Sulphur 409 Nov-Dec 2023
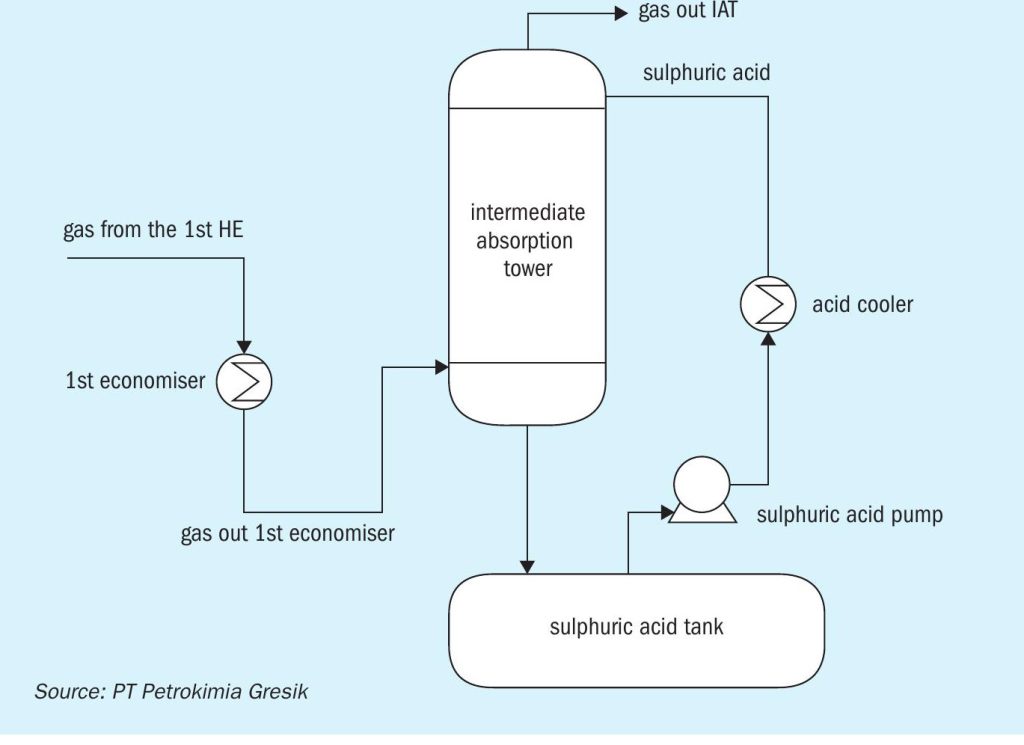
30 November 2023
Innovative redesign of an economiser
Anggi Arifin Nasution and Aldifi Putro of PT Petrokimia Gresik detail an inventive redesign of their economiser, a critical component in sulphuric acid production, focusing on energy efficiency, decarbonisation, process optimisation, and equipment durability.
Petrokimia Gresik, a subsidiary of Pupuk Indonesia that mainly produces fertilizers, is located in Gresik, East Java and occupies an area of more than 450 hectares. It has a total production capacity of 8.9 million t/a, consisting of 5 million tonnes of fertilizer products and 3.9 million tonnes of non-fertilizer products.
Sulphuric acid is one of the most important raw materials for Petrokimia Gresik, and is used for a range of products including ZA (ammonium sulphate), SP-36 (superphosphate), and NPK Phonska (compound fertilizer). To meet the demand for sulphuric acid, Petrokimia Gresik has two sulphuric acid plants with a total capacity of 1.17 million t/a. The first plant was built in 1984, and the second plant was commissioned in June 2015.
The revamped 1,800 t/d sulphuric acid plant, Unit II, described in this article is equipped with modern technology. It uses the double contact double absorption (DCDA) process, which can achieve higher conversion efficiency and lower emission levels than the single contact single absorption (SCSA) process. The plant also has a heat recovery system that can generate steam and electricity from the waste heat of the sulphuric acid production.
The revamped sulphuric acid plant supplies the phosphoric acid plant and the NPK fertilizer plant, which are also located in the same complex. By having an integrated production system, Petrokimia Gresik can optimise its operational efficiency and reduce its production costs. This will enable Petrokimia Gresik to provide high-quality and affordable fertilizers to farmers and contribute to the national food security program.
Problem description
The function of the 1st economiser (E-1203) in a sulphuric acid plant is to decrease the temperature of SO3 gas from the 1st heat exchanger (on the shell side) before it enters the intermediate absorption tower (IAT) and increase the temperature of boiler feed water prior to its entry into the steam drum (on the tube side). Fig. 1 shows the absorption process flow diagram for Sulphuric Acid Unit II.
The original design of the 1st economiser consisted of a double-finned tube with demineralised water between the inner and outer tube that serves to keep the temperature of the outer tube, which is in contact with SO3 gas, above the acid dew point. However, when there is damage or corrosion to the outer tube, the demineralised water reacts with SO3 gas to form acid and condensate, which triggers faster corrosion of the inner tube.
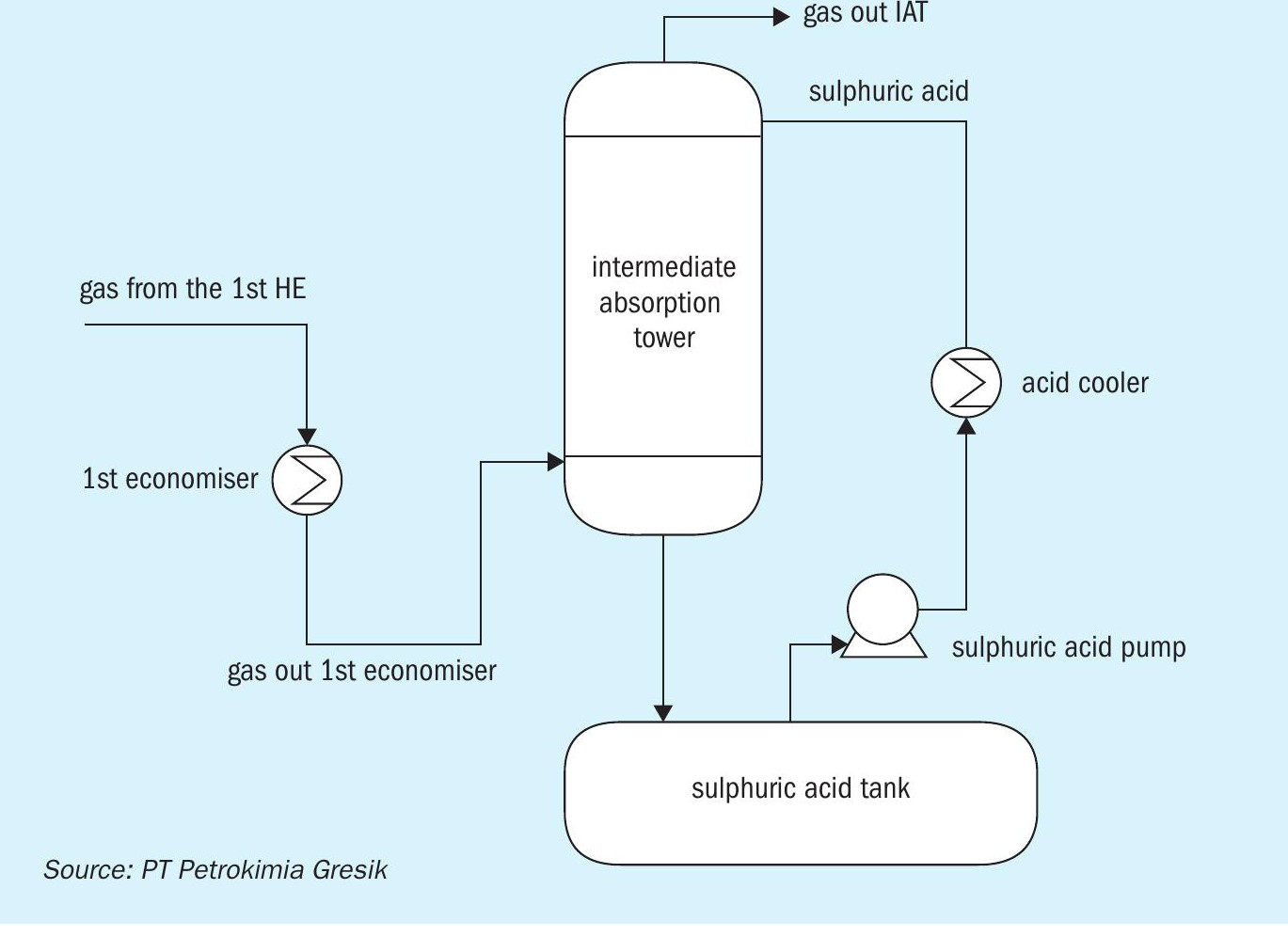
During the July 2019 turnaround, two visual inspections and pressure tests were performed at a pressure of 60 kg/cm2 . A leak was found in one of the tubes (column 12 row 9), which resulted in damage to the surrounding tubes (tubes in columns 10 and 11) and corrosion on the shell side as a result of SO3 reacting with the boiler feed water leak. The tubes in columns 10, 11, and 12 were plugged on the header side, leaving 36 tubes (12.5%) inactive out of a total of 288 tubes. Under design conditions, the SO3 gas inlet temperature into the intermediate absorption tower is 219°C, and the sulphuric acid inlet temperature is 80°C. However, with up to 60 tubes of the 1st economiser plugged within four years (before the 2022 turnaround) the average SO3 gas temperature inlet into the intermediate absorption tower was 254°C. The increase in SO3 gas inlet temperature into the intermediate absorption tower caused splashing of the inlet gas; consequently, more mist acid was produced, which raised the demister load, impacting on the reliability and lifetime of the mist eliminator in the absorption tower.
In addition, the ideal SO3 gas absorption temperature in the intermediate absorption tower is 80°C. In general, the higher the absorption temperature, the more difficult it is to absorb SO3 gas; therefore, a decrease in the intermediate absorption tower inlet gas temperature will improve SO3 gas absorption, which will increase the conversion in bed IV and reduce SO2 gas emissions.
Subsequently, a laboratory examination was conducted to investigate the composition and underlying reason for the scaling observed on the fin tube. The results of the laboratory analysis for the scale content in the 1st economiser finned tube showed mostly SO4 and Fe2 O3 corrosion products (see Table 1).
It was concluded that the scale and leakage of the tube in the 1st economiser was caused by acid formation and corrosion (see Fig. 4). Acid condensation occurs when the temperature of the tube falls below the acid dew point during shutdown and normal operation, such that the exterior of the tube corrodes and produces scale. The original design of the 1st economiser tube was a double-finned tube with demineralised water between the inner and outer tube (finned), which keeps the outer tube temperature above the dew point. However, the presence of demineralised water in the annulus triggers corrosion on the outer tube, resulting in damage to the inner tube, which causes a reaction between SO3 gas and demineralised water.
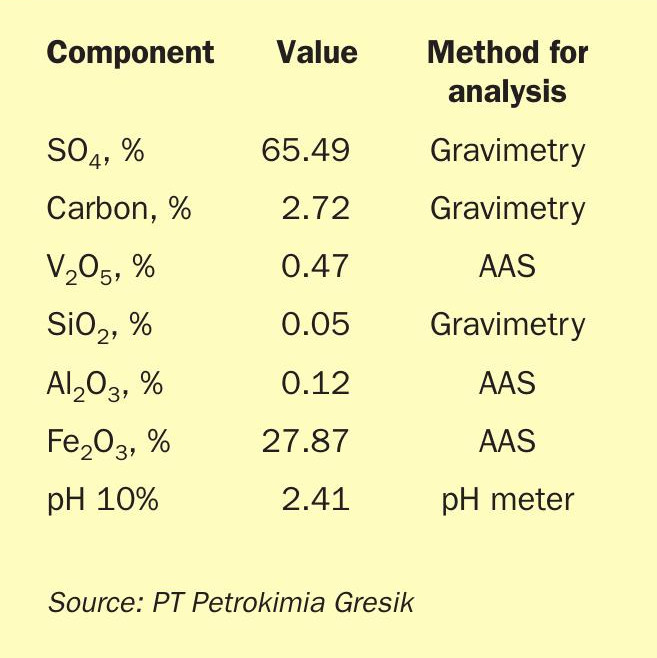
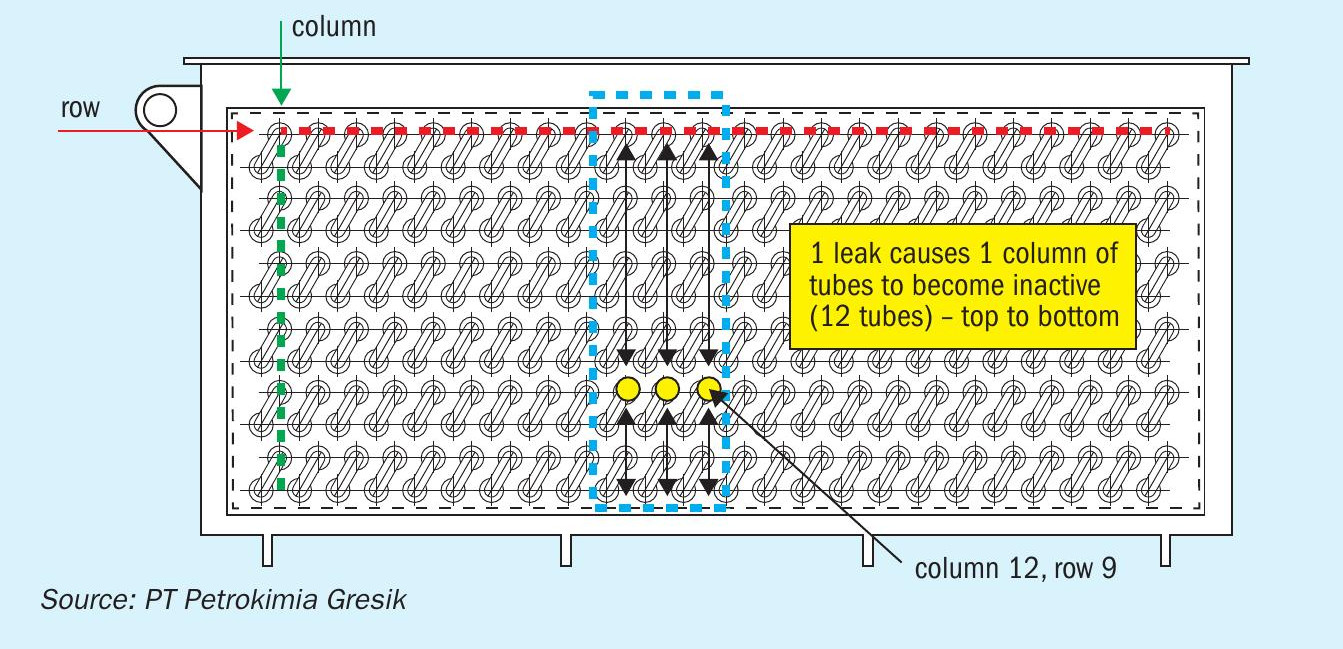
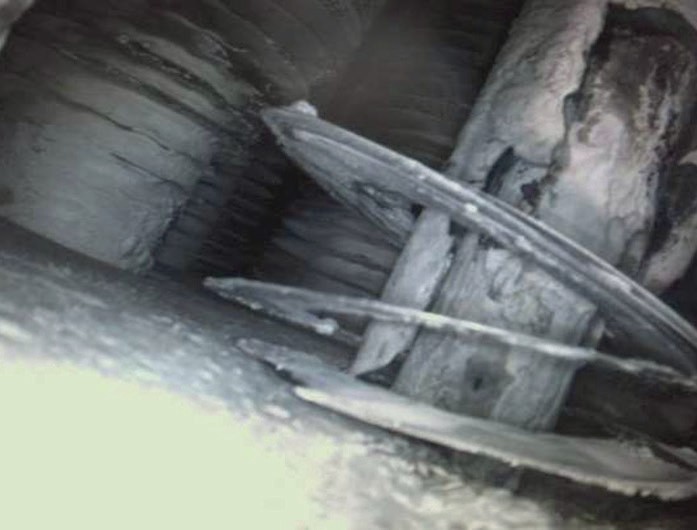
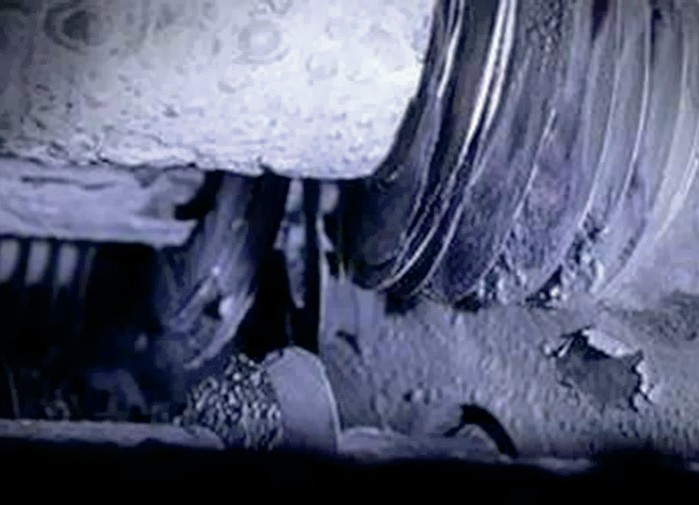
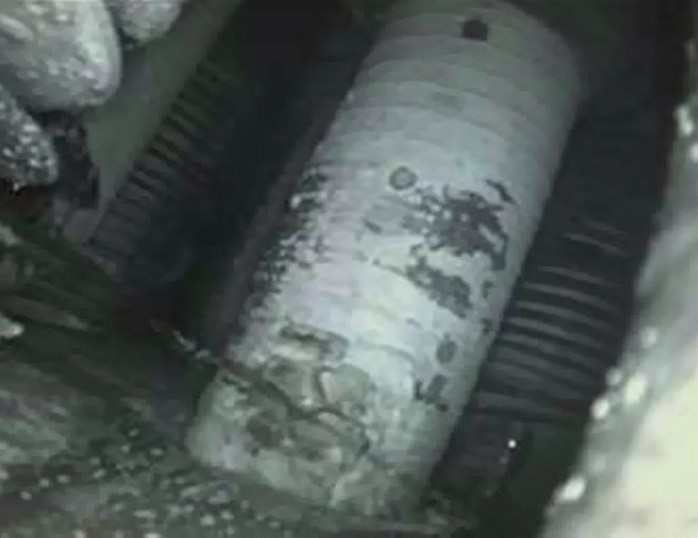
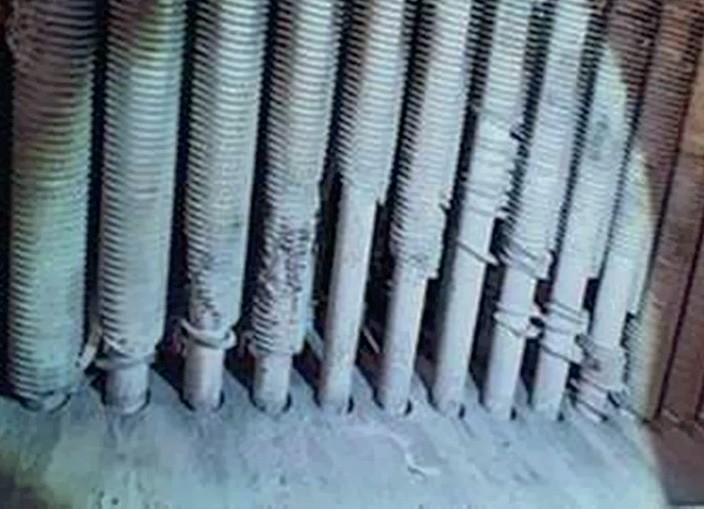
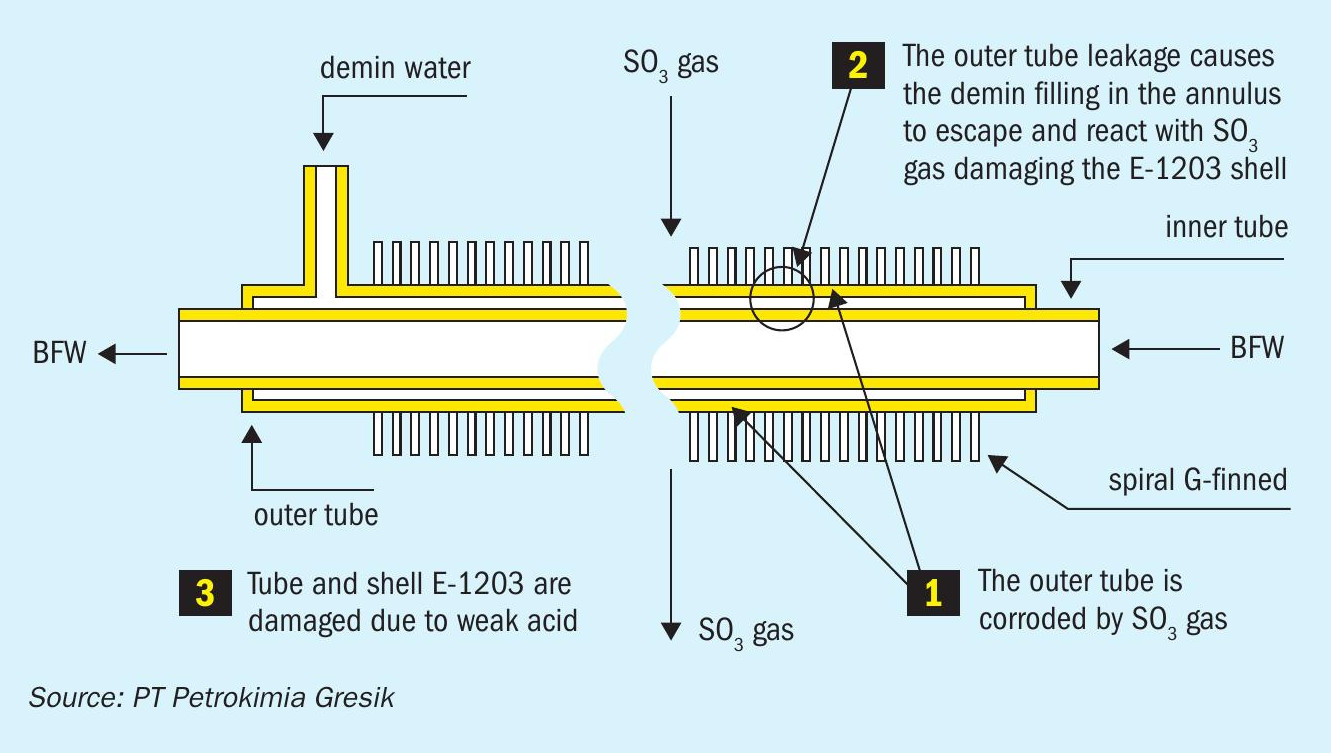
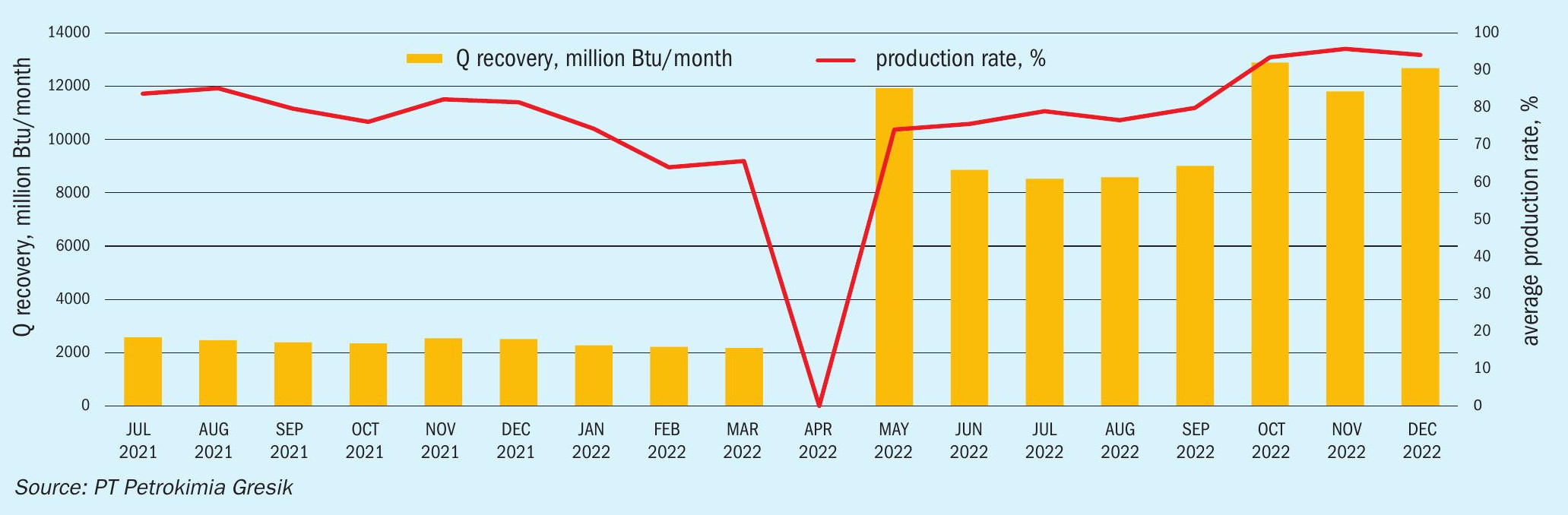
New design of sulphuric acid plant 1st economiser
Modifications have been made to the 1st economiser. It has been changed from a single compartment design, with demineralised water injection in the annulus between the inner and outer tubes, to a dual compartment design, with a single fin tube without an annulus. The modified design uses high heat transfer materials on the six top tubes and corrosion resistant materials on the six bottom tubes, considering that acid condensation tends to occur in the lower part of the economiser. The design and development of the new economiser design was carried out using ASPEN EDR (Exchanger Design and Rating) software as a technical resource for the manufacturing of the equipment. Following completion of the simulation, a new shop drawing design was conducted to determine the dimensions and installation points, as well as to simulate the load capacity of the new 1st economiser using Solidwork software. The purpose of this was to verify that the safety factor of the new equipment corresponds to pre-established standards.
Another crucial aspect involves the implementation of a HAZOP (Hazard and Operability Study), which is performed with the purpose of identifying the potential hazards and consequences associated with the installation of the new 1st economiser design. Fabrication of the economiser was conducted from January to March 2022, and the installation took place in April 2022.
The original design had a single compartment with a total of 24 columns, while the new design has a double compartment design with a total of 48 columns. In addition, the original design includes demineralised water on the annulus with a thickness of 10 mm, resulting in an inside diameter of 28 mm. In the modified design, there is no demineralised water on the annulus, so the inner diameter increases to 38 mm. The upper and lower compartments in the new design feature two different materials to improve heat transfer in the upper compartment while increasing material resistance in the lower compartment, which has a higher risk of acid condensation.
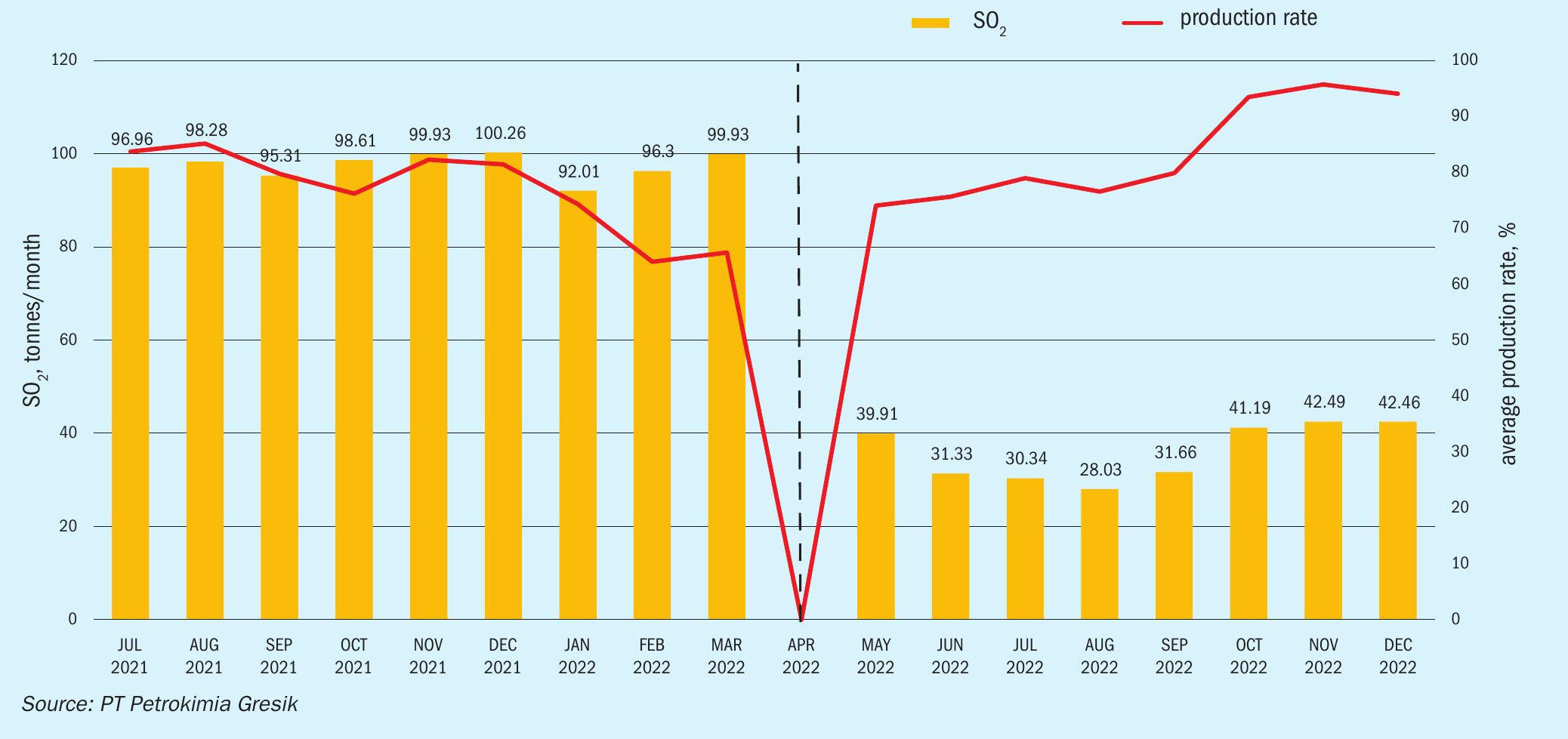
Results of improvement
The installation of the new 1st economiser was carried out during the turnaround in March–April 2022. Based on the heat recovery trend chart (Fig. 5), it is evident that following the modification of the 1st economiser, there was a notable rise in the average heat recovery. The average heat recovery increased from 2,310 million Btu/ month (July 2021 to March 2022) to 8,258 million Btu/month (April 2022 to December 2022), while maintaining a similar production rate. The chart in Fig. 5 indicates that the heat recovery prior to the replacement of the 1st economiser continuously fell below the designated heat recovery. Conversely, following the replacement, the heat recovery consistently surpassed the designated heat recovery. The increase in heat recovery can be expressed through the addition of MPS (medium pressure steam). Before the replacement of the 1st economiser (July 2021 to March 2022), there were average unrecoverable steam losses of 2,031 tonnes per month, whereas, after the replacement of the 1st economiser (April to December 2022), there was an increase in steam recovery (gain) of 933 tonnes per month above the initial design.
In addition, the chart in Fig. 6 clearly shows a decrease in SO2 emissions from the sulphuric acid plant after the modification.
The chart in Fig. 7 depicts the acid condensation drain trend for the 1st economiser from June through December 2022. As predicted in the ASPEN EDR simulation, it can be seen that acid condensation does not occur where the minimum temperature of the outer tube wall is 165.39°C, i.e. higher than the dew point for acid condensation.
The modifications and improvements to the 1st economiser design have resulted in several advantages compared to the initial design, which can be summarised as follows:
- The change in design from a double fin tube with demineralised water to a single fin tube without demineralised water eliminates the risk of a reaction between demineralised water and SO3 when there is an outer tube leak, which can trigger faster inner tube corrosion.
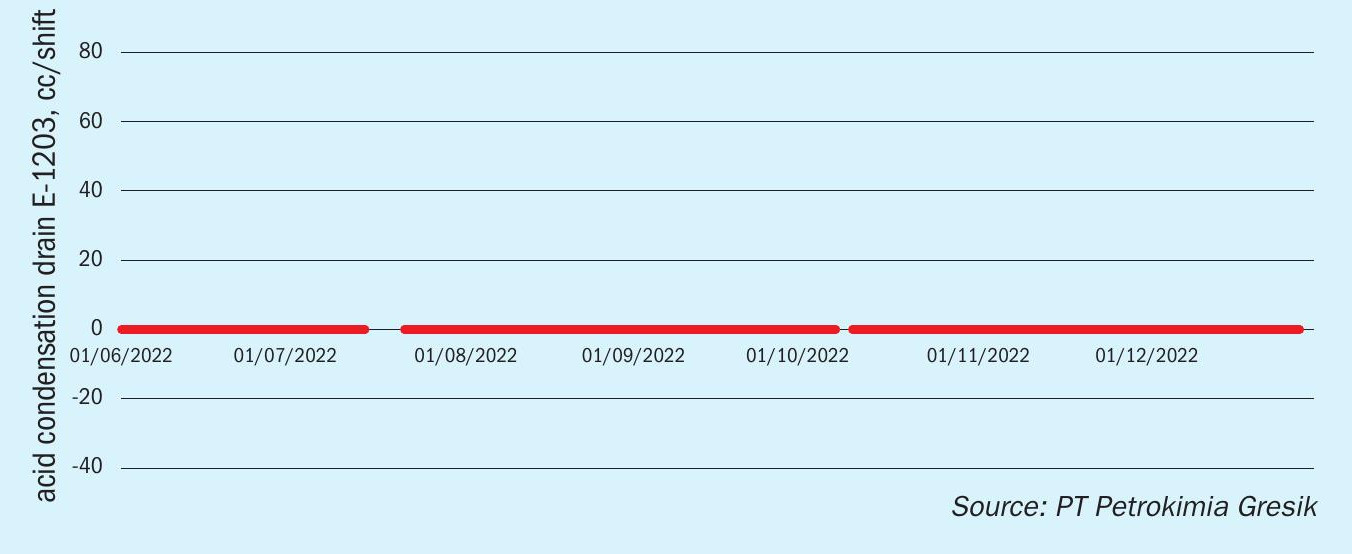
- The design change to a single fin tube eliminates the risk of gaps forming between layers (e.g., carbon steel and aluminium) during the fabrication process.
- Increased reliability by changing the design from a single compartment (24 columns) to a double compartment (48 columns). In order to avoid the potential for galvanised corrosion of the U-tube joints at the boundaries of the 6th and 7th tube rows (dissimilar material), a tube header is added into the system with a flange-to-flange connection, utilising a non-metal spiral wind gasket. Additionally, nuts and bolts are applied, which have been coated with anti-corrosion paint. If there is a failure in one tube, the deactivated tube column will be reduced from 12 tubes to 6 tubes.
- Changes in the dimensions of the thickness and ID tube, namely, the initial design has a metal thickness of 10 mm (excluding 6 mm of stuffing material) to a metal thickness of 11 mm, so that the ID tube changes from the initial design of 28 mm to 38 mm. This makes the tube side pressure drop lower.
- It had the best heat exchange among simulated alternatives, with an over-design of 11.3% over the initial design. Consequently, this improvement has yielded higher steam output and high heat recovery. The gas outlet temperature could be regulated by operating the BFW valve bypass opening.
- Having a minimum outer tube wall temperature higher than the acid dew point (>165 °C) prevents acid condensation which mitigates corrosion and equipment damage, and the corrosion-resistant lower compartment material makes this design safer.
The new design has reduced the inlet gas splashing (sudden shock cooling), which has had a positive impact on the reliability and lifetime of the mist eliminator can be maintained, as well as increasing the heat recovery of the 1st economiser and conversion in bed IV of the sulphuric acid converter.
Conclusion
The economiser is a vital component in sulphuric acid production that affects the energy efficiency, environmental impact, and operational performance of the plant. Petrokimia Gresik’s innovative redesign of the economiser, changed the configuration from a single compartment to a dual compartment and uses different materials and tube types for each compartment. The new design improves heat transfer, reduces corrosion, and lowers the SO3 gas temperature at the intermediate absorption tower inlet. Using ASPEN EDR simulation and field observations at the Petrokimia Gresik plant, the outcomes demonstrate the many benefits of the new design. The results show that the redesigned economiser saves up to 8,258 million Btu/month of energy, decreases SO2 emissions, and extends the equipment lifespan. The successful redesign of the economiser improved the sulphuric acid production process and contributes to the industry’s decarbonisation objectives.
Reference
Acknowledgement
This article was presented at the CRU Sulphur + Sulphuric Acid Conference 2023, New Orleans, LA, 6-8 November 2023.