Sulphur 411 Mar-Apr 2024
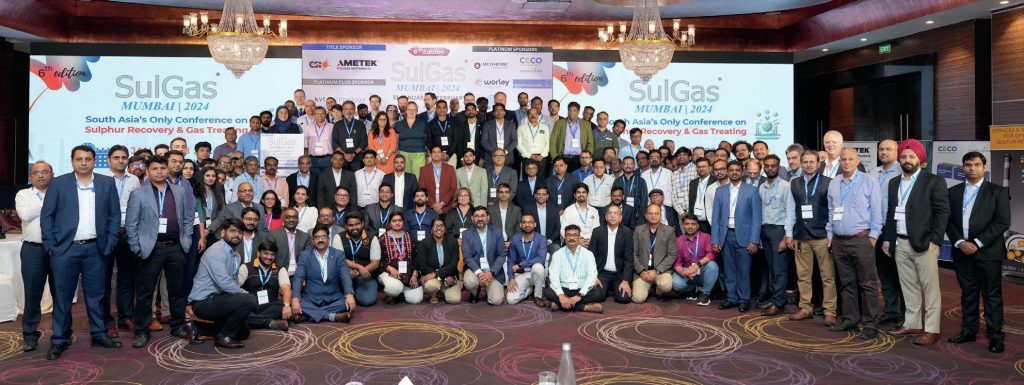
31 March 2024
SulGas Mumbai 2024
CONFERENCE REPORT
SulGas Mumbai 2024
More than 155 attendees, representing more than 68 companies gathered in Mumbai, India, from January 31 to February 2, 2024 for the annual SulGas® conference, organised by Three Ten Initiative Technologies LLP. We report on the key highlights of the event.
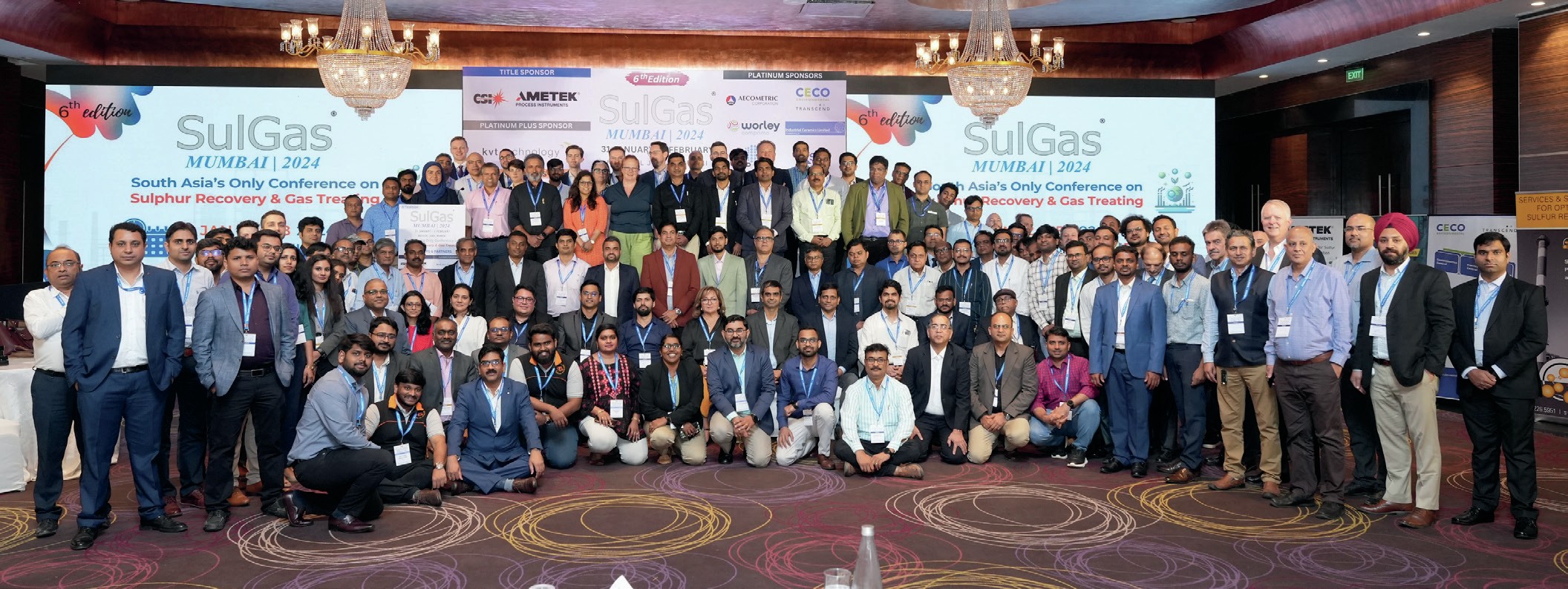
SulGas Mumbai 2024, now in its sixth year, took place over three days from January 31 to February 2 at Novotel Juhu Mumbai. The event brought together public sector oil companies, private refiners, petrochemical, chemical and fertilizer plants, licensors, engineering companies, solvent and column equipment manufacturers as well as control and instrumentation companies. Notable end users including BPCL, ExxonMobil, HMEL, HPCL, IOCL, MRPL, Nayara, Petronas and RIL were among the participants.
The conference featured 33 speakers in interactive technical sessions, with panel discussions at the end of each session and open Q&A, fostering maximum technical exchange among participants. A dedicated exhibition area with full-day access for all delegates ran alongside the conference.
The opening keynote speaker was Mr. S. Bharathan, Director (Refineries) of HPCL, who set the tone for the conference, discussing how sulphur recovery units are indispensable, how challenges can be addressed through innovations, the importance of collaboration for sustainable practices and the commitment to a greener tomorrow.
The conference agenda comprised ten sessions that covered a broad range of topics including: decarbonisation and carbon capture, enhancing SRU capacity and recovery, advances in SRU instrumentation, simulation and control, SRU waste heat boilers, gas processing, operational challenges with SRUs, emissions reduction and decarbonisation, and tail gas treating.
Some of the main topics of the conference are highlighted below.
Decarbonisation and carbon capture
WSA technology for the Indian market
India is a country that depends on imports of crude oil and gas, as well as sulphur and sulphuric acid, which are essential for various industries. Therefore, energy efficiency and product margins are crucial factors for choosing a sulphur recovery solution. Igor Kostromin of Topsoe showed how the WSA technology could replace the conventional SRU and produce sulphuric acid directly from sulphurous gases, without the need for sulphur burning. To meet the strict environmental standards and to maximise the profitability of sulphur recovery, one of the leading refineries in India has opted for Topsoe WSA technology. The plant produces commercial-grade sulphuric acid, which is sold to the domestic or international market. It also generates superheated steam, which is used for power generation or process heating. By using the WSA plant, the refinery significantly reduces its carbon footprint.
Processing ammonia-rich refinery sour gases
Saptarshi Pual of Engineers India Limited discussed the need to explore alternatives for processing of ammonia-rich sour gas streams in refineries as well as gas processing complexes.
Co-processing of theses streams with the H2 S-rich stream for NH3 destruction in the main burner of SRU often causes severe operational issues, while processing via the incinerator (i.e. Claus section bypass) is associated with high capex, and sometimes may lead to high NOx generation/environmental issues. The destruction of ammonia via these routes in Indian refineries is typically in the region of 41,891 t/a, at a time when ammonia demand in India is increasing every year.
In order to overcome the challenges of processing ammonia-rich refinery sour gases and to convert them into a revenue generating stream, EIL has developed and patented ammonia recovery technology to recover ammonia from NH3 -rich sour gases and convert it into valuable products like anhydrous ammonia or aqueous ammonia. The overall recovery of ammonia is >99% and meets the required product specifications: BIS: 662-1980 for anhydrous ammonia and BIS: 799-1985 for aqueous ammonia, using an approach that helps towards minimising carbon footprint.
Energy optimisation in amine sweetening units
Energy optimisation is a critical concern in the oil and gas industry because it directly impacts operational efficiency, cost effectiveness, and environmental sustainability. One area in which significant energy savings can be achieved is the amine sweetening process used to remove acidic gases such as carbon dioxide (CO2 ) and hydrogen sulphide (H2 S) from sour natural gas. Aparnu Saiju of SLB Oilfield Services Company explored the concept of energy optimisation using power recovery turbine (PRT) technology in amine sweetening units, focusing on its potential benefits, implementation strategies, and environmental implications.
The PRT is designed to capture energy that would otherwise be released during pressure reductions and convert it into useful mechanical energy. This recovered energy can be used to reduce the power consumption of various equipment within the unit, such as pumps and compressors, thereby enhancing overall process efficiency. Because the energy produced using PRTs can be used to reduce the power consumption, the PRTs can be instrumental in reducing Scope 2 emissions and help contribute to the industry’s sustainability goals. The decreased use of energy generated from fossil fuels reduces the emission of greenhouse gases such as CO2 .
Enhancing SRU capacity and recovery
Employing effective oxygen enrichment
Sulphur recovery units across the globe need to upgrade to meet new demands for the future. The most common requirement is to process higher sulphur loads as refineries across the globe are processing crudes with higher sulphur content and are also implementing residue conversion projects. Other adaptations are frequently required for processing more challenging feed ‘cocktails’ which may be encountered as there may be a requirement to process lean acid gas streams. Jyoti Bist of Fluor Daniel India Pvt discussed the merits of oxygen enrichment to manage multiple revamp requirements in SRUs, both for capacity enhancements as well as to deal with very lean acid gas streams, as a more efficient and cheaper option to refiners than building a new plant.
Novel case study combining oxygen enrichment and SO2 recovery
Continuing with the theme of maximising sulphur capacity, Kausik Mazumder of Engineers India Ltd presented case studies carried out on a Claus-based sulphur recovery unit (SRU) to enhance its capacity by up to 76% and improve sulphur recovery from 99.2% to 99.9%. A hybridised process was used, which utilises oxygen enrichment to increase capacity while effectively managing the main combustion chamber temperature and SO2 emissions through the incorporation of the SO2 recycle process.
In addition to recovering SO2 from the incinerator flue gas, the SO2 recycle process demonstrates the capability to recover and recycle SO2 from various other flue gases within refineries. Redirecting this reclaimed SO2 to the SRU can significantly reduce overall sulphur emissions from refineries. The findings of the study underscore the substantial potential of combining oxygen enrichment and SO2 recycle to not only enhance SRU capacity but also to improve overall unit operation and mitigate SO2 emissions.
Advances in SRU instrumentation, simulation and control
SRU control strategy
Compositional changes to the acid gas feed to the sulphur recover unit (SRU) cause trouble for plant control and can lead to higher SO2 emissions or down time for the SRU. There are two main control strategies employed: feedback control and feedback with feedforward control. A third less commonly used control strategy is dual air demand (DAD). Selwyn Pandian of Galvanic Applied Sciences discussed how DAD can be used to improve SRU performance and reduce SO2 emissions by deploying an H2 S and SO2 analyser after the first sulphur condenser. The ability to react to and correct for acid gas feed composition and flow upsets quickly reduces the risk of soot formation on the first catalyst bed and protects the tail gas treating unit from the effects of SRU excursions.
Kinetics-based sulphur plant models
SulphurPro® is a mass and heat transfer-based simulation software that employs a reaction kinetics approach to simulate the entire sulphur plant, from the reaction furnace to the stack. It relies on fundamental chemistry and detailed information on kinetic reaction mechanisms and heat transfer, providing a significant advantage over other simulation tools, and incorporates the latest sulphur research from organisations like Alberta Sulphur Research Limited (ASRL).
Dr Anand Govindarajan of Three Ten Initiative Technologies demonstrated four use cases where a kinetics-based model assisted plant operations in maintaining reliability and saving capital and operating expenses.
How to optimise SRU emissions during upset conditions
Modern process instrumentation has the potential to help reduce the emissions from a sulphur recovery unit, but the application challenges with regard to measurement reliability and safety aspects are high (the SRU has the most toxic gas mixtures of the entire refinery). In his presentation Jochen Geiger of Ametek Process Instruments stressed that knowledge, understanding, and awareness training are essential to maintain the instruments, and that without the instrument signals the emission targets are not achievable.
Auto loading scheme for air blowers
Nirmalya Nandi of Bharat Petroleum Corporation described an auto loading scheme that has been introduced for the main combustion chamber air blowers at BPCL Bina refinery. The new auto loading scheme uses the ADA signal and discharge pressure and has successfully overcome the problems that had been experienced with the manual loading scheme, which relied on operator judgement based on acid gas feed flow and reading of the air demand analyser as per design.
The Digital Process Monitor
The pursuit of operational excellence requires continuous process monitoring, together with qualified analysis of the collected data. Digital Process Monitor (DPM), a cloud-based solution co-developed by a series of companies within the Maire Group (Nextchem, Stamicarbon, Tecnimont, KT-Kinetics Technology) provides a process digital twin which consists of an accurate process plant model, which, by incorporating the licensor’s knowledge and expertise in sulphur recovery technology, can provide continuous insights into plant performance. Process data are captured from the plant to feed a digital replica of plant processes, unlocking operational excellence through increased productivity and energy savings with a consequent reduction in the plant’s carbon footprint.
Daniela Boni of NextChem provided an overview of the main features of the Digital Plant Monitor, focusing on the related benefits in terms of overall operational improvements and plant efficiency for the sulphur recovery unit.
Ammonia destruction in SRUs
A detailed reaction mechanism for predicting ammonia destruction in sulphur recovery units has been developed and validated by Indian Institute of Technology Delhi that effectively captures the combustion and pyrolysis chemistry of ammonia in the presence of several active species such as H2 S, CO2 , and hydrocarbons found in the feed stream to SRU. In his presentation, Dr Abhijeet Raj of IIT explained how the mechanism was then used to investigate the suitable process conditions that could lead to the destruction of ammonia in the thermal stage of the SRU. The results suggest that the detailed reaction mechanism proposed in the study can be used to optimise the furnace parameters to achieve the desired levels of ammonia destruction without significantly decreasing sulphur production and aggravating CO emissions from the SRU.
SRU Claus furnace and waste heat boilers
Anurag Kumar of Magnalore Refinery and Petrochemical Ltd shared the root cause analysis for a case study with multiple tube failures in an SRU waste heat boiler. This presentation was followed by another case study by Prasenjit Pal of Engineers India Ltd who reported on failures to Claus furnace refractory, brick lining, choke rings, thermowells, tubesheet and areas around nozzles. A root cause analysis of the failures was carried out addressing design, material selection and quality of workmanship during installation.
Gas processing
Amine foaming issues
Mohd Firdaus Sabturani drew upon PETRONAS’ extensive experience of operating amine-based acid gas removal units (AGRUs) in their LNG processing plant where foaming issues are commonly encountered. Severe foaming issues which cause loss of production or plant upset are typically handled via a root cause failure analysis (RCFA) approach whereby each RCFA session shall be carried out by the multi-disciplinary team of engineers including process technologist, operation, maintenance, inspection and reliability engineers.
PETRONAS has identified several common root causes and subsequently recommended the necessary operational and design improvements to address the identified root causes. These operational and design improvements have improved the performance of the amine treating units and reduced foaming issues significantly to achieve a stable AGRU operation.
Application of improved version of Thiopaq O&G
Recently, an improved version of the biological sulphur recovery process Thiopaq O&G (TOG) process has been developed: Thiopaq O&G Ultra (TOG Ultra). Like TOG, the TOG Ultra process is a biotechnological process, and uses naturally occurring bacteria to convert dissolved sulphide into elemental bio-sulphur.
Srinivas Vadlamani shared the results from the multi-year operation of a pilot plant of the TOG Ultra process, and the findings from the design and engineering phases of the implementation of the first full-scale plant. The TOG Ultra process achieves a 50% lower NaOH consumption and bleed stream formation, leading to a 25% decrease in opex compared to the TOG process. In addition to a strong reduction in opex, the TOG Ultra process has improved the acceptance of biological SRUs for larger sulphur loads.
Operational challenges with SRUs
SRU alarm management and operator training
Human errors are still one of the major causes for unit upsets and hazards. The Operator Training Simulator (OTS) provides a perfect platform to address this concern. Pranay Veer Singh of Fluor Daniel India Pvt provided an in-depth insight of the OTS and highlighted the inbuilt scenarios inside the model, the most important being the start-up, shut down and specific upset scenarios.
Alarm management provides further insights to operations personnel as to how to minimise errors resulting from delayed response to reaction to plausible alarms in an SRU. Alarm priority and ranking based upon the criticality of SRU plant operation cycle was also highlighted.
New SRU block at HPCL, Visakh Refinery
Part of the Visakh Refinery Modernization Project (VRMP), a new SRU block has been installed at the HPCL refinery, Visakhapatnam, India. Ellen Ticheler of Worley Comprimo discussed the different stages of the project from the engineering phase up to and including the start-up, and the various challenges encountered during the project.
Tail gas treating
TGTU operations
Akash Mendpara of Sulfur Recovery Engineering presented a concise yet thorough analysis of sulphur recovery in the oil and gas industry, emphasising the critical role of tail gas treating units (TGTUs). Critical cost drivers in a TGTU were discussed supported by real world case studies and simulation model data.
The research identifies natural gas consumption in thermal oxidisers of SRUs as a significant cost driver. Effective management of excess oxygen levels and temperature control in these oxidisers is crucial. This management is essential not only for reducing operational costs but also for minimising CO2 emissions, aligning with environmental compliance mandates and carbon tax regulations.
SO2 breakthrough in a tail gas unit
Ganesh Gujar of Bharat Petroleum Corporation discussed ways to prevent and mitigate SO2 breakthrough in a tail gas unit and presented a range of recommendations including having effective contaminant control in the amine and SWS systems providing feed to the SRU/TGTU, avoiding manual air control operations, making neutraliser injection an automated system triggered by a reliable pH meter, and installing a rapid purge for spent solution in the desuperheater sections of two stage quench towers that use pre-loaded caustic.
The seventh edition of the SulGas conference is scheduled to take place in Mumbai from February 5 to 7, 2025.