Sulphur 413 Jul-Aug 2024
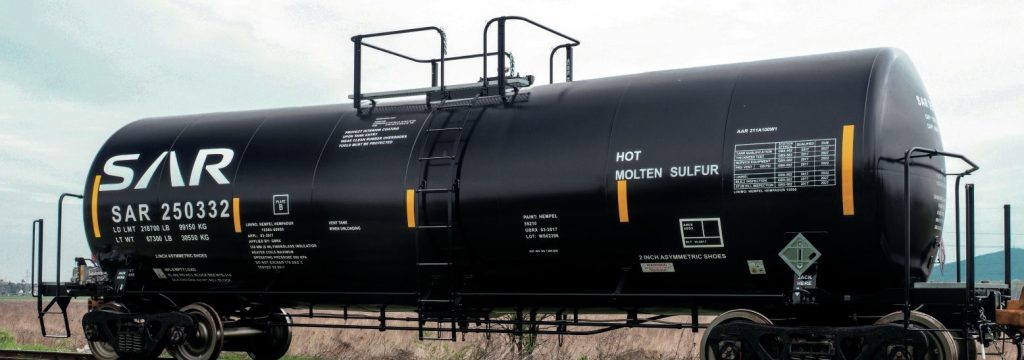
31 July 2024
Handling liquid sulphur
SULPHUR
Handling liquid sulphur
Liquid sulphur presents unique challenges in its handling and transport compared to solid sulphur.
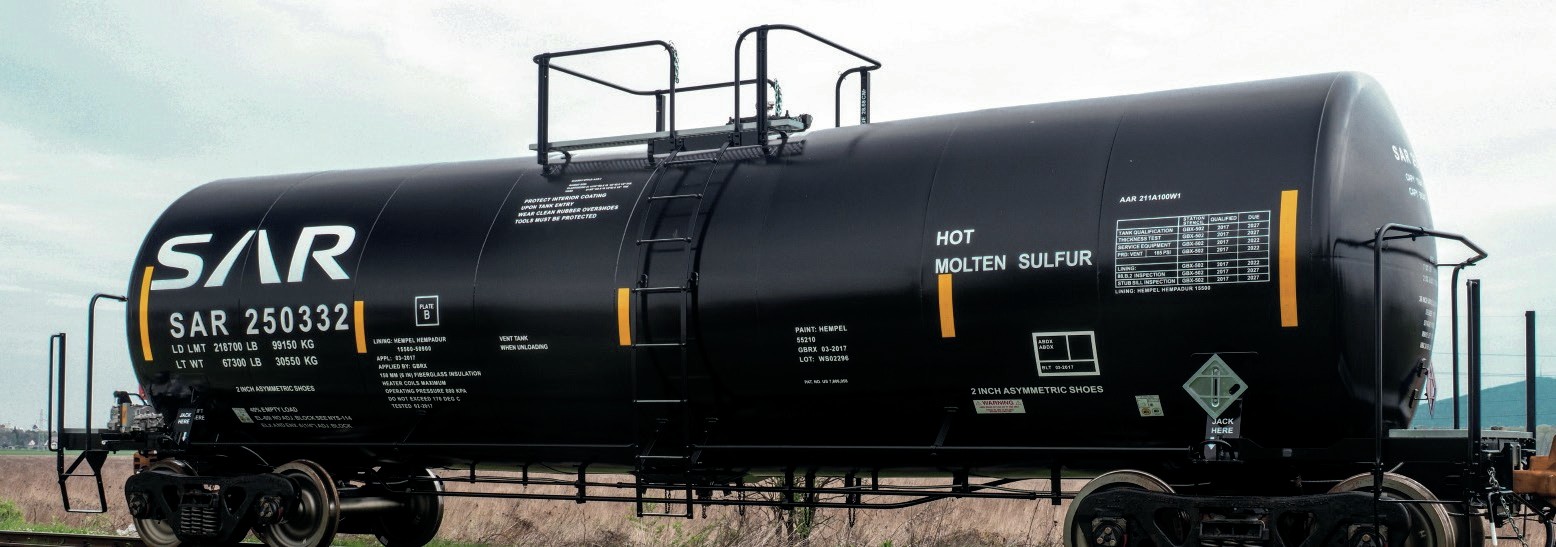
Sulphur comes from a Claus plant in liquid form, and the feed to a sulphuric acid plant – by far the most likely destination for recovered sulphur – is also as a liquid. There is an argument, then, for transporting it from one place to the other in liquid form as well. However, shipping and storing liquid sulphur brings with it various challenges and expenses which have so far restricted its use to a few well-integrated routes.
Shipping solids
Transporting solid sulphur has the advantage of relatively low handling and storage costs. The sulphur can be stored in open areas, perhaps with side walls to shield the sulphur from prevailing winds, and can be moved using open conveyors. This means that quite large volumes can be stored fairly easily. Sea transport of solid sulphur is similarly subject to relatively fewer restrictions than liquid sulphur; regular single deck bulk carriers can be used, provided that precautions are taken for carriage of solid sulphur, such as some form of corrosion protection for handling machinery and hold spaces.
However, transportation in this way is also subject to various problems. Sulphur stored in the open is subject to contamination by dust and water, and potential losses. Sulphur dust is also a well-recognised fire hazard, and various sprays may be required at stages of storing and handling to prevent or minimise dust formation. If storage spaces such as ship holds are not properly pre-treated, there is the potential for serious corrosion of steel, and resulting costly and time consuming lime washes to treat it. Finally most sulphur is used molten by consumers, so customers must supply energy to re-melt the solid sulphur at the other end, and potentially remove various contaminants.
Shipping liquids
On the one hand, liquid sulphur is less corrosive, and being transported in enclosed systems poses fewer environmental risks. There is far less chance of contamination and no re-melting is required at the destination. However, it must be maintained within quite a narrow temperature range, of around 125-145 °C (and typically 135140 °C). Around 158 °C sulphur undergoes a phase change and its viscosity rises very quickly, making it far more difficult to pump, while if the temperature drops there is the risk of the sulphur freezing solid, requiring long and expensive re-heating to melt it again.
Liquid storage obviously has limited capacity in heated tanks at source and destination, and so requires an integrated logistical arrangement, with coordinated storage on both sides and guaranteed transportation services.
Degassing
A prime concern for handling molten sulphur is the emission of hydrogen sulphide gas during loading of, e.g. trucks or rail cars. Nearly all molten sulphur contains some level of H2 S, and the agitation during transit or leading can result in the release of this hazardous gas. During the loading process, proper venting of H2 S to the atmosphere through a stack or to a scrubber or burner is essential for the safety of personnel, and it is also recommended that loading personnel wear a self contained breathing apparatus and do not rely strictly on mechanical means for their safety. Liquid sulphur is commonly degassed by passing air through it to convert H2 S into SO2 , reducing H2 S concentrations down to 10 ppmv before storage, compared with 250–300 ppmv in conventional sulphur pits, though dealing with SO2 and increasing restrictions on SO2 emissions can complicate the process. Even so, H2 S can accumulate in storage tank head spaces if the molten sulphur is stored for a long time, and air sweep techniques are necessary to prevent this from becoming problematic.
Tankers
International maritime laws on transport of liquid sulphur place significant restrictions on the ships that can carry it, and in practise it is shipped almost exclusively in dedicated vessels which are custom-built or converted for solely that task. Liquid sulphur is carried in separate tanks in the vessel’s hold, anchored on rubber-containing pedestals to allow for thermal expansion. Thermal expansion can also affect both the structural strength and the capacity of the tanks. The hull is generally double- or triple-walled, compartments separated by transverse bulkheads with insulation to minimise heat loss.
Cargo temperatures are maintained between 130-140 °C to keep the sulphur molten and at low viscosity. The temperature is measured electrically using thermocouples, and connected to an alarm system. Tanks, transfer pipes and valves must be temperature controlled at all times to keep from freezing shut.
In the past, steam was used to heat tanks and pipes, but this carries the risk of increased corrosion by formation of sulphuric acid with a leak, so many tankers have switched to an oil-based heating system for the main sulphur tanks.
The deck cargo pipe systems must also be insulated and heated to keep sulphur from solidifying. Generally this uses a skin effect electric heat tracing system, as familiar from many land-based sulphur pipelines, where an insulated conducing cable is run inside a ferromagnetic heating tube. The cable is connected to the heating tube at one end and a power source is connected between the cable and the heat tube at the opposing end. The inductive interaction between the current in the insulated cable and the return current in the heat tube causes heating which is then transferred to the neighbouring pipeline.
Other shipboard pipe systems use welded heating jackets, carrying steam, pressurised hot water, or hot oil.
Pipelines
Sulphur pipelines are used for transporting large volumes of sulphur over short distances, for example from a recovery plant to a forming plant. The main concern is keeping the sulphur molten over the distance and allowing for easy remelting should the pipeline become clogged. Several different heating methods can be used, mainly steam jacketing or skin effect heat tracing. Steam jacketing involves surrounding the ‘core’ or ‘inner’ pipeline carrying the liquid with a larger secondary pipeline or ‘jacket’. Steam in the space between the two pipes keeps the transported substance at roughly the same temperature as the steam. Potential issues include the difficulty in identifying leakage points and failures, and cross-contamination can occur if a leak appears in the interior pipeline, contaminating the liquid sulphur with steam. Heat tracing is an electrical heating element run along the length of a pipe. It is typically less costly than the construction of jacketed pipelines, although it is dependent on a reliable electricity supply, and many loading sites have steam readily available.
Truck/rail cars
For long distance travel overland, liquid sulphur is shipped in trucks or more typically rail cars. This is particularly true in North America, where sulphur often travels from Canadian gas plants to US consumers by rail. As with shipping vessels, maintaining the sulphur temperature above 120 °C and below 150 °C is imperative, and the tank cars will be heavily insulated with rock wool or fibreglass, and equipped with electrical heating coils. The main hazards are associated with loading and unloading of the tank cars. Generally the sulphur is unloaded from the bottom of the car using a hose or insulated unloading arm. Cold spots throughout the loading arm must be minimised in order to eliminate the risk of the product hardening within the arm, and steam-jacketing or strap-on heating elements can be used to provide even heating within the loading arm.