Sulphur 408 Sept-Oct 2023
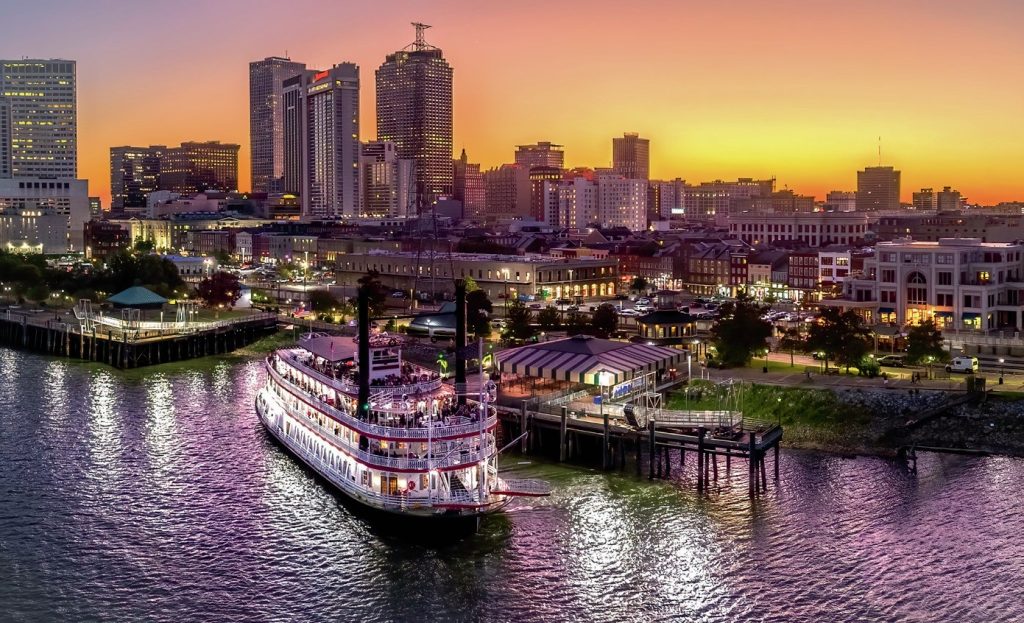
30 September 2023
Join the debate in New Orleans
CONFERENCE PREVIEW
Join the debate in New Orleans
CRU’s Sulphur + Sulphuric Acid 2023 Conference and Exhibition takes place at the Sheraton New Orleans, Louisiana, USA, 6-8 November. Take part in this leading annual forum for the global sulphur and sulphuric acid community to learn, connect and do business. Hear from industry leaders and subject experts from around world and across the industry.
The 39th Sulphur + Sulphuric Acid 2023Conference and Exhibition returns this year to the history-rich and fun-filled city of New Orleans. For over 35 years this event has been the premier networking and professional development event for those involved in the production, consumption and trade of sulphur and sulphuric acid.
Commercial agenda
In 2023, you can expect an expanded market outlooks agenda, including expert insights from CRU’s analysis teams on major supply and demand markets, including sulphur and sulphuric acid, plus additional industry updates from key players from across the supply chain.
In addition to the commercial agenda, the extensive technical programme will provide technical updates on the production and processing of sulphur and sulphuric acid, with industry-leading presentations covering new innovations in process technology, materials and equipment developments, as well as practical case studies highlighting operational experiences and plant improvements.
Participants will also be able to interact with speakers and SME’s via live streamed panel discussions and Q&A sessions and attend troubleshooting clinics.
Interactive troubleshooting clinic
On the first day of the conference there will be troubleshooting clinics for sulphur and sulphuric acid. Both seasoned plant operators/engineers and those less familiar with these processes will benefit from these sessions which aim to address real-world challenges encountered while operating or maintaining sulphur recovery and related facilities/sulphur-burning, metallurgical, and regenerative sulphuric acid production facilities. These interactive sessions will explore common operational challenges, examine potential root causes, and collaboratively work toward practical solutions. Delegates are encouraged to share troubleshooting topics in advance and/or in person, during the session.
Exhibition
Running alongside the agenda will be an exhibition of world-class solution providers serving the sulphur and sulphuric acid industries providing the opportunity to discover new innovations the latest developments in process technology, equipment and instrumentation.
Technical programme
On the second and third days of the conference the technical programme is split into parallel streams, for sulphur and sulphuric acid.
Sulphur stream
The sulphur stream programme features 18 presentations and 4 panel sessions covering the following key topics:
- Sulphur product: Safe and effective forming and handling;
- Sulphur plant design: Challenges and solutions for new/existing facilities;
- Innovations in hydrotreating, gas treating and sulphur recovery;
- The shifting sulphur industry landscape.
In addition, there will be a special session by Motiva and panellists on a joint industry RCA success story about lowering sulphur tank emissions and sulphur pit degassing.
Sulphuric acid stream
The sulphuric acid stream programme features 20 presentations and 4 panel sessions covering the following topics:
- Future of sulphuric acid: Energy transition, circular economy and supply chain;
- Sulphuric acid plant performance: Catalyst and emissions; l Sulphuric acid plant design: Technology and equipment;
- Sulphuric acid plant operations: Best practices, debottlenecking, reliability;
- Sulphuric acid plant energy management: Gas cooling and waste heat recovery.
Technical programme highlights
A selection of abstracts from the Sulphur + Sulphur Acid Conference technical programme.
How Keyera is handling sulphur in a challenging environment
Efficient and reliable systems are essential for managing the large volumes of natural gas liquids involved in sulphur handling. The innovative AMECO reclaimer had to tackle operational problems such as reclaim rate, durability in extreme temperatures, and protection against corrosive sulphur dust. It boasts an impressive 2000 t/h reclaim rate and exceptional durability tailored for the harsh Northern Alberta environment. Automation and remote-control features minimise human intervention on-site, thereby enhancing safety.
A retrofit solution for remelting a sulphur pipeline
Sulphur has been safely transported in sulphur pipelines several km long with both resistive skin heating (electric) and hot water (glycol) jackets. However, if the heat is interrupted long enough for the sulphur to solidify, the phase behaviour of sulphur causes challenges for any remelting process.
As many longer pipelines have very practical and efficient resistive heating, ASRL proposes incorporating a supplemental internal flow line which could be used to circulate hot glycol/water only after a freezing event. If this strategy were employed, the radial stress could potentially be relieved before re-energising resistive heating and therefore safely re-establishing flow.
New low-density titanium dioxide catalyst for improved sulphur recovery
Axens has developed a new titania-based catalyst called CRS 41, which has a much larger porosity than Axens’ benchmark titania catalyst CRS 31. Thanks to a proprietary binder used during catalyst manufacturing, the porosity of CRS 41 is increased while the required mechanical resistance for loading is preserved. The large porosity of CRS 41 results in a significant improvement in product performance, allowing customers to achieve higher COS/CS2 conversions by reducing the reactor size or the titania requirement by 10%.
The new CRS 41 features a reduced sock loading density of 700 kg/m3 , which makes it ≈20% lighter than CRS 31. Thus, the cost-to-fill is more attractive than with CRS 31 without compromising performance and pressure drop.
Living with hotspots at the SRU thermal oxidiser combustion chamber due to refractory failures since 2010
Malaysian Refining Company Sdn Bhd’s (MRCSB) sulphur recovery units were revamped in 2009 to increase the sulphur processing capacity. However, both newly revamped SRU trains experienced repetitive hotspots caused by refractory failures. The plant operation team managed the SRU trains with hotspot conditions, executing shutdown activities for both SRU trains alternately every 12 months since their commissioning in 2010.
The presentation will cover the problems faced by MRCSB, efforts performed to identify the root cause of the problem and current efforts being taken to eliminate the hotspot issues.
Enhancing durability of equipment through innovative redesign of the economiser in sulphuric acid production
This presentation details the inventive redesign of an economiser at the 1,800-t/d sulphuric acid DCDA plant at Petrokimia Gresik. The original configuration led to significant corrosion and 21% tube inactivity within 6 years, impairing thermal efficiency and increasing the SO3 gas outlet temperature to the intermediate absorption tower. This caused sudden shock cooling, resulting in acid mist that triggered corrosion of the mist eliminator and gas-to-gas heat exchanger tube and finally impacted SO2 emission and plant performance.
A unique redesign was introduced which significantly reduced the average SO3 gas temperature at the IAT inlet, decreasing acid mist production and prolonging the operational lifespan of the mist eliminator and eliminating acid condensation in the economiser.
Case study for the replacement of the upper part of a co-current flow quench tower
Eco Services, Dominguez Plant, operates a spent acid unit in Los Angeles, California. After the spent acid furnace and the waste heat boiler the waste gas has to be cleaned and cooled down in a co-current flow quench tower. Due to the high thermal- chemical-and mechanical stress in the quench tower the acid resistant brick lining system was frequently damaged during operation, necessitating lengthy and costly repairs in each shutdown.
STEULER-KCH recommended using a new, workshop-fabricated, acid- and heat-resistant brick lining system. In the shutdown the damaged, existing upper part of the quench tower was removed and the new pre-brick lined equipment installed. The quench tower has been running without damage since 2020.
How to avoid living with an “ex-con” – Making smart converter selection choices
This presentation will look at converter design considerations ranging from stacked, staid and catenary configurations, will delve into cost/benefits of upgraded materials, will discuss when an internal heat exchanger is a good choice and how various configurations affect reliability and maintenance.
The new normal in project implementation: learnings from Covid times
The Covid pandemic has changed engineering and project implementation and it is highly unlikley that we will return to pre-Covid ways of working. The impacts can be seen in many areas of the business, including new ways of working based on digital tools, the hybrid office and ways of communicating with one another.
Metso will discuss the learnings from the pandemic and will also focus on further post pandemic refinements of project implementation based on digital tools and virtual teams that will take place to potentially cope with the future challenges such as supply chain bottlenecks and regionalisation versus globalisation strategies.