Fertilizer International 523 Nov-Dec 2024
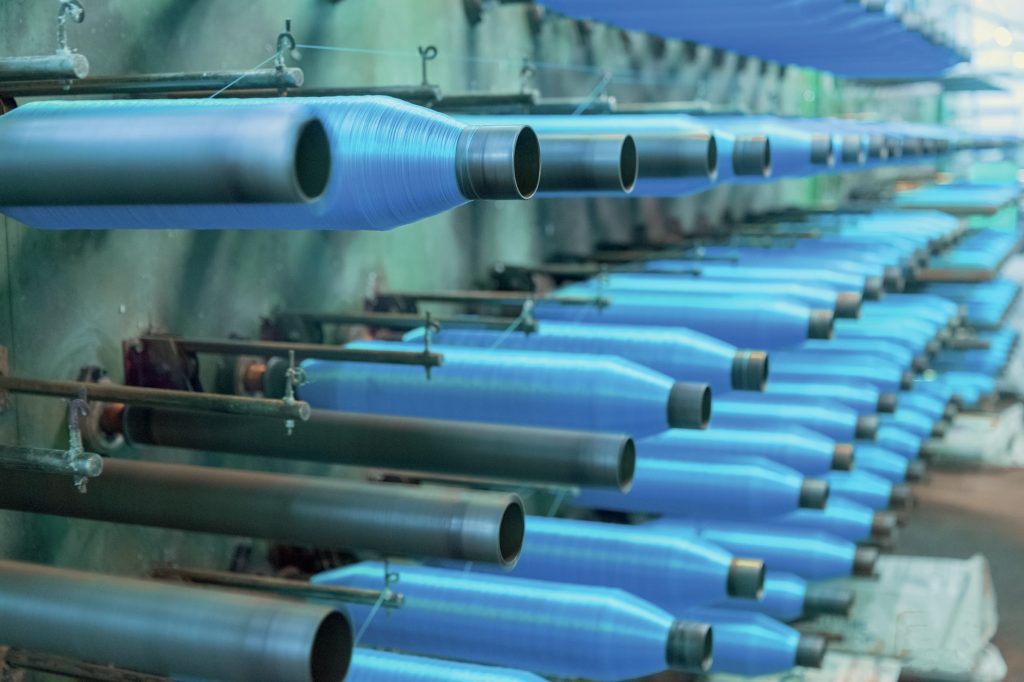
30 November 2024
Ammonium sulphate – a low-carbon sustainable pathfinder?
SUSTAINABILITY
Ammonium sulphate – a low-carbon sustainable pathfinder?
Emerging evidence suggests that by-products used as fertilizers, particularly ammonium sulphate, may emerge as winners from the EU’s implementation of the carbon border adjustment mechanism (CBAM). In this article, Franck Boher of Upgraid investigates whether by-products can help reshape sustainable fertilizer production in Europe.
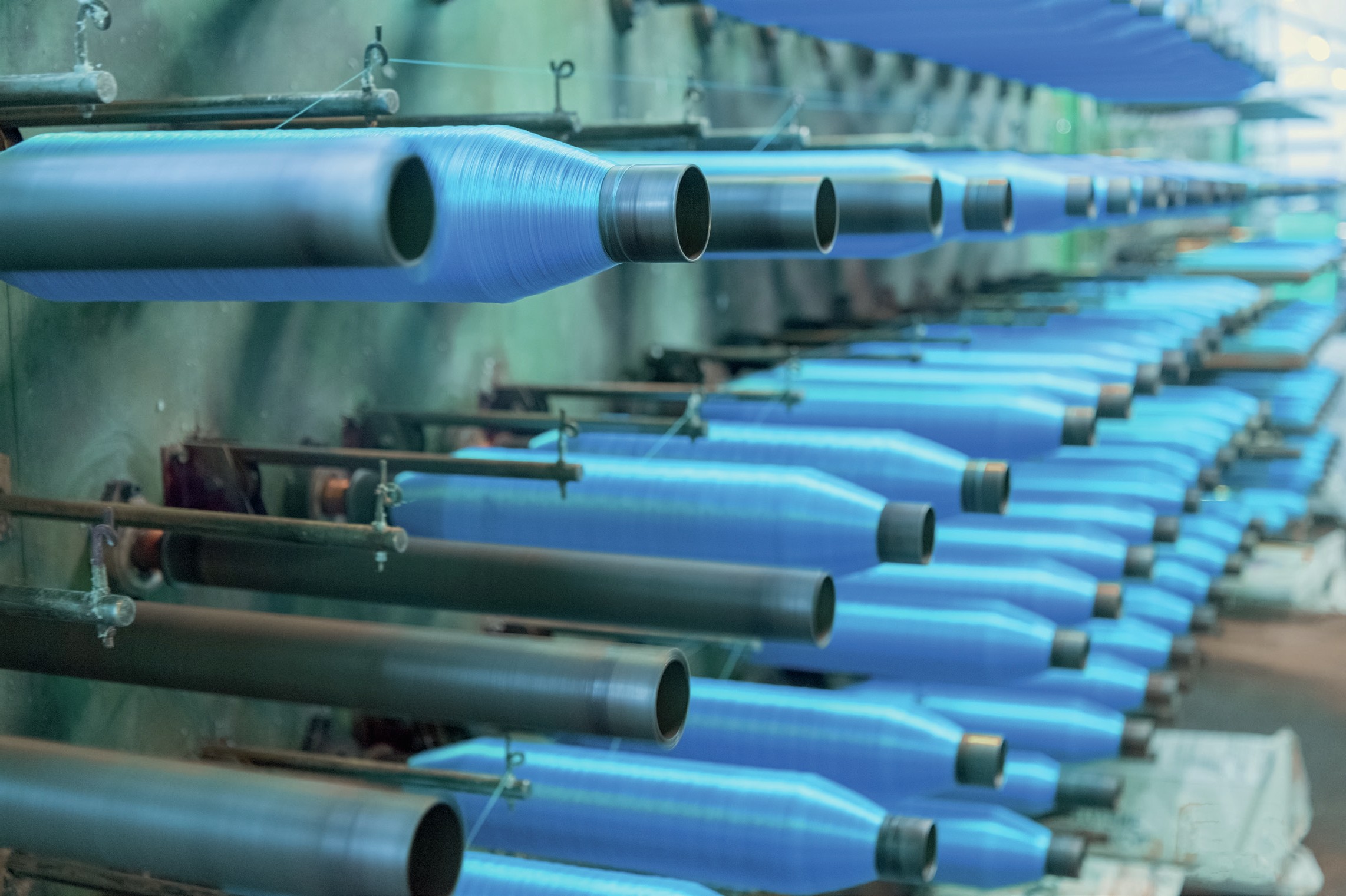
False choices
Recent events suggest that many fertilizer producers in Europe are struggling to maintain a delicate balancing act between EU sustainability requirements and the imperatives of worldwide competitiveness. Over the last 12 months alone, Yara’s Montoire and Timac Agro’s Tonnay NPK plants have closed in France, for example.
But does more sustainable always equate to more expensive and less viable. Instead, what if this is a false dichotomy and there are actually strong synergies between sustainability and competitiveness – with the two even going hand-in-hand?
EU regulations offer some hope
EU authorities have a two-pronged agenda. On the one hand, they are seeking to protect and grow industrial investment and employment in Europe, while simultaneously encouraging industrial players to adopt more sustainable and circular business models.
Across Europe, to meet these policy objectives, industrial projects designed to boost both sustainability and competitiveness have received substantial financial stimuli and subsidies over the last 10 years. Astute companies and individuals, who know how to navigate and take advantages of incentive programmes, can drastically reduce their business investment costs and speed up their returns on investment. To fully benefit from these potentially lucrative policy incentives, the skill is matching the right technology with the right funding source and the right project partners.
Even more significantly, EU regulators are gradually shifting policies to new goals such as:
- The protection of end consumers, e.g. chemicals regulation (REACH) and the fertilising products regulation (EU 2019/1009)
- Creating a level playing field between countries inside and outside the EU via the carbon border adjustment mechanism (CBAM).
Other EU policy measures are attempting to gain competitive advantages for the region’s industrial players. The way in which life cycle assessment (LCA) and analysis of business circularity, for example, are becoming key requirements for financial incentives at member state level provides some evidence of this.
In this article, we highlight how the ammonium sulphate market provides an excellent case study on how by-products used as fertilizers could emerge as winners from the implementation of these new EU regulations.
Ammonium sulphate – not a primary product
There is a sizeable and growing fertilizer market for ammonium sulphate internationally. Around 32 million tonnes are produced worldwide each year, according to International Fertilizer Association (IFA) statistics, with supply growing at 3-4 percent per annum. While this volume is far exceeded by annual urea production globally (190 million tonnes) it is broadly comparable to the market size of other nitrogen fertilizers such as ammonium nitrate (AN, 48 million tonnes) and calcium ammonium nitrate (CAN, 15 million tonnes).
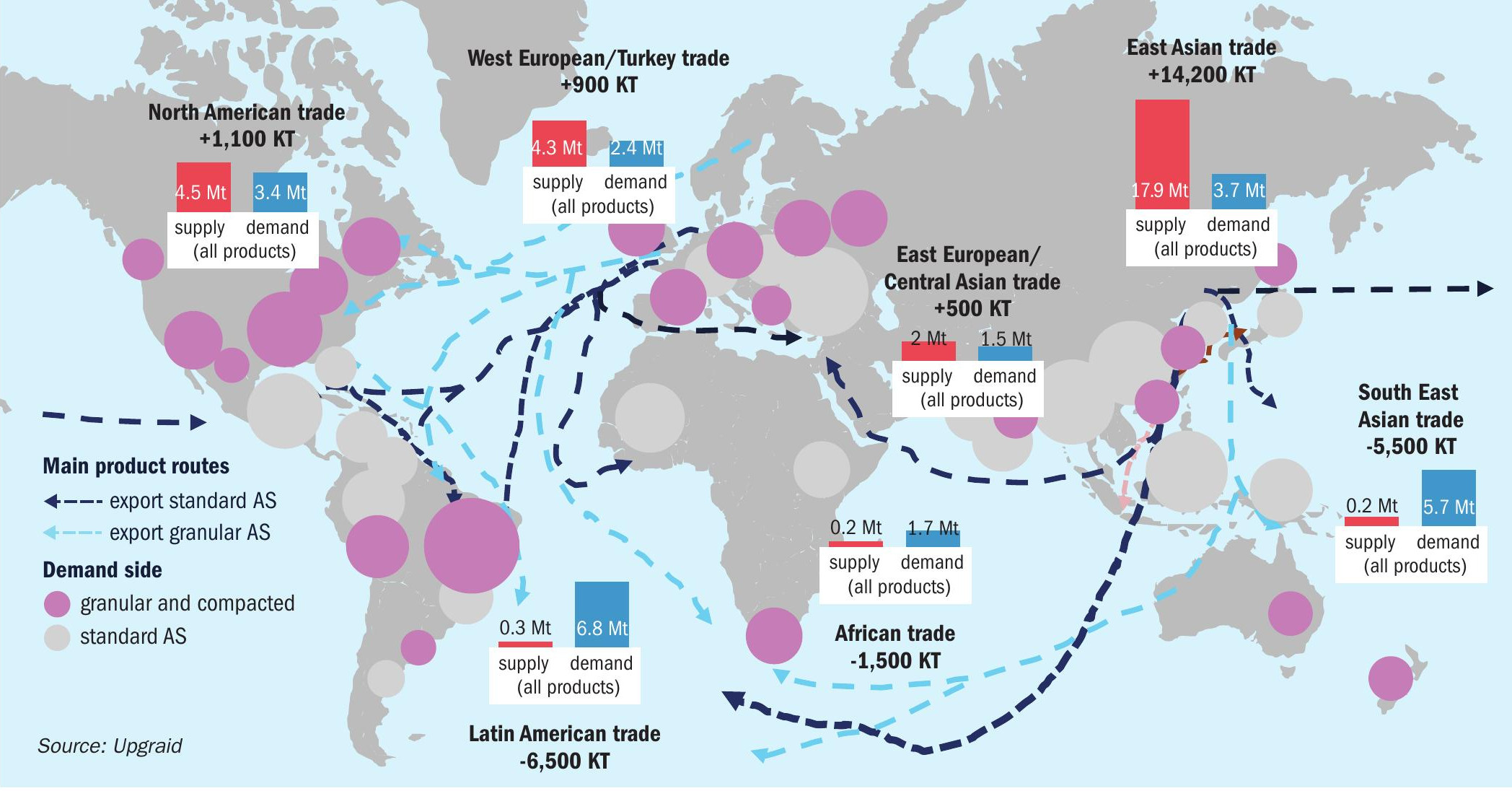
The main supply and demand centres and trade flows for granular, compacted and standard ammonium sulphate are shown in Figure 1. This illustrates how integral AS supply chains are to the global fertilizer market.
Ammonium sulphate is also in a unique position as, unlike other fertilizer commodities, it is typically not a primary product. Instead, more than 90 percent of the market is generated outside of the fertilizer sector as an industrial by-product. Consequently, AS is subject to very different market dynamics and price setting mechanisms in comparison to other fertilizers.
The boost to ammonium sulphate from CBAM?
Ammonium sulphate falls into the reporting scope of CBAM due to the carbon footprint of the ammonia (direct carbon value) and electricity (indirect carbon value) used in its production. Similar to other nitrogen fertilizers, the EU has published default values for ammonium sulphate for use in CBAM reporting. These defaults apply in cases where international suppliers are not able to directly verify the carbon footprint of the imported ammonium sulphate source. Values vary substantially from one nitrogen fertilizer to another, when calculated on a per unit of nitrogen basis (Table 1).
Current default values suggest that ammonium sulphate is subject to around 50 percent less carbon tax (per unit of nitrogen) than nitrates, with the caveat that this applies to the CBAM’s transition phase ending in 2026. Nonetheless, this already provides a sizeable competitive edge over certain nitrogen fertilizers – and is not the only competitive advantage offered by ammonium sulphate either.
Building a competitive edge
Primary (i.e. on-purpose) ammonium sulphate production is marginal, supplying less than 10 percent of global output while, conversely, 90 percent of world output originates as a by-product sourced from a range of different industrial processes.
In fact, ammonium sulphate is generated as a by-product by more than eight diverse chemical industry value chains – these ranging from polymer manufacture to electricity production, and from the production of amino acids to the making of electric vehicle (EV) batteries. These very different industries all have one thing in common though: they all split their carbon footprint between the primary core product and the by-product (ammonium sulphate).
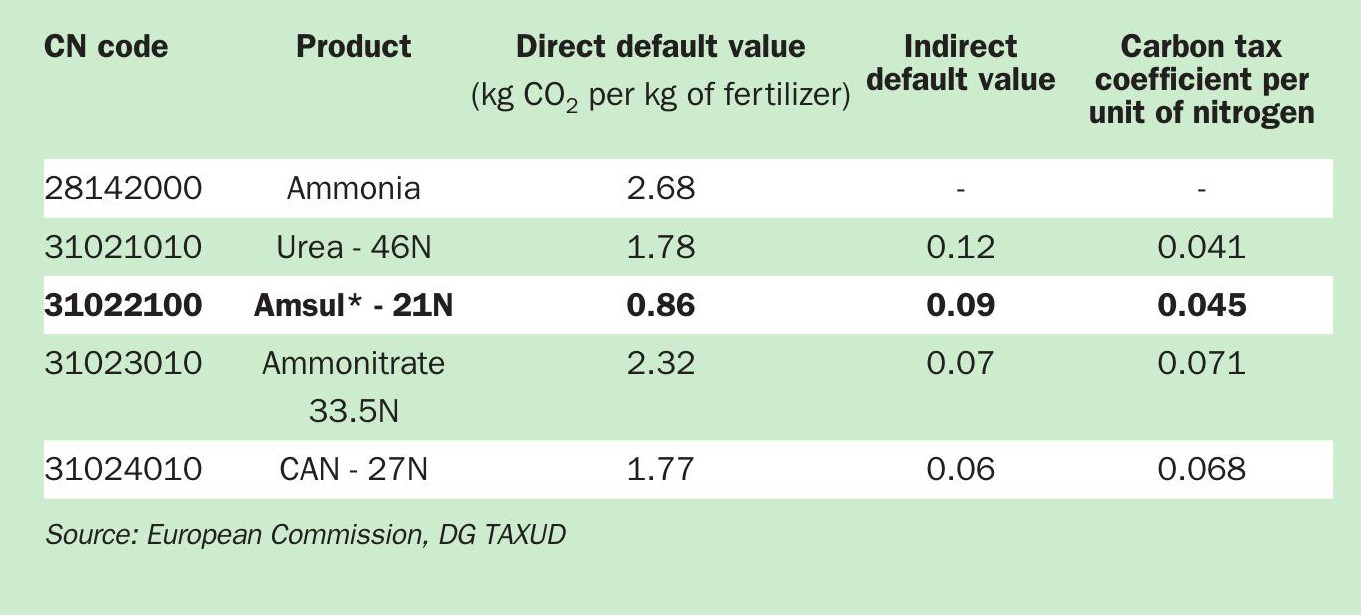
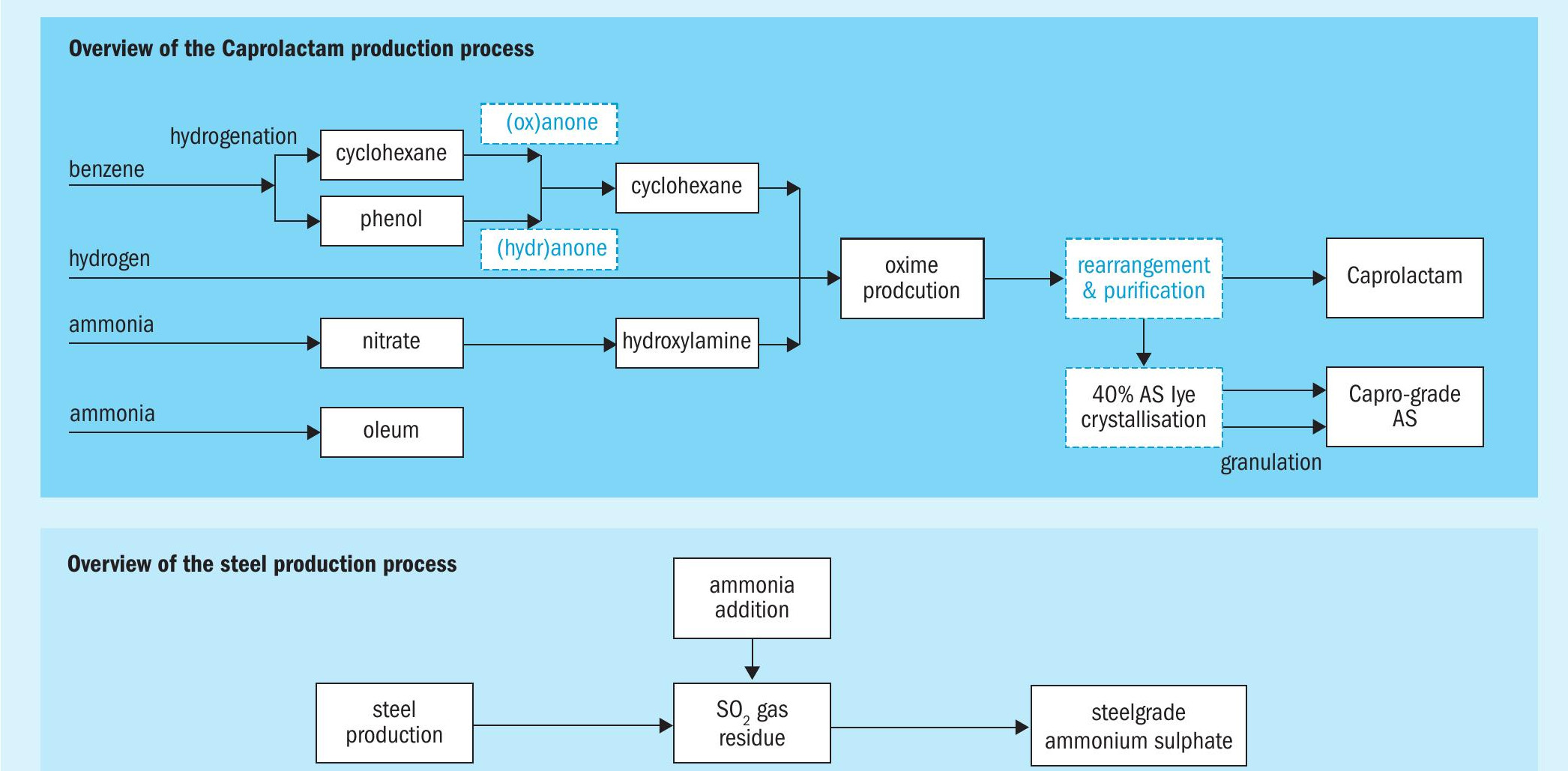
Currently, until the end of the CBAM transition phase in 2026, upstream industries actually have a degree of flexibility in how they allocate the portions of their ammonia carbon footprint between their core product and by-product, provided they document the chosen option. Unsurprisingly, the wide range of chemical industry values chains that generate by-product ammonium sulphate have made different choices which, in the end, will result in different amounts of carbon tax paid per tonne of AS produced.
This is a fact that fertilizer buyers, such as distributors and agricultural cooperatives, should be aware of when weighing up their sourcing options for ammonium sulphate in future. Answers on the carbon tax question are generally provided by pinpointing two things: firstly, the point of entry for ammonia into the process; and, secondly, whether the purpose of adding ammonia is for manufacturing the primary product or the by-product.
In general, the earlier ammonia is incorporated into the process for manufacturing the main product, the more likely it is that the already low carbon tax of ammonium sulphate can be reduced further (see Figure 2), as long as the industrial producer is properly documenting this.
In caprolactam manufacture (Figure 2, top), ammonia is a starting material added upstream as part of the main synthesis process. Consequently, the generation of caprolactam-grade ammonium sulphate, as a by-product, is more carbon-neutral because the carbon footprint of ammonia is already accounted for in the core product.
For steel-grade ammonium sulphate, in contrast, ammonia is incorporated downstream for the sole purpose of producing ammonium sulphate (Figure 2, bottom). This gas scrubbing process – and other AS production processes that treat sulphate residues with ammonia – is responsible for the entire carbon footprint of ammonia and, as a result, will pay higher carbon tax under CBAM, unless a switch is made to using blue or green ammonia instead.
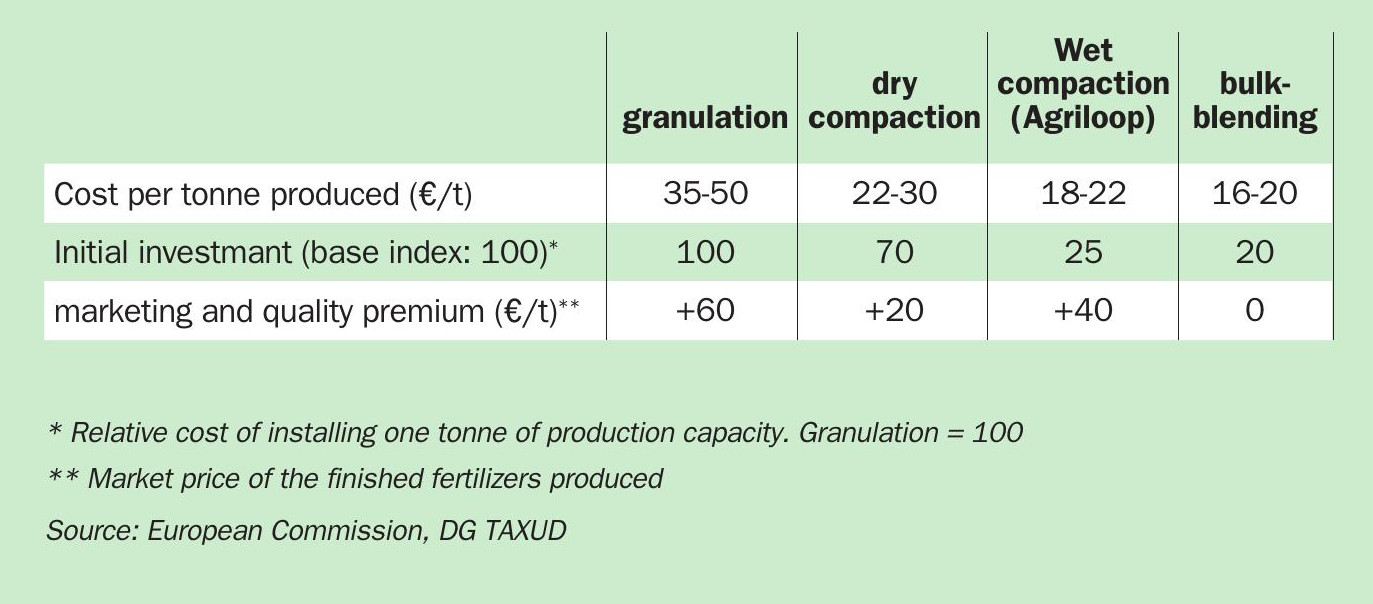
GREEN POLYMERS ARRIVE – BUT AT A PREMIUM
In the polymer industry, major European players like BASF, Lanxess, Fibrant, Domo Chemicals and Ube are developing low-carbon nylon and its precursor low-carbon caprolactam as part of their innovation pipelines.
The introduction of EcoLactam® – an ultra-low footprint nylon – by Fibrant, the world’s largest caprolactam and ammonium sulphate producer with production plants in The Netherlands (Geleen) and China (Fuzhou and Nanjing), is one example. The carbon footprint of EcoLactam® is up to 70 percent lower than standard nylon, according to Fibrant.
The demand for low-carbon nylon is being set by the clothing industry. High profile companies in the sports and outdoor apparel/footwear sector, in particular, have generally been first movers on sustainability and made very public pledges on carbon reduction. In any case, the carbon footprint of European caprolactam and nylon is already on a downwards trajectory having fallen by at least 20 percent over the last five years or so.
For many shoe and clothing makers, sustainability is an important part of their appeal to environmentally-aware consumers. In this context, a switchover to ‘green’ nylon provides these companies with a marketing edge – and therefore a potential competitive advantage that can justify its price premium. Despite this, a carbon tax is still seen as a necessary pre-condition for scaling up European production of low-carbon nylon.
While large-scale production will take time, a clear dividend for the fertilizer industry and its sustainability agenda is that low-carbon nylon manufacturing for the apparel sector could provide a growing source of low-carbon ammonium sulphate fertilizer as by-product – with clothing shoppers not farmers having to pay the premium for this.
In the scenario shown in Figure 2, steel-grade AS may end up paying pay twice as much carbon tax (e30-40/t) as caprolactam-grade AS.
To sum up, one fact is certain: splitting the carbon tax between a core product and a by-product should make ammonium sulphate even more attractive versus other nitrogen fertilizer options.
By-products – lowering production costs?
Fertilizer production in Europe has an industrial footprint that dates back more than a 100 years – starting with the founding of BASF, DSM, ICI, Rhône-Poulenc and other national industry champions. Unfortunately, this long and proud chemical industry heritage also has its disadvantages. Fertilizer production assets – which once symbolised Europe’s chemical engineering innovation and excellence – are now ageing and will require major investment if they are to adapt to the requirements of EU climate and energy policies. This includes the ‘greening’ of manufacturing processes and product portfolios by switching to low-carbon (green and blue) ammonia (see box). In the meantime, newer plants are springing up outside of the EU which are designed from the ground-up with sustainability and energy efficiency in mind.
Increasingly, for the European fertilizer industry, ticking both boxes for sustainability and competitiveness has become a prerequisite for survival. How then to achieve this?
When it comes to the granulation of compound fertilizers, for example, the question boils down to a simple cost equation: is Europe able to produce sustainably at e25 per tonne what it currently produces at e50/t or higher when gas costs surge?
Energy costs can vary from 25 percent to more than 60 percent of total fertilizer production costs, depending on the process used. Fertilizer finishing technologies, for example, generally rely on energy-intensive equipment and/or drying processes (Table 2). The evaporation and removal of water, in particular, consumes a high amount of electricity or steam.
Upgraid believes that shifting the European fertilizer production model away from energy-intensive granulation and compaction plants to energy-efficient processes that evaporate less water and are more scalable would certainly help make the industry more competitive again. By-product fertilizers such as ammonium sulphate could again be part of the solution here.
Ammonium sulphate has a crystalline structure that requires only minimal water evaporation to produce granules. Indeed, the compaction of ammonium sulphate stands out as a scalable and cost-competitive industrial model capable of producing granulated fertilizers with a minimal carbon footprint, as shown by the Agriloop wet compaction process in Table 2. The advantages include:
- A 40 percent reduction in energy consumption per tonne of product produced
- Achieves 65 percent primary throughput versus around 40 percent for drum granulation and dry compaction
- A 60 percent cut in CO2 emissions per tonne of product produced
- Cuts water consumption per tonne of product produced by a factor of four
- Valorising chemical and agro-industry by-products and transforming these into high quality granulated fertilizers
- Is scalable from 6-96 tonnes per hour
- Can granulate NPK, NKS and NPS fertilizers.
Summing up
In a nutshell, the European fertilizer industry – and, more broadly, the other value chains in the region’s ageing and commoditised chemical sector – are now at a crossroads where they will need to derive maximum value from their product portfolios if they are to survive. Now, more than ever, the use of by-products as fertilizers should be a particular focus.
Ammonium sulphate, for example, combines regulatory advantages, exemplifies the circular economy and offers a cost-optimised production model. This by-product stands out as a viable way of reconciling competitiveness and sustainability. It also has great potential as a stepping stone and transition product until green ammonia becomes affordable and widely adopted along the value chains of the chemical and fertilizer industries.