Sulphur 415 Nov-Dec 2024
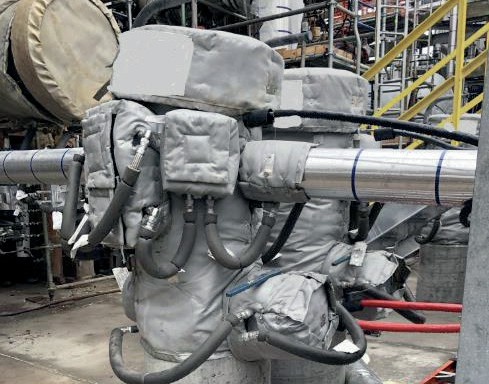
30 November 2024
Rejuvenation of a vintage SRU
SRU REVAMPING
Rejuvenation of a vintage SRU
In this revamp case study Scott Kafesjian and Quinn Kotter of Wood demonstrate how Wood sulphur technology was implemented at a 46-year old refinery SRU to improve reliability, operability and performance to meet new requirements for increased flexibility and higher availability.
A recent revamp project executed by Wood was contracted by a North American refiner with two operating SRUs – SRU A, dating to 1974, and SRU B, a modular unit, designed and delivered by Wood in 2006. Each SRU included a 3-reactor Claus section, incinerator, and caustic scrubber. Having installed a NaHS (sodium hydrosulphide) unit in 2013 to treat another sour gas stream, SRU A became a non-essential unit, only maintained for safe operation, with minimal investment otherwise.
A recent change in the refinery operating strategy elevated the importance of SRU A due to higher projected crude throughput and sulphur content. Accordingly, SRU A capacity was projected to become essential and high availability was required to enable the desired future operation of the refinery.
Major investment in sulphur units (usually regarded as cost centres) is difficult to justify, which is why SRU A had been somewhat neglected, but the revised strategy motivated and justified the revamp project.
Background
It was clear that with the escalated role of SRU A, a revamp would be necessary; however there were many known issues to overcome to meet the future demands, including:
- the thermal stage was inadequate to process sour water stripper acid gas; only amine acid gas could be fed;
- an obsolete, maintenance intensive, difficult-to-control reactor reheat scheme was in place;
- the 3rd Claus reactor became inoperable early in the life of the unit and subsequently had been completely bypassed;
- the sulphur pit concrete was severely degraded and excessive fugitive emissions were present;
- the burner management system (BMS), although functional, was antiquated and obsolete;
- air flow to the SRU was manually controlled due to an inoperable air demand analyzer (ADA);
- excessive CO emissions from an undersized quasi-natural draft incinerator;
- severe corrosion due to caustic carry-over from the tail gas SO2 scrubber to downstream equipment.
Long-term improvement to SRU A was needed to ensure that it could reliably meet projected refinery sulphur production and serve as a backup to SRU B.
The revamp scope was identified in the bidding stage as:
- replace end-of-life/obsolete equipment;
- eliminate the ineffective reactor reheat scheme;
- recommission the No. 3 Claus reactor;
- replace the ADA and stack CEMS;
- replace local burner control panel with SIL2 rated, remote PLC;
- eliminate corrosion issues related to the SO2 scrubber.
The process scheme prior to the revamp is shown in Fig. 1.
Highlights of the configuration include:
- an obsolete acid gas burner and single chamber thermal reactor;
- two-pass waste heat boiler developing steam at 250 psig with sulphur rundown connections;
- hot gas bypass reheat scheme for the No. 1 and No. 2 Claus reactor inlet streams (where the “hot gas” consists of a portion of the thermal reactor effluent mixed with a portion of the first WHB pass effluent);
- the 1st and 2nd sulphur condensers were in a common shell (developing 40 psig steam) and the 3rd sulphur condenser was a BFW heater in a separate shell;
- the No. 3 Claus reactor had been bypassed (piping removed) and abandoned in place;
- the ADA was out of service and air control was manually adjusted based on acid gas feed rate and caustic consumption over time;
- a quasi-natural draft incinerator located after the No. 3 sulphur condenser, followed by heat exchange to scrubber effluent upstream of the stack;
- after heat recovery, incinerator effluent was further cooled in a venturi quencher then entered a packed bed caustic scrubber for SO2 removal;
- sulphites in the scrubber blowdown were oxidised and routed to the refinery WWTP;
- a booster blower downstream of the scrubber was used to control incinerator outlet pressure to maintain draft;
- booster blower outlet was heated against incinerator effluent and routed to atmosphere via the stack.
At the start of the project, it was anticipated that there would be additional scope developed since a unit turnaround was scheduled to begin shortly after project kick-off. Inspections planned during the turnaround were expected to result in additional “discovery” scope.
The project scope also included consideration of improvements to safety, reliability, performance and operability leading to recommendations to the owner. Recommendations would be evaluated based on technical justification and their estimated cost. Numerous improvements were recommended by Wood based on process evaluation and turnaround findings.
Post-turnaround, it was known that the unit would need to operate for about two years before the revamp could be implemented during the next planned unit shutdown.
Scope evolution
Table 1 summarises turnaround findings and the proposed interim action before the revamp.
In the early phase of the project Wood recommended several key process configuration changes in addition to the initial known revamp scope:
- eliminate gas/gas heat exchanger;
- eliminate booster blower;
- replace induced draft incinerator with forced draft design capable of improved control, higher operating temperature and increased residence time;
- route incinerator effluent directly to quencher;l replace quencher with new venturi with upgraded MOC designed for higher inlet temperature;
- replace scrubber packing with more efficient, lower pressure drop packing;
- replace degraded stack with higher metallurgy, smaller diameter stack supported by existing structure;
- include an engineered external thermal protection system (ETPS) for the thermal reactor;
- improve thermal reactor air flow control algorithm to stabilise operation and utilise the new ADA output;
- replace sulphur pit with an above-grade sulphur header and storage tank.
Fig. 2 shows the configuration of SRU A after the revamp. Highlighted changes to the unit configuration include known owner defined changes/additions and Wood’s recommended changes/additions.
Wood also recommended complete replacement of the waste heat boiler; however, this was not approved due to high cost, lack of plot space, and turnaround findings showing acceptable remaining life of all components.
Challenges
As the project progressed through the stage gate process (FEL-1/2/3), several challenges were encountered.
Unit location: Being an older unit located near the refinery boundary, the unit was restricted by roads on three sides and an operating unit on the fourth side, rendering plot space very limited. Existing equipment was tightly spaced. Existing utility piping was a mix of active and inactive lines, without clear status documentation.
Sulphur product collection: A significant challenge was that limited elevation was available for sulphur rundown line routing to allow product collection by gravity flow. Both sulphur condensers and the WHB remained at their original location and elevation. The condensers were adequately elevated for proper line routing. The most difficult sulphur collection location was the sulphur outlet from the second pass of the WHB, which was the farthest from the new sulphur header and at the lowest elevation. Enabling gravity drainage required replacing the existing vertical sulphur outlet nozzle with a nozzle oriented tangentially to the bottom of the outlet plenum (Fig. 3). Sulphur seals on all rundown lines were specified with zero elevation change from inlet to outlet (Fig. 4). Furthermore, minimal slope of rundown lines was specified (1/8” per foot of running length). The collection header was set at minimum elevation above grade as the owner did not allow below grade installation.
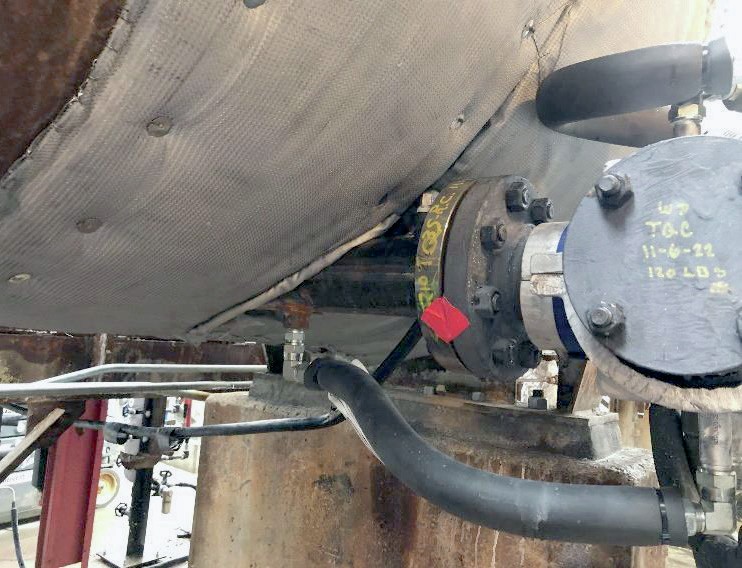
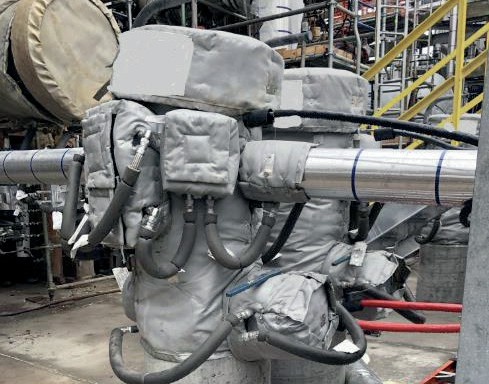
Pandemic: Part way through the project, COVID-19 became a household word and the “new normal” way of working had to be defined, accepted, and complied with while minimally disrupting project progress.
Scope additions and changes were common as the owner and Wood identified and sorted out various “want to have” and “must have” items. This working environment required a nimble project team, constant attention to agreed scope, timely communication between owner and engineer, and a steady stream of change notices requiring preparation, review, and approval.
Restore SWSG feed: A major addition to the revamp scope took place after completion of detailed engineering based on owner philosophy change – the unit was to be able to process sour water stripper acid gas feed to in the event that SRU B was completely out of service. This change necessitated the following additions:
- restore SWS KO drum;
- replace the feed piping for SWS gas and add piping for amine acid gas rear chamber split;
- include flow measurement and control for SWS gas;
- preheat both acid gas feed streams (accomplished with engineered external heating elements);
- revision of thermal reactor vessel and ETPS size;
- refractory and checker wall revisions;
- thermal reactor temperature measurements (internal and external).
Unit sulphur production capacity is reduced when SWSG is fed, so there was a derate of unit capacity. Nearly all aspects of the design had to be checked to assure there was no impact due to SWSG processing.
The overall project duration from award to introduction of acid gas feed was 47 months. The discovery turnaround occurred about three months after project award, simultaneous with the FEL 1/2 effort and Wood’s process evaluation and reconfiguration recommendations. FEL 3 was completed and detailed engineering began about six months after award, followed by equipment bidding and order placement in the following months. Shortly thereafter, Covid protocols were initiated, inevitably slowing progress as the owner, Wood, and vendors adjusted to the global supply chain impact. As a result, detailed engineering duration was months longer than originally planned. Shortly after detailed engineering completion, addition of SWSG processing was requested and additional design work began as a result.
Wood was not directly involved in the construction activities, however, Wood provided support during commissioning, pre-startup checkout, and startup. Successful start-up of the unit was accomplished, and early performance indicates significant operating cost savings are realised from greatly reduced caustic consumption in the scrubber due to improved sulphur recovery in the Claus section.
Summary
A change in refinery strategy placed increased importance on the availability, controllability, performance, and safety of an existing 46-year-old SRU.
The many benefits of Wood sulphur technology improved reliability, availability, efficiency, and performance, reduced maintenance and improved safety, while meeting owner requirements, and enabling SRU A to fulfil its elevated role in the refinery.