Sulphur 410 Jan-Feb 2024
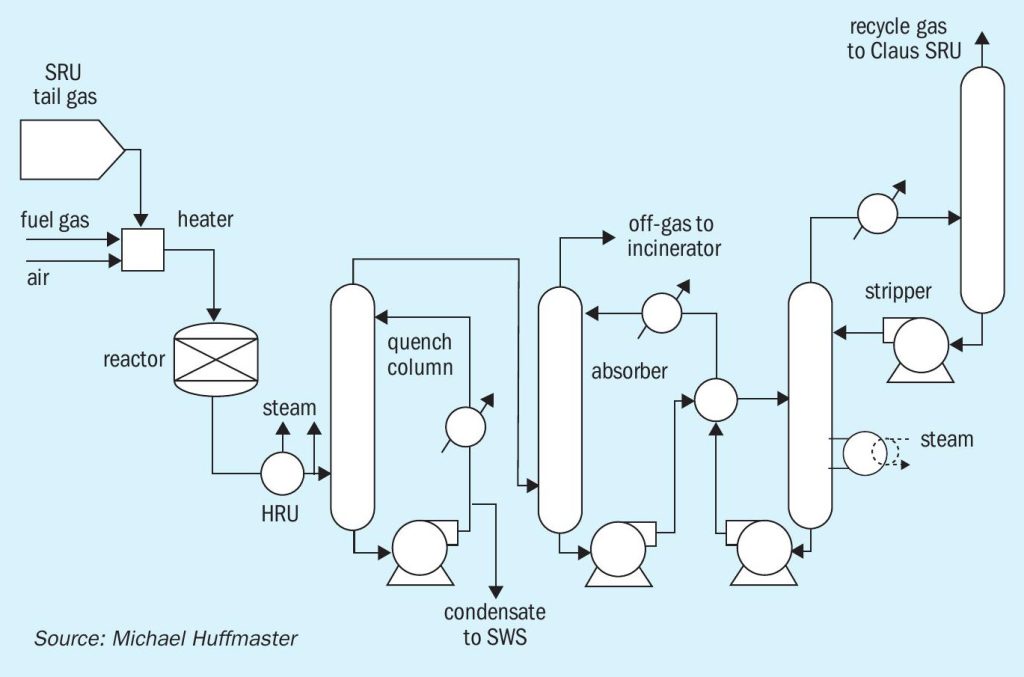
31 January 2024
Cobalt-molybdenum catalyst activation in low temperature TGUs
CLAUS TAIL GAS TREATING
Cobalt-molybdenum catalyst activation in low temperature TGUs
Part 1
Cobalt-molybdenum (CoMo) catalysts are integral components of tail gas units (TGUs), playing a vital role in reducing harmful sulphur dioxide (SO2 ) emissions arising from Claus sulphur recovery units. Effective activation of these catalysts is essential for their optimal performance. The consequence of sulphiding at low temperatures and atmospheric pressure in low temperature TGUs is to compromise effectiveness of catalyst activation. In the first part of this two-part article, Michael Huffmaster, Consultant, explores CoMo catalyst activation at low pressure, focusing on sulphiding reaction pathways and the impact of temperature and the composition of the sulphiding media on reaction kinetics, specifically the concentration of H2 , H2 S, and H2 O.
Cobalt-molybdenum (CoMo–Al2O3) catalysts are integral components of tail gas units, playing a vital role in reducing harmful sulphur dioxide (SO2 ) emissions from Claus sulphur recovery units in refineries and gas plants. The catalyst function is to convert all sulphur species from the Claus unit to hydrogen sulphide (H2 S) in the hydrogenation reactor. This H2 S is recovered via an amine system and recycled to the upstream Claus unit. Relatively sulphur-free off gas is incinerated and released to atmosphere.
A reduction in SO2 emission to the atmosphere has been achieved via sulphur recovery units and removal of sulphur from fuels over the past 50 years. Air quality, thus quality of life, has improved. This progress needs to continue in our contemporary practices and innovations.
Claus and TGU processes are complementary, combining to recover sulphur from amine acid gas and sour gas, found in gas treating and refining applications. The Claus process produces elemental sulphur and typically achieves 96% sulphur recovery. The TGU improves the overall sulphur recovery to 99.9%.
The role of the catalyst in the hydrogenation reactor is providing catalytic sites for conducting TGU reactions at operating temperature. Effective activation of CoMo catalysts is essential for their optimal performance. As important as it is for TGU operation, activation is not well understood, owing to complicated chemistry1,4 and because conventional TGU in-situ techniques produce good results.
The advent of low temperature tail gas catalysts has led to units constructed without the capability to achieve temperatures of 300 to 315°C traditionally applied for activation of these catalysts. Many low temperature TGU (LT TGU) offer only 240°C reactor inlet or lower. The consequence of low temperature activation has been weak catalyst activity.
Activation utilising H2 S and H2 proceeds with reduction and sulphidation of MoO3 through a number of steps, involving complex and poorly delineated chemistry1,14 . Sulphidation of CoO is more straightforward, but its interaction with MoS2 nanoparticle edge to promote active sites is also complicated and not well defined. Examining research and proposed reaction mechanisms helps clarify the impact of temperature and the composition of the media on sulphiding kinetics at atmospheric pressure, specifically the concentration of hydrogen (H2 ), hydrogen sulphide (H2 S), and water (H2 O).
Improving effectiveness of catalyst activation in low temperature tail gas units lies in utilising heat of exothermic activation reactions and managing process parameters to achieve bed temperatures greater than 260 to 270°C. As constraint, operations must be in concert with catalyst activation limitations for temperatures and guidelines to achieve good metals dispersion while avoiding damage such as cobalt reduction.
TGU and low temperature impact
The TGU process converts SO2 , elemental sulphur and other sulphur species, to H2 S which is then recovered and recycled to the Claus unit. Additionally, CO is converted via water-gas shift. A conventional TGU is shown in Fig. 1. Its line-up includes an inlet heater or reducing gas generator, hydrogenation reactor, and amine circuit.
Key equipment changes related to conventional vs. low temperature operation are highlighted in Fig. 2. These changes provide reactor preheat using a high pressure steam heater exchanger in lieu of a burner or reducing gas generator and delete a low pressure steam energy recovery exchanger.
A heater is used to raise the feed gas to the required TGU reactor inlet temperature. The reactor inlet temperature is set to ensure reactions proceed sufficiently to achieve conversion of sulphur species necessary to meet stringent environmental regulations. The relationship of sulphur species conversion with catalyst kinetic activity coefficient and reactor space velocity is addressed in other papers6 , but the designer’s role is to provide sufficient catalyst to achieve the operating company’s required conversion based on catalyst vendors’ activity data for selected operating temperatures.
Introduction of enhanced catalysts with strong activity at low temperatures enabled TGUs to operate with 200 to 220°C reactor inlet temperature. In conventional TGUs the heater is a line burner (or reducing gas generator) or a high temperature heat media exchanger and is required to deliver process temperatures of 250 to 300°C. Low temperature TGUs often feature a heat exchanger (steam or heat media), which reduces capital cost, improves operability and can offer extended catalyst life, all desirable features.
A consequence of the low temperature configuration is preheater downgrade and inability to achieve more than 240°C as the inlet temperature to the reactor. This limitation arises because heat exchangers use condensing MP steam at 600 psi or 42 bar. Field reports suggest operating systems may see 5 to 10 degrees lower temperature. The reactor temperature inlet of 240°C in low temperature TGUs is also the maximum temperature for catalyst sulphiding. In contrast, conventional TGUs are capable of reactor inlet temperatures of 300 to 315°C for final heat soak during sulphiding, which achieves strong activation.
Research published at Brimstone (Huffmaster et al, 2019) examined the influence of activation variables, in particular range of temperatures. Examination of temperature, time, and H2 concentration revealed diminished activity from low temperature activation. As shown in Fig. 3, the best achieved activation at 220°C was 66% of the activity of fresh catalyst. The effect of low hydrogen concentration was found to exacerbate low temperature activation, needing 10% or 0.15 bar for minimal 66% activity and falling below 55% at lower values of 1.5% or 0.02 bar. Furthermore, this finding was consistent across all TGU catalysts vendors suggesting the fundamental character of CoMo-Al2 O3 catalyst is closely tied to activation9 .
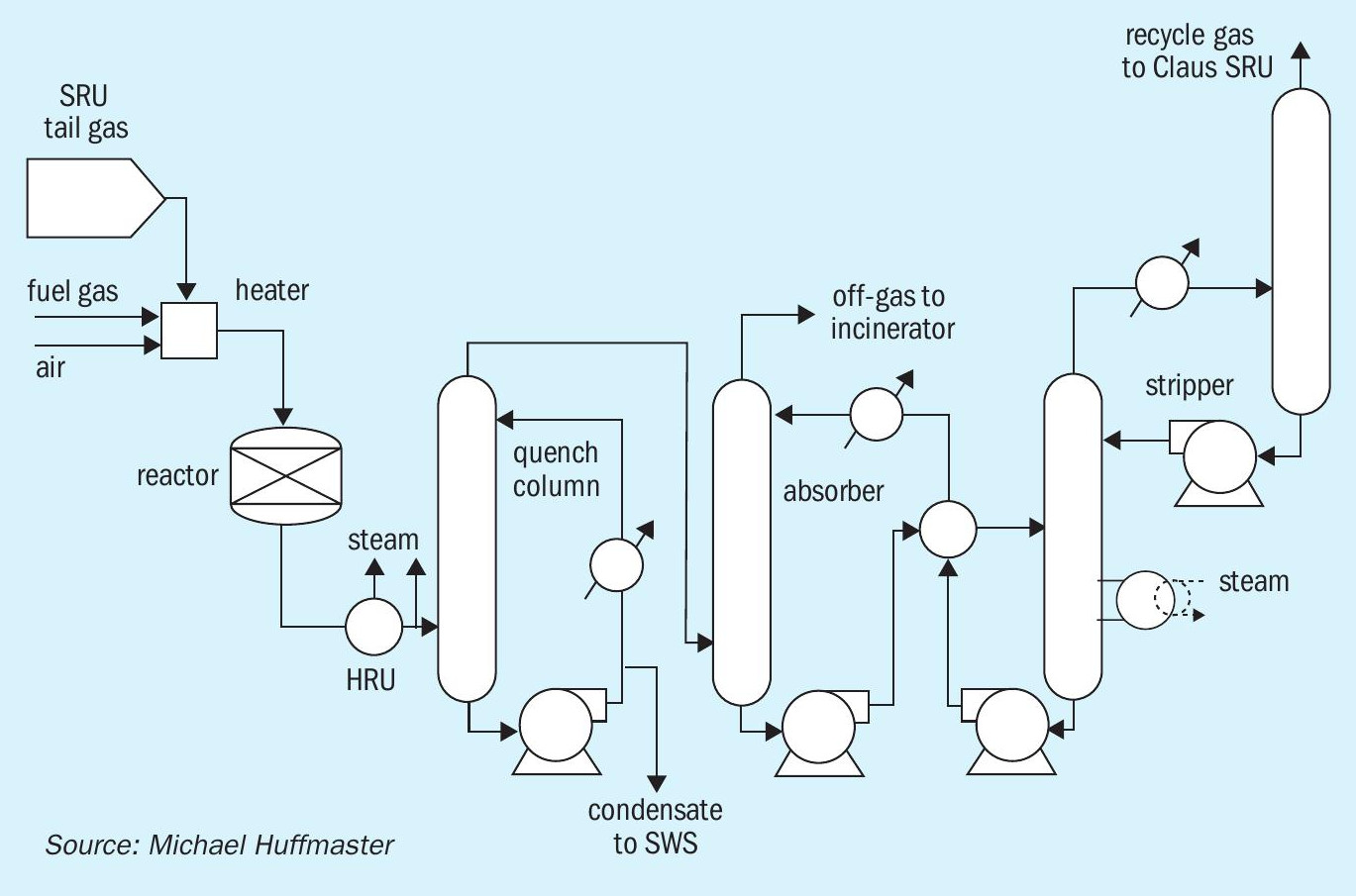
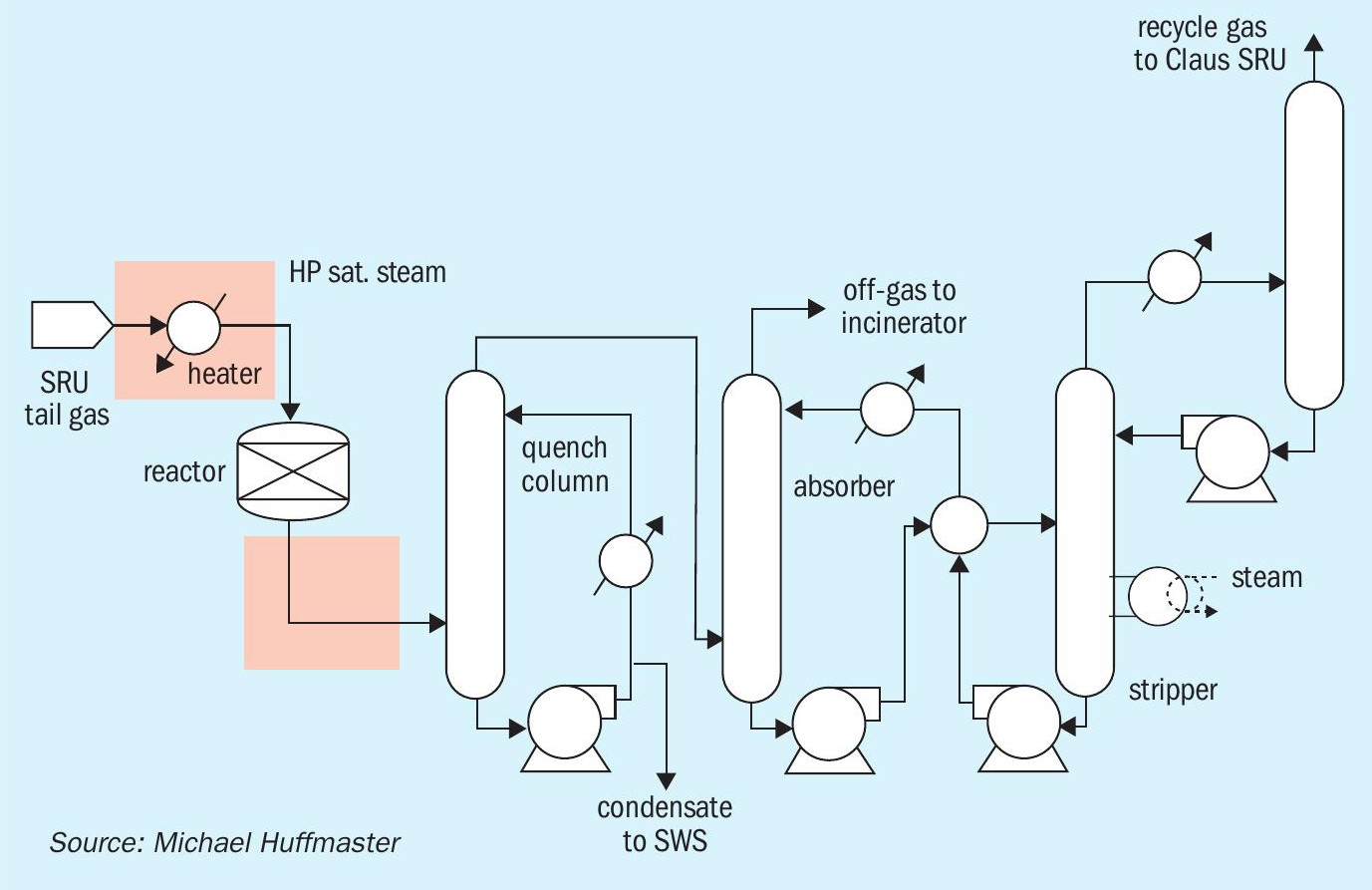
Performance in several low temperature TGUs of in-situ sulphided catalyst was approximately 50% of full catalyst activity; this activity level is typically associated with spent catalyst. Of these field-applied activation practices, some only realised 225°C bed inlet temperature and exhibited very shallow exotherms. Undoubtedly other influences affected these units such as high initial water load, low hydrogen partial pressure, and slow temperature ramp up.
This reveals design shortcomings on preheat even for low temperature units. As well, operations adopt very conservative practices, erring on the side of caution, and duly following decades-long practices heeding catalyst supplier’s cautions to raise temperature slowly to avoid temperature excursion as excessive temperature could damage catalyst. These conservative practices combine for less than effective activation at low temperature, not even achieving 240°C in the bed.
Tail gas unit catalyst
The CoMo-Al 2 O 3 catalyst is widely applied in refineries for hydro desulphurisation (HDS) and hydro treating, accounting for 10% of worldwide catalyst volume. Because these are major markets, they enjoy scientific and technical interest. Tail gas applications do not attract the same level of interest as HDS, but they use similar catalysts. Much of the HDS developments and basic research can be useful as applied to TGU catalysts.
The manufactured form of TGU catalyst is oxidic, with MoO 3 /CoO metals on a high surface area γ-alumina support, which is highly porous, with minimal diffusional resistance, designed for heterogeneous gas phase application. Metal oxides are impregnated and dispersed on an activated alumina support to provide a large number of catalytic sites. TGU catalysts are Type I, calcined to disperse and distribute the impregnated metals. Type II catalysts utilise a chelate to improve dispersion and are not calcined.
CoMo catalysts require activation to have catalytic function in the process environment of hydrogen and hydrogen sulphide. Activation is achieved by heating in a controlled process with hydrogen and H 2 S, traditionally finished at 315 to 345°C.
The activated MoS 2 /CoS form of these catalysts are active for these tail gas reactions:
Metal-catalysed hydrogenation
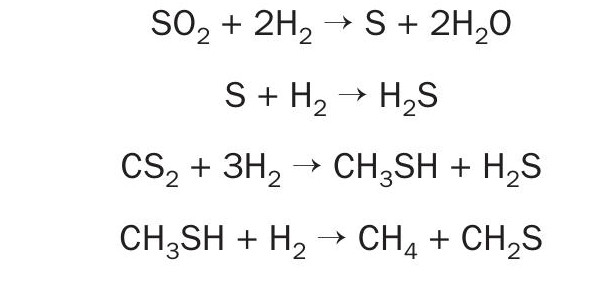
Shift reactions
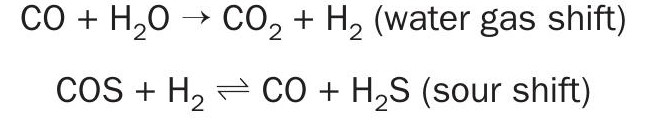
Alumina-catalysed hydrolysis
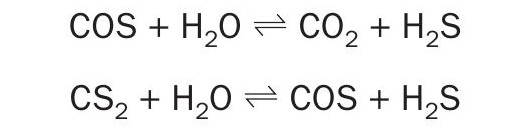
Note: SO participates in other reactions, including reduction by CO; reduction by CS ; Claus reaction with H S which proceeds on alumina until SO is extinguished.
Strong activity at operating temperature enables the reactor to achieve high conversion of sulphur species, required for the TGU to attain high sulphur recovery and low emissions. Low temperature catalysts developed over the last 20 years express strong kinetic activity at temperatures as low as 200 to 230°C when fully activated.
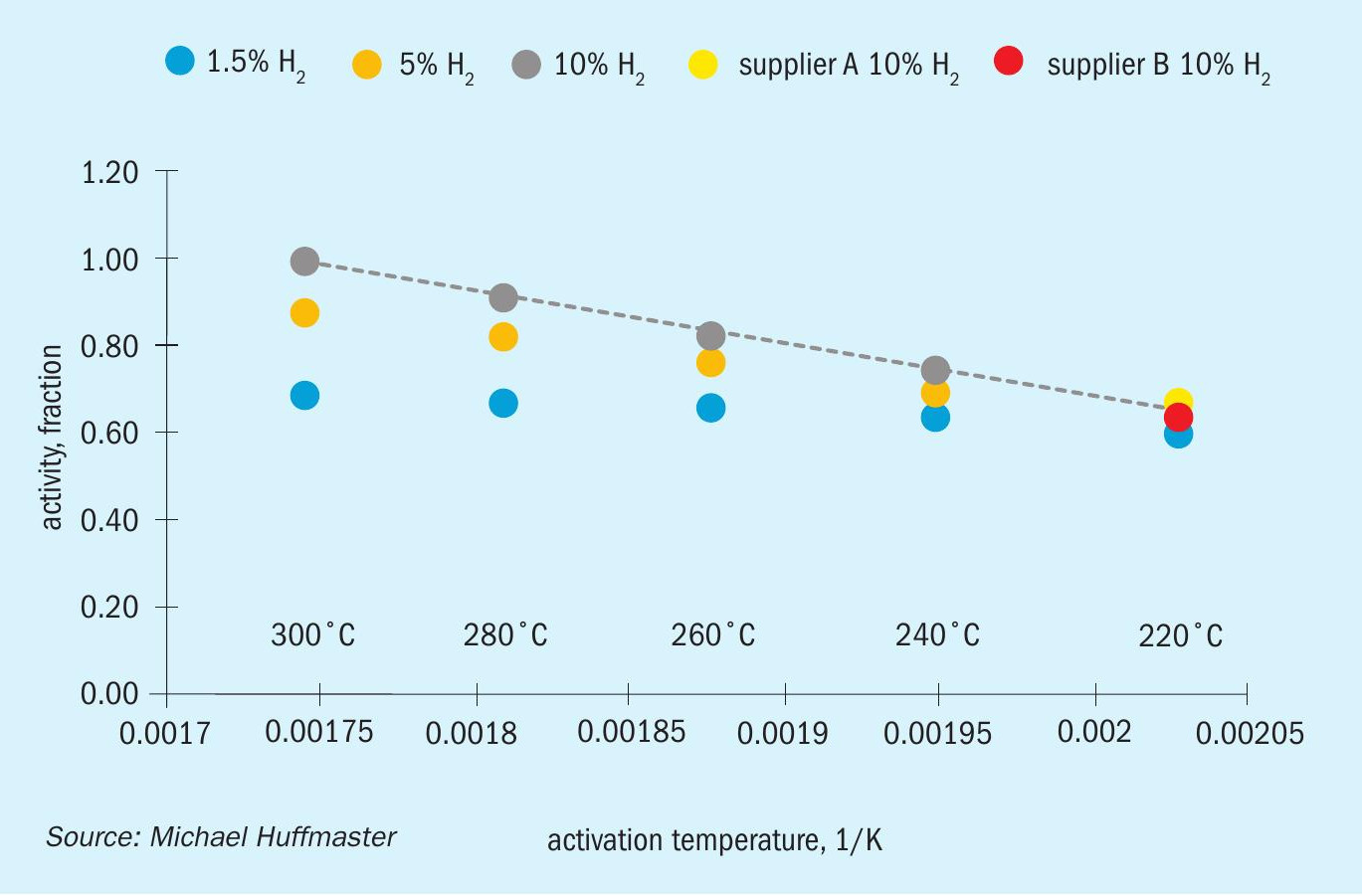
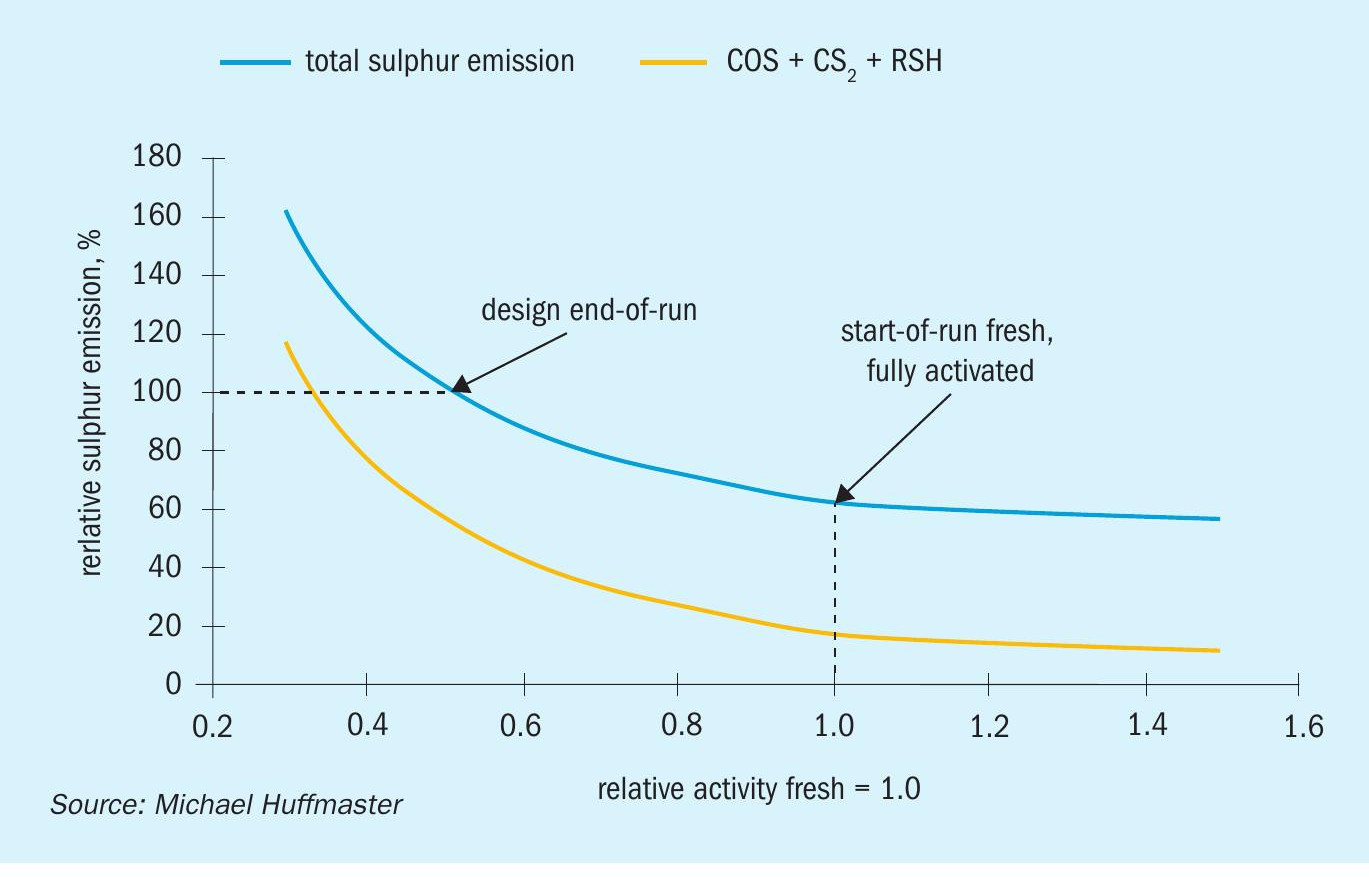
The consequence of weak activation from low temperatures is diminished catalytic function. The consequence of diminished function and low operating temperature is reduced conversion of target reactions. This condition increases the concentration of sulphur species such as COS, CS 2 , and CH 3 SH in the reactor outlet, which slip past the amine system and raise emissions.
An example of expected sulphur emission as a function of relative catalyst activity is shown in Fig. 4. Relative activity reflects decline of catalyst activity through aging and poisoning. The emissions include sulphur species COS, CS 2 , and RSH which pass through the absorber, as well as slip of H 2 S at the absorber and other sources such as pit vent, sulphur degasser or sour water tank vents. At the design point, approximately half the emissions are from COS, CS 2 , and RSH. Sulphur emissions vary with conversion achieved on COS, CS 2 , and RSH. Conversion is impacted by relative activity and residence time. Sulphur species conversion is reasonably represented as following first order reaction mechanics6 :
conversion = (1 – e-kt ),
where k = activity coefficient and t = residence time or 1/space velocity
The design point shown is to achieve 100 % target emission at end of run (EOR), typically set at catalyst relative activity = 0.5, thus ensuring there is sufficient catalyst inventory to achieve required conversion at EOR. At start of run (SOR) with fresh, fully activated catalyst the relative activity = 1 and expected emissions are about 63% of permitted or design.
Emissions would be higher if activation is weak and emissions could possibly exceed design when catalyst ages. If a low temperature activation achieves relative activity = 0.7 then initial emission is 78% of design. With activity decline by half over normal service life, relative activity = 0.35 and emissions would be 140% of design. Throughput could be reduced to 70% to maintain emission compliance.
Catalyst activity declines over life due to aging and poisoning, so sufficient catalyst inventory is needed for the unit to meet required environmental performance at EOR. For LT TGU, activity decline from aging is slower at low temperatures, although starting with weak activation means weaker activity over life and could require shortened catalyst cycles to stay in environmental compliance. Reactor temperature increase improves conversion and could extend life, although that capability will be limited in LT TGU design.
The function of the catalytic reactor depends on design parameters such as space velocity (gas rate/catalyst inventory) and operating temperature. If performance is limited then the operator may increase temperature, reduce throughput, or reduce catalyst service life. Reducing service life by increase in catalyst replacement frequency adds to operating cost but has less severe economic impact than out-of-cycle or unscheduled outage for catalyst replacement.
Activation OF Co Mo Al2 O3 catalyst
Tail gas catalysts and HDS catalysts are prepared in the form of highly dispersed molybdenum oxides on supports such as γ-alumina with 250 to 300 m2 /g surface-area to which promoters like cobalt (or nickel) are added. These are subsequently converted into the catalytically active phase by sulphidation, a controlled process conducted typically in H2 S/H2 atmospheres at temperatures between 300 and 400°C:
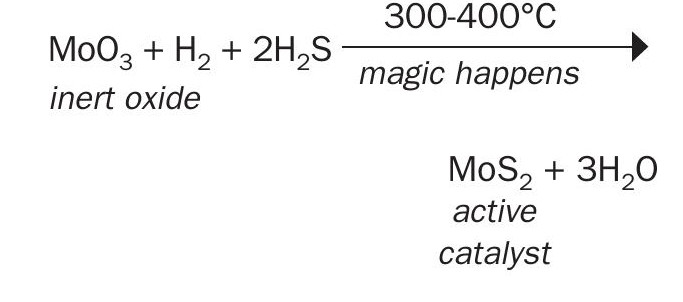
Whereas it would be useful to know the mechanism of sulphiding, as it is important to the delivery of effective catalysts, the activation chemistry of CoMo-Al2 O3 catalyst is complex and not that well understood1,4 . Research and field experience define major steps that help analyse activation and influence of process variables.
Research effort in industry and academia have probed the chemistry of HDS catalyst reaction and activation for over four decades. The investigations have followed the Topsoe Co-Mo-S model2,3 . The range of catalyst forms covered includes model compounds, e.g., MoO3 and CoMo, alumina supported catalysts, and commercial catalysts, some calcined, others not. Conditions range from ambient temperature to 400°C and system pressures from atmospheric to 20 atm with H2 /H2 S (5 to 15%). Insights also come from MoS2 monolayer-related HER studies and semiconductor research.
Research papers inform reaction pathways and kinetic steps to consider. Model compounds utilised in research are simpler systems; promoted systems enhance catalytic performance but add complexity. Alumina supports improve dispersion as well enhance sulphiding but have interactions and add complexity4 . Several essential activation steps have been elucidated, especially by advances in intense spectrographic techniques. Advancement in computational techniques for molecular properties and interactions are beginning to quantify thermochemical properties for reaction intermediates, providing the opportunity to refine sulphidation kinetics.
Research shows that the impact of high partial pressures is that sulphidation completes in a shorter time or at a lower temperature, although catalysts differ between studies. A few studies offer some information to help understand low hydrogen partial pressure.
Research identifies that above 240°C crucial steps occur, namely, transition and reduction to MoS2 followed by transformation from amorphous to the nanoparticle or slab through crystallisation.
This is of significant note for low temperature activation. The crystallisation process also needs evaluations for how it is best represented. A number of variables need consideration and an approach other than traditional nucleation theory may help, due to observations of clustering and organising14 .
Findings in these articles inform important steps and transitions in the activation pathway. They help understanding of TGU catalyst activation because TGU catalyst and HDS catalysts are similar in composition and function and activation, incorporating MoS2 nanoparticles promoted by cobalt. A summary and pathway for sulphidation of CoMo catalyst using a tail gas unit sulphiding procedure is discussed in the box on page 46.
TGU sulphiding can be summarised in three steps:
- Initial sulphur uptake (170 to 240°C): Sulphiding is initiated at 170 to 200°C in H2 and H2 S at 1 atm pressure. MoO3 and CoO are converted to their respective sulphides, proceeding through a number of parallel pathways and intermediates to form amorphous MoS2 and CoS. This first phase is characterised by sulphur replacing oxygen, then reduction of molybdenum to mixed valence, and loss of oxidic crystal structure.
- Reduction and transition (240 to 260°C): In raising the temperature from 240°C to 260°C a critical transition occurs with molybdenum becoming mostly Mo+IV, an ordering of MoS2 and seeding initial nucleation sites.
- Annealing and transformation (260 to 315°C): This phase ramps to 315°C with the catalyst reacting up to stoichiometric sulphur and the transformation of amorphous MoS2 to crystalline. Activated catalyst has nanoparticles of crystalline MoS2 (monolayer or 2 to 4 layer slabs) with CoS promotion on the edges which are active catalytic sites on the alumina substrate. This completes activation.
Sulphiding reactions can initiate at ambient temperature in a H2 /H2 S environment, but TGU sulphiding is initiated at 180 to 200°C. Reactions from initiation to 240°C are captured as first phase.
Delving deeper into the chemical pathways, first consider small crystallites of MoO3 (20–40 Å) intermixed with CoO, populating the surface of an alumina substrate5 . These crystallites are well dispersed and only a few molecular layers thick (~ 2.5 average), expressing a surface area on the order of the alumina substrate.
This particle size can be estimated from knowing crystallites are distributed to a depth within pores of 60–90 Å. The size of these, within limits, are 20 to 40 Å, which fits within 40% of pore diameter. Stacking on the order of 2 to 4 layers fits with 6.5 Å per layer for the MoS2 , as pores are not obstructed. This gives us a crystallite or platelet of 6 to 12 units across of MoO3 or MoS2 . Roughly 50% to 70% of the molecular entities would be exposed to the sulphiding medium, with the balance as interior layer or in contact or interacted with the substrate.
When the surface portion of the oxidic crystal is exposed to the sulphiding environment, it reacts with vigour. Internal layers are hidden by a very low permeability outer layer or shell such that diffusional resistance retards their reaction. Additionally, a portion of the crystal atomic structure interacts with the substrate to form quite stable chemical bonds during calcining5 . The interacted portion of the oxidic crystals have higher activation energy barriers to sulphide. The temperature required for sulphiding CoAl2 O4 was 625°C1 , therefore it would not sulphide at TGU conditions.
On this landscape consider sulphiding reactions pathways for metal oxide: crystals of MoO3 and CoO dispersed on γ-Al2 O3 are exposed to a H2 S/H2 mixture at ~ 1 atm:
- Initial sulphiding: reactions are initiated at 150 to 170°C and this chemistry prevails to 200°C, (sulphiding can initiate at ambient temperature)
– Surface layer in the MoO3 crystal lattice exchanges terminal oxygen (Mo=O) for sulphur, forming oxysulphides4,5,11,18
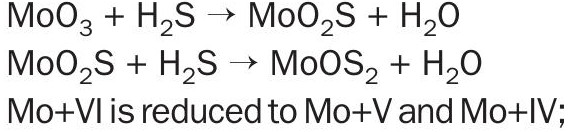
possible structures are:

– Cobalt oxide is sulphided

– Bridging ligands of sulphide and disulphide, S= and S2 = bond to adjacent molybdenum, disrupt the MoO3 lattice and create more terminal oxygen; the process continues, sulphur replacing terminal oxygen, relaxing the lattice, creating more terminal oxygen5,7 .
Activation reactions delineate potential pathways
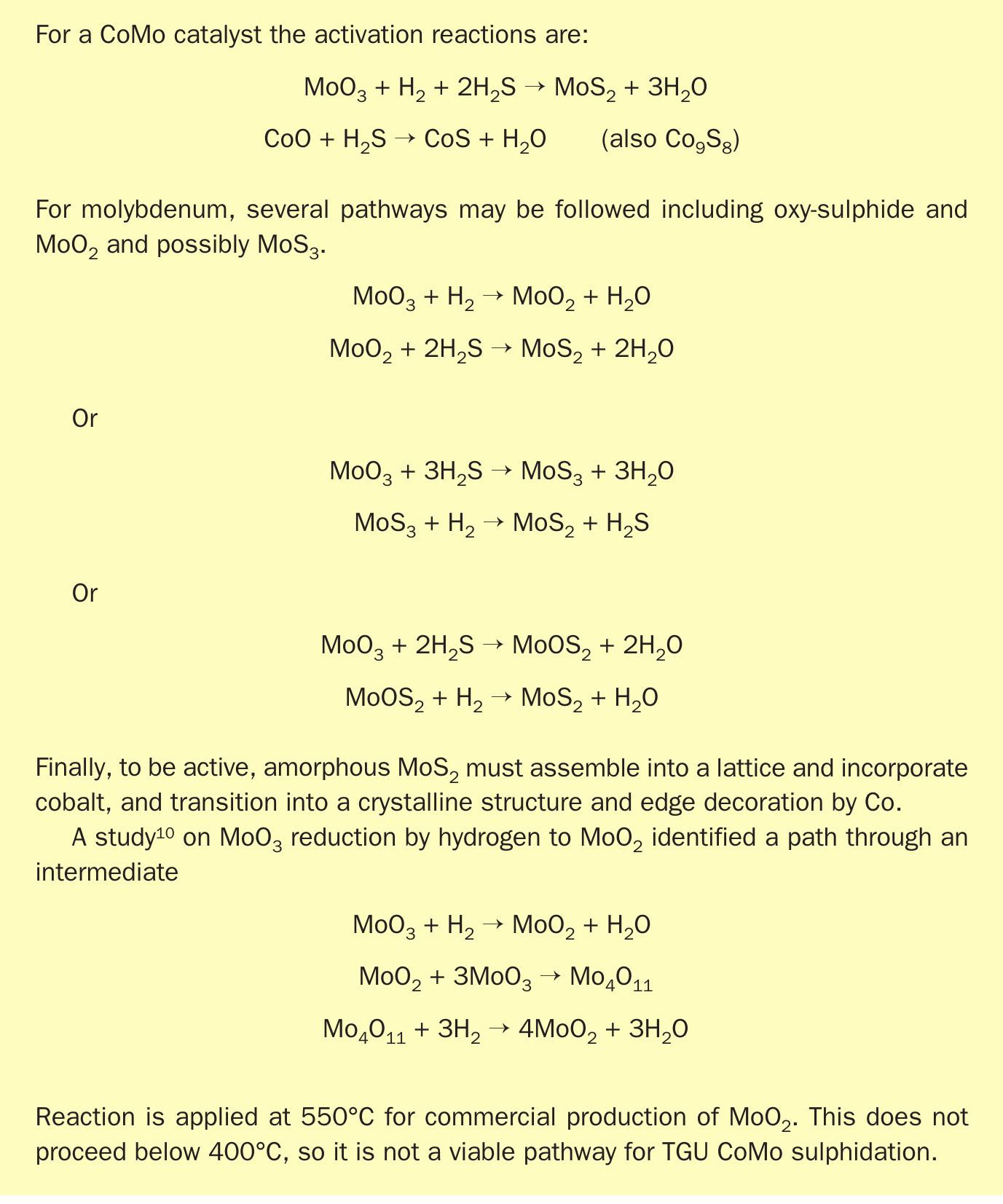
- The formal structure of MoO3 is lost. Sulphides formed are amorphous.
- Hydrogen can now be dissociated on CoS or MoOS2 to form atomic hydrogen above 150°C13 . Molecular hydrogen and sulphur are too bulky to enter the crystal interior. Molybdenum oxides are not reduced by molecular hydrogen at these temperatures (below 400 to 550°C)10 .
– Atomic hydrogen diffuses into the crystallite interior and reduces MoO3 11
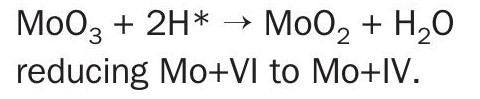
– The oxy sulphide can also reduce with atomic hydrogen, forming a MoS2 shell

MoOS2 + 2H* Õ MoS2 + H2 O m MoO3 (or oxy sulphide) can also react with H2 S to form amorphous tri-sulphide

Mo+VI may be reduced to Mo+V and Mo+IV; possible structures are:
Mo6+ S3 2-or Mo2S4 2S2 2-or Mo4+ S2S2 2-
– At 200°C most exposed active surfaces of metal crystallites are converted to sulphide or oxy sulphide and interiors have been reduced by atomic hydrogen to MoO2 .
- In the range 200 to 240°C more of the oxy sulphides and MoO2 are converted to MoS2 ; hydrogen reacts directly with Mo-S sites7 and S2 2ligands are converted to S2, depending on hydrogen partial pressure. Molybdenum valence is varied and the MoS2 formed is amorphous4,5 .
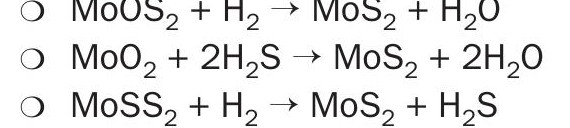
- Reduction – transition, a crucial change in the 240 to 260°C range:
– Mo+IV increases to 70% from 17%7 .
– Evolution of H2 S, potentially reflecting S2 2ligands reducing to S24,11 .
– Some studies find Mo-O signal disappears at this transition indicating conversion of MoOS2 and remaining MoO2 (in 20 atm H2 Mo-O bond signal extinguishes at 150°C)4,5 .
– The Mo-S coordination number (CN) is ~ 4 after the transition, indicating amorphous MoS24 ; Molybdenum atoms are bonded to four sulphur atoms; Haandel indicates nucleation of crystalline MoS2 begins.
- Annealing – transformation, temperature increased from 260°C to 300-350°C
– Nucleation continues and amorphous MoS2 transforms via crystallisation into slabs; bond length for Mo-Mo increases to (3.17Å) corresponding to crystalline MoS24 .
– Hydrogen facilitates crystallisation transition, reducing activation energy8,13 .
– Sulphur uptake continues until completed with S:Mo ratio of ~2.
– Coordination number of Mo-S increases to 6, indicating a MoS2 crystalline structure4 .
– The S:Co ratio is ~ 1; Have CoS and Co9 S8 ; latter is dominate, but not active19 .
– Incorporation of CoS on the edge of the MoS2 slab19 .
- MoS3 reduction to MoS2 – enhanced by higher H2 partial pressures or higher temperatures; decomposes at 310°C; studies report MoS3 are (Mo3 ) cluster structures, amorphous, poorly organised but of Mo+IV valence20 .
Transition of amorphous MoS2 into crystallites is accomplished with annealing, forming nanoparticles or slabs and Co interacting on the edge of 2H MoS2 two-dimensional nanocrystal-active catalyst sites. Molybdenum is bonded to six sulphur atoms, each sulphur atom is bonded to three molybdenum shown in Fig. 5.
The sulphiding reaction pathways identify crucial aspects of activation, including important transition point at temperature of 240 to 260°C. Also required is the presence of hydrogen sulphide or a sulphur source, hydrogen, and annealing amorphous MoS2 to form activated crystalline slabs8,12 .
Sulphidation practice varies, with completion at 300°C or 345°C or 400°C. Many reports state sulphiding is completed at 300°C. Others report further refinement and activity enhancement with annealing at 350 to 400°C. Most activation studies heat soak at final temperature, typically for two hours.
In commercial catalysts metals are well dispersed. This is an important feature because dispersion lowers the temperature of sulphidation reactions to as low as ambient from as high as 300°C on non-supported model substances5 . Additionally, the presence of cobalt promotor enhances sulphiding. Alumina substrate is also an active catalyst in tail gas system for hydrolysis reactions.
The chemical formula of molybdenum disulphide is MoS2 . The most stable crystalline form is 2H, a monolayer, with a hexagonal plane of S atoms on either side of a hexagonal plane of Mo atoms. Strong covalent bonds are between the Mo and S atoms, but weak van der Waals bonds hold layers together. Each molybdenum atom is bonded to six sulphur atoms (Mo-S CN = 6) and each sulphur atom is bonded to three molybdenum atoms.
Layers slide on each other with little friction, which is why MoS2 finds use as a lubricant. Layers can be mechanically separated to form 2-dimensional sheets of MoS2 .
Molybdenum disulphide belongs to a class of materials called ‘transition metal dichalcogenides’. Transition metal atoms are groups 4-12 in the periodic table and a chalcogen is group 16. Applications include catalysis, solid state lubricants, semiconductor/electronics, hydrogen-evolving reactions, batteries, photocatalysts, and a growing list.
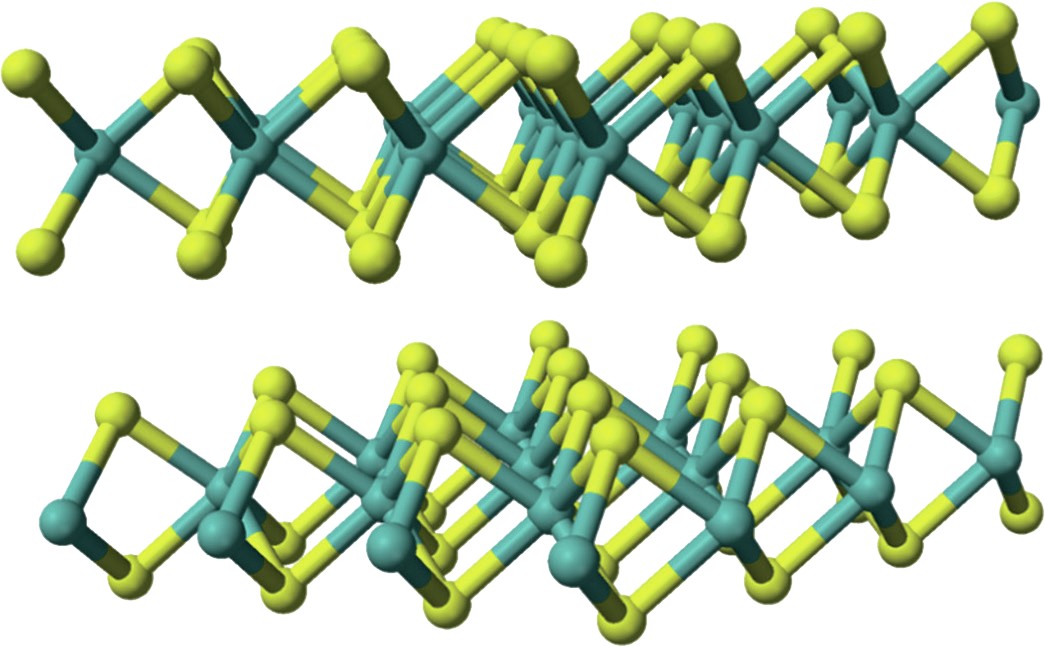
Pressures and composition
Partial pressure of the reactants H2 S and H2 is set by concentration and total pressure. Most published studies are at pressures of 1 to 20 bar and 5–15% H2 S in hydrogen. Sulphidation reactions proceed readily at lower temperatures when conducted at higher pressures. For low pressure conditions there are a few HER studies8 . The 2019 tail gas low temperature activation study was at 2.5 to 10% H2 at 3.5% H2 S and 5% H2 S in H2 at 1 atm. HDS gas activation conditions may be as high as 20 to 30 bar of hydrogen with 1 to 3% H2 S whereas tail gas pressure is 1 atm with 1-4% H2 S and 2-8 % H2 .
Sulphidation reaction rates are in proportion to hydrogen sulphide partial pressure and metal surface area. Whereas high H2 S partial pressure increases reaction rates, a greater concern is very low H2 S partial pressures. At very low H2 S concentrations, hydrogen can reduce cobalt oxide to metal, especially at elevated temperatures17 .
Hydrogen partial pressure impacts reaction rates. With chemisorption and dissociation the high pressure impact is muted (reaction rate α square root pressure) but over a range of 1000-fold partial pressure its effects are still significant. Low hydrogen concentrations, less effective at reducing molybdenum, hinders the proper sulphidation of the catalyst; formation of metal sulphides, essential for catalytic activity, is incomplete.
The role of hydrogen is important in several intermediate reactions and influenced by its partial pressure. An important step in completing sulphidation is reducing S2 2ligands (oxy sulphides and S2 2bridging ligands form at lower temperatures) and hydrogen is an important driving force for this reaction, which begins above 200°C, developing the MoS2 matrix and may continue into the 240 to 260°C transition4,5,7 . Atomic hydrogen is thought to reduce MoO3 to MoO2 . If MoS3 is present hydrogen helps reduce it to MoS2 below the thermal decomposition temperature of 315°C. Hydrogen readily adsorbs onto terminal sulphur so oxy-sulphides are a catalyst for dissociation of molecular hydrogen.
Low pressure activation may also push the transition temperature higher and may reduce rate of growth of slab structures. Hydrogen is crucial to development MoS2 crystals. HER studies on hydrogen effect on amorphous MoS2 transition to crystal identify hydrogen presence reduces activation energy (1.6 eV vs 3.5 eV). Bulk nucleation and crystallisation were noted in 0.005 atm H2 at 300°C, whereas no crystallisation occurred absent hydrogen at 300°C in one hour8 .
Water
Water dampens thermal response, being adsorbed or desorbed on the alumina. Heat of chemisorption used is 50 kJ/mol. Energy to desorb 0.01 wt fraction from one kilogram catalyst is 28 kJ, about 10% of the energy of activation. At 10% v water in gas at 1 atm and 200°C, equilibrium water on alumina is 0.0126 wt fraction. This effect is more pronounced at higher relative humidity, e.g., lower temperature and higher water concentration.
Water is the product of reduction and sulphidation reactions. Equilibrium for gas–solid reactions is established by product/reactant ratios of the gaseous species, so water vapour exerts a back pressure for weaker reactions. Water inhibits the reduction of molybdenum oxide or cobalt oxide or moly oxy-sulphide by hydrogen. Elevated water concentrations reduce the grain size of MoO2 .
MoO3 and MoO2 are hydrophobic in contrast to most metal oxides and less affected by water. The amorphous MoO2 may have affinity for water on exposed metal atoms and increase the number of oxygen vacancies, which would reduce the rate of sulphur uptake. The impact of water on oxy sulphides is unknown, but hydrogen bonding on terminal oxygen could diminish hydrogen dissociation.
Heat effects
The reaction sequence outlined and the physical features of oxide crystals offer an explanation for observed sulphiding reaction behaviour: early vigour and strong response to temperature which moderates after initial sulphiding. Once about one-third of sulphur uptake is reached, the thermal response is muted even as temperatures are raised above 240°C.
A mechanism of molybdenum–oxygensulphur ring-structure activation complexes supports the stepwise oxygen replacement by sulphur and conversion of MoO3 which progresses through oxy-sulphide intermediates15 . The calculated enthalpy by density functional theory (DFT) for these intermediates suggest an even distribution of the “overall” heat of reaction energy among sulphur addition steps16 . With successive activation barriers and smaller Gibbs energy functions the Kp are smaller ~ 10 – 1000 vs 106 overall, and the main driving force for the slower reactions as H2 S partial pressure (and H2 S: H2 O ratio).
It is known that initial sulphiding reactions express strong exotherms. Clearly the initial sulphiding step has a higher proportion of heat of reaction or a low activation energy for a stronger kinetic activity coefficient. Intermediates, such as oxy sulphides or reduction reactions must proceed slowly and require higher temperature, suggesting higher activation energies. The characterisations of thermochemical properties for reaction intermediates though DFT calculations is an area of developing research which will help better understand the sulphidation process.
Heat of reaction goes in part to heat the catalyst and in part to heat the sulphiding gas flowing through the bed. With gradual heat release steps, a greater portion of the energy is carried with the gas, and with higher gas rates more heat is carried with the gas and temperature rise is smaller.
Heat of reaction is from published thermodynamic data bases. Enthalpy of formation for MoS2 now taken as -230 kJ/ mol (NBS, AIP) vs previously used value of -276 kJ/mol NIST/JANAF. The molybdenum disulphide heat of formation is less negative and the corresponding expected heat effects are smaller – reduced from previously published values. Enthalpy of formation for MoS2 now taken as -230 kJ/ mol (NBS, AIP) vs previously used value of -276 kJ/mol NIST/JANAF.
The overall heat of reaction for the activation of MoO3 is taken as 174.86 kJ/mol in this work. Additionally, the published heats of formation are for crystalline solids, meaning there needs to be apportioning of the heat of reaction related to activation to crystallisation transformation as well.
Heat of reaction goes in part to heat the catalyst and in part to heat the sulphiding gas flowing through the bed. Gas flow can preheat the lower bed but with gradual heat ramp steps a greater portion of the energy is carried out of the bed with the gas and bed temperatures are lower. With higher gas rates more heat is carried with the gas and temperature rise is smaller.
Laboratory and research activations are usually temperature controlled. In situ field activation is adiabatic. Although the exothermal response of sulphiding is not a major consideration for laboratory work, the exotherms of field activation must be addressed and controlled.
Time and temperature
Time and temperature dependencies have not been well defined for transformation since many published studies are conducted to 300 to 350°C or higher. For activation at low temperature this blind spot is rather critical. Activation at lower temperatures prolongs the reduction and sulphidation process. The lower thermal energy available at these temperatures slows kinetics; longer exposure times may help reduction and sulphiding of metal oxides, but may not be sufficient to ensure full activation. This extended duration might lead to the adverse outcome of less transformation, increased MoS2 stacking, and more cobalt in the inactive Co9 S8 motif, further affecting catalyst efficiency.
The time period for many these referenced studies was two to three hours. Where data are available on metals composition and spectrograph at various temperatures from 220 to 280°C, they clearly support that at fixed exposure times higher temperatures advance sulphidation and crystallisation7,8,14 . General tail gas studies have historically applied “full” activation at 300°C for three hours. The 2019 study at lower temperatures extended times up to 18 hours, with improved activation at extended times, but not realising full activation potential9 . Field practices are typically 8 to 12 hours including a heat soak.
A more strongly calcined catalyst has a greater number of strong interactions between substrate and metal, forming CoAl2 O4 (spinel) or Al2 (MoO4 )3 . Metal-substrate bonds must be overcome in order to form sulphide, requiring substantial activation energy; this requires higher temperatures and higher H2 S or H2 partial pressure. Many of these metal-substrate bonded metals are not sulphided by TGU procedures, as they require temperatures in the 600 to 1,000°C range18 . Generally, a higher fraction of cobalt interacts with substrate, but as much as 20% of molybdenum may be bound in this way and unavailable for catalysis1,5.
Accomplishing the transformation step, crystallisation, by heating may seem counterintuitive; however sulphiding conditions are well below melting point so amorphous MoS2 is figuratively frozen. Annealing generally heats to just below melting point – or a point of atomic mobility, holds and cools.
Annealing occurs by the diffusion of atoms within a solid material, so that the material progresses towards its equilibrium state. Heat increases the rate of diffusion by providing the energy needed to break bonds. The movement of atoms has the effect of redistributing and eradicating irregularities and defects. THe melting point of MoS2 is 2883 K (JANAF) or 2375°C (NIH/ NBS). The onset of mobility of atoms in a solid is generally taken as Hüttig temperature, melting point/3. For MoS2 this would be 610 to 688°C, normally the minimum for a reforming process such as annealing. American Chemical Society suggests MoS2 sublimes at 435°C, indicating a somewhat earlier onset of atomic mobility.
Many literature references discuss annealing at temperatures in the range of 400 to 800°C and some specific studies report defect reduction/property improvement from 2H MoS2 as low as 300°C. Overall, it is indeed extraordinary and fortunate that crystallisation will occur in the 260 to 315°C temperature range.
For activation of low temperature catalysts at 260°C and below the process must be assessed in the lab and by field trial. This will hopefully be reported in the near future. Modelling can address managing exotherms and the degree to which catalyst bed temperatures can be raised safely. The question is how much benefit to activation can be obtained by prolonging elevated bed temperatures.
References