customers is the priority of our highly-experienced chemical, technical, logistic and commercial staff – a team that collectively has more than 150 years of customer-focussed business experience.
- Sustainable technology: we select well-studied and highly pure raw materials for use in all our products, with strict adherence to the maximum limit of two percent polycyclic aromatics. Holland Novochem was the first company to develop and supply bio-based and biodegradable coatings to the fertilizer industry worldwide. The successful development of bio-based coatings enables us to supply customers with products that are free of microplastics and conform to environmental regulations such as REACH. Use of bio-based coatings also avoids the price fluctuations that can affect inorganic products.
PRODUCT RANGE
Fertilizer additives are Holland Novochem’s bread and butter. The company’s product range includes:
- NovoFlow anti-caking and moisture repellent coatings: these provide protection against caking and moisture uptake. They are suitable for all major types of fertilizers. Formulations are custom-made – according to the specific needs of fertilizer producers – to reduce caking and/or moisture.
- NovoDust anti-dust coatings: these substantially reduce dust generation during the handling and storage of fertilizers. Dust prevention is becoming an increasingly important due to the introduction of ever more stringent environmental and safety regulations – and the general requirement for cleaner workplaces.
- NovoCor corrosion inhibitor for liquid fertilizers: the addition of an inhibitor is essential for highly corrosive liquid fertilizers, such as UAN and AN solutions. NovoCor works by creating a stable organic barrier film on metal surfaces. This provides long-term corrosion protection for the whole of the distribution chain, from production to the end-user.
- NovoFoam anti-foaming agent: this strong anti-foaming product controls foam formation during the reaction of phosphate rock with acids.
- NovoTec granulation additive: this granulation enhancer can optimise the production process and/or improve the quality of fertilizer granules for a variety of fertilizer grades, especially AN, CAN and NPKs.
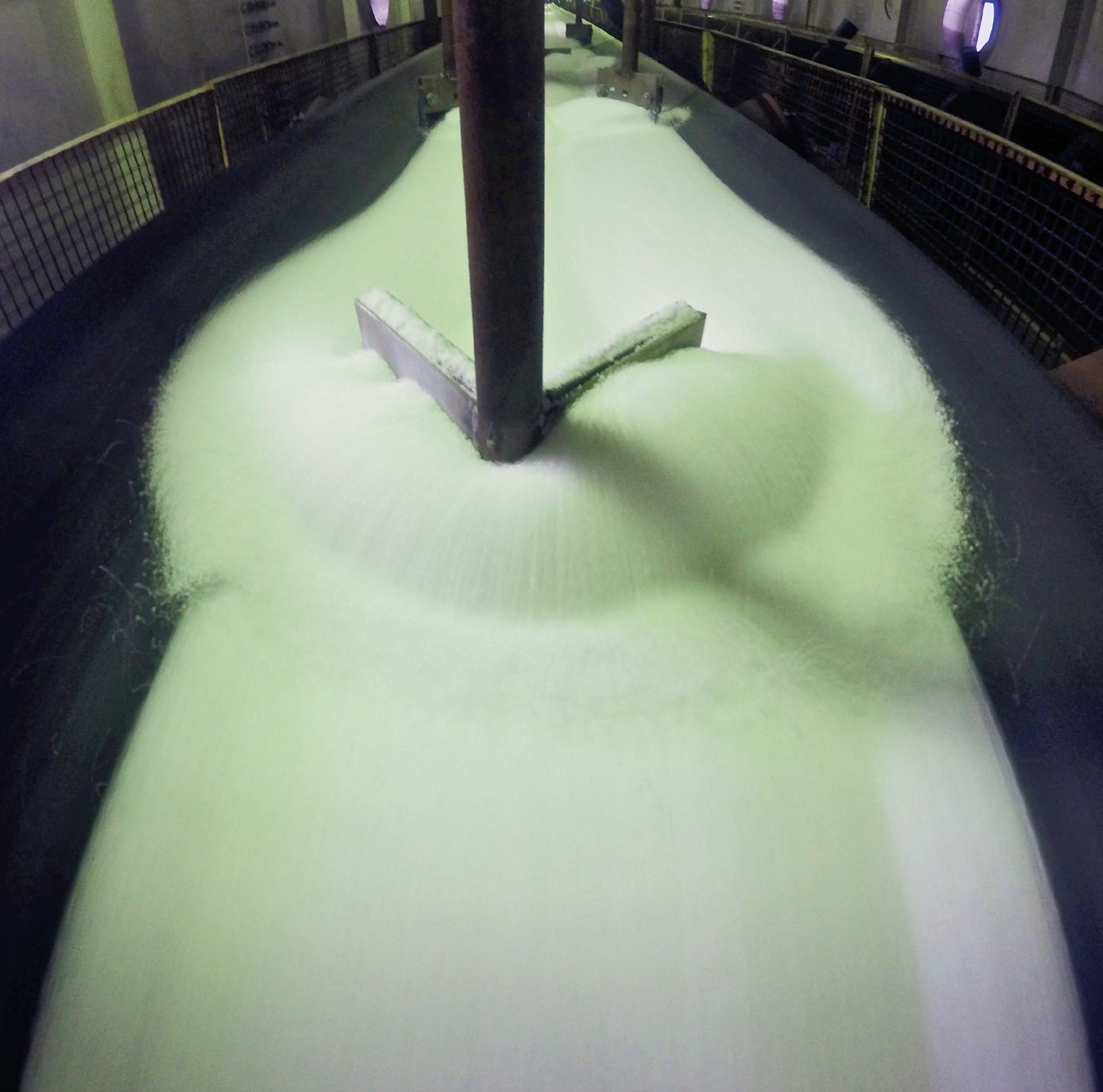
- Independence: the way we operate means the company is not restricted to using specific in-house raw materials, such as amines or paraffins.
- Cost awareness: we are able to meet the wishes of our customers by finding the optimal balance between price and performance.
- State-of-the-art laboratory: our modern lab has all the necessary facilities to run specific tests on fertilizer additives, enabling us to design custom-made formulations and to develop new applications.
- Consistent high quality and reliability: production from one single location close to Rotterdam is highly advantageous as it allows our very experienced production and logistics teams to guarantee in-time-delivery and security of supply to customers.
Customer service holds the key
The Holland Novochem’s philosophy is to focus on delivering the best service with the best products. We understand that each fertilizer plant and every product it generates require dedicated customer service. Our drive and motivation is therefore to work with our customers to find the most suitable and best performing additives for their specific products. In recent years, this has involved prioritising sustainability and reducing the carbon footprint of our products.
In these disruptive times, the best way of helping customers stay ahead, in our view, is by providing them with innovative tailor-made solutions that match both their current needs as well as future environmental requirements. We achieve this by working in close cooperation with our customers, sharing our extensive expertise and R&D know-how, to provide them with future-proof answers.
It’s only natural
Traditionally, fertilizer additives, such as anti-caking agents and moisture repellents, have been based on petrochemical compounds, especially paraffins and mineral oils. The performance of these additives can be further enhanced by the addition of other active ingredients derived from petrochemicals such as alkyl amines.
During the last few years, there has been strong and growing awareness that petrochemicals need to be replaced with more sustainable products derived from natural sources. This transition is being encouraged by international and regional policies. The United Nations has set 17 Sustainable Development Goals (SDGs) for 2030, for example, while the Green Deal policy package launched by the European Commission commits the EU to becoming climate neutral by 2050. Both developments are likely to prompt a further shift away from traditional coating agents within a relatively short time span.
Holland Novochem first began to carry out extensive research on bio-based fertilizer additives twenty years ago. Since then, the results of these highly productive studies have formed the basis of dozens of successful patents. Over time, the company has seen increasingly widespread adoption of its sustainable coating products by customers worldwide, with the numbers increasing annually. These new fertilizer additives are commonly derived from vegetable oils such as sunflower, rapeseed and soybean oil.
While this is a very positive development for the fertilizer industry, the complete transition from traditional coating oils to bio-based alternatives could have a downside if it affects the overall availability of vegetable oils. Fertilizer industry demand should not, in our view, restrict the availability of vegetable oils as food commodities. This situation can be avoided if the vegetable oil industry provides new production capacity to meet the extra demand from the fertilizer sector and other industries.
Farmers will still need standard fertilizers to grow enough crops to feed the entire world population. Despite the best efforts of producing companies and industry trade associations, the production of climate-neutral fertilizers, protected by fully sustainable additives, cannot be guaranteed at present. Fluctuations in the availability and price of feedstocks and raw materials, such as natural gas and ammonia, can also have a hugely adverse effect on fertilizer industry operations.
Nevertheless, Holland Novochem believes it has a natural responsibility to provide our customers with products that – as well as keeping them competitive – contribute to the wellbeing of our beautiful planet for years to come. Indeed, our R&D team is continuing to optimise our bio-based product line. Recent breakthroughs have already established highly sustainable and environmentally friendly anti-caking agents.
FEECO INTERNATIONAL
Coating drums: nutrient use efficiency’s secret weapon
In the fertilizer market, coatings are an essential tool in controlling both product perception and performance, thereby helping manufacturers to meet changing customer preferences and demands.
Coatings have long been used to control the dust and caking behaviour of fertilizer granules during transport and handling. Most recently, however, there has been increasing interest in the ability of coatings to control the release rate of nutrients from granules in soils, a characteristic that can maximise the nutrient use efficiency (NUE) of fertilizers.
What many fertilizer producers fail to recognise, though, is that two critical factors will determine whether coatings achieve their desired effect:
- Firstly, the formulation of the coating itself and its corresponding physical and chemical properties
- Secondly, how the coating is applied onto the fertilizer product.
To put it simply, even the best coating agent is only as good as its application method. That makes finding the right coating process and equipment absolutely critical. As this article will highlight, more and more fertilizer producers are turning to coating drums to deliver the best results.
Coating to improve nutrient use efficiency
Coatings provide a powerful tool for managing the rate of nutrient release from fertilizer granules, a valuable characteristic that has become increasingly important as growers seek to boost crop productivity by maximising their yields while simultaneously minimising nutrient losses.
Coated granular fertilizers, usually known as controlled-release fertilizers (CRFs), are advanced products that supply crops with a ‘slow drip’ of nutrients that more closely matches how plants take up nutrients. This contrasts with the immediate nutrient release that can accompany the application of traditional commodity fertilizers, a characteristic that can be both inefficient and bad for the environment. Plants can only take up so much when nutrients are oversupplied, leaving the remainder to be lost as runoff.
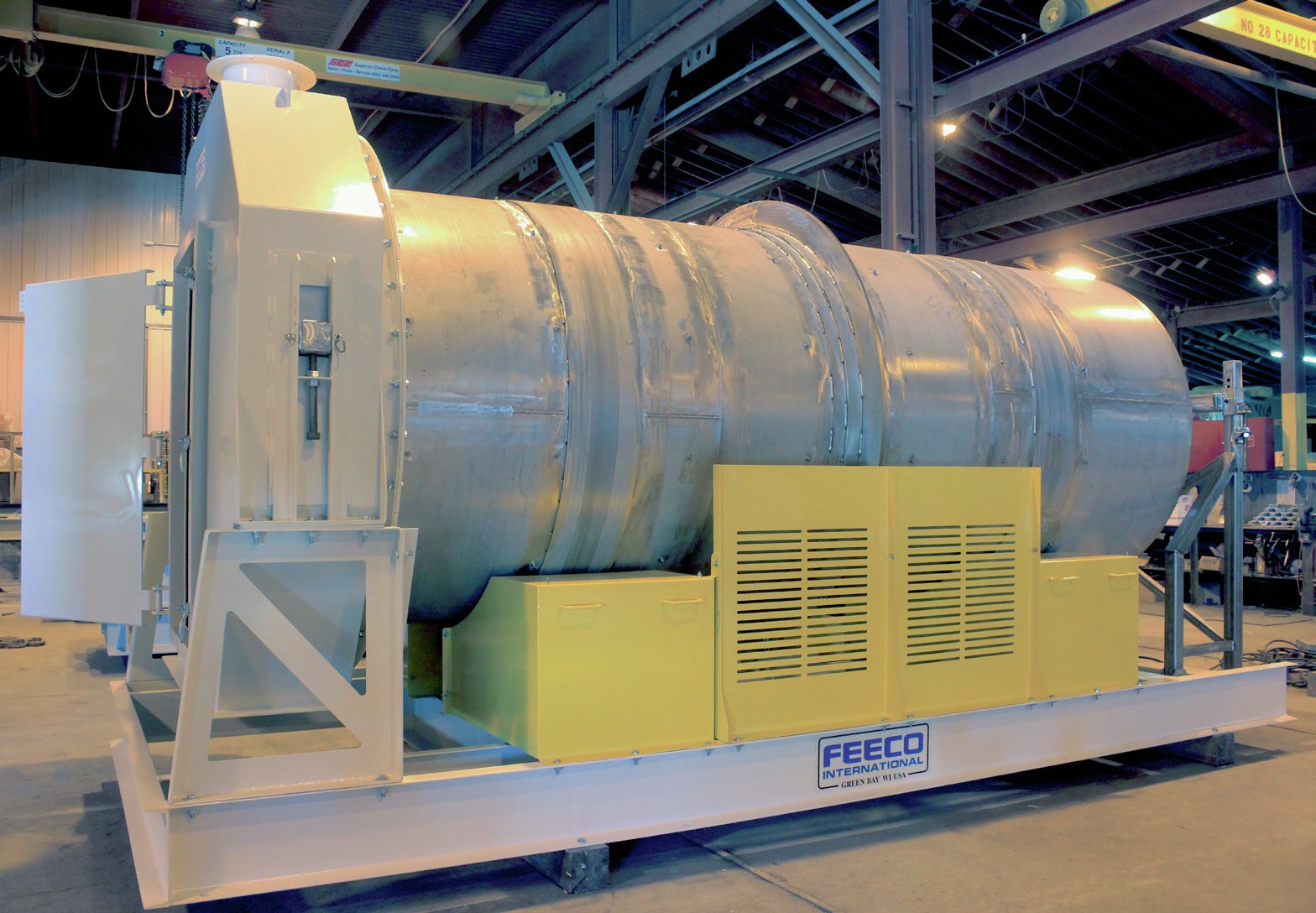
An extensive range of coatings, both organic and inorganic, is available on the market, each having inherent advantages and disadvantages. Waxes, oils and polymers are among the most common types of coating applied in the fertilizer industry.
In general, while individual coating agents behave differently, they all have the same essential function: controlling the release of nutrients by creating a coating that acts as a barrier between the nutrient and its surrounding environment. The gradual breakdown of this barrier controls (prevents or slows) the rate at which moisture can infiltrate the granule and start releasing nutrients.
While the underlying principle is simple, coatings have become a science in their own right. Thanks to sophisticated coatings technology, CRFs have now been developed that are incredibly effective at producing more food from the same (or smaller) plots of land. That is because the improved NUE of these products ensures that more nutrients end up in the crop and less are lost to the environment.
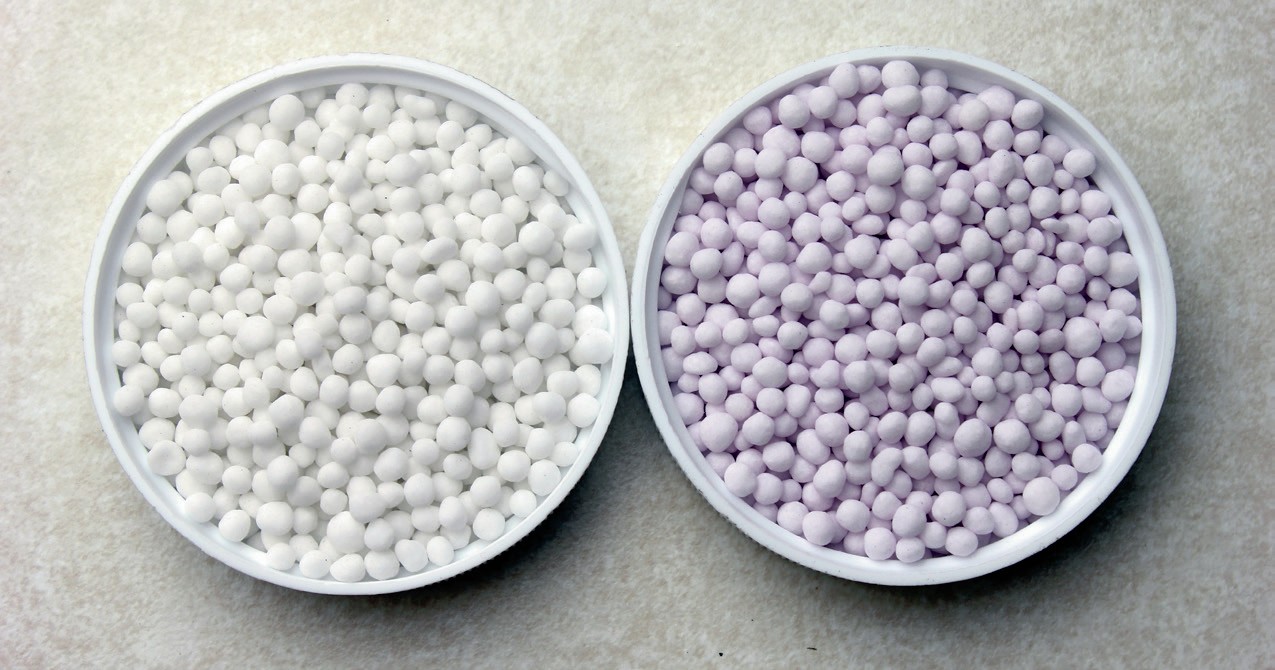
Coating drums: the key to uniform coating
As previously mentioned, in addition to improving NUE, coating protects fertilizer granules during transport and handling. This is a vital way of combating two common problems faced by fertilizer producers, traders and distributors – namely dust formation and caking. If left unprotected, breakage and moisture damage to fertilizer granules can infringe on profits, and also leave suppliers facing liabilities and many other frustrations.
Additionally, applying a coating to granular fertilizers, by improving product appearance as well as performance, allows manufacturers to ‘add value’ and market these granules as premium products to an increasingly discerning market.
The effectiveness of any coating agent, as previously mentioned, is dependent upon its application. For a coating to be effective, it must be applied at, firstly, the right thickness and, secondly, as uniformly as possible. Product performance can suffer greatly if both these conditions are not met, because of sub-standard behaviour in shipping, handling, storage, and eventual field application.
It is for these reasons that the coating drum has become the equipment of choice for coating fertilizer granules. When properly designed, a coating drum can achieve both a high level of coating uniformity and deliver the high throughput required by the industry. These valued process characteristics are a result of the unique coating mechanisms that occur inside coating drums during their operation.
Coating drum operation
The general operating principles of coating drums are similar to other types of rotary drum found in fertilizer plants.
Material is fed into the inlet of a rotating drum on a continuous basis. A spray system distributes the coating across the material bed. As the drum rotates, the bed tumbles, distributing the coating via granule-to-granule contact. Tumbling flights help to achieve an even coating distribution throughout the bed by encouraging rotation and agitation (bed turning, see Figure 1). Gravity helps to move material through the coating drum, which is slightly angled with the inlet end raised. Material is processed for a predetermined retention time within the drum before being discharged continuously.
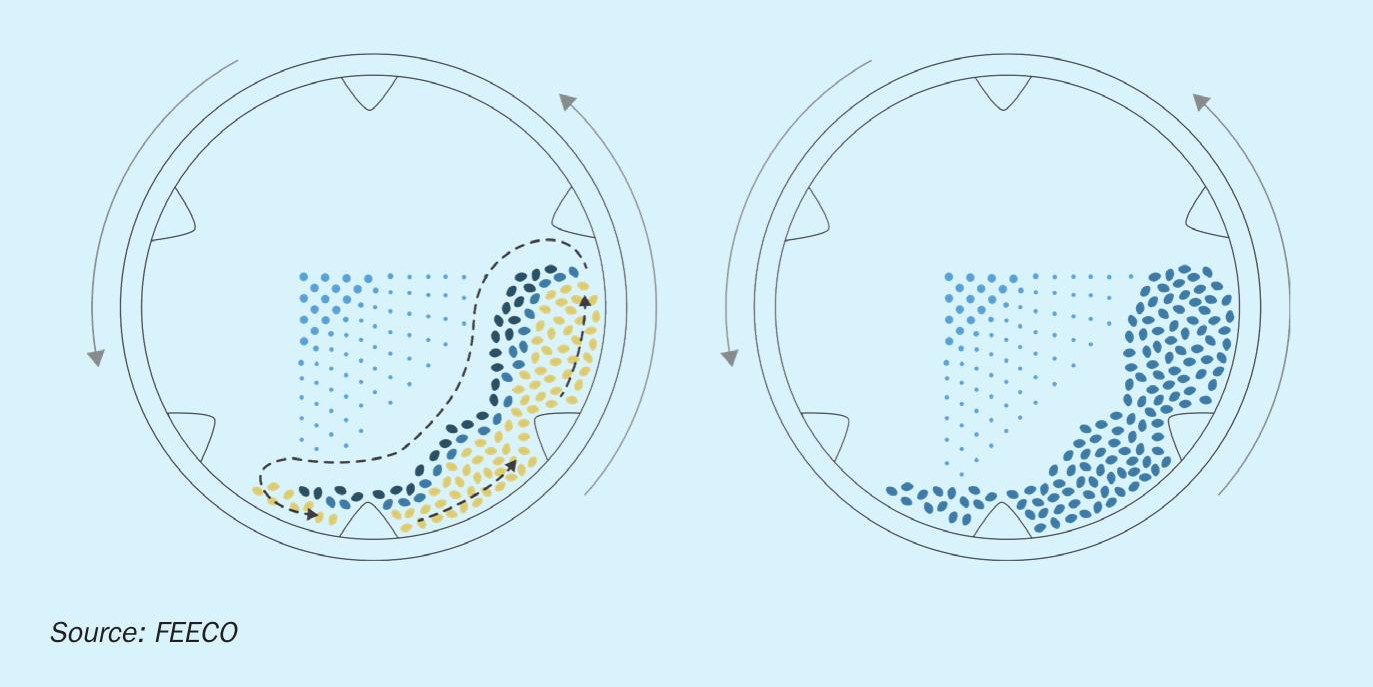
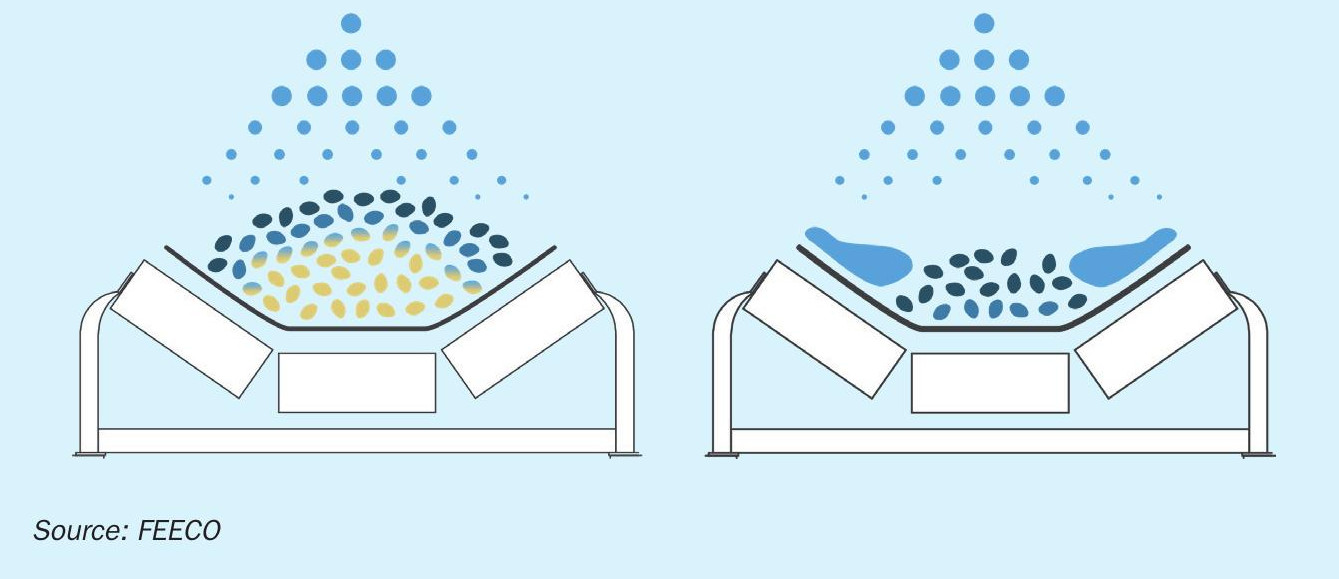
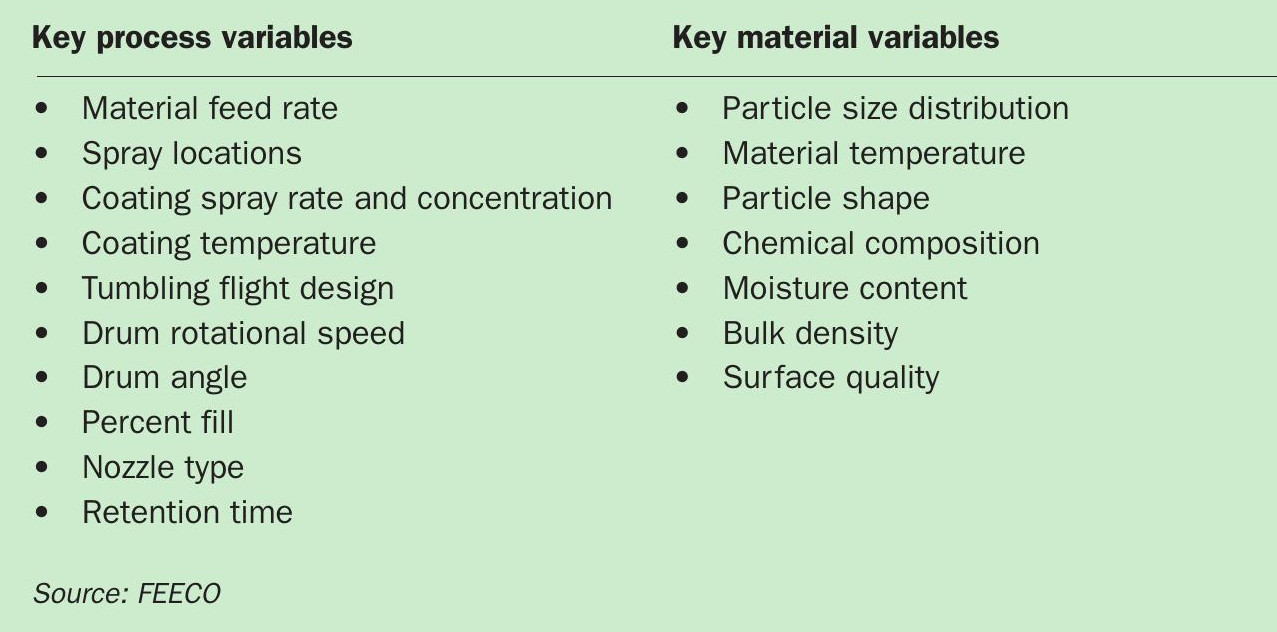
This approach is in stark contrast to how granules are coated on a conveyor belt, another popular but less effective fertilizer coating method. Some producers try to ensure all the granules on the conveyor belt are properly coated by reducing the quantity of material being conveyed. However, this can result in both overspray (spraying onto the belt) as well as the oversaturation of materials with the coating agent (Figure 2). This wastes significant amounts of coating and often causes operational problems.
For this reason, fertilizer producers that switch from conveyor belt coating to a coating drum process can often reduce the amount of coating agent applied while still achieving the desired result. Plant downtime and maintenance can also be reduced, because the build-up of overspray on conveyor belts is completely avoided.
“Coatings provide a powerful tool for managing the rate of nutrient release from fertilizer granules, a valuable characteristic that has become increasingly important as growers seek to boost crop productivity
Developing an effective coating drum process
Numerous factors influence the coating process. These include both process variables and variables introduced by the physical and chemical characteristics of fertilizer materials (Table 1). With so many factors influencing the coating process, testing is an integral part of designing a successful coating machine.
Fertilizer producers, by taking advantage of testing services, such as those provided at FEECO’s Innovation Center, can understand how well a selected coating will perform with their materials in practice. Such tests can also establish the coating drum’s design requirements and determine the process parameters needed to achieve the desired result. Test runs can be used to help evaluate different coatings and coating formulations, and establish key process criteria such as percent fill, spray rates, etc. Valuably, these data can then be incorporated in the design of the commercial-scale coating drum unit.
Concluding remarks
As well as preventing water absorption and dust generation, coating can be a powerful tool for controlling the rate of nutrient release from fertilizer products. This is particularly true when the process is carried out in a coating drum. The unique tumbling action imparted by the rotating drum, combined with its bed turning action, evenly coats the surface of every granule. The resulting controlled release fertilizers (CRFs) are reliable and effective, thanks to their superior coating uniformity, offering growers much better nutrient use efficiency (NUE) compared to standard products.