Sulphur 410 Jan-Feb 2024
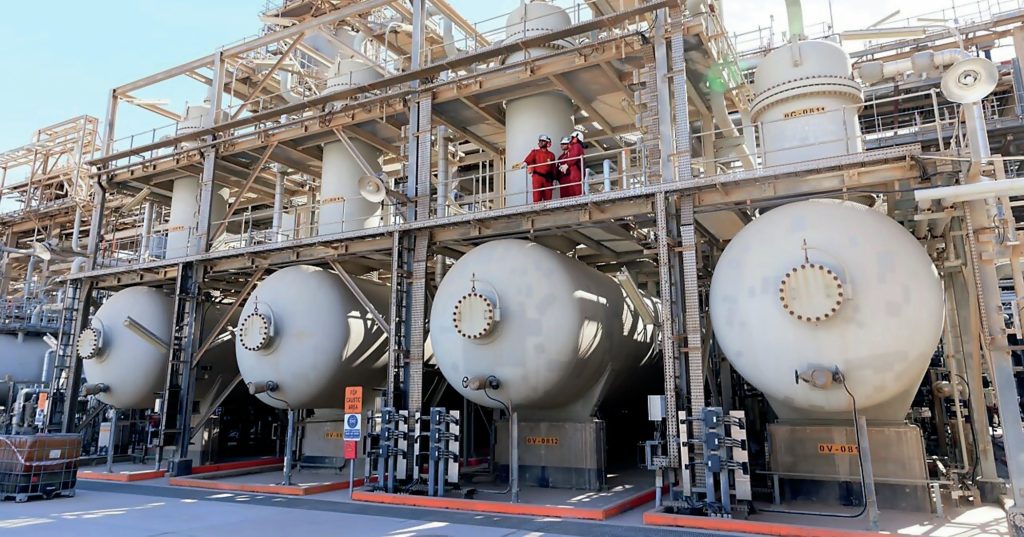
31 January 2024
Small-scale sulphur recovery
SULPHUR RECOVERY
Small-scale sulphur recovery
Small quantities of sulphur in a refinery or gas feed can present challenges for conventional large scale sulphur recovery techniques.
Around 40% of the world’s natural gas reserves contain enough hydrogen sulphide to be classified as sour. However, the percentage of H2 S can vary widely, from as high as 90% in some fields, to the limits of what can be defined as sour (around 4ppm). Likewise refinery streams can vary significantly according to the sulphur content of the feed. Biological sources often have a small amount of sulphur, for example in refineries producing renewable diesel and jet fuel from sources such as used cooking oils, waste animal fats or vegetable oils such as rapeseed. Units processing gas from biological sources may also deal with smaller sulphur quantities in process streams.
Extraction of the H2 S is usually achieved using a regenerative solvent, which extracts CO2 as well as H2 S to produce acid gas. But where small volumes of H2 S are present the acid-gas stream may consist mainly of CO2 . Claus plants are generally set up to process significant quantities of sulphur in a feed, but can struggle where levels of H2 S are low and/or volumes of gas being processed are small. In the past low levels of hydrogen sulphide were sometimes flared, but in e.g. the US, regulations prevent the flaring of gas with more than 230 mg/m3 of H2 S (approx. 350 ppm). If conventional Claus processing is not suitable, a variety of techniques can be used to treat smaller quantities of sulphur, either removing or recovering it, depending upon the situation.
Scavengers
Where there are very low levels of sulphur in the gas stream (<0.1 t/d), such as in sewage plants, or lone gas wells where flaring is not possible, scavenger systems are typically used which bind the H2 S either chemically or physically. There are dry scavengers and wet scavengers. The smallest scale removal systems typically use solid-based (‘dry’) scavengers. Iron oxide is a common scavenger, reacting to form iron sulphide and water. The iron sulphide can then be disposed of in landfill without requiring special permits. However, the system can be capital and labour intensive for larger volumes.
Regenerative solid beds using zeolites can be used, using adsorption to take the H2 S from the system, but generating an H2 S-rich gas stream as the adsorber is regenerated. Large vessel size, limited capacity, and the need for parallel trains for regeneration during service can increase capex and space requirements. Additionally, dealing with sulphur waste creates potential issues for both operations handling and OPEX considerations.
There are also a wide variety of liquid scavengers, soluble in variously water, oil or organic solvents, including copper carbonate, zinc oxide, hydrogen peroxide, triazine, sodium nitrite, chlorine dioxide, sodium chlorite, etc etc. These products depend on the type and composition of the scavenger and the conditions at which the reaction takes place. Like solid scavengers, liquid scavengers can be divided into regenerative and non-regenerative types. Non-regenerative scavengers include aldehydes such as formaldehyde, although safety and handling issues generally militate against their use. The most commonly used non-regenerative liquid H2 S scavenger used is triazine. However, while the reaction byproducts are biodegradable, unreacted triazine is highly toxic to aquatic life and treatment of the waste stream is required. Nitrate/nitrite solutions have similar removal capacity compared to triazine, though they can produce nitrogen oxides, nitric acid, and insoluble precipitates from reacting with H2 S.
Caustic scrubbing
A special case of liquid scavenger is caustic scrubbing systems. These use a caustic stream, usually containing a solution of sodium hydroxide, to react with the hydrogen sulphide. Caustic scrubbing is typically employed where the amount of sulphur to be removed is less than 10 t/d. The type of scrubber used depends upon the CO2 content of the gas to be treated. Where CO2 levels are low, the gas can be processed through a recirculating caustic solution. However, CO2 can react with the solution leading to high rates of consumption and sodium carbonate precipitation, and specialised designs are required for higher CO2 streams which allow preferential reaction of the H2 S. The product of the scrubber is a mix of sodium sulphide (Na2 S) and sodium bisulphide (NaHS), depending on the ratio of H2 S to caustic in the solution, which can be sold depending on the proportion of sodium carbonate in the mix from CO2 in the gas stream.
Liquid redox
Liquid reduction-oxidation (redox) systems are in effect a regenerative scavenger. Redox systems usually use iron and chelating agents for the reaction. Sour gas passes through an absorber column where the H2 S is stripped from the gas. This spent solution is sent to an oxidizer unit to regenerate. The iron is initially reduced from ferric (Fe3+ ) state to ferrous (Fe2+ ) by the H2 S, then oxidised back to iron-(iii) in the oxidiser unit. The oxidation process produces a H2 S-rich waste gas stream, but can also result in elemental sulphur production due to the reactivity of the oxidising agents. This process can be used to remove less then 20 t/d of H2 S, or where complete stripping of sulphur is required.
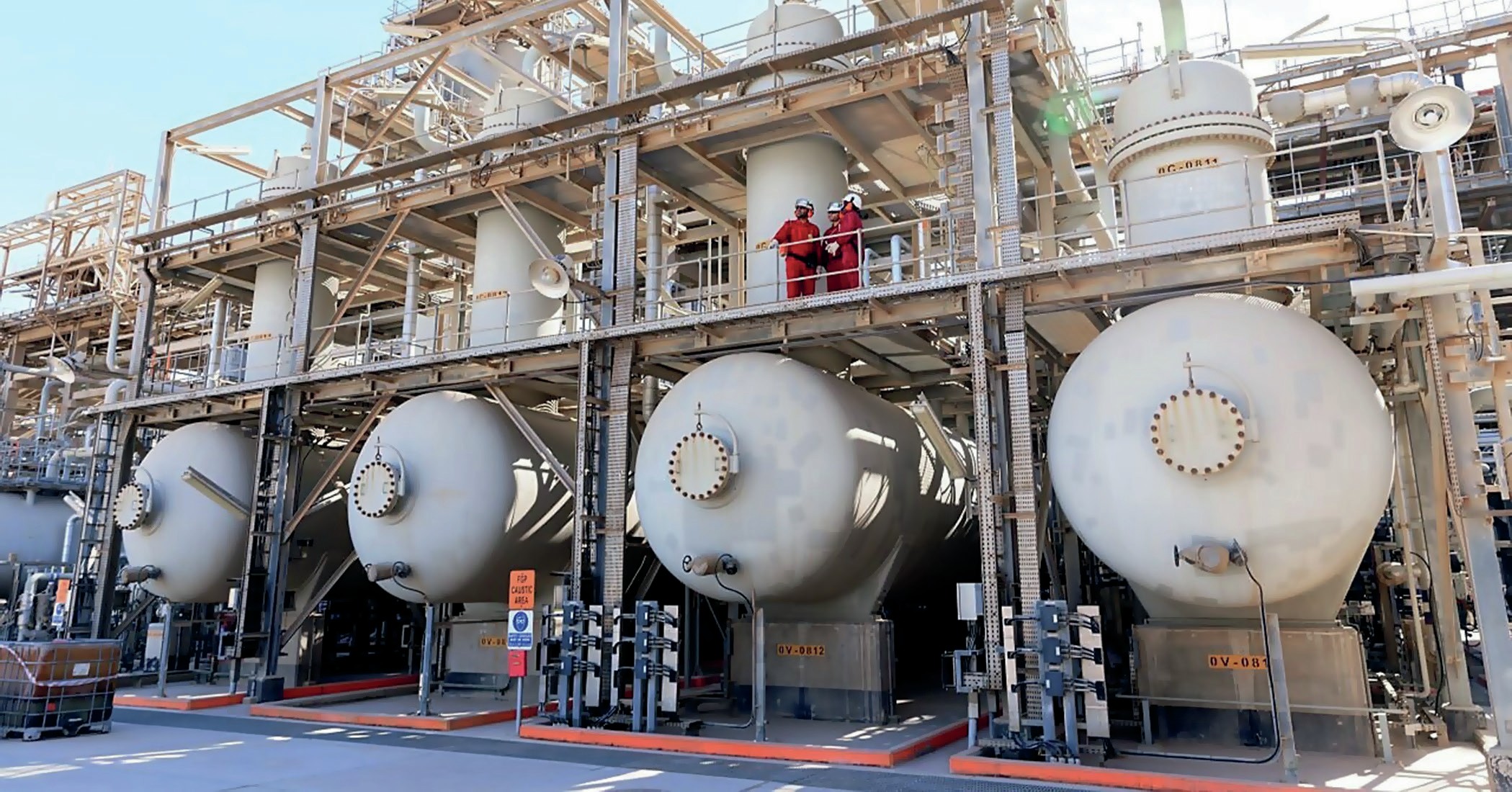
Merichem offers the LO-CAT process, a proprietary liquid redox process that converts H2 S to solid elemental sulphur. The process uses an aqueous solution of iron, whose catalytic performance is enhanced by a proprietary blend of chemicals. Direct treatment of a sour gas stream uses a separate absorber and oxidizer. This configuration is a lot like an amine unit – a closed-loop circulating solution – but in lieu of steam for regeneration, the LO-CAT process uses air to oxidise the iron catalyst back to Fe3+ . When hydrocarbons are not present in the vapor stream an autocirculation unit can be used that combines the absorber and oxidiser into a single vessel and eliminates pumping of the working solution. The process produces a sulphur cake that is mostly solid sulphur, but also contains some moisture and proprietary chemicals and may not be suitable for all end users.
Shell offers the SulFerox process, similar to LO-CAT but using a different chelating agent. Various contactor types are available, such as sparged towers, spray towers and pipeline contactors. After contacting the sour gas and solution in the contactor, the gas/liquid mixture is separated, yielding treated sweet gas and the depleted SulFerox solution. After optional degassing, the reduced iron chelate solution is regenerated via reaction of Fe2+ back to Fe3+ with oxygen from an air source in the regenerator vessel. The sulphur product can be obtained as a filter cake as per LO-CAT or alternatively as molten sulphur.
Biological processes
Biological processes selectively remove H2 S by using it in bacterial respiration, converting it to mercaptans or elemental sulphur and sulphate. The operating temperature range is very limited due to the biological nature of the process. Shell markets its Thiopaq system, originally developed by Paques BV for the treatment of biogas, which is produced by the anaerobic digestion of wastewater. Co-operation with Shell led to further development of the process for application at high pressure in oil and gas environments. Shell says that it can be economically applied to projects recovering up to 150 t/d of sulphur. For the natural gas and petrochemical environments, the process is licensed by Paqell BV, a joint-venture company of Shell Global Solutions International BV and Paques BV.
Low capacity Claus
Below about 20% H2 S in the acid gas feed to a Claus the flame in the reaction furnace becomes unstable. In such cases, the acid gas and air can be preheated before mixing in the front-end burner. Maintaining a proper feed temperature is crucial for operation of the Claus and tail gas reactors, and this is another area where alternatives are available for small processors. Large facilities use steam or hot oil when available, but these can be expensive options for small processors, requiring additional infrastructure and operations. For smaller units, however, an electric reheater may be applied to perform this task. These reheaters are effective, inexpensive to install and simple to control.
However, when the acid-gas stream contains less than 10% H2 S, it may be too difficult to achieve the necessary recovery efficiency. In such a situation, the acid-gas stream can be treated in an additional sweetening step with a solvent that preferentially absorbs the H2 S and leaves most of the CO2 behind. After solvent regeneration, the acid gas feed to the Claus plant is sufficiently enriched in H2 S content. So-called acid gas enrichment can bring H2 S concentrations up from around 1% to 25%, allowing normal Claus operation. Care must be taken to avoid contamination of the enrichment solution, however. If hydrocarbons, amine, or corrosion inhibitors enter the solution, the performance of the solvent will suffer and require potentially expensive replacement.
Selectox
A derivative of the Claus process is the Selectox process, developed by Parsons and Unocal and licensed through UOP. Once-through Selectox is suitable for lean acid gas streams (1-5% hydrogen sulphide), which cannot be effectively processed in a Claus unit. The process is similar to a standard Claus plant, except that the thermal combustor and waste heat boiler are replaced with a catalytic reactor. The Selectox catalyst promotes the selective oxidation of hydrogen sulphide to sulphur dioxide, i.e., hydrocarbons in the feed are not oxidised. These plants typically employ two Claus catalytic stages downstream of the Selectox reactor, to achieve an overall sulphur recovery of 90-95%.
For feeds greater than 5% hydrogen sulphide, the Recycle Selectox process can be used. In this variation a portion of the process gas leaving the condenser downstream of the Selectox reactor is recycled so as to limit the outlet gas temperature from the reactor to >205°C. Selectox produces a conventional 99.9% pure sulphur product.