Fertilizer International 519 Mar-Apr 2024
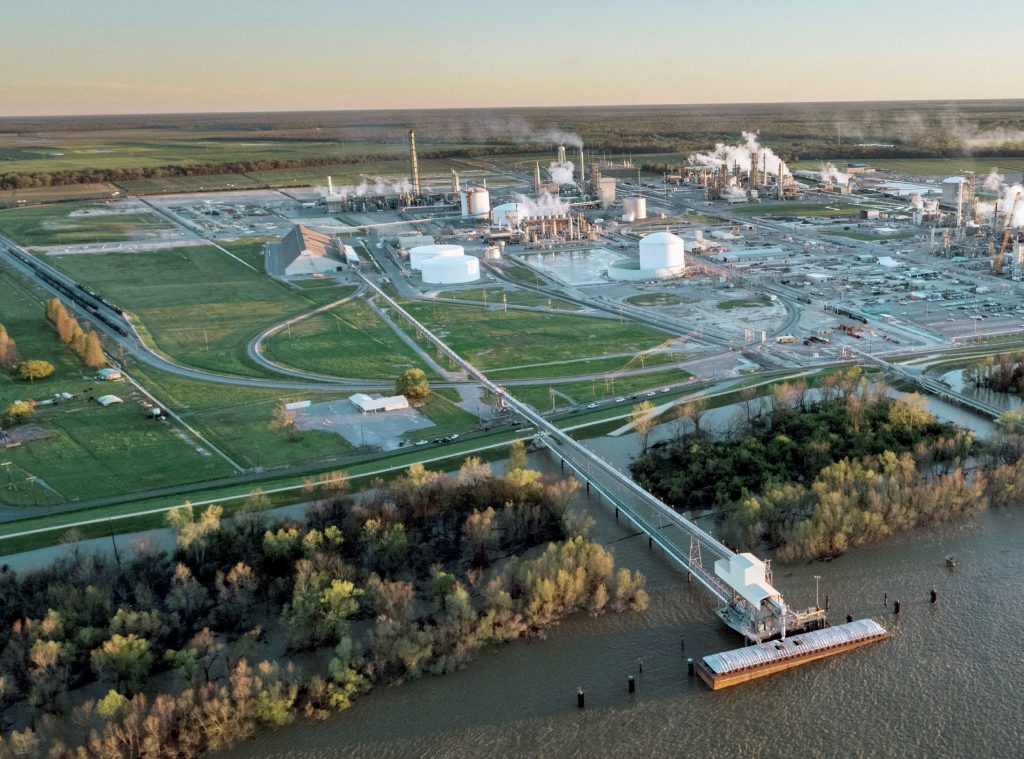
31 March 2024
Worldwide trends in urea process technologies
FERTILIZER PRODUCTION
Worldwide trends in urea process technologies
Mark Brouwer and Jo Eijkenboom of ureaknowhow.com examine the major shifts in global urea production. They also discuss the future of the urea industry and, in particular, how the sector is being affected by the increasing focus on low-carbon ammonia production.
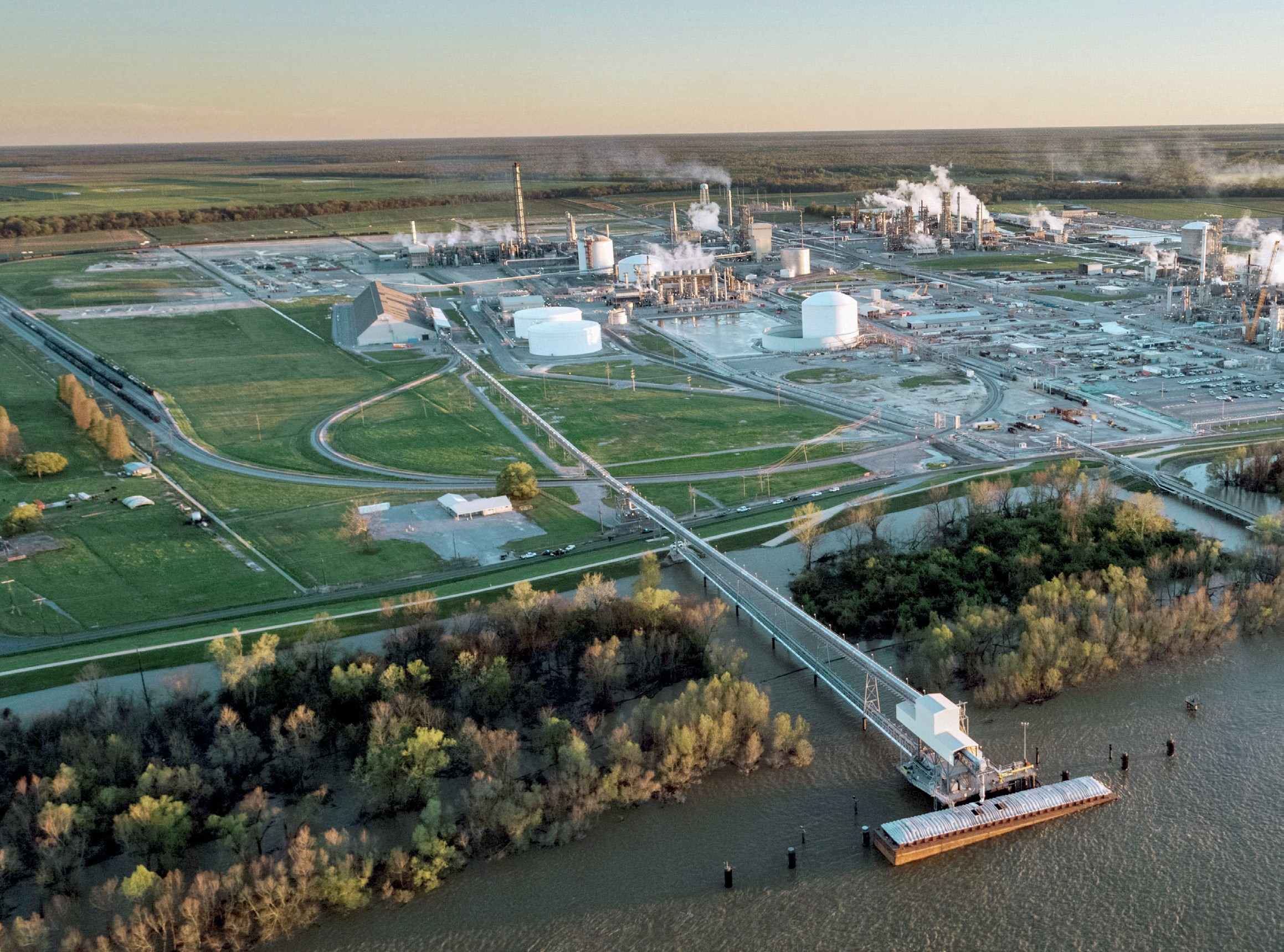
Introduction
Urea production on an industrial scale can trace its origins back to the first half of the 20th Century. Because it is a mature technology, plant operators typically have high expectations when it comes to the performance of modern plants and urea process design. To meet those expectations, technology licensors generally need to offer a urea process concept that combines: high feedstock conversion, low energy consumption, low environmental footprint, low initial investment, high operating reliability and high product quality.
In this article, we examine the market share of the main global urea process licensors (Stamicarbon, Saipem, TEC, Casale, NIIC and Chinese design institutes) over the last three decades, and predict how their market share is likely to change in the near future.
Worldwide trends in urea process technologies are also summarised – including recent Chinese innovations.
Finally, the future of the urea industry is discussed, at a time when low low-carbon ammonia generation is becoming an investment and sustainability priority.
The article reviews and updates our original International Fertiliser Society paper with the same title published nearly a decade ago in 20152 .
Urea process technologies
The popularity of the different urea process technologies offered by the four major urea licensors over the last 30 years is illustrated by Figure 1. This shows the number of urea plants (177 in total globally, excluding China) constructed annually using Casale, NIIK, Saipem, Stamicarbon and TEC process technologies between 1993 and 2023.
All of the urea plants constructed over this period, with the exception of one NIIC reference, are based on either CO2 or NH3 stripping technology. The urea plant breakdown by technology licensor is as follows:
- 42 percent Stamicarbon
- 37 percent Saipem
- 16 percent TEC
- 3 percent Casale
- 1 percent NIIC.
These percentages are based on the number of urea production lines.
From Figure 1, it is apparent that Casale, NIIC and TEC have all improved their market share in recent decades – a trend of growing popularity that is set to continue in our view.
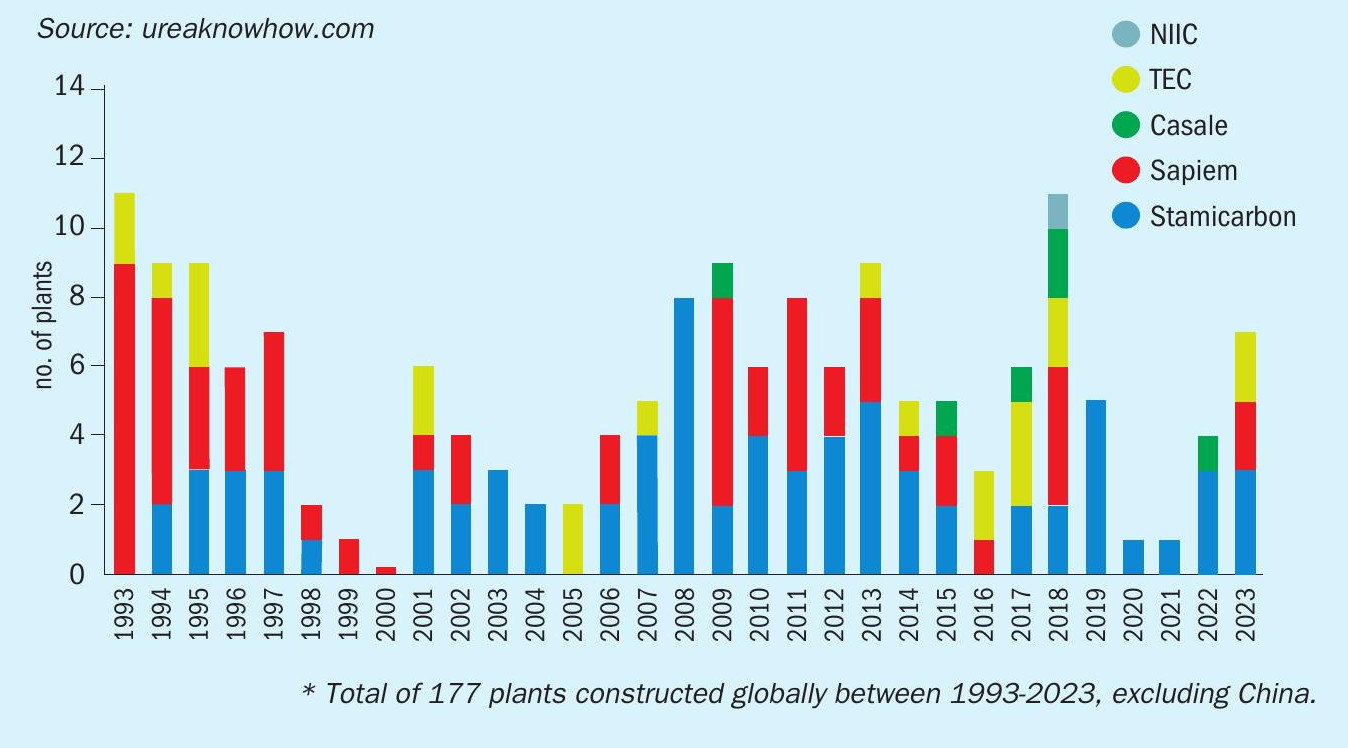
NIIC’s market share is likely to grow due to the geopolitical situation affecting its home market in Russia and the growth in domestic demand for urea.
TEC and Casale, meanwhile, are benefitting from the introduction to the market of their innovative ACES21-LP (Low Pressure) process and Green Granulation technology (Fertilizer international 517, p36), respectively. Casale has also expanded its technological portfolio to cover almost every nitrogen fertilizer production process.
In future, we predict that the relative market shares of the two dominant urea licensors, Stamicarbon and Saipem, will remain at a similar ratio in the near term, while TEC, Casale, NIIC and the Chinese design institutes will all grow their market shares.
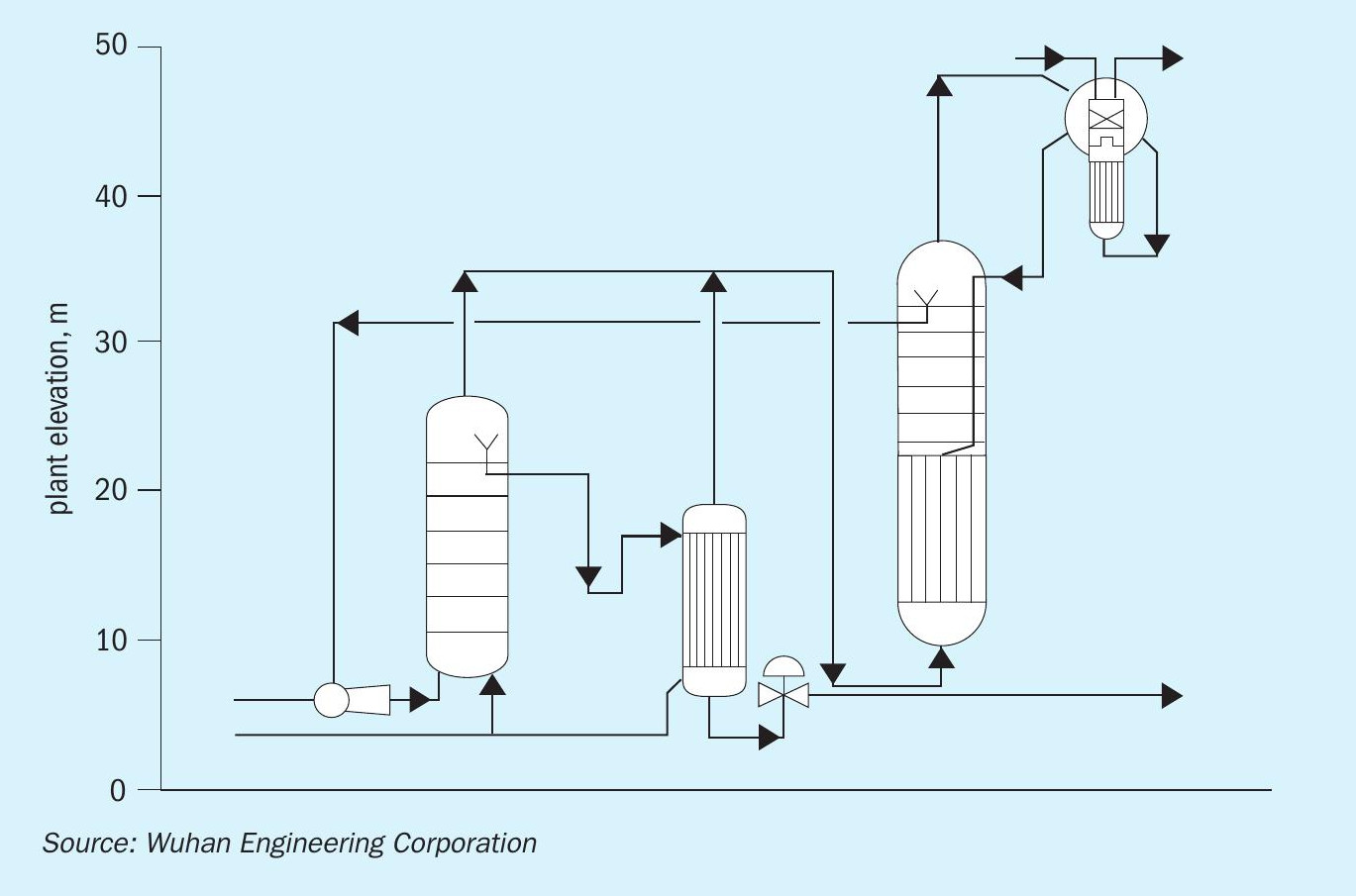
Chinese innovation
Historically, Chinese CO2 stripping plants have typically been based on a falling film, high-pressure carbamate condenser design. Domestic Chinese companies can engineer, procure and construct these ‘Stamicarbontype’ plants at a very competitive cost. Indeed, Chinese CO2 stripping plants can be built for 25 percent of the investment cost of similar plants in other parts of the world, according to some estimates1 .
Nowadays, China is also increasingly active in developing its own proprietary technologies. The ‘Technology of High Efficiency Synthesis and Energy Saving’ (THESES) process developed by the Wuhan Engineering Corporation is one example of the country’s urea process innovation1 . The synthesis section of THESES plants combines a vertical submerged condenser and reactor with a low-elevation layout using a high-pressure ejector (Figure 2). The technology has been demonstrated since January 2014 by the operation of the 500 tonnes per day (t/d) urea plant at Meifeng, Sichuan.
Another example of Chinese process innovation is the JX Urea Technology developed by Chengdu-based company JX. This new technology reduces the steam, cooling water and power consumption of conventional ‘total recycle’ urea plants. The energy consumption of JX Urea Technology is comparable to urea stripping technologies yet can be delivered at a substantially lower investment cost. This technology has been proven by the operation of a 1,000 t/d capacity plant since January 2009. There are also plant references at 1,500 and 2,000 t/d capacity.
Worldwide trends in urea process technologies
Globally, the main trends in urea production plants and technology include:
- Ever larger plant capacities
- Higher safety and reliability standards
- Lower energy consumption figures
- Lower emissions
- Submerged condensation in the synthesis section
- The use of high alloy construction materials
- Product innovation.
These trends are discussed below.
Ever larger plant capacities
The production capacities of urea plants have been on the increase since the mid-1950s, a long-term trend driven by economies of scale, cost reductions and innovations in process technology, materials and plant design. Mega urea plants – defined here as those of 3,000+ t/d capacity – have become increasingly popular since their emergence in the late 1990s.
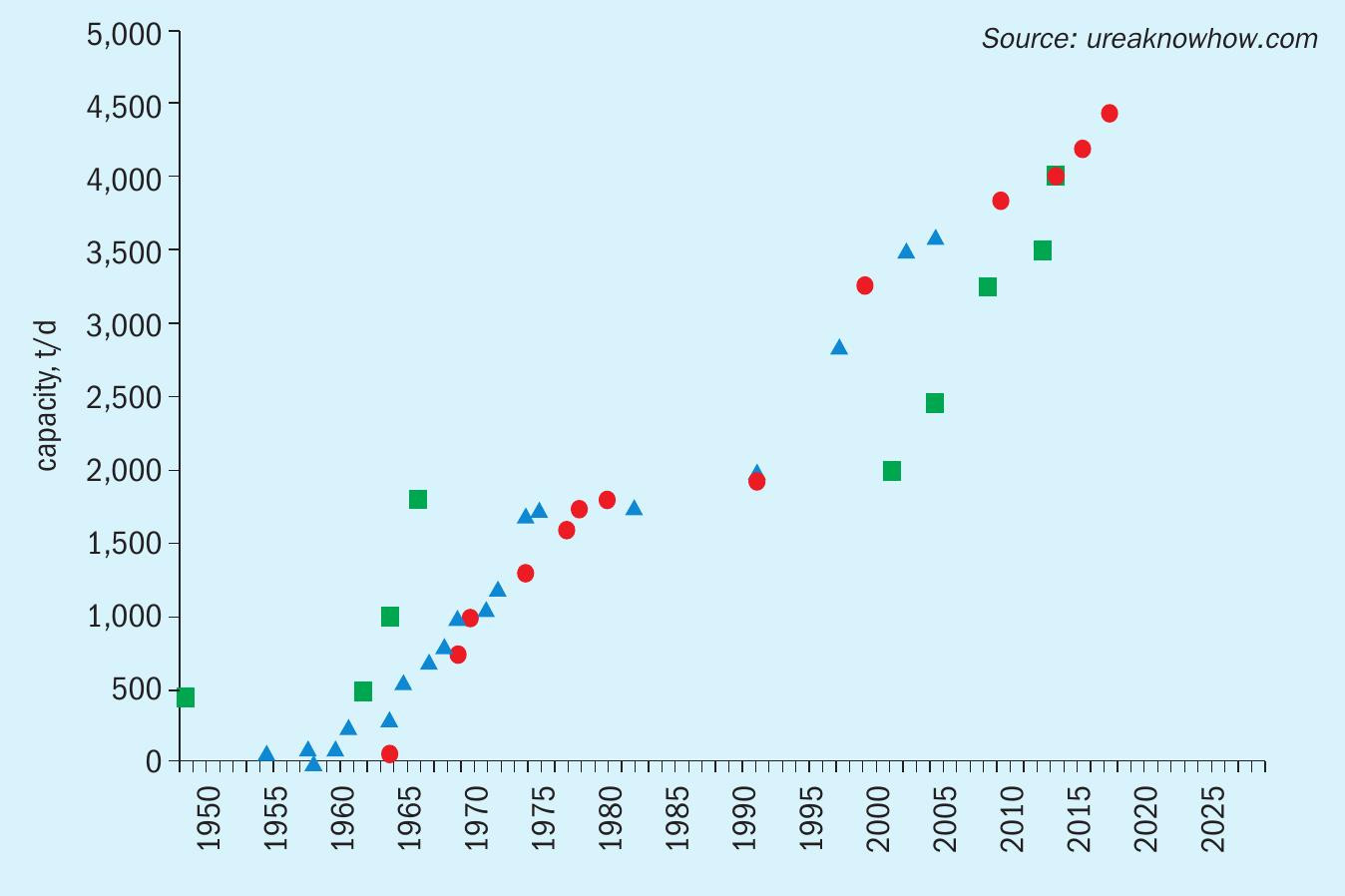
The increase in the production capacity of urea plants over the last 70 years is shown in Figure 3. This covers technology licenses awarded annually, by company, dating back to 1948. These include plants designed by Stamicarbon (triangle symbol), Saipem (diamond symbol) and TEC (square symbol).
The rise in the design capacity of urea plants over time – for all the major licensors – is a clear and consistent trend. Currently, Saipem, Stamicarbon and TEC all have urea plants in operation with a capacity above 4,000 t/d.
The trend for increasing design capacity looks set to continue. Due to economies of scale, we expect the first 5,000+ t/d capacity urea plant to be built within the next decade. If Stamicarbon applied its ‘medium-pressure add-on’ option as a debottlenecking technology to one of its current 3,500+ t/d urea plants, for example, this would increase urea production capacity to more than 5,000 t/d.
Revamp projects deploying de-bottlenecking technologies at existing urea plants have also enabled licensors to significantly exceed original plant design capacities. Examples include:
- Yara Canada, a 2,000 t/d Stamicarbonlicensed plant now running at 3,300 t/d
- Profertil, a 3,250 t/d Saipem-licensed plant de-bottlenecked to 4,200 t/d but operating at around 3,950 t/d
- Erdos, a twin 1,000 t/d Stamicarbonlicensed plant de-bottlenecked to 3,520 t/d single train capacity
- Sichuan Chemical Works, a TEC-licensed plant de-bottlenecked to 2,460 t/d using ACES21 technology.
The shift in industry focus in recent years away from large-scale urea plants to large-scale low-carbon ammonia projects is another noteworthy change (see discussion below).
Higher safety and reliability standards
The trend for increasing production capacities, noted above, has been delivered through better operational safety, exacting reliability standards and higher on-stream times at urea plants. These improvements have been achieved by introducing:
- High pressure piping and valves
- Proper leak detection systems
- More instrumentation
- Digital tools such as operator training simulators
- Digital twins of operating plants.
Lower energy consumption
Energy consumption of urea plants improved markedly following the introduction of CO2 stripping in the late 1960s, falling from around 1,200-1,400 kg/t to 900 kg/t. In general, the efficiency of urea plants has been more or less constant in recent decades, with no significant differences between the various process technologies1 .
However, Stamicarbon has recently been able to reduce urea plant energy consumption to less than 600 kg/t with its Ultra Low Energy (ULE) design (Fertilizer International 516, p21). This new design (Figure 4) achieves a remarkably low steam consumption by introducing:
- A medium-pressure recirculation step
- A heat exchanger between the submerged high-pressure carbamate condenser and the liquid outlet of the CO2 stripper
- A heat exchanger between the medium-pressure carbamate condenser and the evaporation heater.
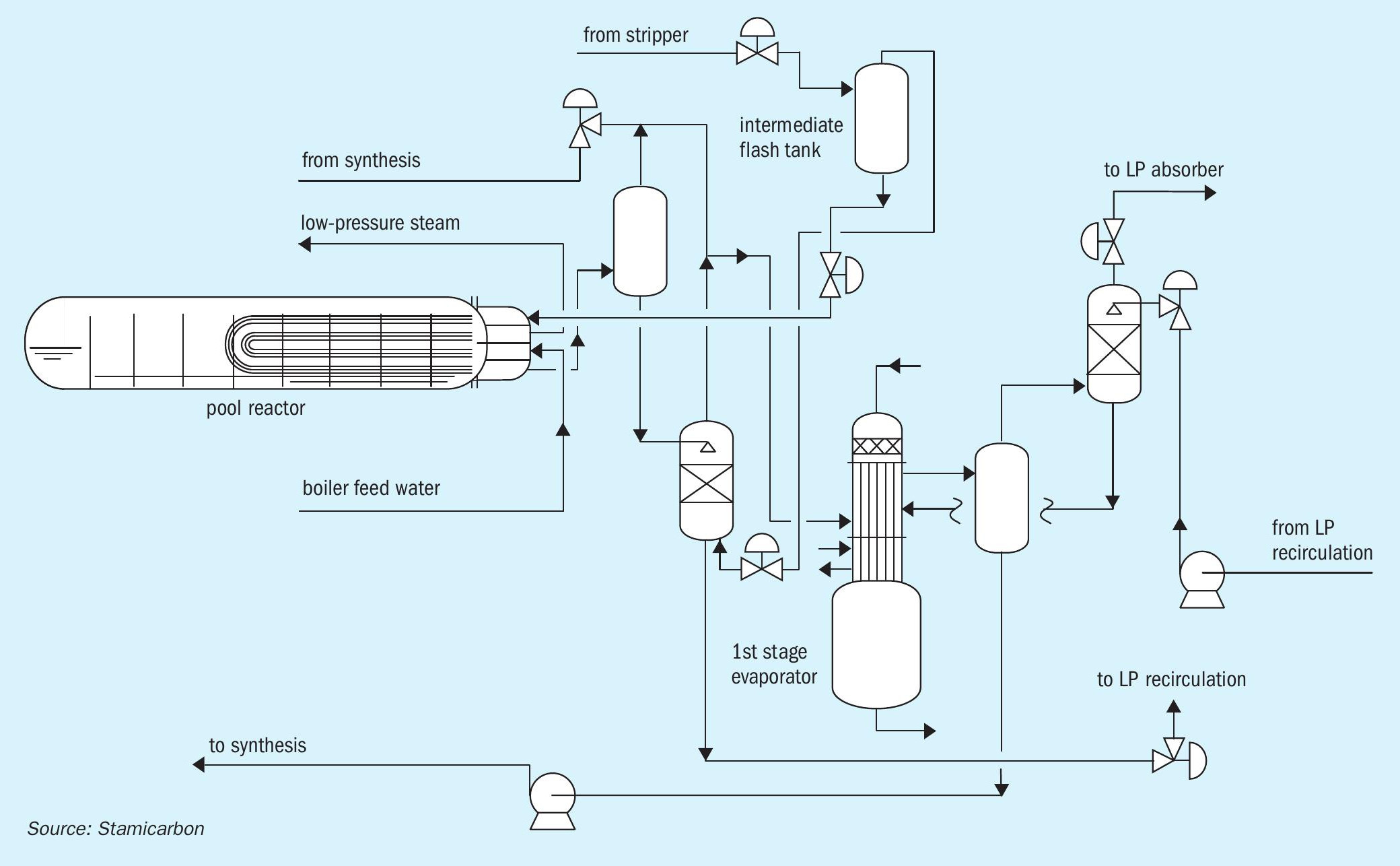
Stamicarbon’s ULE technology has proven very successful to date. The company has already signed contracts for seven ULE urea plants, the largest of these having a nameplate capacity of 3,850 t/d (Fertilizer International 514, p10).
Stamicarbon has been able to reduce steam consumption to less than 800 kg/t by configuring the medium-pressure recirculation section in creative ways – for example, as a medium-pressure flash vessel arranged in series downstream of the CO2 stripper. Stamicarbon has also used this installation set up as a powerful tool for increasing urea plant capacity by as much 50 percent.
Currently, nearly all urea licensors incorporate a medium-pressure recirculation section in their process designs. The successful drive to improve ammonia and carbon dioxide consumption at urea plants also means this is now approaching theoretical limits.
Nonetheless, there is still scope for efficiency improvements in other sections of the urea plant – by introducing integrally geared CO2 compressors, for example, or adopting Casale’s Green Granulation fluidised bed granulation technology.
Lower emissions
Urea plants operating globally need to comply with increasingly strict emissions requirements. Environmental permits for new plants in the USA are particularly stringent (<10 ppm NH3 and urea dust limits plus requirements for plume opacity). Urea plants operating in Saudi Arabia also need to implement acid washing to minimise NH3 emissions from prilling towers and granulation plants.
These regulatory developments, and the growing capacity of urea plants, have spurred efforts to reduce finishing plant emissions. IPCO’s Rotoform granulation technology, for example, has helped eliminate emissions from plants manufacturing specialty products such as technical urea, AdBlue and urea + ammonium sulphate.
The Grandperspective Scanfeld gas detector is a potential emissions gamechanger for the urea industry in our view. This automated, early-warning gas leak detection system can identify more than 400 chemicals at a distance using remote sensing.
A separate emissions and health concern is the use of formaldehyde to condition the final urea product. Formaldehyde is commonly used as an anti-caking agent and as a granulation agent in fluid bed granulation.
Although typically applied in the form of urea-formaldehyde solution, it is difficult to completely eliminate exposure to free formaldehyde. Consequently, leading companies are engaged in finding formaldehyde alternatives. Stamicarbon has been developing an alternative coating system for prills, for example, while both tkIS and Casale have developed alternatives for formaldehyde in fluid bed granulators.
Submerged condensation in the synthesis section
Submerged condensation in the synthesis section has been another important process development. This technological innovation was first introduced by Stamicarbon’s PoolCondenser in 1996. TEC then followed suit with the Vertical Submerged Carbamate Condenser (VSCC). Casale also introduced the Full Condenser as a ‘submerged’ revamp option for falling film high-pressure carbamate condensers. Using a submerged condenser in the synthesis section has a number of benefits1,2 :
- More efficient condensation as the heat transfer coefficient is around 40 percent higher than that of falling film condensation.
- This makes it possible to either reduce the heat-exchanging surface, cutting initial investment costs, and/or reduce energy consumption by raising LP (lowpressure) steam pressure.
- Ammonium carbamate is also retained in the condenser long enough for a significant proportion to convert to urea and water.
- This allows the condenser to be operated at a higher process temperature, enabling further reductions in the heat-exchanging surface and/or increases in LP steam pressure.
- Easier and more stable operation as the submerged condenser moderates fluctuations in NH3 /CO2 ratio.
High alloy construction materials
Another marked trend in urea process technologies is the development of high alloy super-duplex stainless steels with improved corrosion resistance. These materials are less sensitive to chloride stress corrosion cracking. They also offer other benefits as an engineering material, such as higher strength and thinner wall thickness. Importantly, construction using high alloy materials improves plant operational reliability and safety. This means urea plants can remain on-stream for longer periods, raising output and increasing their profitability.
Stamicarbon and TEC have both pioneered the use of super duplex stainless steel in high-pressure synthesis sections. Stamicarbon, for example, offers Safurex, a duplex (austenitic/ferritic) stainless steel, as the standard construction material for its urea plant synthesis sections. Tens of Stamicarbon urea plants with a Safurex synthesis section are currently in operation.
Safurex, developed in collaboration with Sandvik Materials Technology, possesses superior mechanical properties and is highly corrosion resistant at low oxygen concentrations, allowing for much lower air dosing in urea plants.
Similarly, many TEC plants use high pressure equipment made with DP28W™ , a duplex stainless steel. DP28W™ provides improved corrosion resistance in comparison to conventional duplex steel and shows excellent passivation behaviour in urea carbamate solutions2 .
A successful collaboration between Casale and Tubacex, meanwhile, created the super duplex Uremium29.
Saipem has developed OmegaBond tubes for its thermal stripping process. These combine a protective zirconium inner layer and a titanium outer tube2 . For its other high pressure equipment items, Saipem currently prefers 25-22-2 austenitic steel. The company is also developing a super duplex with Tubacex for its NH3 stripper.
Product innovation
Improving nitrogen use efficiency (NUE) and developing multi-nutrient fertilizers have been two of the main trends in urea product innovation. Combining urea with sulphur is a particular area of interest as this nutrient mixture can improve NUE. The range of available sulphur-enriched urea products includes urea + sulphur, urea + ammonium sulphate and urea + magnesium sulphate.
Other producers have focussed their efforts on developing inhibited or coated urea products – these being specifically designed to deliver nitrogen to crops more efficiently. Inhibitors reduce nitrogen losses by delaying the hydrolysis of urea and preventing ammonia volatilisation, while coatings regulate the release of nitrogen over the growing season.
The use of inhibited urea products has now become mandatory in certain European countries such as Germany. The EU is also specifying the use of biodegradable coatings in controlled-release fertilizers (CRFs) in future.
The use of NEEM-coated urea in India has helped to improve NUE on the subcontinent. India is also targeting enhanced nutrient efficiency by launching nano urea on the market.
Looking ahead, the rise of carbon farming and demand from food retailers and manufacturers for more efficient and low-carbon fertilizers is only likely to strengthen the current trend towards more efficient and sustainable urea products.
Discussion – the future of urea production
The 2015 Paris Agreement, by driving the global expansion in renewable energy capacity, is now leading to greater green hydrogen and green ammonia generation. This, in turn, is impacting the fertiliser industry, with leading ammonia producers (CF Industries, Fertiberia, Nutrien, Yara etc.) already investing in and expanding their production assets to enter the low-carbon ammonia market. Incumbent energy producers and new entrants have also launched large-scale projects to supply the emerging power generation and shipping fuel markets for low-carbon ammonia, e.g. NEOM in Saudi Arabia.
In future, based on the generation of green ammonia from renewable energy, we expect to see a worldwide trend for locating nitrogen fertilizer projects much closer to centres of agricultural demand. Typically, these new nitrogen fertilizer plants – which are mainly at the feasibility stage currently – will be much smaller in scale compared to the modern mega plants of today. However, the reverse is true of low-carbon ammonia projects serving the energy/fuel market, as generally these are being planned at a very large scale.
The increasing availability of low carbon ammonia, a consequence of the energy transition, provides the perfect stepping stone for the production of ‘green fertilizers’. These are typically ammonium nitrate-based fertilizers with a low carbon footprint.
Ammonium nitrate production does, however, come with limitations. Products, because they are potentially explosive, are tightly controlled due to safety risks and regulatory concerns over their misuse. Relative to urea, ammonium nitrate can also incur higher transportation, storage and application costs for producers, traders, retailers and farmers (on a per tonne of nutrient basis) due to its lower nitrogen content.
It is now possible to produce low-carbon urea using processes which consume carbon dioxide feedstocks generated by other sources. For smaller scale projects, however, production schemes for ‘value added’ low-carbon fertilizer products – such as urea ammonium nitrate (UAN), urea ammonium sulphate (UAS) and urea-based NPKs – are likely to be more feasible/profitable than straight urea production.
Large-scale investment will be required to make the transition from conventional nitrogen fertilizers produced from fossil fuel feedstocks (natural gas and coal) to their low carbon alternatives. Long transition times will be necessary too, given that nitrogen production complexes typically have a 40-50 year life. Natural gas-rich regions are also expected to remain big exporters of urea with investments continuing to favour the creation of higher margin downstream products using low-cost natural gas feedstocks.
As is well known, fertilizers make a major contribution globally to securing the supply of abundant and high-quality food. However, the environmental impacts associated with fertilizer use are now shifting the focus towards lower application rates and greater nutrient use efficiency (NUE). Delivering improvements in NUE will require a combination of:
- Innovative technologies that enhance fertilizer efficiency
- New regulations by policymakers that restrict the use of conventional ‘straight’ urea
- Improved farming practices
- Changes in consumer behaviour.
Such large-scale transformations take time and, while first steps are being taken, much more needs to be done to respect the world’s planetary boundaries. In particular, the fertilizer industry will need to shift production away from standard bulk commodities to specialty products – to support farmers as they seek to increase crop yields while at the same time avoid damaging environmental impacts.
When it comes to reducing agricultural greenhouse gas emissions, urea is generally seen as the least-sustainable type of nitrogen fertilizer. One of the main reasons for this is that every molecule of urea applied on farmland releases one molecule of carbon dioxide. Additionally, urea applications are also associated with the release of ammonia and nitrous oxide emissions.
A combination of better farming practices, and the use of urea granules treated with inhibitors or coatings, can reduce the carbon footprint of nitrogen fertilizers. Yet the adoption of such techniques and technologies in small-scale farming will always be a challenge.
Consequently, urea will remain a valuable source of nitrogen in agriculture for the foreseeable future, despite a greater focus on improving NUE and reducing the GHG emissions associated with its use. In our view, urea will continue to be an especially vital fertilizer when it comes to providing food security in developing countries where it will retain links to important cropping systems such as rice cultivation.
Summary
We conclude that the main future trends in urea process technologies will be:
- Urea plants with ever larger nameplate capacities
- Lower energy consumption
- Emissions reduction
- Submerged condensation in the synthesis section
- The use of high alloys in equipment construction
- A shift to the manufacture of multi-nutrient urea products, as well as coated and inhibited urea products with higher use efficiency.
References