Fertilizer International 523 Nov-Dec 2024
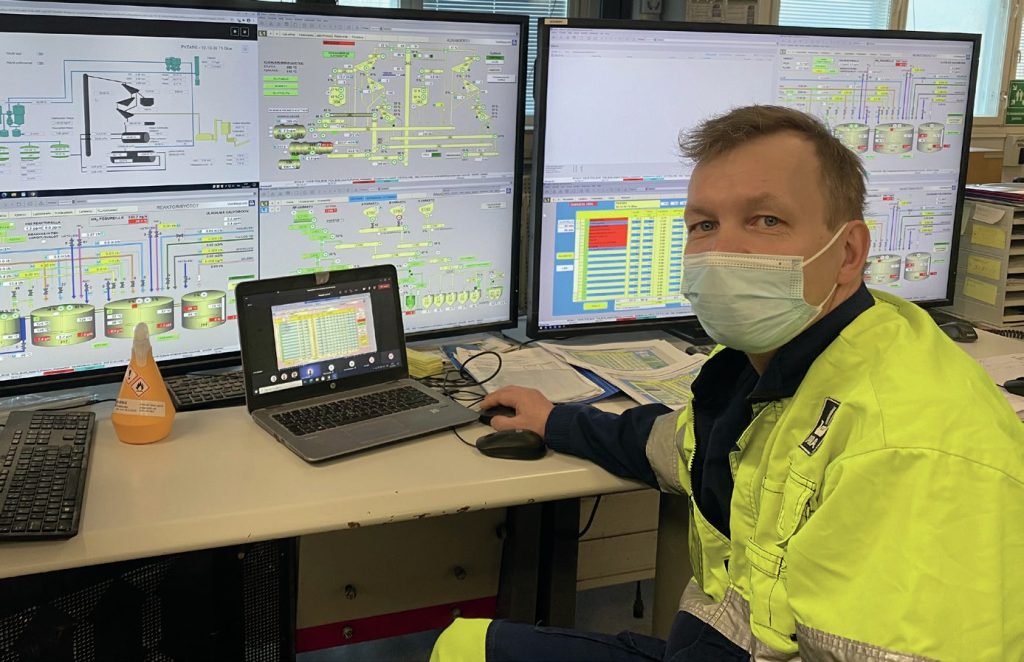
30 November 2024
Yara’s Golden Batch tool – digitally optimising NPK production
PRODUCTION TECHNOLOGY
Yara’s Golden Batch tool – digitally optimising NPK production
The ‘golden batch’ refers to stable periods at production plants that consistently generate high quality NPK products at high output. Yara’s Golden Batch digital tool digitises and stores past data from optimal production runs, making these easy to retrieve and implement again in future. Yara’s Marianne Ytterbø provides an overview of this novel digital tool, explains how it was developed, and highlights key benefits.
Introduction and overview
The Golden Batch is a digital tool built and developed by Yara for NPK fertiliser plants. The basic idea of the tool is to digitise historical records of ‘good production’ held by operators in binders and notebooks. The tool provides access to data on previous successful production runs in a user-friendly way and, by making these searchable, allows operators to follow up on this knowledge during current production. It also continuously monitors the plant, ensuring the best production periods are always captured and stored for the future.
Central to the tool’s development has been an objective definition of ‘good production’. Having a clear definition plays a dual purpose as it allows:
- Firstly, the identification of golden batches in historical datasets, and
- Secondly, the identification of superior production periods during current plant operations – providing scope for further ‘real time’ production optimisation.
This approach, by avoiding subjective assessments of NPK production runs, helps improve production standardisation, troubleshooting capabilities and the training of new personnel.
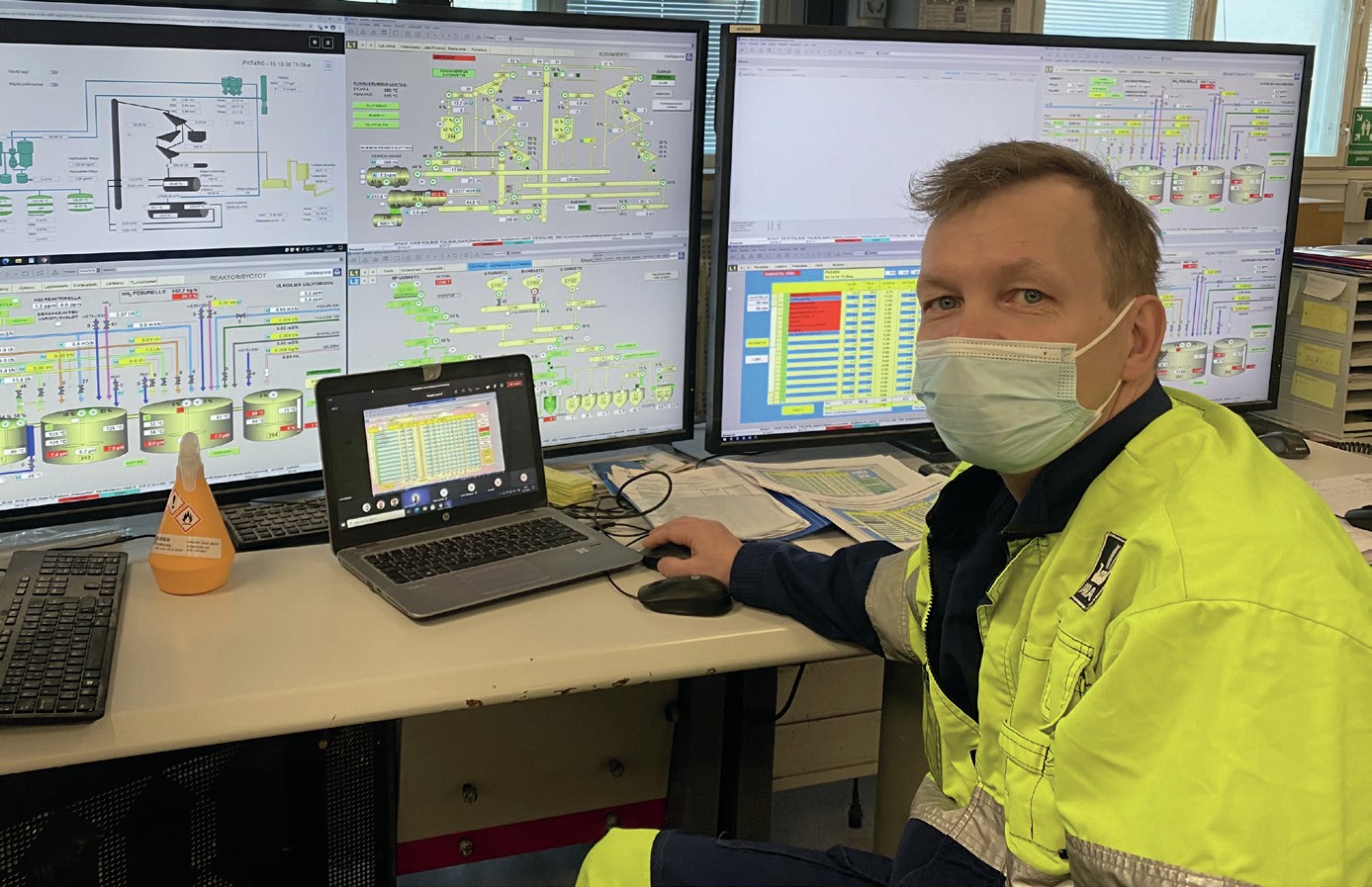
Unsurprisingly, adopting such a novel and transformative tool has not been without its challenges. In particular, operator training and implementation at NPK production plants has demanded substantial time and effort – but, nevertheless, these actions have been imperative for unlocking the full potential of the tool.
Presently, the Golden Batch tool has been successfully implemented at eight Yara NPK plants. Overall, this has resulted in high user adoption, as a clearly observable trend, albeit with challenges at some plants. Also, at the initial plant where the tool was deployed, a post-project review revealed a significant increase in the production rate after implementation.
Importantly, the Golden Batch is not a static solution. Instead, it is a dynamic tool designed for continuous improvement. The app will continue to evolve in future – in response to user needs, innovative ideas, and constructive feedback.
Yara’s Digital Production department
Yara identified the potential for generating significant value from digital transformation at its production plants in 2018, and established a department called Digital Production to unlock this potential. This new department built up the company’s in-house digital competencies by recruiting developers and data scientists.
The core principle of the department is ‘value first’. In practice, this means adopting a methodology where problems, and the potential value to Yara of overcoming these, are comprehensively understood before work starts on developing solutions. To put it simply, the department focuses on the ‘why’ before delving into the ‘how’ – always gaining a thorough understanding of why a particular issue merits resolution before considering how to rectify it.
Identifying priority production issues at Yara plants requires an analysis of the potential value of the proposed solution coupled with an estimate of the amount of effort required to unlock this value. Consideration is also given to whether proposed solutions can be effectively scaled and replicated across multiple plants.
To analyse and answer these questions, personnel at the Digital Production department work alongside plant experts as part of cross-functional and multidisciplinary teams.
Description and origins of the tool
The core functions of the Golden Batch tool are to:
- Continuously monitor the production process
- Identify and preserve exemplary production runs – known as ‘golden batches’ in a comprehensive database.
These golden batches serve as reference points, providing operators with access to the best production settings at their fingertips.
The Golden Batch tool is based on an idea that originated at Yara’s NPK fertiliser plant in Uusikaupunki, Finland, and was subsequently developed in a collaboration between the plant’s staff and Yara’s Digital Production team. The aim was to provide NPK plant operators with easier access to the best production settings.
The Golden Batch tool – by offering intensive, focused, and regular access to information on the best reference batches – has enabled operators to achieve higher production rates during NPK production runs. Furthermore, the tool allows operators to achieve stable production more quickly – after start up or NPK grade changes – by providing a clear visual overview of production target values.
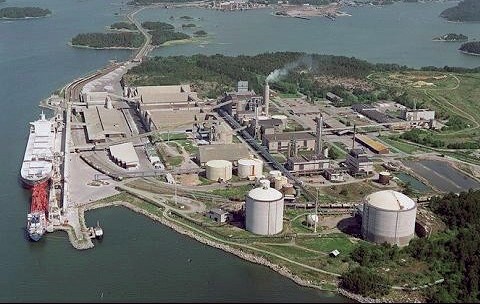
Tool development at Uusikaupunki
A promising production solution identified early on by the Digital Department was (as already mentioned) based on an idea from the NPK production team at Uusikaupunki.
When production was running well, plant operators at Uusikaupunki captured control system screenshots and subsequently maintained these in binders for future reference (see photo). Their motivation was to preserve these successful plant settings and use this information for fine-tuning future production runs.
The Uusikaupunki plant produces many NPK product grades, with each individual grade requiring a different way of optimising the process to ensure good production runs. In addition, the plant’s running behaviour will also be influenced by day-to-day variations in operating conditions. These can include differences in the types of raw materials being consumed, fluctuations in ambient temperature, and the level of clogging in production equipment.
All these variables can make it difficult for the operators to keep track of and properly adjust the production process and optimise this for each combination of NPK grade and plant operating conditions. However, using the reference binders, operators at Uusikaupunki could now browse back and find a suitable screenshot as a starting point for adjusting the current process.
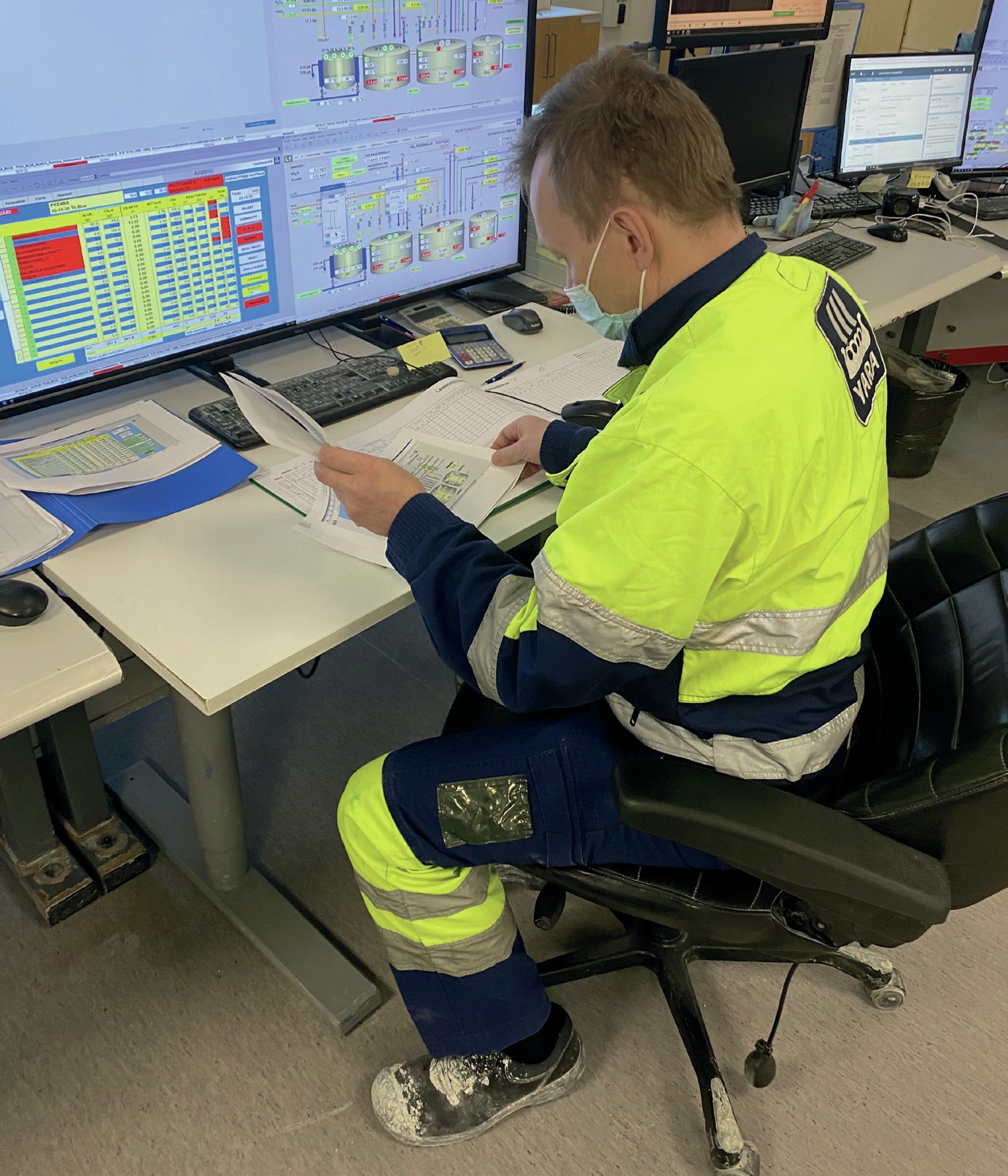
The original concept for the Golden Batch tool had two aspects: firstly, to digitise these reference binders and, secondly, ensure that exemplary reference batches – new golden batches – were automatically detected in future so they could be preserved for subsequent use.
Golden batch definition
The starting point for collaboration with the Uusikaupunki plant was formulating a definition of ‘good production’ by analysing historical process data. The initial focus was on identifying periods characterised by a high production rate. However, data analysis revealed that high production rate alone was an insufficient as a criterion, because ‘good production’ also required operational stability, this being characterised by low process variance over an extended duration. Taking stability into account was necessary to ensure that any reference batches saved for future use could be sustained over a lengthy time period.
For example, while it is possible to ramp up NPK production to an extremely high rate, this is not necessarily stable as it can potentially lead to undesirable outcomes subsequently, such as the clogging of crucial production equipment. The incorporation of long-term consequences as part of the definition was therefore crucial, because solely maximising production rates – without due regard for future consequences at the plant – could result in adverse effects and operational difficulties.
Various stability criteria were evaluated before coming up with a suitable and comprehensive definition of stable production. The purpose of this exercise was to identify a set of criteria that, from the historical dataset, could:
- Identify stable production periods for the majority of NPK product grades
- While simultaneously excluding periods marked by instability.
The criteria examined included variance of the production rate itself, along with other pertinent ‘tags’ such as the electric currents of important motors and recycle rates. (Note: a tag is a control system object that contains a variable, time stamp and data quality information.)
During the examination of historical data plots, a decision was made to accommodate brief periods of instability – as shown by short, intermittent spikes in the data – where these were within a much longer stable period.
The eventual outcome was a robust methodology and definition for detecting periods of high and stable production. But this was not all. NPK plant operators are also required to monitor and control other important production parameters. In particular:
- The plant needs to generate high quality NPK end products that meet quality standards and avoids excessive amounts ‘off-spec’ material
- Emissions from the production process need be kept low to meet environmental regulations.
At Uusikaupunki, product that does not meet the Yara quality standard is stored in separate silos and recycled back into the process as raw material. Operators need to prevent these silos from overfilling.
Therefore, due to their importance, both emissions and product quality were incorporated into the definition of good production by introducing a concept known as ‘comparable production rate’. This penalises emissions and the production of undersize products while rewarding the consumption of off-spec products in the production process.
From this, the following finalised definition of a golden batch was agreed. This combines the definition of high and stable production with the concept of comparable production rate:
“A golden batch is identified as a six-hour period characterised by stable production and exceeding 80 percent of the highest production rate achieved for that product grade in the past. In instances where multiple stable periods occur during a production campaign, the golden batch is determined based on the period with the highest comparable production rate.”
This systematic approach provided a reliable means of identifying and preserving periods of good production from the past as reference points for future operations.
Operating conditions and product quality
As mentioned previously, optimal plant settings depend on both the product grade and on the operating conditions.
Operating an NPK plant is something of an art, requiring knowledge of how to adjust the plant in response to numerous conditions affecting the production process. To reduce complexity, it was agreed with plant experts that the Golden Batch tool should include selected operating conditions if these:
- Affect how the plant runs
- And/or affect the production rate that can be obtained
- But are outside the operator’s control.
For example, an increase in the outside temperature may require a reduction in production rate at the plant because of limited cooling capacity. Outside temperature, therefore, while affecting plant capacity and production output, is an operating condition outside of the control of operators who have no influence on the weather.
Allowing for operating conditions is important as, in the past, production references were solely based on the maximum rate achieved previously for each NPK grade. This was unrealistic and could be demoralising for operators when such rates were clearly unachievable under current operating conditions. Golden batch references, in contrast, avoid this issue by ensuring the saved database includes NPK references for all combinations of the selected operating conditions.
Production quality is also a high priority for Yara. Consequently, all NPK products are analysed and checked against quality specifications. This includes measurements of chemical content and physical properties, such as granule shape, dusting tendency, and compressibility. Most quality measurements are carried out at least once every 8 hours or determined using online instruments.
As discussed above, one variable, the quantity of undersize granules, is used in the calculation of the comparable production rate. This ensures that quality considerations are incorporated into the identification of golden batches.
As well as this, additional quality criteria are taken into account using ‘quality stars’. For each golden batch, quality star ratings are awarded based on performance of the product batch against a range of variables.
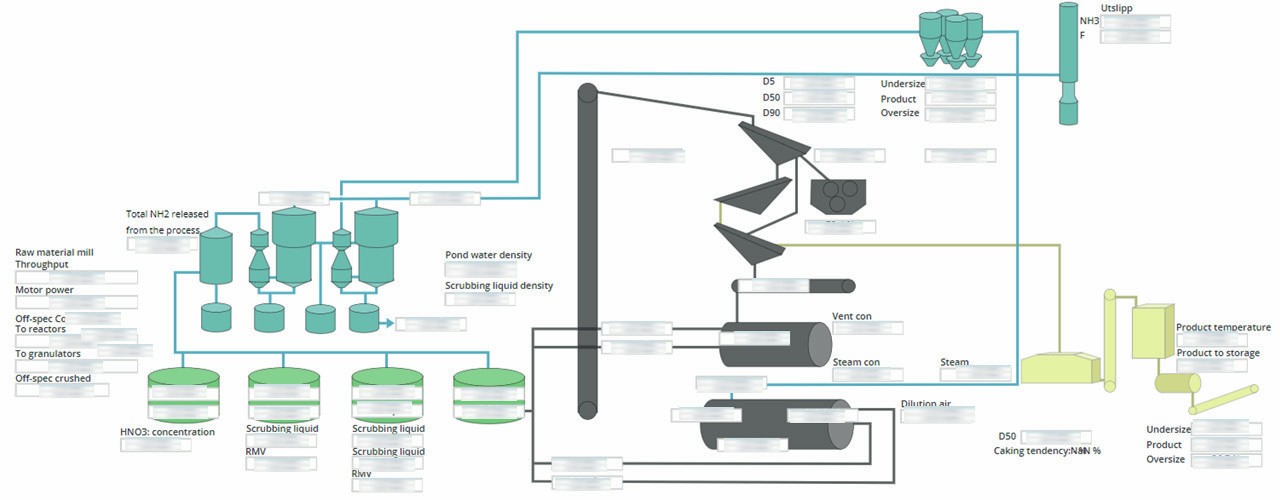
Golden Batch tool user interface
As already explained, Yara was able to establish and categorise golden batches as production references, according to operating conditions and their assigned quality star ratings. Once this was done, a user-friendly interface was developed to allow operators to access this information. Four key operator steps and tool functions were identified:
1. Search for golden batches matching their current operating conditions. A simple search page was constructed, enabling operators to input details on the product they intend to produce and the current plant conditions. Certain conditions, determined by tag values, are also detected automatically, such as outside air temperature.
2. Evaluate the golden batches available. The tool then displays the relevant golden batches to the operator so that they can evaluate them and select the best reference to use for the upcoming production run. For each golden batch, a match percentage is calculated, indicating how well its operating conditions reflect current plant operating conditions. This allows operators to easily evaluate each of the golden batches – based on the percentage score for operating conditions, the production rate achieved and the product quality registered.
3. Select the golden batch to use as a reference for the current production. Operators can then select the best reference based on their experience and their evaluation of current plant conditions.
4. Follow up using the golden batch reference. Process variables are shown by the interface in the form of flow sheet (Figure 1) designed to represent the plant and based on the control system screens (see main photos). This allows operators to easily recognise the production process and quickly see the values of the relevant tags. Having selected the best golden batch reference, operators are directed to the flow sheet where the golden batch values for selected plant tags are displayed. These represent the average values of these tags during the period when the golden batch was produced. Operators can utilise these as benchmarks for the ongoing production, the aim being to align the current plant values with the golden batch values for the relevant tags.
New golden batches
The tool continuously monitors the production process and looks for new golden batches. The discovery of a new golden batch requires all necessary criteria to have been exceeded. The comparable production rate for the period also needs to be higher than it has been in the past for the same operating conditions. Checking for this happens in two steps:
1. Suitability as a candidate: does this production period meet all golden batch criteria?
2. Comparing the candidate batch with historical data: is it better than a golden batch already saved in the database?
Golden batch candidates are called ‘golden windows’. The tool automatically checks for these by periodically monitoring production and assessing whether this has been ‘golden’ in recent hours (i.e., it meets all golden batch criteria), as illustrated in Figure 2.
Potentially, all golden windows could be golden batches. However, only the best golden window from each campaign can be a golden batch. Furthermore, for each NPK product grade and group, only the top three golden windows end up being designated golden batches and made available to users for future reference. In this context, a group is a specific combination of operating conditions – such as high ambient temperature and low clogging, for example.
Evaluation and results
To assess performance, data analysis was carried out after the Golden Batch tool had been live and operational for one year. This assessed plant performance improvements, the uptake and usage of the tool by operators, and operator feedback.
The tracking carried out at Uusikaupunki indicated notably high levels of tool usage. Qualitative feedback on the tool from the plant’s operators was, in general, highly positive. Operator comments included:
- “Easy to find the best batch and information without having to dig in production logbooks. It only takes a little time to get used to it.”
- “More, and more accurate, information than currently available in the production logbook.”
- “You gain courage to run at a high production rate when you know you have gone there before.”
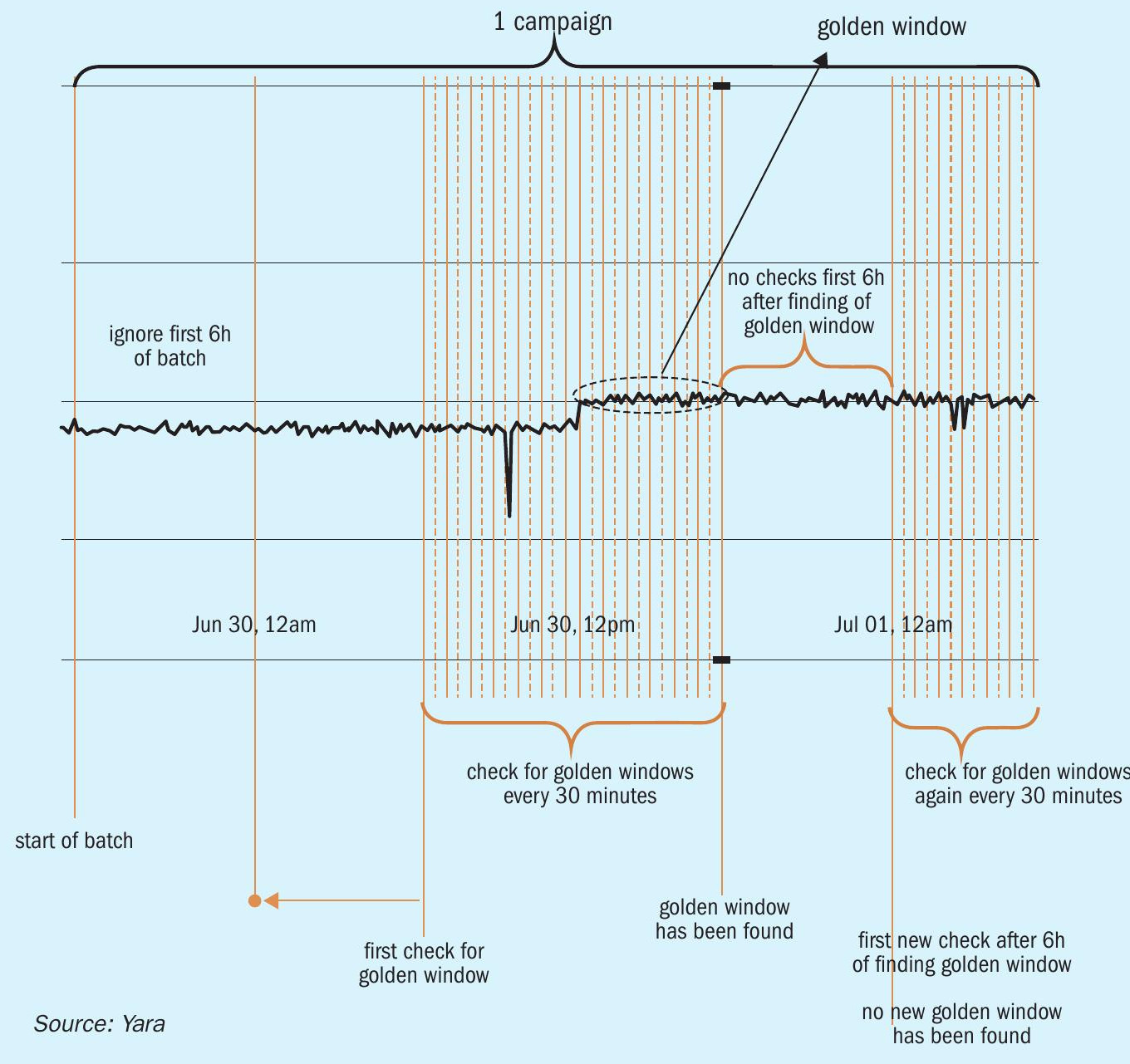
Production logs confirmed that the tool was being actively used in a timely and effective manner. As might be expected, operators often used the tool to search for and select reference batches when they were transitioning between different NPK product grades.
A comparison of average production rates indicated a 2.5 percent increase at Uusikaupunki after the Golden Batch tool became operational. This was not universally true, however, as a product-byproduct analysis revealed an increase in output for some products partly offset by a decrease for others.
An analysis of losses, as documented in Yara’s reporting system, revealed a decrease in losses after the implementation of the Golden Batch tool. An enhancement in overall equipment efficiency was also noted. Importantly, these improvements were achieved without compromising NPK product quality.
Challenges and lessons learned
The journey to develop and scale up the Golden Batch tool encountered various technical, operational, and strategic challenges along the way. Overcoming these also offered valuable lessons, as shared below:
- Data quality and consistency. Individual NPK plants have very different levels of instrumentation. Therefore, when key data is not logged digitally, operators will need to refer to other, non-digital sources instead to find good settings, such as personal logbooks and personal production experiences.
- Complexity of the production process. Some production challenges are hard to accurately measure because NPK fertilizer production is an inherently complex process. Unstable granulation is one notable example. There are many factors that determine how well granules form during production. Not all of these are measured and, consequently, the tool may not be able to support all production settings.
- User training and adoption. Training operators to effectively use the Golden Batch tool requires time, a resource typically limited at production plants. Nonetheless, ensuring comprehensive end-user training and support remains paramount. Experience from the roll out has confirmed that a well-structured training programme, coupled with accessible user manuals and ongoing assistance, contributes to a smoother transition to this new way of working.
Future developments
The Golden Batch tool has been rolled out to eight Yara plants with expansion to additional sites currently underway. As well as helping operational teams increase plant production rates, the tool is also contributing to other continuous improvement activities, such as troubleshooting high emissions, for example. Also, when production issues occur, examination of records for golden batches where these are absent can provides insights into how production can be conducted to avoid these.
The benefits of the Golden Batch tool are independent of the production process. This makes its roll out to plants producing other fertilizer products, not just NPKs, a future option. After all, saving and having access to data for good production periods is relevant for all production plants.
A substantial amount of valuable data, both on tool usage and how NPK plants are operating in comparison to the golden batch settings, has now been collected. An analysis of this data is currently underway to identify which of the golden batch criteria fail more frequently. This is expected to provide insights into potential production bottlenecks at different plants. A separate analysis of how production plants perform over time for different NPK grades is also in progress. The results of this will help in product portfolio planning.
The Golden Batch tool should also support Yara’s other priority areas in future. These include reducing production emissions and energy consumption, as well as ensuring NPK plants have the flexibility to accept different quality raw materials. This can be done by adding emissions and utilities monitoring to the tool, for example. Connecting the tool to data sources for raw material inputs should also enable production settings and production quality to be mapped against the quality of the raw materials being consumed.
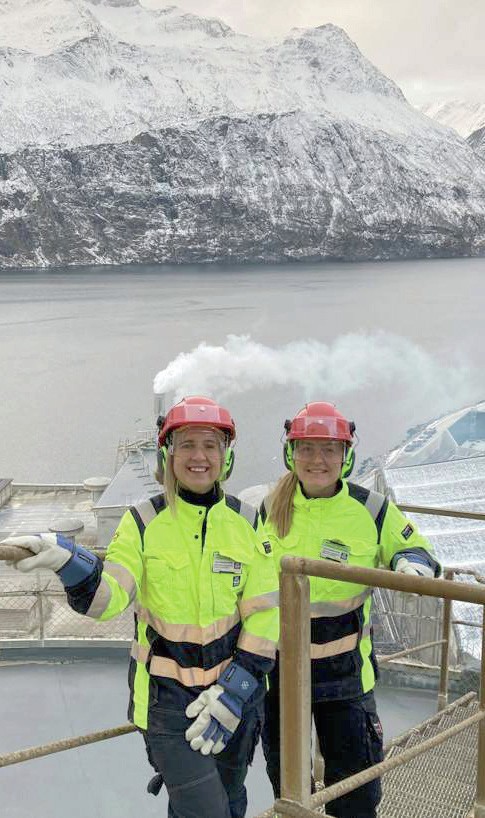
Conclusions
With the deployment of the Golden Batch tool, best operational practice at fertilizer plants is stored and made easily retrievable, to be used as references for current production. This aids operators in pushing up production rates as well as helping troubleshoot process issues.
This article provides an overview of the journey from ideation to realisation, highlighting the collaboration between Yara’s Digital Production team and engineers at the company’s NPK fertilizer plant in Uusikaupunki, Finland.
As the tool is rolled out to eight plants and its use expands, continuous improvements are being implemented, based on the feedback and experiences of operators. Each new deployment prompts plant-specific refinements, alongside general updates to the user interface and the introduction of new functionality.
Future planned developments include using the data collected by the tool for continuous plant improvement activities and adding capabilities for monitoring emissions and energy consumption. The feasibility (and desirability) of securely integrating the Golden Batch tool as part of the control system – so it is directly available to operators – is also being investigated.
Importantly, the tool is not specific to just NPK production. This raises the possibility of a roll out to other types of fertilizer production plants as a future option.
About the author and the article
Marianne Ytterbø is Yara’s Product Manager at Digital Production for the Golden Batch application. This article is based on the paper presented at the International Fertiliser Society (IFS) Conference, Cambridge, UK, 7th December 2023, and subsequently published by the Society.
Reference